- 1School of Chemical Sciences, Mahatma Gandhi University, Kottayam, Kerala, India
- 2Textile Manufacture and Textile Chemistry Division, ICAR-Central Sheep and Wool Research Institute, Avikanagar, Rajasthan, India
- 3School of Energy Materials, Mahatma Gandhi University, Kottayam, Kerala, India
- 4Department of Chemistry, Sree Narayana College for Women, Kollam, Kerala, India
In the reported work, the wool fabric was coated with epoxy resin by hand layup method to fabricate the wool-epoxy composites. Hydrophobic nanosilica was used as a filler to improve their mechanical characteristics. The physico-mechanical properties of the composites were analyzed using various analytical techniques. The surface morphology was examined with the aid of Scanning Electron Microscope. The biodegradability of the developed composites was determined by soil burial test. The presence of nanosilica in the composite was confirmed by Fourier Transform Infrared Spectroscopy (FTIR). According to the findings, up to 0.5% nanosilica content significantly increases the tensile and impact strength of the wool-epoxy composites. The contact angle measurement showed a slight enhancement in the hydrophobic properties of the composites due to the dispersion of hydrophobic nanosilica particles. The presence of nanosilica slightly reduced the water diffusivity in wool-epoxy-nanosilica composites when compared to wool-epoxy composites. The SEM images detected nanosilica inside the composites. After soil burial test, all the composites showed a weight reduction below 1.0%.
1 Introduction
Fiber reinforced epoxy composites are well-known structural materials in aerospace, automobile, and wind energy industries (George et al., 2022; Samant et al., 2022). Carbon and glass fibers are commonly used for this purpose. However, the ever-increasing demand for synthetic fiber reinforced polymer composites has raised a serious environmental and sustainable challenge (Tanvir et al., 2017; Anand et al., 2018). The overwhelming concern for environmental conservation prompted composite engineers and researchers to replace synthetic fibers in polymer composites with natural fibers (Asthana and Srivastava, 2021). During the last two decades, natural fibers extracted from various plants have been extensively used to reinforce epoxy matrix. However, the low fire resistance of plant-based lignocellulosic fibers has limited their use in the aerospace and construction industries, where considerable flame retardancy is required (Yang et al., 2017; George and Thomas, 2021; Fernandes et al., 2022; Susan George et al., 2022). Apart from plant-based fibers, those extracted from animals are recently getting attention as natural reinforcing fillers for polymers. They were successfully used for the thermo-mechanical reinforcement of many polymers. Animal extracted protein-based fibers includes wool (Semitekolos et al., 2021), chicken feather fiber (Vijayan et al., 2021), silk (Yang et al., 2017), were proved as efficient fillers for epoxy matrix too.
Wool fiber is formed by keratin protein and growth from an outer skin layer of sheep. The high wear and tear resistance and excellent insulation properties of wool fibers make them a good choice for reinforcing filler. They also have good elongation and elastic recovery. In comparison with other plant based bast fibers like flax, jute, and banana, only few attempts have been reported with wool-polymer composites. Unsaturated polyester (Triki et al., 2016), poly propylene (Conzatti et al., 2013; Kim and Bhattacharyya, 2016), natural rubber (Jose et al., 2022a) have been used as a matrix for wool. Few investigations on wool-natural/synthetic fiber hybrid composites have been published [Jose et al., 2022b (a)]. In a study, wool fiber-epoxy composite with different fiber loading was fabricated by Semitekolos et al. (2021). The flexural and shear strength analysis depicts that the developed composites maintain their mechanical properties for up to 4.1 phr fiber loading. The TGA analysis showed higher thermal stability. The composites exhibited 30% less thermal conductivity in comparison with neat epoxy and this could be used for the development of insulating panels. In another study, Bharath et al. (2019) fabricated wool-epoxy composite with 60% fiber loading by hand lay-up method. The toughness of the composites was optimized by Taguchi design method. They observed that the thickness of the composite is having a high percentage of contribution to tensile strength, whereas, the void diameter contributes more to fracture toughness.
Wool is prone to moisture attack due to its natural hydrophilic nature. This will have a negative impact on their performance during their tenure. Incorporating nano fillers into fiber reinforced epoxies to balance performance is a relatively new practice (Mittal et al., 2016). The complicated interactions among the components in such hybrid polymer systems dictate the final property, which can be easily modified with composition and morphology.
For the reported study, Indian coarse wool, which is of no commercial use at present, has been used as reinforcement for epoxy resin. Due to the high diameter and medullation, this wool cannot find applications in the apparels or carpet industries and thus not fetching a good price in the market. The sheep rearers are selling this at very cheap price. The aim of the current research is to give a value addition to this wool through the development of composites for domestic/industrial applications. Though a couple of reports are available on wool-epoxy composites, no works has been reported on coarse wool reinforced epoxy composite with fillers. In comparison with synthetic fibre reinforced epoxy composites, the newly developed coarse wool-based composites not only reduce the carbon footprint but also add value to the coarse wool.
Thus, in the current investigation, wool-epoxy fiber composites were prepared by hand layup method. To enhance the mechanical properties of the composites, hydrophobic nanosilica was added as filler. The role of nanosilica on the physico-mechanical properties, water, and moisture related properties, and biodegradation studies of the wool-epoxy-nanosilica composite has been investigated.
2 Materials and methods
2.1 Materials
Fabric made up of coarse wool was sourced from M/S ICAR- Central Sheep and Wool Research Institute, Avikanagar, Rajasthan, India. (Fiber diameter—44 μm, bundle strength—10.93 g/tex, staple length—4.3 cm, and medullation—66%). The yarn prepared using this fiber was having 2.3 Nm count (Nm is the weight of 1.0 kg of yarn) with a tenacity of 3.22 cN/tex. The fabric was woven in a handloom and the resultant fabric was having 3.0 mm thickness, 600 g/m2 areal density and 3.2 MPa tensile strength. The preparation and properties of fiber, yarn and fabric are detailed in our previous work (Jose et al., 2022a).
Diglycidyl ether of bisphenol A (DGEBA) based epoxy resin (Lapox L-12) and hardener (Lapox K-6) was purchased from M/S Atul India Limited, India. The hydrophobic nanosilica was purchased from CAB- O- SIL (TS 530), and the acetone (assay- 99%) from Merck, India.
2.2 Preparation of epoxy-nanosilica-wool composites
The required concentrations of nanosilica (0.5, 2.5, 5.0% on the weight of epoxy resin) were initially dispersed in 50 mL acetone via ultrasonication for 30 min to form a uniform dispersion. This was added to the pre-calculated amount of epoxy resin under mild stirring in a magnetic stirrer. After mixing, the mixture was kept in a hot oil bath for 6 h to evaporate the acetone. The mixture was then cooled and the hardener (Lapox K-6) was added in the ratio 10:1 (on weight basis) and stirred well. For the composite preparation, the fabric to epoxy resin + hardener ratio was kept as 1:2.5 (on weight basis). The mixture containing epoxy resin, hardener and the nanosilica was poured on the wool fabric (3 layers) and spread with the aid of hand driven roller. After coating the resin, the three layered nano silica dispersed epoxy coated wool fabric was cured in a compression moulding at 60°C for 5 min by applying a pressure of 5 kg/cm2. Subsequently, it was allowed to cool gradually by keeping inside the mould for 6 h. The samples were denoted as EWS-0.5, EWS-2.5, and EWS-5.0, in which the last number denoted the weight percentage of silica added to the epoxy resin. A control three-layered wool-epoxy composite sample was also prepared by keeping all the parameters constant, but without adding nanosilica, for the comparative investigation (EWS-0). The epoxy-nanosilica-wool composite samples were cut into the required sizes for further testing. All the samples were preconditioned at 25°C and 65% RH before the characterization of composites.
2.3 Characterization of composites
The tensile strength and the Izod impact strength of the wool-epoxy-nanosilica composites were determined using a Universal Testing Machine (Tinius Olsen H50KT) and Impact tester (ZwickRoell, HIPT25P) as per the ASTM standards ASTMD 638 and 256 respectively. The surface morphology of the composites was examined through Scanning Electron Microscope (JEOL-JSM-6390). The surface wettability studies of the composites were measured on a Phoenix contact angle analyzer using deionised water as solvent. The FTIR analysis was performed with spectrometer (Perkin Elmer Spectrum Two) from the wavenumber ranging 4,000–400 cm−1 using 28 scans. The thickness of the composites was measured using a thickness gauge (Mitutoyo). To assess the rate of biodegradation of the composite, the soil burial test was carried out following the method as described elsewhere. In brief, the developed composite samples were dried at 105°C for 1 h and pre-conditioned the desiccator by keeping 65% RH and 25°C. The soil medium for the burial test was prepared by combining equal quantities of soil and cow dung with a sufficient amount of water. The mixture was then filled in a tray having a size of 30 × 30 × 8 cm. After applying soiling to a depth of 4 cm, the composite samples were placed, and the soil was filled up to a thickness of 6 cm. The samples were kept on a closed shelf with adequate air passage. To maintain the moisture content of the culture, water was sprinkled in every 2 days. After 120 days, samples were removed, rinsed with water, ethanol, and dried at 105°C for 1 h. The dried samples were conditioned again in a desiccator at 65% RH, weighed, and the weight loss was calculated. Three replicas were taken for the test, and the average weight loss was recorded. The weight loss was taken as a measure of biodegradation of the composite (Maran et al., 2014; Samant et al., 2023). To examine the water absorption properties, the composite samples were immersed in distilled water and weighed at regular intervals. The experiment was repeated until a steady weight was obtained.
3 Results and discussion
3.1 Mechanical properties
The physico-mechanical properties of the control and nanosilica incorporated wool-epoxy composites are shown in Table 1.
Figure 1 shows the stress strain curve of wool-nanosilica-epoxy composites. It is observed from the figure that the tensile strength and elongation properties of the wool-epoxy composite got significantly enhanced by the addition of nanosilica up to 2.5%. The control sample (EWS-0) has a tensile strength of 19.18 MPa. While adding nanosilica to 0.5% and 2.5%, the tensile strength increased up to 32% and 10.5% respectively in comparison with the control composite sample. A further increase in the nanosilica addition (5.0%) reduced the tensile strength. The elongation properties of the silica-incorporated wool-epoxy composites showed also an increment up to 2.5%. A modest increase in elongation was observed with the addition of 0.5% and 2.5% nanosilica. The modulus of the wool-epoxy composite was found to be initially lowered by the addition of 0.5% and further increased with 2.5% nanosilica.
3.2 FTIR analysis
The FTIR spectra of wool fiber and nanosilica is shown in Figure 2A. In the wool fiber, the stretching vibrations of carbonyl group are indicating a peak at 1,637 cm−1. A shallow curve at the 3,275–3,300 cm−1 region indicates the existence of–OH group, which may be originated from the inherent moisture content associated with the wool fiber. The band at 1,521 cm−1 is attributed to the bending deformation C–N–H bond (Jose et al., 2019). A minor peak at 1,233 cm−1 indicates the group C–N stretching and N–H in-plane bending vibrations in the wool fiber (Jose et al., 2018; Rani et al., 2020; Kadam et al., 2021). The characteristics peaks of silica are at 1,060 cm−1, 846 cm−1, and around 480 cm-1 which corresponds to asymmetric vibration of Si–O, asymmetric vibration of Si–OH and Si–O–Si bending vibration respectively (Hsiao et al., 2013).
The FTIR spectrum of the wool-epoxy composite with nanosilica is shown in Figure 2B. Most of the peaks remain same in all composites, however the intensity of the peaks decreased with the increase in the concentration of nanosilica. Two major peaks in the wool fiber (1,530 and 1,219 cm−1) were found to be shifted to 1,505 cm−1 and 1,233 cm−1 respectively in the composites. The peak at 827 cm−1 is assigned to four simulated vibrational modes namely, 844, 851, 853, and 856 cm−1. Their closeness which arises due to the C=O and C=C stretching and CH out plane bending in epoxy (Ramirez Herrera et al., 2013).
3.3 SEM analysis
Mechanism of failure during the tensile test and the fiber matrix interface properties have been well studied by using SEM. Figure 3 represents the SEM images of tensile fractured surfaces of wool-epoxy-nanosilica composites. The microscopic images clearly reflect the wool fibres are successfully embedded in the epoxy matrix. Presence of numerous micro scales (Figure 3A) on the wool surface would help them to adhere to epoxy matrix. Reinforcement of wool alone in epoxy is not enough to get desired properties, however it helps in stress transmission from one fiber to another fiber to a small extent. The fracture morphology of epoxy wool system with/without silica addition shows various basic failure mechanisms in fiber reinforced systems such as fiber pull-out, fiber deformation and fiber-matrix interface debonding. While comparing the failure surface of EWS-0 (Figure 3B) with EWS-0.5 (Figure 3C), EWS-2.5 (Figure 3D), and EWS-5.0 (Figure 3E), the surface became rougher with increasing the nanosilica content. The incorporation of nanosilica makes the fracture surface rougher, may be attributed by the localized plastic deformation in the EWS-0.5 (Figure 3C), EWS- 2.5 (Figure 3D), and EWS-5.0 (Figure 3E) systems. Furthermore, the debonding and fiber breakage phenomenon could be clearly observed in EWS- 2.5 (Figure 3) system and the degree of fiber breakage is increasing with the increase of nanosilica loading. Formation of several islands (represented by yellow solid lines) of nanosilica within the epoxy system is responsible for this phenomenon. Instead of stress concentrators, these islands help to attain better properties in the composites.
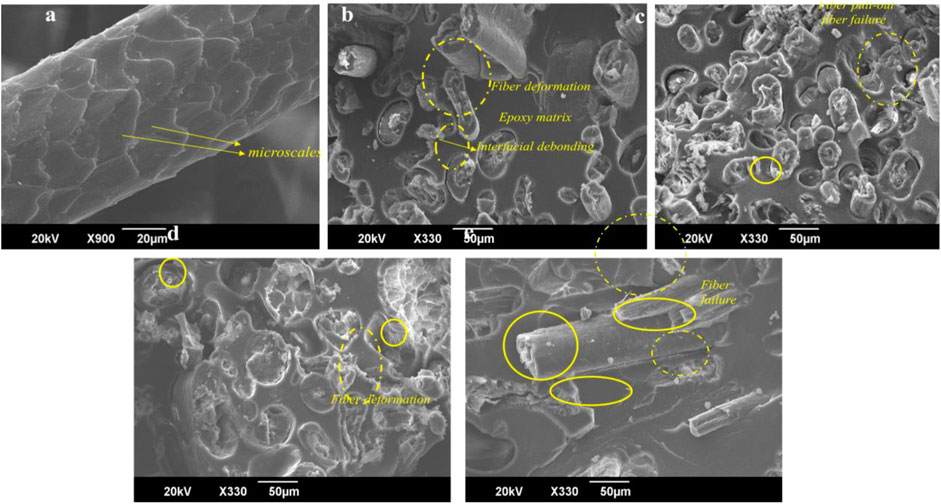
FIGURE 3. SEM images of (A) Coarse wool fiber, tensile fractured surfaces of (B) EWS-0, (C) EWS-0.5, (D) EWS-2.5, and (E) EWS-5.
Nanosilica reinforced epoxy/wool system exhibited much rougher and irregular fracture surface, owing to the blocking effect and crack pinning of nanosilica islands (represented by yellow solid lines). Furthermore, the debonding and fiber breakage phenomenon could be clearly observed in EWS-2.5 system and the degree of fiber breakage is increasing with the increase of nanosilica loading. In addition to the various mechanism of failure, we have observed several fabrications assisted fiber deformation. Those deformations of the wool fibers are clearly visible in Figures 3B, D. This deformation is formed due to the pressure build-up while fabricating the composites in compression moulding.
3.4 Izod impact strength
The impact strength of control wool-epoxy composite (EWS-0) was found to be 1555 J/m2. Incorporation of silica nanoparticles increases its impact strength to 2654 J/m2, 1926 J/m2 and 1743 J/m2 at 0.5 wt%, 2.5 wt% and 5.0 wt% of nanosilica respectively (Figure 4). This means that the addition of nanosilica increases the impact strength by 58.52, 23.85, and 12.09% respectively. Similar to tensile strength, among all the fabricated composites, 0.5 wt% of silica exhibited a substantial enhancement of impact strength to the EWS-0 system. The decrease in the impact strength of EWS-2.5 and EWS-5.0 may be due to the aggregation of nanosilica on the matrix. These clustering results in the formation of quite large unbound inclusions, similar to very large particles (Surendran et al., 2021). Similarly, the debonding of the matrix around the wool surface act as a stress concentrator and results in poor crack propagation resistance which in turn leads to a poor toughening effect (Joy et al., 2020).
3.5 Water diffusion studies
Water absorption of epoxy composites is critically important and needs to be analyzed for many outdoor applications as it adversely affects their performance. The mass percentage of epoxy composite versus the square root of immersion time gives the water uptake profile.
The water uptake profile of wool-epoxy and wool-epoxy-nanosilica composites is shown in Figure 5. As the silica content increased, the water absorption enhanced and reached a maximum of 2.5 wt% of silica (Table 2). Swelling of wool-epoxy-silica composites in water can be determined using the parameters such as molar solvent uptake (Qt) and diffusion coefficient (D).
Where Wi, Ws, Ms, and ρs are the initial weight of the sample, final weight after the swelling studies, molar mass of the solvent, density of the solvent respectively. In order to study the ability of the water molecule to move among the epoxy segments, the diffusion coefficient (D) has been calculated. It was found that D has not much affected by the presence of nanosilica, with a slight decrease in D indicating the barrier effect induced by the filler in the diffusion of water molecules into the bulk of the composites. The nano dispersion of silica particles imparts a tortuous path for the penetration of absorbed water molecules. It could be confirmed a higher water uptake and lower water diffusivity in wool-epoxy-nanosilica composites when compared to wool-epoxy composites.
3.6 Contact angle studies
Moisture absorption properties of wool-epoxy-nanosilica composites were strongly associated with the hydrophobic/hydrophilic nature of the composites.
Figure 6 illustrates the dynamic water contact angle measurements of the surface of the composites. EWS-0 has a water contact angle of 63°, revealing its hydrophilic nature owing to the presence of polar groups on the surface. However, the addition of hydrophobic nanosilica gradually enhanced the hydrophobicity of wool-epoxy-nanosilica composites. This can also be attributed due to the creation of several islands of nanosilica in the wool -epoxy system as explained in the fracture morphology. The addition of 5.0wt% of nanosilica makes the epoxy surface slightly hydrophobic with a contact angle value of 77°± 1°.
3.7 Moisture related properties
Among natural fibers, wool is having the highest moisture content (15%). Being synthetic, epoxy resin possess poor moisture uptake due to the lack of hydroxyl group. Figure 7 shows the moisture content of wool-epoxy-nanosilica composites. The control composite showed moisture content of 3.74%. The lower concentration of nanosilica (0.5%, 2.5%) in the composites did not mark any significant reduction in the moisture content. However, the addition of 5% nanosilica causes a reduction in moisture content to 2.84%. This difference is significant and is 25% less than the control composite sample. The low moisture absorption might be attributed to the high concentration of hydrophobic nanosilica in the composites.
3.8 Accelerated soil burial analysis
The weight loss due to the biological degradation after 120 days in soil is shown in the Figure 8. Wool, being a natural fibre is susceptible to degradation, whereas the epoxy component is not. Among all the tested composites, 0.50% concentration of nanosilica added composites showed a slight increase in the weight loss (0.9%). The variation in the weight loss due to biodegradation in other samples is negligible. Irrespective of the nanosilica concentration, all the samples showed a weight loss of below 1.0% after 120 days of soil burial test. The poor biological degradation rate may be due to the coating of epoxy resin over natural wool fiber, which reduces the inherent rate of degradation of wool fiber. It is concluded that the presence of nanosilica does not have any role in the soil degradation of wool-epoxy composite. The image of the coarse wool-epoxy-nanosilica composites (EWS-0.05) is shown in the Figure 9.
4 Conclusion
Herein, wool-epoxy composites were prepared by the hand layup method. The impact of nanosilica as a filler in the composites was investigated. The tensile and impact strength of the composites was increased with the inclusion of nanosilica up to 0.5%, and further addition of the filler resulted in a slight reduction. The moisture content of the composites did not show any significant difference with the addition of nanosilica, except at a very high concentration (5%). In comparison with the control sample, the addition of nanosilica generated roughness in the surface of the composites, as shown in the SEM images. The water contact angle showed a marginal increase with the incorporation of nanosilica. In all the developed composites, the weight loss induced by the accelerated soil degradation was found to be below 1.0% only.
Data availability statement
The original contributions presented in the study are included in the article/supplementary material, further inquiries can be directed to the corresponding author.
Author contributions
SJ, Conceptualization, preparation of fabric and composites, draft preparation; TJ, Sample preparation, moisture study, biodegradation study; ST, Technical guidance and manuscript correction; JG, Mechanical testing of composites, draft preparation; NN, FTIR and SEM sample analysis; PP and AB, Diffusion studies, manuscript correction.
Acknowledgments
Second author and corresponding author would like to acknowledge Defence Research and Development Organisation (DRDO) India, Naval Research Board under Grant (NRB-429/MAT/18-19) and Department of Science and Technology, India (DST), through Innovation of Science Pursuit for Inspire Research programme [INSPIRE (IF190284)].
Conflict of interest
The authors declare that the research was conducted in the absence of any commercial or financial relationships that could be construed as a potential conflict of interest.
Publisher’s note
All claims expressed in this article are solely those of the authors and do not necessarily represent those of their affiliated organizations, or those of the publisher, the editors and the reviewers. Any product that may be evaluated in this article, or claim that may be made by its manufacturer, is not guaranteed or endorsed by the publisher.
References
Anand, P., Rajesh, D., Senthil Kumar, M., and Saran Raj, I. (2018). Investigations on the performances of treated jute/Kenaf hybrid natural fiber reinforced epoxy composite. J. Polym. Res. 25 (4), 94–99. doi:10.1007/s10965-018-1494-6
Asthana, A., and Srivastava, V. (2021). Mechanical behavior of silk/hemp/steel wool–Epoxy composite. Mater. Today Proc. 44, 2228–2231. doi:10.1016/j.matpr.2020.12.358
Bharath, K. N., Manjunatha, G. B., and Santhosh, K. (2019). “Failure analysis and the optimal toughness design of sheep–wool reinforced epoxy composites,” in Failure analysis in biocomposites, fibre-reinforced composites and hybrid composites (Sawston, United Kingdom: Woodhead Publishing), 97–107.
Conzatti, L., Giunco, F., Stagnaro, P., Patrucco, A., Marano, C., Rink, M., et al. (2013). Composites based on polypropylene and short wool fibres. Compos. Part A Appl. Sci. Manuf. 47, 165–171. doi:10.1016/j.compositesa.2013.01.002
Fernandes, F. A., Jose, S., and Thomas, S. (2022). “Introduction to natural fiber composites,” in Wool fiber reinforced polymer composites (Sawston, United Kingdom: Woodhead Publishing), 1–13.
George, J. S., Paduvilan, J. K., Salim, N., Sunarso, J., Kalarikkal, N., Hameed, N., et al. (2022). Advances and future outlook in epoxy/graphene composites for anticorrosive applications. Prog. Org. Coatings 162, 106571. doi:10.1016/j.porgcoat.2021.106571
George, J. S., and Thomas, S. (2021). The effect of polymeric inclusions and nanofillers on cure kinetics of epoxy resin: A review. Polym. Sci. Ser. A 63 (6), 637–651. doi:10.1134/s0965545x21350145
Hsiao, M. C., Ma, C. C. M., Chiang, J. C., Ho, K. K., Chou, T. Y., Xie, X., et al. (2013). Thermally conductive and electrically insulating epoxy nanocomposites with thermally reduced graphene oxide–silica hybrid nanosheets. Nanoscale, 5(13), 5863–5871.
Jose, S., Nachimuthu, S., Das, S., and Kumar, A. (2018). Moth proofing of wool fabric using nano kaolinite. J. Text. Inst. 109 (2), 225–231. doi:10.1080/00405000.2017.1336857
Jose, S., Shanmugam, N., Das, S., Kumar, A., and Pandit, P. (2019). Coating of lightweight wool fabric with nano clay for fire retardancy. J. Text. Inst. 110 (5), 764–770. doi:10.1080/00405000.2018.1516529
Jose, S., Shanumon, P. S., Paul, A., Mathew, J., and Thomas, S. (2022a). Physico-mechanical, thermal, morphological, and aging characteristics of green hybrid composites prepared from wool-sisal and wool-palf with natural rubber. Polymers 14 (22), 4882. doi:10.3390/polym14224882
Jose, S., Thomas, S., Jibin, K. P., Sisanth, K. S., Kadam, V., and Shakyawar, D. B. (2022b). Surface modification of wool fabric using sodium lignosulfonate and subsequent improvement in the interfacial adhesion of natural rubber latex in the wool/rubber composites. Industrial Crops Prod. 177, 114489. doi:10.1016/j.indcrop.2021.114489
Joy, J., George, E., Thomas, S., and Anas, S. (2020). Effect of filler loading on polymer chain confinement and thermomechanical properties of epoxy/boron nitride (h-BN) nanocomposites. New J. Chem. 44 (11), 4494–4503. doi:10.1039/c9nj05834f
Kadam, V., Rani, S., Jose, S., Shakyawar, D. B., and Shanmugam, N. (2021). Biomaterial based shrink resist treatment of wool fabric: A sustainable technology. Sustain. Mater. Technol. 29, e00298. doi:10.1016/j.susmat.2021.e00298
Kim, N. K., and Bhattacharyya, D. (2016). Development of fire resistant wool polymer composites: Mechanical performance and fire simulation with design perspectives. Mater. Des. 106, 391–403. doi:10.1016/j.matdes.2016.06.005
Maran, J. P., Sivakumar, V., Thirugnanasambandham, K., and Sridhar, R. (2014). Degradation behavior of biocomposites based on cassava starch buried under indoor soil conditions. Carbohydr. Polym. 101, 20–28. doi:10.1016/j.carbpol.2013.08.080
Mittal, V., Saini, R., and Sinha, S. (2016). Natural fiber-mediated epoxy composites–a review. Compos. Part B Eng. 99, 425–435. doi:10.1016/j.compositesb.2016.06.051
Ramírez-Herrera, C. A., Cruz-Cruz, I., Jiménez-Cedeño, I. H., Martínez-Romero, O., and Elías- Zúñiga, A. (2021). Influence of the epoxy resin process parameters on the mechanical properties of produced bidirectional [±45] carbon/epoxy woven composites. Polymers 13 (8), 1273. doi:10.3390/polym13081273
Rani, S., Kadam, V., Rose, N. M., Jose, S., Yadav, S., and Shakyawar, D. B. (2020). Wheat starch, gum Arabic and chitosan biopolymer treatment of wool fabric for improved shrink resistance finishing. Int. J. Biol. Macromol. 163, 1044–1052. doi:10.1016/j.ijbiomac.2020.07.061
Samant, L., Goel, A., Mathew, J. J., and Thomas, S. (2023). Effect of surface treatment on flax fiber reinforced natural rubber green composite. J. Appl. Polym. Sci. 140. doi:10.1002/app.53651
Samant, L., Fernandes, F. A. O., Jose, S., and Alves de Sousa, R. J. (2022). in Natural composites in aircraft structures. Materials, structures and manufacturing for aircraft. Editors M. C. Kuşhan, S. Gürgen, and M. A. Sofuoğlu (Berlin, Germany: Springer International Publishing). 113–126.
Semitekolos, D., Pardou, K., Georgiou, P., Koutsouli, P., Bizelis, I., and Zoumpoulakis, L. (2021). Investigation of mechanical and thermal insulating properties of wool fibres in epoxy composites. Polym. Polym. Compos. 29 (9), 1412–1421. doi:10.1177/0967391120971387
Surendran, A., Pionteck, J., Malanin, M., Vogel, R., Kalarikkal, N., and Thomas, S. (2021). Miscibility, microstructure, and in situ cure analysis of epoxy–SAN–cloisite 20A nanocomposites. New J. Chem. 45 (3), 1395–1403. doi:10.1039/d0nj04282j
Susan George, J., Uthaman, A., Reghunadhan, A., Mayookh Lal, H., Thomas, S., and Vijayan P, P. (2022). Bioderived thermosetting polymers and their nanocomposites: Current trends and future outlook. Emergent Mater. 5, 3–27. doi:10.1007/s42247-022-00362-2
Tanvir, A., El-Gawady, Y. H., and Al-Maadeed, M. (2017). Cellulose nanofibers to assist the release of healing agents in epoxy coatings. Prog. Org. Coatings 112, 127–132. doi:10.1016/j.porgcoat.2017.07.008
Triki, A., Dittmer, J., Hassen, M. B., Arous, M., Bulou, A., and Gargouri, M. (2016). Spectroscopy analyses of hybrid unsaturated polyester composite reinforced by Alfa, wool, and thermo-binder fibres. Polym. Sci. Ser. A 58 (2), 255–264. doi:10.1134/s0965545x16020188
Vijayan, P.P., Bhanu, A. A., Archana, S. R., Babu, A., Siengchin, S., and Parameswaranpillai, J. (2021). Development of chicken feather fiber filled epoxy protective coating for metals. Mater. Today: Proc. 41, 468–472.
Keywords: biodegradation, wool, epoxy composite, nano silica, natural fibre composite
Citation: Jose S, George JS, Jacob TA, Vijayan P P, Bhanu A. V. A, Nedumpillil NN and Thomas S (2023) Nanosilica incorporated coarse wool-epoxy hybrid biocomposites with improved physico-mechanical properties. Front. Mater. 10:1140602. doi: 10.3389/fmats.2023.1140602
Received: 09 January 2023; Accepted: 26 January 2023;
Published: 14 March 2023.
Edited by:
Hafeezullah Memon, Zhejiang Sci-Tech University, ChinaReviewed by:
Khubab Shaker, National Textile University, PakistanMahesh Hosur, Texas A&M University Kingsville, United States
Copyright © 2023 Jose, George, Jacob, Vijayan P, Bhanu A. V., Nedumpillil and Thomas. This is an open-access article distributed under the terms of the Creative Commons Attribution License (CC BY). The use, distribution or reproduction in other forums is permitted, provided the original author(s) and the copyright owner(s) are credited and that the original publication in this journal is cited, in accordance with accepted academic practice. No use, distribution or reproduction is permitted which does not comply with these terms.
*Correspondence: Sabu Thomas, c2FidXRob21hc0BtZ3UuYWMuaW4=