- 1Department of Civil Engineering, SRM Institute of Science and Technology, Kattankulathur, Tamil Nadu, India
- 2Technical College of Engineering, Sulaimani Polytechnic University, Sulaymaniyah, Iraq
- 3Faculty of Engineering, Tishk International University, Sulaymaniyah, Iraq
- 4Institute of Construction Materials, Sydney, NSW, Australia
- 5School of Construction Economics and Management, University of Witwatersrand, Bloemfontein, South Africa
- 6Civil and Environmental Engineering and Construction, University of Nevada, Las Vegas, NV, United States
Introduction: The construction industry uses a large quantity of natural materials in the production of concrete. Although attempts to incorporate green materials in concrete began years ago, not every building uses such materials today, and roadways, particularly, still rely on unsustainable materials.
Methods: Therefore, this study used alternative materials, including fly ash, manufactured sand aggregates, and different molarities of alkaline activators, to incorporate waste byproducts in a geopolymer concrete white-topping pavement layer. Recent developments have led to the emergence of geopolymers as distinct classes of materials. In the 1990s, fly ash-based geopolymers became more popular than other kinds, as they are more efficient compared to Portland cement concrete.
Results: Aluminosilicate gel can be obtained by combining fly ash and alkaline solution. A comprehensive literature review of geopolymer concrete was performed in this study. It examines its critical design parameters, including alkaline solutions, curing temperatures, curing methods, workability, and compressive strength under various environmental conditions. This review provides a unique opportunity for researchers to understand how geopolymer concrete performs.
Discussion: A range of conditions were investigated to determine how to enhance and use this material in a variety of ways. The fresh characteristics of different mixes were studied using slump and Vee-Bee tests, and the characteristics of the cured concrete mixes were determined using flexural, compressive, and flexural fatigue tests. The results indicated that the use of manufactured sand and fly ash with high-molarity alkaline activators results in a geopolymer concrete with an excellent maximum resistance of 5.1 N/mm2 workability, strength, and fatigue properties, making it suitable for use in roadway pavement.
1 Introduction
The construction of concrete pavements must be improved to ensure effective transportation, reduce cost, and promote environmental sustainability, considering the effects of weather, fuel use, cost of repairs, and paving lifetime. Because the initial cost of rigid pavement is considerably higher than that of flexible pavement; the latter has been preferred to date, even though the maintenance cost of rigid pavement is lower. However, the life cycle cost of a pavement includes both the initial investment and maintenance costs. Often, flexible pavement is repaired using a thin white-topping layer of rigid concrete to realize the benefits of reduced maintenance costs at a lower initial investment (Bellum, 2022).
To reduce the initial cost of rigid pavement, fly ash, which contains pozzolanic aluminous and siliceous materials, is often combined in limited quantities with ordinary Portland cement (OPC) and large and fine aggregates (Sandanayake et al., 2018). The use of fly ash also lowers the life cycle cost of rigid concrete pavement in locations subject to heavy rainfall, such as India. India covers 5.66 million km2 and possesses the second-largest crossroad network in the world. Eighty five percent of traffic moves daily over the Indian highway network, causing the road network to deteriorate rapidly. Furthermore, the road network continues to expand; it is expected to add 18,637 km of roads in 2022 alone. Thus, the cost of road construction and maintenance in India is of critical concern (Zhang et al., 2016; Chen et al., 2021).
Furthermore, the construction of roads using OPC concrete consumes substantial energy and generates tremendous quantities of greenhouse gasses, constituting 5%–7% of global emissions (Savadkoohi and Reisi, 2020). As a result, various novel materials have been evaluated to reduce reliance on the ever-increasing manufacture of OPC (Guo et al., 2021). Critically, many of these materials are otherwise waste that must be disposed of, such as fly ash, ∼120 billion tons of which is produced by thermal power plants each year in India. When cement is entirely substituted by pozzolanic materials, such as fly ash, the result is geopolymer concrete (Huang and Ling, 2021).
Core geopolymer concrete elements include alkaline activators and raw materials. Ionic aluminum (Al) and silica (Si) geopolymers have the advantages of low cost, ease of usage, and applicability with alkaline activators typically containing sodium or potassium (Muthuramalingam and Dharmar 2022). Indeed, alkaline activators, such as potassium hydroxide or sodium silicate, have been used together with fly ash (Class F or C) or rice husk and manufactured sand (M-sand) to create different types of geopolymer concrete, which, when applied with alkaline activators, provide a lateral binding resolution equivalent to that of cement (Rath et al., 2020). The compressive strength of geopolymer concrete increases with increasing molar contents of such alkaline activators (Noaman et al., 2019). Furthermore, geopolymer concrete entirely comprising fly ash and M-sand has been shown to realize an 80% reduction in CO2 emissions compared to OPC concrete (Saxena et al., 2022). In addition to their mechanical and environmental benefits, the use of fly ash and M-sand results in a geopolymer concrete with considerable chemical defense against sulfate or magnesium attack and low shrinkage and creep (Ambikakumari Sanalkumar et al., 2019; Sun and Shi, 2022).
The raw materials used in geopolymer concrete are entirely responsible for its high calcium content and impurities play a lesser role. Silica and alumina present in the source materials are activated when exposed to alkaline activators, causing the formation of aluminosilicate gel. When bonded to loose particles, this gel forms geopolymer concrete upon bonding with other unreacted ingredients. Fly ash is composed of a vitreous phase, and a variety of other variables, such as type, concentration, and pH of the activator, affect the reaction. Curing of geopolymer concrete significantly impacts both the microstructure and mechanical properties of the material; it possesses excellent mechanical strength, a low creep frequency, excellent acid resistance, and poses very little shrinkage risk. Several studies have been published on the durability of geopolymer concrete cured at elevated temperatures using waste pozzolans. The polymerization process is more complex with ambient curing than with heat curing; hence, ambient curing is not recommended. Because sodium aluminate silicate hydrate (NASH) and calcium aluminate silicate hydrate (CASH) undergo polymerization at ambient temperatures, the results are not promising. Thus, the use of alternative materials, such as fly ash and M-sand, in concrete can improve the financial viability of roadway construction and repair while reducing environmental impacts. As geopolymer concrete represents a new construction material, it is necessary to quantify the effects of its constituents according to the intended application (Saxena and Gupta, 2022). The thickness of a geopolymer concrete white-topping pavement layer will depend on its strength and the loading of road traffic (Saxena et al., 2021). To the best of our knowledge, this is the first work that uses geopolymer concrete in road pavement.
Few scientific research studies have been conducted on the microstructure and longevity of fly ash-based geopolymer concrete (Amin et al., 2022; Derinpinar et al., 2022). The results of these studies have also been inconsistent. Inorganic geopolymer concrete’s compressive strength and workability should be summarized in accordance with previous studies regarding alkaline solutions used, their curing processes, and curing conditions (Zakka et al., 2021). Therefore, the purpose of this study was to investigate the fate of geopolymer concrete in the aforementioned distinct environments. Future research may be able to improve and adapt geopolymer concrete to a variety of contexts, as discussed in this study. To demonstrate this, geopolymer concrete specimens comprising fly ash, M-sand, and various molarities of alkaline activators were manufactured and evaluated for use in road pavements in terms of their fresh (slump and Vee-Bee) and cured (compressive, flexural, and fatigue strengths) characteristics compared to those of OPC (Koulinas et al., 2020). Different remediation laws apply to alkaline liquid molarities; an alkaline solvent has a 0.45 fly ash ratio and a 100% fly ash cement shift; therefore, the results of this study are expected to aid in the development of geopolymer concrete mixes for cost-effective and environmentally friendly roadway white-topping in India (Ojha and Aggarwal, 2022).
2 Materials and methods
This section explains the material selection in terms of material properties, concrete specimen preparation, and analysis methodology. The physical and chemical properties of raw materials are mentioned in the following sections.
2.1 Aggregates
To meet the requirements of the IS:2386 and IS:383 specifications of the Bureau of Indian Standards (BIS), locally available M-sand and crushed stones were used as fine and coarse aggregates, respectively. The fineness moduli for the aggregates were obtained based on their particle size distributions, determined as per IS 2386 (Part I): 1996. The properties of aggregates determined by laboratory tests are shown in Table 1.
A 10-M solution of NaOH was mixed with fly-ash powder to prepare sodium silicate solution. The alkaline solution was prepared by mixing NaOH powder with water and adding a suitable amount of fly ash (Li and Li, 2022). To obtain a homogenous solution, the mixture was well mixed for 40 min, allowed to cool to room temperature for 24 h, and then stored for 24 h before use.
2.1.1 Fine aggregate
In this study, M-sand was used as the fine aggregate to replace river sand. The chemical composition of raw materials was produced by forming and grinding fine stones to meet the specification requirements, as shown in Table 2. The sieve analysis results shown in Figure 1 indicate a fineness modulus of 3.37.
2.1.2 Coarse aggregate
Coarse aggregate should comprise hard, clean, dense, strong, and non-porous materials, such as crushed stone and/or gravel. The nominal size of the coarse aggregate used in this study was less than 20 mm; its physical properties are shown in Table 1, along with the relevant specification requirements. The sieve analysis results obtained using standard sieve sizes of 22.6, 20, 16, 12.5, 10, and 6.3 mm with 5 kg of aggregates are shown in Figure 2. The results indicate a fineness modulus of 4.28.
2.2 Fly ash
Fly ash (IS:3812) is a waste byproduct created by the burning of powdered carbon and other materials. The material specifications for fly ash for use in concrete in Bangalore, India, are given by IS:3812.
2.3 Alkaline solution and water
The alkaline activator used in this study was composed of sodium hydroxide and silicate (SiO2 = 29%, H2O = 55.9%, and Na2O = 13.7% by weight) (Cheah et al., 2015). The alkaline solution was prepared from pellets obtained from a local contractor after being dissolved in water for 24 h (Figure 3). The water in the concrete mix was used for partitioning and stabilizing, following the removal of all acid, oil, and salt contents, to ensure the strength of hardened cement and fresh concrete as per the IS:456-2000 specifications for water used with OPC concrete (Shehata et al., 2022).
2.4 Mix proportion
The mix design was developed to meet the geopolymer concrete grade M-40, according to IS:10362:2009; its compressive design strength was 40 MPa and its design workability was 25%–50%. The following parameters were applied in the preparation of concrete specimens.
• Fly-ash fineness was described in terms of specific surface areas.
• Sodium hydroxide and sodium silicate were used as the alkaline activator.
• Sodium hydroxide concentrations of 10, 12, and 14 M were evaluated.
• Sodium silicate solution concentration was 51.44% solid content.
• Sodium hydroxide to sodium silicate ratio by mass was 1.0.
The materials were mixed in the following proportions: fly ash, 400 kg/m3; fine aggregate, 670 kg/m3; coarse aggregate, 1,282 kg/m3; water-to-cement ratio, 0.3; sodium silicate, 60 kg/m3; and sodium hydroxide, 60 kg/m3.
2.5 Specimen casting and curing
Nine specimens, with a cube size of 150 × 150 × 150 mm3, were prepared for compressive strength testing, with three specimens each, after curing for 7, 14, and 28 days. Six 100 × 100 × 500 mm3 beam specimens of each mix were also prepared to test the flexural strength (three specimens) and fatigue strength (three specimens) after curing for 28 days. The specimens were cast by placing the concrete in molds in three equal layers. Each layer was vibrated 25 times using a vibratory hammer. The top of each mold was smoothened and leveled, and the outside surfaces were cleaned. The molds and their contents were kept in the curing room at a temperature of 27°C + 50°C and relative humidity not less than 90% for 24 h. All specimens were demolded after 24 h and cured in water at 27°C + 50°C. Before testing, the specimens were confirmed to have been dried by weighing before and after drying.
3 Test methods
3.1 Physical properties
3.1.1 Vee–Bee test
The Vee–Bee test was carried out prior to the casting of the specimens. To test their compressive strength, concrete specimens were cast in 100-mm cubes, while prisms were cast in 100 × 100 × 500 mm3 blocks to conduct flexural strength tests. The compressive strength tests and splitting tensile strength tests in this study were carried out in accordance with IS:516-1959 using a compression testing equipment, with a rate of loading controller and a capacity of 1,000 kN. The impact of curing conditions on the 28-day compressive strength was examined. To determine the average values of the mechanical properties at every age, a minimum of three test specimens were created.
3.2 Strength-influencing parameters
3.2.1 Alkaline solution
A fly ash-based geopolymer concrete is usually made with sodium silicate or potassium hydroxide as an alkaline solution. The alkaline solution typically comprises sodium hydroxide and one of these materials that has a molarity (M) of 7–10. The solution was prepared on the night before fly ash was added. In a concrete mix, coarse and fine aggregates are combined with raw components before the curing process is carried out. To fabricate high strength geopolymers, it was observed that the ratio of sodium silicate to sodium hydroxide should be 0.67–1.00. NaOH concentrations between 10 and 20 million milliliters have little effect on strength. A combination of good alkaline binders and other ingredients should be chosen before combining raw materials. This enhanced performance of concrete is dependent on the water-to-solid ratio, molarity of alkaline solution, water-to-binder ratio, ratio of SiO2 to Na2O by mass, and percentages of matching Na2O by SCM.
3.2.2 Curing process
Several factors affect the amount of geopolymer that sets, including the composition of the alkaline solution and the mass ratio of the alkaline liquid to the fly ash. However, the temperature at which geopolymers cure is the most important factor affecting their qualities. Concrete’s setting time decreases with the increase in curing temperature, and during the curing process, geopolymer concrete polymerizes. In just 3–4 h of curing, the polymerization of concrete becomes more rapid, allowing it to attain up to 70% of its original strength. Increased curing temperatures increase the rate of water loss, which can cause fracturing. Synchronization can only be achieved by bringing together all resources simultaneously. Temperature has an impact on geopolymer concrete performance. Both the inside and the outside of the concrete specimen need to be monitored for temperature changes. It is possible to achieve an even level of heat by using an oven or furnace. Using heat to speed up the first reaction phase is recommended after all precursors have been correctly hybridized and positioned. It ensures early strength gains at a rapid pace. The recommended polymerization temperature range is 60°C–100°C. Strength increases without loss of variability up to 200°C. Specimens lose strength more rapidly at temperatures above 600°C, and the loss is much steeper at temperatures above 800°C. An experimental prediction estimated a 65% loss of compressive strength above 800°C. Considering the test materials, alkaline solution molarity, and activator fusion with other components, there is a considerable difference between this result and the expected variance.
3.2.3 Workability of geopolymer concrete
Just like conventional concrete, concrete made of geopolymer requires water to cure. Geopolymer characteristics can be improved by adding water, but at elevated temperatures, the water will vaporize, causing an increase in porosity of the concrete. The flow of mortar is reduced when the concentration of NaOH and Na2SiO3 is increased. It took 110% ± 5%–135% ± 5% of geopolymer mortar to obtain a workable consistency. Adding superplasticizer or additional water makes mortar easier to handle; however, superplasticizers can negatively affect the strength of geopolymers. This results in greater strength when water is added to superplasticizers than when water is added to geopolymers alone.
3.2.4 Resistance against an aggressive environment
Fly ash-based geopolymers have been shown to be more resistant to extreme environmental conditions (Zhang et al., 2016; Chen et al., 2021). A feature such as this may be particularly beneficial to structures that are exposed to the ocean, e.g., wavebreakers or piers. The weight of geopolymer is only 0.5% less than that of regular concrete that has been submerged in 3% sulfuric acid. It has been reported that high-performance geopolymer materials degrade in acidic environments due to fissures that form in the amorphous polymer matrix, whereas low-performance geopolymer materials develop fragile grainy structures due to zeolite crystallization. The stability of the geopolymer depends on the presence of an aluminosilicate gel. Sulfuric and acetic acid solutions pose a greater threat to geopolymers prepared with sodium silicate activators than those prepared with sodium hydroxide. The geopolymer mortar specimens remained intact and exhibited no discernible color change after 18 weeks of exposure to 10% sulfuric acid. Through an optical microscope, it was possible to observe corroded structures on the exposed surface. Furthermore, it was discovered that specimens with a lower alkali concentration lost more weight than those with higher alkali concentrations, and this was a superior finding as compared to that found in OPC research. Using sodium oxide-containing formulations, studied the endurance of geopolymers in sulfuryl acid. There were different degradation rates for alkali concentrations in the presence of sulfuric acid. An optical microscopic examination showed no structural disintegration, but surface degeneration was clearly visible in specimens with low alkali contents. It should be noted that the specimen with the highest concentration of alkali lost more weight than that with the lowest concentration. However, a specimen with lower alkali levels had a lower degree of vigor. There was a significant difference in residual compressive strength between specimens with lower and higher alkali contents. While small fractures were found on some specimens under an optical microscope, there were no visible cracks on the specimens themselves. As sodium oxide is created by the alkaline activator in the presence of magnesium sulfate, specimen weight increases. There was a greater weight gain among specimens with less sodium oxide. Overall, all specimens weighed just a little more than conventional concrete. It is less likely that alkali silica gel will develop in geopolymers.
3.3 Mechanical properties
The influence of geopolymers on the mechanical properties of concrete was evaluated using a detailed experimental technique that included compressive tests, flexural tests, and fatigue tests.
3.3.1 Compressive strength
Compression tests were conducted according to IS:516-1959. Three 100 × 100 × 100 mm3 cubes were cast and tested. Tests were conducted on specimens between the ages of 7 and 28 days with 10 M, 12 M, and 14 M. The greatest load that could be delivered to the concrete cube that was measured as axial loading was applied vertically to the concrete cube specimen at a displacement rate of 1 mm/min. By dividing the highest applied load by the concrete cube’s cross-sectional area, the compressive strength was computed as shown in Eq. 1.
3.3.2 Flexural tensile strength
The flexural tensile strength of concrete beams was evaluated using the three-pin method, in accordance with IS:516-1959. Tests were conducted on specimens between 7 and 28 days old with 10 M, 12 M, and 14 M. At the center of the beam, an eccentric line load was applied uniformly. Axial loading was applied vertically at a displacement rate of 0.3 mm/min, as shown in Eq. 2
where fc is the compressive strength of the concrete, b varies from 0.33 to 0.94, and n is 1/2 or 2/3.
3.3.3 Fatigue testing
Fatigue tests were carried out to measure the behavior of the beams below the changing loading condition. The fatigue test was carried out at 55% and 65% loading conditions. The evaluation of minimum stress in fatigue was of particular interest in fabricating concrete pavements.
4 Results and discussion
4.1 Fresh concrete properties
Fresh concrete properties are defined by the slump test and Vee-Bee test during mixing time. This study evaluated the fresh concrete properties as a function of the molarity of the alkaline solution, and thereby quantifying the mix suitability for roadway white-topping. The fresh concrete properties were determined using the results of slump tests and Vee-Bee consistometer tests immediately after mixing to quantify the workability of each mix. The concrete slump test represents a simple, low-cost technique to determine the consistency of fresh concrete prior to setting. The slump value of the fresh concrete mix in this study was determined to be zero, indicating a very fluid mix (Safiuddin et al., 2012). The Vee-Bee test uses a consistometer to determine the mobility and compressibility of fresh concrete by measuring the time taken to change the shape of a mass of fresh concrete from one mold to another using a stopwatch; this time is reported as the Vee-Bee time (s). The results are shown in Figure 4, indicating that the 14-M mix was the most workable.
4.2 Concrete hardness properties
To determine the hardness of the concrete, we tested cubes and beams of the concrete specimens through compressive and flexural tests, respectively, after curing for 7, 14, and 28 days to meet the M40 grade of concrete (Figure 5).
4.2.1 Compressive strength
To assess concrete hardness in line with IS:516-1957, compressive strength testing was conducted on cubes cured for 7, 14, and 28 days, and they were properly dried. Each specimen was placed in the center of the compressive testing machine, and a load was applied at a rate of 140 kg/cm2 per minute until the sample broke, at which time the maximum load was recorded as the compressive strength. The results are shown in Figure 6 as the average of three specimen tests. Three samples for each of the following parameters were used: compressive strength, usage of compressive weight, and cross-sectional zones of the cubes, followed by the determination of the averages.
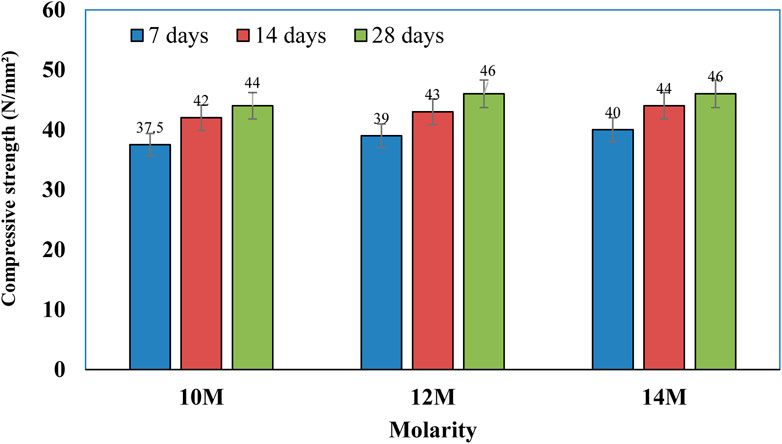
FIGURE 6. Compressive strength of geopolymer concrete mixes according to alkaline activator molarity. Numbers above bars represent mean values, and whiskers indicate standard error.
4.2.2 Flexural strength
After 28 days of curing, the dry beam specimens were tested in a flexural testing machine to determine the flexural strength of each mix. Each specimen was placed on the support points of the machine at the center of the loading system, and the loading point was brought into contact with the specimen. A vertical load was then applied at a rate of 140 kg/cm2 per minute until cracks were observed. The obtained flexural loads at failure are shown in Figure 7, illustrating a clear difference in results according to alkaline activator molarity.
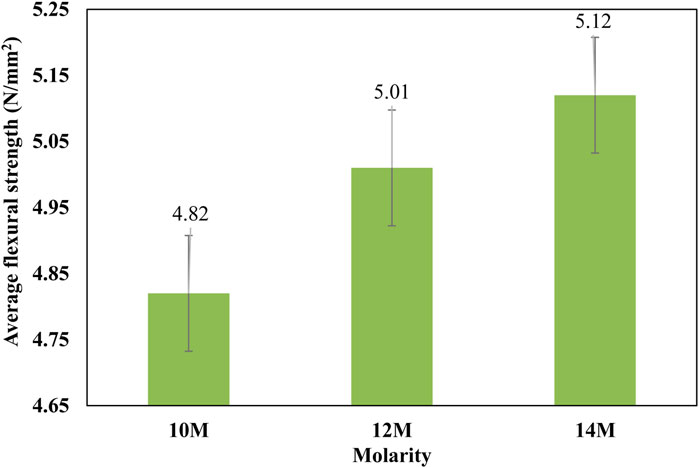
FIGURE 7. Flexural strengths of geopolymer concrete specimens according to alkaline activator molarity (after 28 days’ curing). Numbers above bars represent mean values, and whiskers indicate standard error.
4.2.3 Fatigue testing
Fatigue monitoring was used to measure the behavior of the beams below the changing loading condition. Beam samples were subjected to half-sine waves after cyclical load tests. To determine the fatigue life of the specimen, two stress levels (55% and 65% of failure load) of the static load were applied and repeated, and the number of repetitions until failure at each stress level was measured. The fatigue loading equipment flexure loads were collected, as an average of two samples, and the corresponding displacement was measured until failure was observed. The number of repetitions until failure for geopolymer concrete at different stress levels helps in the development of the fatigue model. Figure 8 shows that increasing the load from 55% to 65% decreased the load cycle count.
5 Energy and cost analysis
In the development of technology for the construction of buildings and pavements, resource utilization and expenditure need to be considered, and material cost is vital in these applications. This is essential for the country’s social and economic growth and is based on environmental positivity.
5.1 Material cost analysis
The development of the construction sector is increasing, but it needs to be economical. In building social change, the cost parameters of every project must be considered. The prices for standard concrete depend on the cost of the cement and material, including construction supplies, such as sand, fly ash, and water (Sandanayake et al., 2018). Material cost also depends on transportation, local availability, and market demand. The market price of the concrete M40 grade was taken as INR 4,600–5,400 per m3. The costs of materials per market price for material per kg are shown in Table 3.
In this study, the materials used were fly ash, coarse aggregate, M-sand, sodium silicate, and sodium hydroxide. The fly ash was purchased at USD 6.5/ton, and one bag contained 50 kg; coarse aggregate was purchased at 8.3 USD/ton; M-sand at 10.9 USD/ton; and cement at 4.78 USD for 50 kg. Therefore, the material used per kg cost was INR 0.5 per kg for fly ash, USD 0.007 per kg for M-sand, USD 0.1 per kg for cement, and USD 0.008 per kg for coarse aggregate. Sodium hydroxide and sodium silicate cost USD 0.33 per kg (Table 4). The cost of OPC for 1 m3 production is shown in Table 5. (Note that 1 USD = 78 INR).
The amount saved in 1 m3 production of geopolymer concrete and OPC is shown in Table 6; the production cost of 1 m3 OPC is higher than that of 1 m3 of geopolymer concrete, being 8.2% higher for OPC class M40 and 7.8% for class M50.
5.2 Energy analysis
Energy consumption and building services have increased owing to the widespread growth of building urbanization (Saxena, Gupta, and Sharma, 2021). The indicator for energy research into building resources is embodied energy, as shown in Table 7.
Embodied energy is the energy expended for any service or good; it includes energy expended in the removal and processing of natural sources, manufacturing the resources, and transferring and carrying the products (Ojha and Aggarwal, 2022). Embodied energy can be used to define the energy cost and actual extra cost of buildings and has been accepted in different manufacturing and mining procedures (Huang and Ling, 2021). Every concrete structure is a composite mixture of materials. The maintenance of concrete constructions over the design lifetime is also included in their embodied energy. Common construction materials and their embodied energy are shown in Tables 8, 9.
The embodied energy for the 1 m3 OPC output was higher than that of the geopolymer concrete output from the aforementioned calculations. OPC grades M40 and M50 had embodied energies 43.8% and 46.2% higher than that of geopolymer concrete, respectively (Table 10). Therefore, the energy savings of geopolymer concrete were concluded to be higher than those of OPC.
5.3 Recommendations
An alkaline medium containing high concentrations of fly ash, M-sand, silica, and other components allows high-strength geopolymer concrete to be prepared. Li et al. (2022), Singh et al. (2021), and Panizza et al. (2020) developed high-strength geopolymer concrete from multiple sources; however, very few studies have been conducted using materials from a single source. Alumina–silica base materials can be combined to produce cost-effective geopolymer concrete by using binary or ternary combinations. When highly concentrated alkali solution (>10 M) is added to unary blends, high-strength geopolymer concrete can be produced economically, thereby offering research and development opportunities for this material.
According to Yuan et al. (2022), the compressive strength increases as the concentration of alkali solution increases, but beyond that point, the strength decreases. As a result of high concentrations of OH* in the solution, polycondensation was inhibited and the strength of the solution was reduced. To create high-quality concrete, the ideal molarity should fall between 10 M and 14 M. When alkaline solutions are used at low concentrations, alkali-activated concrete is produced rather than geopolymer concrete. A better understanding of the differences between alkali-activated concrete and geopolymer concrete microstructural studies is required.
Trials are conducted to formulate mix design procedures. Hence, a sophisticated mix design process is necessary because several variables, such as alkali solution and polymeric binders, must be considered. Although mix design procedures vary according to material sources, the technique can be applied to any material by modifying it appropriately. It is vital that a mix design procedure be developed for geopolymer concrete. In structural elements, geopolymer concrete is seldom used due to the lack of a proper mix design methodology, despite the fact that it offers improved structural properties and durability.
Sandanayake et al. (2018) and Ojha and Aggarwal (2022) studied the durability of geopolymer concrete in the short-term, but few long-term studies have been conducted. The long-term study of geopolymer concrete might prove beneficial for applications in commercial and industrial settings. Sodium silicate improves the ductility of geopolymer concrete, and thus, the seismic performance of geopolymer concrete reinforced with steel fibers can be an important research avenue. Owing to its quick setting characteristics and high resistance to corrosion caused by marine water, geopolymer concrete is a suitable material for use in marine structures. By reducing stress losses in prestressed concrete, geopolymer concrete with high corrosion resistance and less shrinkage can create a revolution in prestressing.
Geopolymer concrete can be produced with high strength using steam curing, low amounts of calcium fly ash, and alkaline liquid; however, there is considerable room for research into geopolymer concretes with lower strength using polymerization activation at room temperature. Alternative alkaline liquids may provide a more stable alkaline solution; hence, their usage merits exploration. Geopolymer mixtures can easily be constructed based on the theory and understanding of conventional mixture proportions, with comparable results in terms of workability and strength for aggregate gradation, strength, and angularity. This study provided recommendations regarding the formulation of mixture proportions and the use of superplasticizers to improve workability and compatibility and demonstrated the superior tensile strength of geopolymer concrete. Research on the shear strength of geopolymer concrete in beam applications is currently being conducted to use this property.
5.4 Future prospects
Synthesis of geopolymers from agro-industrial waste, natural materials, and inexpensive items among academic and industry personnel is becoming increasingly popular. Despite the numerous applications of geopolymer, it remains necessary to develop a code of practice for geopolymer based on research and field data for scaling purposes. Long-term studies are required to determine the durability of geopolymer concrete-based foundations over long periods. However, the price of activators remains a major barrier to the widespread use of geopolymer. Therefore, there should be a focus on reducing the total cost of geopolymerization and its energy footprint. All stages of the transportation, production, and distribution process should be examined to find ways to conserve energy, as this energy has a strong correlation with costs and carbon imprints. In addition to recycling industrial waste and byproducts, recycling municipal and agricultural waste can contribute to the sustainability of geopolymers.
The existing literature does not provide information regarding the biological effects and cytotoxicity of geopolymer on humans and the environment. A wide range of positive and negative effects, and safety concerns associated with the widespread use of geopolymers, need to be reported. Heavy metals and hazardous substances are immobilized in geopolymers, which has become a prominent area of research. It is significantly safer to dispose of these materials in a geopolymer matrix than to landfill them, as decomposition in landfill sites can cause adverse effects on humans, the surrounding soil, air, underground water, and surface water (Figure 9) (Sandanayake et al., 2018).
6 Conclusion
This study investigated the use of alkali activation in conjunction with gas-releasing agents, such as fly ash, for the manufacture of geopolymer concrete. A geopolymer concrete formulation was composed of three groups, each with different alkali contents, but with the same dosage and water-to-binder ratio. We aimed to investigate the effects of an alkali activator on fly ash reaction kinetics and the properties of geopolymer concrete. The following conclusions were drawn.
• Geopolymer concrete containing fly ash increased in compression strength, with increasing curing temperature, sodium silicate-to-sodium hydroxide solution ratio (up to 2.5 only), and alkaline solution concentration, but decreased with an increasing water–geopolymer solids ratio and alkaline solution concentration. Geopolymer concrete was strengthened by increasing the rest period duration during the heat curing regime. Early strength was achieved through heat curing.
• Geopolymer concrete with 14 M and fly ash exhibited greater flexural strength than its control concrete by as much as 83%.
• The flexural fatigue behavior of concrete should be predicted under various stress conditions caused by transit loads. Capacity increased compressively and bent with increased molarity. The maximum resistance was 5.1 N/mm3 for increased molarity; 55% fatigue power and 65% intervals declined as the load increased.
• Energy research revealed that compared to OPC, geopolymer concrete saved approximately 44% of embodied energy.
• Structurally sound, environmentally benign geopolymer matrices can be created from a variety of industrial, municipal, and agricultural wastes. An important factor determining the final performance of the product is the quantity of reactive silica and alumina species.
• Geopolymer can be manufactured more cost-effectively by optimizing the primary materials involved in the manufacturing process, particularly alkaline activators, and fostering an eco-friendly circular economy. The geopolymer’s contribution to the development of new materials, the reduction of pollution, and the improvement of the economy contributes to its circular economy.
To conclude, geopolymer concrete offers a sustainable alternative to conventional materials and its commercial application can be used to dispose of waste and save energy.
Data availability statement
The datasets presented in this study can be found in online repositories. The names of the repository/repositories and accession number(s) can be found in the article/Supplementary Material.
Author contributions
SS wrote the paper and designed the methodology. PS revised the paper and validated it. SH revised the paper and collected data. BA supervised and cross-checked information. AS and AR wrote the paper and supervised it. MK was the fund organizer and supervised the study.
Conflict of interest
The authors declare that the research was conducted in the absence of any commercial or financial relationships that could be construed as a potential conflict of interest.
Publisher’s note
All claims expressed in this article are solely those of the authors and do not necessarily represent those of their affiliated organizations, or those of the publisher, the editors, and the reviewers. Any product that may be evaluated in this article, or claim that may be made by its manufacturer, is not guaranteed or endorsed by the publisher.
References
Ambikakumari Sanalkumar, K. U., Lahoti, M., and Yang, E. (2019). Investigating the potential reactivity of fly ash for geopolymerization. Constr. Build. Mater. 225, 283–291. doi:10.1016/j.conbuildmat.2019.07.140
Amin, M., Elsakhawy, Y., Abu, K., and Abdelsalam, B. A. (2022). Behavior evaluation of sustainable high strength geopolymer concrete based on fly ash, metakaolin, and slag. Case Stud. Constr. Mater. 16, e00976. doi:10.1016/j.cscm.2022.e00976
Bellum, R. R. (2022). Investigation on the Accelerated Pavement Test Track (APTT) in the development of road network using geopolymer concrete. Clean. Mater 4, 100074. doi:10.1016/j.clema.2022.100074
Cheah, C. B., Part, W. K., and Ramli, M. (2015). The hybridizations of coal fly ash and wood ash for the fabrication of low alkalinity geopolymer load bearing block cured at ambient temperature. Constr. Build. Mater. 88, 41–55. doi:10.1016/j.conbuildmat.2015.04.020
Chen, L., Gao, X., Hua, C., Gong, S., and Yue, A. (2021). Evolutionary process of promoting green building technologies adoption in China: A perspective of government. J. Clean. Prod. 279, 123607. doi:10.1016/j.jclepro.2020.123607
Derinpinar, A. N., Karakoç, M. B., and Özcan, A. (2022). Performance of glass powder substituted slag based geopolymer concretes under high temperature. Constr. Build. Mater. 331, 127318. doi:10.1016/j.conbuildmat.2022.127318
Guo, F., Meng, S., and Sun, R. (2021). The evolution characteristics and influence factors of carbon productivity in China’s industrial sector: From the perspective of embodied carbon emissions. Environ. Sci. Pollut. Res. 28, 50611–50622. doi:10.1007/s11356-021-14271-0
Huang, Q., and Ling, J. (2021). Measuring embodied carbon dioxide of the logistics industry in China: Based on industry stripping method and input-output model. Environ. Sci. Pollut. Res. Int. 28, 52780–52797. doi:10.1007/s11356-021-16190-6
Koulinas, G. K., Xanthopoulos, A. S., Tsilipiras, T. T., and Koulouriotis, D. E. (2020). Schedule delay risk analysis in construction projects with a simulation-based expert system. Buildings 10, 134. doi:10.3390/buildings10080134
Li, J., Sun, Z., Wang, L., Yang, X., Zhang, D., Zhang, X., et al. (2022). Properties and mechanism of high-magnesium nickel slag-fly ash based geopolymer activated by phosphoric acid. Constr. Build. Mater. 345, 128256. doi:10.1016/j.conbuildmat.2022.128256
Li, Y.-Y., and Li, H. (2022). China’s interregional embodied carbon emissions: An industrial transfer perspective. Environ. Sci. Pollut. Res. Int. 29 (3), 4062–4075. doi:10.1007/s11356-021-15694-5
Muthuramalingam, P., and Dharmar, B. (2022). Synthesis of slag – ash – Phosphate based geopolymer concrete in the production of sustainable concrete under ambient curing conditions. Iran. J. Sci. Technol. Trans. Civ. Eng. 89, 4243–4254. doi:10.1007/s40996-022-00881-2
Noaman, M. A., Karim, M. R., and Islam, M. N. (2019). Comparative study of pozzolanic and filler effect of rice husk ash on the mechanical properties and microstructure of brick aggregate concrete. Heliyon 5, e01926. doi:10.1016/j.heliyon.2019.e01926
Ojha, A., and Aggarwal, P. (2022). Fly ash based geopolymer concrete: A comprehensive review. Silicon 14, 2453–2472. doi:10.1007/s12633-021-01044-0
Panizza, M., Natali, M., Garbin, E., Ducman, V., and Tamburini, S. (2020). Optimization and mechanical-physical characterization of geopolymers with construction and demolition waste (CDW) aggregates for construction products. Constr. Build. Mater. 264, 120158. doi:10.1016/j.conbuildmat.2020.120158
Rath, B., Debnath, R., Paul, A., Velusamy, P., and Balamoorthy, D. (2020). Performance of natural rubber latex on calcined clay – based glass fiber – reinforced geopolymer concrete. Asian J. Civ. Eng. 21, 1051–1066. doi:10.1007/s42107-020-00261-z
Safiuddin, Md., West, J. S., and Soudki, K. A. (2012). Properties of freshly mixed self-consolidating concretes incorporating rice husk ash as a supplementary cementing material. Constr. Build. Mater. 30, 833–842. doi:10.1016/j.conbuildmat.2011.12.066
Sandanayake, M., Gunasekara, C., Law, D., Zhang, G., and Setunge, S. (2018). Greenhouse gas emissions of different fly ash based geopolymer concretes in building construction. J. Clean. Prod. 204, 399–408. doi:10.1016/j.jclepro.2018.08.311
Savadkoohi, M. S., and Reisi, M. (2020). Environmental protection based sustainable development by utilization of granite waste in Reactive Powder Concrete. J. Clean. Prod. 266, 121973. doi:10.1016/j.jclepro.2020.121973
Saxena, R., and Gupta, T. (2022). Assessment of mechanical, durability and microstructural properties of geopolymer concrete containing ceramic tile waste. J. Mater. Cycles Waste Manag. 24, 725–742. doi:10.1007/s10163-022-01353-5
Saxena, R., Gupta, T., Sharma, R. K., and Panwar, N. L. (2021). Influence of granite waste on mechanical and durability properties of fly ash – based geopolymer concrete. Environ. Dev. Sustain. 23, 17810–17834. doi:10.1007/s10668-021-01414-z
Saxena, R., Gupta, T., Sharma, R. K., and Siddique, S. (2022). Mechanical, durability and microstructural assessment of geopolymer concrete incorporating fine granite waste powder. J. Mater. Cycles Waste Manag. 24, 1842–1858. doi:10.1007/s10163-022-01439-0
Shehata, N., O., Mohamed, A., Taha, E., Ali, M., and Olabi, A. (2022). Geopolymer concrete as green building materials: Recent applications, sustainable development and circular economy potentials. Sci. Total Environ. 836, 155577. doi:10.1016/j.scitotenv.2022.155577
Singh, R. J., Raut, A., Murmu, A. L., and Jameel, M. (2021). Influence of glass powder incorporated foamed geopolymer blocks on thermal and energy analysis of building envelope. J. Build. Eng. 43, 102520. doi:10.1016/j.jobe.2021.102520
Sun, X., and Shi, Q. (2022). Factors influencing embodied energy trade between the belt and road countries: A gravity approach. Environ. Sci. Pollut. Res. Int. 29, 11574–11589. doi:10.1007/s11356-021-16457-y
Yuan, L., Ma, Y., Zhang, J., Men, J., Sun, T., Zhao, H., et al. (2022). Orthogonal analysis and mechanism of compressive strength and microstructure of the metakaolin-fly ash geopolymer. Case Stud. Constr. Mater. 17, e01154. doi:10.1016/j.cscm.2022.e01154
Zakka, W. P., Abdul Shukor Lim, N. H., and Chau Khun, M. (2021). A scientometric review of geopolymer concrete. J. Clean. Prod. 280, 124353. doi:10.1016/j.jclepro.2020.124353
Keywords: fly ash, manufactured sand, pavement white-topping, geopolymer concrete, compressive strength, flexural strength
Citation: S. S, Shakor P, Hasan S, Awuzie BO, Singh AK, Rauniyar A and Karakouzian M (2023) Evaluating the potential of geopolymer concrete as a sustainable alternative for thin white-topping pavement. Front. Mater. 10:1181474. doi: 10.3389/fmats.2023.1181474
Received: 07 March 2023; Accepted: 03 April 2023;
Published: 15 May 2023.
Edited by:
Li Li, Northwest A & F University, ChinaReviewed by:
Erol Yilmaz, Recep Tayyip Erdoğan University, TürkiyeAyaz Ahmad,University of Galway, Ireland
Waqas Ahmad, COMSATS University Islamabad, Pakistan
Majid Ali, Capital University of Science & Technology, Pakistan
Copyright © 2023 S., Shakor, Hasan, Awuzie, Singh, Rauniyar and Karakouzian. This is an open-access article distributed under the terms of the Creative Commons Attribution License (CC BY). The use, distribution or reproduction in other forums is permitted, provided the original author(s) and the copyright owner(s) are credited and that the original publication in this journal is cited, in accordance with accepted academic practice. No use, distribution or reproduction is permitted which does not comply with these terms.
*Correspondence: Pshtiwan Shakor, cHNodGl3YW4uc2hha29yQGFsdW1uaS51dHMuZWR1LmF1; Atul Kumar Singh, YXM5ODkyQHNybWlzdC5lZHUuaW4=