- 1Department of Civil Engineering, Lee Kong Chian Faculty of Engineering and Science, Universiti Tunku Abdul Rahman, Cheras, Malaysia
- 2Department of Mechanical and Material Engineering, Lee Kong Chian Faculty of Engineering and Science, Universiti Tunku Abdul Rahman, Cheras, Malaysia
- 3Department of Architecture and Sustainable Design, Lee Kong Chian Faculty of Engineering and Science, Universiti Tunku Abdul Rahman, Cheras, Malaysia
Concrete is one of the broadly used construction materials in the construction industry. This research intends to recommend the replacement of conventional coarse aggregates with recycled lightweight expanded clay aggregate (LECA) which offers several advantages such as lightweight, low cost, and easy availability. Lightweight concrete (LWC) offers numerous benefits; therefore, many researchers are using lightweight aggregate to produce lightweight structural composites concrete to compensate heavy loads by reducing the concrete self-weight due to lower density of lightweight concrete, improving in thermal properties and fire resistance, saving the cost of transportation and handling of precast units in the site. Different percentages (0, 0.15, 0.30, and 0.45%) of volume fraction of barchip polypropylene (BPP) fibre have been incorporated to improve the mechanical properties of lightweight aggregate concrete (LWA) concrete. In this study, the mixture of crushed lightweight expanded clay aggregate (CLECA) and barchip polypropylene (BPP) fibre have been used to achieve compressive strength between 28 and 37 MPa at 28-days with an oven-dry density ranged between 1900 and 2000 kg/m3. It is found that the inclusion of BPP fibres at an optimum volume fraction concrete enhances the compressive strength, splitting tensile strength and modulus of rupture. The compressive strength of the lightweight aggregate concrete containing 0.45% volume fraction of BPP fibre (CLLWAC-BPP0.45%) had achieved the highest compressive strength of 37 MPa at 28-days with a significant increment of about 31% compared to plain concrete. Hence, the findings of this research showed that the development of eco-friendly lightweight structural composites can be used as an alternative solution for conventional lightweight concrete, infrastructure and marine fields application.
1 Introduction
The advancements of technology and effectiveness in the concrete industry have contributed to fast growth for building materials. Consequently, the development and construction of these buildings and infrastructures demand an enormous amount of materials. Therefore, concrete is undoubtedly the most essential and economic construction material, and it is virtually irreplaceable (Flatt et al., 2012). Massive quantities of various types of lightweight concrete are sourced yearly which are lightweight aggregate concretes, fine aggregates concrete, and foamed concretes (Zhao et al., 2020; Hasan et al., 2021). Among several types of LWC, lightweight aggregate concrete (LWAC) is one of the most common techniques produce by researchers (Polat et al., 2010; Yew et al., 2021).
Nowadays, many researchers from different countries are promoting waste recycle to reduce the pollution rate of Earth such as excess use of non-renewable energy. The countries that are carrying out such actions are Austria which has the highest rate of recycling at 63% of all waste is diverted from landfills. Besides, our neighbour country, Singapore that sends almost 59% of its rubbish or waste to be reused, recycled and so on (General Kinematics Corporation, 2016). Furthermore, carrying out eco-friendly action in construction or marine fields such as using those recycled materials, using by-product aggregate and energy saving in the construction field is one of the basic strategies of sustainable development since it is relevant to environmental impact (Bogas et al., 2015). Consequently, preserve and conserve the availability of scarce raw resources and provide a recycling-friendly construction.
Among all types of concrete, lightweight concrete poses huge market value especially in tackling the optimum design as cost, time and quality are always the main concern in construction. It has been reported that over 10 billion tons of concrete containing sand fine aggregate, crushed granite coarse aggregate is produced every year globally (Kanojia and Jain, 2017). Therefore, the demand for lightweight concrete has been seen increasing progressively due to its emerging unique characteristic. Application of lightweight concrete as the structural members such as beam, column, and slab as the framework of a building structure can tremendously reduce dead loads, hence the overall cost of a project can be reduced. In the current research, non-experimental research has been made by incorporating barchip polypropylene fibre with the combination of crushed lightweight expanded clay aggregate (CLECA) technique to investigate its impacts on the mechanical properties of the lightweight concrete.
2 Materials and Methods
2.1 Materials
2.1.1 Ordinary Portland Cement
The Ordinary Portland Cement (OPC) Type 1 whose 28-days fc is 42.5 MPa. This ORANG KUAT OPC cement with density and fineness of 3,150 kg/m3 and 3,170 cm2/g, respectively. This product meets the Malaysian Standard MS 522: Part 1: 2003 and is certified by MS ISO 14001.
2.1.2 Water and Superplasticizer
Potable water from the local water supply network in the city of Kajang, Malaysia with pH value of 6 was used for both mixing and curing. The polycarboxylic ether (PCE) superplasticizer whose water reduction rate is 25% was added in all mixes to facilitate the workability.
2.1.3 Fine and Coarse Aggregate
River sand with a fineness modulus of 2.75 is used as fine aggregate. Sieve analysis is performed according to ASTM C 136-01 to obtain the grading of fine aggregate used in this study. The distribution of sand is obtained by performing sieve analysis, as shown in Table 1. All mix proportion has been mixed with river sand to improve the workability of lightweight concrete.
In this study, both crushed granite and crushed lightweight expanded clay aggregate (CLECA) was used as coarse aggregate, as shown in Figure 1. This recycled CLECA was collected from Therapeutic Garden Sanctuary in Selangor, Malaysia. The Company reported that more than 15 tonnes of CLECA were generated annually. According to Yew et al. (2021), the crushed dura oil palm shell (OPS) aggregates is able to provide significant improvement of the compressive strength as compared to without crushed aggregate. Furthermore, all these coarse aggregates are required to have sizeable to retain on 4.75 mm sieve.
2.1.4 Fibres
A barchip polypropylene (BPP) fibre is shown in Figure 2 and its physical properties are listed in Table 2.
2.2 Mix Proportions
The mix proportions of all the CLECA lightweight aggregate concrete (LWAC) mixes with different percentages of fibre volume fractions (0, 0.15, 0.3 and 0.45%) was used in this study are illustrated in Table 3. It is noted that a high-volume fraction (Vf) tends to “clog” in the mix and create workability problems (Kosmatka et al., 2002). Thus, low Vf (<0.5%) of the barchip polypropylene (BPP) was used in this experiment.
2.3 Testing Methods
Slump test was carried out in accordance with BS EN: 12350 - Part 2: 2009 to determine the workability of crushed LECA lightweight aggregate fibre-reinforced concrete (CLLWAFRC) with different volume fraction (0, 0.15, 0.3, and 0.45%). Oil was applied on all the surfaces of the moulds before casting. The moulds filled with slumps were vibrated on a shaking table to ensure the uniformity of the mix. The concrete samples were demoulded after 24 +/− 4 h from placing. All the demoulded samples were fully immersed in water at room temperature in a curing tank until they reached the desired testing age.
The 3,000 kN capacity compression test machine was manufactured by Unit Test Scientific Sdn. Bhd. It was set to a constant loading rate of 3.0 kN/s in compliance with BS EN 12390—Part 3 (2009). The same machine was used for the splitting tension test with the loading rate set to 1.5 kN/s in accordance with BS EN 12390—Part 6 (2009). For each mixture sample, cubes with dimensions of 100 mm × 100 mm × 100 mm were cast to test for compressive strength at 7 and 28 days. The splitting tensile strength of mixture samples at 7 and 28 days was examined by cast them into cylinders with a diameter of 100 mm and length of 200 mm. In addition, three prisms (length: 500 mm, width: 100 mm, depth: 100 mm), are used to determine the behaviour of flexural strengths on the 7 and 28 days.
3 Results and Discussion
3.1 Properties of Fresh Concrete (Workability)
The workability of CLLWAC with different percentages of barchip polypropylene (BPP) fibre is represented by the normal slump value, as indicated in Figure 3.
The addition of PP fibre in CLLWAC has a negative effect on workability. Slump values are reduced remarkably with the increase of BPP fibre %. The slump is declined gradually by 4.6, 13.6 and 27.3% at 0.15, 0.30 and 0.45% inclusion of BPP fibre respectively. Similarly, in order to maintain certain workability, more water is required for lubrication in the case of higher fibre %. Superplasticizer can also be used to compensate for the negative effect of fibre on workability.
Addition of fibre decreases the workability of concrete in a way which bridge and hold the cement matrix, forming a network structure in concrete. This structure hence promotes cohesion and adhesion among the matrices. As the fibre content getting higher, the surface area to cement paste increases, contributing to larger internal friction and work done requirements. Consequently, the viscosity of the mixture increases, and the slump flow is hindered. According to Yew et al., 2015, the inclusion of fibres is well known to affect the workability and flowability of plain concrete intrinsically. However, CLLWAC inclusion of BPP fibre from 0 to 0.45% had achieved high workability with the slump value between 140 and 200 mm.
3.2 Density
Demoulded density (DD) and oven-dried density (ODD) were measured for all mixes as shown in Table 4. DD is calculated with the weight of the specimens measured after demoulding; while ODD is calculated with the weight of the specimens measured after being oven-dried for 24 h. All specimens in this study were attributed with DD and ODD in the range of 1965–1995 kg/m3 and 1908–1984 kg/m3, respectively. The outcome fulfilled the objective of obtaining OPSLWC with ODD lesser than 2000 kg/m3. The samples also met the requirement for structural application as structural lightweight concrete (SLWC), defined as concrete with ODD of not greater than 2000 kg/m3 (Newman and Owens, 2003).
underIn general, all densities are observed to have a slight increment as the addition of BPP fibre volume fraction increased. This could be due to the packing density theory, where BPP fibre holds the cement matrix close to one another, causing a packing effect. Therefore, the addition of the fibre material occupied within a unit volume thus increases overall density. In general, density increases as the inclusion of fibre increases. From the previous study, Bagherzadeh et al. (2012) reported a similar outcome.
3.3 Compressive Strength
3.3.1 Continuous Moist Curing
The compressive strength of each mix at 1, 7 and 28 days, as shown in Table 5. The 28-days compressive strength of all mixes was in the range of 28–37 MPa, which met the requirement for structural lightweight concrete (SLWC) (Yew et al., 2020). The inclusion of BPP fibres enhanced the compressive strength by 5.7–27.6% at 7 days and 2.5%–31.0% at 28 days. This phenomenon could be due to the fibre bridging effect of the BPP fibres. From the aspect of geometry, BPP fibre is stiffer and more effective in arresting major cracks. The linking bridge between fibres and cement matrices can prevent the spalling caused by the lateral tension induced by the compressive loading (Yap et al., 2017 and Shafigh et al., 2011). This process is ascribed to the ability of the BPP fibre to arrest cracks or the bridging effect in concrete (Yew et al., 2021). Figure 4 illustrates the failure type of 100 mm cube specimens of plain concrete and CLLWAC-BPP0.45% respectively.
3.4.Splitting Tensile Strength
Figure 5 presents the splitting tensile strength of CLLWAC with different volume fraction percentages of BPP fibre addition at a curing age of 7 and 28 days.
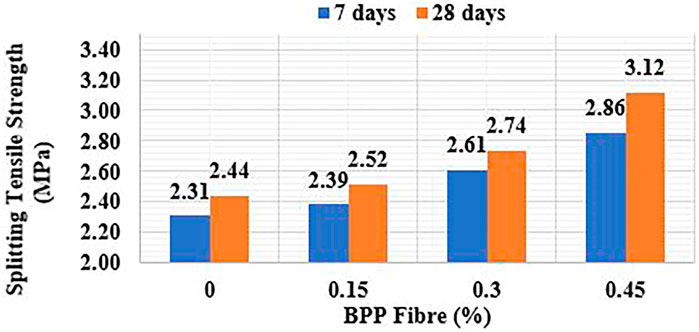
FIGURE 5. Splitting tensile strength of CLLWAC with different volume fraction percentage of BPP fibre at 7 and 28 days.
underThe trend of splitting tensile strength enhancement is clear which presents an increase of strength throughout the increase of BPP fibre percentage, as shown in Figure 5. The splitting tensile strength grows exponentially with the fibre percentage until a peak of 2.86 MPa at 7 days curing age and 3.12 MPa at 28 days curing age. The splitting tensile strength develops slower than compressive strength throughout the curing period. The percentage enhancements are 5.69, 5.63, 4.93 and 9.25% with fibre percentage of 0, 0.15, 0.30, and 0.45% respectively.
The addition of BPP fibre significantly influences the mode and mechanism of rupture of the concrete cylinder. This phenomenon might be attributed to arresting of cracks by BPP fibres, therefore, concrete can be subjected to very large deformations before the total uncontrollable collapse. It can be observed that CLLWAC without fibre reinforcement tends to rupture in a way that split directly into half at failure whilst fibre reinforced CLLWAC only cracked along the longitudinal of the concrete cylinder. It can be noticed that CLLWAC-BPP0.45% is prone to fail in a more ductile mode. This is particularly correct where fibre prolongs concrete’s ability to sustain the load and withstand large deformation without fracturing into pieces. Similar behaviour has been reported for PP and PVC fibre OPS lightweight concrete (Yew et al., 2015; Yew et al., 2016; Loh et al., 2021). The failure pattern of CLLWAC-BPP0% and CLLWAC-BPP0.45%, as shown in Figure 6.
3.5 Modulus of Rupture
According to the study, all specimens are loaded at two points until rupture. Figure 7 records the MOR results of CLLWAC with various volume fractions of BPP fibre at 7 and 28 days curing age.
Based on Figure 7, it can be declared that the MOR increases proportionally to the increment of volume fraction of SPP fibre. The MOR ranged from a minimum of 2.53 MPa to a maximum of 3.53 MPa at 7 days and 2.70 MPa–3.91 MPa at 28 days. The MOR developments as a percentage of CLLWAC-BPP0% are 39.40% at 7 days and 45.01% at 28 days. Therefore, CLLWAC-BPP0.45% had shown the highest MOR similar in the case of compressive strength and splitting tensile strength. Figure 7 distinguish the fracture mode of plain CLLWAC with fibre reinforced CLLWAC. Several views were captured to study their variations in cracking patterns under flexural failure.
Comparing Figure 8, the main difference noticeable was the way the crack propagated through the 100 mm × 100 mm × 500 mm prism under bending. When concrete is subjected to bending, the tensile behaviour is prone to govern its strength as the concrete is brittle and weak in tension. From Figure 8, it can be observed that the presence of fibre inhibits the propagation of crack (bottom). However, crack propagates rapidly parallel to the load applied, splitting the prism into pieces in the case without fibre. Sudden failure usually occurred in the case of lightweight aggregate concrete with lower tensile strength especially when subjected to bending.
The presence of fibres in concrete integrates the cement matrices to minimize the propagation of cracks. As load is applied gradually, the development of cracks initiates, the fibres accommodated the crack faces and control the crack widths or openings. Fibres provide a bridging effect by displacing the minor cracks with the formation of a linking bridge to hold the openings. The stretching of fibres allows stress distribution and promotes an additional energy-absorbing mechanism. These mechanisms delay the failure, at the same time allow greater deformation. Thus, it can be deduced that improvement in the tensile strength of concrete.
Other than the volume fraction, geometry and aspect ratio, the distribution and orientation of fibre in cement matrices also influenced the tensile strength of concrete. The dispersion state of fibre is random due to the influence of aggregates and fibre gravity itself, yet homogenous distribution usually can be ensured at the higher fibre content. Orientation of fibre perpendicular to the load applied resulted in higher tensile strength. Otherwise, paralleled fibres reduce tensile strength because the parallel arrangement increased the weak interfacial transition zone between fibres and cement paste (Jin, 2016).
4 Conclusion
Based on the experimental results of this study, the inclusion of BPP fibre in CLLWAC possessed a positive effect on the mechanical properties. It helps in arresting the propagation of cracks by introducing a bridging effect, enable stress transfer, promote additional energy-absorbing mechanisms, and hence allow larger deformation. Therefore, the following conclusions can be drawn:
1) The inclusion of barchip polypropylene (BPP) fibre has a marginal effect on density. There is a slight increment in density as the BPP fibre percentage increases.
2) The inclusion of BPP fibre in CLLWAC had reduced the workability, where the rate of slump drop accelerated as the fibre content increased.
3) The inclusion of BPP fibre in CLLWAC possessed a positive effect on the mechanical properties. It helps in arresting the propagation of cracks by introducing a bridging effect, enable stress transfer, promote additional energy-absorbing mechanisms, and hence allow larger deformation.
4) Development of splitting tensile strength accelerated as the volume fraction of BPP fibre in CLLWAC increased. The splitting tensile strength escalated an exponential rate, which achieved 2.86 and 3.16 MPa respectively at 7 and 28 days for 0.45% BPP fibre.
5) The higher the BPP fibre percentage in CLLWAC, the higher the MOR. At maximum BPP fibre content of 0.45%, the incremental of MOR at 7 and 28 days is as high as 39.4 and 45.0% respectively.
Data Availability Statement
The raw data supporting the conclusion of this article will be made available by the authors, without undue reservation.
Author Contributions
“Conceptualization, MKY and MCY; methodology, YL and FL; software, JB and SH; validation, JB,MKY, MCY, and YL; formal analysis, SH and FL; investigation, MKY and JB; resources, MKY and MCY; data curation, MKY; writing—original draft preparation, MKY and MCY; writing—review and editing, MKY, MCY, and JB; visualization, FL, YL, and SH; supervision, MKY and MCY; project administration, MKY and MCY; funding acquisition, MKY All authors have read and agreed to the published ver-sion of the manuscript.
Conflict of Interest
The authors declare that the research was conducted in the absence of any commercial or financial relationships that could be construed as a potential conflict of interest.
Publisher’s Note
All claims expressed in this article are solely those of the authors and do not necessarily represent those of their affiliated organizations, or those of the publisher, the editors and the reviewers. Any product that may be evaluated in this article, or claim that may be made by its manufacturer, is not guaranteed or endorsed by the publisher.
Acknowledgments
The authors gratefully acknowledge the financial support from Universiti Tunku Abdul Rahman under the Universiti Tunku Abdul Rahman Research Fund (UTARRF).
References
Bagherzadeh, R., Pakravan, H. R., Sadeghi, A. H., Latifi, M., and Merati, A. A. (2012). An investigation on adding polypropylene fibers to reinforce lightweight cement composites (LWC). J. Engineered Fibers Fabrics 7 (4), 13–21. doi:10.1177/155892501200700410
Bogas, J. A., de Brito, J., and Figueiredo, J. M. (2015). Mechanical characterization of concrete produced with recycled lightweight expanded clay aggregate concrete. J. Clean. Prod. 89, 187–195. doi:10.1016/j.jclepro.2014.11.015
BS EN 12390 (2009). Part 3 testing hardened concrete – compressive strength of test specimens. UK: British Standard Institution.
Flatt, R. J., Roussel, N., and Cheeseman, C. R. (2012). Concrete: An eco material that needs to be improved. J. Eur. Ceram. Soc. 32 (11), 2787–2798. doi:10.1016/j.jeurceramsoc.2011.11.012
General Kinematics Corporation (2016). Top 10 Recycling Countries From Around the World. [online] Available at: https://www.generalkinematics.com/blog/top-10-recycling-countries-around-world/ (Accessed May 3, 2018).
Hasan, M., Saidi, T., and Afifuddin, M. (2021). Mechanical properties and absorption of lightweight concrete using lightweight aggregate from diatomaceous earth. Construction Building Mater. 277, 122324. doi:10.1016/j.conbuildmat.2021.122324
Jin, B. (2016). Investigation on mechanical properties and microstructure of high performance polypropylene fiber reinforced lightweight aggregate concrete. Construction Building Mater. 118, 27–35.
Kanojia, A., and Jain, S. K. (2017). Performance of coconut shell as coarse aggregate in concrete. Construction Building Mater. 140, 150–156. doi:10.1016/j.conbuildmat.2017.02.066
Kosmatka, S. H., Kerkhoff, B., and Panarese, W. C. (2002). Design and control of concrete mixtures. 14th ed. USA: Portland Cem Assoti.
Loh, L. T., Yew, M. K., Yew, M. C., Beh, J. H., Lee, F. W., Lim, S. K., et al. (2021). Mechanical and thermal properties of synthetic polypropylene fiber-reinforced renewable oil palm shell lightweight concrete. Materials 14 (9), 2337. doi:10.3390/ma14092337
Newman, J., and Owens, P. (2003). “Properties of Lightweight Concrete,” in Advanced Concrete Technology. Processes. Editors J. Newman, and B. Choo (Oxford: Butterworth - Heinemann), 3–29. doi:10.1016/b978-075065686-3/50288-3
Polat, R., Demirboğa, R., Karakoç, M. B., and Türkmen, İ. (2010). The influence of lightweight aggregate on the physico-mechanical properties of concrete exposed to freeze-thaw cycles. Cold Regions Sci. Tech. 60, 51–56. doi:10.1016/j.coldregions.2009.08.010
Shafigh, P., Mahmud, H., and Jumaat, M. Z. (2011). Effect of steel fiber on the mechanical properties of oil palm shell lightweight concrete. Mater. Des. 32, 3926–3932. doi:10.1016/j.matdes.2011.02.055
Yap, S. P., Alengaram, U. J., Mo, K. H., and Jumaat, M. Z. (2017). Ductility behaviours of oil palm shell steel fibre-reinforced concrete beams under flexural loading. Eur. J. Environ. Civil Eng., 1–13. doi:10.1080/19648189.2017.1320234
Yew, M. K., Bin Mahmud, H., Ang, B. C., and Yew, M. C. (2015). Effects of low volume fraction of polyvinyl alcohol fibers on the mechanical properties of oil palm shell lightweight concrete. Adv. Mater. Sci. Eng. 2015, 1–11. doi:10.1155/2015/425236
Yew, M. K., Bin Mahmud, H., Ang, B. C., and Yew, M. C. (2015). Effects of low volume fraction of polyvinyl alcohol fibers on the mechanical properties of oil palm shell lightweight concrete. Adv. Mater. Sci. Eng. 2015, 1–11. doi:10.1155/2015/425236
Yew, M. K., Mahmud, H. B., Shafigh, P., Ang, B. C., and Yew, M. C. (2016). Effects of polypropylene twisted bundle fibers on the mechanical properties of high-strength oil palm shell lightweight concrete. Mater. Struct. 49 (4), 1221–1233. doi:10.1617/s11527-015-0572-z
Yew, M. K., Yew, M. C., Beh, J. H., Saw, L. H., Lee, F. W., and Ng, T. C. (2020). Influence of high-performance polypropylene fibre and heat-treated dura oil palm shell on durability properties of lightweight concrete. Eur. J. Environ. Civil Eng., 1–20. doi:10.1080/19648189.2018.1509022
Yew, M. K., Yew, M. C., Beh, J. H., Saw, L. H., and Lim, S. K. (2021). Effects of pre-treated on dura shell and tenera shell for high strength lightweight concrete. J. Building Eng. 42, 102493. doi:10.1016/j.jobe.2021.102493
Keywords: lightweight concrete, polypropylene fibre, lightweight expanded clay aggregate, mechanical properties, density, recycled, eco-friendly
Citation: Yew MK, Yew MC, Han Beh J, Saw LH, Lee FW and Lee YL (2021) Mechanical Properties of Barchip Polypropylene Fibre-reinforced Lightweight Concrete Made With Recycled Crushed Lightweight Expanded Clay Aggregate. Front. Mater. 8:753619. doi: 10.3389/fmats.2021.753619
Received: 05 August 2021; Accepted: 16 September 2021;
Published: 25 October 2021.
Edited by:
Nicholas Fantuzzi, University of Bologna, ItalyReviewed by:
Piotr Smarzewski, Lublin University of Technology, PolandSanjay Mavinkere Rangappa, King Mongkut’s University of Technology North Bangkok, Thailand
Copyright © 2021 Yew, Yew, Han Beh, Saw, Lee and Lee. This is an open-access article distributed under the terms of the Creative Commons Attribution License (CC BY). The use, distribution or reproduction in other forums is permitted, provided the original author(s) and the copyright owner(s) are credited and that the original publication in this journal is cited, in accordance with accepted academic practice. No use, distribution or reproduction is permitted which does not comply with these terms.
*Correspondence: Ming Kun Yew, eWV3bWtAdXRhci5lZHUubXk=