- 1Research Unit of Sustainable Chemistry, University of Oulu, Oulu, Finland
- 2Department of Materials Science and Engineering, The University of Sheffield, Sheffield, United Kingdom
- 3Research Unit of Process Metallurgy, University of Oulu, Oulu, Finland
Chemical precipitation is one of the most widely known methods for treatment of industrial wastewaters with high sulphate content, where sulphate can be precipitated as practically insoluble ettringite (Ca6Al2(SO4)3(OH)12·26H2O). This treatment method is also widely recognised for solidifying hazardous components and toxic elements e.g. arsenic in wastewater. In the ettringite precipitation process, lime and aluminium salts are typically used as starting materials, in stoichiometric amounts to form ettringite from the sulphate-containing water, leading to a pH rise to ∼11.5 and ettringite precipitation. In the current study, for the first time, ye’elimite mineral (Ca4Al6O12SO4), also known as calcium sulfoaluminate (CSA) in cements, is used in order to investigate its suitability to form ettringite precipitate from sulphate and arsenic containing synthetic wastewater and industrial wastewater solutions. The dissolution of ye’elimite prior to dosing, optimal precipitation pH, and arsenic co-precipitation were studied. The effluent and precipitates were characterized using X-ray diffraction (XRD), field emission scanning electron microscopy (FESEM-EDS) and inductively coupled plasma atomic emission spectroscopy (ICP-OES). The results showed that high percentage of sulphate removal (98% in the synthetic wastewater and 87% in the industrial wastewater) can be achieved using ye’elimite as the aluminium source in ettringite precipitation. Additionally, up to 95% arsenic removal was achieved in arsenic co-precipitation experiments from the synthetic wastewater. The current developed technology can be used as a novel ecological and cost-effective approach for removal of sulphate and toxic elements from wastewater.
1 Introduction
Sulphate is a common major anion in industrial wastewaters formed in many industries, such as mining, metal, and pulp manufacturing (Jin et al., 2020). Sulphate anion
The crystalline structure of ettringite
The typically used aluminium reagents, such as sodium aluminate are costly (Sapsford and Tufvesson, 2017; Tian et al., 2019). The choice of aluminium reagent has high impact on operational cost of the ettringite precipitation method. Alternatively, industrial by-products can be utilised as aluminium reagents during ettringite precipitation process, offering ecological benefits and lower costs (Álvarez-Ayuso and Nugteren, 2005). A cost effective sulphate removal process using an aluminium-based proprietary reagent has also been suggested in the literature (Reinsel, 1999). The selection of aluminium reagent influences the efficiency of sulphate removal, as well as sludge density and sludge settling velocity (Sapsford and Tufvesson, 2017).
Ettringite can also be produced using ye’elimite (Ca4Al6O12SO4), the representative hydraulic phase in calcium sulfoaluminate (CSA) cements (Haha et al., 2019). CSA-based clinker can be produced using industrial by-products and are intensively promoted as eco-friendly alternatives to Portland cement (PC), due to their potential to reduce carbon dioxide
Upon hydration, ye’elimite forms the main hydrates in CSA-based cement systems, including highly crystalline ettringite and partially disordered monosulfate, as well as amorphous aluminium hydroxide (Glasser and Zhang, 2001; Hargis et al., 2014). Hence, ettringite is formed in the presence of calcium, sulphate, and hydroxide in the aqueous solution (Fridrichová et al., 2016):
In the present work, the suitability of ye’elimite, together with calcium hydroxide, to form ettringite precipitate from sulphate and arsenic containing synthetic wastewater and industrial wastewater solutions is investigated. Calcium hydroxide can be used unaccompanied to remove sulphate from water; however, in order to reduce
2 Materials and methods
2.1 Materials
Sodium sulphate (VWR, 99.9%) and arsenic pentoxide (VWR, 99.9%) were used for preparation of synthetic wastewater solutions. Hydrochloric acid (VWR, 37%) and calcium hydroxide (VWR, 98%) were used in the ettringite precipitation experiments. Calcium hydroxide was used at 10 wt% aqueous solution (2.045 g calcium hydroxide in 18 ml deionized water) in this study. 1 or 10 M sodium hydroxide solutions (Merck), were used in order to adjust pH of solutions. Aluminium oxide (Alfa Aesar, 99.7%), calcium sulphate (Alfa Aesar 99%), and calcium oxide (Alfa Aesar, 99%) were used to synthesize ye’elimite. The chemical composition of industrial wastewater used in this study is tabulated in Table 1.
2.2 Sample preparation
Three synthetic wastewater solutions were prepared by addition of 2.62 g sodium sulphate and a varying amount of arsenic pentoxide (0, 0.23, and 0.35 g) to 1 L deionized water, which corresponds to sulphate concentration of 2,000 ppm (including sulphate from ye’elimite) and arsenic concentrations of 0, 58, and 100 ppm (mg/L). The synthetic wastewater solution containing sodium sulphate in absence of arsenic pentoxide is referred to as “model solution” in this study.
Ye’elimite (250 g) was synthesized from stoichiometric amounts of aluminium oxide (50.1 wt%), calcium sulphate (22.3 wt%), and calcium oxide (27.6 wt%) at 1,300°C. The raw materials were dried at 800°C prior to firing and mixed by hand in a porcelain mortar for 20 min and added to an alumina crucible. The crucible was placed in a preheated (600°C) muffle furnace (Nabertherm Chamber furnace) and heated to 1300°C with the heating rate of 10°C/min, held for 4 h, and then slowly cooled down to room temperature during 4 h with the average cooling rate of 300°C/h. Ye’elimite was ground using a mortar and sieved using an air jet sieve (Alpine e200LS, Hosokawa Micron, Japan) with particle size of 125 μm. The purity of synthesized ye’elimite was 91.6% (Cuesta et al., 2013), containing minor phases of 5.8% krotite (CaAl2O4) (Hörkner and Müller-Buschbaum, 1976), and 2.6% anhydrite
To achieve maximum sulphate removal efficiency, several dissolution methods for ye’elimite were tested. These include dissolving 1.2 g ye’elimite in 1) 11 ml deionized water at 20°C, 2) 11 ml deionized water at 70°C, 3) calcium hydroxide aqueous solution (2.0 g calcium hydroxide in 18 ml deionized water) at 20°C, and 4) 3 ml hydrochloric acid at 20°C, comprising four different dissolution methods. Ye’elimite was dissolved for 2 h using magnetic stirrer (1400 rpm) in each solutions and then was used as reagent in the ettringite precipitation experiments. Each of these ye’elimite containing solutions were then added separately to 800 of mL model solution simultaneously into four zones (dropwise during 5 min with 400 rpm) using a programmable paddle stirrer equipment (Kemira, Flocculator 2000).
For ettringite precipitation, the calcium hydroxide mixtures were added in stoichiometric ratio into the synthetic wastewater and industrial wastewater solutions
2.3 Analytical techniques
All effluent samples were vacuum filtered through 0.45 μm cellulose nitrate membrane filters (Sartorius) prior to analysis. Aluminium, calcium, and arsenic elements were detected with an inductively coupled plasma atomic emission spectroscopy (ICP-OES). Sulphate was measured with an IC (METROHM 761 Compact IC, Herisau) following standard SFS-EN ISO 10304–1. Magnesium was measured using an atomic absorption spectrophotometer (AAS) (Varian AA240FS) based on standard SFS 3018. Both IC and AAS measurements were done triplicate. pH and conductivity of the effluent samples were measured using a HACH HQ40d portable meter and the turbidity was measured using an Oakton Portable Turbidimeter TN-100.
The synthesized ye’elimite was analysed using a SmartLab 9 kW diffractometer (Rigaku) equipped with D/teX Ultra 250 detector. X-ray diffraction (XRD) pattern was recorded with Co (Kα1 = 1.78892, Kα2 = 1.79278) at 40 kV and 135 mA in a range of 2-theta 5–130° with step size of 0.02° and scanning speed 4.063°/min. The phase quantities from XRD patterns were analysed with Rietveld method using PDXL 2 software (Rigaku, Japan) with PDF-4 + 2020 RDB database.
The dried precipitate samples were analysed with the PANalytical X’Pert PRO X-ray Diffractometer. The difractograms were collected using Cu Kα (1.5406 Å) source at 40 mA and 45 kV in the 2 Theta range of 5–70° and with a scan speed of 0.0235°/s. The XRD analysis was conducted using the HighScore program and Rietveld method.
Field emission scanning electron microscopy (FESEM-EDS) analysis of precipitates was conducted using a Zeiss Ultra plus operated at 15 kV with energy dispersive X-ray spectroscopy (EDS) detector and Aztec software (Oxford Instruments). Arsenic content in the precipitates from arsenic coprecipitation experiments was measured using the ICP-OES. The analysis was conducted according to U.S. EPA Method 3051A, where the microwave-assisted wet digestion was performed using a 3:1 ratio of HNO3 and HCl acid.
3 Results and discussion
3.1 Effectiveness of ye’elimite dissolution method
In order to examine the effectiveness of sulphate removal, different ye’elimite dissolution methods were tested. Figure 1 below shows the percentage of sulphate removal from the model solution (sodium sulphate containing synthetic wastewater in absence of arsenic pentoxide); i.e., when ye’elimite was dissolved in four different solutions: deionized water at 20 and 70°C, solution of 10 wt% calcium hydroxide in deionized water at 20°C, and hydrochloric acid at 20°C. As shown in Figure 1, the dissolution of ye’elimite in hydrochloric acid resulted in significantly higher sulphate removal (95%), indicating that almost all ye’elimite was dissolved and reacted in order to form ettringite, yielding the highest amount of ettringite (84%). Thus, the hydrochloric acid dissolution method of ye’elimite (described in Section 2.2) was selected for further investigations in this study.
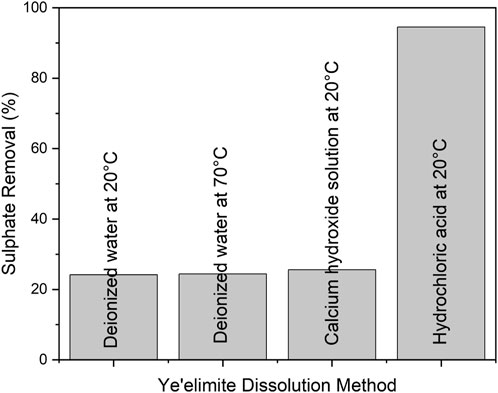
FIGURE 1. Percentage of sulphate removal from the synthetic wastewater using different ye’elimite dissolution methods.
3.2 pH optimisation of ettringite precipitation
pH is an important parameter in ettringite precipitation since ettringite is only stable in the pH range of 10.5–13 (Tolonen et al., 2016; Segundo et al., 2019). Four different pH values were tested for the ettringite precipitation experiment, including 11.0, 11.5, 12.0, and 12.5 (Figure 2). The current results show that the highest percentage of sulphate removal from the model solution was achieved at pH 12–12.5. Similarly pH range of 11–12.5 was suggested for ettringite precipitation in the literature (Chrysochoou and Dermatas, 2006; Almasri et al., 2015). As shown in Figure 3, pH 11.0 was too low to effectively remove sulphate. This can be due to the partial dissolution of formed ettringite, as the pH is close to the lower limit of ettringite stability range.
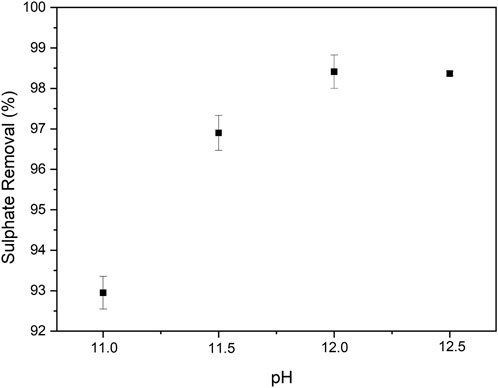
FIGURE 2. Percentage of sulphate removal from the model solution using different precipitation pH. Error bars represent standard deviation (n = 2).
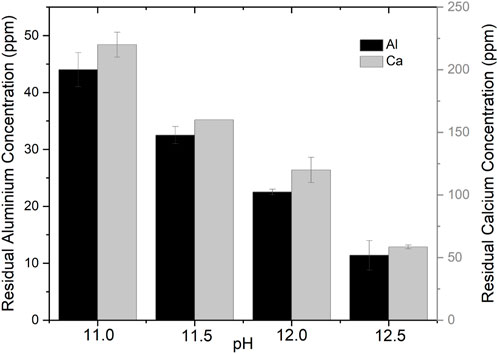
FIGURE 3. Residual aluminium and calcium concentrations with different precipitation pH. Error bars represent standard deviation (n = 2).
Additionally, the residual aluminium and calcium concentrations were measured as a function of pH (Figure 3). The residual aluminium and calcium concentrations were decreased by increasing pH from 11 to 12.5. This can be due to an increase in ettringite stability. At pH 12, the residual aluminium and calcium concentrations were less than 25 mg/L, and 140 mg/L, respectively. As calcium hydroxide and deionized water were added to ettringite in stoichiometric amounts, residual aluminium, calcium, and sulphate were present, due to ettringite solubility. Moreover, the ettringite yield increased with increasing pH by 82%, 86%, 87%, and 88% at pH 11, 11.5, 12, and 12.5, respectively.
X-ray diffractograms of the ettringite precipitates prepared with different pH were used to identify ettringite (ICDD 04-013-3691) and calcite (ICDD 04-066-0867) peaks at pH range 11.0–12.5 (Figure 4). The amounts of ettringite and calcite in the solid samples were determined using full-pattern quantitative Rietveld analysis. The precipitates contained 97%, 98%, 98%, and 96% ettringite at pH 11.0, 11.5, 12.0, and 12.5, respectively. The precipitates also contained 2%–4% calcite, which is common in ettringite precipitation, as calcium reacts with atmospheric CO2 dissolved in water, forming calcite. At pH 12.5, the precipitate contained more calcite than at pH 11.5, and 12.0. This could be due to an increase in CO2 concentration in the water, as dissolution of CO2 increases with increasing pH (Fang et al., 2018). High purity ettringite was attained in the ettringite precipitation experiment in all tested pH values.
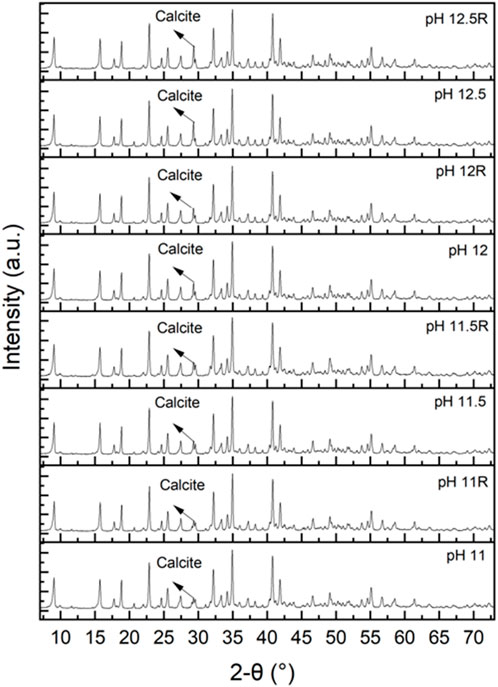
FIGURE 4. X-ray diffraction (XRD) patterns of precipitates from the ettringite precipitation experiments at pH range 11–12.5. R denotes repeated test. The unmarked peaks in the diffractograms are related to ettringite.
3.3 Arsenic removal from synthetic wastewater
Arsenic removal by ettringite precipitation was examined using the synthetic wastewater solutions with initial sulphate concentration of 2,000 ppm and arsenic concentrations of 58 and 100 ppm. Figure 5 shows the percentage of arsenic and sulphate removal from the synthetic wastewater solutions. Sulphate removal decreased with increasing the initial arsenic concentration, which indicates that arsenic was replacing sulphate in ettringite structure. Additionally, the arsenate co-precipitation during ettringite synthesis was studied by Myneni et al. Myneni et al. (1998) using Fourier transform infrared (FTIR) and Raman spectroscopy. It was suggested that
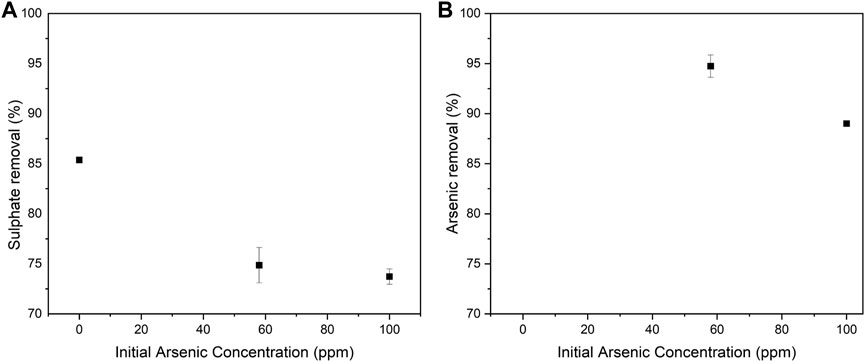
FIGURE 5. Sulphate (A) and arsenic (B) removal as a function of the initial arsenic concentration in the ettringite precipitation experiments using the synthetic wastewater solutions. Error bars represent standard deviation (n = 2).
The precipitates were analysed using ICP-OES, XRD (Figure 6) and FESEM-EDS (see Figure A2). According to XRD and Rietveld analysis, the precipitates were above 98% ettringite, and the remaining was gypsum. The peak associated with arsenic oxide (As4O6 ICDD 01-084-7622) and ettringite (ICDD 04-013-3691) were observed at 31.7° and 31.9°, respectively (Figure 6). The peak intensity at 31.7° was relatively higher when the arsenic concentration in the synthetic wastewater solution was increased from 0 to 100 ppm. This observation is in agreement with ICP-OES measurements where arsenic concentration in the precipitate increased by 0, 25, and 34 mg/g with increasing the initial arsenic concentration in synthetic wastewater solutions (0, 58, and 100 ppm), respectively.
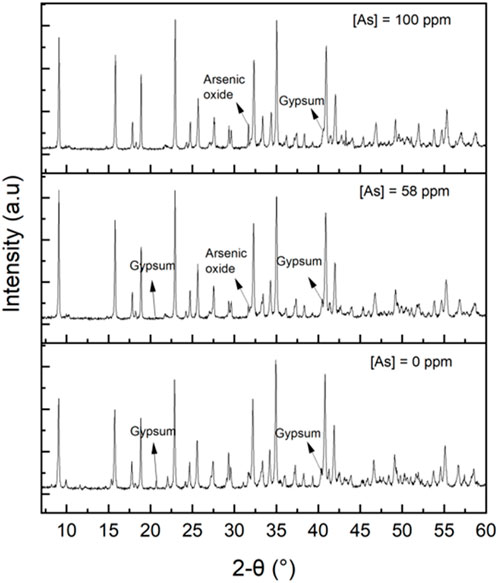
FIGURE 6. X-ray diffraction (XRD) patterns of the precipitates synthesized in the absence of arsenic, in the presence of 58 ppm arsenic, and 100 ppm arsenic.
The FESEM-EDS analysis was conducted for the precipitates from arsenic co-precipitation experiments in both small rectangle area and point analysis and the results are summarized in Table 2. The ratio of Al:S was calculated in different points/areas. The current results show that the ettringite sample precipitated in absence of arsenic pentoxide had the Al:S ratio of approximately 2:3 in all analysed points, while the ettringite samples precipitated in the presence of 58 ppm arsenic, the Al:S ratio was above 2:3 in majority of the analysed points. This indicates that the arsenate ions could have replaced some of the sulphate ions in ettringite molecular structure. However, in some analysed points, the Al:S ratio was approximately 2:3, or even lower (e.g., points number 41 and 48, and area number 51). Lower Al:S ratio could be due to the heterogeneity of the sample as the precipitate also contains gypsum. The ettringite samples precipitated in the presence of 100 ppm arsenic, had the Al:S ratio of above 2:3 in majority of the analysed points. The Al:S ratio was also higher than that of the ettringite samples precipitated in the presence of 58 ppm arsenic, indicating the higher degree of sulphate substitution by arsenate. In point number 102, the Al:S ratio was the same as the ettringite stoichiometric ratio. In point number 107 and area 109, the Al:S ratio was lower, which can be due to the presence of gypsum in the precipitate. The current XRD and FESEM-EDS results demonstrate that the arsenic is removed both as arsenic oxide, and by substitution of sulphate ions in ettringite molecular structure by arsenate.
3.4 Sulphate removal from industrial wastewater
An industrial wastewater with high initial sulphate concentration (16,000 ppm) was used for sulphate removal using ettringite precipitation. The industrial wastewater was treated with gypsum precipitation in order to decrease its sulphate concentration prior to the ettringite precipitation, as sulphate concentration limit (lower than 2,000 ppm) would be useful for ettringite precipitation. The traditional gypsum precipitation at pH 9.5 resulted in only 6.3% sulphate removal with residual sulphate concentration of 15,000 ppm. This is due to an insignificant dosage of calcium hydroxide needed to raise pH of the wastewater (initial pH 7.1 ± 0.3) to target pH 9.5, and to remove of more sulphate as gypsum. Additionally, the wastewater contained magnesium (concentration 2,500 ppm) which can disturb sulphate precipitation by keeping sulphate in the soluble form of magnesium sulphate, as shown in a previous study (Tolonen et al., 2015). Therefore, due to the fact that the sulphate concentration in the industrial wastewater was still above 2,000 ppm, a second gypsum precipitation was conducted as pre-treatment prior to the ettringite precipitation experiment. In this stage, calcium was added as calcium hydroxide in stoichiometric ratio (Ca:SO4 1:1), which led to an increase in pH to 12.9. Following this high pH gypsum precipitation, the sulphate concentration decreased by 78.0%, leading to residual sulphate concentration of 3300 ppm. At pH 12.9, magnesium precipitated both as hydroxide and carbonate. The formed precipitate contained 86.7% gypsum, 3.3% magnesium hydroxide, 2.2% magnesium carbonate and 7.8% calcium carbonate. Magnesium concentration after high pH gypsum precipitation was less than 0.1 ppm.
The ettringite precipitation experiment was conducted using ye’elimite mineral, which further decreased the sulphate concentration in industrial wastewater by 87%–450 ppm. The percentage of sulphate removal after gypsum and ettringite precipitations are shown in Figure 7. The purity of formed ettringite was 99% determined by XRD and Rietveld analysis. Properties of the sludge and the industrial wastewater after the gypsum and ettringite precipitation experiments are shown in Table 3. Formed ettringite is stable as material.
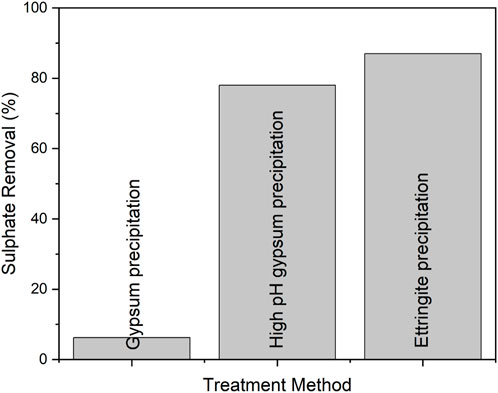
FIGURE 7. The percentage of sulphate removal from the industrial wastewater used in this study by gypsum and ettringite precipitations.

TABLE 3. Properties of the sludge and the industrial wastewater after the gypsum and ettringite precipitation experiments.
4 Conclusion and recommendations
The suitability of Ye’elimite mineral as an alternative aluminium reagent to form ettringite precipitate from sulphate and arsenic containing synthetic wastewater and industrial wastewater solutions was examined. The title study showed that sulphate removal of up to 98% from the synthetic wastewater and 87% from the industrial wastewater can be achieved using ye’elimite as the aluminium source in the ettringite precipitation. The purity of precipitated ettringite was high in both synthetic and industrial wastewaters. Additionally, up to 95% arsenic removal was achieved in arsenic co-precipitation experiments from the synthetic wastewater.
The current study demonstrated that ye’elimite mineral can be used as a novel alternative to aluminium salts for removal of sulphate and arsenic from wastewaters. Additionally, ye’elimite mineral contains calcium, which can also offer the advantage of decreasing the amount of calcium hydroxide required to be employed during the ettringite precipitation process.
In the current study, the ye’elimite dissolution process showed optimised performance when used in combination with hydrochloric acid; however, it is envisaged that ye’elimite sintering process (e.g., residence time, temperature, and cooling rate) and physical properties (e.g., particle size and morphology) can be adjusted to enhance the dissolution. Furthermore, ye’elimite can be doped with other elements, e.g., iron which can substitute aluminium in the ye’elimite structure and this may offer advantages for enhanced dissolution. For further fundamental investigations, the influence of any common ion and/or inhibition effects can be studied. Moreover, the remaining ettringite sludge can be blended and re-fired into ye’elimite to enable circularity, while the carbonation of ettringite sludge offers additional benefits (e.g., carbon capture) or other recycling routes for the ettringite sludge, in an age where resource efficiency is crucial.
The current work has shown that water treatment using cement clinker phases is possible. After all, cements are designed such that water/fluid-particle reaction processes lead to dissolution of a solid oxide and subsequent precipitation of minerals. This study has unlocked a gateway for the utilisation of cement clinker phases/minerals in water treatment, such as those in the mayenite group which can form complex solid solutions.
Data availability statement
The original contributions presented in the study are included in the article/Supplementary Material, further inquiries can be directed to the corresponding authors.
Author contributions
All authors listed have made a substantial, direct, and intellectual contribution to the work and approved it for publication.
Funding
This research was funded by K.H. Renlund Foundation. TH and MD were funded by UKRI Future Leaders Fellowship (MR/V023829/1).
Acknowledgments
The authors would like to thank Sari Tuikkanen for IC analysis and Markus Väyrynen for AAS analysis.
Conflict of interest
The authors declare that the research was conducted in the absence of any commercial or financial relationships that could be construed as a potential conflict of interest.
Publisher’s note
All claims expressed in this article are solely those of the authors and do not necessarily represent those of their affiliated organizations, or those of the publisher, the editors and the reviewers. Any product that may be evaluated in this article, or claim that may be made by its manufacturer, is not guaranteed or endorsed by the publisher.
Appendix A
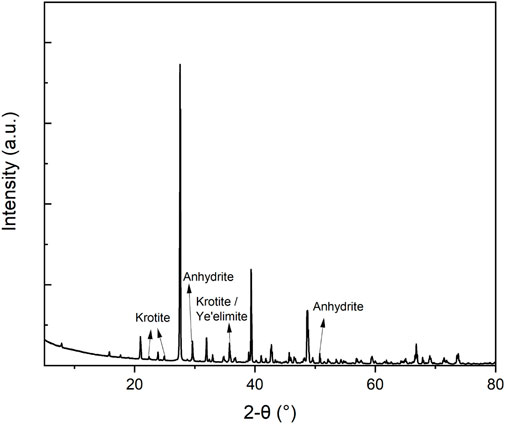
FIGURE A1. X-ray diffraction (XRD) pattern of the synthesized Ye’elimite used in this study. The unlabelled peaks refer to ye’elimite.
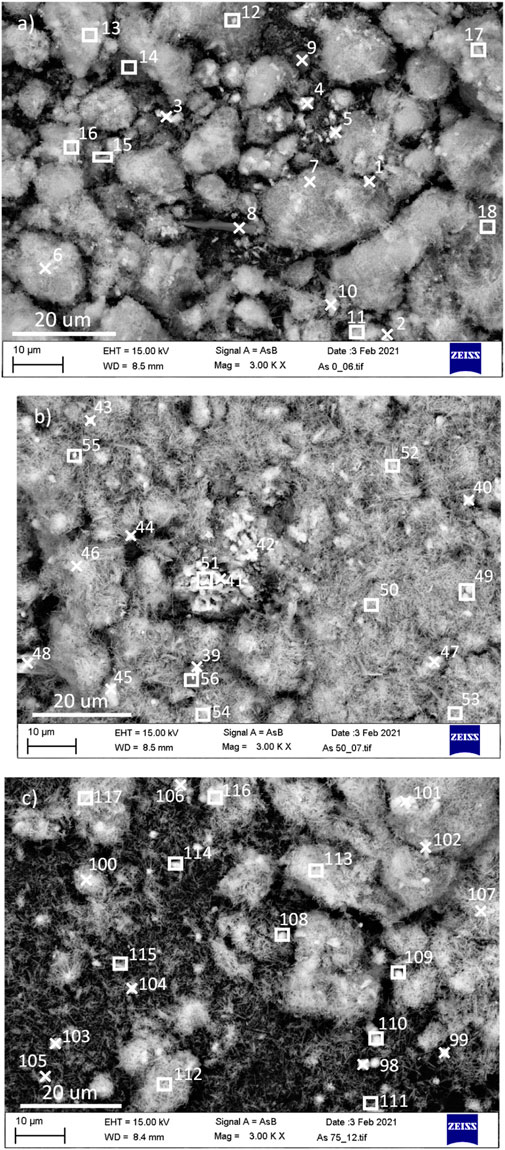
FIGURE A2. FESEM-EDS analysis of the precipitates synthesized (A) in the absence of arsenic, (B) in the presence of 58 mgL−1 arsenic, and (C) 100 mgL−1 arsenic.
References
Albino, V., Cioffi, R., Marroccoli, M., and Santoro, L. (1996). Potential application of ettringite generating systems for hazardous waste stabilization. J. Hazard. Mater. 51 (1-3), 241–252. doi:10.1016/s0304-3894(96)01828-6
Almasri, D., Mahmoud, K. A., and Abdel-Wahab, A. (2015). Two-stage sulfate removal from reject brine in inland desalination with zero-liquid discharge. Desalination 362, 52–58. doi:10.1016/j.desal.2015.02.008
Álvarez-Ayuso, E., and Nugteren, H. (2005). Synthesis of ettringite: A way to deal with the acid wastewaters of aluminium anodising industry. Water Res. 39 (1), 65–72. doi:10.1016/j.watres.2004.07.029
Ambroise, J., and Pera, J. (2004). “Immobilisation of calcium sulphate in demolition waste,” in Sustainable waste management and recycling: Construction demolition waste (London: Thomas Telford Publishing), 173–180.
Arliguie, G., and Grandet, J. (1990). A study of cement hydration in the presence of zinc: The influence of gypsum content. Cem. Concr. Res. 20 (3), 517–524. doi:10.1016/0008-8846(90)90096-g
Beltagui, H., Jen, G., Whittaker, M., and Imbabi, M. S. (2017). The influence of variable gypsum and water content on the strength and hydration of a belite-calcium sulphoaluminate cement. Adv. Appl. Ceram. 116 (4), 199–206. doi:10.1080/17436753.2017.1289722
Berardi, R., Cioffi, R., and Santoro, L. (1998). Matrix stability and leaching behaviour in ettringite-based stabilization systems doped with heavy metals. Waste Manag. 17 (8), 535–540. doi:10.1016/s0956-053x(97)10061-7
Berger, S., Cau Dit Coumes, C., Champenois, J. B., Douillard, T., Le Bescop, P., Aouad, G., et al. (2011). Stabilization of ZnCl2-containing wastes using calcium sulfoaluminate cement: Leaching behaviour of the solidified waste form, mechanisms of zinc retention. J. Hazard. Mater. 194, 268–276. doi:10.1016/j.jhazmat.2011.07.102
Berger, S., Cau Dit Coumes, C., Le Bescop, P., and Damidot, D. (2009). Hydration of calcium sulfoaluminate cement by a ZnCl2 solution: Investigation at early age. Cem. Concr. Res. 39 (12), 1180–1187. doi:10.1016/j.cemconres.2009.08.003
Boehrer, B., and Schultze, M. (2008). Stratification of lakes. Rev. Geophys. 46 (2), RG2005. doi:10.1029/2006rg000210
Champenois, J.-B., Dhoury, M., Cau Dit Coumes, C., Mercier, C., Revel, B., Le Bescop, P., et al. (2015). Influence of sodium borate on the early age hydration of calcium sulfoaluminate cement. Cem. Concr. Res. 70, 83–93. doi:10.1016/j.cemconres.2014.12.010
Champenois, J.-B., Mesbah, A., Cau Dit Coumes, C., Renaudin, G., Leroux, F., Mercier, C., et al. (2012). Crystal structures of Boro-AFm and sBoro-AFt phases. Cem. Concr. Res. 42 (10), 1362–1370. doi:10.1016/j.cemconres.2012.06.003
Chrysochoou, M., and Dermatas, D. (2006). Evaluation of ettringite and hydrocalumite formation for heavy metal immobilization: Literature review and experimental study. J. Hazard. Mater. 136 (1), 20–33. doi:10.1016/j.jhazmat.2005.11.008
Coumes, C. C. D., Courtois, S., Peysson, S., Ambroise, J., and Pera, J. (2009). Calcium sulfoaluminate cement blended with OPC: A potential binder to encapsulate low-level radioactive slurries of complex chemistry. Cem. Concr. Res. 39 (9), 740–747. doi:10.1016/j.cemconres.2009.05.016
Coumes, C. C. D., Dhoury, M., Champenois, J. B., Mercier, C., and Damidot, D. (2017). Combined effects of lithium and borate ions on the hydration of calcium sulfoaluminate cement. Cem. Concr. Res. 97, 50–60. doi:10.1016/j.cemconres.2017.03.006
Cuesta, A., De la Torre, A. G., Losilla, E. R., Peterson, V. K., Rejmak, P., Ayuela, A., et al. (2013). Structure, atomistic simulations, and phase transition of stoichiometric yeelimite. Chem. Mat. 25 (9), 1680–1687. doi:10.1021/cm400129z
Fang, P., Tang, Z. j., Chen, X. b., Huang, J. h., Tang, Z. x., and Cen, C. p. (2018). Removal of high-concentration sulfate ions from the sodium alkali FGD wastewater using ettringite precipitation method: Factor assessment, feasibility, and prospect. J. Chem. 2018, 1–8. doi:10.1155/2018/1265168
Fridrichová, M., Dvorak, K., Gazdic, D., Mokra, J., and Kulisek, K. (2016). Thermodynamic stability of ettringite formed by hydration of Ye’elimite clinker. Adv. Mater. Sci. Eng., 2016, 1–7. doi:10.1155/2016/9280131
Glasser, F. P., and Zhang, L. (2001). High-performance cement matrices based on calcium sulfoaluminate–belite compositions. Cem. Concr. Res. 31 (12), 1881–1886. doi:10.1016/s0008-8846(01)00649-4
Haha, M. B., Winnefeld, F., and Pisch, A. (2019). Advances in understanding ye'elimite-rich cements. Cem. Concr. Res. 123, 105778. doi:10.1016/j.cemconres.2019.105778
Hanein, T., Galvez-Martos, J.-L., and Bannerman, M. N. (2018). Carbon footprint of calcium sulfoaluminate clinker production. J. Clean. Prod. 172, 2278–2287. doi:10.1016/j.jclepro.2017.11.183
Hargis, C. W., Telesca, A., and Monteiro, P. J. (2014). Calcium sulfoaluminate (Ye'elimite) hydration in the presence of gypsum, calcite, and vaterite. Cem. Concr. Res. 65, 15–20. doi:10.1016/j.cemconres.2014.07.004
Hörkner, W., and Müller-Buschbaum, H. (1976). Zur kristallstruktur von CaAl2O4. J. Inorg. Nucl. Chem. 38 (5), 983–984. doi:10.1016/0022-1902(76)80011-5
Jin, Y., Lee, J., Gwak, G., Chung, C. M., Choi, J. W., Cho, K., et al. (2020). Sequential combination of nanofiltration and ettringite precipitation for managing sulfate-rich brines. Environ. Res. 187, 109693. doi:10.1016/j.envres.2020.109693
Luz, C., Pera, J., Cheriaf, M., and Rocha, J. (2007). Behaviour of calcium sulfoaluminate cement in presence of high concentrations of chromium salts. Cem. Concr. Res. 37 (4), 624–629. doi:10.1016/j.cemconres.2006.11.018
Luz, C., Rocha, J., Cheriaf, M., and Pera, J. (2006). Use of sulfoaluminate cement and bottom ash in the solidification/stabilization of galvanic sludge. J. Hazard. Mater. 136 (3), 837–845. doi:10.1016/j.jhazmat.2006.01.020
Luz, C., Rocha, J., Cheriaf, M., and Pera, J. (2009). Valorization of galvanic sludge in sulfoaluminate cement. Constr. Build. Mater. 23 (2), 595–601. doi:10.1016/j.conbuildmat.2008.04.004
Mesbah, A., Cau-dit-Coumes, C., Renaudin, G., Frizon, F., and Leroux, F. (2012). Uptake of chloride and carbonate ions by calcium monosulfoaluminate hydrate. Cem. Concr. Res. 42 (8), 1157–1165. doi:10.1016/j.cemconres.2012.05.012
Morikawa, H., Minato, I., Tomita, T., and Iwai, S. (1975). Anhydrite: A refinement. Acta Crystallogr. Sect. B 31 (8), 2164–2165. doi:10.1107/s0567740875007145
Myneni, S. C., Traina, S. J., Logan, T. J., and Waychunas, G. A. (1997). Oxyanion behavior in alkaline environments: Sorption and desorption of arsenate in ettringite. Environ. Sci. Technol. 31 (6), 1761–1768. doi:10.1021/es9607594
Myneni, S. C., Traina, S. J., Waychunas, G. A., and Logan, T. J. (1998). Vibrational spectroscopy of functional group chemistry and arsenate coordination in ettringite. Geochimica Cosmochimica Acta 62 (21-22), 3499–3514. doi:10.1016/s0016-7037(98)00221-x
Nariyan, E., Wolkersdorfer, C., and Sillanpää, M. (2018). Sulfate removal from acid mine water from the deepest active European mine by precipitation and various electrocoagulation configurations. J. Environ. Manag. 227, 162–171. doi:10.1016/j.jenvman.2018.08.095
Olmo, I. F., Chacon, E., and Irabien, A. (2001). Influence of lead, zinc, iron (III) and chromium (III) oxides on the setting time and strength development of Portland cement. Cem. Concr. Res. 31 (8), 1213–1219. doi:10.1016/s0008-8846(01)00545-2
Peysson, S., Péra, J., and Chabannet, M. (2005). Immobilization of heavy metals by calcium sulfoaluminate cement. Cem. Concr. Res. 35 (12), 2261–2270. doi:10.1016/j.cemconres.2005.03.015
Qian, G., Shi, J., Cao, Y., Xu, Y., and Chui, P. (2008). Properties of MSW fly ash–calcium sulfoaluminate cement matrix and stabilization/solidification on heavy metals. J. Hazard. Mater. 152 (1), 196–203. doi:10.1016/j.jhazmat.2007.06.118
Reinsel, M. A. “A new process for sulfate removal from industrial waters,” in Proceedings National Meeting of American Society for Surface Mining and Reclamation, Scottadale, Arizona, 1999.
Runtti, H., Tolonen, E. T., Tuomikoski, S., Luukkonen, T., and Lassi, U. (2018). How to tackle the stringent sulfate removal requirements in mine water treatment—a review of potential methods. Environ. Res. 167, 207–222. doi:10.1016/j.envres.2018.07.018
Sapsford, D. J., and Tufvesson, S. (2017). Properties of recycled sludge formed from different aluminiferous reagents during the ettringite process. J. Water Process Eng. 19, 305–311. doi:10.1016/j.jwpe.2017.08.016
Segundo, I. D. B., Silva, T. F., Moreira, F. C., Silva, G. V., Boaventura, R. A., and Vilar, V. J. (2019). Sulphur compounds removal from an industrial landfill leachate by catalytic oxidation and chemical precipitation: From a hazardous effluent to a value-added product. Sci. Total Environ. 655, 1249–1260. doi:10.1016/j.scitotenv.2018.11.274
Sun, Q., Li, J., and Wang, J. (2011). Solidification of borate radioactive resins using sulfoaluminate cement blending with zeolite. Nucl. Eng. Des. 241 (12), 5308–5315. doi:10.1016/j.nucengdes.2011.08.028
Tian, X., Zhou, Z., Xin, Y., Jiang, L. M., Zhao, X., and An, Y. (2019). A novel sulfate removal process by ettringite precipitation with aluminum recovery: Kinetics and a pilot-scale study. J. Hazard. Mater. 365, 572–580. doi:10.1016/j.jhazmat.2018.11.032
Tolonen, E.-T., Hu, T., Ramo, J., and Lassi, U. (2016). The removal of sulphate from mine water by precipitation as ettringite and the utilisation of the precipitate as a sorbent for arsenate removal. J. Environ. Manag. 181, 856–862. doi:10.1016/j.jenvman.2016.06.053
Tolonen, E.-T., Rämö, J., and Lassi, U. (2015). The effect of magnesium on partial sulphate removal from mine water as gypsum. J. Environ. Manag. 159, 143–146. doi:10.1016/j.jenvman.2015.05.009
Weeks, C., Hand, R. J., and Sharp, J. H. (2008). Retardation of cement hydration caused by heavy metals present in ISF slag used as aggregate. Cem. Concr. Compos. 30 (10), 970–978. doi:10.1016/j.cemconcomp.2008.07.005
Winnefeld, F., and Lothenbach, B. (2010). Hydration of calcium sulfoaluminate cements—experimental findings and thermodynamic modelling. Cem. Concr. Res. 40 (8), 1239–1247. doi:10.1016/j.cemconres.2009.08.014
Wu, K., Shi, H., and Guo, X. (2011). Utilization of municipal solid waste incineration fly ash for sulfoaluminate cement clinker production. Waste Manag. 31 (9-10), 2001–2008. doi:10.1016/j.wasman.2011.04.022
Zhang, M., and Reardon, E. J. (2003). Removal of B, Cr, Mo, and Se from wastewater by incorporation into hydrocalumite and ettringite. Environ. Sci. Technol. 37 (13), 2947–2952. doi:10.1021/es020969i
Keywords: ye’elimite, calcium sulfoaluminate, ettringite precipitation, sulphate removal, arsenic removal, industrial wastewater treatment
Citation: Nurmesniemi E-T, Huhta M, Derkani M, Isteri V, Hanein T, Hu T, Tanskanen P and Lassi U (2022) Removal of sulphate and arsenic from wastewater using calcium sulfoaluminate (ye’elimite). Front. Mater. 9:943486. doi: 10.3389/fmats.2022.943486
Received: 13 May 2022; Accepted: 24 August 2022;
Published: 13 September 2022.
Edited by:
Tongfei Tian, University of the Sunshine Coast, AustraliaReviewed by:
Piyush Chaunsali, Indian Institute of Technology Madras, IndiaShengwen Tang, Wuhan University, China
Copyright © 2022 Nurmesniemi, Huhta, Derkani, Isteri, Hanein, Hu, Tanskanen and Lassi. This is an open-access article distributed under the terms of the Creative Commons Attribution License (CC BY). The use, distribution or reproduction in other forums is permitted, provided the original author(s) and the copyright owner(s) are credited and that the original publication in this journal is cited, in accordance with accepted academic practice. No use, distribution or reproduction is permitted which does not comply with these terms.
*Correspondence: Visa Isteri, dmlzYS5Jc3RlcmlAb3VsdS5maQ==; Theodore Hanein, dC5oYW5laW5Ac2hlZmZpZWxkLmFjLnVr