- 1School of New Energy and Materials, Southwest Petroleum University, Chengdu, China
- 2Center for Additive Manufacturing, Faculty of Engineering, University of Nottingham, Nottingham, United Kingdom
With the development of wearable electronic devices, conductive polymer composites (CPCs) based flexible strain sensors are gaining tremendous popularity. In recent years, the applications of additive manufacturing (AM) technology (also known as 3D printing) in fabricating CPCs based flexible strain sensors have attracted the attention of researchers due to their advantages of mold-free structure, low cost, short time, and high accuracy. AM technology, based on material extrusion, photocuring, and laser sintering, produces complex and high-precision CPCs based wearable sensors through layer-by-layer stacking of printing material. Some high-performance CPCs based strain sensors are developed by employing different 3D printing technologies and printing materials. In this mini-review, we summarize and discuss the performance and applications of 3D printed CPCs based strain sensors in recent years. Finally, the current challenges and prospects of 3D printed strain sensors are also discussed to provide an insight into the future of strain sensors using 3D printing technology.
Introduction
In recent years, CPCs have been widely used in industrial and academic fields because of their flexibility, controllable conductive properties, easy processing, and low-cost synthesis (Wu et al., 2016; Wang T. et al., 2018; Li et al., 2018). Nanofillers are introduced to the insulating polymer matrix to improve their functional characteristics (Wang et al., 2018b). Due to the superior properties of functionalized CPCs, they are used to make strain sensors which are playing their role in medical diagnosis, soft robotics, health monitoring, human-computer interaction, and many other applications (Wang et al., 2018c; Wang et al., 2019; Zhang et al., 2019). Several methods for fabricating the strain sensors have been developed, such as hot pressing, casting, and extrusion. However, the processing technologies of these methods are complicated and not applicable to complex structures. For example, customized molds are needed to fabricate CPCs based strain sensors by hot pressing method (Huang et al., 2021). The development and production of mold limit the economic benefits during their industrial-scale production.
Since the last decade, AM technology, also known as 3D printing Zhang J. et al. (2020), is used by researchers for the fabrication of CPCs based strain sensors (Zhang et al., 2016; Gnanasekaran et al., 2017; Dawoud et al., 2018). Traditional fabrication methods used for preparing the molds of complex 3D objects are highly inefficient and time consuming. Compared with the conventional fabrication methods, 3D printing technology has the advantages of high resolution, high accuracy, low cost, fast fabrication, and customized for mass production without the need for mold (Abshirini et al., 2019; Dul et al., 2020; Song et al., 2020). Furthermore, due to the micro-orientation in Fused Filament Fabrication (FFF) and Direct Ink Writing (DIW) 3D Printing, the nanofillers are uniformly dispersed in the polymer matrix, leading to the enhanced performance of obtained strain sensor (Guo et al., 2021). Therefore, 3D printing through layer-by-layer manufacturing has shown promising potential to produce flexible strain sensors with complex structures. Their application areas include wearable electronic devices, medical diagnostics, soft robots, and strain direction recognition (Wang et al., 2020; Dan et al., 2021; Gao et al., 2021). Although 3D printing has been widely used in the development of complex structures, it is still a novel method to fabricate strain sensors with complex structures and multiple functions.
At present, there are some reports on the fabrication of CPCs based strain sensors with high performance by 3D printing. Considering the wide application potential of 3D printing in CPCs based strain sensors, it is necessary to review this topic. In this mini-review, 3D printing technologies based on material extrusion, photocuring, and laser sintering, involving Fused Filament Fabrication (FFF), Direct Ink Writing (DIW), Digital Light Processing (DLP), and Selective Laser Sintering (SLS) are discussed. Moreover, high-performance CPCs based strain sensors fabricated by these 3D printing technologies are reviewed. Further, the printing principle, material selection, research progress, recent applications, and prospects of CPCs based 3D printed strain sensors are also discussed.
Fabrication of CPCs Based Flexible Strain Sensors by 3D Printing
3D printed CPCs based flexible strain sensors involve four different fabrication approaches including FFF, DIW, DLP, and SLS. The summary of materials, printing principles, advantages, and disadvantages of these technologies is enlisted in Table 1; Table 2 summarizes the representative researches of strain sensors fabricated by 3D printing in recent years.
Electrical properties of elastic polymer material improve with the introduction of conductive nanofillers. Furthermore, due to the increase of the interface density of nanofillers Arif et al. (2020) and the interaction between nanofillers and polymer matrix (Xiang et al., 2019), the interface between them is well combined, which facilitates a effective stress transfer under strain. Therefore, the mechanical properties of the composites, including strength, Young’s modulus and toughness, are enhanced. (Pan et al., 2020). In addition, the sensing properties such as strain detection range, sensitivity, linearity, response time, resistance responsiveness, stability, and durability under different conditions are equally significant for CPCs based strain sensors. Material type, agglomeration and dispersion of nanofillers, macroscopic and microscopic structure of strain sensors, and different 3D printing parameters (Davoodi et al., 2020; Xu et al., 2020) determine the percolated network structure of the strain sensor, affecting the sensing properties of strain sensor. For example, when the percolation networks are in high density, numerous nanofillers contact with each other. The contact resistance is dominant and a robust percolation network is built. With the decrease of percolation networks density, more nanofillers are separated from each other, and contact resistance is gradually transformed into tunneling resistance. It makes the contact nodes between nanofillers easier to be disconnected, resulting in a higher sensitivity of composite. When the percolation networks are at low density, most of nanofillers could be in the state of tunneling effect. Here the tunneling resistance is dominant, leading to a fragile percolation network, which makes the sensitivity of composite increase sharply (Hu et al., 2012).
Flexible Strain Sensors Fabricated by FFF
Figure 1A illustrates the process for preparing strain sensor using FFF (Christ et al., 2017). The matrix material usually determines the stretchability of the fabricated strain sensor (Waheed et al., 2019; Alam et al., 2020; Arif et al., 2020), and TPU is undoubtedly a promising candidate for fabricating FFF based strain sensors because of its high strength, good elasticity and environmental resistance (Georgopoulou et al., 2020a). However, the lower dispersion of conductive nanofillers in these strain sensors leads to poor sensing performance.
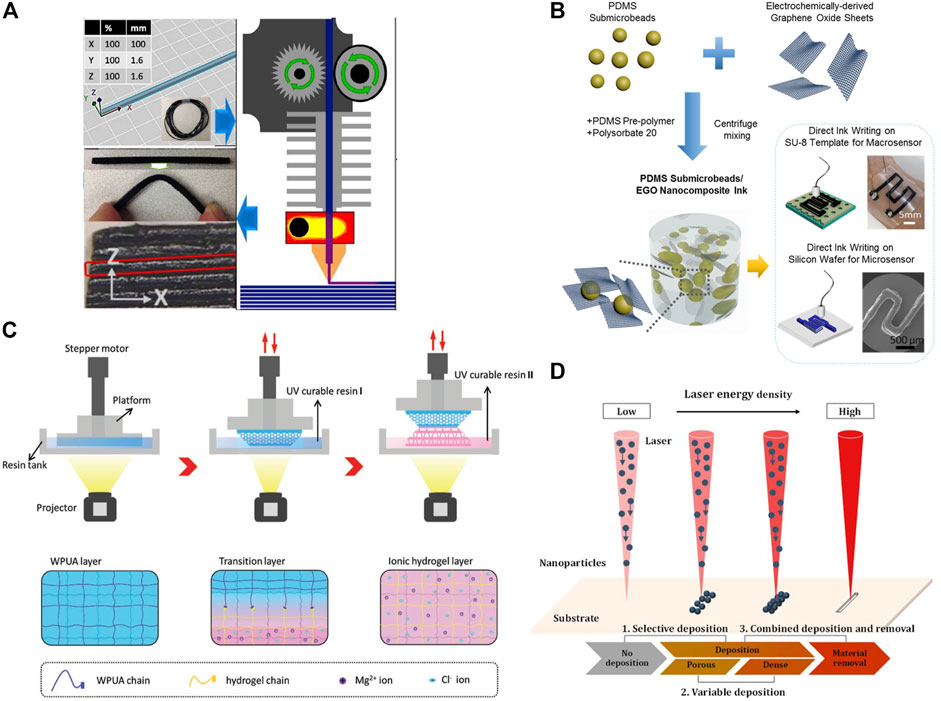
FIGURE 1. The process for preparing strain sensor using (A) FFF (Christ et al., 2017), (B) DIW (Shi et al., 2019), (C) DLP (Yin et al., 2019), and (D) SLS (Song et al., 2020).
The performance of 3D printed strain sensors could be enhanced through a synergistic effect between the nanofillers and increasing interaction between nanofillers and matrix to improve the dispersion of nanofiller in matrix (Georgopoulou and Clemens, 2020b). Xiang et al. (2020b) used FFF to prepare AGNP/CNT/TPU strain sensors with a synergistic effect, where AGNPs interact with CNTs. Micro-orientation (Guo et al., 2021) due to CNTs rearrangement during printing and synergistic effect between AGNPs and CNTs results in a wide strain detection range (0–250%), high sensitivity (GF = 43,260 at 250% strain), linearity (R2 = 0.97 within 50% strain) and fast response (∼57 ms). Synergies between other nanofillers, such as CNTs and GNPs have also been reported to achieve high performance (Xiang et al., 2020a). 1-pyrene carboxylic acid (PCA) was used to modify the TPU/CNT composite, and the dispersion of CNTs in composites was improved by applying the non-covalent interactions between PCA, TPU, and CNTs (Xiang et al., 2019). A 3D-printed piezoresistive strain sensor with a complex structure was also fabricated by non-covalent modification (Xiang et al., 2020c).
Compared with the conventional methods, FFF has the advantages of rapid synthesis (Christ et al., 2017), improved material utilization (Gnanasekaran et al., 2017), simple post-processing, no harmful by-products to the environment (Xiang et al., 2020b), and custom-made mass production without the need of molds (Dul et al., 2020). However, FFF also has some disadvantages: before printing, the prepared composite needs to undergo preprocessing, including granulation of composite and filament extrusion (Xiang et al., 2019). In addition, the printed components have a rough surface and limited physical interaction between adjacent filaments that reduce the structural strength along the deposition direction (Waheed et al., 2019).
Flexible Strain Sensors Fabricated by DIW
Ink extrusion is an effective method to print high-performance strain sensors. Inks have unique rheological properties, including viscoelasticity, shear-thinning, and yield stress, which contribute to the implementation of the DIW process. Usually, DIW is used to print the core components of the sensor or the template to prepare the sensor Wang Z. et al. (2018) and to meet the versatility of test environments. The stretchability of CPCs based strain sensors varies dramatically with the types of polymer materials (Sun et al., 2019; Wei P. et al., 2019). Particularly, PDMS elastomers are widely used in DIW printed flexible strain sensors because of their high stretchability, physiological inertia, controllable viscosity, and room temperature curing ability (Abshirini et al., 2019). Figure 1B illustrates the process of preparing the EGO/PDMS strain sensor by DIW (Shi et al., 2019). However, strain sensors fabricated by DIW using PDMS elastomers have lower sensitivity.
The sensitivity of the strain sensors is improved in two ways. The first is to optimize different printing parameters such as printing times (Song et al., 2017), which affects the degree of conductive network constructed in strain sensors, thus affecting the sensitivity. The other is the construction of a different microstructure. The conductive network of strain sensors, with different microstructures, changes under strain and controls the sensitivity of sensors. For example, a self-compensating two-order strain sensor was fabricated by Ma et al. (2019) through DIW and coating that revealed high GF (from 18.5 to 88 443) in a strain range of 0–350%. These results demonstrated that graphene coated on the surface of the sensor provides an additional conductive path, which self-compensates the loss of conductivity under high strain. Moreover, due to the slip-off and disconnection (Zhang X. et al., 2020) of internal graphene sheets, reduced graphene layers improve the sensitivity under small strain.
In addition, the performance of the flexible strain sensor improves by introducing non-conductive fillers to the CPCs. The immiscible second phase fluid was introduced to Ag/PDMS and Ag/TPU inks to fabricate the strain sensor by DIW (Sun et al., 2019). Due to the capillary action and the connection between the Ag sheets and the immiscible second phase fluid, the strain sensor achieves ultra-stretchability (>1,600%). Moreover, the shear flow generated in DIW rearranges and redistributes the conductive nanofillers (Huang et al., 2018), which results in the better orientation and uniform dispersion of the conductive nanofillers in strain sensors.
Unlike FFF technology, which applies only to thermoplastics, DIW is not limited to specific materials and is suitable for a variety of materials such as metal-based materials (Kim et al., 2019), carbon-based materials (Abshirini et al., 2018), and conductive polymer composites (Shi et al., 2019). However, DIW printing technology also has certain limitations; for different inks with different components, the print pattern requires post-processing such as soaking, sintering, heating, and curing (Khosravani and Reinicke, 2020). In addition, the processing resolution of the DIW printed strain sensors is less than that of FFF.
Flexible Strain Sensors Fabricated by DLP
Photocurable 3D printing is an emerging 3D printing method for wearable electronic devices. In this technique, ultraviolet light illuminates the mixture of photoinitiators, monomers, and prepolymers, initiating layer-by-layer curing according to the software-designed structure.
Photosensitive resins typically include acrylics, polyesters, and polyurethane acrylate containing composite precursors. Amon these, acrylic-based composites demonstrate fragile mechanical strength (Liu et al., 2021). To solve this problem, researchers used reactive diluents of acrylic-based composites to improve the mechanical strength as well as the transparency of composites (Peng et al., 2020a). Some studies report significant improvement in the mechanical stability of DLP-based strain sensors through the interlayer chemical bond formation between two materials, and the preparation process is shown in Figure 1C (Yin et al., 2019). The sensor exhibits excellent structural stability and sensing performance (10,000 loading/unloading cycles) due to the chemical bonds between hydrogel and WPUA. On one hand, the mechanical properties of photosensitive resins could improve by adding nanofillers (Mu et al., 2017; Cortes et al., 2020). On the other hand, the addition of nanofillers may absorb ultraviolet light, leading to the decline of the mechanical properties of the photosensitive resin.
In many studies, the strain detection range of DLP-based strain sensors is low (less than 30%) Cortes et al. (2020) and difficult to meet the practical application requirements. To solve this problem, Xiao et al. (2020) fabricated a flexible strain sensor based on CNTs/epoxy aliphatic acrylate (EAA)/aliphatic urethane diacrylate (AUD) composites and achieved a maximum strain detection range of 60%. Guo et al. (2020) introduced carboxyl CNTs to ACMO resin, which fully mitigated the over-curing of ACMO resin, thus, achieved a 100% strain detection range. Peng et al. (2020b) prepared a strain sensor with high stretchability (∼510%) by DLP printing sacrificial mold method.
These strain sensors have low sensitivity that does not respond to subtle strains. Peng et al. (2018) used DLP to customize the microstructure (pyramid, semisphere, and semicylinder) template and to prepare the strain sensor with high sensitivity (maximum GF of −3.6 kPa−1). At present, the research on strain sensors with a high strain detection range and high sensitivity is still scarce, and most of the designed sensors only achieve sensitivity or detection range. For DLP-based strain sensors, more research needs be done in the future to achieve high performance.
Compared with FFF and DIW based 3D printing, DLP overcomes the pre-processing and post-printing processing and has higher efficiency. Besides, the sample printed by DLP has a high resolution, indicating its higher precision (Liu et al., 2021). However, DLP is limited to the printed materials, only applicable to photosensitive resins, and has a high printing cost, thus limiting the development of DLP technology. In addition, to decrease the resin viscosity and the ultraviolet absorption of nanofillers is challenging for the fabrication of photosensitive composite resins.
Flexible Strain Sensors Fabricated by SLS
Many flexible SLS-based strain sensors have been studied in recent years (Maier et al., 2013). The performance of the strain sensor can be improved by optimizing the printing parameters of SLS and constructing a special conductive network structure. The printing parameters are adjusted to make the conductive network structure in strain sensor more completed, as shown as Figure 1D; (Song et al., 2020). Zhuang et al. (2020) prepared CNT/TPU sensors with a wide range (17–240 kPa) and high sensitivity (0.12–0.549 kPa−1) through SLS and improved the pressure detection range (3–240 kPa) and sensitivity (1.357 kPa−1 for 3–70 kPa, 0.0328 kPa−1 for 70–240 kPa) by adjusting the SLS laser power, layer thickness, and scan spacing. (Zhuang et al., 2021). A segregated structure was constructed by SLS to make the nanofillers selectively distributed on the matrix surface. (Wei S. et al., 2019; Ronca et al., 2019). The segregated structure enables the sensor to achieve a low percolation threshold (0.05 wt%) (Gan et al., 2019). In addition, the synergistic effect improves the sensing performance of SLS-based strain sensors (Rollo et al., 2020).
Comparing the 3D printing methods discussed above, SLS has the highest production efficiency, and the material utilization rate is about 100%. However, powder pollution in the printing process, high operating costs, high equipment cost, and rough product surface are few problems associated with SLS. In addition, the printed product is deformed due to the long storage time and internal stress.
Application
3D printed high-performance strain sensors are applied in many fields such as medical diagnosis and health monitoring (Khosravani and Reinicke, 2020; Liu et al., 2021). For monitoring human movements, 3D printed strain sensors have a wide range of applications (Le et al., 2017), such as finger bending, wrist bending, elbow bending, walking, and running (Christ et al., 2018). In health care systems, 3D printed strain sensors monitor patients’ respiratory and pulse rates, speech recognition, gestures, and blinking (Kim et al., 2017). Another potential application of 3D printed sensors is load recognition, including load distribution of heavy objects and light objects (Zhang et al., 2019). Besides, the high sensitivity strain sensors are also used to detect subtle acoustic vibration signals (Song et al., 2017). When the sensors are stimulated by external forces or sound waves, vibrations increase the sensing resistance patterns, and convert mechanical energy into electrical signals. In addition, DLP-based 3D printing combined with the self-pinning carbon nanotubes and assisted by out-of-plane capillary forces, the prepared strain sensor detects out-of-plane forces (Liu et al., 2018). In general, the 3D printed strain sensors have a wide range of applications in production, life, and scientific research (Bekas et al., 2019).
Discussion
Among different methods for preparing the CPCs based strain sensors, extrusion, photocurable, and laser sintering 3D printing are rapid, precise, customized, and economical, compared to traditional methods. But these methods have certain drawbacks. FFF printing requires pretreatment of the composite material and filament manufacturing. During the FFF printing nozzle blockage and roughness of the surfaces of the finished product are other challenges. Due to the different compositions of the printing ink in the DIW process, the nozzle gets blocked. Moreover, the resolution of DIW is relatively low. DLP has a high manufacturing cost and is limited to photosensitive resins only. In addition, powder pollution in the printing process, high operating costs, high equipment cost, and rough product surface are few problems associated with SLS. Given the above shortcomings, combined with the challenges associated with industrial production, it is necessary to explore new 3D printing methods with high precision, high efficiency, and high applicability.
The development of wearable electronics is rapid, resulting in more electronic product waste and non-decomposable materials, which increase the pressure on the environment. Therefore, the development of recyclable, biodegradable, and biocompatible materials as 3D printing materials is the trend of 3D printed CPCs based strain sensors.
At present, most of the 3D printed CPCs based strain sensors have a single function. With the increasing demand for flexible strain sensors and their wide applicability, the realization of their multi-functional use is also a trend for the future development of 3D printed CPCs based strain sensors.
Conclusion
As a preparation method for flexible strain sensors, 3D printing technology is economical, rapid, highly precise, and has been widely used in industrial and academic fields. In this mini-review, we summarize the printing principle, material selection, advantages and challenges of 3D printing. Based on the research progress, the methods, involving synergistic effect, non-covalent modification, printing parameters, the construction of microstructure, are summarized to improve the strain detection range and sensitivity of 3D-printed strain sensors. Furthermore, 3D-printed strain sensors are used in human motion detection, health care systems, direction recognition and other fields. The challenges and future prospects are put forward. There are still some challenges to be solved to achieve commercialization, the development of 3D printing technology will continue to support the preparation of flexible strain sensors, which will make 3D printing an indispensable technology in the field of wearable electronic devices.
Author Contribution
LL contributed to the compilation of data and the writing of the Manuscript. DX and ZZ contributed to the review, revision and editing of the Manuscript. YW, YL, HL, and CZ contributed to the review, revision of the Manuscript. All authors read and agree to the final text.
Conflict of Interest
The authors declare that the research was conducted in the absence of any commercial or financial relationships that could be construed as a potential conflict of interest.
Publisher’s Note
All claims expressed in this article are solely those of the authors and do not necessarily represent those of their affiliated organizations, or those of the publisher, the editors and the reviewers. Any product that may be evaluated in this article, or claim that may be made by its manufacturer, is not guaranteed or endorsed by the publisher.
Acknowledgments
The authors thank University of Nottingham for the support of this work. This work was also supported within the framework of the National Key Research and Development Program (2019YFE0120300), the Sichuan Science and Technology Program (2021YFH0031), the International Cooperation Project of Chengdu (2019-GH02-00054-HZ) and the Scientific Research Starting Project of SWPU (2019QHZ011).
References
Abshirini, M., Charara, M., Liu, Y., Saha, M., and Altan, M. C. (2018). 3d printing of highly stretchable strain sensors based on carbon nanotube nanocomposites. Adv. Eng. Mater. 20, 1800425. doi:10.1002/adem.201800425
Abshirini, M., Charara, M., Marashizadeh, P., Saha, M. C., Altan, M. C., and Liu, Y. (2019). Functional nanocomposites for 3d printing of stretchable and wearable sensors. Appl. Nanosci. 9, 2071–2083. doi:10.1007/s13204-019-01032-2
Alam, F., Varadarajan, K. M., and Kumar, S. (2020). 3d printed polylactic acid nanocomposite scaffolds for tissue engineering applications. Polym. Test. 81, 106203. doi:10.1016/j.polymertesting.2019.106203
Arif, M. F., Alhashmi, H., Varadarajan, K. M., Koo, J. H., Hart, A. J., and Kumar, S. (2020). Multifunctional performance of carbon nanotubes and graphene nanoplatelets reinforced peek composites enabled via fff additive manufacturing. Composites B: Eng. 184, 107625. doi:10.1016/j.compositesb.2019.107625
Bekas, D. G., Hou, Y., Liu, Y., and Panesar, A. (2019). 3d printing to enable multifunctionality in polymer-based composites: A review. Composites Part B: Eng. 179, 107540. doi:10.1016/j.compositesb.2019.107540
Christ, J., Aliheidari, N., Pötschke, P., and Ameli, A. (2018). Bidirectional and stretchable piezoresistive sensors enabled by multimaterial 3d printing of carbon nanotube/thermoplastic polyurethane nanocomposites. Polymers 11, 11. doi:10.3390/polym11010011
Christ, J. F., Aliheidari, N., Ameli, A., and Pötschke, P. (2017). 3d printed highly elastic strain sensors of multiwalled carbon nanotube/thermoplastic polyurethane nanocomposites. Mater. Des. 131, 394–401. doi:10.1016/j.matdes.2017.06.011
Cortés, A., Sánchez-Romate, X. F., Jiménez-Suárez, A., Campo, M., Ureña, A., and Prolongo, S. G. (2020). Mechanical and strain-sensing capabilities of carbon nanotube reinforced composites by digital light processing 3d printing technology. Polymers 12, 975. doi:10.3390/polym12040975
Dan, L., Cheng, Q., Narain, R., Krause, B., Pötschke, P., and Elias, A. (2021). Three-dimensional printed and biocompatible conductive composites comprised of polyhydroxybutyrate and multiwalled carbon nanotubes. Ind. Eng. Chem. Res. 60, 885–897. doi:10.1021/acs.iecr.0c04753
Davoodi, E., Montazerian, H., Haghniaz, R., Rashidi, A., Ahadian, S., Sheikhi, A., et al. (2020). 3d-printed ultra-robust surface-doped porous silicone sensors for wearable biomonitoring. ACS Nano 14, 1520–1532. doi:10.1021/acsnano.9b06283
Dawoud, M., Taha, I., and Ebeid, S. J. (2018). Strain sensing behaviour of 3d printed carbon black filled abs. J. Manufacturing Process. 35, 337–342. doi:10.1016/j.jmapro.2018.08.012
Dul, S., Pegoretti, A., and Fambri, L. (2020). Fused filament fabrication of piezoresistive carbon nanotubes nanocomposites for strain monitoring. Front. Mater. 7. doi:10.3389/fmats.2020.00012
Gan, X., Wang, J., Wang, Z., Zheng, Z., Lavorgna, M., Ronca, A., et al. (2019). Simultaneous realization of conductive segregation network microstructure and minimal surface porous macrostructure by sls 3d printing. Mater. Des. 178, 107874. doi:10.1016/j.matdes.2019.107874
Gao, X., Qi, S., Kuang, X., Su, Y., Li, J., and Wang, D. (2021). Fused filament fabrication of polymer materials: A review of interlayer bond. Additive Manufacturing 37, 101658. doi:10.1016/j.addma.2020.101658
Georgopoulou, A., and Clemens, F. (2020b). Piezoresistive elastomer-based composite strain sensors and their applications. ACS Appl. Electron. Mater. 2, 1826–1842. doi:10.1021/acsaelm.0c00278
Georgopoulou, A., Sebastian, T., and Clemens, F. (2020a). Thermoplastic elastomer composite filaments for strain sensing applications extruded with a fused deposition modelling 3d printer. Flex. Print. Electron. 5, 035002. doi:10.1088/2058-8585/ab9a22
Gnanasekaran, K., Heijmans, T., van Bennekom, S., Woldhuis, H., Wijnia, S., de With, G., et al. (2017). 3d printing of cnt- and graphene-based conductive polymer nanocomposites by fused deposition modeling. Appl. Mater. Today 9, 21–28. doi:10.1016/j.apmt.2017.04.003
Gul, J. Z., Sajid, M., and Choi, K. H. (2019). Retracted Article: 3D printed highly flexible strain sensor based on TPU-graphene composite for feedback from high speed robotic applications. J. Mater. Chem. C 7, 4692–4701. doi:10.1039/c8tc03423k
Guo, B., Ji, X., Chen, X., Li, G., Lu, Y., and Bai, J. (2020). A highly stretchable and intrinsically self-healing strain sensor produced by 3d printing. Virtual Phys. Prototyping 15, 520–531. doi:10.1080/17452759.2020.1823570
Guo, H., Zhao, H., Niu, H., Ren, Y., Fang, H., Fang, X., et al. (2021). Highly thermally conductive 3d printed graphene filled polymer composites for scalable thermal management applications. ACS Nano 15, 6917–6928. doi:10.1021/acsnano.0c10768
Hu, B., Hu, N., Li, Y., Akagi, K., Yuan, W., Watanabe, T., et al. (2012). Multi-scale numerical simulations on piezoresistivity of CNT/polymer nanocomposites. Nanoscale Res. Lett. 7, 402. doi:10.1186/1556-276X-7-402
Huang, P., Xia, Z., and Cui, S. (2018). 3d printing of carbon fiber-filled conductive silicon rubber. Mater. Des. 142, 11–21. doi:10.1016/j.matdes.2017.12.051
Huang, Q., Tang, Z., Wang, D., Wu, S., and Guo, B. (2021). Engineering segregated structures in a cross-linked elastomeric network enabled by dynamic cross-link reshuffling. ACS Macro Lett. 10, 231–236. doi:10.1021/acsmacrolett.0c00852
Khosravani, M. R., and Reinicke, T. (2020). 3d-printed sensors: Current progress and future challenges. Sensors Actuators A: Phys. 305, 111916. doi:10.1016/j.sna.2020.111916
Kim, J. Y., Ji, S., Jung, S., Ryu, B.-H., Kim, H.-S., Lee, S. S., et al. (2017). 3d printable composite dough for stretchable, ultrasensitive and body-patchable strain sensors. Nanoscale 9, 11035–11046. doi:10.1039/c7nr01865g
Kim, S., Oh, J., Jeong, D., and Bae, J. (2019). Direct wiring of eutectic gallium-indium to a metal electrode for soft sensor systems. ACS Appl. Mater. Inter. 11, 20557–20565. doi:10.1021/acsami.9b05363
Le, M. Q., Ganet, F., Audigier, D., Capsal, J.-F., and Cottinet, P.-J. (2017). Printing of microstructure strain sensor for structural health monitoring. Appl. Phys. A. 123. doi:10.1007/s00339-017-0970-x
Li, Y., Zhou, B., Zheng, G., Liu, X., Li, T., Yan, C., et al. (2018). Continuously prepared highly conductive and stretchable swnt/mwnt synergistically composited electrospun thermoplastic polyurethane yarns for wearable sensing. J. Mater. Chem. C 6, 2258–2269. doi:10.1039/c7tc04959e
Liu, H., Zhang, H., Han, W., Lin, H., Li, R., Zhu, J., et al. (2021). 3d printed flexible strain sensors: From printing to devices and signals. Adv. Mater. 33, 2004782. doi:10.1002/adma.202004782
Liu, Z., Qi, D., Leow, W. R., Yu, J., Xiloyannnis, M., Cappello, L., et al. (2018). 3d-structured stretchable strain sensors for out-of-plane force detection. Adv. Mater. 30, 1707285. doi:10.1002/adma.201707285
Ma, J., Wang, P., Chen, H., Bao, S., Chen, W., and Lu, H. (2019). Highly sensitive and large-range strain sensor with a self-compensated two-order structure for human motion detection. ACS Appl. Mater. Inter. 11, 8527–8536. doi:10.1021/acsami.8b20902
Maier, R. R. J., MacPherson, W. N., Barton, J. S., Carne, M., Swan, M., Sharma, J. N., et al. (2013). Embedded fiber optic sensors within additive layer manufactured components. IEEE Sensors J. 13, 969–979. doi:10.1109/jsen.2012.2226574
Mei, S., Zhang, X., Ding, B., Wang, J., Yang, P., She, H., et al. (2020). 3D‐Printed thermoplastic polyurethane/graphene composite with porous segregated structure: Toward ultralow percolation threshold and great strain sensitivity. J. Appl. Polym. Sci. 138, 50168. doi:10.1002/app.50168
Mu, Q., Wang, L., Dunn, C. K., Kuang, X., Duan, F., Zhang, Z., et al. (2017). Digital light processing 3d printing of conductive complex structures. Additive Manufacturing 18, 74–83. doi:10.1016/j.addma.2017.08.011
Pan, L., Wang, F., Cheng, Y., Leow, W. R., Zhang, Y.-W., Wang, M., et al. (2020). A supertough electro-tendon based on spider silk composites. Nat. Commun. 11, 1332. doi:10.1038/s41467-020-14988-5
Peng, S., Blanloeuil, P., Wu, S., and Wang, C. H. (2018). Rational design of ultrasensitive pressure sensors by tailoring microscopic features. Adv. Mater. Inter. 5, 1800403. doi:10.1002/admi.201800403
Peng, S., Li, Y., Wu, L., Zhong, J., Weng, Z., Zheng, L., et al. (2020a). 3d printing mechanically robust and transparent polyurethane elastomers for stretchable electronic sensors. ACS Appl. Mater. Inter. 12, 6479–6488. doi:10.1021/acsami.9b20631
Peng, S., Wang, Z., Lin, J., Miao, J. T., Zheng, L., Yang, Z., et al. (2020b). Tailored and Highly Stretchable Sensor Prepared by Crosslinking an Enhanced 3D Printed UV‐Curable Sacrificial Mold. Adv. Funct. Mater. 31, 2008729. doi:10.1002/adfm.202008729
Rollo, G., Ronca, A., Cerruti, P., Gan, X. P., Fei, G., Xia, H., et al. (2020). On the synergistic effect of multi-walled carbon nanotubes and graphene nanoplatelets to enhance the functional properties of sls 3d-printed elastomeric structures. Polymers 12, 1841. doi:10.3390/polym12081841
Ronca, A., Rollo, G., Cerruti, P., Fei, G., Gan, X., Buonocore, G., et al. (2019). Selective laser sintering fabricated thermoplastic polyurethane/graphene cellular structures with tailorable properties and high strain sensitivity. Appl. Sci. 9, 864. doi:10.3390/app9050864
Shi, G., Lowe, S. E., Teo, A. J. T., Dinh, T. K., Tan, S. H., Qin, J., et al. (2019). A versatile pdms submicrobead/graphene oxide nanocomposite ink for the direct ink writing of wearable micron-scale tactile sensors. Appl. Mater. Today 16, 482–492. doi:10.1016/j.apmt.2019.06.016
Song, J.-H., Kim, H.-J., Kim, M.-S., Min, S.-H., Wang, Y., and Ahn, S.-H. (2020). Direct printing of performance tunable strain sensor via nanoparticle laser patterning process. Virtual Phys. Prototyping 15, 265–277. doi:10.1080/17452759.2020.1733431
Song, J. H., Kim, Y.-T., Cho, S., Song, W.-J., Moon, S., Park, C.-G., et al. (2017). Surface-embedded stretchable electrodes by direct printing and their uses to fabricate ultrathin vibration sensors and circuits for 3d structures. Adv. Mater. 29, 1702625. doi:10.1002/adma.201702625
Sun, H., Han, Z., and Willenbacher, N. (2019). Ultrastretchable conductive elastomers with a low percolation threshold for printed soft electronics. ACS Appl. Mater. Inter. 11, 38092–38102. doi:10.1021/acsami.9b11071
Waheed, S., Cabot, J. M., Smejkal, P., Farajikhah, S., Sayyar, S., Innis, P. C., et al. (2019). Three-dimensional printing of abrasive, hard, and thermally conductive synthetic microdiamond-polymer composite using low-cost fused deposition modeling printer. ACS Appl. Mater. Inter. 11, 4353–4363. doi:10.1021/acsami.8b18232
Wang, L., Chen, Y., Lin, L., Wang, H., Huang, X., Xue, H., et al. (2019). Highly stretchable, anti-corrosive and wearable strain sensors based on the pdms/cnts decorated elastomer nanofiber composite. Chem. Eng. J. 362, 89–98. doi:10.1016/j.cej.2019.01.014
Wang, T., Zhang, Y., Liu, Q., Cheng, W., Wang, X., Pan, L., et al. (2018a). A self-healable, highly stretchable, and solution processable conductive polymer composite for ultrasensitive strain and pressure sensing. Adv. Funct. Mater. 28, 1705551. doi:10.1002/adfm.201705551
Wang, Y., Hao, J., Huang, Z., Zheng, G., Dai, K., Liu, C., et al. (2018b). Flexible electrically resistive-type strain sensors based on reduced graphene oxide-decorated electrospun polymer fibrous mats for human motion monitoring. Carbon 126, 360–371. doi:10.1016/j.carbon.2017.10.034
Wang, Y., Jia, Y., Zhou, Y., Wang, Y., Zheng, G., Dai, K., et al. (2018c). Ultra-stretchable, sensitive and durable strain sensors based on polydopamine encapsulated carbon nanotubes/elastic bands. J. Mater. Chem. C 6, 8160–8170. doi:10.1039/c8tc02702a
Wang, Z., Liu, X., Shen, X., Han, N. M., Wu, Y., Zheng, Q., et al. (2018d). An Ultralight Graphene Honeycomb Sandwich for Stretchable Light‐Emitting Displays. Adv. Funct. Mater. 28, 1707043. doi:10.1002/adfm.201707043
Wang, Z., Ren, J., Liu, R., Sun, X., Huang, D., Xu, W., et al. (2020). Three dimensional core-shell structured liquid metal/elastomer composite via coaxial direct ink writing for electromagnetic interference shielding. Composites A: Appl. Sci. Manufacturing 136, 105957. doi:10.1016/j.compositesa.2020.105957
Wei, P., Leng, H., Chen, Q., Advincula, R. C., and Pentzer, E. B. (2019a). Reprocessable 3d-printed conductive elastomeric composite foams for strain and gas sensing. ACS Appl. Polym. Mater. 1, 885–892. doi:10.1021/acsapm.9b00118
Wei, S., Zhang, L., Li, C., Tao, S., Ding, B., Zhu, H., et al. (2019b). Preparation of soft somatosensory-detecting materials via selective laser sintering. J. Mater. Chem. C 7, 6786–6794. doi:10.1039/c9tc01331h
Wu, X., Han, Y., Zhang, X., Zhou, Z., and Lu, C. (2016). Large-area compliant, low-cost, and versatile pressure-sensing platform based on microcrack-designed carbon black@polyurethane sponge for human-machine interfacing. Adv. Funct. Mater. 26, 6246–6256. doi:10.1002/adfm.201601995
Xiang, D., Zhang, X., Han, Z., Zhang, Z., Zhou, Z., Harkin-Jones, E., et al. (2020a). 3d printed high-performance flexible strain sensors based on carbon nanotube and graphene nanoplatelet filled polymer composites. J. Mater. Sci. 55, 15769–15786. doi:10.1007/s10853-020-05137-w
Xiang, D., Zhang, X., Harkin-Jones, E., Zhu, W., Zhou, Z., Shen, Y., et al. (2020b). Synergistic effects of hybrid conductive nanofillers on the performance of 3d printed highly elastic strain sensors. Composites Part A: Appl. Sci. Manufacturing 129, 105730. doi:10.1016/j.compositesa.2019.105730
Xiang, D., Zhang, X., Li, Y., Harkin-Jones, E., Zheng, Y., Wang, L., et al. (2019). Enhanced performance of 3d printed highly elastic strain sensors of carbon nanotube/thermoplastic polyurethane nanocomposites via non-covalent interactions. Composites Part B: Eng. 176, 107250. doi:10.1016/j.compositesb.2019.107250
Xiang, D., Zhang, Z., Han, Z., Zhang, X., Zhou, Z., Zhang, J., et al. (2020c). Effects of non-covalent interactions on the properties of 3d printed flexible piezoresistive strain sensors of conductive polymer composites. Compos. Inter. 28, 577–591. doi:10.1080/09276440.2020.1794479
Xiao, T., Qian, C., Yin, R., Wang, K., Gao, Y., and Xuan, F. (2020). 3D Printing of Flexible Strain Sensor Array Based on UV‐Curable Multiwalled Carbon Nanotube/Elastomer Composite. Adv. Mater. Technol. 6, 2000745. doi:10.1002/admt.202000745
Xu, Y.-T., Wang, Y., Zhou, C.-G., Sun, W.-J., Dai, K., Tang, J.-H., et al. (2020). An electrically conductive polymer composite with a co-continuous segregated structure for enhanced mechanical performance. J. Mater. Chem. C 8, 11546–11554. doi:10.1039/d0tc02265a
Yin, X. Y., Zhang, Y., Xiao, J., Moorlag, C., and Yang, J. (2019). Monolithic Dual‐Material 3D Printing of Ionic Skins with Long‐Term Performance Stability. Adv. Funct. Mater. 29, 1904716. doi:10.1002/adfm.201904716
Zhang, D., Chi, B., Li, B., Gao, Z., Du, Y., Guo, J., et al. (2016). Fabrication of highly conductive graphene flexible circuits by 3d printing. Synth. Met. 217, 79–86. doi:10.1016/j.synthmet.2016.03.014
Zhang, J., Ye, S., Liu, H., Chen, X., Chen, X., Li, B., et al. (2020a). 3d printed piezoelectric bnnts nanocomposites with tunable interface and microarchitectures for self-powered conformal sensors. Nano Energy 77, 105300. doi:10.1016/j.nanoen.2020.105300
Zhang, S., Liu, H., Yang, S., Shi, X., Zhang, D., Shan, C., et al. (2019). Ultrasensitive and highly compressible piezoresistive sensor based on polyurethane sponge coated with a cracked cellulose nanofibril/silver nanowire layer. ACS Appl. Mater. Inter. 11, 10922–10932. doi:10.1021/acsami.9b00900
Zhang, X., Xiang, D., Zhu, W., Zheng, Y., Harkin-Jones, E., Wang, P., et al. (2020b). Flexible and high-performance piezoresistive strain sensors based on carbon nanoparticles@polyurethane sponges. Composites Sci. Tech. 200, 108437. doi:10.1016/j.compscitech.2020.108437
Zhuang, Y., Guo, Y., Li, J., Jiang, K., Yu, Y., Zhang, H., et al. (2020). Preparation and laser sintering of a thermoplastic polyurethane carbon nanotube composite-based pressure sensor. RSC Adv. 10, 23644–23652. doi:10.1039/d0ra04479b
Keywords: 3D printing, nanocomposites, strain sensor, nanofillers, performance
Citation: Liu L, Xiang D, Wu Y, Zhou Z, Li H, Zhao C and Li Y (2021) Conductive Polymer Composites Based Flexible Strain Sensors by 3D Printing: A Mini-Review. Front. Mater. 8:725420. doi: 10.3389/fmats.2021.725420
Received: 15 June 2021; Accepted: 03 August 2021;
Published: 12 August 2021.
Edited by:
Andrea Dorigato, University of Trento, ItalyReviewed by:
Yucai Shen, Nanjing Tech University, ChinaAndreas Schiffer, Khalifa University, United Arab Emirates
Copyright © 2021 Liu, Xiang, Wu, Zhou, Li, Zhao and Li. This is an open-access article distributed under the terms of the Creative Commons Attribution License (CC BY). The use, distribution or reproduction in other forums is permitted, provided the original author(s) and the copyright owner(s) are credited and that the original publication in this journal is cited, in accordance with accepted academic practice. No use, distribution or reproduction is permitted which does not comply with these terms.
*Correspondence: Dong Xiang, ZHhpYW5nMDFAaG90bWFpbC5jb20=; Zuoxin Zhou, YWxmcmVkemhvdTYxQGhvdG1haWwuY29t