- 1Department of Electricity and Energy, Kırıkkale Vocational School, Kırıkkale University, Kırıkkale, Türkiye
- 2Control and Automation Department, Kırıkkale Vocational School, Kırıkkale University, Kırıkkale, Türkiye
- 3Electrical and Electronics Engineering Department, Faculty of Engineering, Kırıkkale University, Kırıkkale, Türkiye
- 4Department of Mechanical Engineering, Gazi University Faculty of Engineering, Ankara, Türkiye
- 5Project Coordination Implementation and Research Center, Gazi University, Ankara, Türkiye
- 6Department of Biosciences, Saveetha School of Engineering, Saveetha Institute of Medical and Technical Sciences, Chennai, India
- 7Department of Machining, Assembly and Engineering Metrology, Faculty of Mechanical Engineering, VSB-Technical University of Ostrava, Prague, Czechia
- 8Department of Industrial Engineering, College of Engineering, King Saud University, Riyadh, Saudi Arabia
This experimental study investigated the abrasive wear behaviour of pure copper-based and multi-walled carbon nanotube (MWCNT) doped composites synthesized by the powder metallurgy technique. Composite structures were formed by reinforcing MWCNT at different ratios between 1% and 8% in 99.9% pure copper by powder metallurgy. The microstructures of the nanocomposite samples were analyzed by X-ray diffraction. Then, density and hardness measurements and abrasive wear tests were performed to determine their mechanical properties. The collected data were evaluated with scanning electron microscopy images. It has been determined that copper’s nano-sized carbon reinforcement material has a dry lubricant effect up to a specific ratio, reducing wear losses. On the contrary, wear losses increase as the MWCNT reinforcement ratio increases between 4% and 8%. The best results in lowering wear losses were obtained from the sample with 1% MWCNT reinforcement. Depending on the increase in the amount of nanomaterial reinforcement in the composite structure, it was observed that pore formation enlarges with reinforcement agglomeration. It was concluded that the dense porosity in the composite structure neglects the lubricating properties of the MWCNT reinforcement material and increases the wear losses by having a negative effect.
1 Introduction
Humans have used copper for thousands of years because of the properties of copper, such as high thermal and electrical conductivity, self-lubricating and high melting temperature. It is widely used in the electricity, marine, aviation, automotive, and railway commonly used in industries. However, despite some advantages, its use in heavy-duty applications is limited due to its weak strength and low tribological properties. (Pan et al., 2019; Sadoun et al., 2021). Copper is also one of the most widely used electrical materials and is vital in power systems, transportation, electronics and aerospace. To improve the mechanical properties of copper, different ceramics and nano-sized carbon materials are doped into it. These insoluble and stable particles vary according to the target application. These materials are usually ceramic materials such as oxides (Al2O3, SiO2), borides (TiB2, ZrB2), nitrides (TiN, ZrN), carbides (SiC, B4C, TiC) and carbonaceous materials (carbon nanotubes (CNTs), graphite, graphene, diamond) (Saboorı et al., 2018). In recent years, with the rapid development of precision machinery, high-speed electric railways, aerospace, automotive and other fields, the friction and wear conditions on these working surfaces rapidly deteriorated, leading to significant reductions in the service life and stability of existing parts. One of the effective ways to solve this problem is to select a suitable reinforcement and control the composite structure and interface to prepare copper matrix composites with excellent wear resistance and mechanical properties. The above-mentioned ceramic particle reinforcements improve wear resistance (Zheng et al., 2021a). With the rapid development of materials technology, one way to meet these requirements is to develop suitable nano-reinforced Cu-based composites.
There are various allotropes of the carbon atom. Diamond and graphite are 3D allotropes of carbon. Carbon also forms low-dimensional (2D, 1D, or 0D) allotropes known collectively as carbon nanomaterials. Examples of such nanomaterials are 1D CNTs and 0D fullerenes. Graphene is known as 2D monolayer graphite (Kumar et al., 2015) in the list of carbon nanomaterials. CNTs are rolled sheets of carbon atoms with the same sp2-hybridized structure and have excellent lubricating properties (Wu et al., 2020). Carbon nanotubes (CNTs) are cylindrical structures similar to a rolled graphene sheet with a nanoscale diameter (Wang et al., 2020). CNTs are promising due to their unique structural properties, good electrical and mechanical properties, excellent heat transfer and electrical conductivity, high-temperature strength, and self-lubrication. Therefore, efforts and scientific studies have been made to produce CNT-doped composites with Cu matrix and improve their properties (Sharma et al., 2019; Zuo et al., 2020). CNTs have been proposed as an ideal reinforcement to enhance the mechanical properties of the matrix due to their excellent properties, such as high elastic modulus, high strength, and good thermal/electrical properties (Duan et al., 2019; Muhammet, 2019). Multi-walled carbon nanotubes (MWCNTs) can be defined as concentrically arranged layers of graphene carbon cylinders and were first described by Iijima in 1991 after using an arc discharge evaporation method similar to that used for fullerene synthesis (Jansson, 2021).
Different techniques, such as compression casting, stir casting, infiltration, mechanical alloying, and powder metallurgy, produce metal matrix composites. The mechanical properties of composite materials, such as strength, elastic modulus, and elongation, depend highly on the production method (Sadoun et al., 2021). When the literature is examined, studies examine the properties of composites formed by reinforcing carbon-based nanomaterials into the copper matrix with different production methods (Zhang et al., 2017; Chen et al., 2019; Zhang et al., 2021; Pul, 2022a; Koltsova et al., 2022; Tan et al., 2022; Chika et al., 2023; Singh et al., 2023).
2 Materials and methods
This experimental study used copper (Cu) with an average grain size of 325 mesh with 99.99% commercial purity purchased from Nanografi-Nanoteknoloji-Turkey as the matrix material. Multi-walled carbon nanotubes (MWCNT) used in nanocomposites were also purchased from Nanografi Nanoteknoloji Turkey, and some technical properties of the nanomaterial are given in Table 1.
In this experimental study, the powder metallurgy technique produced nanocomposite structures. For this purpose, firstly, the weight ratios of the matrix and reinforcement materials that will form the composite structure were determined and weighed on a scale with a precision of 1:10000 g. Then, a ZrO2 ball with a diameter of 5 mm was added into the rotary drum mixer at a ratio of 10:1 and homogeneous composite mixtures were obtained by mixing at 300 rpm for 3 h. Furthermore, compact test specimens were obtained by compressing with 700 MPa pressure in a 16 mm diameter mould. In the last stage of the production process, the production process was completed by applying sintering heat treatment at 950°C temperature for 2 h. The matrix-reinforcement ratios used in producing nanocomposite structures are given in Table 2.
The nanocomposite structures were imaged in LEO 1430VP brand/model scanning electron microscope (SEM) to visualize their microstructures, and EDS elemental analyses were performed. In addition, additional imaging and EDS analysis were performed with a HITACHI SU5000 field emission scanning electron microscope (FE-SEM) capable of shooting at higher magnifications to detect nano-sized MWCNT reinforcement particles in the composite structure. X-RD analyses were then performed to examine the phase structures. X-RD analyses were performed with a Shimadzu XRD-6000 LabX model device at 2°/min. They are scanning speed, using Cu K alpha X-ray from 10 to 100° 20 in 0.02-degree steps. Density and hardness measurements were performed to determine the mechanical properties of the composite structures. The densities of the composite structures were calculated according to the mixing rule in Eq. 1, and the porosity amounts were determined according to Eq. 2.
Here, V, unit volume, is the unit density.
Here, ρth is the theoretical density, and ρexp is the experimental density.
Hardness measurements were performed using the Vickers method with a 300 g load and 15 s application time. In the last stage of the study, wear tests were carried out to determine the abrasive wear behaviour of the nanocomposites. Abrasion tests were carried out on 600 mesh size sandpaper at a speed of 1.0 m-1, and 20 N and 40 N loads were applied at 60 min and 120 min. A schematic view of the pin-on-disc test method is given in Figure 1.
Based on the wear loss amounts obtained from the experiments, wear rates K were calculated according to Eq. 3.
In Eq. 3, W (mm3) is the wear volume, K is the wear factor (mm3/Nm), F (N) is the force, V (m/s) is the linear velocity, and T (s) is the test duration. The wear factor indicates the resistance of materials to wear as a function of the volume lost at the wear interface and time, force, and velocity.
3 Results and discussion
3.1 Microstructure
The microstructure images of Cu matrixed MWCNT nanomaterial-reinforced composites produced by powder metallurgy, captured by SEM at ×200 magnification, are given in Figure 2.
The SEM images in Figure 2. Present the different distribution characteristics of the MWCNT doping in the composite structure, which stands out in the first place. It is seen that the porous regions (black regions in the structure) are gradually increasing due to the increase in the amount of nano-reinforcement materials in the composite structure. One of the most common problems in such nano-reinforced composite structures is the inhomogeneous distribution of the reinforcement particles and their tendency to agglomerate together densely (Zuo et al., 2020). A literature review shows that similar reinforcement agglomeration results have been reported in CNT-reinforced and metal matrix composite studies (Zhou et al., 2017a; Şenel et al., 2017). The agglomerated particles caused the formation of porous regions by partially preventing the bonding of the matrix material particles. In addition, those regions deter heat transfer during the sintering. As a result, MWCNT reinforcement has a very high thermal resistance due to its nature; it can act as a thermal barrier and reduce the effect of the sintering process. A study reported that CNT agglomeration prevents the densification and bonding of the matrix in the sintering process applied in the powder metallurgy process and deteriorates the mechanical properties of the composite (Liu et al., 2017).
The homogeneity gradually deteriorated with the increase in the MWCNT ratio in the composite structure, and porous regions started to form. In the literature study, it was reported that homogeneous reinforcement distribution was obtained when a low volume percentage of CNTs was used, and CNT reinforcement of more than 2 wt% did not improve mechanical properties (Rais and Sharma, 2015). EDS analysis was carried out to prove copper’s elemental presence as the composite structure’s main constituent and MWCNT as the reinforcing element. For this purpose, EDS analysis of 1% MWCNT reinforced composite samples is given in Figure 3.
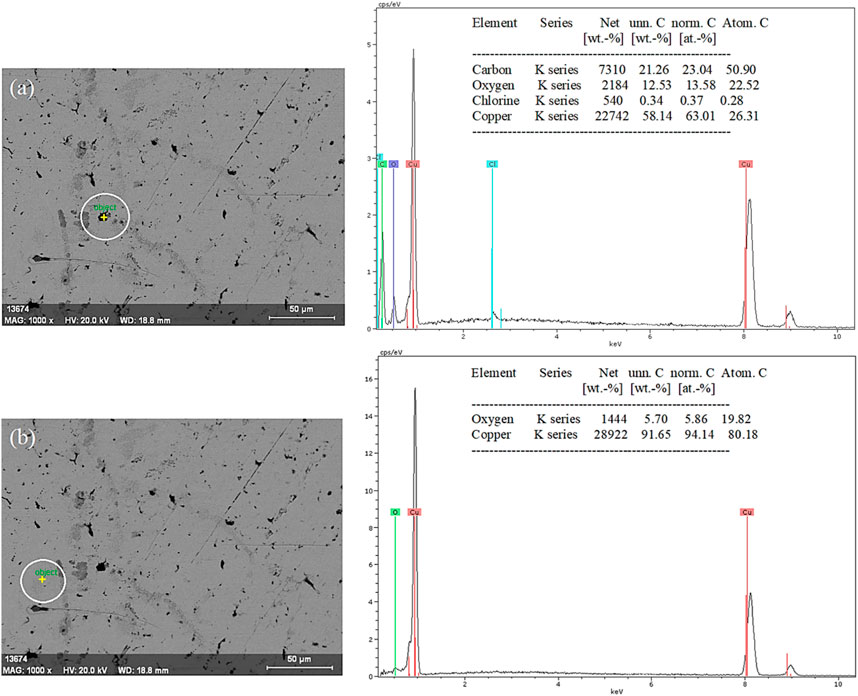
FIGURE 3. EDS analysis of Cu/MWCNT composite structures; (A) reinforcement material, (B) matrix material.
When Figure 3A is examined, it is understood that a high proportion of carbon is in the EDS analysis taken from the region with intense blackness. In addition, it is seen that some oxidation occurred during the sintering heat treatment, which appears as oxygen in the same region. Figure 3B shows the presence of copper, which forms the main structure, and the presence of oxygen with oxidation on the surface. Therefore, it can be stated that the black regions in the microstructure images are mostly filled with carbon-based nanomaterials. At the same time, air gaps in the volumes formed by these dark-coloured regions, which means porous regions, appear as oxygen in EDS analysis. Because the elemental analysis in Figure 3A shows that there is approximately 22% oxygen. In addition, it is understood that oxidation also occurs on the surface of the matrix material Cu in Figure 3B analysis, with 19% oxygen detected. It is also understood from these analyses that copper is a metal that can be oxidized very quickly. The copper matrix’s surface oxidation is a common problem during the composite production process. Research has been conducted on the causes and elimination issues by examining different studies in the literature (Singhal et al., 2012; WuHou et al., 2019).
3.2 Phase analysis (X-RD)
The graphs of XRD analyses performed to investigate the phase and crystal structures of MWCNT-reinforced Cu-based composite structures after sintering heat treatment are given in Figure 4. XRD analyses were performed on the lowest, highest and medium (1%, 4%, 8%) MWCNT reinforced samples to better understand the differences between the composite structures.
The X-RD graph in Figure 4 shows that the most intense reflection for the surface-centered cubic (FC) Cu element in all three composite structures is in the (111) plane at 2θ. Subsequent reflection peaks occurred at (200) and (220) planes. Similar studies have the same results (Kumar et al., 2018; Akbarpour et al., 2019). It is seen that Cu2O phases occur in 4% and 8% MWCNT reinforced composites, unlike 1% MWCNT reinforced composites. It is understood that the matrix material copper is oxidized by the effect of oxygen remaining in the environment during the sintering heat treatment. In a study in the literature, the formation of amorphous copper oxides (CuxOy) between CNTs and Cu is attributed to oxygen diffusion and the thermodynamic reaction that occurs during internal oxidation (Long et al., 2022). As a result of the reaction between the Cu matrix material and MWCNT reinforcing elements, it is seen that a different phase structure is not formed. In addition, due to the deficient concentration of carbon-based MWCNT in the hexagonal P63/MMC crystal structure, the densest peak in the (002) plane at 2θ is not seen in any of the composite structures.
3.3 Porosity and hardness
The porosity values determined according to the density measurements of Cu composite samples reinforced with MWCNT at different ratios are given in the graph in Figure 5.
Figure 5 shows that the amount of porosity gradually increases with the effect of MWCNT doping in the composite structure. In the pure Cu reference sample without MWCNT reinforcement, 19.5% porosity was detected. The powder metallurgy method forms more porosity than other composite production methods. Especially during the sintering heat treatment process, hollow regions can be formed during the expansion of the metals forming the main structure and the growth of their volumes. In addition, ceramic or graphene-based reinforcement materials added to such metallic composites have much lower expansion coefficients than metals. At sintering temperatures applied according to the melting temperature of the matrix metal, the reinforcing materials in the metal are not much affected by the applied sintering temperatures and do not show expansion behaviour. In this case, due to the different thermal behaviour of the matrix and reinforcement materials, there is not enough wetting in the composite structure, and pores are formed between the particles separated from each other. Another critical reason for porosity in Cu/MWCNT composite structures is the MWCNT reinforcement material that exhibits agglomeration behaviour in the Cu matrix. A study in the literature stated that the agglomeration of CNTs significantly reduces the reinforcement effects and makes it difficult to achieve uniform and stable properties of the composites. In addition, the significant difference in bulk density between Cu and CNTs is reported to cause difficulties in the mixing process of matrix and reinforcement (Zheng et al., 2022). In another study, MWCNT with a high reinforcement ratio was reported to cause agglomeration (Stalin et al., 2021). This issue was explained in the section on microstructure evaluation by drawing attention to the SEM images in Figure 2. However, to identify the MWCNT reinforcement particles agglomerated in the porous regions of the composite structure, FE-SEM images taken at different magnifications are given consecutively in Figure 6. In Figure 6C, the MWCNT reinforcement particles, which are densely agglomerated and become a ball, are visible.
The graph of the values obtained from the hardness measurements of Cu composite samples reinforced with MWCNT at different ratios by the Vickers method is given in Figure 7.
In Figure 7, it is seen that there is a significant decrease in hardness values with the effect of nanomaterial reinforced in the Cu matrix. Similar results were noted in different studies in the literature (Garg et al., 2016; Zhou et al., 2017b). The most important reason for this is the porosity in the composite structure. When the porosity values in Figure 5 are examined, it is seen that the pore ratios increase depending on the increase in the amount of MWCNT in the composite structure. Therefore, increasing porosity and decreasing hardness are in a direct proportional relationship. Compared to pure Cu matrix material, while the hardness value of the 1% MWCNT reinforced sample decreased by 50%, this value decreased by approximately 400% in the 8% MWCNT reinforced sample. There is a direct proportional increase between the rate of decrease in hardness values and MWCNT reinforcement ratios. The hardness value decreased eight times as the MWCNT reinforcement ratio increased eight times. The other reason for the low mechanical strength in such composite structures is the composite production technique applied. A study reported that the lack of ductility and strength of composite components produced by powder metallurgy (PM) is one of the disadvantages of the PM method (Mohammed Ridha, 2022).
3.4 Abrasive wear
This experimental study conducted abrasive wear tests by contacting Cu (MWCNT composite samples) on the abrasive sanding surface according to the specified test parameters. The schematic drawing of the lubrication mechanism expressing the self-lubricating property of carbon nanotubes (CNTs) during the abrasion test is shown in Figure 8.
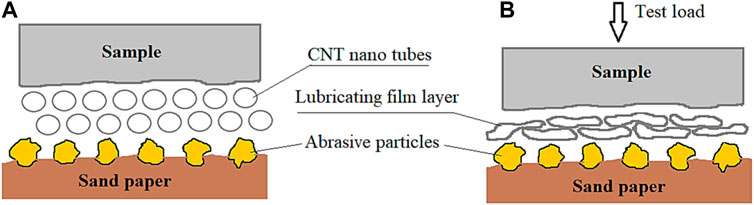
FIGURE 8. Symbolic representation of the dry lubrication mechanism; (A) Before the experiment, (B) During the experiment.
As shown in Figure 8, under the influence of the load and friction applied in the experiments, MWCNT particles form a lubricating film layer between the composite test sample and the abrasive sanding surface, reducing the friction coefficient and reducing wear losses. The amount of material loss in the composite structures and the amount of wear calculated according to Eq. 1 and the computed wear factors according to the abrasive wear tests performed by the pin-on-disc method on nanocomposite samples with pure Cu matrix and MWCNT reinforced at different ratios are given in Table 3. The graphs created according to Table 3 values are detailed in Figures 9, 10.
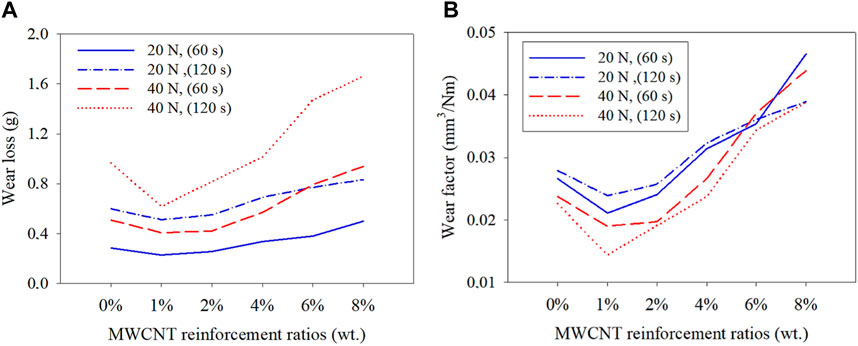
FIGURE 9. Cu/MWCNT composite (A) wear loss, (B) wear factor values according to applied load and wear time.
When the graphs in Figure 9 are analyzed together, it is understood that the lowest wear losses occurred in composites with 1% MWCNT reinforcement at both 20 N and 40 N test loads. Likewise, 2% MWCNT reinforced specimens also showed less wear loss than the reference material pure Cu. Although there was a twofold difference between the abrasion loads applied in the experiments, there was no twofold difference in abrasion losses between the experiments with 20 N and 40 N loads. As can be seen from Table 3, results that are not very proportional in wear values depending on the porosity and homogeneity of the composite structures were obtained. For example, in the 120 s wear test of the 1% MWCNT reinforced sample, although the test load increased by 100% (20 N and 40 N), there was an increase in wear loss of about 20%. In the 60s test with the same loads, the wear loss increase was 80%. If Table 3 continues to be analyzed, it is understood that the amount of wear loss increases approximately twice as much between 60 s and 120 s test times in experiments with 20 N load. However, in the experiments with a 40 N load, it is seen that the amount of wear loss is not doubled like the increase in the wear time, and there are fewer wear losses. With the increase in load in abrasive wear tests, the friction between the composite samples and the abrasive sandpaper is higher. Accordingly, the temperature increase occurs due to the heat generated on the composite sample contact surface. It is evaluated that the lubricating properties of MWCNT reinforcement particles increase with the composite structure softening with increasing temperature. MWCNT particles are more easily transported and spread on the Cu matrix surface, which softens with increasing temperature. Therefore, there was a decrease in wear loss in the wear tests performed at 40 N load and 120 s test duration. When the test results are analyzed in terms of wear factor, it is seen that the lowest wear factor value is obtained from the experiment performed under 40 N load for 120 s. This presentation was realized to be the opposite of the wear loss result. In other words, the lowest wear factor was obtained in the experiment where the highest wear loss occurred (Figure 9B). As the test load and duration increase, the temperature rises in the wear zone due to friction. The matrix metal copper inevitably softens when the temperature rises above a specific value. In this case, it is possible for some of the copper separated from the structure during abrasion to adhere or plaster to the surface again. Similar results were reported in a study on abrasive wear of metal matrix composite materials (Pul, 2022b). Another reason for the decrease in the wear factor is the emergence of the lubricating properties of the MWCNT particles agglomerated in the structure. In the same way, MWCNT, which is densely accumulated and agglomerated in some areas within the composite structure, can spread over the surface without moving away from the surface with increasing test load and duration. It is evaluated that the increased hotness in the wear zone can show the dry lubricant effect of MWCNT particles by spreading more easily on the surface. Therefore, for the above reasons, the wear factor values decrease with increasing load and test time. A study (Singh et al., 2006) reported that in abrasive wear tests, the wear mechanism varies according to the load and material loss is effective under small loads. At the same time, micro-wear is effective under heavier loads. In the same study, it was stated that there is a decrease in subsurface strain consolidation with increasing load amount.
Continuing to examine the wear losses, it is seen that the wear losses first decrease and then gradually increase due to the effect of MWCNT reinforcement material in the Cu matrix. Wear losses were less in composite samples with 1% and 2% MWCNT reinforcement than in pure copper’s reference material. With the increase in MWCNT content to 4%, the wear losses increased abruptly and gradually until the 8% MWCNT reinforced specimen. In a study in the literature, it is reported that under the same load, the coefficient of friction decreases with increasing CNT content. Still, the decrease in the coefficient of friction gradually loses its effect when the CNT content is above 2 wt%. This situation is explained by the self-lubricating effect of CNTs (Zhou Mingyang et al., 2017). Another study in the literature states that carbon-based nanomaterials, especially carbon nanotubes (CNTs) and graphene, play an important role in developing metal matrix nanocomposites. The addition of CNTs and graphene has been reported to improve the mechanical and tribological properties of metal matrix composites, reducing the coefficient of friction and wear rate while increasing the tensile strength. It has also been stated that adding these materials beyond a certain volume fraction can increase the coefficient of friction and wear rate and reduce mechanical properties (Dorri Moghadam et al., 2015).
The 1% MWCNT nanomaterial effect in the Cu matrix reduced wear losses by half. In the sample with 2% MWCNT reinforcement, wear losses decreased by approximately 57%. The self-lubricating or solid lubricant properties of carbon nanotube, a form of graphene, can explain this result. The literature shows that different studies report the lubricant properties of nanographene and carbon nanotubes in a metallic matrix (Tabandeh-Khorshid et al., 2016; Chen et al., 2019; Zheng et al., 2021a). However, the wear losses are not expected to increase significantly with the nano-reinforcement ratio of 4%. Here, a more important reason is the lubricating properties of MWCNT in the background. Reinforcement agglomeration, which occurs with the uneven reinforcement distribution in the composite structure, is the most important reason for this negative result. A similar study in the literature stated that the lubrication effect weakens when the CNT addition exceeds 2 wt%, which may be due to the accumulation of CNTs and high porosity (Zhou Mingyang et al., 2017). This is because the MWCMT nanoparticles, which come together and agglomerate densely, cause the formation of porous regions in the composite structure. These porous regions are present in Figure 2 in the microstructure evaluation section and in the SEM images in Figure 11, where the wear surfaces are visualized. Carbon elements, i.e., nano carbon reinforcement materials, are very intense in the EDS analyses of the porous regions with the SEM images. It is understood from the microstructure images that the reinforcement agglomeration and porosity increase with the increase in the MWCNT ratio in the Cu matrix structure.
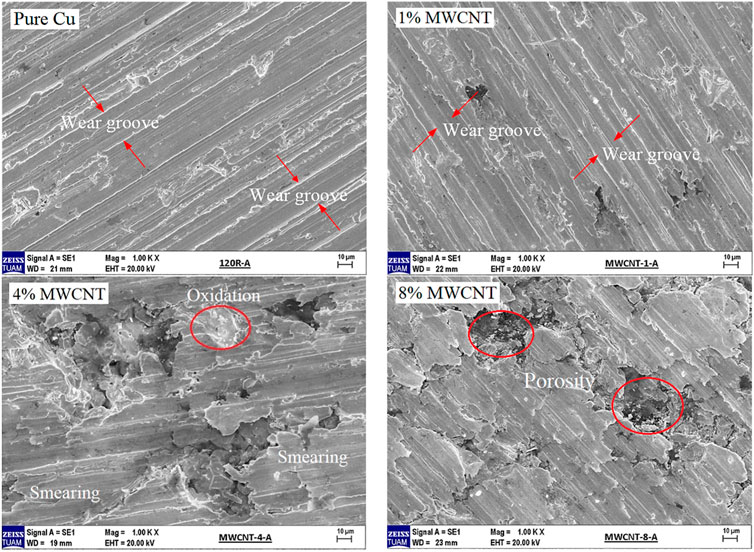
FIGURE 11. Abrasive wear test surface images of Cu/MWCNT composite structures at 40 N load and 120 s test duration.
During the abrasive wear tests, abrasive particles adhere more easily to the porous regions in the composite structure and remove more material from the surface of the composites. The cutting particles of the abrasive remove the MWCNT particles agglomerated in the dense porous regions from the composite structure by breaking them in masses before they can show their lubricating properties. In this case, the resulting porous structure repeats one after another and wear losses increase gradually. The most common structural problems in such nano-reinforced composite structures are inhomogeneous reinforcement distribution and agglomeration. The literature emphasizes that graphite and CNTs form agglomeration and reduce the strength of composites after a certain level. It is stated that it is challenging to distribute such nanomaterials evenly in large volumes (Khanna et al., 2021). This study evaluates that the best homogeneous reinforcement distribution is in the sample with 1% MWCNT reinforcement, followed by the sample with 2% reinforcement. It is understood that this homogeneous structure increases the lubricating properties of MWCNT. The nanomaterial homogeneously distributed in the composite form showed more effective dry lubrication properties. According to the composite production parameters applied in this study, the best result was obtained from a 1% MWCNT-reinforced composite sample. Testing lower MWCNT reinforcement ratios, such as 0.5% and 0.25%, may be recommended in a future study.
3.5 Wear surface morphology
SEM images were taken at different magnifications to examine the worn surfaces of Cu/MWCNT composite structures after abrasive wear tests. In addition, the situation of Cu and carbon-based MWCNT reinforcement materials in the composite structure was examined by performing an EDS analysis. For this purpose, the surface images of 1%, 4% and 8% MWCNT reinforced composites, which are the lowest, medium and highest ratios, taken at 1000X magnification after 40 N load and 120 s test time, are shown in Figure 11.
Looking at the eroded surface images in Figure 11, it is seen that with the increase in the MWCNT ratio, deep hollow and hollow regions are formed on the surfaces. The worn surface of the Cu matrix has the appearance of an exfoliated microstructure. The exfoliation behaviour on the worn surfaces was effective in increasing wear losses. The excessive deformation on the 4% and 8% MWCNT reinforced composite covers is especially remarkable. As mentioned before, the MWCNT particles agglomerated in the composite structure with increasing reinforcement rates, causing the formation of dense porous regions. Some oxidation wear occurred on the surfaces with an abrasive wear mechanism. In addition, it is understood from the SEM images that a large amount of matrix plastering has happened due to the effect of the adhesive wear mechanism. The plastering is more pronounced, especially in 4% and 8% MWCNT reinforced composite structures. The dense amount of MWCNT particles in the porous regions of these samples showed some lubrication effect by rubbing against the matrix surface while moving away from the composite structure. They helped the matrix material Cu to become lubricated and plastered. In addition, the temperature increase caused by friction during the wear tests also effectively softened and lubricated the already soft matrix material. In similar studies, it is stated that as a result of such wear tests, matrix material plastering occurs on the wear surfaces (Pul, 2018). Another study noted that CNTs exposed to the worn surface during the wear process act as a lubricating carbon film thanks to their low friction coefficients. The addition of CNTs into the structure is reported to increase wear resistance due to the strengthening and self-lubricating effects of CNTs (Hoon Nam et al., 2014).
As shown in eroded surface images in Figure 11, it is seen that with the increase in the MWCNT ratio, deep hollow and hollow regions are formed on the surfaces. The worn surface of the Cu matrix has the appearance of an exfoliated microstructure. The exfoliation behaviour on the worn surfaces was effective in increasing wear losses. The excessive deformation on the 4% and 8% MWCNT reinforced composite covers is especially remarkable. As mentioned before, the MWCNT particles agglomerated in the composite structure with increasing reinforcement rates, causing the formation of dense porous regions. Some oxidation wear occurred on the surfaces with an abrasive wear mechanism. In addition, it is understood from the SEM images that a large amount of matrix plastering has happened due to the effect of the adhesive wear mechanism. The plastering is more pronounced, especially in 4% and 8% MWCNT reinforced composite structures. The dense amount of MWCNT particles in the porous regions of these samples showed some lubrication effect by rubbing against the matrix surface while moving away from the composite structure. They helped the matrix material Cu to become lubricated and plastered. In addition, the temperature increase caused by friction during the wear tests also effectively softened and lubricated the already soft matrix material. In similar studies, it is stated that as a result of such wear tests, matrix material plastering occurs on the wear surfaces (Pul, 2018). Another study noted that CNTs exposed to the worn surface during the wear process act as a lubricating carbon film thanks to their low friction coefficients. The addition of CNTs into the structure is reported to increase wear resistance due to the strengthening and self-lubricating effects of CNTs (Hoon Nam et al., 2014).
During the wear tests, the sharp-edged SiC particles on the abrasive remove the agglomerated MWCNT particles in the porous regions from the structure. In this case, the lubricating effect of MWCNT particles is significantly reduced. In addition, during the experiments, the abrasive SiC particles adhere more strongly to the voids on the surface and remove more material from the surface. The images in Figure 11 shows that the primary wear mechanism occurring on the wear surfaces is plastic deformation caused by micro cutting, micro ploughing and micro scratching effects (Kök and Özdin, 2007).
However, in some studies in the literature, it is stated that the direct contact of the matrix material separated from the surface with the effect of carbon nano lubricant such as graphene in the structure is prevented to some extent, and this increases the wear resistance by reducing the ploughing effect and friction coefficient (Baradeswaran and Elayaperumal, 2011; Adeosun et al., 2014; Sharmaa et al., 2016; Velmurugan, 2017). It is seen that the abrasive particles create deep scratches with the ploughing effect. When the surface image of the 1% MWCNT reinforced composite with the lowest wear loss value is compared with the worn surface image of the pure Cu material, it is seen that the wear pits on the pristine Cu material surface are more comprehensive than the 1% MWCNT reinforced sample. Therefore, the 1% MWCNT reinforced sample exhibited the lowest wear loss value among all composite samples. This specimen manifested the self-lubricating or solid lubricating property of MWCNT nanomaterial. The lubricant film layer formed by MWCNT particles on the surface reduced the friction coefficient and effectively reduced wear losses (Pan et al., 2019). This lubricity continued even though it decreased to a 2% reinforcement ratio. However, as the reinforcement ratio increased above 2%, the dense porosity in the composite structure came into play, and the lubricating effect of MWCNT was significantly reduced and eliminated. To prove the elemental presence of MWCNT reinforcement material and matrix material Cu, concentrated in the porous region on the worn surface, EDS analysis performed on the worn surface of 1% MWCNT reinforced composite is given in Figure 12.
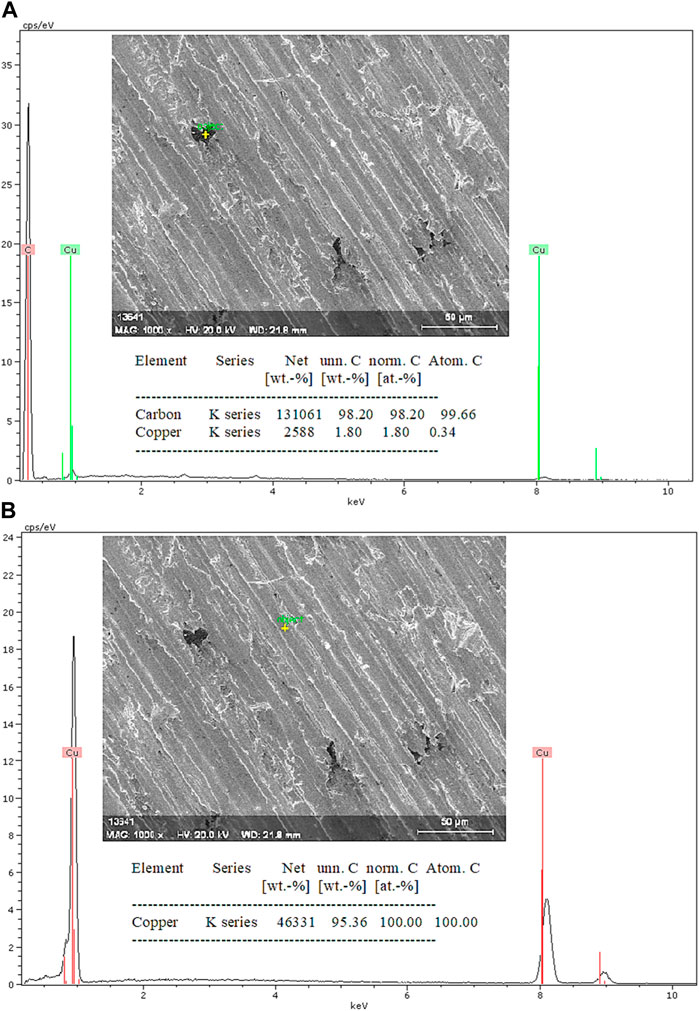
FIGURE 12. Worn surface EDS analysis of 1% MWCNT reinforced composite with Cu matrix; (A) MWCNT reinforcement, (B) Cu matrix.
To see the presence of MWCNT particles in these porous regions in the composite structure in much more detail, FE-SEM images taken at different magnifications are given in Figure 13 to complement each other.
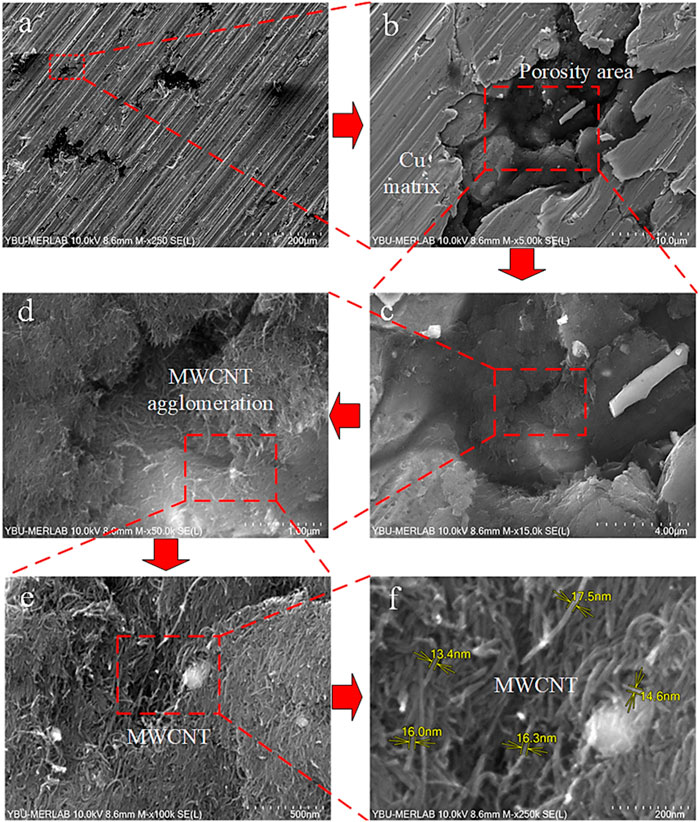
FIGURE 13. MWCNT reinforcement particles in Cu/MWCNT composite structure; (A) 250×, (B) 5.000×, (C) 15.000×, (D) 50.000×, (E) 100.000×, (F) 250.000×.
As shown in Figure 13, MWCNT particles are gathered and agglomerated as a ball. In this way, MWCNT reinforcement particles in large masses in the composite structure cause the formation of porous regions. Due to the friction, pressure and temperature during wear tests, the MWCNT masses in the form of lumps are dispersed and spread over the surface and have a lubricating effect. In the production process of such composite structures, it is essential to distribute the nano-sized reinforcement materials as homogeneously as possible within the main structure. In addition to the importance of the MWCNT ratio in the composite structure on the abrasive wear behaviour, the homogeneous distribution of these nanomaterials is considered the second important issue. Elemental Mapping SEM image and Energy Dispersive Spectroscopy (EDS) analysis taken from the worn surface of the 1% MWCNT reinforced composite is given in Figure 14 to continue to examine the worn surface morphology.
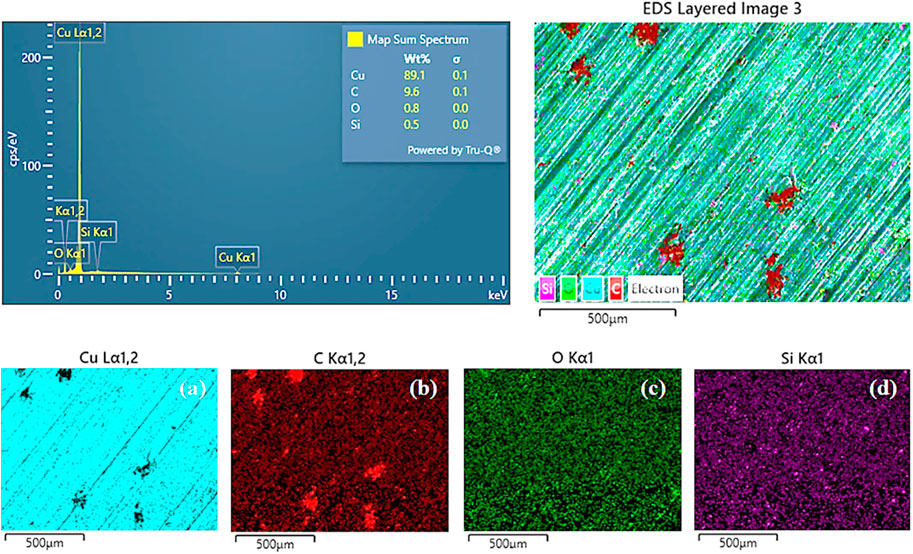
FIGURE 14. Worn surface EDS analysis and elemental distribution FE-SEM mapping images; (A) Copper, (B) Carbon, (C) Oxygen, (D) Silicon.
4 Conclusion
The results obtained from the experimental study are summarized below:
- Porous regions were formed with reinforcement agglomeration depending on the increase in MWCNT reinforcement in the composite structure.
- In the EDS, EDS and XRD analyses, partial oxidation of the Cu matrix material was detected. It took a lot of work to see the deficient concentration of MWCNT in XRD analysis. However, no phase-forming structures other than Cu and Oxygen elements were found due to the heat treatment.
- The presence of MWCNT in the composite samples decreased the density of the structure and increased the porosity. The hardness values decreased in direct proportion to the increase in the MWCNT ratio in the composite structure. Increasing porosity caused the hardness values to fall.
- The best homogeneous reinforcement distribution was observed in the 1% MWCNT reinforced sample, followed by the 2% reinforced sample. It was evaluated that there is a relationship between the lubricating properties of MWCNT in the composite structure and its homogeneous distribution.
- Compared to the pure copper reference specimen, the 1% and 2% MWCNT reinforced specimens showed lower wear losses. With a further increase in the MWCNT reinforcement ratio, the composite structure gradually deteriorated, and the lubricity of MWCNT particles decreased.
- According to the data obtained from abrasive wear tests, it was evaluated that the 1% MWCNT reinforcement rate had the highest dry lubrication effect.
- With increasing test load and time, the amount of wear did not grow at the same rate. The increased heat due to increasing load and time increased the temperature of the wear zone and facilitated the spreading of MWCNT particles on the surface. In this case, wear losses occurred at lower rates compared to the experiments performed at lower loads and times.
- In similar studies to see the dry lubricant effect of MWCNT on such composites, it was evaluated that going above 2% would not be effective, and lower MWCNT reinforcement ratios such as 0.25% and 0.5% may be more helpful.
Data availability statement
The original contributions presented in the study are included in the article/Supplementary material, further inquiries can be directed to the corresponding author.
Author contributions
MP: Conceptualization, Data curation, Funding acquisition, Project administration, Visualization, Writing–review and editing. RY: Data curation, Investigation, Methodology, Project administration, Resources, Software, Writing–original draft, Writing–review and editing. ME: Funding acquisition, Investigation, Methodology, Validation, Visualization, Writing–review and editing. GK: Methodology, Project administration, Software, Visualization, Writing–review and editing. DK: Data curation, Investigation, Project administration, Resources, Writing–review and editing. SS: Funding acquisition, Software, Supervision, Writing–review and editing. YZ: Investigation, Methodology, Project administration, Resources, Writing–review and editing. RC: Writing–review and editing. EA: Methodology, Project administration, Software, Visualization, Writing–review and editing.
Funding
The author(s) declare financial support was received for the research, authorship, and/or publication of this article. This experimental study was supported by the Kırıkkale University Scientific Research Projects Unit with project number 2022/104. The authors extend their appreciation to King Saud University for funding this work through Re-searchers Supporting Project number (RSP2024R164), King Saud University, Riyadh, Saudi Arabia.
Conflict of interest
The authors declare that the research was conducted in the absence of any commercial or financial relationships that could be construed as a potential conflict of interest.
Publisher’s note
All claims expressed in this article are solely those of the authors and do not necessarily represent those of their affiliated organizations, or those of the publisher, the editors and the reviewers. Any product that may be evaluated in this article, or claim that may be made by its manufacturer, is not guaranteed or endorsed by the publisher.
References
Adeosun, S. O., Osoba, L. O., and Taiwo, O. O. (2014). Characteristics of aluminum hybrid composites, world academy of science. Eng. Technol. Int. J. Mater. Metallurgical Eng. 8 (7), 731–738. doi:10.5281/zenodo.1097415
Akbarpour, M. R., Alipour, S., Farvizi, M., and Kim, H. S. (2019). Mechanical, tribological and electrical properties of Cu-CNT composites fabricated by flake powder metallurgy method. Archives Civ. And Mech. Eng. 19, 694–706. doi:10.1016/j.acme.2019.02.005
Baradeswaran, A., and Elayaperumal, A. (2011). Effect of graphite content on tribological behaviour of aluminium alloy - graphite composite. Eur. J. Sci. Res. 53 (2), 163–170.
Chen, X., Tao, J., Liu, Y., Bao, R., Li, F., Li, C., et al. (2019). Interface interaction and synergistic strengthening behavior in püre copper matrix composites reinforced with functionalized carbon nanotube-graphene hybrids. Carbon 146, 736–755. doi:10.1016/j.carbon.2019.02.048
Chika, O. U., Vandi Von Kallon, D., and Sunday Aigbodion, V. (2023). Tribological properties of CNTs-reinforced nano composite materials. Lubricants 11, 95. doi:10.3390/lubricants11030095
Dorri Moghadam, A., Omrani, E., PradeepMenezes, L., and Pradeep, K. (2015). Rohatgi Mechanical and tribological properties of self-lubricating metal matrix nanocomposites reinforced by carbon nanotubes (CNTs) and graphene e A review. Compos. Part B 77, 402e420. doi:10.1016/j.compositesb.2015.03.014
Duan, B., Zhou, Y., Wang, D., and Zhao, Y. (2019). Effect of CNTs content on the microstructures and properties of CNTs/Cu composite by microwave sintering. J. Alloys Compd. 771, 498–504. doi:10.1016/j.jallcom.2018.08.315
Garg, P., Gupta, P., Kumar, D., et al. (2016). Structural and mechanical properties of graphene rein-forced aluminum matrix composites, J. Mat. Environ. Sci. 7 (5), 1461–1473.
Hoon Nam, D., Hwang Kim, J., Cha, S., Jung, S., Kook Lee, J., Mo Par, H., et al. (2014). Hardness and wear resistance of carbon nanotube reinforced aluminum-copper matrix composites, J. Nanosci. Nanotechnol. 14 (12), 9134–9138. doi:10.1166/jnn.2014.10084
Jansson, N. (2021). Carbon nanostructures as lubricant additives, mechanisms, functionalization and future outlook, master’s thesis. Norwegian University of Science and Technology.
Khanna, V., Kumar, V., and Anil Bansal, S. (2021). Mechanical properties of aluminium-graphene/carbon nanotubes (CNTs) metal matrix composites: advancement, opportunities and perspective. Mater. Res. Bull. 138, 111224. doi:10.1016/j.materresbull.2021.111224
Kök, M., and Özdin, K. (2007). Wear resistance of aluminium alloy and its composites reinforced by Al2O3 particles. J. Mater. Process. Technol. 183, 301–309. doi:10.1016/j.jmatprotec.2006.10.021
Koltsova, T. S., Bobrynina, E. V., Larionova, T. V., and Tolochko, O. V. (2022). Structure and properties of copper-based composite with different types of carbon nanostructures. Diam. Relat. Mater. 124, 108933. doi:10.1016/j.diamond.2022.108933
Kumar, B., Manoj, K., and Majumder, K. (2015). Carbon nanotube based VLSI interconnects analysis and design. SpringerBriefs Appl. Sci. Technol. doi:10.1007/978-81-322-2047-3
Kumar, L., Nasimul Alam, S., Sahoo, S. K., and Teja, M. B. K. (2018). Mechanical properties of Cu-MWCNT composites developed by powder metallurgy route. Mater. Today Proc. 5, 19883–19892. doi:10.1016/j.matpr.2018.06.353
Singhal, S. K., Lal, M., Sharma, I., and Mathur, R. B. (2012). Fabrication of copper matrix composites reinforced with carbon nanotubes using a combination of molecular-level-mixing and high energy ball milling. J. Compos. Mater. 47 (5), 613–621. doi:10.1177/0021998312443397
Liu, L., Bao, R., Yi, J., Li, C., Tao, J., Liu, Y., et al. (2017). Well-dispersion of CNTs and enhanced mechanical properties in CNTs/Cu-Ti composites fabricated by Molecular Level Mixing. J. Alloys Compd. 726, 81–87. doi:10.1016/j.jallcom.2017.07.297
Long, F., Guo, X., Song, K., Liu, J., Wang, X., Yang, Y., et al. (2022). An internal-oxidation-based strategy induced high-density alumina in-situ nanoprecipitation and carbon nanotube interface optimization for co-reinforcing copper matrix composites. Compos. Part B Eng. 229, 109455. doi:10.1016/j.compositesb.2021.109455
Mohammed Ridha, H. (2022). Alhakeem, carbon nanotube (CNT) composites and its application. A Rev. Brillance 2 (3), 134–144. doi:10.47709/brilliance.v2i3.1692
Muhammet, E. T. (2019). Investigation of mechanical properties of carbonaceous (MWCNT, GNPs and C60) reinforced hot-extruded aluminum matrix composites. J. Alloys Compd. 788, 352e360. doi:10.1016/j.jallcom.2019.02.253
Muhammet, E. T., Aydin, F., Sun, Y., Zengin, H., and Akinay, Y. (2021). Wear resistance and tribological properties of GNPs and MWCNT reinforced AlSi18CuNiMg alloys produced by stir casting. Tribol. Int. 164, 107201. doi:10.1016/j.triboint.2021.107201
Pan, Y., Lu, X., AlexAVolinsky, B. W. L., Xiao, S.Q., Zhou, C., Yang, L., et al. (2019). Tribological and mechanical properties of copper matrix composites reinforced with carbon nanotube and alumina nanoparticles. Mat. Res. Express 6, 116524. doi:10.1088/2053-1591/ab4674
Pul, M. (2018). Effect of B4C reinforcement ratio and sintering temperature on the mechanical behavior in Al-B4C composites. Sci. Sinter. 50, 51–61. doi:10.2298/SOS1801051P
Pul, M. (2022a). The effect of carbon nanotube amount in machining of ZA-27 matrix carbon nanotube reinforced nano composite. Rev. Matéria 27 (2). doi:10.1590/S1517-707620220002.1326
Pul, M. (2022b). The effect of B4C and GNP reinforcement amounts on abrasive wear behavior in Al 6061/B4C/GNP hybrid composites. NOHU J. Eng. Sci. 11 (4), 1179–1187. doi:10.28948/ngmuh.1142512
Rais, L., and Sharma, R. (2015). The effect of homogeneous dispersion of carbon nano tubes on mechanical properties of aluminium-carbon nano tube nanocomposite-A review. Int. J. Electr. Electron. Engg. 2 (1).
Saboorı, A., Pavese, M., Badını, C., and Fıno, P. (2018). A novel approach to enhance the mechanical strength and electrical and thermal conductivity of Cu-gnp nanocomposites. Metallurgıcal And Materıals Transactıons A 49A, 333–345. doi:10.1007/s11661-017-4409-y
Sadoun, A. M., Abdallah, A. W., Najjar, I. M. R., Basha, M., and Elmahdy, M. (2021). Effect of lattice structure evolution and stacking fault energy on the properties of Cu–ZrO2/GNP nanocomposites. Ceram. Int. 47, 29598–29606. doi:10.1016/j.ceramint.2021.07.129
Şenel, M. C., Gürbüz, M., and Koç, E. (2017). The fabrication and characterization of graphene reinforced aluminum composites. Pamukkale Univ. J. Eng. Sci. 23 (8), 974–978. doi:10.5505/pajes.2017.65902
Sharma, A., Sharma, V. M. A., and Paul, J. (2019). A comparative study on microstructural evolution and surface properties of graphene/CNT reinforced Al6061−SiC hybrid surface composite fabricated via friction stir processing. Trans. Nonferrous Mater. Soc. China 29, 2005–2026. doi:10.1016/S1003-6326(19)65108-3
Sharmaa, P., Khanduja, D., and Sharma, S. (2016). Dry sliding wear investigation of Al6082/Gr metal matrix composites by response surface methodology. Jmaterres Technol. 5 (1), 29–36. doi:10.1016/j.jmrt.2015.05.001
Singh, K., Khanna, V., Singh, S., Anil Bansal, S., Chaudhary Ajit Khosla, V., et al. (2023). Paradigm of state-of-the-art CNT reinforced copper metal matrix composites: processing, characterizations, and applications. J. Mater. Res. Technol. 24, 8572–8605. doi:10.1016/j.jmrt.2023.05.083
Singh, M., Mondal, D. P., and Das, S. (2006). Abrasive wear response of aluminium alloy–sillimanite particle reinforced composite under low stress condition. Mat. Sci. Eng. 419, 59–68. doi:10.1016/j.msea.2005.11.056
Stalin, B., Ravichandran, M., Karthick, A., Meignanamoorthy, M., Sudha, G. T., and Karunakaran, S. (2021). Murugesan bharani, investigations on microstructure, mechanical, thermal, and tribological behavior of Cu-MWCNT composites processed by powder metallurgy. J. Nanomater. 15, Article ID 3913601. doi:10.1155/2021/3913601
Tabandeh-Khorshid, M., Omrani, E., Menezes, P. L., and Rohatgi, P. K. (2016). Tribological performance of self-lubricating aluminum matrix nanocomposites: role of graphene nanoplatelets. Eng. Sci. Technol. Int. J. 19, 463–469. doi:10.1016/j.jestch.2015.09.005
Tan, W., Jiang, X., Shao, Z., Sun, H., Fang, Y., and Shu, R. (2022). Fabrication and mechanical properties of nano-carbon reinforced laminated Cu matrix composites. Powder Technol. 395, 377–390. doi:10.1016/j.powtec.2021.09.072
Velmurugan, C. (2017). Experimental study on the wear characteristics of heat treated aluminium hybrid composites. Int. J. Civ. Eng. Technol. 8 (9), 191–200.
Wang, X., Tan, F., Qi, C., QiPearson, X. M., Li, M., Pan, H., et al. (2020). Comparative study of three carbon additives: carbon nanotubes, graphene, and fullerene-C60, for synthesizing enhanced polymer nanocomposites. Nanomaterials 10, 838. doi:10.3390/nano10050838
Wu, S., Tian, S., Menezes, P. L., and Xiong, G. (2020). Carbon solid lubricants: role of different dimensions. Int. J. Adv. Manuf. Technol. 107, 3875–3895. doi:10.1007/s00170-020-05297-8
WuHou, M. B., Shu, S., Ao, L., Geng, Qi., He, L., ShiYang, Y. M., et al. (2019). High oxidation resistance of CVD graphene-reinforced copper matrix composites. Nanomaterials 9, 498. doi:10.3390/nano9040498
Zhang, H., Liu, Y., Tao, J., Liu, Y., Bao, R., Li, F., et al. (2021). Direct synthesis of carbon nanotube-graphene hybrids on copper powders and the mechanical properties of corresponding composites. Mater. Sci. Eng. A 825, 141861. doi:10.1016/j.msea.2021.141861
Zhang, X., Shi, C., Liu, E., He, F., Ma, L., Li, Q., et al. (2017). In-situ space-confined synthesis of well-dispersed three-dimensional graphene/carbon nanotube hybrid reinforced copper nanocomposites with balanced strength and ductility. Compos. Part A 103, 178–187. doi:10.1016/j.compositesa.2017.09.010
Zheng, Z., Liu, J., Yang, C., Meng, Z., Yang, A., and Lou, D. D. (2021b). Fabrication of carbon nanotubes/Cu composites with orthotropic mechanical and tribological properties. Mater. Sci. Eng. A 804, 140788. doi:10.1016/j.msea.2021.140788
Zheng, Z., Liu, J., Tao, J., Jing, L., Zhang, W., Li, X., et al. (2021a). Effect of electroless coatings on the mechanical properties and wear behavior of oriented multiwall carbon nanotube-reinforced copper matrix composites. Nanomaterials 11, 2982. doi:10.3390/nano11112982
Zheng, Z., Yang, A., Tao, J., Jing, L., Zhang, W., Li, X., et al. (2022). Mechanical and conductive properties of CuMatrix composites reinforced by oriented carbon nanotubes with different coatings. Nanomaterials 12, 266. doi:10.3390/nano12020266
Zhou, M., Qu, X., Ren, L., Fan, L., Zhang, Y., Guo, Y., et al. (2017b). The effects of carbon nanotubes on the mechanical and wear properties of AZ31 alloy. Materials. 10, 1385. doi:10.3390/ma10121385
Zhou, M., Qu, X., Ren, L., Fan, L., Zhang, Y., Guo, Y., et al. (2017c). The effects of carbon nanotubes on the mechanical and wear properties of AZ31 alloy. Materials 10, 1385. doi:10.3390/ma10121385
Zhou, M., Qu, X., Ren, L., Fan, L., Zhang, Y., Guo, Y., et al. (2017a). The effects of carbon nanotubes on the mechanical and wear properties of AZ31 alloy. Materials 10 (1385), 1385–1417. doi:10.3390/ma10121385
Keywords: pure copper, MWCNT, nanocomposite, microstructure, abrasive wear, solid lubricant
Citation: Pul M, Yılmazel R, Erten MY, Küçüktürk G, Kaya D, Salunkhe S, Zümrüt Y, Cep R and Abouel Nasr ES (2024) Investigation of the effect of lubricant properties of carbon nanomaterial in Cu/MWCNT composites on wear. Front. Mater. 10:1337735. doi: 10.3389/fmats.2023.1337735
Received: 13 November 2023; Accepted: 26 December 2023;
Published: 18 January 2024.
Edited by:
Xiangkai Kong, China University of Mining and Technology, ChinaReviewed by:
Lin Wei, Lam Research, United StatesSusu Bao, Ningbo University, China
Li Qingsong, Xiamen University, Xiamen, China in collaboration with reviewer SB
Copyright © 2024 Pul, Yılmazel, Erten, Küçüktürk, Kaya, Salunkhe, Zümrüt, Cep and Abouel Nasr. This is an open-access article distributed under the terms of the Creative Commons Attribution License (CC BY). The use, distribution or reproduction in other forums is permitted, provided the original author(s) and the copyright owner(s) are credited and that the original publication in this journal is cited, in accordance with accepted academic practice. No use, distribution or reproduction is permitted which does not comply with these terms.
*Correspondence: Muharrem Pul, bXB1bEBra3UuZWR1LnRy