- 1Department of Manufacturing Engineering, School of Mechanical Engineering, Vellore Institute of Technology (VIT), Vellore, India
- 2School of Information Technology and Engineering, Vellore Institute of Technology (VIT), Vellore, India
- 3Department of Mechanical and Electromechanical Engineering, National ILan University, Yilan City, Taiwan
The Aluminum metal matrix with particulate reinforcements is the new future of the coming industrial revolution due to the higher strength and availability. Composite reinforcements such as SiC, TiB2, B4C, and others contribute significantly to the increased strength of the Aluminum metal matrix, which can be an optimal choice, also at a lower cost, in some applications where Aluminum is considered or proven to withstand high temperatures. Ultrasonic welding is the process, where, we get the electrical energy, which converts and amplifies into vibration energy for the welding to occur. The challenge we face today is the thickness limitations in ultrasonic welding. The ultrasonic welding of the Aluminum metal sheet with the reinforcements may affect it, as the addition of particulate reinforcements will increase the strength of the Aluminum matrix. Ultrasonic welding can only support a metal sheet with a thickness of up to 2.5 mm in the case of an Aluminum plain sheet. However, if the strength of the Aluminum metal matrix increases, the next step is to achieve ultrasonic welding with the same thickness of Aluminum matrix and reinforced composites that have greater strength than a standard Aluminum sheet. This review will focus on the parameters and the factors which may help decrease the difficulties of Ultrasonic Welding of Aluminum MMC, alongside reviewing the current technologies and research works.
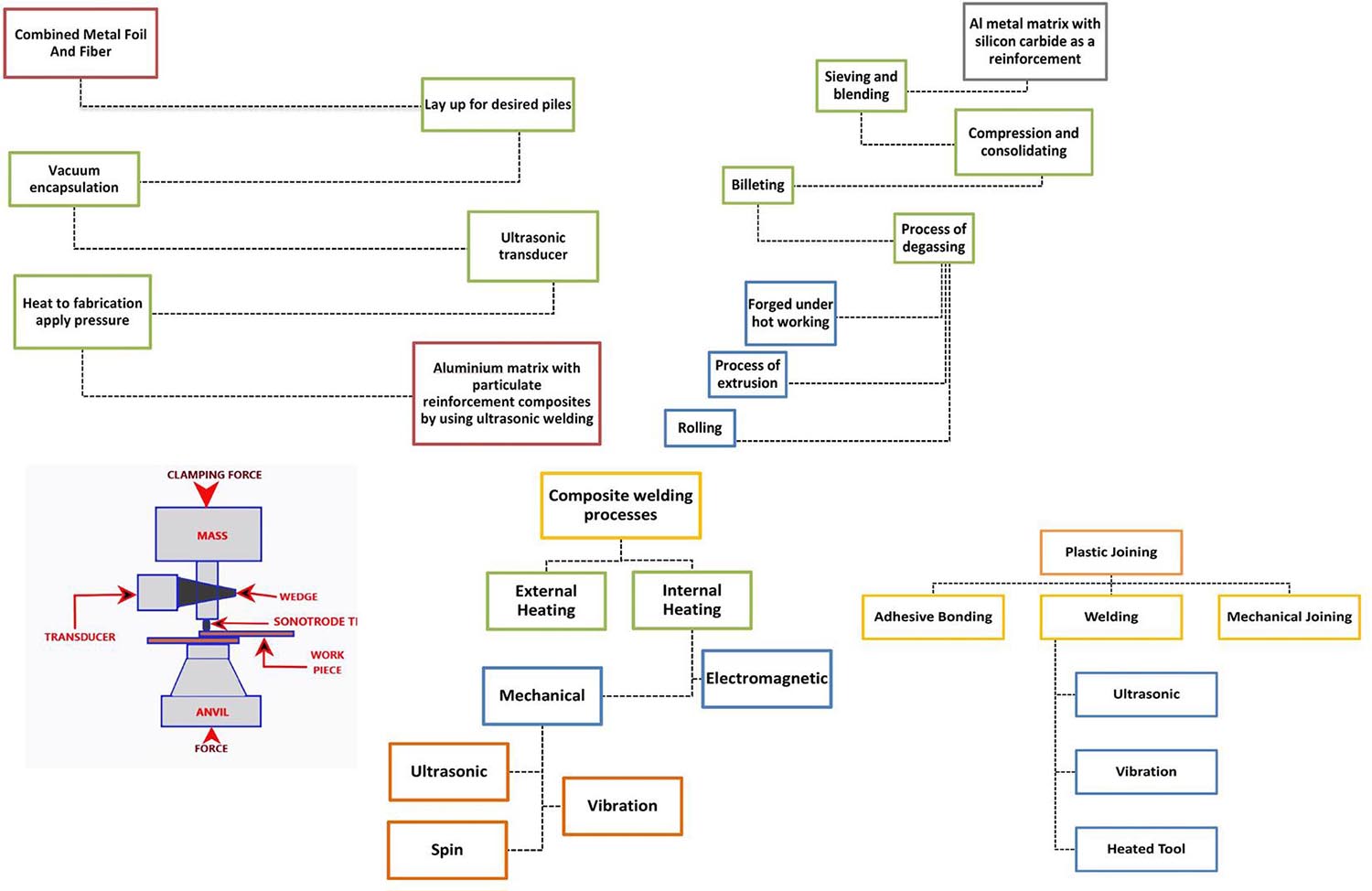
Graphical Abstract. A Brief Review of the Ultrasonic welding process flow and sequence for joining aluminium metal matrix composite.
Introduction
Aluminum, the most abundant metal on earth’s crust, is well known for its corrosion resistance and low density, which allows it to be a benefit for the aviation industry (Wu et al., 1996; Reddy et al., 2009; Ramnath et al., 2014; Raviteja et al., 2014; Shinde et al., 2020). The oxygen bonds with pure Aluminum are quite strong, which is forms or as alumina from the bauxite ore. It undergoes the oxidation process when exposed to the external atmosphere and forms a coating of Alumina (Al2O3). It is hard to surpass this protection over pure Aluminum when kept in an open atmosphere. It has a higher melting temperature than that of pure Aluminum if taken under ideal conditions. The corrosion-resistant nature caused by alumina’s presence over the surface of pure Aluminum is a boon to the industries. The particulate reinforcement in Aluminum enhances its mechanical properties. Also, this brings an advantage for the welding of an Aluminum sheet, which was usually tricky due to alumina’s presence, which acted as a protective shield over the Aluminum surface. Aluminum is the metal available in plenty and with particulate reinforcements as a replacement can be an alternative in many fields across industrial applications which range from home appliance parts to the large-scale heavy electrical industries, aviation and aerospace industries, etc. Due to this rise in demand and special properties and specific similarities to some metals, Aluminum related processes need some advanced research. Also, it can create feasibility in many processes, where some costly and decrease the usage and wastage of rare metals can especially in automotive industries (Surappa, 2003).
Ultrasonic welding has gathered its own pace, in gaining its importance in the potential industrial revolution and technological advancements. The process of ultrasonic welding is for joining similar or dissimilar metals and plastics (Maria, 2014). This process uses vibration energy and relative motion of two similar or dissimilar metal sheets, and the welding process takes place with the fusion of the metal sheets at the point where a sonotrode tip concentrates will experience frictional heat. Figure 1 shows the general process flowchart.
Different types of particulate reinforcement composites are used to make Aluminum ready for welding. Each particulate reinforcement has its distinct properties and depends on the method or the process and the applications to be used. The metal matrix is reinforced with the prerequisite composites (Chak et al., 2020). These usually involve Titanium Diboride (TiB2), Boron Carbide (B4C), Silicon carbide (SiC), etc. For the particulate reinforcement usually stir casting process is used. Further, this is an in-situ method that gives us a better particle-matrix interface and thermodynamically stable outcome.
Mixtures and particles are more delicate. The stir casting process is exothermic, where reactions occur during this frictional heat generation, which gives us a self-stabilizing result once the frictional heat comes into play (Laha et al., 2004; Daoud, 2005; Muñoz-Morris et al., 2005; Pal, 2005; Sukumaran et al., 2008; Mahesh et al., 2011; Bhandare and Sonawane, 2013; Kumar et al., 2013; Inegbenebor et al., 2016; Annigeri Veeresh Kumar, 2017; Horikiri et al., 2017; Srivyas and Charoo, 2018; Vanam et al., 2018; Kumar Sharma et al., 2020).
Details of the Process
Aluminum Matrix Reinforcement
The most efficient and used process is stir casting (Segal, 1995; Etter et al., 2003; Ruch et al., 2006; Saravanan et al., 2007; Yin et al., 2008; Kocimski et al., 2009; Ramu and Bauri, 2009; Xue et al., 2011; Alhashmy and Nganbe, 2015; Li et al., 2016; Kumar and Birru, 2017), for particulate reinforcements. Comparing different methods for Silicon Carbide to be reinforced into the Aluminum metal matrix are compared in Table 1. Moreover, to form a metal matrix, there are several methods used, and they have various range of sizes and shapes; also, when their volume fractions vary, they are prone to give damages to the reinforcements as well as the cost of these methods may vary according to the requirements (Amouri et al., 2016; Jeykrishnan et al., 2017; Prakash et al., 2018).
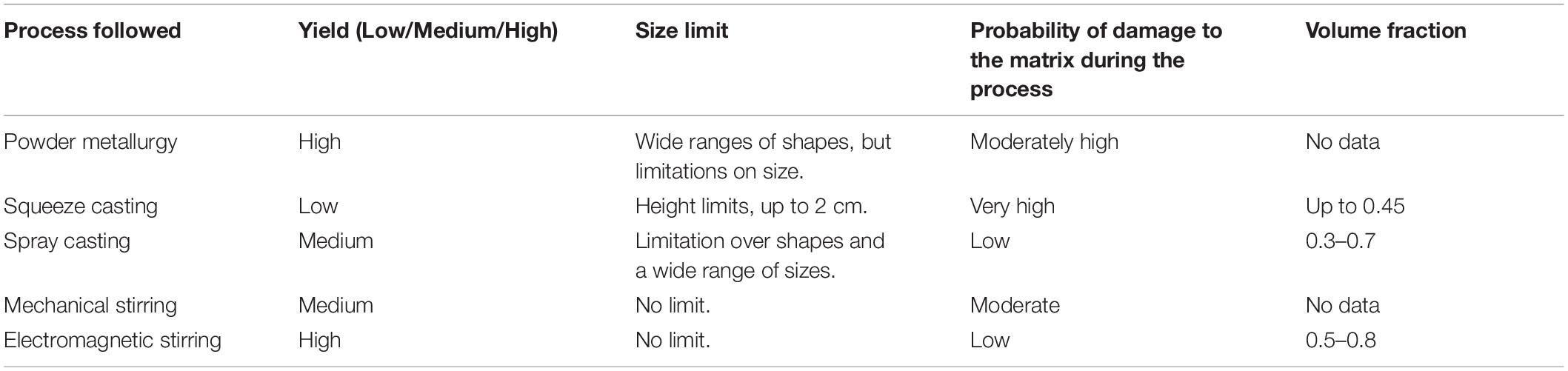
Table 1. Comparison of processes for particulate reinforcements (Sijo and Jayadevan, 2016).
An increment in the Aluminum matrix composite’s tensile strength was reported after the addition of Silicon Carbide (Hashim et al., 2001). As the gradual increment of Silicon carbide by %weight, the tensile strength’s positive change is recorded. With Silicon Carbide, 0% by weight, the tensile strength was 28.5 MPa, and at 5wt%, 20wt% of SiC the composite showed 59.4, 77.56 MPa of tensile strength, respectively, but at 10% by weight of SiC, it displayed a decrease in tensile strength. The addition of SiC displayed less wear of the matrix composite. Also, iron, silicon, manganese, copper, magnesium, and Aluminum can increase the Aluminum matrix’s wettability (Rahman and Rashed, 2014). Specifically, iron gives special properties to the matrix, which involves the uniform distribution of reinforcement, enhanced tensile strength, and grain structure.
Bodukuri et al., 2016, found that the addition of SiC and B4C can cause variation in the densities (Bodukuri et al., 2016). Four types of densities observed are Apparent, tap, green, sintered. There were three combinations, which are as follows:
(1) Aluminum was 90%, silicon carbide was 8%, and boron carbide was 2%;
(2) Aluminum was 90%, silicon carbide was 5%, and boron carbide was also 5%;
(3) Aluminum was 90%, silicon carbide was 3%, and boron carbide was 7%.
Among the above combinations, the second condition’s sample gave the best results. It displayed an apparent density of 1.4, tap density of 1.7, green density of 2.8, and a sintered density of 2.9. Hence this study showed that the percentage of Boron carbide has also played a vital role. The hardness decreased as the Boron carbide decreased by the percentage. Table 2 shows the comparison of the mechanical characteristics for different reinforcements for AMCs, Srivatsan et al. (1991) discussed some standard procedures by sieving follow particulate reinforcement. Then, blending or mixing occurs when we usually add a lubricant in powdered form. Then, it proceeds for compression, which will help us create and consolidate the mixture we have obtained into a particular shape would be required. Then it can machine over the surface of the finally obtained matrix. The process of degassing will take place in such a way we will remove all the entrapped gases from the matrix and would proceed further with the process of forging, extrusion, or rolling (Yashpal et al., 2017). Figure 2 displays further processing after the Aluminum matrix casting with Silicon as a reinforcement.
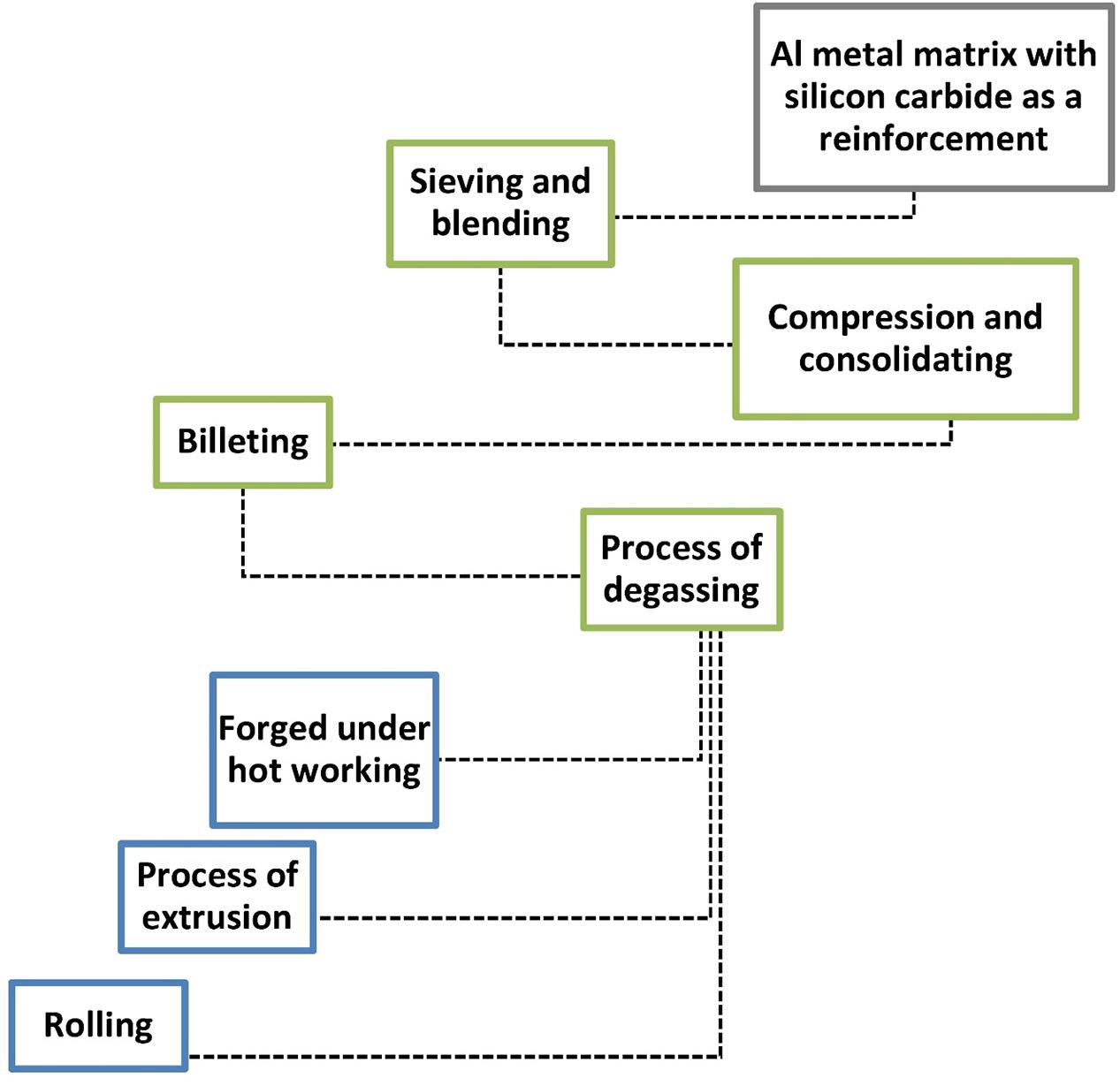
Figure 2. Further processes after casting of Aluminum MMC with SiC addition by stir casting process.
Ultrasonic Welding
The ultrasonic welding process uses a frequency converter that consumes low power and converts to high frequencies’ mechanical power. Figure 3 displays the Ultrasonic welding setup. It has a clamping or pneumatic force applied along with a convertor or piezoelectric transducer, which converts high-frequency electric power supplied by the ultrasonic generator into vibrating motion or vibrating energy, which is further supplied to the horn, concentrating the sonotrode tip on the weld area. The metal sheets to be weld kept on an anvil which will be static (Tsujino et al., 1996; Truckenmüller et al., 2006; Suresh et al., 2007; Ultrasonic Welding, 2009; Yashpal et al., 2017).
Then the heat generation takes place, which would due to this heat generated, the sheets to be weld will experience fusion, which will join them. Hence using ultrasonic frequencies, we can weld two similar or dissimilar thin metal sheets. For an Aluminum sheet without particulate reinforcements, a limit of 2.5–3 mm of thickness is considerable. But, when we add particulate reinforcements in the form of composites, we may experience difficulty using the metal sheet with the same thickness as possible in the general case of the probably pure Aluminum sheet. In the process of ultrasonic welding, the thickness of a workpiece of hard material is usually limited to 1 mm (Hassan et al., 2009; Panteli et al., 2012; Wagner et al., 2013).
Welding pressure is the most important factor which may influence the outcome of any resulting weld, its strength, or the workpiece may be obtained damaged if the pressure tends to be excessive. The clamping force or the welding force also has a huge significance, where by using a load cell the welding force should be calibrated for direct comparison of welding forces to be made, this value varies in different machines.
During ultrasonic treatment, the holes and selectivity of SiCp/Zn-Al filters of metal molecules are cut, and the dispersion of SiC particles is assumed to be similar in both large and small sizes (Truckenmüller et al., 2006). A mechanical actuator is used to create an outer vortex of water to mix the metal liquid well, to help move the smooth parts, and to hold the shapes in place in the suspension; an actively mixed solvent accelerates the risk of traps and gas leaks, creating high porosity in the molten material. Cavitation organizes, improves small air sacs, blows, and falls into water under high-power cyclic ultrasound waves. These large air pockets freeze and float outside the pool due to flooding. Thus, the elimination of dissolved gases dissolved in the water takes place. The small size of the closed bulbs and their larger size, being responsible; when the cavitation in water is performed, it is speedy to lower it to make a more comprehensive volume; unfortunately, stresses are still induced in the bond formed by this metal filling (Yang and Li, 2007; Wagner et al., 2013; Yashpal et al., 2017).
Further, this suggests that pure ultrasonic cavitation is formed within the filler. Agglomerate dispersion and prevention of new coagulation of Silicon carbide particles, not all gases can be removed (Panteli et al., 2012). The manufacturing process and classification of the welding process used for joining composite are shown in Figure 4, and polymeric is shown in Figure 5.
Process Parameters
The process parameters discussed are based on the literature surveys, and collecting evidence from various research works done to date. These parameters will possibly direct the researchers to understand and follow the steps which tend to give an ideal result, irrespective of the cost. Key findings of the literature are provided in Results which explains why these parameters are optimum.
(1) The Aluminum will undergo passivation, and the Aluminum-Oxygen bond is very strong and may be difficult to breakdown this bond. Ultrasonic cavitation is a process that can be used to remove the oxide layers from the aluminum surface, which is quite an efficient process in comparison to the other processes when taken into consideration on the surface level.
(2) The stir casting process for the aluminum obtained with the addition of hard composites like SiC would be done. The cleanest interface of an Aluminum MMC is obtained by the stir casting process. Some additions may include molybdenum, titanium, etc., in small amounts.
(3) After we obtain the stir-casted Aluminum MMC, the next step will be to set the ultrasonic welding machine. We will keep the workpieces over the anvil and press the horn tip over the surface. We need to check if the workpieces are aligned correctly or not kept over the anvil.
(4) Trigger force has to be regulated before the welding, depending on the type of metal used. And the effect of pressure applied over the welding spot will decide if the weld strength and if it has been successful or still requires increment in the pressure for the fusion to take place for a successful joint.
(5) The frequency to be used for the welding processes is 15–40 kHz, which is optimum for plastics and some metals, but Aluminum MMC is having higher tensile strength, the frequency may range up to 70 kHz for the process (Kim et al., 2017).
(6) It has a frequency converter, which will use low power and starts to convert to electric power of high frequencies. After obtaining the electric power of high frequency, we will see how the transducer will eventually convert this high-frequency electric power supplied into vibrating energy.
(7) This vibrating energy is targeted toward the horn, and under this horn, we have a sonotrode tip that will be concentrating on the workpiece surface to weld. The sonotrode tip will eventually generate heat of fusion at the point of its concentration.
(8) During this heat generation, the workpieces (usually the plates or sheets of Aluminum) will eventually experience fusion amongst their aligned surfaces, in between which the tip is focused kept over the anvil, here anvil is static for the energy concentration by the means of tooling profile, which is mounted to the anvil (Tee et al., 1999; Siddiq and Ghassemieh, 2009; Tsujino and Sugimoto, 2014; Rana and Badheka, 2018).
Results
The ultrasonic welding process is used to fabricate Aluminum alloys very commonly (Daniels, 1965; Suresh et al., 1993; Yang et al., 2006; Bhandare and Sonawane, 2013). The MMC, which is to be utilized for structure-related processes, also includes ceramic fibers like silicon carbide. The expected results of each element in the MMC are not directly applicable for or reinforcing the ceramic fibers into the MMC. The physical characteristics, along with mechanical, thermal, also chemical properties, come into play. That temperature and orientation of fiber are also the major contributors for reinforcement of ceramic fibers concerning the direction of welding, with each property having its dominance in the role they play in ultrasonic welding of the MMC. The temperature has a significant influence during the process because it has to be kept in focus during the bond formation to avoid excessive plastic deformation during the interface during the necessary bond formation process. Fiber orientation is fundamental during the fabrication process because its isotropic properties concerning welding access are also considered. Hence, keeping all the parameters into count, in this way, it would obtain the final product, which is welded workpieces of Aluminum by using ultrasonic welding. However, this is applicable for some cases of Aluminum thicknesses, which will range up to less than or equal to 1 mm, because if we try to operate the system with a harder workpiece with similar thickness as in a pure Aluminum case, then it will eventually fail to complete the process of welding, or may damage the ultrasonic welding machine in some cases, especially the tip (Ma et al., 2020). Table 3 is shown in the ultrasonic vibration time(s) v/s shear strength (MPa).
We know that Aluminum is a high corrosion resistive metal; because of alumina’s presence, which has a higher melting temperature than that of pure Aluminum, and we reinforce Aluminum because it increases the strength of the Aluminum matrix so that we can use it in different fields where we need to replace the traditional methods, which are still in use and are a significant cause of depletion of valuable metal, which can be easily replaced by Aluminum and also pointing out toward the abundance of Aluminum present in earth’s crust (Bodunrin et al., 2015).
The mixing of Aluminum and silicon takes place using stir casting, which will give us an Aluminum with the particulate reinforcements with an appropriate and homogenously dispersed mixture of the composites inside the metal matrix (Khmelev et al., 2016; Sarraf and Akrawi, 2016; Gao et al., 2018). We have to see the ultrasonic welding process’s effect when we take the stronger and an Aluminum matrix, having mixed with silicon. The ultrasonic welding process will have to take place with a workpiece that has a thickness of near about 1 mm or less than 1 mm (thickness depends and varies from metal to metal or the plastic or any other material if used, as ultrasonic welding also works for dissimilar metals) in case of Aluminum MMC, to avoid failure of the welding process. If there is any failure reported, the reasons can be due to the process parameters implemented. Furthermore, Aluminum with reinforced composites is now much stronger than the local or pure Aluminum and consists of silicon carbide added, which increases its tensile strength. Molybdenum is also added in some cases to avoid a compromised ductility in the metal (Tsujino et al., 2002; Yang and Li, 2007; Siddiq and Ghassemieh, 2010; Salih et al., 2015).
Ceramic Matrix Composites, where ceramic is the matrix where reinforcements can take place. Metal Matrix Composites, where metal is the matrix phase, which would be reinforced. Aluminum metal matrix composites (AMMCs), where the metal matrix is Aluminum, and the particulate reinforcements were containing mostly ceramics. For example, Titanium borate, silicon carbide, boron carbide, etc. When it comes to getting a result in the ultrasonic welding process, we have to be very careful about some factors involved during this process, which may affect the process of ultrasonic welding positively and negatively (Neppiras, 1965; Benatar and Gutowski, 1989; Gunduz et al., 2005; Rabiei et al., 2008; Matsuoka and Imai, 2009; Sarkari Khorrami et al., 2015). Table 4 is shown the reinforcement composition in different types of Aluminum matrices.
The particulate reinforcements may have an effect contributing to the final results obtained. Table 4 in the ultrasonic welding process, there is a high frictional force generated by the sonotrode tip, due to the presence of dry friction, at the interface of welding of the two metals joining, which is tangential to the surface of the workpiece, is experiencing a rapid increase in temperature over its surface (Xu et al., 2005; Harichandran and Selvakumar, 2016; Chaubey et al., 2020; Madhukar et al., 2020). Furthermore, if the force is not sufficient during the operation, it may not transfer the ultrasonic oscillations that are supposed to generate the heat of fusion using the frictional motion of the sonotrode tip. The changes in the sheet’s weld interface on a microstructural scale after undergoing the welding will experience the excitation of particles which may lead to the fusion of the metals (Xu et al., 2005).
The particulate reinforced Aluminum matrix’s tribological character can be concluded according to the recent research works and the literature survey in section “Aluminum Matrix Reinforcement,” the stir casting process has obtained a clean surface with dispersed reinforcement particles within the matrix with no internal clustering of reinforced composite particles. Also, there is an increase in the hardness in the Aluminum matrix considerably. Along with this, internal intermetallic bonding should be avoided. The addition of molybdenum is one of the options available, which will substantially show increments in tensile strength and homogenous dispersion of the particles across the metal matrix (Sudha et al., 2013). The ductility of the Aluminum metal matrix may be compromised after the addition of composites, which are mostly ceramic particles, so the use of more rigid metal particles can be done to avert a situation of compromised ductility, which can also lead to failure of the component made using this metal matrix with the particulate reinforcements. Excessive SiC addition will also be a cause of failure of the Aluminum MMC, as it may compromise the ductility. The addition of silicon carbide in a limited amount (up to 10wt%) (Babalola et al., 2019) also ensures to reduce surface wear (Gopal et al., 2012; Sudha et al., 2013; Yuvaraj et al., 2015; Taherzadeh Mousavian et al., 2016; Lionetto et al., 2017, 2018; Babalola et al., 2019; Garg et al., 2019).
In this review, we have mainly focused on Aluminum’s MMC. Because we need strength in most of the fields, in which we have seen the involvement of Aluminum-based components in various industries. Expeditiously, we have focused on ultrasonic welding of Aluminum MMC and are commonly reinforced with silicon carbide, which is more prominently used (Bobić et al., 2009; Kala et al., 2014; Raju et al., 2015; Maurya et al., 2016). Tables 5–7 show infiltration pressure v/s thermal conductivity at different temperatures.
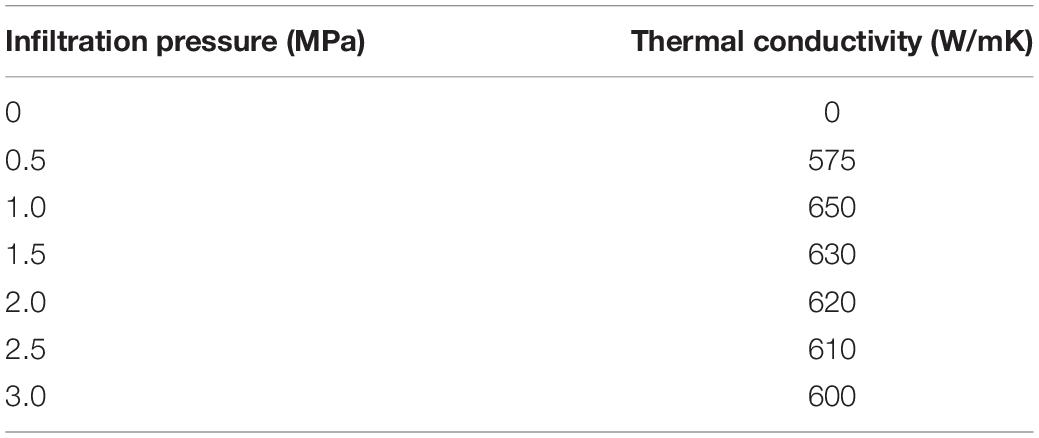
Table 5. Infiltration pressure v/s thermal conductivity (at 750°C) (Zhang et al., 2014).
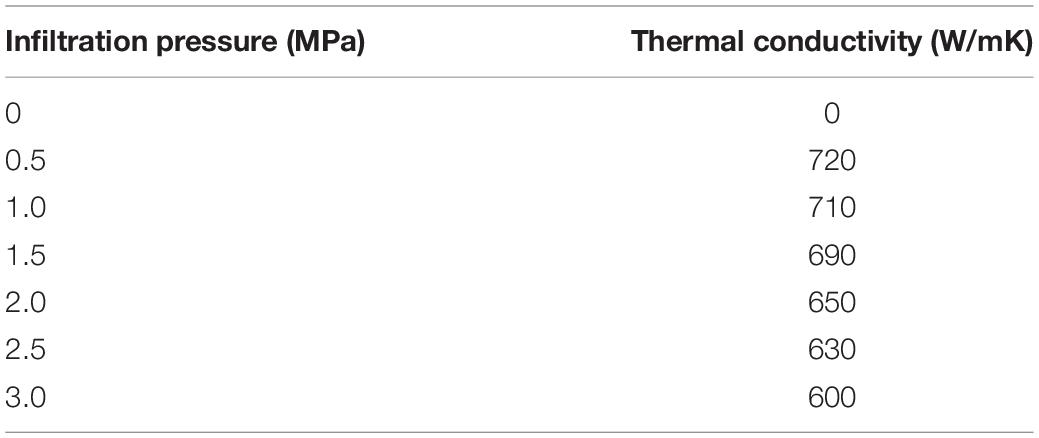
Table 6. Infiltration pressure v/s thermal conductivity (at 800°C) (Zhang et al., 2014).
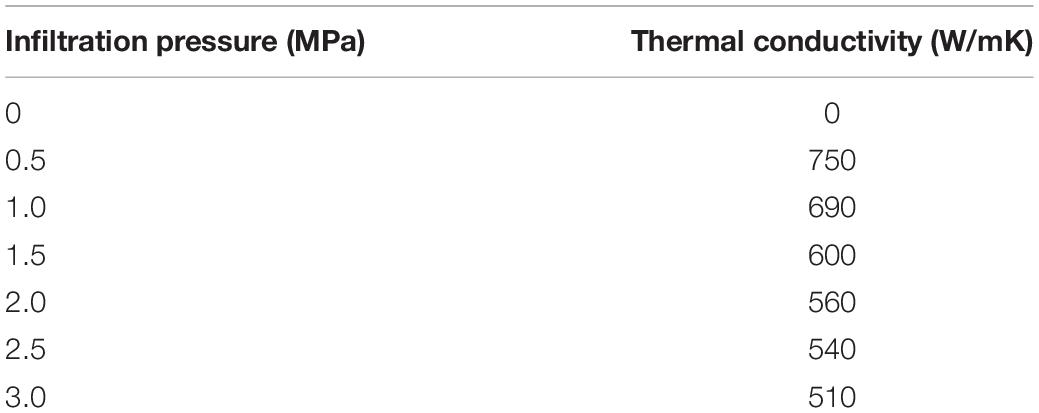
Table 7. Infiltration pressure v/s thermal conductivity (at 850°C) (Zhang et al., 2014).
The diffusion rate in the Aluminum matrix is directly proportional to the infiltration temperatures and pressure, i.e., the diffusion rate will also increase alongside an increase in infiltration pressure and infiltration temperature. Further, this illustrates that there can be an optimum value of pressure where we can observe maximum thermal conductivity. While there is an increase reported in the infiltration temperature, this optimal pressure will decrease gradually (refer to Tables 5–7; Zhang et al., 2014).
The stir casting process starts with a preheating of the workpiece for an hour at 700°C (Venkatesh et al., 2019). The next step is to overheat for three-quarters of an hour, followed by the salts’ addition or what we call the reinforcement ingredients, including silicon carbide or titanium borate, etc. along with a significant amount of molybdenum. The next process is mechanical stirring and ultrasonic vibration, followed by removing the slag after the primary process is completed. Physical methods like chipping wire brush remove the unrequired or accidentally entered components in the matrix. This has the last step: bottom pour casting, which is done using ladles and pours stopper rod for efficient pouring. After completing all the procedures mentioned above, we will obtain a stir casting result of the Aluminum metal matrix. It can be further extruded out at first and then can be machined according to the requirements.
Factors that will affect our results in ultrasonic welding which will have an impact on the final product of welding:
(1) Design of joint is the most critical part of the discussion when we come across the ultrasonic welding on the resulting weld. The joint’s design will affect in many ways geometrically, depending on machining done on the surface, appearances, and capability of molding. The most common and best results obtained from Ultrasonic welding are in Lap joints (Leng et al., 2017). The Design For Manufacturing (DFM) review is always mandatory before the process starts and in such cases to avert such design-related issues, which can cause issues with the welding device as well as with the component with a complicated design being welded with that particular welding device, here ultrasonic welding device (Poli, 2001).
(2) The frequency ranges involved in the welding process may have an adverse effect during the process, which usually ranges from 15 to 40 kHz is the usual range for plastics, for metals it may extend up to 70 kHz. Welding strength increases with the welding time under any conditions, at 40 kHz the welding strength is smaller than that at 20 kHz (Kim et al., 2017). This is due to friction heat between the metal sheets at a point where the horn tip is concentrated, and Aluminum diffusion is facilitated better at 20 kHz than at 40 kHz. This parameter will determine the device equipment, which is perfect for use in any case. For example, delicate and small components or parts with very minute tolerance values will require high frequencies, which will help apply pressure at a point with more accuracy and the adverse effects of ultrasonic vibrations. Moreover, let us consider medium-sized or the more prominent components, low frequencies up to 15 kHz, where the process outcome, i.e., the weld quality is apt (Daoud, 2004; Yang, 2008; Elangovan et al., 2009; Yan et al., 2011).
(3) The type of material used is a factor that may have a significant effect on the final result. The strength of the metal sheet will have an impact on the resulting weld. The temperatures recorded during the Ultrasonic welding process at the weld interface should be less than that of the melting temperature reported for an Aluminum alloy (Siddiq and Ghassemieh, 2008). The thickness is also a significant factor here; when it considers Aluminum with reinforcements, that due to the presence of composites like silicon carbide, there might be an increase in tensile strength reported, so the customarily used Aluminum (pure or local quality) has a limit of 3 mm thickness which can be welded whereas, in case of Aluminum MMC optimum thickness is only 1 mm (Wang et al., 2016). Furthermore, when the reinforcement is taken into account for the metal matrix and the strength increase will surely pull down the limit of the workpiece’s thickness to be used to near about 1 mm or lower.
(4) The ultrasonic welding process parameters may also have a variation and influence the final welding. The setting-like amplitude is to be adjusted appropriately, as the amplitude increases the intermetallic thickness increases, and the trigger forces the time setting (Figure 6) and energy or distance-related settings. In particular, the limits have to be set in such a prescribed way or will give a significant result (Daoud, 2004). The amplitude setting is to control the vibrational amplitude. Time settings are the setting for or limiting the time for vibration during ultrasonic welding. The trigger force is to specify the appropriate amount of pressure to be applied over the workpiece during ultrasonic welding. The parameters are crucial because if incorrect or insufficient parameters are given into the input, this may cause an issue within the welding setup and may result in flaws in the resulting weld we will obtain (Sharma et al., 2019).
(5) The horn used during the ultrasonic welding process is an essential part. During the process, it needs to be fabricated using a material having acoustic properties and high fatigue strength. The prerequisite properties of the horn material must be having longevity and durability. The use of Titanium is appropriate.
Zhu et al. (2011), performed this experiment for mechanical property analysis, the shear test method was selected for the final determination of failure around the welding point to assess the welding’s effectiveness and the weld’s bond strength and strength over the Aluminum alloy matrix. The sonotrode tip surface was not ideal and was a sand grinding surface. The possibilities that fewer or no atomic bonds within the welded region can be reported are high when there is very low weld strength or if the required welding time required for welding the workpiece was not sufficient. As per the graph in Figure 6, the welding joint’s strength seems to decrease after a specific time limit was reached (Zhu et al., 2011).
When it comes to results for the peel test, there are some points which are the conclusions concerning the graph (Figure 6), are as following:
The objective of welding an Aluminum MMC to any other metal is expected to be difficult, and weld strength can be decreased, if the sonotrode operation, i.e., the vibration energy applied will not be sufficient to obtain a strong weld.
Along with short welding time, there might be a possibility that there are residual oxides at the weld surface because the presence of oxides may hamper the weld strength of the joint. Particularly while welding, the gases may have entrapped during the high temperature of the weld pool. The lack of precaution may cause this issue to occur in the first place (Siddiq and Ghassemieh, 2008; Zhu et al., 2011; Sharma et al., 2019).
Conclusion
The production strategies most commonly used to make AMC are briefly described in this article. Mixing and powder metallurgy are most commonly used. Supportive design measures, such as extrusion, rolling, and production, are effectively updated to improve mechanical properties. Advances in recycling innovation for AMC are still an open area where some restrictive revisions should be possible for the times to come for a potential industrial boom (Tee et al., 1999; Mordyuk et al., 2014; Tony Thomas et al., 2014).
Aluminum MMC’s mechanical properties depend on the type of mesh, forces (simple, diverse, speed, size, flow in the frame), wettability, and response during the forming cycle. Mechanical and agricultural wastes are used as a reinforcing element in Aluminum MMC. Less work has been done on the improved nanomolecular compound, which requires additional testing of the formation cycle and updating the nanocomposites’ mechanical properties (Mavhungu et al., 2017; Garg et al., 2019; Singh et al., 2020).
• Some screening and simulation methods have been developed in such a way that they will predict the mechanical properties. The combination of several demonstration procedures predicts a reaction with greater accuracy and reliable quality than a particular technique.
• AMCs have been used effectively in space innovation, the aerospace industry, the automotive segment, electric and electronic fields, and other applications. It is also considered necessary to select an evaluation to examine AMC is used on a significant scale as it is effective (Yang et al., 2004; Rao and Padmanabhan, 2012; Patel et al., 2015; Ramanathan et al., 2019).
• The current challenge of removing alumina coating efficiently still exists as alumina (Al2O3) the passivation layer is difficult to surpass; this is a boon and a bane for the industries. Alumina helps Aluminum to be able to resist corrosion even in extreme environments if taken in ideal conditions (Agarwal et al., 2002; Raja and Raja, 2014; Garg et al., 2019). And alumina is a bane for a fundamental reason, as we know that alumina has a higher temperature than pure Aluminum. Alumina removal-related technology has been tested using ultrasonic cavitation or by addition of Sodium Hydroxide (Dimitescu et al., 2018; Mehrabian et al., 2018; Nayebi et al., 2018; Long et al., 2019; Park et al., 2019). But even if implemented, current industries can potentially face more cost in manufacturing Aluminum-based components and removing alumina. It would be primarily the cost of the machine, its power consumption and maintenance included, if we consider about the machine, we use is completely removing alumina coating, hypothetically for now (Griffiths and Turnbull, 1994). Research in this area is still required in terms of cost-cutting and Lean Six Sigma implementation studies can also be done to reduce wastage and increase working efficiency.
• Aluminum has a bright future in welding because of its density, the aviation industry is thriving, and the abundance of aluminum and aluminum with reinforcements will have a significant contribution to the replacement of some rare metals in many fields of research and many parts of the industry (Srinivasan and Senthil Kumaran, 2020; Srinivasan et al., 2020). In the coming future, the steel consumption-related indexes may vanquish, but the maximum abundance of aluminum under the crust of earth will help the world sustain itself in the future.
• Ultrasonic welding device requires an extensive amount of research for the horn and sonotrode tip, for thicker metal work pieces (i.e., sheets, plates, etc.) to be utilized and to create ease in future projects involving dissimilar metals or harder metals and eradicate the issues related to thickness. The aluminum reinforced metal matrix, if taken into consideration, would need very high research work over the lower frequencies, which will help generate a tremendous amount of friction force and allow the fusion of thicker metals.
Author Contributions
SS and KS: conceptualization, methodology, software, and formal analysis. Y-CH: validation, supervision, project administration, and funding acquisition. SS, KS, and UC: investigation. UC and RM: resources and data curation. SS, UC, and RM: writing—original draft preparation. KAr and KAp: writing—review and editing and visualization. All authors have read and agreed to the published version of the manuscript.
Funding
This research was partially funded by the Ministry of Science and Technology of Taiwan, grant nos. MOST 109-2221-E-197-011 and MOST 109-2622-E-197-007-CC2.
Conflict of Interest
The authors declare that the research was conducted in the absence of any commercial or financial relationships that could be construed as a potential conflict of interest.
Abbreviations
Al, Aluminum; MMCs, Metal matrix composites; SiC, Silicon carbide; Al2O3, Aluminum oxide; SC, Stir casting; PM, Powder metallurgy; SQ, Squeeze casting; CC, Compo casting; CG, Centrifugal casting; EMS, Electromagnetic stir casting; PI, Pressure-less infiltration; ARB, Accumulative roll bonding; IC, Investment casting; ISPM, In situ powder metallurgy; HT, Heat treatment; p, Particles.
References
Agarwal, A., McKechnie, T., and Seal, S. (2002). The spray forming of nanostructured Aluminum Oxide. JOM 54, 42–44. doi: 10.1007/bf02709093
Alhashmy, H. A., and Nganbe, M. (2015). Laminate squeeze casting of carbon fiber reinforced aluminum matrix composites. Mater. Design 67, 154–158. doi: 10.1016/j.matdes.2014.11.034
Altinkok, N., and Koker, R. (2004). Neural network approach to prediction of bending strength and hardening behaviour of particulate reinforced (Al–Si–Mg)-aluminium matrix composites. Mater. Design 25, 595–602. doi: 10.1016/j.matdes.2004.02.014
Altinkok, N., and Koker, R. (2006). Modelling of the prediction of tensile and density properties in particle reinforced metal matrix composites by using neural networks. Mater. Design 27, 625–631. doi: 10.1016/j.matdes.2005.01.005
Amouri, K., Kazemi, S., Momeni, A., and Kazazi, M. (2016). Microstructure and mechanical properties of Al-nano/micro SiC composites produced by stir casting technique. Mater. Sci. Eng. A 674, 569–578. doi: 10.1016/j.msea.2016.08.027
Annigeri Veeresh Kumar, U. K. G. B. (2017). Method of stir casting of Aluminum metal matrix composites: a review. Mater. Today Proc. 4, 1140–1146. doi: 10.1016/j.matpr.2017.01.130
Babalola, P. O., Inegbenebor, A. O., Bolu, C. A., and John, S. I. (2019). Comparison of the mechanical characteristics of aluminium sic composites cast in sand and metal moulds. Int. J. Mech. Eng. Technol. 10, 1671–1681.
Baradeswaran, A., and Elaya Perumal, A. (2014). Study on mechanical and wear properties of Al 7075/Al2O3/graphite hybrid composites. Compos. Part B Eng. 56, 464–471. doi: 10.1016/j.compositesb.2013.08.013
Benatar, A., and Gutowski, T. G. (1989). Ultrasonic welding of PEEK graphite APC-2 composites. Polym. Eng. Sci. 29, 1705–1721. doi: 10.1002/pen.760292313
Bhandare, R. G., and Sonawane, P. M. (2013). Preparation of aluminium matrix composite by using stir casting method. Int. J. Eng. Adv. Technol. (IJEAT) 3, 61–65.
Bobić, B., Mitrović, S., Babić, M., and Bobić, I. (2009). Corrosion of aluminium and zinc-aluminium alloys based metal-matrix composites. Tribol. Ind. 31, 44–53.
Bodukuri, A. K., Eswaraiah, K., Rajendar, K., and Sampath, V. (2016). Fabrication of Al–SiC–B4C metal matrix composite by powder metallurgy technique and evaluating mechanical properties. Perspect. Sci. 8, 428–431. doi: 10.1016/j.pisc.2016.04.096
Bodunrin, M. O., Alaneme, K. K., and Chown, L. H. (2015). Aluminium matrix hybrid composites: a review of reinforcement philosophies; mechanical, corrosion and tribological characteristics. J. Mater. Res. Technol. 4, 434–445. doi: 10.1016/j.jmrt.2015.05.003
Chak, V., Chattopadhyay, H., and Dora, T. L. (2020). A review on fabrication methods, reinforcements and mechanical properties of aluminum matrix composites. J. Manuf. Process. 56, 1059–1074. doi: 10.1016/j.jmapro.2020.05.042
Chaubey, A., Dwivedi, R., Purohit, R., Rana, R. S., and Choudhary, K. (2020). Experimental inspection of aluminium matrix composites reinforced with SiC particles fabricated through ultrasonic assisted stir casting process. Mater. Today Proc. 26, 3054–3057. doi: 10.1016/j.matpr.2020.02.634
Daniels, H. P. C. (1965). Ultrasonic welding. Ultrasonics 3, 190–196. doi: 10.1016/0041-624x(65)90169-1
Daoud, A. (2004). Wear performance of 2014 Al alloy reinforced with continuous carbon fibers manufactured by gas pressure infiltration. Mater. Lett. 58, 3206–3213. doi: 10.1016/j.matlet.2004.06.012
Daoud, A. (2005). Microstructure and tensile properties of 2014 Al alloy reinforced with continuous carbon fibers manufactured by gas pressure infiltration. Mater. Sci. Eng. A 391, 114–120. doi: 10.1016/j.msea.2004.08.075
David Raja Selvam, J., Robinson Smart, D. S., and Dinaharan, I. (2013). Synthesis and characterization of Al6061-Fly Ashp-SiCp composites by stir casting and compocasting methods. Energy Procedia 34, 637–646. doi: 10.1016/j.egypro.2013.06.795
Dimitescu, A., Babiş, C., Alecusan, A. M., and Chivu, O. (2018). Prepare for brazing aluminium samples by ultrasonic cleaning. IOP Conf. Ser. Mater. Sci. Eng. 400:022021. doi: 10.1088/1757-899x/400/2/022021
Elangovan, S., Semeer, S., and Prakasan, K. (2009). Temperature and stress distribution in ultrasonic metal welding—An FEA-based study. J. Mater. Process. Technol. 209, 1143–1150. doi: 10.1016/j.jmatprotec.2008.03.032
Etter, T., Papakyriacou, M., Schulz, P., and Uggowitzer, P. J. (2003). Physical properties of graphite/aluminium composites produced by gas pressure infiltration method. Carbon 41, 1017–1024. doi: 10.1016/s0008-6223(02)00448-7
Gao, M., Kang, H., Chen, Z., Guo, E., Peng, P., and Wang, T. (2018). Effect of reinforcement content and aging treatment on microstructure and mechanical behavior of B4Cp/6061Al composites. Mater. Sci. Eng. A 744, 682–690. doi: 10.1016/j.msea.2018.12.042
Garg, P., Jamwal, A., Kumar, D., Sadasivuni, K. K., Hussain, C. M., and Gupta, P. (2019). Advance research progresses in aluminium matrix composites: manufacturing & applications. J. Mater. Res. Technol. 8, 4924–4939. doi: 10.1016/j.jmrt.2019.06.028
Gopal, K. U. B., Sreenivas, R. K. V., and Vasudeva, B. (2012). Effect of percentage reinforcement of B4C on the tensile property of aluminium matrix composites. Int J Mech Eng. Rob. Res. 1, 290–295.
Griffiths, A. J., and Turnbull, A. (1994). An investigation of the electrochemical polarisation behaviour of 6061 aluminium metal matrix composites. Corros. Sci. 36, 23–35. doi: 10.1016/0010-938x(94)90106-6
Gunduz, I., Ando, T., Shattuck, E., Wong, P., and Doumanidis, C. (2005). Enhanced diffusion and phase transformations during ultrasonic welding of zinc and aluminum. Scr. Mater. 52, 939–943. doi: 10.1016/j.scriptamat.2004.12.015
Harichandran, R., and Selvakumar, N. (2016). Effect of nano/micro B4C particles on the mechanical properties of aluminium metal matrix composites fabricated by ultrasonic cavitation-assisted solidification process. Arch. Civil Mech. Eng. 16, 147–158. doi: 10.1016/j.acme.2015.07.001
Hashim, J., Looney, L., and Hashim, M. S. J. (2001). The enchancement of wetability sic particle in cast aluminium matrix composite. J. Mater. Process. Technol. 119, 329–335.
Hassan, A. M., Alrashdan, A., Hayajneh, M. T., and Mayyas, A. T. (2009). Prediction of density, porosity and hardness in aluminum–copper-based composite materials using artificial neural network. J. Mater. Process. Technol. 209, 894–899. doi: 10.1016/j.jmatprotec.2008.02.066
Horikiri, G., Kitazumi, T., Natori, K., and Tanaka, T. (2017). Improvement in mechanical properties of semi-solid AA7075 aluminum alloys by equal-channel angular pressing. Procedia Eng. 207, 1451–1456. doi: 10.1016/j.proeng.2017.10.912
Inegbenebor, A. O., Bolu, C. A., Babalola, P. O., Inegbenebor, A. I., and Fayomi, O. S. I. (2016). Aluminum silicon carbide particulate metal matrix composite development via stir casting processing. Silicon 10, 343–347. doi: 10.1007/s12633-016-9451-7
Jeykrishnan, J., Jayanthi Nathan, S., and Karthik, M. R. (2017). Fabrication and characterization of aluminum titanium di-boride metal matrix composites using stir casting technique. Int. J. Mech. Eng. Technol. 8, 13–18.
Kala, H., Mer, K. K. S., and Kumar, S. (2014). A review on mechanical and tribological behaviors of stir cast aluminum matrix composites. Procedia Mater. Sci. 6, 1951–1960. doi: 10.1016/j.mspro.2014.07.229
Khmelev, V. N., Slivin, A. N., Abramov, A. D., Vakar, M. E., and Nesterov, V. A. (2016). “Development of ultrasonic welding technology by hand tool,” in Proceedings of the 2016 17th International Conference of Young Specialists on Micro/Nanotechnologies and Electron Devices (EDM), Novosibirsk. doi: 10.1109/edm.2016.7538741
Kim, W. H., Kang, E. J., and Park, D. S. (2017). Evaluation of welding performance of 20 kHz and 40 kHz ultrasonic metal welding. IOP Conf. Ser. Mater. Sci. Eng. 248:012013. doi: 10.1088/1757-899x/248/1/012013
Kocimski, J., Arthur, W., Kustron, P., Chertov, A. M., Maev, R. G., Korzeniowski, M., et al. (2009). “Modelling ultrasonic wave propagation in a multilayered medium for resistance spot welding,” in Proceedings of the 2009 IEEE International Ultrasonics Symposium, Rome. doi: 10.1109/ultsym.2009.5441580
Kumar Sharma, A., Bhandari, R., Aherwar, A., and Pinca-Bretotean, C. (2020). A study of fabrication methods of aluminum based composites focused on stir casting process. Mater. Today Proc. 27, 1608–1612. doi: 10.1016/j.matpr.2020.03.316
Kumar, A., Lal, S., and Kumar, S. (2013). Fabrication and characterization of A359/Al2O3 metal matrix composite using electromagnetic stir casting method. J. Mater. Res. Technol. 2, 250–254. doi: 10.1016/j.jmrt.2013.03.015
Kumar, B. P., and Birru, A. K. (2017). Microstructure and mechanical properties of aluminium metal matrix composites with addition of bamboo leaf ash by stir casting method. Trans. Nonferrous Metals Soc. China 27, 2555–2572. doi: 10.1016/s1003-6326(17)60284-x
Laha, T., Agarwal, A., McKechnie, T., and Seal, S. (2004). Synthesis and characterization of plasma spray formed carbon nanotube reinforced aluminum composite. Mater. Sci. Eng. A 381, 249–258. doi: 10.1016/j.msea.2004.04.014
Leng, X., Yang, W., Zhang, J., Ma, X., Zhao, W., and Yan, J. (2017). High-performance joining technology for aluminium matrix composites using ultrasonic-assisted brazing. Mater. Sci. Technol. 34, 660–663.
Li, C., Wang, X., Wang, L., Li, J., Li, H., and Zhang, H. (2016). Interfacial characteristic and thermal conductivity of Al/diamond composites produced by gas pressure infiltration in a nitrogen atmosphere. Mater. Design 92, 643–648. doi: 10.1016/j.matdes.2015.12.098
Lionetto, F., Balle, F., and Maffezzoli, A. (2017). Hybrid ultrasonic spot welding of aluminum to carbon fiber reinforced epoxy composites. J. Mater. Process. Technol. 247, 289–295. doi: 10.1016/j.jmatprotec.2017.05.002
Lionetto, F., Mele, C., Leo, P., D’Ostuni, S., Balle, F., and Maffezzoli, A. (2018). Ultrasonic spot welding of carbon fiber reinforced epoxy composites to aluminum: mechanical and electrochemical characterization. Compos. Part B Eng. 144, 134–142. doi: 10.1016/j.compositesb.2018.02.026
Long, Y., Bai, F., Zhang, Y., Saalbach, K.-A., and Twiefel, J. (2019). Impacts of ultrasound on oxide removal – An attempt towards acid-free cleaning. Ultrasonics Sonochem. 57, 1–11. doi: 10.1016/j.ultsonch.2019.05.003
Ma, L., Zhou, C., Wen, Q., Li, M., Zhong, H., and Ji, S. (2020). Ultrasonic-promoted Rapid transient liquid phase bonding of high volume fraction SiC particle reinforced aluminum-based metal matrix composite in low temperature. Ultrasonics 106:106159. doi: 10.1016/j.ultras.2020.106159
Madhukar, P., Selvaraj, N., Rao, C. S. P., and Veeresh Kumar, G. B. (2020). Fabrication and characterization two step stir casting with ultrasonic assisted novel AA7150-hBN nanocomposites. J. Alloys Compd. 815:152464. doi: 10.1016/j.jallcom.2019.152464
Mahesh, V. P., Nair, P. S., Rajan, T. P. D., Pai, B. C., and Hubli, R. C. (2011). Processing of surface-treated boron carbide-reinforced aluminum matrix composites by liquid–metal stir-casting technique. J. Compos. Mater. 45, 2371–2378. doi: 10.1177/0021998311401086
Maria, V. (2014). Ultrasonic Welding of Aluminum: A Practical Study in Consistency, Part Marking and Control Modes (2007). Retrospective Theses and Dissertations. 15932. Available online at: https://lib.dr.iastate.edu/rtd/15932 (accessed September 27, 2020).
Matsuoka, S., and Imai, H. (2009). Direct welding of different metals used ultrasonic vibration. J. Mater. Process. Technol. 209, 954–960. doi: 10.1016/j.jmatprotec.2008.03.006
Maurya, R., Kumar, B., Ariharan, S., Ramkumar, J., and Balani, K. (2016). Effect of carbonaceous reinforcements on the mechanical and tribological properties of friction stir processed Al6061 alloy. Mater. Design 98, 155–166. doi: 10.1016/j.matdes.2016.03.021
Mavhungu, S. T., Akinlabi, E. T., Onitiri, M. A., and Varachia, F. M. (2017). Aluminum matrix composites for industrial use: advances and trends. Procedia Manuf. 7, 178–182. doi: 10.1016/j.promfg.2016.12.045
Mehrabian, M., Nayebi, B., Dietrich, D., Lampke, T., and Shokouhimehr, M. (2018). Characteristics of dynamically-formed surface oxide layers on molten zinc–aluminum alloys: a multimodality approach. Thin Solid Films 667, 34–39. doi: 10.1016/j.tsf.2018.10.008
Mordyuk, B. N., Prokopenko, G. I., Milman, Y. V., Iefimov, M. O., Grinkevych, K. E., Sameljuk, A. V., et al. (2014). Wear assessment of composite surface layers in Al–6Mg alloy reinforced with AlCuFe quasicrystalline particles: effects of particle size, microstructure and hardness. Wear 319, 84–95. doi: 10.1016/j.wear.2014.07.011
Muñoz-Morris, M. A., Gutierrez-Urrutia, I., and Morris, D. G. (2005). Effect of equal channel angular pressing on strength and ductility of Al–TiAl composites. Mater. Sci. Eng. A 396, 3–10. doi: 10.1016/j.msea.2004.11.046
Nayebi, B., Mehrabian, M., Shahedi Asl, M., and Shokouhimehr, M. (2018). Nanostructural approach to the thickening behavior and oxidation of calcium-stabilized aluminum foams. Mater. Chem. Phys. 220, 351–359. doi: 10.1016/j.matchemphys.2018.09.017
Neppiras, E. A. (1965). Ultrasonic welding of metals. Ultrasonics 3, 128–135. doi: 10.1016/s0041-624x(65)80003-8
Pal, T. K. (2005). Joining of aluminium metal matrix composites. Mater. Manuf. Process. 20, 717–726. doi: 10.1081/AMP-200055116
Panteli, A., Robson, J. D., Brough, I., and Prangnell, P. B. (2012). The effect of high strain rate deformation on intermetallic reaction during ultrasonic welding aluminium to magnesium. Mater. Sci. Eng. A 556, 31–42. doi: 10.1016/j.msea.2012.06.055
Park, B., Lee, D., Jo, I., Lee, S. B., Lee, S. K., and Cho, S. (2019). Automated quantification of reinforcement dispersion in B4C/Al metal matrix composites. Compos. Part B Eng. 181:107584. doi: 10.1016/j.compositesb.2019.107584
Patel, V. K., Bhole, S. D., Chen, D. L., Ni, D. R., Xiao, B. L., and Ma, Z. Y. (2015). Solid-state ultrasonic spot welding of SiCp/2009Al composite sheets. Mater. Design (1980-2015) 65, 489–495. doi: 10.1016/j.matdes.2014.09.049
Poli, C. (2001). Design for Manufacturing: A Structured Approach. Boston, MA: Butterworth-Heinemann.
Prakash, S., Sasikumar, R., and Natarajan, E. (2018). Superior material properties of hybrid filler-reinforced aluminum MMC through double-layer feeding technique adopted in bottom tapping stir casting. High Temp. Mater. Process. Int. Q. High Technol. Plasma Process. 22, 249–258.
Rabiei, A., Vendra, L., and Kishi, T. (2008). Fracture behavior of particle reinforced metal matrix composites. Compos. Part A Appl. Sci. Manuf. 39, 294–300. doi: 10.1016/j.compositesa.2007.10.018
Rahman, M. H., and Rashed, H. M. M. A. (2014). Characterization of silicon carbide reinforced aluminum matrix composites. Procedia Eng. 90, 103–109. doi: 10.1016/j.proeng.2014.11.821
Raja, K. S. S., and Raja, V. K. B. (2014). “Effect of boron carbide particle in wear characteristic of cast aluminium A356 composite,” in Proceeding of the National Conference on Contemporary Approaches in Mechanical Automobile and Building Sciences-2014, IOSR Journal of Mechanical and Civil Engineering, Chennai. 73–77.
Raju, P. R. M., Rajesh, S., Raju, K. S. R., and Raju, V. R. (2015). Effect of Reinforcement of Nano Al2O3 on Mechanical Properties of Al2024 NMMCs. Mater. Today Proc. 2, 3712–3717. doi: 10.1016/j.matpr.2015.07.152
Ramanathan, A., Krishnan, P. K., and Muraliraja, R. (2019). A review on the production of metal matrix composites through stir casting – Furnace design, properties, challenges, and research opportunities. J. Manuf. Process. 42, 213–245. doi: 10.1016/j.jmapro.2019.04.017
Ramnath, B. V., Elanchezhian, C., Annamalai, R. M., Aravind, S., Sri Ananda Atreya, T., Vignesh, V., et al. (2014). Aluminium metal matrix composites–a review. Rev. Adv. Mater. Sci. 38, 55–60.
Ramu, G., and Bauri, R. (2009). Effect of equal channel angular pressing (ECAP) on microstructure and properties of Al–SiCp composites. Mater. Design 30, 3554–3559. doi: 10.1016/j.matdes.2009.03.001
Rana, H., and Badheka, V. (2018). Influence of friction stir processing conditions on the manufacturing of Al-Mg-Zn-Cu alloy/boron carbide surface composite. J. Mater. Process. Technol. 255, 795–807. doi: 10.1016/j.jmatprotec.2018.01.020
Rao, S. R., and Padmanabhan, G. (2012). Fabrication and mechanical properties of aluminium-boron carbide composites. Int. J. Mater. Biomater. Appl. 2, 15–18.
Raviteja, T., Radhika, N., and Raghu, R. (2014). Fabrication and mechanical properties of stir cast Al-Si12Cu/B4C composites. Int. J. Res. Eng. Technol. 3, 343–346.
Reddy, G. M., Srinivasa Rao, K., and Mohandas, T. (2009). Friction surfacing: novel technique for metal matrix composite coating on aluminium–silicon alloy. Surface Eng. 25, 25–30.
Ruch, P. W., Beffort, O., Kleiner, S., Weber, L., and Uggowitzer, P. J. (2006). Selective interfacial bonding in Al(Si)–diamond composites and its effect on thermal conductivity. Compos. Sci. Technol. 66, 2677–2685. doi: 10.1016/j.compscitech.2006.03.016
Salih, O. S., Ou, H., Sun, W., and McCartney, D. G. (2015). A review of friction stir welding of aluminium matrix composites. Mater. Design 86, 61–71. doi: 10.1016/j.matdes.2015.07.071
Saravanan, M., Pillai, R., Ravi, K., Pai, B., and Brahmakumar, M. (2007). Development of ultrafine grain aluminium–graphite metal matrix composite by equal channel angular pressing. Compos. Sci. Technol. 67, 1275–1279. doi: 10.1016/j.compscitech.2006.10.003
Sarkari Khorrami, M., Samadi, S., Janghorban, Z., and Movahedi, M. (2015). In-situ aluminum matrix composite produced by friction stir processing using FE particles. Mater. Sci. Eng. A 641, 380–390. doi: 10.1016/j.msea.2015.06.071
Sarraf, Z. S. A., and Akrawi, J. A. (2016). “Design, simulation and fabrication of ultrasonic welding device used to improve welding parameters,” in Proceedings of the 2016 7th International Conference on Mechanical and Aerospace Engineering (ICMAE), London. doi: 10.1109/icmae.2016.7549544
Segal, V. M. (1995). Materials processing by simple shear. Mater. Sci. Eng. A 197, 157–164. doi: 10.1016/0921-5093(95)09705-8
Sharma, P., Dabra, V., Sharma, S., Khanduja, D., Sharma, N., Sharma, R., et al. (2019). Microstructure and properties of AA6082/(SiC + Graphite) hybrid composites. Refractories Ind. Ceram. 59, 471–477. doi: 10.1007/s11148-019-00256-7
Shinde, D. M., Sahoo, P., and Paulo Davim, J. (2020). Tribological characterization of particulate-reinforced aluminum metal matrix nanocomposites: a review. Adv. Comp. Lett. 29:2633366X20921403.
Siddiq, A., and Ghassemieh, E. (2008). “Modelling and characterization of ultrasonic consolidation process of aluminium alloys,” in Proceedings of the 2008 MRS Spring Meeting, San Francisco, CA, 125–132.
Siddiq, A., and Ghassemieh, E. (2009). Theoretical and FE analysis of ultrasonic welding of aluminum alloy 3003. J. Manuf. Sci. Eng. 131:041007. doi: 10.1115/1.3160583
Siddiq, A., and Ghassemieh, E. (2010). Fibre embedding in aluminium alloy 3003 using ultrasonic consolidation process—thermo-mechanical analyses. Int. J. Adv. Manuf. Technol. 54, 997–1009. doi: 10.1007/s00170-010-3007-6
Sijo, M. T., and Jayadevan, K. R. (2016). Analysis of stir cast aluminium silicon carbide metal matrix composite: a comprehensive review. Procedia Technol. 24, 379–385. doi: 10.1016/j.protcy.2016.05.052
Singh, V. P., Patel, S. K., Ranjan, A., and Kuriachen, B. (2020). Recent research progress in solid state friction-stir welding of aluminium–magnesium alloys: a critical review. J. Mater. Res. Technol. 9, 6217–6256. doi: 10.1016/j.jmrt.2020.01.008
Srinivasan, K., and Senthil Kumaran, S. (2020). Quality assessment of friction welding using image super-resolution via deep convolutional neural networks. Mater. Today Proc. 22(Pt 4), 2266–2273. doi: 10.1016/j.matpr.2020.03.347
Srinivasan, K., Deepa, N., Vincent, D. R., and Senthil Kumaran, S. (2020). Realizing the resolution enhancement of tube-to-tube plate friction welding microstructure images via hybrid sparsity model for improved weld interface defects diagnosis. J. Intern. Technol. 21, 61–72.
Srivatsan, T. S., Ibrahim, I. A., Mohamed, F. A., and Lavernia, E. J. (1991). Processing techniques for particulate-reinforced metal aluminium matrix composites. J. Mater. Sci. 26, 5965–5978. doi: 10.1007/bf01113872
Srivyas, P. D., and Charoo, M. S. (2018). Role of reinforcements on the mechanical and tribological behavior of aluminum metal matrix composites – a review. Mater. Today Proc. 5, 20041–20053. doi: 10.1016/j.matpr.2018.06.371
Sudha, K., Subramani, N., Vijayaraghavan, K., and Arunsankar, V. V. (2013). Analysis and investigation on A2024 metal matrix composites with B4C and graphite. Int. J. Innov. Res. Sci. Eng. Technol. 2, 4636–4642.
Sukumaran, K., Ravikumar, K. K., Pillai, S. G. K., Rajan, T. P. D., Ravi, M., Pillai, R. M., et al. (2008). Studies on squeeze casting of Al 2124 alloy and 2124-10% SiCp metal matrix composite. Mater. Sci. Eng. A 490, 235–241. doi: 10.1016/j.msea.2008.01.054
Surappa, M. K. (2003). Aluminium matrix composites: challenges and opportunities. Sadhana 28, 319–334. doi: 10.1007/bf02717141
Suresh, K. S., Rani, M. R., Prakasan, K., and Rudramoorthy, R. (2007). Modeling of temperature distribution in ultrasonic welding of thermoplastics for various joint designs. J. Mater. Process. Technol. 186, 138–146. doi: 10.1016/j.jmatprotec.2006.12.028
Suresh, S., Mortensen, A., and Needleman, A. (1993). Fundamentals of Metal Matrix Composites, Butterworth-. Boston, MA: Heinemann.
Taherzadeh Mousavian, R., Azari Khosroshahi, R., Yazdani, S., Brabazon, D., and Boostani, A. F. (2016). Fabrication of aluminum matrix composites reinforced with nano- to micrometer-sized SiC particles. Mater. Design 89, 58–70. doi: 10.1016/j.matdes.2015.09.130
Tee, K. L., Lu, L., and Lai, M. O. (1999). In situ processing of Al–TiB2 composite by the stir-casting technique. J. Mater. Process. Technol. 8, 513–519. doi: 10.1016/s0924-0136(99)00038-2
Tony Thomas, A., Parameshwaran, R., Muthukrishanan, A., and Kumaran, M. (2014). Development of feeding and stirring mechanism for stir casting of aluminium matrix composites. Procedia Mater. Sci. 5, 1182–1191.
Truckenmüller, R., Cheng, Y., Ahrens, R., Bahrs, H., Fischer, G., and Lehmann, J. (2006). Micro ultrasonic welding: joining of chemically inert polymer microparts for single material fluidic components and systems. Microsyst. Technol. 12, 1027–1029. doi: 10.1007/s00542-006-0136-9
Tsujino, J., and Sugimoto, E. (2014). “Ultrasonic welding of electronic parts and devices using a long and thin complex vibration welding tip,” in Proceedings of the 2014 IEEE International Ultrasonics Symposium, Chicago, IL. doi: 10.1109/ultsym.2014.0232
Tsujino, J., Hidai, K., Hasegawa, A., Kanai, R., Matsuura, H., Matsushima, K., et al. (2002). Ultrasonic butt welding of aluminum, aluminum alloy and stainless steel plate specimens. Ultrasonics 40, 371–374. doi: 10.1016/s0041-624x(02)00124-5
Tsujino, J., Ueoka, T., Hasegawa, K., Fujita, Y., Shiraki, T., Okada, T., et al. (1996). New methods of ultrasonic welding of metal and plastic materials. Ultrasonics 34, 177–185. doi: 10.1016/0041-624x(96)81780-x
Ultrasonic Welding (2009). Handbook of Plastics Joining. Boston, MA: Elsevier, 15–35. doi: 10.1016/b978-0-8155-1581-4.50004-4
Vanam, J. P., Chiranjeevi, R., Kumar, R. S., Ramana, V. V., and Kumar, A. S. (2018). Effect of SiC on mechanical, microstructure and tribological properties of aluminum MMC processed by stir casting. IOP Conf. Ser. Mater. Sci. Eng. 455:012017. doi: 10.1088/1757-899x/455/1/012017
Venkatesh, R., Sethi, D., Kolli, V., and Saha Roy, B. (2019). Experimental investigation of aluminium matrix composite production and joining. Mater. Today Proc. 18, 5276–5285. doi: 10.1016/j.matpr.2019.07.551
Wagner, G., Balle, F., and Eifler, D. (2013). Ultrasonic welding of aluminum alloys to fiber reinforced polymers. Adv. Eng. Mater. 15, 792–803. doi: 10.1002/adem.201300043
Wang, Q., Zhu, L., Chen, X., Yan, J., Xie, R., Li, P., et al. (2016). Si particulate-reinforced ZnAl based composites joints of hypereutectic Al50Si alloys by ultrasonic-assisted soldering. Mater. Design 107, 41–46. doi: 10.1016/j.matdes.2016.05.121
Wu, S., Wang, H., and Tjong, S. (1996). Mechanical and wear behavior of an Al/Si alloy metal-matrix composite reinforced with aluminosilicate fiber. Compos. Sci. Technol. 56, 1261–1270. doi: 10.1016/s0266-3538(96)00085-1
Xu, Z., Yan, J., Wu, G., Kong, X., and Yang, S. (2005). Interface structure of ultrasonic vibration aided interaction between Zn–Al alloy and Al2O3p/6061Al composite. Compos. Sci. Technol. 65, 1959–1963. doi: 10.1016/j.compscitech.2005.02.004
Xue, C., Yu, J. K., and Zhu, X. M. (2011). Thermal properties of diamond/SiC/Al composites with high volume fractions. Mater. Design 32, 4225–4229. doi: 10.1016/j.matdes.2011.04.032
Yan, J., Xu, Z., Shi, L., Ma, X., and Yang, S. (2011). Ultrasonic assisted fabrication of particle reinforced bonds joining aluminum metal matrix composites. Mater. Design 32, 343–347. doi: 10.1016/j.matdes.2010.06.036
Yang, Y. (2008). Fabrication of Long-Fiber-Reinforced Metal Matrix Composites Using Ultrasonic Consolidation. Ph. D. thesis. Logan, UT: Utah State University.
Yang, Y., and Li, X. (2007). Ultrasonic cavitation based nanomanufacturing of bulk aluminum matrix nanocomposites. J. Manuf. Sci. Eng. 129, 497–501.
Yang, Y., Janaki Ram, G. D., and Stucker, B. E. (2006). Process Parameters Optimization for Ultrasonically Consolidated Fiber-Reinforced Metal Matrix Composites Department of Mechanical and Aerospace Engineering 84322-4130. Logan, UT: Utah State University
Yang, Y., Lan, J., and Li, X. (2004). Study on bulk aluminum matrix nanocomposite fabricated by ultrasonic dispersion of nano-sized SiC particles in molten aluminum alloy. Mater. Sci. Eng. A 380, 378–383. doi: 10.1016/j.msea.2004.03.073
Yashpal, S., Jawalkar, C. S., Verma, A. S., and Suri, N. M. (2017). Fabrication of aluminium metal matrix composites with particulate reinforcement: a review. Mater. Today Proc. 4, 2927–2936. doi: 10.1016/j.matpr.2017.02.174
Yin, Z., Tao, S., Zhou, X., and Ding, C. (2008). Microstructure and mechanical properties of Al2O3–Al composite coatings deposited by plasma spraying. Appl. Surface Sci. 254, 1636–1643. doi: 10.1016/j.apsusc.2007.07.135
Yuvaraj, N., Aravindan, S., and Vipin. (2015). Fabrication of Al5083/B4C surface composite by friction stir processing and its tribological characterization. J. Mater. Res. Technol. 4, 398–410. doi: 10.1016/j.jmrt.2015.02.006
Zhang, Y., Li, J., Zhao, L., and Wang, X. (2014). Optimisation of high thermal conductivity Al/diamond composites produced by gas pressure infiltration by controlling infiltration temperature and pressure. J. Mater. Sci. 50, 688–696. doi: 10.1007/s10853-014-8628-y
Keywords: aluminum metal matrix composites, particulate reinforcement, ultrasonic welding, ultrasonic vibrations, welding engineering
Citation: Selvaraj SK, Srinivasan K, Chadha U, Mishra R, Arpit K, Apurb K and Hu Y-C (2021) Contemporary Progresses in Ultrasonic Welding of Aluminum Metal Matrix Composites. Front. Mater. 8:647112. doi: 10.3389/fmats.2021.647112
Received: 29 December 2020; Accepted: 06 April 2021;
Published: 30 April 2021.
Edited by:
Mazeyar Parvinzadeh Gashti, PRE Labs Inc., CanadaReviewed by:
Mohammadreza Shokouhimehr, Seoul National University, South KoreaHamid Reza Baharvandi, University of Tehran, Iran
Guntram Wagner, Technische Universität Chemnitz, Germany
Copyright © 2021 Selvaraj, Srinivasan, Chadha, Mishra, Arpit, Apurb and Hu. This is an open-access article distributed under the terms of the Creative Commons Attribution License (CC BY). The use, distribution or reproduction in other forums is permitted, provided the original author(s) and the copyright owner(s) are credited and that the original publication in this journal is cited, in accordance with accepted academic practice. No use, distribution or reproduction is permitted which does not comply with these terms.
*Correspondence: Yuh-Chung Hu, eWNodUBuaXUuZWR1LnR3