- College of Materials and Chemical Engineering, Chuzhou University, Chuzhou, China
Carbon fiber (CF)-reinforced epoxy is the most commonly used advanced composite with high performance. However, these composites usually face intractable disposal problems in their lifecycles, due to the stable cross-linked network structures of epoxy. To address this dilemma, this work proposes a facile yet efficient strategy for recycling carbon fibers from traditional carbon fiber-reinforced epoxy composites using epoxy–anhydride systems as a matrix. Diglycidyl ester of aliphatic cyclo (DGEAC) and methylhexahydrophthalic anhydride (MHHPA) were used as matrix, while T300 woven carbon fiber was used as reinforcement, to construct the composites CF/DGEAC/MHHPA. The epoxy matrix exhibited a high glass transition temperature (Tg = 126°C), high decomposition temperature (Td5 = 300°C), and good solvent resistance. By using 1,5,7-triazabicyclo[4.4.0]dec-5-ene (TBD) as a catalyst, the DGEAC/MHHPA networks could be degraded completely in ethylene glycol (EG) at 180°C within 6 h because of transesterification reactions between EG and the networks. Taking advantage of this result, a fiber recycling process was developed for carbon fiber composites, where the cross-linked networks of epoxy could be degraded with 100% carbon fiber recycling. Furthermore, the recycled carbon fiber maintained nearly 100% similarity in surface microscopic morphology and chemical structure compared with virgin carbon fiber. This work proposes a simple and efficient strategy for recycling carbon fiber from traditional high-performance composites, offering a convenient concept for the cyclic utilization of advanced composites.
Introduction
Carbon fiber-reinforced polymers (CFRPs), which are among the most popular advanced composites, simultaneously possess superior mechanical, thermal, and weight properties, and they have been broadly applied in the aerospace, sports equipment, and automotive industries (Yao et al., 2018; Tapper et al., 2020). Among them, epoxy is the most commonly used matrix, as it provides both high performance and good manufacturability. However, epoxy’s cross-linked networks after curing usually lead to a difficult recycling process of these composites at end of their service life, thus placing a heavy burden on the environment (Oliveux et al., 2015; Tapper et al., 2020). Many efforts have been made in recent years to recycle carbon fibers (CFs) from carbon fiber-reinforced epoxy, including through mechanical and thermochemical recycling (Navarro et al., 2020). Nevertheless, these methods destroy the basic properties of carbon fibers; they also often require high energy consumption, which invisibly increases the recycling cost.
To radically resolve this problem, dynamic epoxy networks have been developed in recent years (Montarnal et al., 2011; Denissen et al., 2016; Ruiz de Luzuriaga et al., 2016; Yang et al., 2021; Zhao et al., 2022). These epoxy-amine, epoxy-anhydride, or epoxy-acid systems have dynamic covalent networks formed by ester bonds (Montarnal et al., 2011; Zhao et al., 2022), imine bonds (Wang et al., 2019a), acetal bonds (Ma et al., 2019), or bisulfide bonds (Ruiz de Luzuriaga et al., 2016), all of which could be chemically degraded by bond-exchange reactions. If such epoxy systems were used as a matrix to design CFRPs, the CFs could be recycled readily (Wang et al., 2019b). For example, Qi et al. prepared CFRPs using dynamic networks constructed by ester bonds, and CFs can be recycled by transesterification reactions (TERs) using ethylene glycol (EG) as solvent (Yu et al., 2016). Zhu et al. designed CFRPs using vanillin-based epoxy, and the cross-linked networks contained large amounts of imine bonds, which could be degraded at ambient temperature under acidic conditions, resulting in the non-destructive recycling of CFs (Wang et al., 2019a). They also synthesized degradable epoxy resins containing spiro diacetal and utilized them as a matrix to prepare CFRPs (Ma et al., 2019). Due to the dynamic spiro diacetal structures, the cross-links could be completely degraded in the HCl solution. Although the CFRPs discussed above could be degraded at mild temperatures with carbon fiber recycling, there is still a large gap between them and commercial CFRPs using traditional epoxy systems in terms of their mechanical properties, costs of material synthesis, and acid resistance.
In fact, many traditional epoxy systems contain large amounts of hydroxyl groups and ester bonds, so they can also be considered dynamic cross-linked polymers. However, most of these could not be reprocessed, reshaped, or readily degraded by TERs, which has been ascribed to their extremely low reaction rates (Yang et al., 2019). In other words, if the TER rate were high enough, the cross-linked networks would exhibit dynamic properties. Recently, many efforts have been made to improve the reaction rate for TERs. One of the most important involved the concentration and the type of catalysts (Capelot et al., 2012; Chen et al., 2019a). For example, Capelot et al. (2012) first studied the influences of different catalysts on TERs-based epoxy vitrimers, with their results indicating that both 1,5,7-triazabicyclo[4.4.0]dec-5-ene (TBD) and zinc acetate exhibited higher catalysis efficiency than did triphenylphosphine. Besides, a higher TERs rate could be achieved by increasing the catalyst concentration. Apart from catalysts, the network structure design was also studied. For instance, Chen et al. (2019b) prepared a series-dynamic epoxy and found that its dynamic properties could be improved significantly by the synergy of TERs and disulfide exchange. Our group has improved glass transition temperature (Tg) and stress relaxation rate simultaneously by using natural glycyrrhizic acid in epoxy vitrimers, in which the large amounts of hydroxyl groups and the small distances between reaction groups lead to a significant increase of TERs (Wu et al., 2021). Another typical example in our recent work is that neighboring group participation during TERs could enhance the reaction rate, while the auto-catalytic high-performance epoxy matrix is prepared (Zhao et al., 2022). The networks could be completely degraded in EG at 190°C within 40 h. Although the works discussed above focused on the internal design of dynamic epoxy networks, they also establish an important fact: the rising TERs rate benefits dynamic properties such as the ready chemical degradation of cross-linked networks.
Inspired by the aforementioned efforts, this study proposes a facile yet efficient strategy for recycling carbon fiber from traditional CFRPs using epoxy–anhydride systems as a matrix. In this case, a high-performance, commercial, and low-cost epoxy system was prepared, with methylhexahydrophthalic anhydride (MHHPA) used as a curing agent to react with diglycidyl ester of aliphatic cyclo (DGEAC), forming the cross-linked networks DGEAC/MHHPA (Figure 1A). In fact, the networks contained ester bonds in high concentrations, which could be activated and thereby react with EG at high temperatures in the presence of catalyst TBD (Figure 1B). Based on this idea, the CFRPs were prepared using DGEAC/MHHPA and could be recycled efficiently in EG at 180°C with 100% carbon fiber recycling (Figure 1C). In addition, the recycled fibers exhibited nearly 100% similarity to surface microscopic morphology and chemical structures compared with virgin fibers. This work proposes a simple yet efficient strategy for recycling carbon fibers from composites based on a conventional epoxy–anhydride system, which provides a new concept for the cyclic utilization of CFRPs.
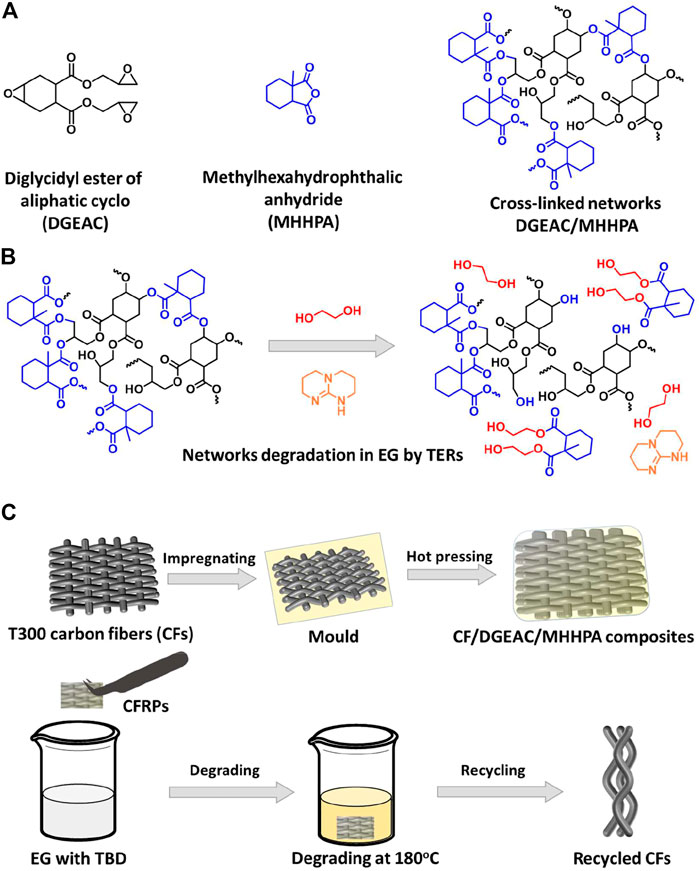
FIGURE 1. (A) Chemical structures of DGEAC, MHHPA, and DGEAC/MHHPA networks. (B) Proposed mechanism of transesterification reactions (TERs)-induced degradation of DGEAC/MHHPA networks in ethylene glycol (EG) in the presence of catalyst TBD. (C) Scheme of the preparation and recycling process of CF/DGEAC/MHHPA composites.
Materials and methods
Materials
DGEAC (Tianjin Jindong Chem), MHHPA (Energy Chemical), woven carbon fiber T300 (GW3011, Weihai Tuozhan), TBD, and EG (Energy Chemical) were applied directly without any purification.
Preparation of DGEAC/MHHPA networks
First, liquid DGEAC was blended with the liquid hardener MHHPA in a beaker at room temperature to obtain uncured DGEAC/MHHPA (homogenous solution); the viscosity of uncured DGEAC/MHHPA was 33.43 Pa S at ambient temperature (20°C). Subsequently, the solution was heated to 100°C and then poured into a stainless mold (100 mm × 80 mm × 1 mm). Then the stainless mold was placed in a press vulcanizer at 100°C. After curing at 180°C for 2 h at a pressure of 15 MPa, the DGEAC/MHHPA networks were obtained. The stoichiometric ratio of the anhydride/epoxy group was 0.5/1.
Preparation of CF/DGEAC/MHHPA composite laminates
Initially, liquid DGEAC was blended with liquid hardener MHHPA in a beaker at room temperature to obtain uncured DGEAC/MHHPA (homogenous solution). Subsequently, four slices of T300 woven carbon fibers were dip-coated layer by layer in the DGEAC/MHHPA mixture. The impregnation process used the hand paste method. The weight fraction of resins was around 30%. After that, the impregnated carbon fibers were put into a mold (100 mm × 80 mm × 1 mm) layer by layer. Finally, the mold was placed in the vulcanizer at 180°C for 2 h at a pressure of 15 MPa. For CF/DGEAC/MHHPA composites, the weight fraction of CFs was around 70%, while the volume fraction of CFs was 63%.
Chemical degradation of DGEAC/MHHPA networks and CF/DGEAC/MHHPA composites
Pure DGEAC/MHHPA matrix (∼20 mg) and CF/DGEAC/MHHPA composite laminates (∼50 mg) were immersed in EG (5 ml) at 180°C. The catalyst TBD was dissolved in EG before degradation. At different degradation times (2, 4, 6, 8, and 10 h), each sample was fetched from EG and then dried at 180°C for 24 h. After degradation, the products were filtrated and dried at 180 °C for 24 h to remove EG. Then the component was analyzed by high-performance liquid chromatography-mass spectrometry (HPLC-MS, Thermo Fisher Scientific, Oribit). Ethyl alcohol was used as a solvent. Data were acquired in positive-ion mode. Chromatographic conditions were as follows: the column was Eclipse XDB-C18 (2.1 × 150 mm, 3.5 μm), the mobile phase A was 5 mmol/L ammonium acetate, phase B was methyl alcohol, the flow rate was 0.3 ml/min, and the injection volume was 10 μL. Conditions for electrospray mass spectrometry were as follows: dry gas temperature of 450°C, nebulizer pressure of 10 Psig, GS1 of 30 Psig, GS2 of 70 Psig, capillary voltage of 4.5 kV, and m/z range of 100–2000. The cleavage plane of CF/DGEAC/MHHPA composite laminates was observed using a scanning electron microscope (SEM, JSM-6510LV). Raman spectra of virgin and recycled carbon fibers were measured by a Raman spectrometer (Horibar, Japan) with 50 ms–5 s exposure time and 3 mW laser energy.
Characterization
Fourier transform infrared spectroscopy (FTIR) was analyzed on a spectrophotometer (Nicolet 6700). Each sample was ground or mixed with potassium bromide (KBr, 100 mg), then compressed into a disk. The scan range was from 4000 to 400 cm−1. A thermogravimetric analyzer (TGA, TA-Q600) was used to evaluate the thermal stability of DGEAC/MHHPA networks (∼5 mg) from 30 to 700°C under a nitrogen atmosphere. The heating rate was 10°C/min. A differential scanning calorimeter (DSC, Netzsch, STA449F5) was applied to study the glass transition of DGEAC/MHHPA networks from room temperature to 250°C at a heating rate of 20°C/min. Interlaminar shear strength (ILSS) of the CF/DGEAC/MHHPA composite laminates (20 mm × 10 mm × 1 mm) was tested according to the JC 773–2010 standard using a mechanical testing machine (MTS-CMT4304). The crosshead motion rate was set at 1 mm/min. The ILSS can be calculated by Eq. 1:
where Pb represents the maximum force at breaking, b is the width of the sample (∼10 mm), and h is the thickness of the sample (∼1 mm). For flexural properties, the CF/DGEAC/MHHPA composite samples (60 mm × 15 mm × 1 mm) were tested according to the ASTM D7264 standard. The span-to-thickness ratio was 16:1. The crosshead motion rate was set at 2 mm/min. The flexural stress (σ) can be calculated by Eq. 2:
where p represents the applied force, L is the support span (16 mm), b is the width of the sample (∼15 mm), and h is the thickness of the sample (∼1 mm). The flexural strain (ɛ) is calculated by Eq. 3:
where δ represents the mid-span deflection (mm), L is the support span (mm), and h is the thickness of the specimen (mm). The dynamic mechanical properties of CF/DGEAC/MHHPA composite sample (30 mm × 5 mm × 1 mm) were studied using a dynamic mechanical analyzer (DMA, Mettler Toledo, DMA1) in the double cantilever beam mode. The heating rate was 5°C/min from 25 to 250°C. The frequency was set at 1 Hz and the amplitude was 10 µm.
Results and discussion
Curing and characterization of DGEAC/MHHPA networks
The cross-linked networks were constructed by curing reactions (Figure 1A), and their formation could be identified using FTIR spectra. As shown in Figure 2, the monomers and DGEAC/MHHPA networks were investigated. The signals at 1740 and 905/853 cm−1 were assigned to ester bonds and epoxy groups from DGEAC, and the signals at 2945/2865 and 1859/1789 cm−1 were assigned to methylene and inner ester bonds from MHHPA (Figure 2A). After the curing reactions, epoxy peaks from DGEAC at 905/853 cm−1 disappeared (Figure 2B), while the large ester peak at 1736 cm−1 and hydroxyl peak at 3534 cm−1 remained. These results showed that the epoxy groups and the anhydride groups were consumed completely, with cross-linking network formation.
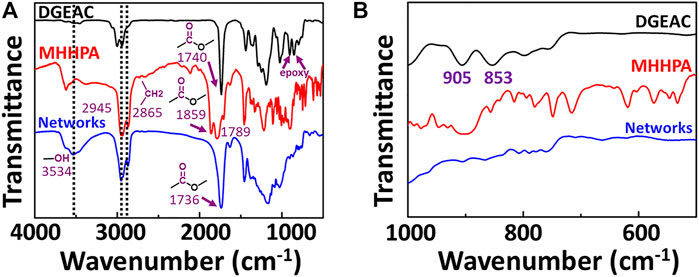
FIGURE 2. FTIR spectra of DGEAC, MHHPA, and cured DGEAC/MHHPA networks. The wavenumber was 4000–500 cm−1 and 1000–500 cm−1 for (A,B), respectively.
To further identify the cross-linked networks, gel content tests of DGEAC/MHHPA networks were studied at room temperature. After swelling in acetone, tetrahydrofuran (THF), dimethyl sulfoxide (DMSO), MeOH, EtOH, HCl (1 M), H2SO4 (1 M), NaOH (1 M), and H2O for 48 h, all the DGEAC/MHHPA networks maintained high gel contents over 97% (Figure 3), revealing that the DGEAC/MHHPA networks exhibited good solvent resistance in acidic and alkaline aqueous solutions and in organic solvents.
The thermal properties of DGEAC/MHHPA networks were investigated using a thermogravimetric analyzer (TGA) and a differential scanning calorimeter (DSC) (Figure 4). The temperature at 5% of weight loss (Td5) was 300°C, exhibiting good thermal stability of DGEAC/MHHPA networks (Figure 4A). In addition, the glass transition temperature (Tg) of 126 °C for DGEAC/MHHPA networks is shown in Figure 4B and reveals the rigid structure of DGEAC/MHHPA. Furthermore, apart from the glass transition, there was no exothermic peak at high temperatures, indicating complete curing reactions between DGEAC and MHHPA.
Degradation of DGEAC/MHHPA networks
All the results discussed above indicate that permanent cross-linked networks were constructed by curing reactions and could not be degraded by a commonly used solvent at room temperature. However, the large amount of ester bonds could react with EG at high temperatures in TERs. Our previous work reported a series of TERs-based epoxy vitrimers, and these systems could be reshaped, reprocessed, physically recycled, self-healed, and degraded at high temperatures (Wu et al., 2020; Wu et al., 2021; Zhang et al., 2021). Under these circumstances, TBD played an important role as a catalyst, resulting in TERs-induced network rearrangements at high temperatures. For the vitrimer degradation process, EG was usually used as solvent and reactant to offer large amounts of hydroxyl groups, while the intrinsic catalyst TBD improved the TERs (Kuang et al., 2018; Hamel et al., 2019; Wu et al., 2020). Inspired by this concept, this work proposes a facile yet effective strategy in which TBD is used as an external catalyst to dissolve in EG, thus reacting with DGEAC/MHHPA networks by TERs. As shown in Figure 5A, the DGEAC/MHHPA networks hardly degraded without TBD at 180°C for 10 h, while the residual weight/original weight approached 100%. Upon the addition of 0.006 mol/L TBD, the DGEAC/MHHPA networks totally degraded under the same conditions. The results confirmed that the degradation process is controlled by TERs and can also be improved by the conventional catalyst TBD (Figure 1B). To further study this process, the degradation kinetics of DGEAC/MHHPA networks was investigated by measuring relative weights at different degradation times. With the addition of 0.006 mol/L, the weight decreased to 47% in the first 4 h, reduced to 28% at 8 h, and finally reached 5% at 10 h (Figure 5B, black color). Meanwhile, with the increase in TBD concentration (0.012 mol/L), the degradation rate rose significantly, and the weight declined to 39% at 4 h and reached 0 at 6 h (Figure 5B, red color). The degradation rate in the first 2 h was relatively slow, revealing the solvent warming and materials swelling during the initial process. After that, the degradation rate became much higher, indicating that the TERs-induced dissociation was inundated with DGEAC/MHHPA networks. Latterly, the degradation rate decreased as the mass of networks was reduced. The above results also indicate that the concentration of catalyst determines the degradation rate of DGEAC/MHHPA networks directly, and the external TBD could swell into the networks and further promote TERs. Therefore, the degradation process could be optimized by catalysts to avoid large energy consumption by high temperatures and long hours. Note that this degradation strategy using external catalysts for epoxy networks is simple yet efficient. In our previous work, internal catalysts were not encouraged in epoxy vitrimers because of their influence on the curing process and networks’ performance, and different methods were proposed to improve and regulate the dynamic networks, such as increasing the concentration of hydroxyl groups in networks (Wu et al., 2021), designing multiple dynamic covalent bonds (Gong et al., 2022), and mediating neighboring group participation (Zhao et al., 2022). However, the methods proposed here are much more straightforward and universal. Although the concentration of catalysts in degradation was much higher than in the reported epoxy vitrimer preparation, the solvents with dissolved catalysts could be reused for another degradation process, thus reducing the cost of catalysts.
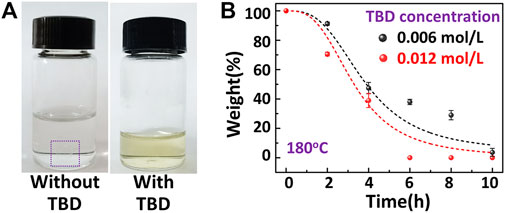
FIGURE 5. (A) Digital photos of DGEAC/MHHPA networks in EG with and without TBD after 10 h at 180°C. (B) Degradation kinetics of DGEAC/MHHPA in EG at 180°C. Concentration of TBD was 0.006 and 0.012 mol/L for black color and red color, respectively. Line is the fit with the logistic function.
Recycling of CF/DGEAC/MHHPA composites
The above results using DGEAC/MHHPA networks suggest the feasibility of degradation cross-linked networks via TERs, and this strategy could be helpful in recycling carbon fibers (CFs) from CF/DGEAC/MHHPA composites. CF/DGEAC/MHHPA composites were prepared as shown in Figure 6A. The fiber volume fraction of CF/DGEAC/MHHPA was 63%. The cleavage plane of CF/DGEAC/MHHPA composite laminates is shown in Figure 6B and exhibits a robust interface between the matrix and the CFs. The interlaminar shear strength (ILSS) of CF/DGEAC/MHHPA composites was 27.24 MPa (Figure 6C). To evaluate the mechanical properties of CF/DGEAC/MHHPA composites, flexural tests were additionally performed. As shown in Figure 6D, the flexural strength and modulus were 622 MPa and 59 GPa, respectively, which are similar to traditional carbon fiber-reinforced epoxy composites using epoxy–anhydride systems as a matrix. To investigate the dynamic mechanical properties of CF/DGEAC/MHHPA composites, dynamic mechanical analysis (DMA) was used with a double cantilever beam model. The storage modulus (E’) of CF/DGEAC/MHHPA composites was 7.7 GPa at room temperature, dropped rapidly at around 90°C, and finally remained at 1.1 GPa during the rubber plateau (Figure 6E). The peaks of tan δ, assigned as the Tg, was 110 °C for composites, which approached the Tg of DGEAC/MHHPA networks.
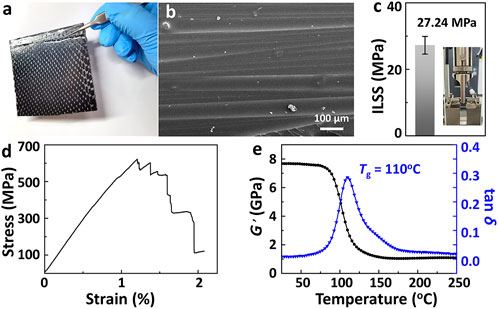
FIGURE 6. (A) Digital photo of CF/DGEAC/MHHPA composite laminates. (B) SEM image of the cleavage plane of CF/DGEAC/MHHPA composite laminates. (C) Interlaminar shear strength (ILSS) of CF/DGEAC/MHHPA. Inset photo is the sample during ILSS test. (D) Stress–strain curve of CF/DGEAC/MHHPA composites under flexural tests. (E) Storage modulus (G′, black line) and tan δ (blue line) of CF/DGEAC/MHHPA composites.
In order to recycle CFs from CF/DGEAC/MHHPA composites, EG was applied as a solvent and reactant and TBD was used as a catalyst for degrading DGEAC/MHHPA matrix through TERs. The proposed mechanism of the degradation process is illustrated in Figure 7A. Initially, the matrix swelled with EG and TBD accessing the polymer networks. Subsequently, the hydroxyl groups of EG participated in TERs at 180°C in the presence of TBD, causing the partial degradation of DGEAC/MHHPA networks. Finally, a large proportion of the ester bonds in the networks were degraded, where the clean CFs could be left. Notably, sizing agents are always attached to the surface of commercial carbon fibers, which might react with epoxy resins. However, ester bonds linked between matrix and sizing agents can also be degraded by EG, and the limited sizing agent concentration would hardly influence the properties of recycled CFs. To further verify the TERs-induced degradation process, the component of degradation products was further investigated using high-performance liquid chromatography–mass spectrometry (HPLC-MS). The mass spectrometry cleavage features were used to determine the structures of products at different retention times (Figure 7B). The products at 2.25–2.80 min showed [M + H]+ at m/z 140 and [M + Na]+ at m/z 349. The products at 3.77–5.02 min showed [M + Na + H2O]+ at m/z 509. The products at 37.70–39.82 min showed [M]+ at m/z 274 and [M]+ at m/z 534. The derived molecular formula is shown in Figure 7B and confirms the occurrence of TERs during the degradation process. The degradation kinetic of CF/DGEAC/MHHPA composites was studied by measuring their relative weights at different degradation times, as shown in Figure 7C. Following the results of the degradation of DGEAC/MHHPA networks, the concentration of the catalyst TBD was set at 0.006 mol/L. The relative weight of CF/DGEAC/MHHPA declined to 80% during the initial 2 h, then decreased to 75% at 6 h and finally reached 72%, which approached the actual weight fraction of CFs. Note that the degradation rate of CF/DGEAC/MHHPA composites was higher than that of DGEAC/MHHPA networks, which might be due to the composites’ offering interspace for solvent entrance and reaction. Digital photos of the recycling process are shown in Figure 7D; the solution color slightly deepened as the immersing time with the separation of CFs. After 10 h, the DGEAC/MHHPA matrix was removed completely from CFs. Because the volume of the composite samples was relatively small, the recycled CFs seemed incompact. However, the above degradation process hardly led to the destruction of CFs, and these recycled CFs could be reused in other ways, such as chopped fibers.
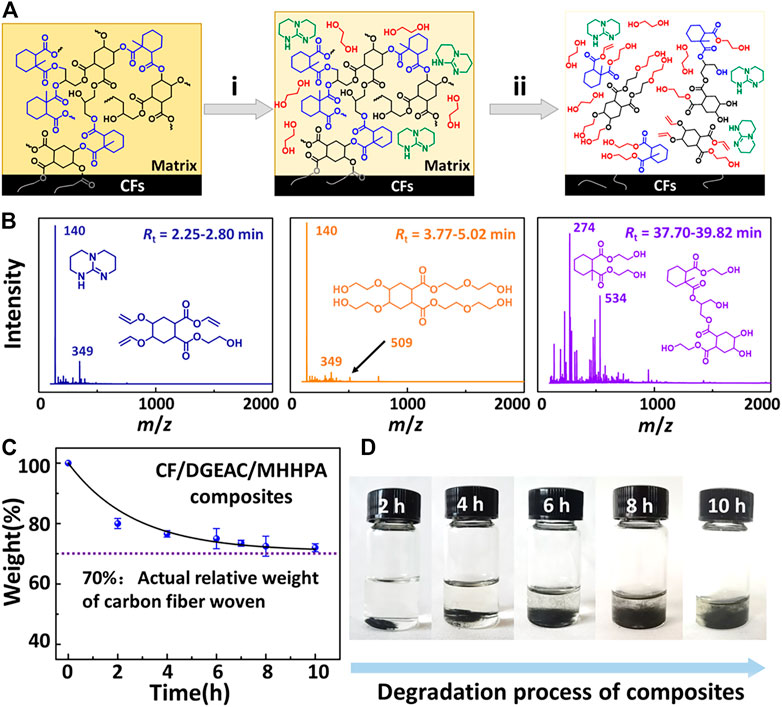
FIGURE 7. (A) Proposed degradation mechanism of CF/DGEAC/MHHPA composites at 180°C in EG in the presence of TBD. (i) DGEAC/MHHPA matrix swelled in EG at 180°C. (ii) DGEAC/MHHPA matrix completely degraded in EG at 180°C. (B) HPLC-MS chromatogram of CF/DGEAC/MHHPA composites. Retention time of degradation products was 2.25–2.80, 3.77–5.02, and 37.70–39.82 min. Products at 2.25–2.80 min showed [M + H]+ at m/z 140 and [M + Na]+ at m/z 349. Products at 3.77–5.02 min showed [M + Na + H2O]+ at m/z 509. Products at 37.70–39.82 min showed [M]+ at m/z 274 and [M]+ at m/z 534. (C) Degradation kinetics of CF/DGEAC/MHHPA in EG at 180°C. Line is the fit with the exponential decay function mt = mf + mr e−t/τ, where mt, mf, mr represent the weight fraction of residual composites, the weight fraction of CFs in original composites before degradation (0.71), and the weight fraction of matrix in original composites before degradation (0.29), while τ (2.67 h) is the characteristic time when mt–mf decreases to 36.8% of mr. (D) Digital photos of the recycling process of CF/DGEAC/MHHPA composites in EG at 180°C.
To evaluate the effects of CFs in this recycling process, their surface microscopic morphology and chemical structure were investigated. As shown in Figure 8A, the surfaces of virgin and recycled CFs were observed by SEM. It is clear that the surface of virgin CFs was smooth and clean, while the surface of recycled CFs only contained a little matrix after the degradation process, which is similar to that of virgin CFs. Meanwhile, the chemical structure of virgin and recycled CFs was studied using Raman spectra, as shown in Figure 8B. It was clear that there was no difference between virgin CFs and recycled CFs, indicating that the degradation hardly affected the graphitization structure of CFs. The Ktex of virgin and recycled CFs were also evaluated, as shown in Figure 8C. The Ktex of recycled CFs was 0.639 g/m, which was slightly higher than that of virgin CFs.
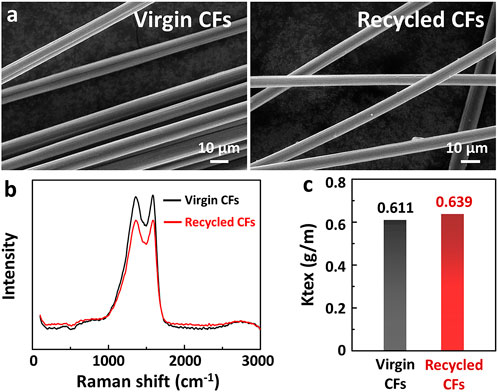
FIGURE 8. (A) SEM images of the surface microscopic morphology of virgin and recycled CFs. (B) Raman spectra of virgin and recycled CFs. (C) Ktex of virgin and recycled CFs.
Conclusion
This work has proposed a facile yet efficient strategy for recycling carbon fibers from traditional CFRPs using epoxy–anhydride systems as a matrix. Epoxy matrix DGEAC/MHHPA was prepared using traditional epoxy–anhydride reactions from DGEAC and MHHPA. The DGEAC/MHHPA cross-linked networks exhibited a high glass transition temperature (Tg = 126°C), high decomposition temperature (Td5 = 300°C), and good solvent resistance. By using TBD as a catalyst, the DGEAC/MHHPA networks could be degraded completely in EG at 180°C by 10 h because of the TERs between EG and networks. Meanwhile, with the increase of TBD concentration (0.012 mol/L), the degradation rate improved significantly, with total degradation by 6 h. Based on these results, carbon fiber composites CF/DGEAC/MHHPA were prepared using DGEAC/MHHPA as a matrix. The CF/DGEAC/MHHPA composites exhibited good mechanical properties with a flexural strength of 622 MPa and modulus of 59 GPa and also maintained good thermal stability (Tg = 110°C). By using EG as solvents and TBD as catalysts at 180°C, the relative weight of CF/DGEAC/MHHPA composites decreased to 72% at 10 h, with the matrix completely degraded and CFs recycled. Furthermore, the recycled CFs maintained nearly 100% similarity to surface microscopic morphology and chemical structure compared with virgin CFs. This work proposes a simple yet efficient strategy for recycling carbon fibers from traditional high-performance composites, offering a convenient concept for the cyclic utilization of advanced composites.
Data availability statement
The original contributions presented in the study are included in the article/supplementary material, further inquiries can be directed to the corresponding authors.
Author contributions
JW designed and supervised the project and also wrote and edited the article. YP assisted in analysis and editing. YP, ZR, JA, ZZ, and JB performed the experiments and analyzed the data. XJ contributed to the writing-review. All authors contributed to the manuscript revision and read and approved the submitted version.
Funding
This work was supported by the grant “Anhui Province Key Laboratory of Environment-friendly Polymer Materials” (2022KF011). This work was also supported by research funds from Chuzhou University (2022qd012), the Key Research and Development Program of Anhui Province (No. 202104b11020010) and National Undergraduate Training Program for Innovation and Entrepreneurship (2022CXXL086)..
Conflict of interest
The authors declare that the research was conducted in the absence of any commercial or financial relationships that could be construed as a potential conflict of interest.
Publisher’s note
All claims expressed in this article are solely those of the authors and do not necessarily represent those of their affiliated organizations, or those of the publisher, the editors, and the reviewers. Any product that may be evaluated in this article, or claim that may be made by its manufacturer, is not guaranteed or endorsed by the publisher.
References
Capelot, M., Unterlass, M. M., Tournilhac, F., and Leibler, L. (2012). Catalytic control of the vitrimer glass transition. ACS Macro Lett. 1, 789–792. doi:10.1021/mz300239f
Chen, M., Zhou, L., Wu, Y., Zhao, X., and Zhang, Y. (2019). Rapid stress relaxation and moderate temperature of malleability enabled by the synergy of disulfide metathesis and carboxylate transesterification in epoxy vitrimers. ACS Macro Lett. 8, 255–260. doi:10.1021/acsmacrolett.9b00015
Chen, Q., Li, Y., Yang, Y., Xu, Y., Qian, X., Wei, Y., et al. (2019). Durable liquid-crystalline vitrimer actuators. Chem. Sci. 10, 3025–3030. doi:10.1039/c8sc05358h
Denissen, W., Winne, J. M., and Du Prez, F. E. (2016). Vitrimers: Permanent organic networks with glass-like fluidity. Chem. Sci. 7, 30–38. doi:10.1039/c5sc02223a
Gong, H., Wu, J., Zhao, Z., Guo, Z., Gao, L., Zhang, B., et al. (2022). Recyclable high-performance glass-fiber/epoxy composites with UV-shielding and intrinsic damage self-reporting properties. Chem. Eng. J. 446, 137392. doi:10.1016/j.cej.2022.137392
Hamel, C. M., Kuang, X., Chen, K., and Qi, H. J. (2019). Reaction-diffusion model for thermosetting polymer dissolution through exchange reactions assisted by small-molecule solvents. Macromolecules 52, 3636–3645. doi:10.1021/acs.macromol.9b00540
Kuang, X., Shi, Q., Zhou, Y., Zhao, Z., Wang, T., and Qi, H. J. (2018). Dissolution of epoxy thermosets via mild alcoholysis: The mechanism and kinetics study. RSC Adv. 8, 1493–1502. doi:10.1039/c7ra12787a
Ma, S., Wei, J., Jia, Z., Yu, T., Yuan, W., Li, Q., et al. (2019). Readily recyclable, high-performance thermosetting materials based on a lignin-derived spiro diacetal trigger. J. Mat. Chem. A Mat. 7, 1233–1243. doi:10.1039/c8ta07140c
Montarnal, D., Capelot, M., Tournilhac, F., and Leibler, L. (2011). Silica-Like malleable materials from permanent organic networks. Science 334, 965–968. doi:10.1126/science.1212648
Navarro, C. A., Giffin, C. R., Zhang, B., Yu, Z., Nutt, S. R., and Williams, T. J. (2020). A structural chemistry look at composites recycling. Mat. Horiz. 7, 2479–2486. doi:10.1039/d0mh01085e
Oliveux, G., Dandy, L. O., and Leeke, G. A. (2015). Current status of recycling of fibre reinforced polymers: Review of technologies, reuse and resulting properties. Prog. Mater. Sci. 72, 61–99. doi:10.1016/j.pmatsci.2015.01.004
Ruiz de Luzuriaga, A., Martin, R., Markaide, N., Rekondo, A., Cabañero, G., Rodríguez, J., et al. (2016). Epoxy resin with exchangeable disulfide crosslinks to obtain reprocessable, repairable and recyclable fiber-reinforced thermoset composites. Mat. Horiz. 3, 241–247. doi:10.1039/c6mh00029k
Tapper, R. J., Longana, M. L., Norton, A., Potter, K. D., and Hamerton, I. (2020). An evaluation of life cycle assessment and its application to the closed-loop recycling of carbon fibre reinforced polymers. Compos. Part B Eng. 184, 107665. doi:10.1016/j.compositesb.2019.107665
Wang, B., Ma, S., Yan, S., and Zhu, J. (2019). Readily recyclable carbon fiber-reinforced composites based on degradable thermosets: A review. Green Chem. 21, 5781–5796. doi:10.1039/c9gc01760g
Wang, S., Ma, S., Li, Q., Xu, X., Wang, B., Yuan, W., et al. (2019). Facile in situ preparation of high-performance epoxy vitrimer from renewable resources and its application in nondestructive recyclable carbon fiber composite. Green Chem. 21, 1484–1497. doi:10.1039/c8gc03477j
Wu, J., Gao, L., Guo, Z., Zhang, H., Zhang, B., Hu, J., et al. (2021). Natural glycyrrhizic acid: Improving stress relaxation rate and glass transition temperature simultaneously in epoxy vitrimers. Green Chem. 23, 5647–5655. doi:10.1039/d1gc01274f
Wu, J., Yu, X., Zhang, H., Guo, J., Hu, J., and Li, M.-H. (2020). Fully biobased vitrimers from glycyrrhizic acid and soybean oil for self-healing, shape memory, weldable, and recyclable materials. ACS Sustain. Chem. Eng. 8, 6479–6487. doi:10.1021/acssuschemeng.0c01047
Yang, Y., Terentjev, E. M., Zhang, Y., Chen, Q., Zhao, Y., Wei, Y., et al. (2019). Reprocessable thermoset soft actuators. Angew. Chem. Int. Ed. Engl. 58, 17474–17479. doi:10.1002/anie.201911612
Yang, Y., Xu, Y., Ji, Y., and Wei, Y. (2021). Functional epoxy vitrimers and composites. Prog. Mater. Sci. 120, 100710. doi:10.1016/j.pmatsci.2020.100710
Yao, S.-S., Jin, F.-L., Rhee, K. Y., Hui, D., and Park, S.-J. (2018). Recent advances in carbon-fiber-reinforced thermoplastic composites: A review. Compos. Part B Eng. 142, 241–250. doi:10.1016/j.compositesb.2017.12.007
Yu, K., Shi, Q., Dunn, M. L., Wang, T., and Qi, H. J. (2016). Carbon fiber-reinforced thermoset composite with near 100% recyclability. Adv. Funct. Mat. 26, 6098–6106. doi:10.1002/adfm.201602056
Zhang, W., Wu, J., Gao, L., Zhang, B., Jiang, J., and Hu, J. (2021). Recyclable, reprocessable, self-adhered and repairable carbon fiber-reinforced polymers using full biobased matrices from camphoric acid and epoxidized soybean oil. Green Chem. 23, 2763–2772. doi:10.1039/d1gc00648g
Keywords: carbon fiber-reinforced polymers, composites, epoxy, carbon fiber recycling, transesterification reactions
Citation: Wu J, Pan Y, Ruan Z, Zhao Z, Ai J, Ban J and Jing X (2022) Carbon fiber-reinforced epoxy with 100% fiber recycling by transesterification reactions. Front. Mater. 9:1045372. doi: 10.3389/fmats.2022.1045372
Received: 15 September 2022; Accepted: 03 November 2022;
Published: 24 November 2022.
Edited by:
Xiangdong Liu, Changchun Institute of Applied Chemistry (CAS), ChinaReviewed by:
Junheng Zhang, South-Central University for Nationalities, ChinaVeronique Michaud, Ecole Polytechnique Fédérale de Lausanne, Switzerland
Gang Sui, Beijing University of Chemical Technology, China
Copyright © 2022 Wu, Pan, Ruan, Zhao, Ai, Ban and Jing. This is an open-access article distributed under the terms of the Creative Commons Attribution License (CC BY). The use, distribution or reproduction in other forums is permitted, provided the original author(s) and the copyright owner(s) are credited and that the original publication in this journal is cited, in accordance with accepted academic practice. No use, distribution or reproduction is permitted which does not comply with these terms.
*Correspondence: Jianqiao Wu, d3VqaWFucWlhbzEwMTJAMTYzLmNvbQ==; Xianghai Jing, YWVyb3N1bkBhbGl5dW4uY29t