- 1Shangdong Hi-Speed Group Innovation Research Institute, Jinan, China
- 2Shandong Transportation Institute, Jinan, China
- 3Shandong Engineering Laboratory of Bridge-Tunnel Performance Evaluation and Durability Promotion, Jinan, China
Aiming at the existing grouting material, there are a series of problems such as poor fluidity of the grouting, rapid loss of fluidity, non-compactness of the grouting after hardening, gaps or holes, and the like. In this paper, fly ash, limestone powder, and silica fume are used to replace cement, and the influence of mineral admixtures on the fluidity, rheological properties, and strength of the grouting material are systematically studied. The experiment found that: fly ash, limestone powder, and silica fume can all improve the fluidity of the grouting material, and the effect of fly ash is the best. Compared with pure cement grouting, the initial fluidity and 60 min fluidity of the grouting material mixed with 40 wt% fly ash were reduced by 35.5% and 53.8% respectively. Fly ash and limestone powder mixed into the grouting material will significantly improve the rheological properties, while silica fume will reduce the flow properties of the grouting. The addition of fly ash and limestone powder will reduce the mechanical properties of the grouting material, while silica fume can improve the mechanical properties of the grouting material. Compared with pure cement grouting, the 28 days compressive strength with 4 wt% limestone powder grouting material is reduced by 4.5%, and the flexural strength is reduced by 6%; the 28 days compressive strength with 4 wt% silica fume grouting material is increased by 6.5%, the flexural strength increased by 1%.
1 Introduction
In recent years, the construction of highway bridges in our country has developed rapidly. The design and construction of long-span prestressed concrete bridges have become a popular trend. Prestressed concrete technology has the advantages of using high strength materials, promoting the lightweight structure, with large span ability, and effectively avoid concrete cracking. However, all the advantages of the prestressed concrete bridge structure must be based on the integrity of the bond between the prestressed reinforcement and the structural concrete. According to the different characteristics of fabrication, design and construction, the prestressed concrete structure can be divided into pre-tensioning method and post-tensioning method. At present, the post-tensioning method has been widely used in the construction of highway bridges. The cantilever construction, site pouring and span construction mainly adopt the post-tensioning method. Duct grouting is an important part of post-tensioning prestressed structure construction. It plays an important role in protecting prestressed reinforcement from harmful ion erosion. Moreover, it directly affects the overall stiffness and strength of the prestressed concrete component, making the prestressed reinforcement and surrounding concrete joint as a whole. To improve and ensure the quality of prestressed duct grouting, the quality of grouting material is the premise. It is necessary to choose the raw materials and optimize the mix ratio design. The performance of the grouting material is directly related to the durability of the post-tensioning prestressed concrete structure (Feng and Wang, 2012; Song et al., 2014a; Ba, 2018; Zhang et al., 2020; Tan et al., 2022).
Prestressed duct grouting material as an important construction material for prestressed structures, scholars have done a lot of research on it. Li (2011) prepared a new grouting material made of ordinary Portland cement and rapid hardened sulphoaluminate cement as the compound system, adding retarder (tartaric acid and boric acid) and early strength admixture (lithium carbonate). Due to the characteristics of high early strength and rapid hardening. Compared with the conventional grouting material, the prepared grouting material has higher early strength and better working performance. However, it is difficult to control the setting time, so it is proposed that the cementing material of prestressed grouting should not choose thioaluminate cement, but mainly ordinary silicic acid cement. Song et al. (2014b) improved the physical properties of grouting material by changing mixing parameters and replacing cement varieties. Cheng et al. (2014) explored the influence of volume deformation and submicrostructure of prestressed pore by adding plastic expansion agent. Li (Li et al., 2018) studied the influence of ultrafine calumonite on the performance of the grouting material. The study shows that the increase of the calcium increases the strength and setting time of the grouting material.
Xiang et al. (2018) studied the influence of limestone powder on the performance of the grouting material. The results show that in a certain range, the fluidity of the grouting material is gradually increased with the increase of limestone powder. Moreover, it has a positive effect on improving the strength of the grouting material and can inhibit the contraction of the grouting material in the later stage. Through microscopic testing and characterization, it is known that the strength increase is mainly due to the physical filling effect of limestone powder, which makes the interior more dense. The pozzolanic activity of limestone powder and other mineral admixture will also lead to the increase of the grouting material strength. Ma et al. (2021) studied the influence of gypsum on the fluidity, mechanical properties and shrinkage rate of the grouting material. The results show that when the gypsum (CaSO4) exists simultaneously with the water-reducing agent, the adsorption and steric hindrance will improve the initial fluidity of the grouting material. At the same time, CaSO4 can promote the generation of calcium sulfoaluminate in the hydration products, which improve the strength of the grouting material. In addition, the increase in the amount of calcium can fill the gap between hydration products, making the grouting material more dense and improve the stability of the grouting material. Masbin et al. formulated a prestressed grouting agent from fly ash, silicon ash, water-reducing agent, expansion agent, cellulose and defoaming agent (Shu et al., 2021a). The effects of various raw materials on the variability of compressive strength were studied through the test system. And the mix ratio was optimized by applying the Logit model. The test results show that the dosage of water-reducing agent and defoaming agent will increase the variability of the compressive strength of the grouting material. While silica fume, expansion agent and cellulose will inhibit the variability of the compressive strength to some extent. The compressive strength of the optimized grouting material can reach more than 60 MPa in 7 days and 74 MPa in 28 days. Moreover, the data error of the same group is within 10%, and the variability is significantly reduced. Shu et al. (2021b) used fly ash (FA) or steel slag powder (SS) as raw material, and studied the influence of FA and SS on the fluidity and mechanical properties of grouting material. The results show that the optimal amounts of FA and SS were 40% and 20%. The grouting material containing 40% FA or 20% SS have good mobility and mechanical properties. Guan and Zhong (2013) deeply studied the physical and mechanical properties, rheological properties and microstructural changes of ultrafine high-performance grouting cement. The study shows that when the fly ash is mixed into the ultrafine cement, the fluidity of the grouting material can be greatly improved. Because the pozzolanic activity of the fly ash, it can improve the hardening strength of the late grouting material stage. The interior can be more dense, and the impermeability of the slurry can be enhanced.
Liu et al. (2023) prepared nano-silica (NS) -modified aqueous epoxy resin (WEP) by in situ polymerization and mixed it into the grouting material. The characteristics and microstructure of composite grouting material and the microscopic coordination mechanism of each slurry composition is analyzed. The results show that increasing the NS concentration in WEP can shorten the setting time and improve the stability of the composite grouting material. When the NS content in WEP was 4%, the compressive strength of the specimens increased by 33.71% at 3 days and 39.03% at 28 days. The composite material of NS and WEP can promote the production of the hydration products C-S-H and C-A-S-H, and promote the fine crystallization of the hydration products. Hydrated crystals were grown on NS of the WEP surface, thereby bridging the resin film and cement particles. Zhang et al. (2021) used polypropylene fiber (PP), polyvinyl fiber (PVA) and basalt fiber (BF) as a mixture of the grouting material, studied the fiber on the basic mechanical properties, toughness and the best content and length of each fiber. The results show that fiber is the ideal material to improve the toughness of the grouting material. The best content of each fiber in the grouting material is 0.5% (PP), 0.3% (BF) and 0.1% (PVA), and the best length is 9 mm (PP), 3 mm (BF) and 3 mm (PVA). The best content of each fiber in grouting material is 0.5% (PP), 0.3% (BF) and 0.1% (PVA), and the best length is 9 mm (PP), 3 mm (BF) and 3 mm (PVA).
Sun et al. (2020) introduced thioaluminate cement, hydroxypropyl methyl cellulose, lithium carbonate and calcium formate in the cementing system, and prepared the prestressed duct grouting material for railway that meets the requirements of JTG/TF 50-2011 “Technical Specification for Construction of Highway Bridge and Culverts” under the condition of −5°C. Yang et al. (2019) studied the effect of expansion agent on the limiting expansion rate of grouting material. The result shows that the rate of limiting expansion increased with the increase of expansion agent. In a certain dosage range, the expansion agent has an obvious effect on increasing the early limiting expansion rate of grouting material. Wang and Zhang (2017) developed a duct grouting material, which has high fluidity, small flow loss, micro expansion and no bleeding occur. They selected polycarboxylicacid water reducer, plastic expansion agent, defoaming agent as chemical admixture. By performing orthogonal test to optimize the raw materials and the mix ratio. The prepared duct grouting material meets the requirements of JTG/TF 50-2011 “Technical Specification for Construction of Highway Bridge and Culverts.” He et al. (2023) proposed that the combination of superabsorbent polymer (SAP) and the expansion agent can effectively reduce the shrinkage deformation of ultra-high strength cement-based grouting materials (UHS-CGM) in dry environment. Moreover, the effects of different SAP sizes and dosage on the compressive strength, inhibitory expansion rate, internal relative humidity (IRH) and hydration characteristics of UHS-CGM containing MgO expansion agent (MEA) were studied. And the composition and content of hydration products are analyzed by TG and XRD by SEM. The results show that SAP improved the hydration degree of UHS-CGM and the expansion efficiency of MEA, significantly improved the inhibitory expansion rate of UHS-CGM under standard curing and sealed curing. While reduced the compressive strength of UHS-CGM, which increased with the increasing size and dose of SAP.
At present, there is a comprehensive study on the addition of adding appropriate admixture to the grouting material and the optimization of the mix ratio of raw materials. But the existing research on the rheology or working performance of the grouting is less. Studying the rheological characteristics of grouting can provide a basis for adjusting the ratio of the grouting and controlling the preparation process of materials. Thus, improving the construction performance of the material and its physical and chemical properties as well as application effect. This paper combined with the test system of fly ash, limestone powder, silicon ash mineral admixture on the grouting material flowability, rheology, mechanical properties of the law, in order to improve the working performance and mechanical properties of the grouting material.
2 Experiment
2.1 Raw materials
The cement is P·O 42.5 cement from Shanshui Dongyue with a density of 3.10 g/cm3 and a specific surface area of 380 m2/kg. The fly ash is Beijing-taipei Grade I fly ash with a density of 2.2 g/cm3, a fineness of 5.9% and a loss on ignition of 2.1%, water requirement ratio 95%; Limestone powder; Sika water reducing agent, white powder, water reducing rate 27%, air content 2.4% (water reducing rate and air content 1%), expansion agent. The 3 and 28 days compressive strength (CS) and flexural strength (FS) of the main cement materials used in this experiment are shown in Figure 1.
2.2 Specimen preparation
In the traditional sense, the vast majority of prestressed duct grouting materials is pure cement slurry. Only a certain amount of water reducing agent, expansion agent and thickening agent are added to prepare the duct grouting materials on site. The mixing is not sufficient and the influence of various factors makes the quality of the duct grouting materials can not be guaranteed. Thus, there are a series of problems such as poor fluidity, fast flow loss, large drainage rate of serous slurry, stratified segregation, uncompaction after slurry hardening, void or holes (Zhang et al., 2019; Chen et al., 2020; Ma et al., 2022; Mou et al., 2022; Wang et al., 2022). Therefore, this study is based on the literature review and previous experiments (Xie et al., 2020; Khan et al., 2021; Khan et al., 2022a; Khan et al., 2022b; Sha et al., 2023). The key parameters of water-binder ratio, water-reducing agent and expansion agent are determined in Table 1. On the basis of these parameters, the working state of the grouting material can be adjusted by adjusting the composition of the cementitious material and adding admixtures until the grouting material with excellent performance can be prepared. First, the test raw materials will be proportionally prepared dry mixture, and pre-mixing. Then first add water to the mixing pot, then add the dry mixture, then start the mixing device, from low-speed mixing (500 r/min, stirring 1 min) to high-speed full mixing (2,000 r/min, stirring 9 min, blade linear speed of 15 m/s).
The working performance (fluidity) of the mixed grouting was tested first, and then the grouting was poured into a 40 mm × 40 mm × 160 mm cement mortar triple die for molding. The grouting level was slightly higher than the test model height for the first time, to be the surface of the “Plastic” state after the collection. After the specimens for mechanical properties testing were finished, polyethylene film was applied to the surface of the specimens (as shown in Figure 2) and the molds were removed after indoor curing at a temperature of 20°C ± 2°C or 1 day, remove the mold and move to the concrete standard curing room for standard curing, until the specified age to take out the mechanical properties of the test.
2.3 Testing methods
2.3.1 Working performance
2.3.1.1 Liquidity
The working performance (fluidity) of the grouting material was tested in accordance with the “Test code for cement and cement concrete for highway engineering” (JTG E 30) (JTGE30-2005.2005-03-03, 2005) (as shown in Figure 2).
2.3.1.2 Rheological properties
The rheological properties of mortar were tested by BML rheometer.
2.3.2 Mechanical properties
The compressive strength and flexural strength of the grouting material at 3, 7, and 28 days were measured by automatic pressure testing machine for cement mortar strength. The test method was carried out according to “Testing method for strength of cement mortar (ISO method)” (GB/T 17671) (Standardization Administration of China, 2009).
3 Results and discussions
3.1 The influence of mineral admixture on the working performance of the grouting material
3.1.1 Effect of fly ash on the fluidity of the grouting material
In order to study the effect of the content of fly ash on the working performance of the grouting, the same content of fly ash was used to replace 10 wt%, 20 wt%, 30 wt%, 40 wt%, 50 wt% of the cement. The test mix ratio and fluidity test results are shown in Table 2 and Figure 3.
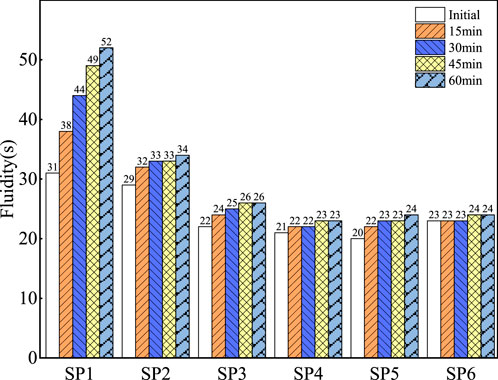
FIGURE 3. Test results of the effect of fly ash on the working performance of the grouting material.
Figure 3 reflects the effect of the amount of fly ash on the performance of the grouting material. It can be seen from Figure 3 that the fluidity of the grouting decreases with time. As the time increased from 0 to 60 mins, the fluidity of pure cement grouting increased from 31 to 52 s, and the fluidity increased by 67.7%. The fluidity of the grouting material mixed with 50 wt% fly ash increased from 23 to 24 s, and the fluidity increased by 4.35%. It can be seen that the addition of fly ash can significantly reduce the time loss of the grouting material. When the content of fly ash in the grouting material increases from 0 wt% to 40 wt%, the initial fluidity of the grouting material tends to decrease. However, when the content of fly ash is 50 wt%, the initial fluidity of the grouting material increases. When the content of fly ash in the grouting material increases from 0 wt% to 50 wt%, the initial fluidity of the grouting material decreases from 31 to 23 s, a decrease of 25.8%, and the 60 min fluidity of the grouting material decreases from 52 to 24 s, a decrease of 53.8%. In summary, the addition of fly ash can effectively improve the working performance of the grouting material and reduce the loss of fluidity over time, but the dosage should not be too high.
3.1.2 Effect of limestone powder on the fluidity of the grouting material
In order to study the effect of limestone powder on the working performance of the grouting material, an equal content of limestone was used to replace 5 wt% 10 wt%, and 20 wt% cement. The test mix ratio and fluidity test results are shown in Table 3 and Figure 4.
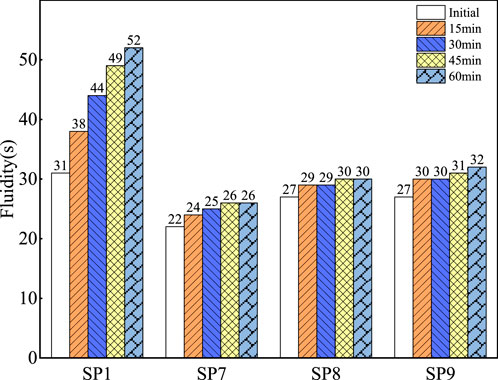
FIGURE 4. Test results of the effect of limestone powder on the working performance of the grouting material.
Figure 4 reflects the effect of adding limestone powder on the working performance of the grouting material. It can be seen from Figure 4 that the fluidity of the grouting decreases with time. The content of limestone powder increased from 0 wt% to 5 wt%, and the initial fluidity of the grouting material decreased from 31 to 22 s, a decrease of 29%. As the time increased from 0 to 60 mins, the fluidity of the grouting material decreased from 52 to 26 s, a decrease of 50%. It can be seen that the incorporation of limestone powder can effectively improve the working performance of the grouting material and greatly reduce the loss of the fluidity of the grouting material over time. However, when the limestone powder content increased from 5 wt% to 20 wt%, the initial fluidity of the grouting material increased from 22 to 27 s, an increase of 23%. The fluidity of the grouting increased from 26 to 32 s at 60 min, an increase of 23%. In summary, limestone powder can significantly improve the fluidity of the grouting material and reduce the loss of fluidity of the grouting material over time. However, excessive limestone powder will inhibit the working performance of the grouting material, resulting in a decrease in the fluidity of the grouting material.
3.1.3 Effect of silica fume on the grouting material fluidity
In order to study the influence of silica fume on the performance of grouting material, an equal content of silica fume was used to replace 4 wt%, 5 wt%, and 6 wt% cement. The test mix ratio and fluidity test results are shown in Table 4 and Figure 5.
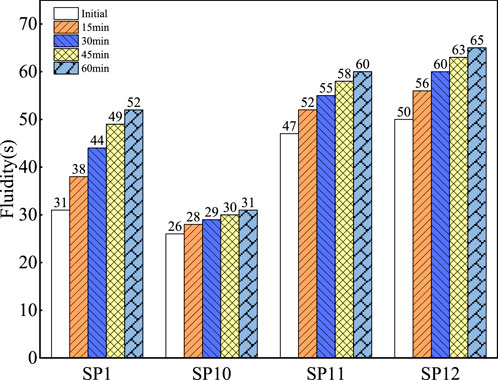
FIGURE 5. Test results of the effect of silica fume on the working performance of the grouting material.
Figure 5 reflects the effect of silica fume on the performance of the grouting material. It can be seen from Figure 5 that with 4 wt% silica fume, the initial fluidity of the grouting decreased from 31 to 26 s, a decrease of 16%. And the 60 min fluidity decreased from 52 to 31 s, a decrease of 41%. Silica fume can improve the working performance of the grouting, and can significantly reduce the loss of the fluidity of the grouting material over time. When the content of silica fume increased from 4 wt% to 6 wt%, the initial fluidity of the grouting material increased from 26 to 50 s, an increase of 92%. The fluidity of the grouting material increased from 31 to 65 s at 60 min, an increase of 109%. The working performance of the grouting material is very sensitive to the change of the silica fume content, and excessive silica fume will seriously inhibit the working performance of the grouting material. Therefore, the content of silica fume in the grouting material needs to be strictly controlled, otherwise the working performance of the grouting material will be severely inhibited.
3.1.4 Effect of fly ash, limestone powder and silica fume on rheological properties of the grouting material
Figure 6 is the relationship curve between shear stress and shear rate of pure cement grouting and mixed with different amounts of fly ash, silica fume and limestone powder grouting material drawn using the data measured by the rheometer. It can be seen from Figure 6 that there is an obvious positive correlation between the shear stress and the shear rate of the grouting material. From the curve of shear stress and shear rate of cement paste, it can be seen that when the shear rate is low, the shear stress increases rapidly. But with the further increase of the shear rate, the growth rate of the shear stress gradually slows down. The rheological curve of pure cement grouting material can fit well with the modified Binghan model, where R2 can reach 0.97. The relationship between shear stress and shear rate can be described by fitting Eq. 1.
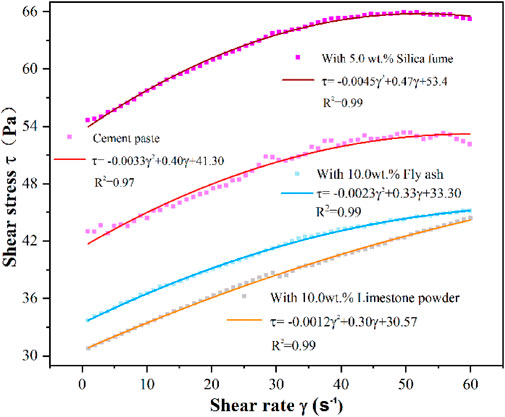
FIGURE 6. Effect of fly ash, silica fume and limestone powder on rheological properties of the grouting material.
When 10 wt% fly ash was added to the grouting material, the rheological properties of the grouting material changed significantly. When the shear rate is constant, the shear stress of the grouting mixed with 10 wt% fly ash is significantly smaller than that of the pure cement grouting. There is also an obvious positive correlation between the shear stress and the shear rate of the grouting material mixed with 10 wt% fly ash. Similar to the pure cement grouting material, the rheological curve of the grouting material mixed with 10 wt% fly ash can also fit the modified Binghan model very well, in which R2 can reach 0.99. Therefore, the relationship between the shear stress and the shear rate of the grouting material mixed with 10 wt% fly ash can be described by the fitting Eq. 2.
When adding 10 wt% limestone powder to the grouting material, the rheological properties of the grouting material also changed significantly. When the shear rate is constant, the shear stress of the grouting material mixed with 10 wt% limestone powder is smaller than the shear stress of the pure cement grouting material and the grouting material mixed with 10 wt% fly ash. The shear stress and shear rate of the same grouting material mixed with 10.0 wt% limestone powder also have a significant positive correlation. The rheological curve of the grouting material can also fit well with the modified Binghan model, where R2 can reach 0.99. Therefore, the relationship between the shear stress and the shear rate of the grouting material mixed with 10 wt% fly ash can be described by the fitting Eq. 3.
When adding 5 wt% silica fume to the grouting material, the rheological properties of the paste changed significantly. When the shear rate is constant, the shear stress of the grouting material mixed with 5 wt% silica fume is significantly greater than that of the pure grouting material, grouting material mixed with 10 wt% fly ash and grouting material mixed with 10 wt% limestone powder. The rheological curve of the grouting material can also fit well with the modified Binghan model, where R2 can reach 0.99. Therefore, the relationship between the shear stress and the shear rate of the grouting material mixed with 10 wt% fly ash can be described by the fitting Eq. 4.
Combining the above four fitting equations, it can be known that mixing fly ash and limestone powder into grouting material will significantly improve the rheological properties of grouting material. When 10 wt% fly ash is added to the grouting material, the apparent viscosity and yield stress of the grouting material are reduced from 0.40 Pa∙s and 41.3 Pa to 0.33 Pa∙s and 33.3 Pa, reduced by 17.5% and 19.4%. This may be due to the fact that the spherical structure of fly ash reduces the friction between grouting material. Compared with the pure cement grouting the apparent viscosity and yield stress are reduced by 25% and 26% when 10 wt% of limestone powder is added to the grouting material. However, when adding 5 wt% silica fume, the apparent viscosity and yield stress of the grouting increased significantly. Compared with the pure cement grouting, the apparent viscosity and yield stress of the grouting increased from 0.40 Pa∙s and 41.3 Pa to 0.47 Pa∙s and 53.4 Pa, which increased by 17.5% and 30%. Therefore, the incorporation of fly ash and limestone powder can improve the working performance of the grouting material, while silica fume can reduce the rheological properties of the grouting material.
3.2 Effect of mineral admixture on mechanical properties of the grouting material
3.2.1 Effect of fly ash on mechanical properties of the grouting material
Figure 7A reflects the 3, 7, and 28 days flexural strength of pure cement grouting material and grouting material mixed with different proportions of fly ash. It can be seen from Figure 7A that the 3, 7, and 28 days flexural strength of pure cement grouting material (SP1) is higher than that grouting material with fly ash. Compared with pure cement grouting material, when the fly ash content is 10 wt%, 20 wt%, 30 wt%, 40 wt% and 50 wt%. The 3 days flexural strength of the grouting material is reduced by 13.33%, 28.33%, 38.33%, 48.33% and 55%, respectively; The 7 days flexural strength of the grouting material is reduced by 12.79%, 23.26%, 32.56%, 40.70% and 47.67%, respectively; The 28 days flexural strength of the grouting material is reduced by 11.65%, 23.30%, 32.04%, 39.81% and 48.54%, respectively; It can be seen that with the increase of the amount of fly ash, the flexural strength of the grouting material gradually decreases, and the influence of the addition of fly ash on the early strength of the grouting material is more significant.
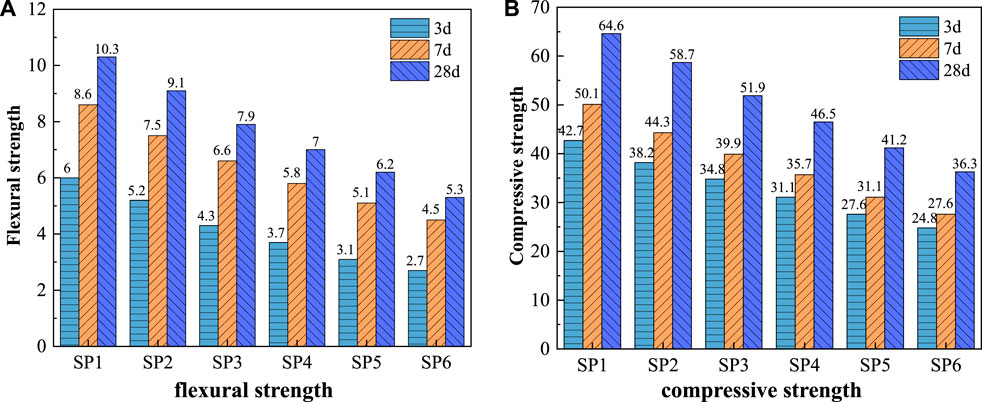
FIGURE 7. Mechanical properties of the grouting material mixed with fly ash. (A) flexural strength; (B) compressive strength.
Figure 7B reflects the 3, 7, and 28 days compressive strength of pure cement grouting material and grouting material mixed with different proportions of fly ash. It can be seen from Figure 7B that the 3, 7, and 28 days compressive strength of pure cement grouting material (SP1) is higher than that grouting material with fly ash. Compared with pure cement grouting material, when the fly ash content is 10 wt%, 20 wt%, 30 wt%, 40 wt% and 50 wt%. The 3 days compressive strength of the grouting material is reduced by 10.54%, 18.50%, 27.17%, 35.36% and 41.90%, respectively; The 7 days compressive strength of the grouting material is reduced by 11.58%, 20.36%, 28.74%, 37.92% and 44.91%, respectively; The 28 days compressive strength of the grouting material is reduced by 9.13%, 19.66%, 28.02%, 36.22% and 43.81%, respectively; It can be seen that with the increase of the content of fly ash, the compressive strength of the grouting material gradually decreases.
In summary, the addition of fly ash will reduce the mechanical properties of the grouting material, but when the content is small (less than 10%), it has little effect on the mechanical properties. And the mechanical properties of the grouting material increase significantly with age.
3.2.2 Effect of limestone powder on mechanical properties of the grouting material
Figure 8A reflects the 3, 7 and 28 days flexural strength of pure cement grouting material and grouting material mixed with different proportions of limestone powder. It can be seen from Figure 8A that the 3 days, 7, and 28 days flexural strength of pure cement grouting material (SP1) is higher than that grouting material with limestone powder. Compared with pure cement grouting material, when the limestone powder content is 5 wt%, 10 wt%, and 20 wt%. The 3 days flexural strength of the grouting is reduced by 5.00%, 20.00% and 31.67%, respectively; The 7 days flexural strength of the grouting is reduced by 3.59%, 10.38% and 24.75%, respectively; The 28 days flexural strength of the grouting is reduced by 5.82%, 15.53% and 29.13%, respectively; It can be seen that with the increase of the amount of limestone powder, the flexural strength of the grouting material gradually decreases. However, when the amount of limestone powder is less (5 wt%), the flexural strength of the grouting material is only reduced by about 5%.
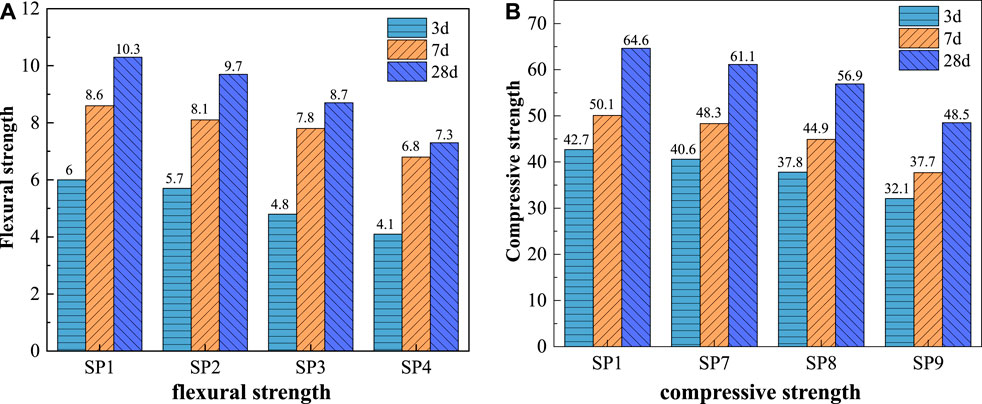
FIGURE 8. Mechanical properties of the grouting material mixed with limestone powder. (A) flexural strength; (B) compressive strength.
Figure 8B reflects the 3, 7, and 28 days compressive strength of pure cement grouting material and grouting material mixed with different proportions of limestone powder. It can be seen from Figure 8B that the 3, 7, and 28 days compressive strength of pure cement grouting material (SP1) is higher than that grouting material with limestone powder. Compared with pure cement grouting material, when the limestone powder content is 5 wt%, 10 wt%, and 20 wt%. The 3 days compressive strength of the grouting is reduced by 4.92%, 11.48% and 24.82%, respectively; The 7 days compressive strength of the grouting is reduced by 3.59%, 9.30% and 24.75%, respectively; The 28 days compressive strength of the grouting is reduced by 5.42%, 11.92% and 24.92%, respectively; It can be seen that with the increase of the content of limestone powder, the compressive strength of the grouting material gradually decreases.
In summary, the addition of limestone powder will reduce the mechanical properties of the grouting material, but when the content is small (5%), it has little effect on the mechanical properties of the grouting material. The mechanical properties of the grouting material will increase significantly with age.
3.2.3 Effect of silica fume on mechanical properties of the grouting material
Figure 9A reflects the 3, 7, and 28 days flexural strength of pure cement grouting material and grouting material mixed with different proportions of silica fume. It can be seen from Figure 9A that the 3, 7, and 28 days flexural strength of pure cement grouting material (SP1) is lower than that grouting material with silica fume. Compared with pure cement grouting material, when the silica fume content is 4 wt%, 5 wt%, and 6 wt%. The 3 days flexural strength of the grouting material is increased by 8.33%, 8.33% and 10.00%, respectively; The 7 days flexural strength of the grouting is increased by 2.33%, 2.33% and 3.49%, respectively; The 28 days flexural strength of the grouting is increased by 0.97%, 1.94% and 1.94%, respectively; It can be seen that the increase of silica fume content can promote the development of the early flexural strength of the grouting material, but has little effect on the later strength of the grouting material.
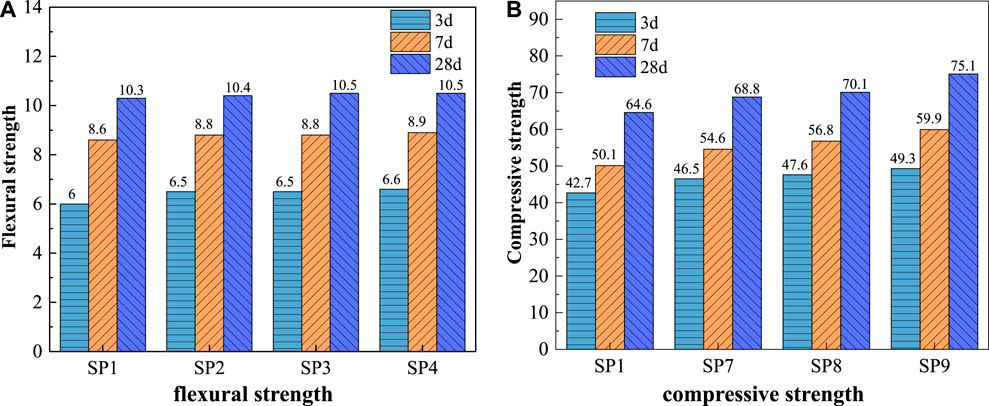
FIGURE 9. Mechanical properties of the grouting material mixed with silica fume. (A) flexural strength; (B) compressive strength.
Figure 9B reflects the 3, 7, and 28 days compressive strength of pure cement grouting material and grouting material mixed with different proportions of silica fume. It can be seen from Figure 9B that the 3, 7, and 28 days compressive strength of pure cement grouting material (SP1) is lower than that grouting material with silica fume. Compared with pure cement grouting material, when the silica fume content is 4 wt%, 5 wt%, and 6 wt%. The 3 days compressive strength of the grouting material is increased by 8.90%, 11.48% and 15.46%, respectively; The 7 days compressive strength of the grouting material is increased by 8.98%, 13.37% and 16.36%, respectively; The 28 days compressive strength of the grouting material is increased by 6.50%, 8.51% and 16.25%, respectively; It can be seen that as the content of silica fume increases, the compressive strength of the grouting material increases gradually.
In summary, silica fume can improve the mechanical properties of grouting material, and with the increase of silica fume content, the effect of improving the compressive strength of grouting material is more significant.
4 Discussion
At the present stage, the adjustment of the water binder ratio of the grouting material is limited between 0.26 and 0.28. Which can effectively avoid the bleeding phenomenon of the grouting material and improves the early strength of the grouting material (Song et al., 2014b; Gao et al., 2022). With the decrease of the water binder ratio of the grouting material. The requirements of all kinds of new grouting material are getting higher and higher, which promotes the grouting matierial construction technology constantly updated and improved (Shi, 2020). Grouting materials mixed with appropriate amount of admixtures, such as fly ash, silica fume, limestone powder, etc., can fully meet the needs of mechanical properties and working properties in the current construction. Therefore, the demand for the admixture of the grouting matierial is getting lower and lower. In some special cases that must be mixed with admixture. It should be considered to use good compatibility with the grouting or cement, low chloride, nitrite content, can ensure good grouting mobility, no bleeding and can meet the requirements of mechanical strength specification and construction (Cheng et al., 2014; Yang, 2020). Mineral admixture should be grade I fly ash, slag or silica fume, and the quality should meet the standard requirements. Mineral admixture should be selected according to the engineering needs, and the materials conducive to improve the fluidity and stability of the grouting material should be selected (Xiang et al., 2018). The mixing water shall not contain substances harmful to prestressed tendons or cement. Test and construction of the water source must be tested in the water source and can be used only after meeting the requirements.
5 Conclusion
This paper systematically studies the influence of different contents of fly ash, limestone powder and silica fume on the working performance and mechanical properties of the grouting material, and the main conclusions are as follows:
(1) Fly ash and limestone powder can effectively improve the working performance of the grouting and reduce the loss of fluidity of the grouting material over time, and the effect of fly ash is the most significant. Compared with the pure cement grouting material, the initial fluidity and 60 mins fluidity of the grouting material mixed with 40 wt% fly ash are reduced by 35.5% and 53.8%. The initial fluidity and 60 mins fluidity of the grouting material mixed with 5 wt% limestone powder decrease by 30% and 41%. But when the fly ash content is 50 wt% and the limestone powder content is 10 wt%, the working performance of the grouting material begins to decrease.
(2) Adding 4 wt% silica fume can improve the working performance of the grouting material, and the initial fluidity and 60 min fluidity of the grouting are reduced by 16% and 41%. However, as the content of silica fume increases, the working performance of the grouting will be significantly reduced, and the fluidity of the grouting will be increased over time.
(3) Fly ash and limestone powder mixed into grouting will significantly improve the rheological properties of the grouting material, but silica fume will reduce the rheological properties of grouting material. Compared with the pure cement grouting material, the apparent viscosity and yield stress of the grouting material mixed with 10 wt% fly ash decreased by 17.5% and 19.4%, respectively; The apparent viscosity and yield stress of the grouting mixed with 10 wt% limestone powder decreased by 25% and 26%, respectively. But mixed with 5 wt% silica fume, the apparent viscosity and yield stress of the grouting increase significantly. Compared with the pure cement grouting material, the apparent viscosity and yield stress of the grouting material mixed with 5 wt% silica fume increase by 17.5% and 30%, respectively.
(4) The addition of fly ash and limestone powder will reduce the mechanical properties of the grouting material. Compared with the pure cement grouting material, the 28 days compressive strength of the grouting material with 10 wt% fly ash is reduced by 9% and the flexural strength is reduced by 12%; The 28 days compressive strength of the grouting material with 4 wt% limestone powder is reduced by 4.5% and the flexural strength is reduced by 6%. With the increase of the content of fly ash and limestone powder, the mechanical properties of the grouting material tended to decrease gradually.
(5) The addition of silica fume can improve the mechanical properties of the grouting material. Compared with pure cement grouting, the 28 days compressive strength of 4 wt% silica fume grouting material is increased by 6.5%, and the 28 days flexural strength is increased by 1%. With the increase of silica fume content, the mechanical properties of the grouting material tend to increase gradually, especially the increase of compressive strength is the most obvious.
Data availability statement
The original contributions presented in the study are included in the article/Supplementary Material, further inquiries can be directed to the corresponding author.
Author contributions
All authors listed have made a substantial, direct, and intellectual contribution to the work and approved it for publication.
Conflict of interest
The authors declare that the research was conducted in the absence of any commercial or financial relationships that could be construed as a potential conflict of interest.
Publisher’s note
All claims expressed in this article are solely those of the authors and do not necessarily represent those of their affiliated organizations, or those of the publisher, the editors and the reviewers. Any product that may be evaluated in this article, or claim that may be made by its manufacturer, is not guaranteed or endorsed by the publisher.
References
Ba, W. (2018). Research on formulation and performance of high-performance pore grouting agent. Highw. Traffic Technol. Appl. Technol. Ed. 14 (04), 132–135.
Chen, J., Liu, F., Bai, X., Wang, D., and Wang, J. (2020). Effect of aerogels on properties of sleeve grouting materials. Tianjin Constr. Sci. Technol. 30 (6), 49–50.
Cheng, P., Song, X., Li, B., and Hu, S. (2014). Effect of plastic expansion agent on the volume deformation and submicroscopic structure of pre-stressed duct grouting materials. Bull. Chin. Ceram. Soc. 33 (6), 1329–1335.
Feng, X., and Wang, W. (2012). Influence of rotational speed on slurry properties of prestressed channels. J. China & Foreign Highw. 32 (05), 173–176.
Gao, Y., Ma, P., Kang, S., Cheng, B., Yang, W., Gu, X., et al. (2022). Dynamic evolution of the plastome in the Elm family (Ulmaceae). Metal. Mine 51 (1), 14–20. doi:10.1007/s00425-022-04045-4
Guan, X., and Zhong, Q. (2013). Research on the performance of micro-fine cement-based grouting material and its engineering application. Saf. Coal Mines 44 (6), 142–145.
He, X., Yang, J., Niu, M., Zhang, G., and Li, G. (2023). Study on expansion effect and hydration characteristics of ultra-high strength cement-based grouting materials based on humidity compensation. Case Stud. Constr. Mater. 18, e01941. doi:10.1016/j.cscm.2023.e01941
Jtge30-2005.2005-03-03, (2005). Test code for cement and cement concrete for highway engineering. British Columbia, Canada: Abe books.
Khan, M., Cao, M., Ai, H., and Hussain, A. (2022). Basalt fibers in modified whisker reinforced cementitious composites. Period. Polytech. Civ. Eng. 66 (2), 344–354. doi:10.3311/ppci.18965
Khan, M., Cao, M., Ai, H., and Hussain, A. (2022). Basalt fibers in modified whisker reinforced cementitious composites. Period. Polytech. Civ. Eng. 66 (2), 344–354. doi:10.3311/ppci.18965
Khan, M., Cao, M., Xie, C., and Ali, M. (2021). Efficiency of basalt fiber length and content on mechanical and microstructural properties of hybrid fiber concrete. Fatigue & Fract. Eng. Mater. Struct. 44 (8), 2135–2152. doi:10.1111/ffe.13483
Li, H., Guan, X., Zhang, X., Ge, P., Hu, X., and Zou, D. (2018). Influence of superfine ettringiteon the properties of sulphoaluminate cement-based grouting mate-rials. Constr. Build. Mater. 166 (166), 723–731. doi:10.1016/j.conbuildmat.2018.02.013
Li, Q. (2011). Research on the properties of super early-strength cement-based grouting. Harbin, China: Harbin Institute of Technology.
Liu, W., Sun, Y., Meng, X., and Qin, Y. (2023). Experimental analysis of Nano-SiO2 modified waterborne epoxy resin on the properties and microstructure of cement-based grouting materials. Energy 268, 126669. doi:10.1016/j.energy.2023.126669
Ma, J., Cheng, Z., Ke, L., Yang, L., Yuan, D., Yang, Y., et al. (2022). Effects of coal gasifier slag on properties of mortar. Jiangxi Build. Mater. (05), 27–28+31.
Ma, Z., Xu, D., Feng, L., Chang, Q., and Fu, P. (2021). Effect of gypsum on the properties of pre-stressed duct grouting material. Concrete (8), 155–159.
Mou, C., Cheng, K., Liu, R., Jia, E., Sun, H., Niu, T., et al. (2022). Cooperative optimization of mineral admixtures of cement-based grouting materials for semi-flexible pavement. Bull. Chin. Ceram. Soc. 41 (3), 1102–1112.
Sha, F., Fan, R., Gu, S., and Xi, M. (2023). Strengthening effect of sulphoaluminate cementitious grouting material for water-bearing broken rocky stratum. Constr. Build. Mater. 368, 130390. doi:10.1016/j.conbuildmat.2023.130390
Shi, Y. (2020). Application and mechanism analysis of CSA expansion agent in grouting material. New Build. Mater. 47 (11), 134–137.
Shu, B., Zhou, M., Yang, T., Li, Y., Song, P., Chen, A., et al. (2021). Performance study and engineering application of grouting materials with a large content of solid waste. Constr. Build. Mater. 312, 125464. doi:10.1016/j.conbuildmat.2021.125464
Shu, B., Zhou, M., Yang, T., Li, Y., Song, P., Chen, A., et al. (2021). Performance study and engineering application of grouting materials with a large content of solid waste. Constr. Build. Mater. 312, 125464. doi:10.1016/j.conbuildmat.2021.125464
Song, X., Li, B., and Chen, M. (2014). Study on the influencing factors of properties of pre-stressed duct grouting material. Concrete (09), 138–141.
Song, X., Li, B., and Chen, M. (2014). Study on the influencing factors of properties of pre-stressed duct grouting material. Concrete (09), 138–141.
Standardization Administration of China, (2009). Testing method for strength of cement mortar (ISO method). Beijing, China: State Administration of Market Supervision and Administration; Standardization Administration of China.
Sun, Y., Huo, M., and Chen, X. (2020). Experimental study on a prestressed passage grouting material for negative temperature railway. New Build. Mater. 47 (9), 123–126.
Tan, X., Wu, X., Yang, J., Zhao, J., Zeng, H., and Liang, C. (2022). Effects of granite waste powder on the performance of cement mortar. China Concr. Cem. Prod. (10), 96–100.
Wang, H., Wang, C., Li, W., Zhang, B., Jiang, B., Yin, H., et al. (2022). Study on the preparation and performance of high strength grouting materials. China Concr. Cem. Prod. (9), 66–69.
Wang, L., and Zhang, S. (2017). Research of high fluidity grouting material of post-tensioned prestressed girder. Constr. Technol. 46 (5), 59–65121.
Xiang, J., Liu, L., Cui, X., He, Y., Zheng, G., and Shi, C. (2018). Effect of limestone on rheological, shrinkage and mechanical properties of alkali–Activated slag/fly ash grouting materials. Constr. Build. Mater. 191 (166), 1285–1292. doi:10.1016/j.conbuildmat.2018.09.209
Xie, C., Xie, C., Cao, M., Si, W., and Khan, M. (2020). Experimental evaluation on fiber distribution characteristics and mechanical properties of calcium carbonate whisker modified hybrid fibers reinforced cementitious composites. Constr. Build. Mater. 265, 120292. doi:10.1016/j.conbuildmat.2020.120292
Yang, H., Wu, W., Chen, D., Ye, X., Guo, Z., and Yao, T. (2019). Effect of expansive agent on the restrained expansion rate of duct grouting material. New Build. Mater. 46 (7), 56–59.
Yang, Y. (2020). Research on grouting defects of prestressed tunnel based on impact-echo method. Journal of Shenyang Jianzhu University (Nat. sci.) 36 (03), 457–464.
Zhang, H., Li, G., and Li, X. (2020). Study on the duct grouting materia with orthogonal experiment. Low. Temp. Archit. Technol. 42 (02), 21–23+52.
Zhang, P., Su, Y., Fan, J., Feng, H., Shao, J., Guo, H., et al. (2021). Experimental research on the mechanical behavior of grouted sleeves with fiber-reinforced grouting material under cyclic loading. Structures 34, 2189–2204. doi:10.1016/j.istruc.2021.08.083
Keywords: mineral admixture, working performance, mechanical properties, bleeding, dosage, grouting material
Citation: Shen Q, Jiang R, Cong B, Guo B, Shang H and Ji X (2023) Study on the effect of mineral admixtures on working and mechanical properties of the grouting material. Front. Mater. 10:1197997. doi: 10.3389/fmats.2023.1197997
Received: 31 March 2023; Accepted: 25 May 2023;
Published: 07 June 2023.
Edited by:
Yangyang Zhang, Yanshan University, ChinaReviewed by:
Waqas Ahmad, COMSATS University Islamabad, Abbottabad Campus, PakistanMuhammad Usman Farooqi, Capital University of Science & Technology, Pakistan
Copyright © 2023 Shen, Jiang, Cong, Guo, Shang and Ji. This is an open-access article distributed under the terms of the Creative Commons Attribution License (CC BY). The use, distribution or reproduction in other forums is permitted, provided the original author(s) and the copyright owner(s) are credited and that the original publication in this journal is cited, in accordance with accepted academic practice. No use, distribution or reproduction is permitted which does not comply with these terms.
*Correspondence: Ruishuang Jiang, cnVpc2h1YW5namlhbmdAMTYzLmNvbQ==