- 1National Engineering Laboratory for Modern Silk, College of Textile and Clothing Engineering, Soochow University, Suzhou, China
- 2Nano Fusion Technology Research Group, Institute for Fiber Engineering (IFES), Interdisciplinary Cluster for Cutting Edge Research (ICCER), Shinshu University, Nagano, Japan
- 3Yuyue Home Textile Co., Ltd., Binzhou, China
With the improvement of living standards, people’s awareness of health and environmental protection continues to strengthen. The production of textiles with antibacterial functions is one of the effective ways to protect people from or reduce bacterial invasion. Therefore, textiles with antibacterial functions are increasingly favored by people. At the same time, due to the impact of global warming, people are committed to reducing carbon emissions in all aspects of life. The biodegradable material polypropylidene carbonate (PPC) that can consume carbon dioxide (CO2) in the production process fully conforms to people’s environmental protection concept. However, polypropylidene carbonate itself has poor thermal stability and narrow application range. Polypropylidene carbonate thermoplastic polyurethane (PPC-TPU) is obtained by chain extension modification, which can broaden the application range of polypropylidene carbonate. To develop a yarn with excellent antibacterial and mechanical properties, which can be woven into fabrics for medical applications while taking into account environmental protection and degradability, the antibacterial yarn in this article was prepared by electrospinning using PPC-TPU and polylactic acid (PLA) yarn as raw materials. The preparation process was optimized by adjusting the supply speed, winding collection speed and horn barrel speed, and the optimal concentration of antimicrobial agent was explored by adding different concentrations of benzalkonium bromide antimicrobial. Through the characterization of the properties of the materials, we believe that PPC-PLA yarn with the addition of 5% benzalkonium bromide has broad development prospects in the medical field due to its excellent mechanical and antibacterial properties.
1 Introduction
With the progress of science and technology and the improvement of living standards, the demand for textiles is no longer limited to warmth and insulation, but extends to higher requirements for textile functionality, such as antibacterial, anti-mite, healthcare, and waterproof and moisture permeable properties (Cai et al., 2012; Chung and Lee, 2014; Rodriguez et al., 2014; Kong and Yang, 2021; Maleki et al., 2022). Since 2020, public health events triggered by epidemics have become the focus of global health and safety issues. Antibacterial modified textiles can effectively inhibit the growth and reproduction of microorganisms, block the transmission of bacteria in the human body and environment, and greatly reduce the risk of cross-infection (Qiu et al., 2020). Against this background, research on antibacterial modification of textiles has become a research hotspot in universities, enterprises, and research institutions.
Antibacterial functional yarn generally refers to functional textiles with antibacterial or bactericidal properties, and fibers are the precursor to yarn (HE-Yuan et al., 2013). Both natural fibers with antibacterial functions directly spun into yarn and synthetic fibers made by adding antibacterial materials into spinning solutions can be used as spinning materials for antibacterial yarns. Electrospinning is the only one that can produce continuous nanofibers in large quantities and is easy to obtain, cost-effective, and widely applicable, so it is one of the most widely used methods for preparing nanofibers (Costa et al., 2012; Liu et al., 2022). Compared with traditional antibacterial modification, nanofibers prepared by electrospinning technology have significantly improved antibacterial properties and durability (Li et al., 2009; Wang et al., 2020). However, currently, most nanofibers prepared by electrospinning technology are collected as randomly oriented non-woven fabric structures, and their poor mechanical properties limit their application range, mainly used in fields that do not require high fiber alignment, such as filtering materials, drug release, and wound dressings (Gibson et al., 2001; Bhardwaj and Kundu, 2010). Therefore, nanofibers need to be processed into yarns before they can be applied to textile processing technology like traditional fiber yarns (Smit et al., 2005). Then, a curling device was used to stretch the electrospun nanofibers that were previously in a random arrangement state, and the fibers were curled onto a spool. Wang and others used a self-bundling device to obtain nanofibers through electrospinning technology. To obtain self-bundling nanofiber yarn, a grounding needle was connected to one end of the device, and the yarn was stretched and collected onto a winding axis by moving the needle backward (Wang et al., 2008). Gu B.K et al. (Gu et al., 2007) used four-directional auxiliary electrodes to form a jet stream and then twisted the nanofibers to form yarns.
Antibacterial finishing technology is a technique for treating finished fabrics with antibacterial agents. Specifically, a solution containing antibacterial agents is applied to the fabric using coating, immersion, or other processes, and then the fabric is dried. The antibacterial agents are then fixed onto the fabric through adsorption, chemical bonding, or van der Waals forces, giving the fabric a certain degree of antibacterial function (Faheem et al., 2017; Gao et al., 2021). Common post-processing methods include impregnation, surface coating, and graft modification (Vila et al., 2020). Wei et al. (Wei et al., 2018) used electrospinning technology to prepare PAN nanofibers doped with indium-doped tin oxide nanoparticles, collected them in an ethanol bath to form electrospun nanofiber yarns, and then uniformly attached silver nanoparticles to the surface of ZnO nanorods. The resulting Ag-ZnO micro-nano particles with antibacterial function were introduced into the loose fiber structure, giving the fabric antibacterial properties. Kang et al. (Kang et al., 2016) connected carboxymethyl chitosan and silver nanoparticles to the surface of cotton fabric through atomization modification. The treated cotton fabric exhibited excellent antibacterial properties, and the inhibition rates of Escherichia coli and Staphylococcus aureus were both above 95% after 50 washes. Wang et al. (Wang et al., 2016) prepared a composite material of ZnO and chitosan (CMCS), and then used plasma technology to attach the material to the surface of the fabric, successfully obtaining fabric with antibacterial and UV-resistant properties.
Polypropylitic carbonate (PPC) is a new type of aliphatic carbonate material synthesized by open-loop copolymerization of carbon dioxide and propylene oxide. Because the main chain of PPC contains ester groups, it has good biodegradability and biocompatibility, and because PPC itself is non-toxic, low cost, strong plasticity and other advantages, it is expected to become the focus of research in the biomedical industry. However, the thermal stability of PPC itself is poor, which limits the application range of PPC. If PPC is modified into polypropylidene carbonate thermoplastic polyurethane (PPC-TPU) by chain extension, the molecular chain structure can be adjusted, and the modified high molecular weight PPC (PPC-TPU) has better performance. In our previous study, we used dicyclohexylmethane diisocyanate (HMDI) and 1, 4-butanediol (BDO) to prepare PPC-TPU by reacting with PPC.
This study used PPC-TPU as raw materials and DMF and acetone as solvents to prepare spinning solutions by adding different concentrations of low molecular weight organic antibacterial agents - benzalkonium bromide. The spinning solutions were collected through polylactic acid (PLA) yarn using electrospinning technology to prepare antibacterial nanofiber yarn. The optimal process for preparing the antibacterial yarn and fabric was explored through mechanical and antibacterial tests. At present, most antibacterial textiles on the market use post finishing, and their antibacterial properties will decrease with time and washing times. The process steps are cumbersome, and changes in temperature and humidity during the post finishing process may also affect the performance of the yarn itself. In addition, inorganic antibacterial agents such as Silver nanoparticle and nano zinc oxide are mostly used in the research of antibacterial textiles. The purpose of this study is to develop a yarn with excellent antibacterial and mechanical properties, which can be woven into fabrics for medical applications while taking into account environmental protection and degradability. In this article, quaternary ammonium salt antibacterial agent benzalkonium bromide is used to study the compatibility of benzalkonium bromide with PPC-TPU and its antibacterial effect on yarns. Usually, antibacterial yarns do not consider degradability issues. However, we use environmentally friendly biodegradable materials such as PPC and PLA as raw materials, which can improve the degradation performance of antibacterial yarns to a certain extent, reduce the pressure of global environmental pollution, and have good development prospects.
2 Experimental section
2.1 Experimental materials
The PPC-TPU was of our own manufacture. The PLA yarn was purchased from Shandong Huafang Spinning Co., Ltd. The Acetone (AT, Shanghai Lingfeng Technology Co., Ltd.), N,N-Dimethylformamide (DMF, J&K Scientific Co., Ltd.) and benzalkonium bromide (C21H38BrN, Shanghai Macklin Biochemical Technology Co., Ltd.) were used as received without further purification. All of the chemicals used were of analytical grade.
2.2 Experimental instruments and equipment
The characterization of our samples mainly include the materials structure, morphology, and performance. The morphology of the material was characterized by SEM (S-4800). The chemical group composition of the material was measured by Fourier Transform Infrared (FTIR) instrument (Bruker Vertex 70v). The material strength is characterized by a universal material stretching machine (CMT5105).
2.3 Synthesis of modified PPC
As shown in Figure 1A, the PPC used in this study is a product that has been modified through independent chain expansion. High molecular weight PPC-TPU was synthesized through chain extension reaction using low molecular weight liquid polypropylene carbonate polyol as raw material, adding isocyanate and chain extender. After the chain extension reaction, PPC changes from liquid particles to solid particles, with significant improvements in thermal stability and mechanical properties. Soluble in organic solvents such as acetone and DMF, which is more conducive to further experiments.

FIGURE 1. (A) PPC chain extension reaction process; (B) Physical image of PPC-PLA yarn; (C) Schematic diagram of electrospinning.
2.4 Preparation process of PPC-PLA yarn
2.4.1 PLA electrospinning process flow
As shown in Figure 1C, we have constructed a multi needle conjugated electrospinning device (Zhu et al., 2021). The conjugated configuration of the needle sprays spinning solution, and the nanofibers are bunched and twisted, and the winding device receives it. It can continuously prepare oriented nanofiber yarns, increasing production capacity. The yarn can meet the strength requirements of further production, and has uniform thickness, softness, and weaving ability, This provides a new way for the development of antibacterial textiles. Firstly, the syringe will spray nanofibers onto the trumpet shaped rotating cylinder. At this time, two syringes need to be used to spray fibers from both sides to the middle of the trumpet shaped rotating cylinder, ensuring a more uniform amount of nanofibers received by the rotating cylinder. PLA yarn passes through the center of the rotating cylinder, and as the rotating cylinder rotates, the sprayed fibers are evenly wrapped onto the PLA yarn in the center, forming a core-spun yarn structure with an outer layer of PPC-TPU nanofibers and an inner layer of PLA yarn, Finally, the yarn is collected by the rear cylindrical drum (Figure 1B).
2.4.2 PPC-PLA optimization of yarn electrospinning process
Using the spinning solution ratio obtained from our previous research, the solvent ratio is acetone: DMF = 3:7, with a PPC concentration of 40% added. Stir under a magnetic stirrer at 40°C for 4–5 h until evenly stirred. PPC-PLA core-spun yarn was prepared using multi needle conjugated electrospinning technology, and the core was made of degradable PLA yarn. Use two 5 mL sized syringes to extract 2 mL of spinning solution, discharge the air from the tube, connect the 18th needle (inner diameter 0.84 mm), and place it in the electrospinning machine. The needle and the receiving roller are connected to the positive and negative voltage poles respectively. The distance from the needle to the receiver is 15 cm, the applied voltage is 17–18 kV, the temperature is (23 ± 1.5)°C, and the relative air humidity is (40 ± 5)%.
In order to achieve the optimal PLA electrospinning effect, this chapter selected different liquid supply speeds of 0.1 mL/h, 0.3 mL/h, 0.5 mL/h, 0.7 mL/h, different winding collection speeds of 0.3 rpm, 0.5 rpm, 0.7 rpm, 1.0 rpm, and different horn speeds of 50 rpm, 100 rpm, 150 rpm, and 200 rpm for the spinning process The PPC-PLA yarn obtained at the speed of the trumpet was subjected to SEM testing to investigate its morphological and structural characteristics.
2.4.3 Preparation of antibacterial yarn
Add six concentration gradients of benzalkonium bromide antibacterial agents to the spinning solution, with concentrations of 1%, 2%, 3%, 5%, 7%, and 9% (w/v), and stir at 40°C for 2–3 h until evenly stirred to obtain the spinning solution with antibacterial agents added. Using the same electrospinning process as above.
2.5 Characterization of material properties
2.5.1 Mechanical testing
Clamp PLA yarn with a specialized fixture and test its mechanical properties using a dual arm universal material testing machine. The tensile rate is 50 mm/min, and the elongation of the yarn at complete fracture is recorded to obtain the maximum force (Fb) that the stress is subjected to at this time, divided by the original cross-sectional area (S0) of the sample, The unit is N/mm2 (MPa). The tensile strength can be calculated using Eq. 1
(Ivana et al., 2020). Wherein, Fb (N)- Maximum tensile force; S0 (mm2)- Yarn cross-sectional area.
2.5.2 Antibacterial performance testing
The plate counting method was used to select Gram-positive Staphylococcus aureus and Gram-negative Escherichia coli as representative strains. Take 20 cm of yarn from each concentration and sterilize overnight under ultraviolet light for later use. Add two bacterial liquids (CFU = 1 × 104) 500 μL and each sample yarn were co cultured in a shaking table at 37°C for 2 h, and then extract the cultured bacterial liquid 50 μL coated on the surface of the agar plate. The experimental group consisted of PPC-PLA yarns loaded with 3%, 5%, 7%, and 9% benzalkonium bromide, while the control group consisted of pure PPC-PLA yarns. Each group consists of three parallel groups.
3 Results and discussion
3.1 Best spinning process for PPC-PLA yarn
In order to explore the optimal spinning process of PLA yarn, this chapter examined variables such as liquid supply speed, winding collection speed, and horn speed. We used cold field emission scanning electron microscopy to verify the optimal spinning process of PPC-PLA yarn. Firstly, we investigated the spinning structures of different liquid supply speeds and selected four spinning processes with different liquid supply speeds: 0.1 mL/h, 0.3 mL/h, 0.5 mL/h and 0.7 mL/h, as shown in Figure 2A. After SEM analysis, Based on its cross-sectional analysis, a feeding speed of 0.1 mL/h does not effectively cover the surface of PLA yarn with PPC-TPU. The image displayed by scanning electron microscopy is closer to the blank sample state of PLA, while a feeding speed of 0.3 mL/h shows bead formation without obvious fiber morphology and obvious adhesion. A feeding speed of 0.7 mL/h shows clear fiber morphology, but there is still adhesion and bead formation, and the fiber surface is not smooth, The diameter distribution is uneven, while the diameter distribution of the yarn spun at a feed speed of 0.5 mL/h is more uniform, and the fiber surface is smoother, resulting in the best fiber forming effect; Secondly, the winding collection speed was investigated. At a fixed supply speed of 0.5 mL/h, four different spinning processes with winding collection speeds of 0.3 rpm, 0.5 rpm, 0.7 rpm and 1.0 rpm were selected, as shown in Figure 2B. Through SEM analysis, it was found that the winding collection speed of 0.3–0.5 rpm did not effectively cover the surface of PLA yarn with PPC-TPU, but it was observed that the coverage effect improved as the winding collection speed increased. Finally, at a winding and collection speed of 1.0 rpm, PPC-TPU can cover the surface of PLA yarn well; Similarly, the effect of cone speed on spinning process was investigated. In response to this factor, we investigated four different horn speeds of 50 rpm, 100 rpm, 150 rpm, and 200 rpm (as shown in Figure 2C). After SEM analysis, it was found that the horn speed of 50–150 rpm could not effectively cover the surface of PLA yarn with PPC-TPU, while the horn speed of 200 rpm achieved good PPC-TPU coverage. In summary, in the subsequent experiments, our spinning process was spun at a liquid supply speed of 0.5 mL/h, a winding collection speed of 1.0 rpm, and a horn speed of 200 rpm.
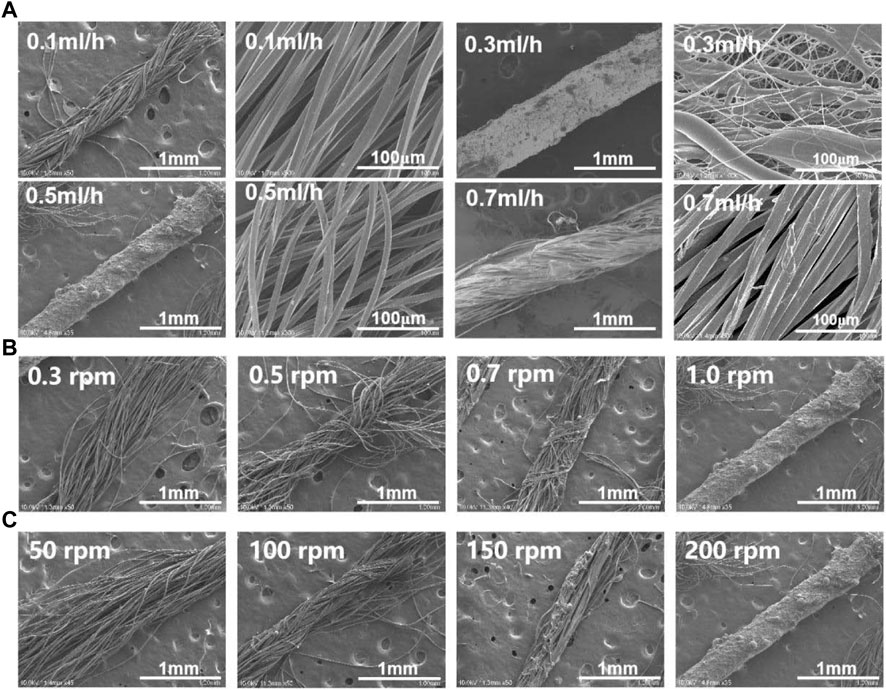
FIGURE 2. (A) SEM images and fiber diameter distribution of samples at different liquid supply speeds; (B) SEM images of samples collected at different winding speeds; (C) SEM images of samples at different horn speeds.
3.2 Infrared spectrum testing of PPC-PLA yarn under optimal spinning process
As shown in Figure 3A, from two infrared spectrum, it can be seen that there are strong double peaks at 1050-1300 cm-1, which are the absorption peaks of carboxylic acid ester bonds. At the same time, there is a clear ester carbonyl characteristic peak at 1750 cm-1, and an amino association characteristic peak of secondary amides at 3300 cm-1. The results show that the PPC-coating sample has obvious PPC-TPU characteristics. And the cross-sectional SEM images of PLA yarn and PPC-PLA yarn in Figure 3D can clearly, prove that PPC-TPU is well covered on PLA yarn.

FIGURE 3. (A) Infrared spectrum of PPC-PLA yarn under optimal spinning process and PPC-TPU; (B) The tensile elongation diagram of PPC-PLA yarn under the optimal spinning process; (C) The tensile strength diagram of PPC-PLA yarn under the optimal spinning process; (D) SEM images of PLA yarn cross-section (Left) and PPC-PLA yarn.cross-section (Right).
3.3 Mechanical properties testing of PPC-PLA yarn under optimal spinning process
We conducted mechanical tests on the PLA yarn after PPC-TPU spinning, with the elongation of the yarn at complete fracture as the testing endpoint. From Figures 3B, C, it can be clearly seen that the elongation at break of the PLA yarn after spinning increased from 9.58% to 19.07%. At the same time, the maximum stress suffered during the process was analyzed, and the tensile strength was obtained by dividing it by its cross-sectional area, which was 17.98N and 25.90N, respectively, and was 259.2 MPa and 3471 MPa, respectively, The tensile strength has been significantly improved, effectively improving the mechanical strength of PLA yarns.
3.4 Exploration of the optimal concentration of antibacterial agent added to PPC-PLA yarn using benzalkonium bromide as antibacterial agent
This study investigated the effect of benzalkonium bromide concentration on PPC-PLA yarn. Six concentration gradients were set for samples with benzalkonium bromide added. After SEM analysis, as shown in Figure 4A, it can be seen that adding 1%, 3% and 5% benzalkonium bromide has good fiber formation phenomenon, while adding 7% and 9% benzalkonium bromide has varying degrees of bead formation and adhesion. In comparison, adding 1%, 3% and 5% concentration benzalkonium bromide samples results in good fiber morphology, uniform diameter distribution, and smoother surface.
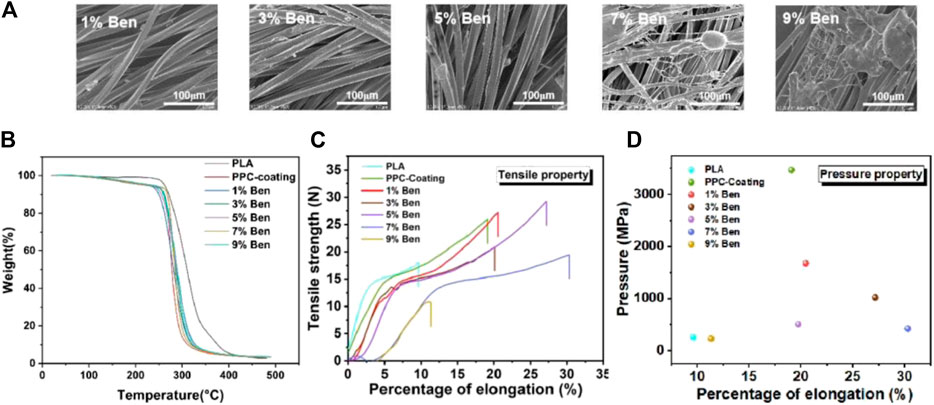
FIGURE 4. (A) SEM images of samples with different concentrations of benzalkonium bromide added; (B) Thermogravimetric analysis of PPC-PLA yarn with different concentrations of benzalkonium bromide added; (C) Schematic diagram of PPC-PLA yarn tension elongation with different concentrations of benzalkonium bromide added; (D) Schematic diagram of tensile strength of PPC-PLA yarn with different concentrations of benzalkonium bromide added.
3.5 Thermal properties analysis of PPC-PLA yarn using benzalkonium bromide as an antibacterial agent
Figure 4B shows the thermogravimetric curves of PPC-PLA yarns with benzalkonium bromide at different concentrations and pure PLA yarns without PPC-TPU in the control group. When comparing the thermogravimetric curves of pure PLA yarn with PPC-PLA yarn with benzalammonium bromide antibacterial agent, a slight difference in thermal decomposition temperature can be observed. The initial decomposition temperature is about 214°C and 262°C respectively, which is considered to be due to the low thermal decomposition temperature of PPC-TPU, which is covered with PLA yarn and partially cross-linked with PLA polymer structure. The thermal decomposition temperature of the original PLA yarn was affected. The thermogravimetric curves of PLA yarn with six different concentrations of benzalammonium bromide antibacterial agent were further observed. It was found that the concentration of benzalammonium bromide had little effect on the overall thermal decomposition temperature of yarn, and the thermogravimetric curves were consistent. The reason is that its nature is stable and it will not interact with the yarn system to affect its thermal decomposition temperature. Therefore, it is more appropriate to select benzalammonium bromide as an antibacterial agent to be added into PLA yarn, which has antibacterial effect without affecting the related properties of yarn.
3.6 Analysis of mechanical properties of PPC-PLA yarns using benzalkonium bromide as an antibacterial agent
Figures 4C, D show the tensile test results of PPC-PLA yarn with different concentrations of benzalkonium bromide added. It can be seen that the concentration of benzalkonium bromide has a significant impact on the mechanical properties of PPC-PLA yarn. As the concentration of benzalkonium bromide increases, the tensile strength of PLA yarn gradually decreases. Although the tensile strength of PLA yarn covered with PPC-TPU is reduced compared to pure PLA yarn, the addition of lower concentrations of benzalkonium bromide can still maintain good tensile strength, and the stress-strain curve follows an elastic material curve. In addition, considering the factors of tensile strength, the mechanical properties of yarns added with 9% concentration of benzalkonium bromide are poor. Compared with pure PLA yarns and PLA yarns covered with PPC-TPU, the addition of benzalkonium bromide can effectively improve their mechanical properties with a tensile rate of 9.58% and 19.08%. Compared to 5% and 7%, 3% has poor tensile force and strength. When the concentration of benzalkonium bromide is 5% and 7%, the fracture elongation is higher and similar to 27.15% and 30.31%. However, from the perspective of tensile strength, its corresponding tensile strength is 507.5 MPa and 423 MPa. Therefore, adding 5% concentration can withstand greater force. At the same time, we can see that the mechanical strength of the yarn with a concentration of 9% is poor, mainly due to the uneven distribution of nanofibers on the surface of PLA yarn (as shown in Figure 4A), resulting in uneven stress on the yarn. Taking into account mechanical factors, it is believed that the addition of 5% concentration of benzalkonium bromide has good tensile strength, while also providing higher elongation at break and stronger tensile properties. Madheswaran et al. (Madheswaran et al., 2022) used polyurethane (PU) yarns and polyamide 6 (PA6) yarns as the substrate, and wrapped a layer of antibacterial nanofiber film containing chlorhexidine (CHX) on the yarn, thereby preparing surgical sutures with good antibacterial and mechanical properties. Although the mechanical properties of the samples coated with nanofiber films in their study were improved compared with the original yarns, the breaking strength was all below 2.5N, which was not as good as that of the samples in this study.
3.7 Analysis of antibacterial performance of PPC-PLA yarns using benzalkonium bromide as an antibacterial agent
We used the plate counting method to test the antibacterial performance of samples with different concentrations of benzalkonium bromide added. As shown in Figures 5A, B, it is clear that the control group without the addition of antibacterial agent has no antibacterial performance. Only 1% of the five concentrations in the experiment have a few colonies, the antibacterial rate of Escherichia coli is 86%, the antibacterial rate of Staphylococcus aureus is 78%, and 3%–9% have excellent antibacterial performance, the antibacterial rate reaches 100%, and no colonies are produced. Benzalkonium bromide has a strong antibacterial ability, because its structure contains positively charged Quaternary ammonium cation cations, which are easy to absorb negatively charged microorganisms on the surface, hinder their physiological activities, and play a bactericidal role (Semreen et al., 2018). Overall, the PPC-PLA yarn with the addition of benzalkonium bromide as an antibacterial agent has excellent antibacterial properties. Lou et al. (Lou et al., 2023) selected Hydroxypropyl cellulose (HPC) and Polyvinyl pyrrolidone (PVP) as raw materials and wrapped them on absorbable collagen sutures by electrospinning technology, and added different concentrations of zinc acetate to the HPC/PVP spinning solution to make it have antibacterial properties. Many colonies were still generated in the plate counting experiment of HPC/PVP/Zn nanofiber yarns at low zinc acetate concentrations. Only HPC/PVP/Zn nanofiber yarns with high zinc acetate concentration can achieve 99.9% bacteriostatic rate.
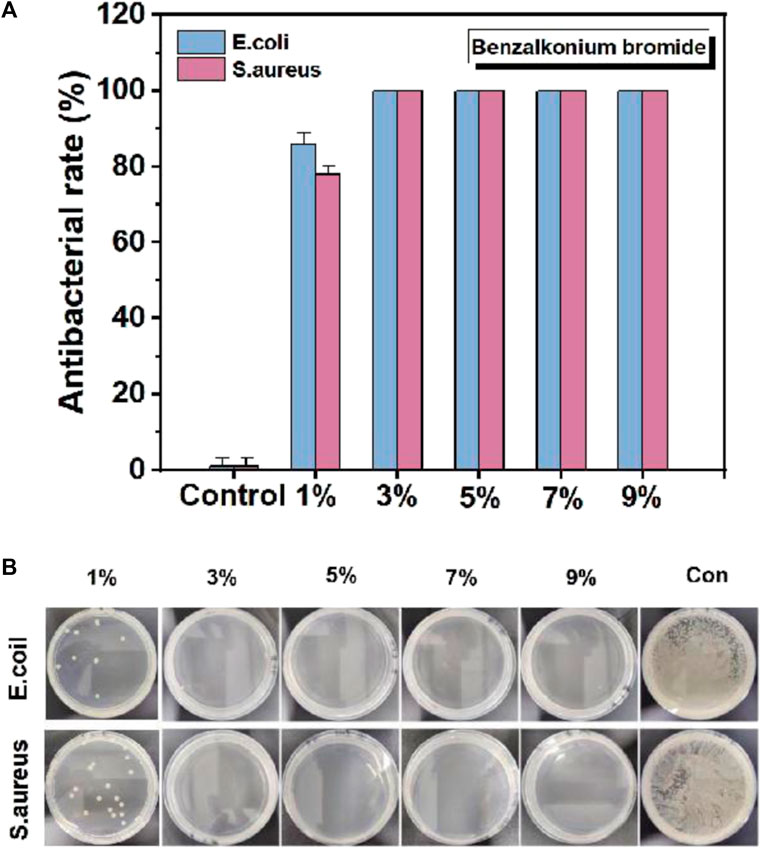
FIGURE 5. Antibacterial effect of adding different concentrations of benzalkonium bromide PLA spinning under plate counting method. (A) The antibacterial rate of benzalkonium bromide at different concentrations, and (B) the number of bacterial colonies at different concentrations of benzalkonium bromide.
4 Conclusion
In this article, we prepared PPC-PLA yarn with an outer layer of PPC-TPU nanofibers and an inner layer of PLA yarn by electrospinning technology. Through optimization of the spinning process and antibacterial performance testing, we obtained good mechanical strength and application value.In summary, we believe that PPC-PLA yarn with the addition of 5% benzalkonium bromide has broad development prospects in the medical field due to its excellent mechanical and antibacterial properties. Electrospinning technology makes it easier to produce, and the use of biodegradable materials that consume carbon dioxide as raw materials makes it more environmentally friendly and can be used to prepare new antibacterial yarns and fabrics for cutting-edge medical applications.
Data availability statement
The original contributions presented in the study are included in the article/Supplementary Material, further inquiries can be directed to the corresponding author.
Author contributions
K-QZ: Writing–review and editing, Funding acquisition, Supervision. NZ: Writing–original draft, Conceptualization, Data curation, Formal Analysis, Methodology, Project administration. LZ: Data curation, Investigation, Software, Validation, Visualization, Writing–original draft. Y-HD: Funding acquisition, Resources, Supervision, Writing–review and editing. IK: Resources, Supervision, Writing–review and editing. H-GG: Resources, Writing–review and editing.
Funding
The authors declare financial support was received for the research, authorship, and/or publication of this article. This research was funded by Natural Science Foundation of China, grant number 51873134.
Acknowledgments
The authors acknowledge the financial support from China National Textile and Apparel Council Key Laboratory for Silk Functional Materials and Technology, Priority Academic Program Development of Jiangsu Higher Education Institutions (PAPD).
Conflict of interest
Author H-GG was employed by Yuyue Home Textile Co., Ltd.
The remaining authors declare that the research was conducted in the absence of any commercial or financial relationships that could be construed as a potential conflict of interest.
Publisher’s note
All claims expressed in this article are solely those of the authors and do not necessarily represent those of their affiliated organizations, or those of the publisher, the editors and the reviewers. Any product that may be evaluated in this article, or claim that may be made by its manufacturer, is not guaranteed or endorsed by the publisher.
Supplementary material
The Supplementary Material for this article can be found online at: https://www.frontiersin.org/articles/10.3389/fmats.2023.1257394/full#supplementary-material
References
Bhardwaj, N., and Kundu, S. C. (2010). Electrospinning: A fascinating fiber fabrication technique. Biotechnol. Adv. 28 (3), 325–347. doi:10.1016/j.biotechadv.2010.01.004
Cai, X., Lin, M. S., Tan, S. Z., Mai, W. J., Zhang, Y. M., Liang, Z. W., et al. (2012). The use of polyethyleneimine-modified reduced graphene oxide as a substrate for silver nanoparticles to produce a material with lower cytotoxicity and long-term antibacterial activity. Carbon 50 (10), 3407–3415. doi:10.1016/j.carbon.2012.02.002
Chung, J., and Lee, S. (2014). Development of nanofibrous membranes with far-infrared radiation and their antimicrobial properties. Fibers Polym. 15 (6), 1153–1159. doi:10.1007/s12221-014-1153-4
Costa, R. G. F., de Oliveira, J. E., de Paula, G. F., Picciani, P. H. D., de Medeiros, E. S., Ribeiro, C., et al. (2012). Eletrofiação de polímeros em solução: parte II: aplicações e perspectivas. Polimeros-Ciencia E Tecnol. 22 (2), 178–185. doi:10.1590/s0104-14282012005000018
Faheem, S., Baheti, V., Behera, P., and Naeem, S. (2017). Development of flame retardant high loft polyester nonwovens. J. Text. Inst. 108 (8), 1357–1364. doi:10.1080/00405000.2016.1251289
Gao, D. G., Li, X. J., Li, Y. J., Lyu, B., Ren, J. J., and Ma, J. Z. (2021). Long-acting antibacterial activity on the cotton fabric. Cellulose 28 (3), 1221–1240. doi:10.1007/s10570-020-03560-5
Gibson, P., Schreuder-Gibson, H., and Rivin, D. (2001). Transport properties of porous membranes based on electrospun nanofibers. Colloids Surfaces a-Physicochemical Eng. Aspects 187, 469–481. doi:10.1016/s0927-7757(01)00616-1
Gu, B. K., Shin, M. K., Sohn, K. W., Kim, S. I., Kim, S. J., Kim, S. K., et al. (2007). Direct fabrication of twisted nanofibers by electrospinning. Appl. Phys. Lett. 90 (26). doi:10.1063/1.2753109
He-Yuan, , Cheng-Shu, X. U., and Wen-Zhao, S. (2013). Research progress in antimicrobial finish of textiles. Dye. Finish.
Ivana, S., Stana, K., and Ivana, V. (2020). Influential parameters of starching process on mechanical properties of yarns intended for multifunctional woven fabrics for thermal protective clothing. Polymers 13 (1), 73. doi:10.3390/polym13010073
Kang, C. K., Kim, S. S., Kim, S., Lee, J., Lee, J. H., Roh, C., et al. (2016). Antibacterial cotton fibers treated with silver nanoparticles and quaternary ammonium salts. Carbohydr. Polym. 151. doi:10.1016/j.carbpol.2016.06.043
Kong, Q. D., and Yang, Y. S. (2021). Recent advances in antibacterial agents. Bioorg. Med. Chem. Lett. 35, 127799. doi:10.1016/j.bmcl.2021.127799
Li, L., Li, Y., Li, J. S., Yao, L., Mak, A. F. T., Ko, F., et al. (2009). Antibacterial properties of nanosilver PLLA fibrous membranes. J. Nanomater. 2009. doi:10.1155/2009/168041
Liu, R. R., Hou, L. L., Yue, G. C., Li, H. K., Zhang, J. S., Liu, J., et al. (2022). Progress of fabrication and applications of electrospun hierarchically porous nanofibers. Adv. Fiber Mater. 4 (4), 604–630. doi:10.1007/s42765-022-00132-z
Lou, C. W., Hung, C. Y., Wei, M. D., Li, T. T., Shiu, B. C., and Lin, J. H. (2023). Antibacterial surgical sutures developed using electrostatic yarn wrapping technology. J. Funct. Biomaterials 14 (5), 248. doi:10.3390/jfb14050248
Madheswaran, D., Sivan, M., Valtera, J., Kostakova, E. K., Egghe, T., Asadian, M., et al. (2022). Composite yarns with antibacterial nanofibrous sheaths produced by collectorless alternating-current electrospinning for suture applications. J. Appl. Polym. Sci. 139 (13), 51851. doi:10.1002/app.51851
Maleki, H., Yilmaz, D., Rahbar, R. S., and Aksoy, S. A. (2022). Electrospun poly (lactic acid) -cotton core-shell yarns: processing, morphology, and mechanical properties. J. Compos. Mater. 56 (23), 3541–3552. doi:10.1177/00219983221116670
Qiu, Q. H., Chen, S. Y., Li, Y. P., Yang, Y. C., Zhang, H. N., Quan, Z. Z., et al. (2020). Functional nanofibers embedded into textiles for durable antibacterial properties. Chem. Eng. J. 384, 123241. doi:10.1016/j.cej.2019.123241
Rodriguez, C., Di Cara, A., Renaud, F. N. R., Freney, J., Horvais, N., Borel, R., et al. (2014). Antibacterial effects of photocatalytic textiles for footwear application. Catal. Today 230, 41–46. doi:10.1016/j.cattod.2013.12.023
Semreen, M. H., El-Gamal, M. I., Abdin, S., Alkhazraji, H., Kamal, L., Hammad, S., et al. (2018). Recent updates of marine antimicrobial peptides. Saudi Pharm. J. 26 (3), 396–409. doi:10.1016/j.jsps.2018.01.001
Smit, E., Buttner, U., and Sanderson, R. D. (2005). Continuous yarns from electrospun fibers. Polymer 46 (8), 2419–2423. doi:10.1016/j.polymer.2005.02.002
Vila, J., Moreno-Morales, J., and Balleste-Delpierre, C. (2020). Current landscape in the discovery of novel antibacterial agents. Clin. Microbiol. Infect. 26 (5), 596–603. doi:10.1016/j.cmi.2019.09.015
Wang, C. X., Lv, J. C., Ren, Y., Zhou, Q. Q., Chen, J. Y., Zhi, T., et al. (2016). Cotton fabric with plasma pretreatment and ZnO/Carboxymethyl chitosan composite finishing for durable UV resistance and antibacterial property. Carbohydr. Polym. 138, 106–113. doi:10.1016/j.carbpol.2015.11.046
Wang, F., Dai, J., Huang, L., Si, Y., and Ding, B. (2020). Biomimetic and superelastic silica nanofibrous aerogels with rechargeable bactericidal function for antifouling water disinfection. ACS Nano 14, 8975–8984. doi:10.1021/acsnano.0c03793
Wang, X. F., Zhang, K., Zhu, M. F., Yu, H., Zhou, Z., Chen, Y. M., et al. (2008). Continuous polymer nanofiber yarns prepared by self-bundling electrospinning method. Polymer 49 (11), 2755–2761. doi:10.1016/j.polymer.2008.04.015
Wei, Y. F., Chong, Y. B., Du, H. J., Kong, J. H., and He, C. B. (2018). Loose yarn of Ag-ZnO-PAN/ITO hybrid nanofibres: preparation, characterization and antibacterial evaluation. Mater. Des. 139, 153–161. doi:10.1016/j.matdes.2017.10.061
Keywords: electrospinning, nanofibers, yarn, antibacterial, polypropylidene Carbonate, polylactic Acid
Citation: Zhou N, Zhu L, Dong Y-H, Kim IS, Gao H-G and Zhang K-Q (2023) Preparation of biodegradable polypropylene carbonate-polylactic acid core yarn by electrospinning and its antibacterial finishing. Front. Mater. 10:1257394. doi: 10.3389/fmats.2023.1257394
Received: 12 July 2023; Accepted: 21 August 2023;
Published: 05 September 2023.
Edited by:
Jong Seto, University of California, United StatesReviewed by:
Haitao Yu, University of California, United StatesSakshi Yadav Schmid, Pacific Northwest National Laboratory (DOE), United States
Copyright © 2023 Zhou, Zhu, Dong, Kim, Gao and Zhang. This is an open-access article distributed under the terms of the Creative Commons Attribution License (CC BY). The use, distribution or reproduction in other forums is permitted, provided the original author(s) and the copyright owner(s) are credited and that the original publication in this journal is cited, in accordance with accepted academic practice. No use, distribution or reproduction is permitted which does not comply with these terms.
*Correspondence: Ke-Qin Zhang, a3F6aGFuZ0BzdWRhLmVkdS5jbg==