- 1Engineering Materials and Structures (eMast) ikohza, Malaysia–Japan International Institute of Technology (MJIIT), Universiti Teknologi Malaysia, Kuala Lumpur, Malaysia
- 2Faculty of Mechanical and Manufacturing, Universiti Tun Hussein Onn Malaysia, Parit Raja, Malaysia
- 3Mechanical Engineering Department, Universitas Sebelas Maret, Sukarta, Indonesia
- 4Faculty of Applied Sciences, Universiti Teknologi MARA (UiTM), Cawangan Pahang, Kampus Jengka, Pahang, Malaysia
Magnetorheological (MR) foam is a newly developed porous smart material that is able to change its properties continuously, actively, and reversibly in response to controllable external magnetic stimuli. Unfortunately, the stiffness or also known as storage modulus of MR foam is still rather low and insufficient, in the range of below 100 kPa only, due to weak interparticle interaction between CIPs and the foam matrix, which consequently restricts the potential of MR foam to be used in future sensor applications or in other semi-active devices. Therefore, the aim of this research is to enhance the structural and storage modulus of MR foam by adding silica nanoparticles as an additive. Consequently, MR foam samples with different compositions of silica nanoparticles in the range of 0–5 wt% were prepared via an in situ method. The rheological properties were tested under an oscillatory shear mode with the absence and presence of magnetic fields using a rheometer, with the input parameters of strains between 0.001% and 10% and range of magnetic flux density between 0 and 0.73 T for a magnetic field sweep test. The rheological findings show that with the addition of silica nanoparticles, particularly at 4 wt%, have enhanced the storage modulus of MR foam by 260%, which attributed to the highest stiffness from 45 to 162 kPa. Meanwhile, the change of storage modulus under the influence of magnetic fields (0 T–0.73 T) somehow showed small increment, about ∆1 kPa for each concentration of silica nanoparticles in MR foams, due to non-magnetic behavior of silica. The morphological characteristics of MR foams were described by an elemental analysis carried out by a using variable pressure scanning electron microscope (VPSEM) equipped with energy dispersive x-ray spectroscopy (EDX). The micrographs demonstrated large open-cell pores for MR foam, while MR foam with silica nanoparticles exhibited more closed-cell pores, associated with the enhancement of its storage modulus. It indicates that the silica nanoparticles have encouraged well dispersion of the particles in the foam matrix, which improved and strengthened the microstructure of MR foams through formation of silane coupling bonds of silica in the filler-matrix structure. Overall, incorporation of silica nanoparticles as an additive in the MR foam could provide advantage in enhancing the structure and mechanical properties of MR foam, for various future smart devices.
1 Introduction
Nowadays, the progression of advance technologies such as soft robotics, soft grippers, soft actuators, and sensor devices have been developing, which leads to the innovation of advance materials that can be stimulated rapidly and sensitively under the influence of external stimuli. Since the last decade, magnetorheological (MR) foam has emerged as a newly developed smart soft solid material that can change its behavior continuously, actively, and reversibly under the influence of a magnetic field (Gong et al., 2013). It is attributed to the embedded magnetic particles in the foam as a matrix phase. In comparison with other MR solid material, such as MR elastomer (Umehara et al., 2018), MR foam has a unique porous and cellular structure that forms chemically by trapping gases in the liquid phase during the foaming process (Cain et al., 2013). Its porous structure has not only entitled the material to be low in density and physically lightweight (Davino et al., 2012) but also contributes to a great cushioning effect to absorb vibrations and shock impact (Linde et al., 1972). In fact, embedding magnetic particles in the structure of foam has emphasized the material to be evolved from a rigid system to a controllable one as MR foam has responded well to the tunable magnetic field stimuli (Schümann et al., 2015). In recent years, one of the challenging problems which arises in this domain application has been mentioned by Yin et al. (2017), who stated that soft robotic grippers are always lacking in variable stiffness and thus limits the function of the gripper to be adjustable into desired stiffness according to the operational object. Therefore, the indicated features of MR foam have been intriguing and growing appeals among researchers as its flexibility and controllable stiffness corresponding to the applied magnetic fields would result in its potential for future soft robotic gripper material. The improvement is also in line with the development of material’s technology in which researchers attempt to provide an adjustable material for soft robotic grippers (Zaidi et al., 2021), since the improvement of finger-like operating mechanism is crucial to move and handle various objects conveniently during the operations (Meng et al., 2020).
In order to address more potential applications of MR foam, researchers have examined the rheological properties of the material in terms of capability to store more energy upon applied shear stress before fracture. In addition, the enhancement of the storage modulus of MR foam has become a significant concern in order to broader its stiffness range for various purposes (Muhazeli et al., 2020). Theoretically, the storage modulus, G′, is a term for the amount of energy stored in a viscoelastic material before distorting, which refers to the stiffness of the material (Boczkowska et al., 2012; Zhang et al., 2019). There are several methods introduced to enhance the properties of MR foam, including storage modulus for wider spectrum of technology advancement such as increasing CIP’s content (Muhazeli et al., 2019), using particles coating (Scarpa and Smith, 2004), dual-matrix method (Ge et al., 2015), and incorporating additives into MR materials (Saiz-Arroyo et al., 2011). Previous studies have stated that by reinforcing higher composition of magnetic filler (CIPs) into the MR foam, the magnetic responsiveness of the MR foam could be enhanced as a result of the increased magnetic saturation of the material. In addition, under the influence of magnetic field excitations, MR foam has broaden its range of storage modulus from a low to higher level, making it suitable to be potential components in soft robotics sensor technology (Rizuan et al., 2021). Unfortunately, the reported storage modulus of MR foam thus far is insufficient, since the application of soft robotic material requires stiffness of more than 100 kPa (Zaidi et al., 2021). For example, in the previous study carried out by Gong et al. (2013), a flexible MR foam with 60 wt% of CIPs exhibited the storage modulus up to 72 kPa. Meanwhile, Rizuan et al., 2021 incorporated more CIPs of about 75 wt% in the MR foam, which enhanced the storage modulus up to 75 kPa, by about 3% increment only. These findings in return have restricted the potential of MR foam to be used in stated applications or in other semi-active devices. It is noted that the ability to store energy is a key aspect for the elastic materials to sustain greater applied stress elastically, especially under different magnetic field values and dynamic frequencies (Scarpa and Smith, 2004). Therefore, improvement in the storage modulus of the MR foam has become a significant concern in order to enhance the strength of the material upon deformation for the MR foam to become more advantageous and widen its potential for various purposes.
On the other hand, introducing additives into MR solid materials has become a more practical approach in providing significant enhancement toward the corresponding properties, with simpler procedure and a cost effective approach (Tamaddoni moghaddam and Naimi-Jamal, 2017; Zainudin et al., 2020). In fact, incorporating additives into MR elastomers (MRE) include, but not limited to, graphite (Li et al., 2009; Tian et al., 2011; Shabdin et al., 2019), cobalt ferrite (Aziz et al., 2019), carbon nanotubes (CNTs) (Kumar and Lee, 2019), and silica (Abd Rashid et al., 2021), and the additives have been proven to result in the enhancement toward specific properties of the material. These additives have their own roles and purposes to enhance some properties of MRE such as conductivity, MR effect, and magnetic interaction depending on the amount and type of additives that were being incorporated (Ahmad Khairi et al., 2019). In 2009, Li et al. introduced 25 wt% of graphite into the mixture of 55 wt% CIPs and 20 wt% silicon rubber (MRE), and it was observed that the graphite has increased the conductivity of MRE as well as reduced its resistance by more than 85% (Li et al., 2009). Meanwhile, a study by Tian et al. who stated that the addition of 23.81% micron-sized graphite particles in the MRE has increased the storage modulus up to 1 MPa, particularly under the influence of 400 mT of the applied magnetic field as compared to the sample without additive (Tian et al., 2011). Nevertheless, Shabdin et al. added 20 g of graphite into the mixture of 12.5 g of CIPs, 22.5 g of silicon rubber, and 5 g of silicon oil, and the result showed that the MR effect of the MRE was increased by about 3% as compared to the non-additive sample (Shabdin et al., 2019). However, the composition of CIPs and addition of graphite as an additive need to be controlled as adding more would lead to brittleness of MRE, which would accelerate the deformation of the material (Zainudin et al., 2020). On the other hand, Aziz et al. introduced Ni–Mg–cobalt ferrite nanoparticles, with an average size of 35–80 nm into an MRE, and the result revealed that the MRE with Ni–Mg–cobalt ferrite nanoparticles exhibited 43% higher storage modulus as compared to the MRE without the additive (Aziz et al., 2019). However, cobalt ferrite nanoparticle have been stated to induce extreme toxicity to human and biological systems that may cause cell death and DNA damage. Thus, the used of cobalt ferrite–based additives have been restricted for wider applications. Meanwhile, CNT, which is known to possess high elastic and strong bond due to its multi-layer nature, has been used in MRE generally to enhance the storage modulus and lower the loss factor of the MRE (Eatemadi et al., 2014). Similarly, Kong et al. have proven that a significant increment in the storage modulus of MRE, particularly from 600 to 1200 kPa, has been achieved by the MRE with the rising percentage of the CNT from 1 to 6 wt% added into the composite, respectively (Kong et al., 2018). Unfortunately, CNTs involve a very complex synthesis process that is highly toxic to human body and environment (Eatemadi et al., 2014).
Nevertheless, silica nanoparticles are commonly used as an additive to enhance material’s properties due to its non-toxic property, significantly low density, simpler fabrication process, great nucleating agent for crystallinity growth, and high thermal stability (Anuar et al., 2018; Khaidir et al., 2020). Abd Rashid et al., 2021 studied the addition of silica nanoparticles in the range of 0 per hundred rubber (phr) to 20 phr in the ethylene propylene diene monomer (EPDM)–based MRE, and the MRE showed good interfacial bonding between the filler and matrix phases; in addition, it led to the improvement of particle’s dispersion. As a result, the initial storage modulus of the MRE was observed to be increased from 0.29 to 0.45 MPa with the addition of silica nanoparticles from 0 to 11 wt%, respectively, as the adhesiveness of silica has improved the interactions between the CIPs and the EPDM matrix (Abd Rashid et al., 2021). It is notable as well that the increment in the rheological properties of MRE was parallel with the enhancement of the tensile strength and elongation break of the MRE. Specifically, the enhancement in tensile strength of the MRE was stated by about 20%, from 52 to 62 shore A with the silica content added from 0 to 11 wt% (Abd Rashid et al., 2021).
On the other hand, the used of nanosized particles have also given advantages for it to be used in polymer composite to improve hardness, mechanical stiffness, and thermal stability (Anuar et al., 2018; Khaidir R. E. et al., 2019, Khaidir et al., 2019 R., 2020). This is because the nanoparticles have a relatively high surface area attributed to the nanoscale dimensions; hence, the nanoparticles can mix well with the polymer chains at the molecular level and improve mechanical and thermal properties (Saha et al., 2008). Furthermore, the nanosized particles can fill the voids between the micron-sized CIPs and thus offer higher MR effect as a result of enhance stiffness or storage modulus of the MR material (Bastola and Hossain, 2020). For example, Nikje and Tehrani, 2010 showed a great improvement in elastic modulus of rigid polyurethane (PU) foam from 3.7 MPa to 6.3 MPa after 1 wt% of n-(2-aminoethyl)-3-aminopropyltrimethoxy-silane (AEAP)-silica nanoparticles was added into the PU foam. Meanwhile, Saiz-Arroyo et al. stated that the silica nanoparticles has the ability to disperse well in the polymer matrices (Saiz-Arroyo et al., 2011). In fact, by adding silica content from 0 to 3 wt% in the low-density polyethylene (LDPE) foam, the elastic modulus of the composite foam could be enhanced by 51% (Saiz-Arroyo et al., 2011). These studies somehow show the ability of silica nanoparticles that act as additive to enhance the storage modulus of a polymer-based material. However, there has been no study related to the used of silica nanoparticles to enhance properties of the MR foam, particularly at low stiffness of the material. Therefore, a new fabrication sample of MR foams with the addition of silica nanoparticles as additive will be introduced with the range of silica nanoparticles from 1 to 5 wt%, in order to enhance the storage modulus as well as other rheological properties of the MR foam. It is expected that the addition of silica nanoparticles could result in the enhancement of the filler–matrix interactions in the MR foam which, simultaneously correspond to the improvement in the foam’s properties physically, mechanically, and rheologically. Consequently, with enhanced stiffness of the MR foam with the addition of silica nanoparticles has the ability to store more energy; thus, it could grasp and move the object more securely as compared to the low stiffness of the MR foam.
2 Experimental method
2.1 Sample preparation
Figure 1 shows the synthesis process of flexible MR foam samples that were prepared by the in situ polymerization method. The two main components needed to produce the polyurethane foam are polyol and isocyanates that acted as a chemical reactant and agent, respectively. In particular, polyether polyols (PPG)–based triol with a molecular weight of 6000 g/mol and the density of 1.03 g/ml together with the 4,4′-methylene bis(phenyl isocyanate) benzene that has the density of 1.00 g/ml were purchased from Smooth-On. Inc., United States. Meanwhile, the reinforced magnetic particles were carbonyl iron particles (CIPs) that was purchased from CK Materials Lab Co. Ltd., Seoul, Korea. It was an OM-typed with an average size of 3–5 μm and exhibited the density of 4.5 g/cm3. As for the additive silica nanoparticles (SiO2), it was derived from rice husk via using the solid state method, having the average size of 700 nm and was collaboratively received from UTHM, Johor.
The MR foam was prepared by mixing the fixed concentration of CIPs, 75wt%, into the total weight of main components of foam, polyols, and isocyanates (20 g). Upon the in situ fabrication of MR foam, the CIPs was added into the 50wt% of polyols, which was about 10 g, and it was stirred at a speed of 550 rpm for about 30 s by using a Multimix High Speed Dispersed (HSD) mechanical stirrer in order to ensure well mixing of the mixture. Then another 50 wt% of isocyanates (10 g) was poured into the mixture of polyols and CIPs, and it was continuously stirred for another 20 s. Then the final mixture of the materials was immediately poured into a cylindrical open tube as a mold, and the foaming process of MR foam took place taking the shape of the mold. The mold was prepared with a dimension of 20 mm in diameter and 15 cm in thickness. Prior to the addition of silica nanoparticles to the MR foam, the additive varied from 0 to 5 wt% respective to the total of MR foam. Thus, the calculation for each material was carried out, as shown in Table 1.
In order to prepare MR foams with silica nanoparticles, the additive was firstly grounded with CIPs using a mortar and pestle to ensure the homogeneous mixing of the particles, as illustrated in Figure 1. Then the solid mixture of the particles was poured into the polyols (10 g) and was stirred for about 30 s, at a speed of 550 rpm. The isocyanates with the amount of 10 g was then added to the mixture, stirred for another 20 s, and the final mixture was immediately poured into the cylindrical mold as the foaming process would take place shortly. The foaming process would occur vigorously and the samples would solidify instantly. All samples were left for 24 h at room temperature of 25 °C to ensure that the samples were fully hardened before the samples were being cut for testing and characterization procedures.
2.2 Sample characterization and rheological testing
The rheological properties of MR foams were analyzed and evaluated by using a MCR302 modular compact rheometer (MCR) from Anton Paar, Germany. The rheometer was equipped with a controllable parallel plate (PP20/MRD/T1/P2) that has a patented Toolmaster™ technology with a diameter of 20 mm and a constant 1 mm gap setup measured by Trugap™ feature that recognizes the real measuring gap. In this current work, MR foams underwent an oscillatory shear mode test to investigate the effect of different concentrations of silica nanoparticles to the viscoelastic properties of the MR foam, especially in terms of storage modulus and the MR effect. The variation of the final properties of MR foams would be further analyzed by varying input parameters of 0.001%–10% sweep strains, with different constant current input from 0 A to 4 A and constant 1 Hz frequency to evaluate the elasticity and deformation value of the MR foam through the determination of the linear viscoelastic (LVE) range. The current input of 0 A, 1 A, 2 A, 3 A, and 4 A are approximately equivalent to 0 T, 0.17 T, 0.35 T, 0.53 T, and 0.73 T, respectively. The magnetic flux density, B (T) were manipulated during current sweep test or also known as the magnetic field–dependent test to analyze the absolute MR effect of the MR foam with different composition of silica nanoparticles. Upon the rheological test, each sample was cut into 1-mm-thick and 20-mm-diameter sections. All samples were tested under room temperature and each of the samples was tested with 30 interval points for every measurement.
Nevertheless, the morphological characteristics of MR foams were observed through variable pressure scanning electron microscopy (VPSEM), by using the JSM-IT300LV model from JEOL Ltd, Tokyo, Japan. VPSEM provided a high resolution of 3.0 nm at 30 kV and unsurpassed low kV performance; thus, it has the ability to identify fine pore images of the MR foam. In this work, the MR foam samples were cut into 1-mm thickness with a diameter of 20 mm each and primarily coated with platinum using the sputter coating method before being analyzed under VPSEM. The SEM micrograph were characterized on the cross-sectional part to observe the pores and strut structures of the MR foam. Notably, the images were taken under ×50 to × 2000 magnifications, and all testing were carried out at room temperature of 25 °C. Equipped with the energy dispersive X-ray spectroscopy (EDX) in the VPSEM, the EDX would provide mapping information on the element compositions in MR foams.
3 Results and discussion
3.1 Storage modulus of MR foams
3.1.1 Strain dependent test
A strain sweep test was conducted under the oscillatory shear mode with a controlled range of shear strains from 0.001% to 10% and a fixed frequency of 1 Hz. In this research, the effect of silica as an additive toward the improvement of storage modulus of MR foams was mainly observed, and the change in the linear viscoelastic (LVE) region of MR foams were determined. The LVE region gives rigidity information of the MR material by indicating the range which the material could withstand, given shear strain before the structure begin to deform permanently (Kang et al., 2020). Moreover, it is crucial to determine the limit value of the LVE region in order to ensure that further testing including frequency sweep and magnetic field sweep can be performed within specified strain without destroying the sample. As for solid-based materials, it does not flow; thus, the stiffness or storage modulus, G′, would be considered to describe the elasticity of the material rather than its viscosity. Therefore, as shown in Figure 2, the storage modulus, G′, of MR foams with the addition of silica in different concentrations were plotted, corresponding to the applied shear strains and with respective to the off-state and on-state conditions.
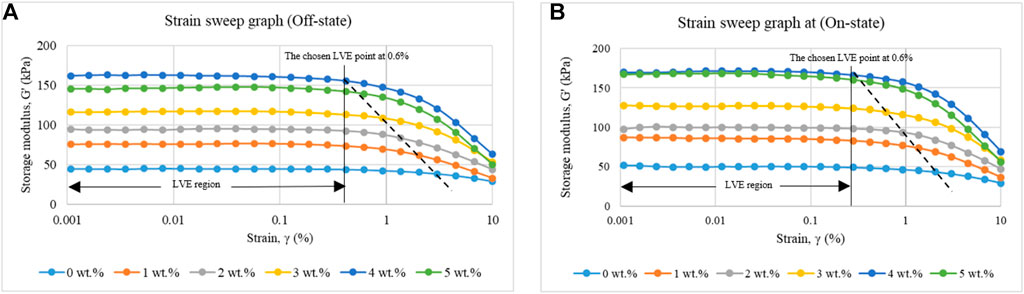
FIGURE 2. Change of storage modulus of MR foams with different concentrations of silica nanoparticles during (A) off-state (0 T) and (B) on-state (0.73 T) conditions.
In particular, Figure 2 presents the changed in the storage modulus of MR foams that have been embedded with silica nanoparticles as an additive, in the range of 0–5 wt% concentrations. The samples were tested under different applied magnetic flux density of 0 T (off-state) and 0.73 T (on-state). It can be seen that all samples showed constant storage modulus, G′, along with the increasing applied strains, especially from 0.001% to 0.1%. This shows that the elastic region of the overall samples was in the stated range, where the structure would be returned to its original position even after the removal of applied strains. Thus, the graphs show no change in the value of the storage modulus (linear). However, it was observed that the graphs started to show its downturn after the strains were increased more than 0.6%. This phenomenon corresponded to the deformation phase of MR foams caused by the applied strain beyond its elastic limit of the samples. In the deformation phase, the samples would continue being stretched but was unable to return to its original position, indicating the transition of the samples from elastic to plastic deformation. Hence, it explained the drop values of storage modulus, G′, as lesser energy can be stored by the samples upon further deformation of the samples.
Overall, the LVE region of MR foam samples would be determined by using the Agire-Olabide’s method where the point deviates by at least 10% after the downturn slope (Yunus et al., 2019). The slanting lines (dash lines) were drawn on the graphs indicating the drop point of the LVE limit for each MR foam, especially with different concentration of silica nanoparticles from 1 to 5 wt%. Based on the graphs, it was observed that the LVE regions have started to reduce when silica nanoparticles were added to the MR foam samples. In fact, during the off-state condition, the pure MR foam exhibited the lowest storage modulus but a slightly longer LVE region, between 0.001% and 3.03% of applied strains. Then when silica nanoparticles were added to MR foams up to 5 wt%, the storage modulus increased regularly but a shorter range of LVE regions were noted correspondingly. For instance, the MR foam with 4 wt% of silica nanoparticles presented the highest storage modulus, but in return, the LVE region become shorter, in between 0.001% and 0.62% particularly at the off-state condition. In addition, all MR foams at the on-state condition exhibited further shorter LVE regions as compared to the ones at the off-state conditions, as shown in Figure 2B. The shorter LVE regions indicated that the samples have become stiffer with the addition of silica nanoparticles and even stiffer under the influence of a magnetic field (on-state condition). A similar trend has been reported by Abdul Rashid et al., who stated that MRE samples with the addition of silica nanoparticles as an additive possessed shorter LVE region as compared to the MRE without silica (Abd Rashid et al., 2021). These results implied that the LVE limit of MR foams are dependent on the concentration of silica nanoparticles in the matrix phase. In fact, it is a common phenomenon in a polymer composite as the addition of filler particles or additives in the polymer matrix would lead to the deterioration of the material’s structure as the shorter elastic region would be acquired, known as the Payne effect (Mohd Nasir et al., 2021). Thus, it explained the shorter LVE region of MR foams with higher concentrations of silica nanoparticles. Nevertheless, based on the finding of the LVE region for all MR foams, the selected constant strain value for other testing procedure is about 0.6% to ensure that all testing samples were in the LVE region; hence, the testing samples were still in the elastic region.
Generally, the viscoelastic materials that are subjected to shear stress would be undergo shear deformation. When the shear stress has exerted onto the material, some amount of energy would be stored and can be retrieved after each cycle. Meanwhile, the rest of the energy would be dissipated as heat and could not be retrieved. Hence, the stored energy in the material is referred as stiffness and also known as storage modulus, G′, the amount of energy could be stored by the material upon deformation. Based on the graphs in Figure 2A, it shows that the addition of silica nanoparticles has caused increment in the storage modulus of MR foams, particularly at the off-state condition from 1 to 4 wt%. The values were then increased slightly at the on-state condition when 0.73 T was applied to all the samples, indicating the stiffer MR foams and more energy could be stored by the samples elastically. In fact, Table 2 summarizes the values of storage modulus of MR foams with different concentrations of silica nanoparticles, and at both conditions of off-state and on-states, respectively. It can be observed that at 0 wt% of silica nanoparticles, the storage modulus of MR foam was noted around 45 kPa, particularly at zero magnetic field. This value has been very slightly increased when the magnetic flux density was applied to the MR foam from 0.17 T to 0.73 T. The increment values were noted to be around 1–4 kPa only and this finding is in a good agreement with the study stated by Rizuan et al., 2021 in which the storage modulus, G’ of MR foam increased slightly, around 1 kPa–5 kPa when the magnetic field was between 0.0 T and 0.73 T. In comparing with the off-state condition, the CIPs are distributed randomly in the polymer matrix of PU foam in the absence of the magnetic field causing the low initial storage modulus values (Li et al., 2020b). Meanwhile, with the presence of the magnetic field, the result showed the increment in the storage modulus of MR foam during the on-state condition which was attributed to the enhancement in the interparticle magnetic forces between the CIPs, as toward the applied magnetic field simultaneously. Nevertheless, by comparing MRE to MR foam, the slight increment in the storage modulus of MR foams is due to the porous structure of foam itself, where the CIPs were embedded in the struts of foam and were separated by the pores, causing the CIPs are quite farther between the pores. When the magnetic field was induced to the MR foam, CIPs would tend to attract to one another in the strut walls thus slightly increased the storage modulus of MR foams. Meanwhile in an MRE, the CIPs are distributed in a smaller area of the rubber matrix and no foaming process occurred in an MRE during curing thus, interparticle of CIPs are much closer resulted in stronger magnetic forces between the particles when the magnetic field was applied, thus explaining the greater storage modulus increment as compared to MR foams. The similar trend was observed for other MR foams that were incorporated with different concentrations of silica nanoparticles.
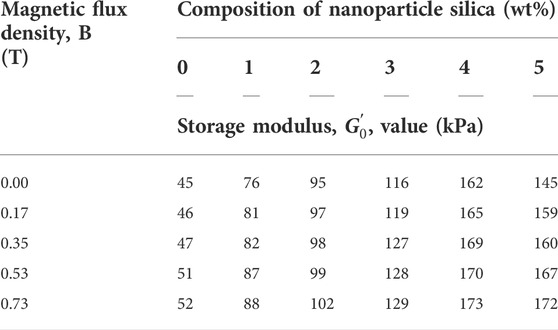
TABLE 2. | Initial storage modulus,
In contrast, when 1 wt% of silica nanoparticles were added to the MR foam, the corresponding storage modulus has been significantly increased from 45 to 76 kPa, at the off-state condition. Despite at zero magnetic field influence, the increment in the storage modulus of MR foams have continued to enhance to 95 kPa, 116 kPa and 162 kPa for silica nanoparticles of 2, 3 and 4 wt%, respectively. In MR foam, silica nano-particles would act as a cross-linker and not as a chain extender, in which silica nano-particles would strengthen the matrix-fillers interaction by cross-linking interactions. This would increase the interfacial bonding between the filler and polymer matrix that subsequently enhanced the modulus of MR foams. There has been a study conducted by Burgaz and Kendirlioglu (2019) regarding the interactions between the PU foam and silica nanoparticles. The study stated that the silica possessed the hydrophilic behavior in which it encourages the silanol functional groups of silica to have a bond via H-bonding interactions with ether oxygens of polyol, or also known as the silane coupling agent (Burgaz and Kendirlioglu, 2019). Since silica used was in nanosized particles, it has a larger surface area, which provides a better dispersion in the polymer matrix thus creating more silane coupling agents in the matrix phase (Nikje et al., 2009). The silane coupling agents that are presented in the MR foam would hinder the relaxation of mobility of particles in the polymer segment thus, making the particles difficult to move (Nikje et al., 2009). This has explained the stiffer progression of MR foams with the addition of silica nanoparticles as compared to the one without silica. Nevertheless, at the on-state conditions 0.17–0.73 T that were applied to the MR foam, the storage modulus somehow showed a slight increment, particularly in the range 1–5 kPa indicating the non-magnetic behavior of silica nanoparticles to respond to the applied magnetic fields. Therefore, the increment in the storage modulus of MR foams is due to the CIP’s responsiveness toward the increasing values of magnetic field strength. As magnetic polarization of CIPs in MR foams become stronger with magnetic fields, the respective chain-like structures of MR foam enhanced thus explaining the increased value of storage modulus (Chuah et al., 2015).
Nevertheless, it was observed that when the concentration of silica nanoparticles was added up to 5 wt%, the storage modulus was noted lower than the 4 wt% of silica nanoparticles in the MR foam. In fact, the value of storage modulus has dropped from 162 kPa (4 wt%) to 145 kPa (5 wt%), particularly at the off-state condition. This finding might be due to the agglomeration of silica nanoparticles in the polymer matrix when silica was added excessively. Generally, silica is known as an inorganic material that act as a nucleating agent for the polymer-matrix materials that at every addition or increasing its composition, it increases the crystallinity of the polymer composite via the interparticle connection that build between the silica particles and matrix polymer by silane coupling agent (Saiz-Arroyo et al., 2011). Hence, when excessive silica nanoparticles were added, the crystallinity of the material increased which might lead to the formation of particle’s aggregation in the foam matrix phase. This resulted in the imbalance distribution of silica nanoparticles that affected the dimensional stability of foam’s cellular structure and finally caused reverse effect of stiffness enhancement in the MR foam. Therefore, the storage modulus of MR foam with 5 wt% silica nanoparticles has decreased indicating the excessiveness of the additive added more than 4 wt%. Somehow, at presence of magnetic fields (on-state condition), the storage modulus with 5 wt% silica nanoparticles still increased slightly attributed to the CIPs that responded to the applied magnetic field, as discussed in previous paragraph.
3.1.2 Magnetic field–dependent test
The magnetic field–dependent test of MR foams with different composition of silica nanoparticles was conducted under the fixed strain of 0.6% and a constant frequency of 1 Hz. The chosen strain of 0.6% lies under the LVE region in which the amount of given strain is within the range of elastic limit. Correspondingly, the absolute MR effect were extracted and presented, as shown in Figure 3.
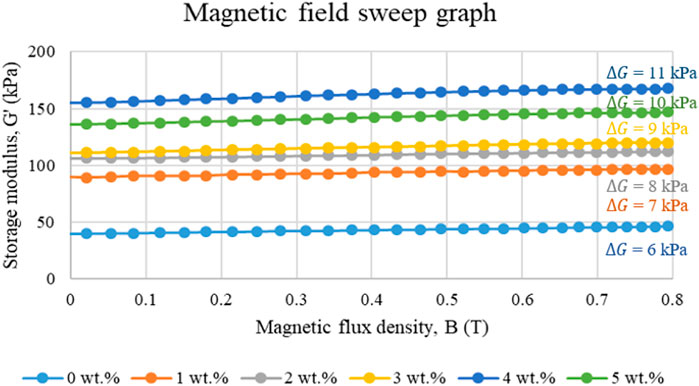
FIGURE 3. Change of storage modulus, G′, of MR foams with different composition of silica nanoparticles under the influence of different magnetic flux density, B.
Figure 3 shows the relationship between the storage modulus, G′ of MR foams with different compositions of silica nanoparticles under the influence of different magnetic flux density, B. Overall, it could be observed that as the magnetic flux density increased, the storage modulus of MR foams increased, up to 0.8 T. The increment of the storage modulus of all MR foams are due to the responsiveness of the CIPs in the foam’s structure toward the applied magnetic fields that subsequently caused changes in the stiffness of the material, reversibly and continuously, and it is also known as MR effect (Plachy et al., 2018; Li et al., 2021). The MR effect analysis is one of the important resultant parameters to measure the responsiveness of MR foams in terms of the changeable storage modulus under the influence of applied magnetic fields, and the output would be advantageous for the material to be applied in controllable actuator and soft robotic sensors (Kang et al., 2020). The change in the behaviors of MR foam under the influence of magnetic stimuli can be expressed by the absolute MR effect. The absolute MR effect,
where
In particular, the initial storage modulus of MR foam without the silica nanoparticles is about 40 kPa and the value was increased slightly to 46 kPa when the magnetic flux density was applied at 0.8 T. Hence, the difference or absolute MR effect of the MR foam was about 6 kPa. This finding is in consistent with a study done by Rizuan et al., 2021, who stated that the pure MR foam with 75 wt% of CIPs has the increment of 6 kPa in modulus when the magnetic field was from 0 to 0.8 T. Figure 4A shows the illustration of MR foam indicating the distribution of CIPs and silica nanoparticles over the composite area, particularly at the off-state condition. The large surface area of nanosized silica particles in the MR foam has created more silane coupling agents formed between the O-H functional group of silica with ether-oxygen of polyol via H-bonding interactions. These bonds have enhanced the interparticle interactions between the CIPs and silica nanoparticles to the matrix structure of MR foam. Thus, the silica nanoparticles should be observed over the CIPs surfaces and in the matrix phase of MR foam. However, there are gaps between the particles as no magnetic field was induced to the MR foam, and the stiffness of the material is completely dependent on the composite foam that embeds both CIPs and silica nanoparticles. At the on-state condition or when there was induction of the magnetic field, the storage modulus of the MR foam increased, indicating the magnetic interactions between the CIPs and its responsiveness toward the magnetic field stimuli. This phenomenon somehow caused shrink of the MR foam slightly due to reducing gap between the attraction of the particles, especially among the CIPs (Wang et al., 2020). The phenomenon can be illustrated in Figure 4B showing stronger interaction between particles-matrix phases with applied magnetic fields. Indeed, as shown in Figure 3, the storage modulus of MR foam with 1 wt% of silica nanoparticles has increased by 7 kPa, from 89 kPa at the off-state condition to 96 kPa at the on-state condition. Similar small increasing trend of 8, 9 and 11 kPa in the absolute MR effect, ΔG were observed for other MR foams with silica nanoparticles of 2, 3 and 4 wt% respectively, and it showed the stiffer MR foams with the strength of magnetic fields. Even though the changes are found to be small for each MR foam, the increasing value of storage modulus somehow showed the structural transformation of MR foam with induction of the magnetic field (Alekhina et al., 2019). In fact, MR foam that under the influence of the magnetic field would cause the magnetic domain of the CIPs were aligned according to the direction of magnetic fields (Rizuan et al., 2020). Thus, the stiffness of MR foams increased in line with the increasing value of storage modulus, particularly with greater strength of magnetic fields as stronger magnetic interactions would be taken place between the CIPs (Li et al., 2020a).
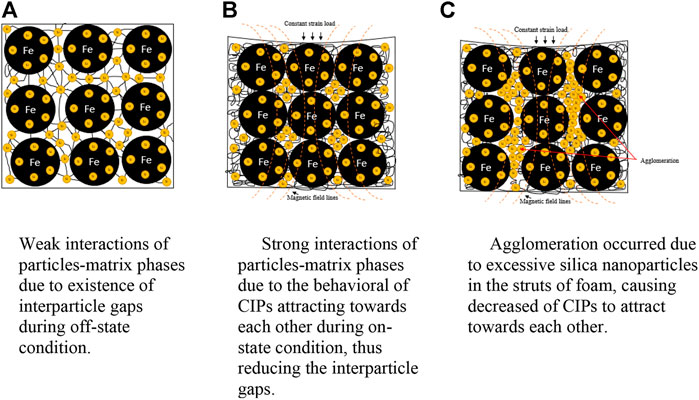
FIGURE 4. Schematic illustration of particles–matrix interactions in MR foam, at off- and on-state conditions. (A) Weak interactions of particles–matrix phases due to existence of interparticle gaps during the off-state condition. (B) Strong interactions of particles–matrix phases due to the behavioral of CIPs attracting toward each other during the on-state condition, thus reducing the interparticle gaps, (C) Agglomeration occurred due to excessive silica nanoparticles in the struts of foam, causing decrease of CIPs to attract toward each other.
However, in terms of silica nanoparticles that were added into MR foams in different concentrations, the value of storage modulus at zero magnetic field showed a significant increment. As observed in Figure 3, the initial storage modulus, G0’ of each MR foam increased with the increased of silica nanoparticles, particularly from 1 wt% to 4 wt% samples. These findings indicated the stiffer MR foams at the initial state or with absence of the magnetic field as more silica nanoparticles were embedded in the foam structure. Then as magnetic fields were induced to MR foams, for instance at 0.8 T, the increased in storage modulus from one MR foam sample to another were noted very slightly, about 1 kPa increment showing the non-magnetic behaviour possessed by the silica nanoparticles toward the applied magnetic field. In fact, these findings were in agreement with the work done by Abd Rashid et al. (2021) who stated that a small increment were observed for the initial storage modulus of MRE samples, between 0.03 and 0.06 MPa for different concentrations of silica nanoparticles, about 3 to 6wt%. Indeed, the small increment in the storage modulus of MR foams indicated the improvement of particles-matrix interaction when silica nanoparticles were added in the structure of MR foam. Hence, the changed in the storage modulus of MR foams increased simultaneously with the increasing composition of silica nanoparticles. This positive trend also has been discussed in previous section of strain sweep test as adding more silica nanoparticles resulted in the significant enhancement of storage modulus of MR foams, particularly at the initial state and not under the influence of applied magnetic fields.
On the other hand, the absolute MR effect,
3.2 Morphological characterizations of MR foams
Figure 5 shows the micrograph of MR foams with (A) the MR foam without silica additive and (B) the MR foam with 4 wt% of silica nanoparticles. Generally, the structure of MR foam includes cell pores that are enclosed by struts as shown in both Figures 5A,B. It was observed that the MR foam (Figure 5A exhibited more open cell pores correspond to the typical structure of flexible foam while MR foam with silica nanoparticles are observed to have more closed cell pores (Figure 5B) (Scarpa et al., 2004). The resultant structure of MR foam is mainly due to the particle’s dispersion including the silica nanoparticles that play a significant role in controlling the cell size of the pores during the polymerization process. The process includes gas formation, cell nucleation growth and cells distribution that would lead to the stabilization of the foam structure (Tamaddoni Moghaddam et al., 2019).
In general, the magnetic particles are embedded in the struts and cell walls of MR foam during foaming process. The distribution of the particles is separated by the pores of the foam matrix, in which would affect the rheological properties of the MR foam. As shown in Figure 5A, significant numbers of non-uniform sized of open-cell pores with large cavities like tunnel have been observed. The formation of pores began with the bubbles of carbon dioxide, CO2 that were formed via reaction of isocyanate groups with water, thus releasing CO2 during the gas formation process. Then the bubbles started to grow from the expansion of the blowing gas and merged into coalescent pores structure during the 2nd stage, cell nucleation growth process. In this case, the nucleation growth of pores in MR foam occurred where gas bubbles from the neighboring phase diffused and created randomly large bubbles, resulted in more open-cell pores structure. This resultant open-cell pores structure of MR foam also similar and has been discussed by Rizuan et al., 2021 where the porosity and deep cavities MR foam with 75 wt% of CIPs were characterized. The presence of deeper cavities was influenced by the coalescent of more bubbles, subsequently forming connecting not only deeper but large cavities in the structure of MR foam. Hence, the distribution of the particles is more scattered and significant distance between CIPs were observed due to the existence of large pores. Referring to the result of strain dependent test that has been discussed in previous sub-section, MR foam basically exhibited low storage modulus, about 45 kPa correlated to the nature porosity of MR foam which would affect its ability to withstand higher applied load. The addition of silica nanoparticles is expected to alter the resultant structure of MR foam and simultaneously enhanced the storage modulus of MR foam, accordingly.
In fact, MR foam with 4 wt% of silica nanoparticles possessed improved storage modulus, around 162 kPa and the respective micrograph as shown in Figure 5B, the MR foam looks more closed-cell pores structure with smaller size cavities. At first, the gas bubbles (CO2) were released through the reaction between isocyanate groups of PU foam that in contact with water. Then on the second stage of cell nucleation growth process, silica nanoparticles in the MR foam began to act as nucleation sites for the silane coupling bond to form via H-bonding, that improved the bonding between particles and matrix phase (polyol). In addition, the advantage of nano-sized silica particles is its large surface area where nucleation growth of bubbles becomes more intense, and a greater number of silica nanoparticles could create more silane coupling bonds in the matrix phase. Thus, the mixture turned out to be more viscous and aided bubbles nucleation process resulted in closed-cell pores formation and less porous structure in the MR foam. The growth of bubbles then stopped upon foaming process end, creating porous structure of MR foam. Hence, the distribution of particles including CIPs and silica are more compact due to reduced gaps between smaller pores and adjacent struts would become nearer. The morphological structure also become more compact and denser causing the MR foam became stiffer and as a result the storage modulus of the material has been enhanced. This phenomenon corresponds to the significant increment in the storage modulus of MR foam with more silica nanoparticles. In fact, when the magnetic field was induced to the MR foam, stronger magnetic forces between the CIPs are acquired due to closer gap between the particles in the struts of MR foam, resulting stiffer composite material. Nevertheless, the increment storage modulus of MR foam with magnetic fields are smaller indicating non-magnetic behavior owned by the silica nanoparticles which are unable to respond to the magnetic field stimuli.
However, the excessive silica nanoparticles in the MR foam, particularly with 5 wt% somehow resulted in negative impact toward the structural and properties of MR foam. Figure 6A showed the micrograph of non-agglomerated particles in the foam matrix when 4 wt% of silica nanoparticles were added to the MR foam. The CIPs and silica nanoparticles were well distributed and embedded in the structure of polymer foam matrix. However, the agglomeration of particles was observed in the MR foam with 5 wt% of silica nanoparticles as shown in Figure 6B. It is attributed to the excessive silica nanoparticles where the amount of polymer that is available to build up bonds with the silica is limited during the polymerization process (Davino et al., 2012), causing agglomeration of silica in the matrix phase. The aggregation of silica nanoparticles also would affect the dimensional stability of the cellular structure of MR foam, thus explaining a decrement in the storage modulus of the material, as has been highlighted in previous section.
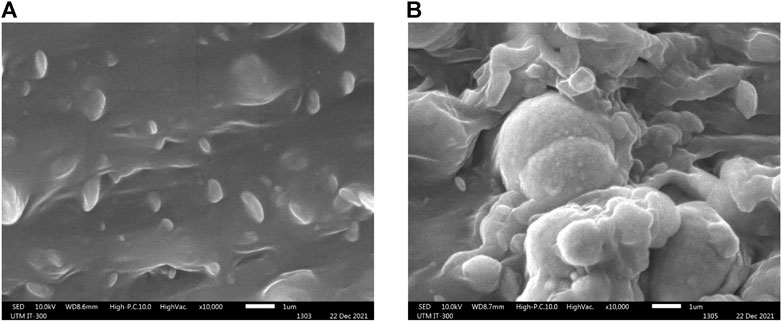
FIGURE 6. Micrograph of (A) non-agglomerated particles in MR foam with 4 wt% of silica nanoparticles and (B) agglomerated particles in MR foam with 5 wt% of silica nanoparticles.
Figure 7 depicts the EDX mapping analysis of MR foam with the addition of silica nanoparticles and the analysis showed presence of iron (Fe), carbon (C), silicon (Si) and oxygen (O) correspond to the CIPs (Fe), silica nanoparticles (SiO2) and carbon for matrix phase. In addition, it was observed that the silica nanoparticles have been well distributed entire the composite area as presented in Figure 7D, including the silica on the surface of the CIPs and in matrix phase of MR foam. This finding also corresponded to the schematic illustrated in Figure 4A.
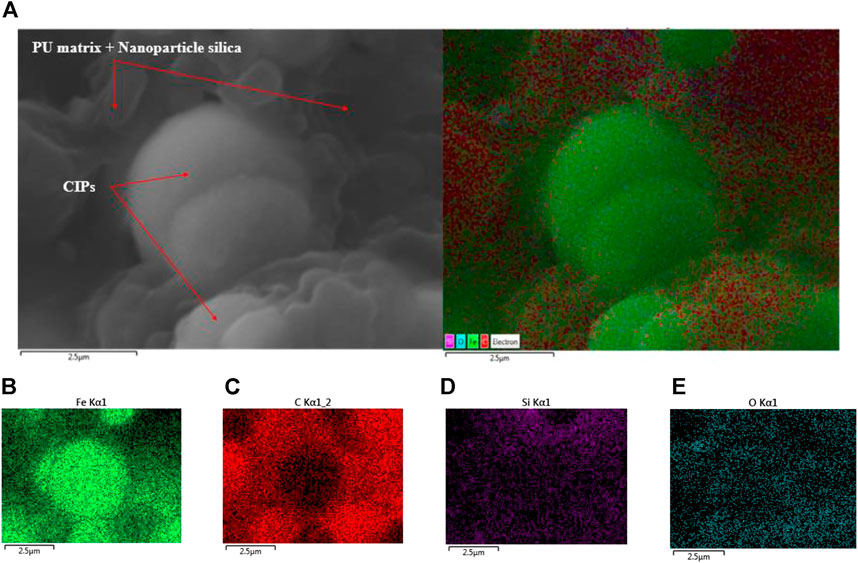
FIGURE 7. Mapping analysis of (A) MR foam with addition of silica nanoparticles and respective elements of (B) iron, Fe; (C) carbon, C; (D) silicon, Si; and (E) oxide, O.
4 Conclusion
In this work, MR foams with fixed 75 wt% of CIPs have been fabricated with different composition of silica nanoparticles in the range of 0–5 wt%., with the increment of 1 wt% The samples were run to investigate the effects of silica nanoparticles toward the enhancement of the viscoelastic properties, particularly storage modulus and morphological of MR foams. It was identified that under the influence of applied strains, MR foam with 4 wt% of silica nanoparticles demonstrated significant increment in storage modulus, about 260% increase as compared to the MR foam without the addition of silica nanoparticles. In fact, under the influence of magnetic fields from 0 T to 0.73 T, the absolute MR effect of the MR foam was enhanced by about 11kPa, attributed to the responsiveness of the CIPs toward the induced magnetic stimuli showing stiffer MR foam at the on-state condition. Similar findings for other MR foams were observed as the corresponding storage modulus increased with the increased of silica nanoparticles, simultaneously with applied magnetic fields. The findings somehow showed the stiffer MR foams with more embedded particles in the matrix structure, including CIPs and silica nanoparticles (1–5 wt%), at the off-state condition. The enhancement is attributed to the presence of silica nanoparticles that has strengthened the filler-matrix bonding by the formation of silane coupling bond between silica to the PU matrix and CIPs. The stiffness of each MR foam was further increased at the on-state condition due to stronger magnetic interaction of the CIPs and toward the applied magnetic fields. However, the MR foam with 5 wt% of silica nanoparticles showed drop in storage modulus due to the agglomeration of particles in the cellular matrices. Meanwhile, the change in modulus, ∆G, from one to another MR foam with increment of 1 wt% of silica nanoparticles showed small increment as well, about 1 kPa particularly at the on-state condition showing the non-magnetic properties of silica additive toward the applied field. Furthermore, the micrograph images have shown the open-cell pores structure with large cavities in the structure of the MR foam while less porous and closed-cell pores structure were observed for MR foam with silica nanoparticles. The silica nanoparticles also were well distributed entire the MR foam indicating the homogeneity properties of the material.
Data availability statement
The original contributions presented in the study are included in the article/Supplementary Material; further inquiries can be directed to the corresponding authors.
Author contributions
All authors listed have made a substantial, direct, and intellectual contribution to the work and approved it for publication.
Funding
This research work is supported and funded by the Universiti Teknologi Malaysia (UTM) Zamalah (Vot No. 0060N) and the Japan International Cooperation Agency Fund (JICA Fund) (Vot No. 4B696). The authors also declared that this research was funded by Universitas Sebelas Maret through Hibah Kolaborasi Internasional (HKI) 2022 (Contract No. 254/UN27.22/PT.01.03/2022).
Conflict of interest
The authors declare that the research was conducted in the absence of any commercial or financial relationships that could be construed as a potential conflict of interest.
Publisher’s note
All claims expressed in this article are solely those of the authors and do not necessarily represent those of their affiliated organizations, or those of the publisher, the editors, and the reviewers. Any product that may be evaluated in this article, or claim that may be made by its manufacturer, is not guaranteed or endorsed by the publisher.
References
Abd Rashid, R. Z., Johari, N., Mazlan, S. A., Abdul Aziz, S. A., Nordin, N. A., Nazmi, N., et al. (2021). Effects of silica on mechanical and rheological properties of EPDM-based magnetorheological elastomers. Smart Mat. Struct. 30, 105033. doi:10.1088/1361-665X/ac1f64
Ahmad Khairi, M. H., Mazlan, S. A., Ubaidillah,, , Choi, S. B., Abdul Aziz, S. A., Mohamad, N., et al. (2019). Role of additives in enhancing the rheological properties of magnetorheological solids: A review. Adv. Eng. Mat. 21, 1–13. doi:10.1002/adem.201800696
Alekhina, Y. A., Omelyanchik, A. S., Peddis, D., Spiridonov, V. V., Rodionova, V. V., Perov, N. S., et al. (2019). Magnetorheological foams for multiferroic applications. J. Magn. Magn. Mat. 485, 413–418. doi:10.1016/j.jmmm.2019.04.001
Anuar, M. F., Fen, Y. W., Zaid, M. H. M., Matori, K. A., and Khaidir, R. E. M. (2018). Synthesis and structural properties of coconut husk as potential silica source. Results Phys. 11, 1–4. doi:10.1016/j.rinp.2018.08.018
Aziz, S. A. A., Mazlan, S. A., Ubaidillah, U., Shabdin, M. K., Yunus, N. A., Nordin, N. A., et al. (2019). Enhancement of viscoelastic and electrical properties of magnetorheological elastomers with nanosized Ni-Mg cobalt-ferrites as fillers. Mater. (Basel) 12, 1–18. doi:10.3390/ma1221353110.1016/j.compositesb.2020.108348
Bastola, A. K., and Hossain, M. (2020). A review on magneto-mechanical characterizations of magnetorheological elastomers. Compos. Part B Eng. 200, 108348. doi:10.1016/j.compositesb.2020.108348
Boczkowska, A., Awietjan, S. F., Pietrzko, S., and Kurzydłowski, K. J. (2012). Composites : Part B mechanical properties of magnetorheological elastomers under shear deformation. Compos. Part B Eng. 43, 636–640. doi:10.1016/j.compositesb.2011.08.026
Burgaz, E., and Kendirlioglu, C. (2019). Thermomechanical behavior and thermal stability of polyurethane rigid nanocomposite foams containing binary nanoparticle mixtures. Polym. Test. 77, 105930. doi:10.1016/j.polymertesting.2019.105930
Cain, A. A., Nolen, C. R., Li, Y. C., Davis, R., and Grunlan, J. C. (2013). Phosphorous-filled nanobrick wall multilayer thin film eliminates polyurethane melt dripping and reduces heat release associated with fire. Polym. Degrad. Stab. 98, 2645–2652. doi:10.1016/j.polymdegradstab.2013.09.028
Chuah, W. H., Zhang, W. L., Choi, H. J., and Seo, Y. (2015). Magnetorheology of core-shell structured carbonyl iron/polystyrene foam microparticles suspension with enhanced stability. Macromolecules 48, 7311–7319. doi:10.1021/acs.macromol.5b01430
Davino, D., Mei, P., Sorrentino, L., and Visone, C. (2012). Polymeric composite foams with properties controlled by the magnetic field. IEEE Trans. Magn. 48, 3043–3046. doi:10.1109/TMAG.2012.2198634
Eatemadi, A., Daraee, H., Karimkhanloo, H., Kouhi, M., Zarghami, N., Akbarzadeh, A., et al. (2014). Carbon nanotubes: Properties, synthesis, purification, and medical applications. Nanoscale Res. Lett. 9, 1–13. doi:10.1186/1556-276X-9-393
Ge, L., Xuan, S., Liao, G., Yin, T., and Gong, X. (2015). Stretchable polyurethane sponge reinforced magnetorheological material with enhanced mechanical properties. Smart Mat. Struct. 24, 037001. doi:10.1088/0964-1726/24/3/037001
Gong, Q., Wu, J., Gong, X., Fan, Y., and Xia, H. (2013). Smart polyurethane foam with magnetic field controlled modulus and anisotropic compression property. RSC Adv. 3, 3241–3248. doi:10.1039/c2ra22824f
Kang, S. S., Choi, K., Nam, J. Do, and Choi, H. J. (2020). Magnetorheological elastomers: Fabrication, characteristics, and applications. Mater. (Basel) 13, 1–24. doi:10.3390/ma13204597
Khaidir, R. E. M., Fen, Y. W., Zaid, M. H. M., Matori, K. A., Omar, N. A. S., Anuar, M. F., et al. (2019b). Exploring Eu3+ -doped ZnO-SiO2 glass derived by recycling renewable source of waste rice husk for white-LEDs application. Results Phys. 15, 102596. doi:10.1016/j.rinp.2019.102596
Khaidir, R. E. M., Fen, Y. W., Zaid, M. H. M., Matori, K. A., Omar, N. A. S., Anuar, M. F., et al. (2020). Addition of ZnO nanoparticles on waste rice husk as potential host material for red-emitting phosphor. Mat. Sci. Semicond. process. 106, 104774. doi:10.1016/j.mssp.2019.104774
Khaidir, R. E. M., Fen, Y. W., Zaid, M. H. M., Matori, K. A., Omar, N. A. S., Anuar, M. F., et al. (2019a). Optical band gap and photoluminescence studies of Eu3+ -doped zinc silicate derived from waste rice husks. Optik 182, 486–495. doi:10.1016/j.ijleo.2019.01.061
Kong, L., Li, F., Wang, F., Miao, Y., Huang, X., Zhu, H., et al. (2018). High-performing multi-walled carbon nanotubes/silica nanocomposites for elastomer application. Compos. Sci. Technol. 162, 23–32. doi:10.1016/j.compscitech.2018.04.008
Kumar, V., and Lee, D. J. (2019). Mechanical properties and magnetic effect of new magneto-rheological elastomers filled with multi-wall carbon nanotubes and iron particles. J. Magn. Magn. Mat. 482, 329–335. doi:10.1016/j.jmmm.2019.03.075
Li, S., Li, Y., and Li, J. (2021). Thixotropy of magnetorheological gel composites: Experimental testing and modelling. Compos. Sci. Technol. 214, 108996. doi:10.1016/j.compscitech.2021.108996
Li, S., Liang, Y., Li, Y., Li, J., and Zhou, Y. (2020a). Investigation of dynamic properties of isotropic and anisotropic magnetorheological elastomers with a hybrid magnet shear test rig. Smart Mat. Struct. 29, 114001–114023. doi:10.1088/1361-665x/ab9e09
Li, S., Tian, T., Wang, H., Li, Y., Li, J., Zhou, Y., et al. (2020b). Development of a four-parameter phenomenological model for the nonlinear viscoelastic behaviour of magnetorheological gels. Mat. Des. 194, 108935. doi:10.1016/j.matdes.2020.108935
Li, W., Kostidis, K., Zhang, X., and Zhou, Y. (2009). “Development of a force sensor working with MR elastomers,” in IEEE/ASME int. Conf. Adv. Intell. Mechatronics, AIM, 233–238. doi:10.1109/AIM.2009.5230010
Linde, R. K., Seaman, L., and Schmidt, D. N. (1972). Shock response of porous copper, iron, tungsten, and polyurethane. J. Appl. Phys. 43, 3367–3375. doi:10.1063/1.1661721
Meng, J., Gerez, L., Chapman, J., and Liarokapis, M. (2020). “A tendon-driven, preloaded, pneumatically actuated, soft robotic gripper with a telescopic palm,” in 2020 3rd IEEE int. Conf. Soft robot. RoboSoft, 476–481. 2020. doi:10.1109/RoboSoft48309.2020.9115986
Mohd Nasir, N. A., Nazmi, N., Mohamad, N., Ubaidillah, U., Nordin, N. A., Mazlan, S. A., et al. (2021). Rheological performance of magnetorheological grease with embedded graphite additives. Mater. (Basel) 14, 1–15. doi:10.3390/ma14175091
Muhazeli, N. S., Nordin, N. A., Mazlan, S. A., Rizuan, N., Choi, S., Abd Fatah, A. Y., et al. (2019). Characterization of morphological and rheological properties of rigid magnetorheological foams via in situ fabrication method. J. Mat. Sci. 54, 13821–13833. doi:10.1007/s10853-019-03842-9
Muhazeli, N. S., Nordin, N. A., Ubaidillah, U., Mazlan, S. A., Aziz, S. A. A., Nazmi, N., et al. (2020). Magnetic and tunable sound absorption properties of an in-situ prepared magnetorheological foam. Mater. (Basel) 13, 1–16. doi:10.3390/ma13245637
Nikje, M. M. A., Garmarudi, A. B., Haghshenas, M., and Mazaheri, Z. (2009). Improving the performance of heat insulation polyurethane foams by silica nanoparticles. Nanotechnol. Constr. 3, 149–154. doi:10.1007/978-3-642-00980-8_19
Nikje, M. M. A., and Tehrani, Z. M. (2010). Thermal and mechanical properties of polyurethane rigid foam/modified nanosilica composite. Polym. Eng. Sci. 50, 468–473. doi:10.1002/pen.21559
Plachy, T., Kratina, O., and Sedlacik, M. (2018). Porous magnetic materials based on EPDM rubber fi lled with carbonyl iron particles. Compos. Struct. 192, 126–130. doi:10.1016/j.compstruct.2018.02.095
Rizuan, N., Mazlan, S. A., Ubaidillah, U., Sedlacik, M., Aziz, S. A. A., Nazmi, N., et al. (2021). Sensitivities of rheological properties of magnetoactive foam for soft sensor technology. Sensors 21, 1–19. doi:10.3390/s21051660
Rizuan, N., Mazlan, S. A., UbaidillahAbdul Aziz, S. A., Nazmi, N., and Yunus, N. A. (2020). Enhancement of sensitivity of magnetostrictive foam in low magnetic fields for sensor applications. Polymer 211, 123083. doi:10.1016/j.polymer.2020.123083
Saha, M. C., Kabir, M. E., and Jeelani, S. (2008). Enhancement in thermal and mechanical properties of polyurethane foam infused with nanoparticles. Mater. Sci. Eng. A 479, 213–222. doi:10.1016/j.msea.2007.06.060
Saiz-Arroyo, C., Escudero, J., Rodríguez-Pérez, M. A., and De Saja, J. A. (2011). Improving the structure and physical properties of LDPE foams using silica nanoparticles as an additive. Cell. Polym. 30, 63–78. doi:10.1177/026248931103000202
Scarpa, F., Bullough, W. A., and Lumley, P. (2004). Trends in acoustic properties of iron particle seeded auxetic polyurethane foam. Proc. Institution Mech. Eng. Part C J. Mech. Eng. Sci. 218, 241–244. doi:10.1243/095440604322887099
Scarpa, F., and Smith, F. C. (2004). Passive and MR fluid-coated auxetic PU foam - mechanical, acoustic, and electromagnetic properties. J. Intell. Mat. Syst. Struct. 15, 973–979. doi:10.1177/1045389X04046610
Schümann, M., Seelig, N., and Odenbach, S. (2015). The effect of external magnetic fields on the pore structure of polyurethane foams loaded with magnetic microparticles. Smart Mat. Struct. 24, 105028. doi:10.1088/0964-1726/24/10/105028
Shabdin, M. K., Rahman, M. A. A., Mazlan, S. A., Ubaidillah, , Hapipi, N. M., Adiputra, D., et al. (2019). Material characterizations of gr-based magnetorheological elastomer for possible sensor applications: Rheological and resistivity properties. Mater. (Basel) 12, 1–15. doi:10.3390/ma12030391
Tamaddoni moghaddam, S., and Naimi-Jamal, M. R. (2017). Effect of novel magnetic nanoparticles on morphology properties of polyurethane foam, 4828. doi:10.3390/ecsoc-21-04828
Tamaddoni Moghaddam, S., Naimi-Jamal, M. R., Rohlwing, A., Hussein, F. B., and Abu-Zahra, N. (2019). High removal capacity of arsenic from drinking water using modified magnetic polyurethane foam nanocomposites. J. Polym. Environ. 27, 1497–1504. doi:10.1007/s10924-019-01446-7
Tian, T. F., Li, W. H., Alici, G., Du, H., and Deng, Y. M. (2011). Microstructure and magnetorheology of graphite-based MR elastomers. Rheol. Acta 50, 825–836. doi:10.1007/s00397-011-0567-9
Umehara, Y., Yamanaga, Y., Akama, S., and Kato, S. (2018). Railway actuator made of magnetic elastomers and driven by a magnetic Field, 1–7. doi:10.3390/polym10121351
Wang, N., Liu, X., Sun, S., Królczyk, G., Li, Z., and Li, W. (2020). Microscopic characteristics of magnetorheological fl uids subjected to magnetic fields. J. Magn. Magn. Mat. 501, 166443. doi:10.1016/j.jmmm.2020.166443
Yin, H., Zhang, X., Li, J., Cao, J., Zhao, Y. M., and Cheng, B. L. (2017). Effects of selenium on Fusarium growth and associated fermentation products and the relationship with chondrocyte viability. Biomed. Environ. Sci. 30, 134–138. doi:10.3967/bes2017.017
Yunus, N. A., Mazlan, S. A., UbaidillahAbdul Aziz, S. A., Shilan, S. T., Abdul Wahab, N. A., and Abdul Wahab, N. (2019). Thermal stability and rheological properties of epoxidized natural rubber-based magnetorheological elastomer. Int. J. Mol. Sci. 20, 1–19. doi:10.3390/ijms20030746
Zaidi, S., Maselli, M., Laschi, C., and Cianchetti, M. (2021). Actuation technologies for soft robot grippers and manipulators: A review. Curr. Robot. Rep. 2, 355–369. doi:10.1007/s43154-021-00054-5
Zainudin, A. A., Yunus, N. A., Mazlan, S. A., Shabdin, M. K., Aziz Abdul, S. A., Nordin, N. A., et al. (2020). Rheological and resistance properties of magnetorheological elastomer with cobalt for sensor application. Appl. Sci. (Basel). 10, 1–12. doi:10.3390/app10051638
Keywords: magnetorheological foams, carbonyl iron particles, silica nanoparticles, storage modulus, porosity, silane coupling
Citation: Khaidir REM, Nordin NA, Mazlan SA, Abd Rahman H, Ubaidillah , Abdul Aziz SA and Nazmi N (2022) Stiffness enhancement of magnetorheological foam by structural modification using silica nanoparticles additive. Front. Mater. 9:959489. doi: 10.3389/fmats.2022.959489
Received: 01 June 2022; Accepted: 25 July 2022;
Published: 25 August 2022.
Edited by:
Yancheng Li, Nanjing Tech University, ChinaReviewed by:
Huixing Wang, Nanjing University of Science and Technology, ChinaShaoqi Li, Nanjing Tech University, China
Ying Dan Liu, Yanshan University, China
Copyright © 2022 Khaidir, Nordin, Mazlan, Abd Rahman, Ubaidillah, Abdul Aziz and Nazmi. This is an open-access article distributed under the terms of the Creative Commons Attribution License (CC BY). The use, distribution or reproduction in other forums is permitted, provided the original author(s) and the copyright owner(s) are credited and that the original publication in this journal is cited, in accordance with accepted academic practice. No use, distribution or reproduction is permitted which does not comply with these terms.
*Correspondence: Nur Azmah Nordin, bnVyYXptYWgubm9yZGluQHV0bS5teQ==; Ubaidillah, dWJhaWRpbGxhaF9mdEBzdGFmZi51bnMuYWMuaWQ=
†These authors have contributed equally to this work