- 1School of Materials Science and Engineering, Henan University of Science and Technology, Luoyang, China
- 2National Engineering Laboratory for Bearing Tribology, Henan University of Science and Technology, Luoyang, China
Polyether ether ketone (PEEK) is one of the representatives of special engineering plastics. Due to the high molding temperature, the molding method of ordinary plastics and cavity abrasives are difficult to meet the requirements. In view of this, pure PEEK was prepared by vacuum hot pressing sintering technology at different sintering temperatures. The mechanical properties and microstructure characterization results showed that the pure PEEK prepared at 350 °C showed excellent friction and wear properties. Then PEEK and CF/PEEK composites were prepared at the optimum sintering temperature. The friction experiments of prepared materials were carried out using UMT-2. The effects of ambient humidity on the tribological properties, wear mechanism and antistatic properties of prepared materials were systematically studied. The surface analysis and properties of the materials were measured by 3D profiler, scanning electron microscope, friction electrostatic tester. The results showed that friction coefficient of PEEK and CF/PEEK composite changed slightly with increase of ambient humidity. The wear rate of PEEK decreased firstly and then increases, which reached the lowest of 3.09 × 10−5 mm3/Nm when the ambient humidity was 40%. The wear rate of CF/PEEK composite changed slightly, which was significantly lower than that of PEEK, and the main wear mechanism was adhesive wear. The surface friction static electricity of PEEK and CF/PEEK composites decreased with the increase of humidity.
1 Introduction
PEEK is a semi-crystalline aromatic thermoplastic engineering plastic, whose unique structure enables it to have excellent self-lubrication and other excellent properties (Yan et al., 2020; Zhang et al., 2020; Hron et al., 2021). With development of manufacturing industry, the bearing capacity and wear resistance of a single polymer material are not enough to meet different requirements. In order to improve its comprehensive performances, the most effective method is to compound the material (Abdul, 2021; Li et al., 2021; He et al., 2022; Huang et al., 2022). Carbon fiber (CF) has excellent properties such as wear resistance, high electrical conductivity (Bijwe et al., 2013; Guo et al., 2017), which is widely used as a reinforcement material and is often doped with resin to prepare high-performance composite materials (Qiu et al., 2021).
J. Paulo Davim (Davim and Cardoso, 2005) et al. conducted a study on the friction and wear properties of CF reinforced polyether ether ketone composites under water lubrication. The study found that surface roughness, one-way sliding speed, and contact stress all have a significant impact on the friction coefficient. Zhang Zhiyi (Zhang et al., 1996) et al. prepared CF/PEEK composites with different carbon fiber content, and studied the friction properties of the composites under different loads. The study showed that when the carbon fiber content was between 10% and 20%, CF/PEEK composites exhibited good friction and wear properties. JJ Sha (Sha et al., 2013) et al. analyzed the interfacial adhesion between CF and the matrix material, and the analysis results showed that the interfacial strength of unidirectional CF reinforced phenolic resin matrix composites was similar to that of bidirectional CF reinforced phenolic resin matrix composites, but showed different values. The interfacial strength of unidirectional CF reinforced phenolic resin matrix composites is slightly higher than that of bidirectional CF reinforced phenolic resin matrix composites. The difference in interfacial strength may be caused by the thermally induced residual stress caused by the mismatch of the thermal expansion coefficient between CF and the matrix. Huang Yudong (Guo et al., 2010) et al. prepared CF reinforced resin matrix composites and conducted some performance analysis on them. The research results showed that the changes in tensile strength and thermal curing temperature of the composites were caused by defects on the CF surface. Due to the brittle fracture of CF, the change trend of roughness was opposite to the change trend of strength. Wang Huaiyuan (Wang et al., 2007) et al. studied the friction and wear properties of whisker and CF filler reinforced polytetrafluoroethylene composites under dry, wet, and alkaline conditions. The results show that due to the proper cooling and boundary lubrication of alkali, the friction properties of CF/PTFE composites under alkaline solution conditions are superior to those under dry and wet conditions. In the water state, the tribological performance of carbon fiber/polytetrafluoroethylene is better than that of titanate whisker/polytetrafluoroethylene. The sliding wear rate of PTFE composites modified with hydrophilic fillers is high under water lubrication conditions. Ziwei Guan (Guan et al., 2020) et al. investigated the influence of high hydrostatic pressure on tribological characteristics of CF/PEEK against 431SS. The results suggest that the average friction coefficient decreases with increased hydrostatic pressure. Hydrostatic pressure helps reduce the wear rates of CF/PEEK and 431SS. As the pressure increases, the main wear and friction mechanism of CF/PEEK changes from adhesive wear to fatigue wear, while the main wear mechanism of 431SS is abrasive wear. Yingna Liang (Liang et al., 2020) et al. study the tribological properties of friction pair between 316L stainless steel and CF/PEEK with nonsmooth surface under seawater lubrication. The experimental results indicate that the friction process of the smooth surface friction pair is mainly based on abrasive wear and adhesive wear. Pits on the specimen surface produce a hydrodynamic effect and store wear debris. The friction process of the nonsmooth surface friction pair is mainly controlled by a ploughing mechanism with only a slight amount of adhesive wear. The geometrical arrangement of the elliptical and triprism pits increases the convergence gap range and produces a higher bearing capacity.
Most polymer materials have good insulation. However, it is easy to accumulate charge or generate high potential static electricity on the surface during friction process (Jian et al., 2009; Xu et al., 2018), which could result in electrical corrosion speeding up the wear of machines and parts, and even causes factory fire in serious cases. Therefore, it is necessary to eliminate frictional static electricity of polymer. The composite conductive polymer material is prepared by combining the polymer matrix material with conductive fillers (carbon fiber, graphene, and metal powder, etc.) (Lapčinskis et al., 2021), which not only retains the excellent properties of the polymer, but also obtains good electrical conductivity. Moreover, environment such as humidity also affect tribo-static electricity, which is rarely involved.
At present, the main molding methods of polymer-based materials include: molding, extrusion, injection molding, melt spinning and 3D printing technology. PEEK is one of the representatives of special engineering plastics. Due to the high molding temperature, the molding method and cavity abrasives of ordinary plastics are difficult to meet the requirements. In this paper, PEEK materials were prepared by vacuum rapid hot-pressing sintering technology. The optimum sintering temperature was determined by the mechanical properties and microstructure characterization results of pure PEEK. Then CF/PEEK composites were prepared at the best process parameters, and the effects of different humidity on their tribological properties and tribostatic properties were systematically investigated.
2 Experimental details
In this study, PEEK powder with a grade of 450 G and particle size of 1200 mesh was provided by Dongguan Chuanao Engineering Plastic Material Co., Ltd. The reinforcing material used in this experiment is high modulus carbon fiber (CF) powder, with an average particle size of approximately 900 mesh, provided by Carbon Technology (Shenzhen) Co., Ltd. Absolute ethanol (analytical pure) was obtained from Tianjin Yongda Chemical Reagent Co., Ltd.
Firstly, pure PEEK was prepared by FHP-828 rapid hot pressing sintering furnace. The optimal molding temperature was explored through the results of the basic properties characterization. Then, pure PEEK and 20% wt. CF/PEEK composites are prepared at the optimal sintering parameters, which are as follows: sintering temperature 350°C, vacuum degree about 10−1 Pa, pressure 13 MPa, holding time 10 min.
The molecular composition and molecular structure of the prepared PEEK were analyzed using a Japanese Shimadzu model IRTracer-100 Fourier transform infrared spectrometer, and whether the functional groups of the PEEK powder changed after sintering was compared. The test spectral range is 4000 to 600 cm−1. The characteristic peak diffraction angles of PEEK and CF/PEEK were characterized using a D8-advanced X-ray diffractometer. The detection conditions were as follows: the scanning step length was 0.02°/step, the scanning rate was 5°/min, and the scanning range was 10°–50°.
The Shore hardness of PEEK composite was tested using a D-type Shore hardness tester. Place the sample on a firm surface, hold the hardness tester in your hand, press the indenter smoothly into the sample at a position about 12 mm from the edge of the sample, and read when the two surfaces fully contact. Test 5 times at different locations and calculate the average value. This hardness tester complies with the relevant provisions of GB/T 531.1-2008. The CMT6103 electronic universal testing machine was used to conduct tensile tests on PEEK materials prepared at different temperatures. The tensile samples were prepared in accordance with the national standard GB/T528-2009, and the tensile rate was 2 mm/min.
UMT-2 is used to carry out the tribological tests under dry sliding friction and different ambient humidity of 20%, 40%, 60%, and 80%. The friction pair is GCr15 stainless steel ball (diameter of 6.35 mm, Ra of 0.02 µm and HRC 62), the applied load is 50 N, the rotation speed is 300 r/min, the rotation radius is 4 mm, and the test time is 30 min. The depth and width of wear scar were measured by 3D profilometer, and the volumetric wear rate of PEEK and CF/PEEK composites were calculated. The worn surface morphology was characterized by SEM.
Friction electrostatic test: when the friction test is carried out, GCr15 ball is fixed as the upper test piece, and PEEK matrix composite is rotated clockwise as the lower test piece. During friction separation, the non-contact FMX-003 electrostatic tester is used to detect the friction static electricity on the surface of the separated PEEK based composite material. The smaller the test electrostatic voltage value is, the better the antistatic property of the material is.
3 Result and discussion
3.1 Effect of sintering temperature on the structure of PEEK materials
Figure 1 shows the XRD spectra of PEEK materials prepared at different sintering temperatures. It can be clearly seen that PEEK has four relatively strong diffraction peaks at different sintering temperatures, which appear at the same positions. Diffraction angle corresponding to four crystal characteristic diffraction peaks 2θ are 18.71°, 20.76°, 22.81°, and 22.83°, respectively, and the corresponding crystal faces are (110), (111), (200), and (211), respectively. The diffraction peaks are basically consistent with the positions and shapes of the diffraction peaks in literature (Xu et al., 2006). It can be seen that the processing and molding process does not change the crystalline state of PEEK. On the other hand, even if the temperature rises to 350 °C, PEEK does not undergo decomposition and cracking reactions.
The infrared spectra of PEEK materials prepared at different sintering temperatures are shown in Figure 2. It can be seen that the positions and shapes of the characteristic peaks of the materials prepared at the three sintering temperatures are approximately the same, indicating that the molding temperature does not change the functional groups in the PEEK structure. Among them, 840 cm−1 and 764 cm−1 are the C-H plane flexural vibration absorption bands of the benzene ring, and 840 cm−1 is the characteristic peak of the aromatic ring para substitution, 929 cm−1 is the symmetric stretching vibration band of R-CO-R, 1163 cm−1 is the C-H plane flexural vibration absorption band of the benzene ring in the aromatic ether or aromatic ketone structure, 1226 cm−1 is the asymmetric stretching vibration band of R-O-R, 1308 cm−1 is the R-CO-R benzene ring in-plane vibration band, 1597 cm−1 and 1501 cm−1 are in-plane vibration bands of the R-O-R benzene ring, and 1,652 cm−1 is a C=O stretching vibration band.
3.2 Effect of sintering temperature on mechanical properties of pure PEEK
The hardness values of PEEK prepared at the three sintering temperatures are shown in Table 1. It can be seen that the Shore hardness of PEEK increases slightly when the sintering temperature is between 340°C and 350°C. When the sintering temperature is 340°C, the melting point of the PEEK material is not reached, and the PEEK powder is pressed and molded by hot pressing. At this time, the compactness is poor, resulting in a lower hardness value of the prepared PEEK material; When the sintering temperature is 345°C, the temperature is near the melting point of PEEK, and the powder PEEK begins to melt to form a molten state. Due to uneven heating in the sintering furnace, some powders do not fully form a molten state, and the molten state is mixed with powder particles. At this time, the density of PEEK is improved, and the hardness value slightly increases; When the sintering temperature reaches 350°C, the PEEK powder completely forms a molten state in the abrasive tool, and slightly flows out of the molten PEEK. During the sintering process, the prepared PEEK material reaches a relatively dense state by controlling a constant pressure, at which point the hardness value of the prepared PEEK material is the maximum.
Figure 3 shows the stress-strain curves of PEEK materials prepared at three sintering temperatures. As can be seen from the figure, with the increase of sintering and molding temperature, the tensile strength of PEEK materials gradually increases, the elongation at break slightly increases, and the elastic modulus gradually increases from 6.246 to 6.416 GPa. Due to the insufficient melting of PEEK at low sintering temperatures, the liquid and solid phases are mixed together, and the two-phase contact zone between the liquid and solid phases destroys the continuity of the PEEK matrix material. Therefore, the tensile properties of PEEK materials at low sintering temperatures are poor. As the sintering temperature continues to rise, PEEK melts more fully, forming a single liquid phase. During the cooling and solidification process, PEEK molecules are closely aligned, preserving the good continuity of the PEEK matrix material, thereby improving the tensile properties of the PEEK material.
3.3 Effect of sintering temperature on friction and wear properties of pure PEEK
The instantaneous friction coefficient and average friction coefficient of PEEK at three sintering temperatures in the rotary sliding dry friction state are shown in Figure 4. From Figure 4A, it can be seen that the instantaneous friction coefficient is divided into two stages. The first stage is the running-in stage. From the beginning of the test, the friction coefficient continues to increase with time. Then, at the second stage, the friction coefficient gradually stabilizes until the end of the test. During the running-in stage, the GCr15 ball rubs against the polished surface of PEEK material, resulting in a constant increase in friction coefficient. During the stabilization stage, the counter GCr15 ball has worn through the polished surface of the PEEK material, causing counter grinding with the PEEK substrate, so the friction coefficient is relatively stable. The friction coefficient of PEEK with a sintering temperature of 340°C fluctuates greatly when it reaches a stable stage. The friction coefficient curve of PEEK with a sintering temperature of 345°C at the stable stage began to be relatively stable, with no fluctuations, but there were significant fluctuations before the end of the test. The friction coefficient curve of PEEK at a sintering temperature of 350°C during the stable stage has been very stable, without fluctuations until the end of the test. Because the higher the sintering temperature, the better the compactness of the formed PEEK material, which can play an effective support role when subjected to external forces. Therefore, the friction coefficient fluctuation during the stable stage of PEEK with a sintering temperature of 350°C is small. Figure 4B is a comparison diagram of the average friction coefficient of PEEK materials under three sintering temperatures. From Figure 4B, it can be intuitively seen that as the sintering temperature increases, the average friction coefficient of PEEK gradually decreases from 0.34 to 0.25. The average friction coefficient of PEEK prepared at 350°C decreases by about 24% compared to the average friction coefficient of PEEK prepared at 340°C. Therefore, when the sintering temperature is 350°C, PEEK materials exhibit good friction properties.
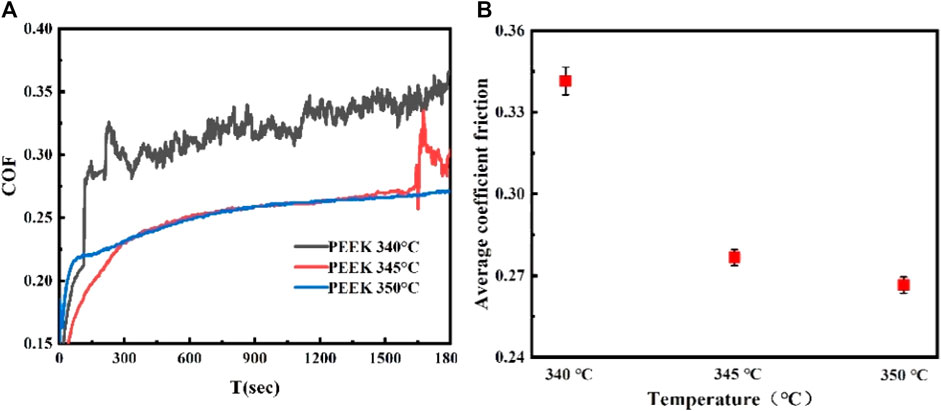
FIGURE 4. Friction coefficient of PEEK for three sintering temperatures (A) instantaneous friction coefficient and (B) average friction coefficient.
The wear rates of PEEK prepared at three sintering temperatures are shown in Figure 5. As can be seen from the figure, with the increase of sintering temperature, the wear rate of PEEK material shows a significant decrease trend, from 1.32*10−3 mm3/Nm reduced to 5.13*10−5 mm3/Nm. Under the same friction conditions, the wear rate of PEEK sintered at 350°C decreases by two orders of magnitude compared to that of PEEK sintered at 340°C. In addition, it can be seen from the figure that the wear rate error range of PEEK prepared at sintering temperature of 350°C is smaller than that of PEEK prepared at 340°C. This indicates that the bearing capacity and stability of PEEK sintered at 340°C are poor, and therefore, the wear performance of PEEK sintered at 340°C is poor. On the contrary, PEEK sintered at 350°C has good compactness and has a certain bearing capacity against external pressure, so it exhibits certain good wear performances.
3.4 The effects of ambient humidity on friction coefficient and wear rate
Figure 6 shows the friction coefficients and wear rate of PEEK and CF/PEEK with four ambient humidity. It can be seen that the ambient humidity has little influence on the instantaneous friction coefficient and has a certain influence on the fluctuation of the friction coefficient. When the humidity is 20%, there is no water film on the surface of the materials, which is affected by the stable van der Waals force. At this time, the instantaneous friction coefficient is relatively stable. When the humidity increases to 40%, a discontinuous water film forms on the material surface, which is not only subject to stable van der Waals force, but also subject to unstable adhesion force, so the instantaneous friction coefficient has a certain fluctuation. When the humidity is 60%, water molecules form a continuous water film on the surface of the material, which is subject to stable van der Waals force and adhesion force, so the instantaneous friction coefficient basically does not fluctuate. When the humidity continuously increases to 80%, the capillarity of water molecules increases, forming a relatively thick water film on the surface of the material. At this moment, the instantaneous friction coefficient fluctuates again, because of that the corresponding adhesion increases, while the van der Waals force decreases (Robert et al., 2002; Qing et al., 2006). Moreover, the friction coefficient of CF/PEEK is lower than that of PEEK with different humidity respectively.
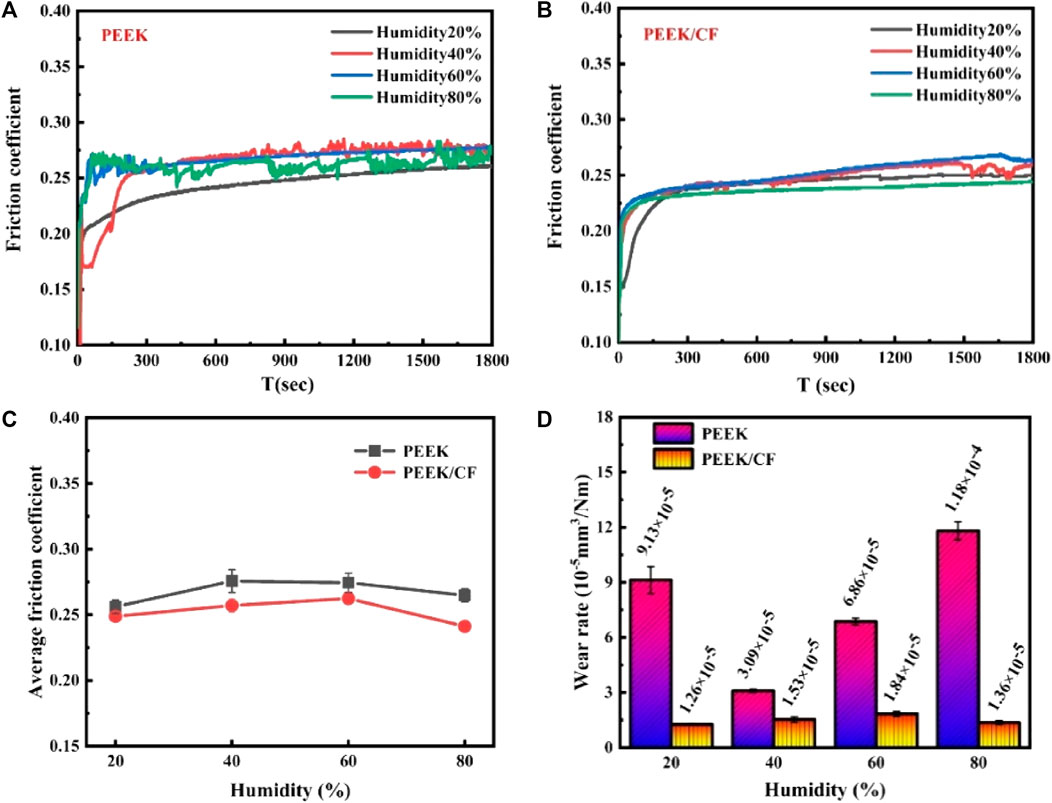
FIGURE 6. Instantaneous friction coefficient curves of PEEK (A) and CF/PEEK (B), comparison diagram of the average friction coefficient (C), and the wear rate of PEEK and CF/PEEK (D).
The wear rates of prepared materials with four humidity are shown in Figure 6D. It shows that with increase of humidity, the wear of pure PEEK first decreases, and then gradually increases, which reaches the lowest when the humidity is 40%. Due to the relatively low humidity, the surface of PEEK material is rough, where the shear force is large, and the corresponding wear rate is high. With increase of humidity, the van der Waals force between friction pairs decreases, but the adhesion force between water molecules increases. The wear rate is the lowest when the humidity increases up to 40%, because of that the van der Waals force and adhesion force are relatively small. When humidity up to 60% and 80%, the water is immersed into the material matrix through the surface, resulting in the intensification of adhesion and peeling. Compared to pure PEEK, humidity has slight effect on the wear rate of CF/PEEK composites. CF disperses in PEEK matrix, which disperses friction shear force with low humidity, while reduces the adhesion between friction pairs with high humidity. Therefore, humidity has slight effect on the wear rate of CF/PEEK composites.
Figure 7 shows the three-dimensional topography and cross-sectional profile curve of the worn surface of PEEK and CF/PEEK composites with different humidity. According to the three-dimensional topography of the worn surface a) and b), the worn surface of pure PEEK first becomes smooth and then becomes rougher with the increasing of humidity, which reaches the smoothest state with the humidity of 40%. However, the humidity has slight effect on the worn surface of CF/PEEK. When the humidity is 80%, there is almost no scratch on the worn surface of CF/PEEK. From the cross-sectional profile curves of pure PEEK and CF/PEEK composites, it can be seen that with the increase of humidity, the wear scar depth of pure PEEK first slightly shallows then sharply deepens, where the scratch width gradually widens. Compared to pure PEEK, the wear scar depth and width of CF/PEEK change slightly.
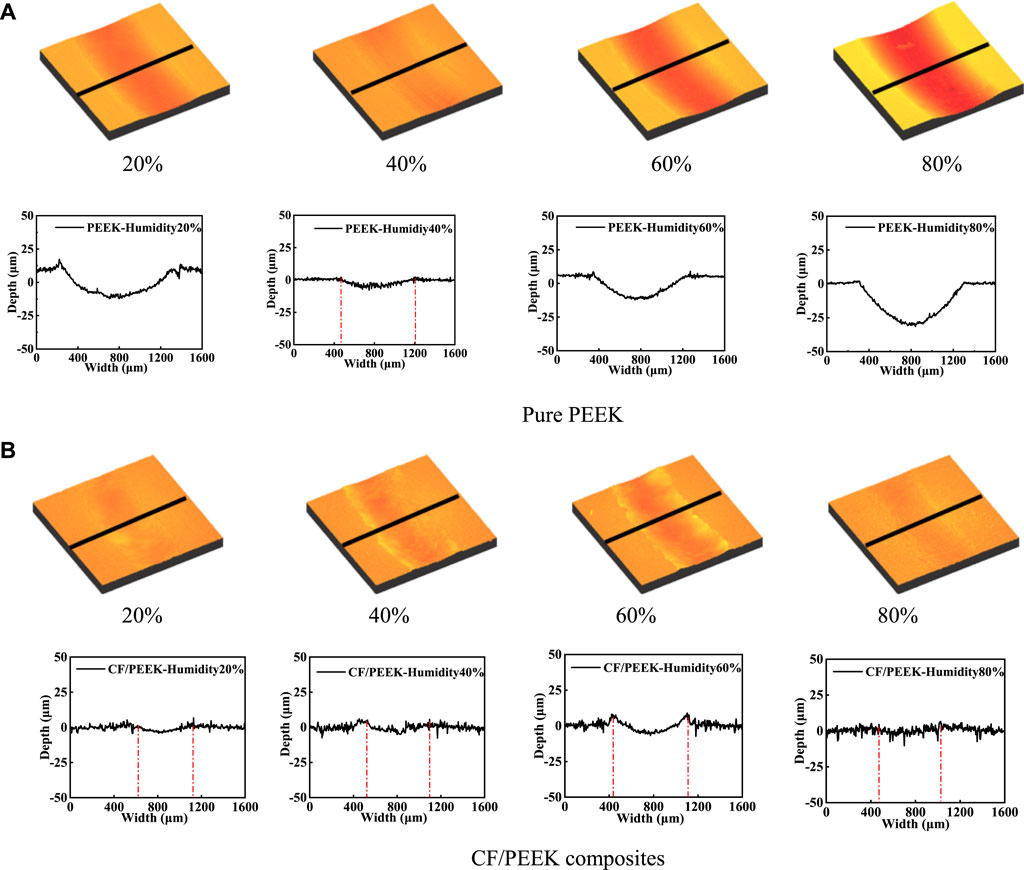
FIGURE 7. 3D morphologies and profile curves under different environmental humidity. (A) Pure PEEK. (B) CF/PEEK composites.
3.5 Evolution of wear mechanism with different humidity
Figures 8(A–D), (A1–D1) show the worn surface morphology of pure PEEK and CF/PEEK composites with four different humidity, respectively. Figures 8A–D show that fish scale lines and furrows appear on the surface of pure PEEK with low humidity. With the increase of humidity, water immerses into the PEEK matrix material along the surface, which increases the peeling pits on the surface of pure PEEK material and weakens the furrow phenomenon. Therefore, under the condition of low humidity, the wear mechanism of pure PEEK is mainly abrasive wear and adhesive wear, which evolves to adhesive wear as the humidity increasing to high humidity. It can be seen from Figures 8 A1–D1 that with four different humidity, the surface of CF/PEEK composite is flat, where are only slight fish scale lines and a few micro scratches. There is almost no wear on the surface of CF/PEEK composite. Therefore, the wear mechanism of CF/PEEK composite with four different humidity is slight abrasive wear and slight adhesive wear.
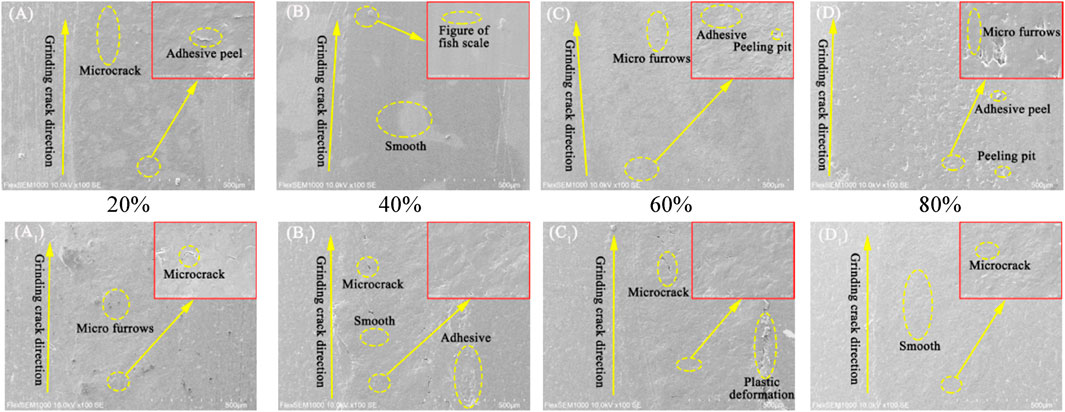
FIGURE 8. Wear surface topography of PEEK (A–D) and CF/PEEK (A1–D1) under different humidity. The Yellow single arrow in the figure is the direction of the scratch, and the red box in the upper right corner is an enlarged view of the local position of the wear scar.
3.6 Evolution of tribo-static electricity with different humidity
Figure 9 is the comparison diagram of friction electrostatic voltage between pure PEEK and CF/PEEK composites after friction with four ambient humidity. It shows that with the increase of humidity, the friction electrostatic voltage on the surface of pure PEEK and CF/PEEK composites shows a monotonic decreasing trend. When the humidity of CF/PEEK composites is 20%, a relatively high friction electrostatic voltage can be detected on the surface. When the environmental humidity increases to 60% and 80%, the electrostatic voltage can not be detected on the friction surface, and the voltage value is 0 V. There is no voltage dissipation medium on the surface and inside of pure PEEK material, thus the surface friction electrostatic voltage is relatively higher with four different humidity. With the increase of humidity, the friction electrostatic voltage value decrease, because of that water molecules act as a conductive medium on the friction surface. On the other hand, CF in CF/PEEK composites forms a continuous conductive network in PEEK matrix, which is a good conductive medium. However, the rate of surface charge accumulation is greater than that of dissipation with low humidity, where higher surface friction static electricity can be detected. As humidity increasing, water molecules act as conductive media on the surface and CF acts as conductive media inside the matrix. At this time, the rate of charge accumulation is less than the rate of dissipation, where the electrostatic voltage value of the friction surface is 0 V.
4 Conclusion
Pure PEEK was prepared by vacuum hot pressing sintering technology at different sintering temperatures. PEEK materials with a processing and molding temperature of 350°C have good tensile properties. The mechanical properties and microstructure characterization results show that the pure PEEK material prepared at 350°C showed excellent friction and wear properties.
With increase of ambient humidity, the friction coefficient of PEEK and CF/PEEK has slight change. The wear rate of PEEK decreases firstly and then increases, which reaches the lowest when the ambient humidity is 40%. Comparing to pure PEEK, the wear rate of CF/PEEK composites changes slightly, and the wear mechanism is mainly adhesive wear. The surface tribo-static electricity of PEEK and CF/PEEK composites decreases gradually with the increase of humidity.
Data availability statement
The original contributions presented in the study are included in the article/supplementary material, further inquiries can be directed to the corresponding author.
Author contributions
XP, SY, methodology, formal analysis, writing—original draft. CS, conceptualization, resources, writing—review and editing, supervision. SH and JX, visualization, writing—original draft. SW, YY, and DL, investigation. XP and CS, supervision, project administration. All authors listed have made a substantial, direct, and intellectual contribution to the work and approved it for publication. All authors contributed to the article and approved the submitted version.
Funding
This work was supported by the National Natural Science Foundation of China (92266205, 52105181), the Natural Science Foundation of Henan (222300420436), Key research development plan and “unveiling and commanding” of Ningbo City (2022Z050), the National Innovation and Entrepreneurship Training Program for College Students in Henan Province (202210464028).
Acknowledgments
This article also thanks the technical support from Provincial and Ministerial Co-construction of Collaborative Innovation Center of Non-ferrous Metal New Materials and Advanced Processing Technology.
Conflict of interest
The authors declare that the research was conducted in the absence of any commercial or financial relationships that could be construed as a potential conflict of interest.
Publisher’s note
All claims expressed in this article are solely those of the authors and do not necessarily represent those of their affiliated organizations, or those of the publisher, the editors and the reviewers. Any product that may be evaluated in this article, or claim that may be made by its manufacturer, is not guaranteed or endorsed by the publisher.
References
Abdul, S. M. (2021). Recent advances in UHMWPE/UHMWPE nanocomposite/UHMWPE hybrid nanocomposite polymer coatings for tribological applications: A comprehensive review. Polymers 13, 608. doi:10.3390/polym13040608
Bijwe, J., Sharma, S., Sharma, M., Parida, T., and Trivedi, P. (2013). Exploration of potential of solid lubricants and short fibers in Polyetherketone (PEK) composites. Wear 301, 810–819. doi:10.1016/j.wear.2013.01.059
Davim, J. P., and Cardoso, R. (2005). A note on the effect of temperature on the friction and wear behaviour of carbon-fibre-reinforced Polyetheretherketone (PEEK-CF30) at dry sliding. Microstruct. Mater. Prop. 1 (1), 3–10. doi:10.1504/ijmmp.2005.008128
Guan, Z., Wu, D., Cheng, Q., Wang, Z., Tang, M., and Liu, Y. (2020). Friction and Wear characteristics of CF/PEEK against 431 stainless steel under high hydrostatic pressure water lubrication. Mater. Des. 196, 109057. doi:10.1016/j.matdes.2020.109057
Guo, H., Huang, Y., Liu, L., and Shi, X. (2010). Effect of epoxy coatings on carbon fibers during manufacture of carbon fiber reinforced resin matrix composites. Mater. Des. 31 (3), 1186–1190. doi:10.1016/j.matdes.2009.09.034
Guo, L., Qi, H., Zhang, G., Wang, T., and Wang, Q. (2017). Distinct tribological mechanisms of various oxide nanoparticles added in PEEK composite reinforced with carbon fibers. Compos. Part A Appl. Sci. Manuf. 97, 19–30. doi:10.1016/j.compositesa.2017.03.003
He, G., Yuan, J., Li, Y., Wu, L., and Men, X. (2022). Preparation of MoS2/ZnS nano-powder and tribological behavior of MoS2/ZnS nano-powder reinforced polyimide composites[J]. Tribology 42 (2), 265–274. doi:10.16078/j.tribology.2021047
Hron, R., Kadlec, M., and Růžek, R. (2021). Effect of the test procedure and thermoplastic composite resin type on the curved beam strength. Mater. (Basel, Switz. 14, 352. doi:10.3390/ma14020352
Huang, S., Pang, X., and Yue, S. (2022). Effects of load on fretting wear behaviors of 304 stainless SteelsChinese full text. Tribology 5, 555–561. doi:10.16078/j.tribology.2022047
Jian, L., Ning, L., Yang, S., Wang, J., and Hua, M. (2009). Triboelectrification electrostatic potential of MC nylon 6 under point contact dry sliding. Tribol. Lett. 36, 199–208. doi:10.1007/s11249-009-9473-z
Lapčinskis, L., Linarts, A., Mālnieks, K., Kim, H., Rubenis, K., Pudzs, K., et al. (2021). Triboelectrification of nanocomposites using identical polymer matrixes with different concentrations of nanoparticle fillers. J. Mater. Chem. A 9 (2021), 8984–8990. doi:10.1039/d0ta12441a
Li, G., Ye, Y., Ma, Y., Feng, Q., Wilhelm, J., Wang, X., et al. (2021). Prolonged activation of innate immune pathways by a polyvalent STING agonist. Tribology 41, 455–466. doi:10.1038/s41551-020-00675-9
Liang, Y., Gao, D., and Zhao, J. (2020). Tribological properties of friction pair between 316L stainless steel and CF/PEEK with nonsmooth surface under seawater lubrication. Tribol. Trans. 63 (4), 658–671. doi:10.1080/10402004.2020.1734704
Qing, T., Shao, T., and Wen, S. (2006). Effects of relative humidity on surface adhesion[J]. Tribology 26 (4), 295–299. doi:10.3321/j.issn:1004-0595.2006.04.002
Qiu, C., Ma, X., Wang, Y., Guo, Z., and Wu, H. (2021). Research and application progresses of thin-ply carbon fiber reinforced polymer matrix composites[J]. Aeronautical Manufacturing Technology 64 (14), 22–31.
Robert, J., Hubert, M. P., Jamie, A. S., and Hodges, C. S. (2002). Adhesion forces between glass and silicon surfaces in air studied by AFM: effects of relative humidity, particle size, roughness, and surface treatment. Langmuir 18, 8045–8055. doi:10.1021/la0259196
Sha, J. J., Dai, J. X., Li, J., Wei, Z., Hausherr, J. M., and Krenkel, W. (2013). Measurement and analysis of fiber-matrix interface strength of carbon fiber-reinforced phenolic resin matrix composites. J. Compos. Mater. 48 (11), 1303–1311. doi:10.1177/0021998313485264
Wang, H., Feng, X., Shi, Y., and Lu, X. (2007). Effects of fibrous fillers on friction and wear properties of polytetrafluoroethylene composites under dry or wet conditions. China Particuology 5 (6), 414–419. doi:10.1016/j.cpart.2007.08.003
Xu, L., Zhao, J., and Lei, Y. G. “Wuhan,” in Proceedings of the 2006 Annual Meeting of Hubei Provincial Chemical and Chemical Society and Expert Forum on Circular Economy, 2006.
Yan, Y., Mao, Y., Li, B., and Zhou, P. (2020). Machinability of the thermoplastic polymers: PEEK, PI, and PMMA. Polymers 13, 69. doi:10.3390/polym13010069
Zhang, L., Lin, Z., Zhou, Q., and Liang, Y. (2020). PEEK modified PLA shape memory blends: Towards enhanced mechanical and deformation properties. Front. Mater. Sci. 14, 177–187. doi:10.1007/s11706-020-0502-z
Keywords: PEEK, CF/PEEK, tribological performances, ambient humidity, tribo-static electricity
Citation: Pang X, Yue S, Huang S, Xie J, Wang S, Yue Y, Song C and Li D (2023) Effects of ambient humidity and sintering temperature on the tribological and antistatic properties of PEEK and CF/PEEK. Front. Mater. 10:1197604. doi: 10.3389/fmats.2023.1197604
Received: 31 March 2023; Accepted: 02 May 2023;
Published: 15 May 2023.
Edited by:
Yongxin Wang, Chinese Academy of Sciences (CAS), ChinaCopyright © 2023 Pang, Yue, Huang, Xie, Wang, Yue, Song and Li. This is an open-access article distributed under the terms of the Creative Commons Attribution License (CC BY). The use, distribution or reproduction in other forums is permitted, provided the original author(s) and the copyright owner(s) are credited and that the original publication in this journal is cited, in accordance with accepted academic practice. No use, distribution or reproduction is permitted which does not comply with these terms.
*Correspondence: Chenfei Song, Y2Zzb25nQGhhdXN0LmVkdS5jbg==