- 1Faculty of Civil Engineering and Mechanics, Jiangsu University, Zhenjiang, China
- 2College of Mechanical Engineering, Yangzhou University, Yangzhou, China
The present article investigates the microstructure and mechanical properties of A356 matrix composite reinforced with TiB2 particles synthesized by the salt metal reaction of as-cast and T6 state. Microscopic observations of the prepared composites reveal that in-situ grown TiB2 particles are characterized with regular shapes and nearly uniform distributed in the A356 matrix. A clear interface between the A356 matrix and TiB2 particles was observed. The detailed analysis of mechanical properties of synthesized composites of as-cast and T6 state show that the ultimate tensile strength and Young’s modulus of the synthesized composites increased with the increasing weight percentage (wt%) of in-situ TiB2 particles in the A356 matrix, but the Poisson’s ratio of the synthesized composites decreased with the increase of TiB2 particles wt%. The Young’s modulus of the composites increased by up to 10.8% and the Poisson’s ratio decreased by up to 3.2% with the increase of TiB2 particles wt%, compared to A356 alloy. With the increase of TiB2 particle wt%, the yield strength of the composites decreased at first (when the TiB2 particle wt% is less than 1%) then increased, while elongation and percent reduction in area increased at first and then decreased. Furthermore, T6 heat treatment can refine grain and effectively improve the mechanical properties of composites.
Introduction
In-situ aluminum composites, which possess the advantages of small reinforcements and strong particle-matrix bonding, are studied as one of the most promising alternatives for effectively eliminating the inherent defects of ex-situ particulate composites (Qian et al., 2020; Raveendran et al., 2020; Pariyar et al., 2021; Zhao et al., 2021). Previous studies have also shown that in-situ particles can significantly enhance the mechanical properties of composites for refining the size of grain in the matrix (Afkham et al., 2018; Guan et al., 2021). In addition, Rahoma et al. (2015) studied the effect of heat treatment on the microstructure and mechanical properties of in-situ matrix composites and found that the ductility of matrix composites could be enhanced by increasing the aging temperatures. Kai et al. (2021) studied the effects of Zr on the microstructure and mechanical properties of B4C/Al composites and pointed out that the addition of Zr could promote the wettability of the composite as well as the uniform distribution of the particles. To improve the dispersity of in situ particles in the matrix effectively, some external physical fields, such as electromagnetic and ultrasonic fields, were used during the preparation of the in-situ particle reinforced aluminum composites (Kai et al., 2016; Kai et al., 2019).
Al–Si based cast alloy composites (such as A356) have been widely used in automobile, aerospace, and electronics industries because of their high strength ratio and modulus ratio and better resistance to wear and corrosion (Jelinek et al., 2012; Kim et al., 2021). In order to improve the integrated properties of hypereutectic Al−Si alloys, many processing technologies have been studied to obtain superior mechanical properties. One of them is to synthesize ceramics with particle-reinforced aluminum alloy matrices by in-situ reactions (Tao et al., 2018; Logesh et al., 2020; Zhang et al., 2020). Among various reinforced particles, TiB2 particles are one of the promising candidates because of their high hardness, high modulus, and exceptional erosion resistance (Chen et al., 2009a; Liang et al., 2019; Fattahi et al., 2020; Senthil Kumar et al., 2020). The mechanical properties and strengthening mechanisms of TiB2/A356 composites have been studied by many researchers, and their reports indicate significant improvements in tensile properties (Chen et al., 2009b; Wang et al., 2014; Xue et al., 2020). Mandal et al. (2008) investigated the aging response of the alloy when dispersed with TiB2 particles and observed that different amounts of TiB2 alter the particle size distribution of Si, which affects the mechanical properties. Karbalaei Akbari et al. (2015) indicated that the tensile properties of nanocomposites were evidently different from the enhancement of microparticles. Zulkamal et al. (2018) reported that the addition of TiB2 particles refined the microstructure of the material and improved the wear resistance of the semi-solid A356 alloy. Deepak et al. (2019) have conducted low cycle fatigue tests on in-situ TiB2/A356 composites and found that TiB2 particles had a significant impact on the structure, hardness, tensile strength, and fatigue life of the composites.
Our review of the literature indicates that limited information is available on the integrated mechanical properties of A356 matrix composite reinforced with in-situ grown TiB2 particles. Although some research works exist on the yield strength, ultimate tensile strength, and wear of composites, reports on the Poisson’s ratio of TiB2/A356 in-situ composites are still lacking. Therefore, in this work, the A356 matrix composites reinforced with in-situ grown TiB2 particles were synthesized by salt–metal reaction. An attempt is to study the microstructure and mechanical properties of composites of as-cast and T6 state as detailed as possible.
Materials and Methods
Materials
The raw materials that were used in the present work are commercial A356 alloy, inorganic salt KBF4 (KBF4 ≥ 99.80%, Fe2O3 ≤ 0.05, H2O ≤ 0.15) and K2TiF6 (K2TiF6 ≥ 99.80%, Fe2O3 ≤ 0.05, H2O ≤ 0.15) powders. The chemical composition of A356 alloy is shown in Table 1. In-situ endogenous TiB2 particles were synthesized as reinforcing phase, and physical properties were shown in Table 2. The formation of the TiB2 particles in the inorganic salt melt is given by the following chemical reactions (Bartels et al., 1997):
Processing of TiB2/A356 In-Situ Composites
The TiB2/A356 in-situ composites were prepared by the inorganic salt metal reaction technique. The required KBF4 and K2TiF6 halide salt was strictly mixed uniform in a grinding bowl according to the mass ratio Ti: B = 1:2, and was preheated to 300°C for 3 h in an electric furnace to remove moisture content. The A356 alloy and pure aluminum were heated to 800°C in a graphite crucible inside an electric furnace under nitrogen gas protection and stirred mechanically with a speed of 500 r/min. The ready-mixed KBF4 and K2TiF6 powders were added and pressed into the melt and underwent a chemical reaction with the melt to synthesize TiB2 particles. In the reaction process, the melt was still stirred for 10 min to distribute the TiB2 particles. After a reaction time of half an hour, the composites melt was degassed, dross-decanted and refined, and then set for 10 min at 720°C. Finally, the composites melt was poured into a preheated copper mold, and cooled at room temperature to obtain the as-cast composites.
Each prepared TiB2/A356 in-situ composite ingot (wt% of TiB2 particles are 0%, 1%, 3%, and 5% respectively) was sectioned into two parts. One part was conducted T6 heat treatment with following steps: the composites ingot were first heated to 550°C and solution treatment for 12 h, then water quenching, finally aging treatment for 2 h at 120°C and aging treatment for 8 h at 150°C. Some composites feedstock of as-cast and T6 state were machined into the testing specimens with dimensions 10 mm × 10 mm × 10 mm. The testing surface of the specimen was carefully polished until the surface was clear and clean.
Microstructural Characterizations
The microstructures of the A356 alloy and TiB2/A356 in-situ composites were characterized using an optical microscope and scanning electron microscope (JSM-7001F) with energy dispersive X-ray (EDX). Figure 1 shows optical micrographs of the A356 alloy and 3wt% TiB2 composites of as-cast. From Figure 1A, it can be seen that the microstructures of as-cast A356 alloy show a dendritic structure. But the addition of TiB2 particles refines the structure of the dendrites as shown in Figure 1B. And it is also found that the TiB2 particles decrease the size of needles Si to finer size in composites compared with that of A356 alloy. This suggests that TiB2 particles have the effect of refining grain, as reported in earlier papers (Wang et al., 2014; Liang et al., 2019).
Further, SEM photomicrographs were taken to analyze the effect of TiB2 particles in the matrix after T6 heat treatment. Figure 2 shows SEM photos of the prepared composite of as-cast and T6 state, respectively. The microstructure of composites in Figure 2B shows that the dendritic eutectic Si grains were broken and spheroidised after T6 heat treatment. TiB2 particles are distributed on the boundaries of grains which may refine the eutectic silicon and cause an increase in mechanical properties of composites compared with those of the matrix.
The composition of the prepared composites was identified using energy dispersion spectrum (EDS) analysis. Figure 3 shows the SEM micrograph and EDS of the A356–1wt% TiB2 composites. As shown in Figure 3B, the EDS peaks for TiB2 particles include compositional information of Ti and B except the Al matrix around the particles. And Ti and B peaks correspond to the composition of TiB2 particles. This suggests that the TiB2 particles were successfully synthesized in composite by in-situ salt metal reactions.
Figure 3A SEM micrograph reveals the size and distribution of in-situ grown TiB2 particles inside the composites of as-cast. It is observed that most of the in-situ grown TiB2 particles have a size of about 50–300 nm and are distributed nearly uniformly in the matrix. This contributes to the better mechanical properties of the composites. The SEM images of TiB2 particles at higher magnification are shown in Figure 4, and it is evident that in-situ grown TiB2 particles present regular shapes such as ellipsoids, quadrangles, and pentagons. In addition, the clean interface between the TiB2 particles and A356 alloy can be observed. which is needed to enhance the mechanical properties and increase the load carrying capability of composites.
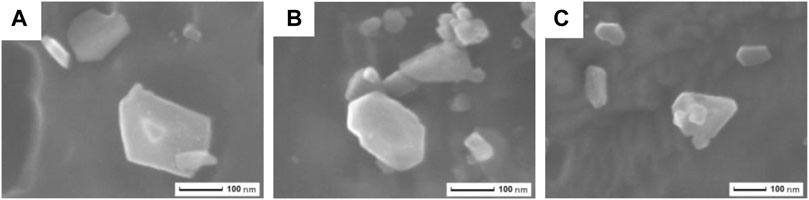
FIGURE 4. SEM images of TiB2 particles at higher magnification (A) region 1 (B) region 2 (C) region 3.
Tensile Testing
Equipment and Specimen
The type of specimen used in the tensile test is shown in Figure 5. The cross-sectional area of the flat tensile specimen has been accurately determined as 10 mm × 2.5 mm and the length between two gage marks on the specimen is a distance L0 = 57 mm. The tensile tests were conducted using a universal testing machine at room temperature. Before the formal test, each specimen is preloaded to 30 MPa (elastic limit is more than 40 MPa) and unloaded. Then the formal tensile test was conducted with loading speed controlled by displacement of 0.1 mm/min in the elastic stage. This kind of test was repeated at least three times on average to determine the Young’s modulus Poisson’s ratio of the composites. After the elasticity stage, the loading speed rate was set as 0.3 mm/min until the specimen fractured. From the stress-strain diagram recorded by the computer according to the load-displacement data, one can measure and determine the yield strength, ultimate tensile strength, percent elongation, and percent reduction in area of the composites. Each value of tensile properties is an average of at least three specimens.
Mechanical Properties
Young’s modulus and Poisson’s ratio are fundamental mechanical parameters of composites and involve only the straight-line segment of the stress-strain diagram of tensile tests. The normal stress σ is proportional to the strain ε as Hooke’s law
Where the stress σ can be calculated using the applied load, and strain ε can be read directly using an electrical-resistance strain gage. Then Young’s modulus E can be determined by Eq. 2. Poisson’s ratio υ characterizes the ratio between the lateral strain ε′ and longitudinal strain ε of material under tensile load within the elastic range.
To measure the lateral strain and longitudinal strain of composites under the tensile load, the electrical strain gages were pasted at the surface of the specimen before testing, as shown in Figure 6A. On one side surface, two pieces of electrical strain gage were pasted lateral and longitudinal respectively, while two pieces of electrical strain gage were pasted at the same position on another side surface of the specimen. The full-bridge connection scheme in Figure 6B is used to eliminate the influence of initial bend and eccentric loading that may exist in the process of testing, and improve the measurement precision of the Poisson’s ratio. Then the strain formula read by the strain gauge is as follows:
where εds is strain of the strain gauge, εt is the strain caused by temperature variation, εw is bending strain of specimen, εT is the strain of axial or lateral under the load.
The TiB2/A356 in-situ composites have no obvious yield stage in the stress-strain diagram, but also show certain plastic characteristics. Therefore, the yield strength σ0.2 was used, which is obtained by drawing a line parallel to the straight-line segment of the stress-strain diagram through the point with the abscissa ε = 0.2%. As the load increases, the specimen eventually breaks, and the largest force is reached. The stress corresponding to this largest force is denoted by the ultimate tensile strength (UTS) σb.
The ductility of composites is characterized by its percent elongation δ
Where, L0 and L1 denote the initial length of the specimen and its final length after rupture, respectively. Another measure of ductility is the percent reduction in area Ψ
Where, A0 and A1 denote the initial cross-sectional area of the specimen and its minimum cross-sectional area after rupture, respectively.
Results and Discussion
Young’s Modulus and Poisson’s Ratio
Figure 7 shows the variation of Young’s modulus and Poisson’s ratio of the prepared composites as a function of weight percentage (wt%) of TiB2 particles. A obvious enhancement is observed in Young’s modulus of the composites comparing with that of the non-reinforced A356 alloy, and the increase is nearly linear with the increasing wt% of TiB2 particles of as-cast and T6 state. The average Young’s modulus of composites of T6 state with TiB2 particles wt% of 1%, 3%, and 5% increase by 3.02%, 8.08%, and 10.87% respectively, compared with A356 alloys. Therefore, the addition of high modulus particles is one of the most effective methods to improve the Young’s modulus of composites. From Figure 7A, it is also found that T6 heat treatment can increase the Young’s modulus of composites by a small amount, which increases to a maximum of 1.76% compared with the as-cast composites of 5 wt% TiB2. This is attributed to the fact that Young’s modulus characterizes the overall performance of the composites and is determined by atomic nature of metal and lattice type, with less influence from grain size and second phase dispersion. That is, the Young’s modulus of composites is insensitive to the variation of the microstructure caused by the T6 heat treatment.

FIGURE 7. Effect of TiB2 content on: (A) Young’s modulus, and (B) Poisson’s ratio of TiB2/A356 composites.
Figure 7B shows the influence on Poisson’s ratio of the prepared composites with increasing of wt% of TiB2 particles. It can be observed that the addition of TiB2 to the A356 alloy decreased the Poisson’s ratio of composites of as-cast and T6 treatment. The average Poisson’s ratio of composites with wt% of TiB2 particles of 1%, 3%, and 5% decreased to about 1.20%, 1.92%, and 3.18%, respectively, compared to that of A356 alloy. This is because the Poisson’s ratio of A356 alloy is 0.321 and the Poisson’s ratio of TiB2 particles is 0.11, and the presence of hard TiB2 particles influences the elastic deformation of composites. Therefore, with the increase of TiB2 particles, the Poisson’s ratio of composites shows a decreasing trend. From Figure 7B, it can be found that microstructural variation occurring at higher processing temperatures influences the Poisson’s ratio slightly. The average Poisson’s ratio of composites with TiB2 particles of 1%, 3%, and 5% in T6 state decreases by 0.6%, 0.73%, and 1.22%, respectively, compared to that of composite in as-cast.
Yield Strength and Ultimate Tensile Strength
The effect of wt% of TiB2 particles on the yield strength and ultimate tensile strength of the prepared composites is presented in Figure 8. It shows that the yield strength and ultimate tensile strength of composites of as-cast and T6 state increased with the increase of wt% of TiB2 particles. The enhancement in tensile strength of composites is the synthetic effect of various parameters that affect the mechanical properties of composites. The grain refinement and strong thermal stress at TiB2/A356 interface because of the difference in the thermal expansion coefficient of A356 alloys and TiB2 particles are important reasons to increase the strength of composites. A well bonded and clean interface leads to the transfer of tensile load from the A356 matrix to the distributed TiB2 particles effectively, and is also a reason for the increasing tensile strength of composites. From the figure, it also can be found that the average yield strength and ultimate tensile strength of composites of T6 state are much greater than that of as-cast composites. One of the reasons is that T6 heat treatment can effectively improve the microstructure of composite as analyzed in Microstructural Characterizations. Which causes the enhancement of tensile strength of composites.
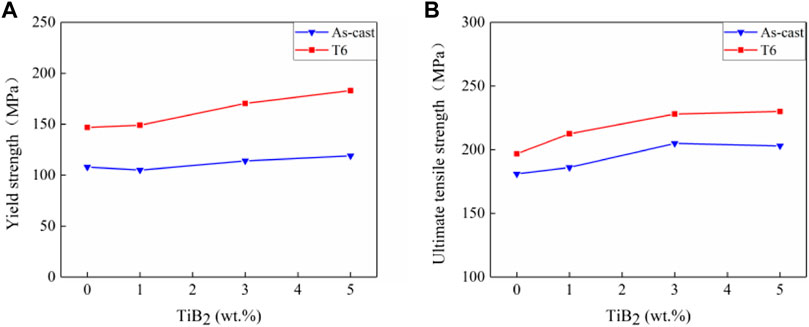
FIGURE 8. Effect of TiB2 content on: (A) Yield strength, and (B) Ultimate tensile strength of TiB2/A356 composites.
It is noted from Figure 8A that when the wt% of TiB2 particles is less than 1%, the yield strength of the composites does not increase significantly, and is less than that of A356 alloy. This is because the addition of reinforced particles can enhance the strength of the A356 matrix, but the presence of reinforced particles will also damage the continuity of the matrix alloy to a certain extent, and even form microporosity which is known as a defect in the matrix. Therefore, the strengthening and weakening factors of mechanical properties of composites offset the effects of each other, and thus, with less wt% of TiB2 particles (in this work, less than 1 wt%), the reinforcement degree of the particles is not enough to offset the weakening factors in the matrix structure. However, with the increasing of the wt% of TiB2 particles to a critical value, the strengthening effect of particles on A356 alloy is greter than the weakening factors in the matrix structure, and the yield strength of the composites shows an increasing trend with the increasing of wt% of TiB2 particles.
Figure 8B shows that the ultimate tensile strength of the prepared composites increases with the increase of the wt% of TiB2 particles, but further increase of in-situ TiB2 particle content (in this work, more than 5 wt%) leads to the reduction in the ultimate tensile strength of the composites. This is because, in contrast to the elastic property of composites, ultimate tensile strength characterizes the local performance of composites and is more sensitive to various defects inside composites. In the preparation of in-situ TiB2/A356 composites, it is inevitable to cause an amount of porosity, particle clusters, and slag inclusion, which result in stress concentration and micro-cracks are likely to occur in the periphery with small load. Figure 9 shows the fracture photos of the specimen with low tensile strength (particles 5 wt%). It can be seen that there is slag inclusion of reaction residues, pores, and porosity of different sizes inside the composites. These defects reduce the tensile strength of the composites to a certain extent. Another reason is that the increasing wt% of TiB2 particles increased the viscosity of the halide melt, which reduces the fluidity of the A356 melt and reduces the diffusion of reactants, which leads to difficulty in the chemical reaction and casting molding. Therefore, higher wt% of TiB2 particles would weaken the enhancement effect of the composites. Wood et al. (Chen et al., 2009a) reported that the volume fraction of in-situ synthesized particles should not be higher than 12% to ensure the good fluidity of the composites and the final casting forming.
Elongation and Percent Reduction in Area
Figure 10 show the elongation of the prepared composites of as-cast and T6 state and the percent reduction in area (PRA) for different wt% of TiB2 particles. It can be seen that with the increasing wt% of TiB2 particles, the elongation and percent reduction in area of the composites increase at first (wt% of TiB2 particles less than 1%) and then decrease on both as-cast and T6 state. The elongation of composites decreased to a maximum of 38.7%, and the percent reduction in area decreased by about 19.6% when adding 5 wt% TiB2 particles to the A356 alloy. On the one hand, the presence of hard TiB2 particles decreases the ductility of composites; on the other, the presence of TiB2 particles can refine the grain of composites, and grain refinement improves not only the strength but also the plasticity and toughness of the composites because when there are more grains in a certain volume, the deformation is borne by more grains. Therefore, the in-situ TiB2/A356 composites can endure large plastic deformation, showing good ductility. Within less wt% of TiB2 particles, the improvement degree of the ductility offset the brittleness of the matrix, which leads to an increase in the elongation and percent reduction in area of the composites with the increase of TiB2 particles up to 1 wt%. Once the improvement of ductility is not enough to offset the increase of brittleness, the elongation and percent reduction in area of the composite show a decreasing trend with the increasing wt% of TiB2 particles.
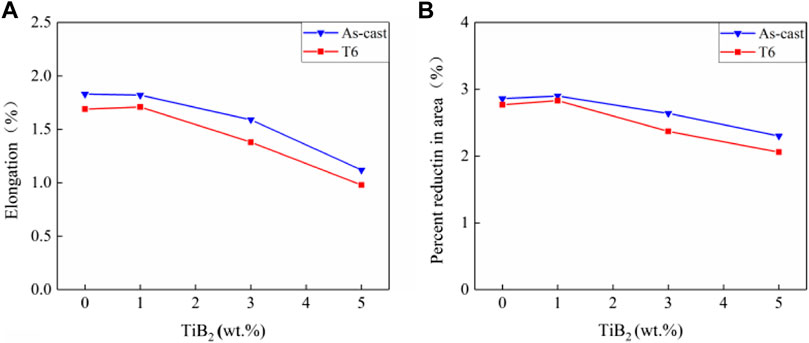
FIGURE 10. Effect of TiB2 content on: (A) Percent elongation, and (B) Percent reduction in area of TiB2/A356 composites.
Fracture Behavior
Figure 11A shows the photos of the specimen of the prepared composite after fracturing at room temperature. It can be seen that the deformation of the specimen is tiny without an obvious necking phenomenon on the fracture surface, and the fracture surface is relatively flat and nearly vertical to the tensile stress. The fracture morphology with 100 times magnified view in Figure 11B reveals the glossy crystalline bright surface. These phenomena show the characteristics of brittle fracture.
The fracture SEM morphology of the prepared composites is presented in Figure 12, which shows that there are many uniformly distributed voids with different sizes and tear edges on the tensile fracture of the composites. The larger voids lead to ductile fractures, while smaller size voids cause brittle fracture macroscopical and ductile fracture microscopical. This contributes to the debonding of the interface between the TiB2 particles and A356 matrix under the action of external load, which is easy to induce crack initiation and expand along the interface to form voids. The voids gradually grow up with the deformation process and expand rapidly once passing through the interface, which leads to the final fracture of the composites.
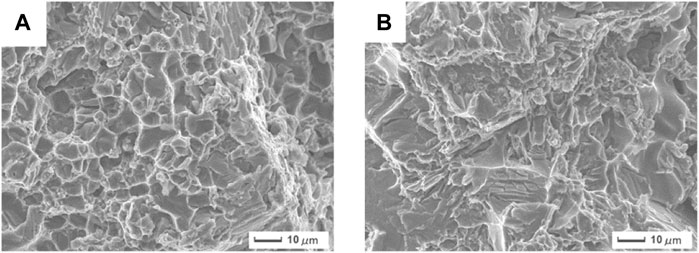
FIGURE 12. The SEM fractographs of the fracture of TiB2/A356 in-situ composites on (A) as-cast and (B) T6 treatment.
Conclusion
In the present study, A356 alloy reinforced with various wt% (0, 1%, 3%, and 5%) of TiB2 particles were prepared by the reaction of KBF4 and K2TiF6 with melted aluminum. The in-situ grown TiB2 particles were characterized with regular shapes and nearly uniformally distributed in the alloy matrix. A clear interface and good interface bonding between the A356 matrix and TiB2 particles was achieved. The mechanical properties of the prepared composites of as-cast and T6 state were studied with an axial tensile test and the strain electrical measurement method. A great enhancement in tensile properties is obtained compared with those of the non-reinforced A356 alloys. As the proportion of TiB2 particles increases, the Young’s modulus and ultimate tensile strength of the composites increase, while the Poisson’s ratio of the composites decreases. The yield strength of the composites decreases at first (when particle wt% is less than 1%) then increases, while elongation and percent reduction in area increase at first and then decrease with the increasing wt% of TiB2 particles. T6 heat treatment can refine the grain and effectively improve the mechanical properties of TiB2/A356 in-situ composites.
Data Availability Statement
The raw data supporting the conclusion of this article will be made available by the authors, without undue reservation.
Author Contributions
WW: Data curation; Roles/Writing—original draft TZ: Data curation; Formal analysis WH: Investigation; Methodology; Project administration; SJ: Writing—review and editing; Supervision.
Funding
This work is sponsored by the Six Talent Peaks Project in Jiangsu Province (Grant No. 2019-KTHY-059).
Conflict of Interest
The authors declare that the research was conducted in the absence of any commercial or financial relationships that could be construed as a potential conflict of interest.
Publisher’s Note
All claims expressed in this article are solely those of the authors and do not necessarily represent those of their affiliated organizations, or those of the publisher, the editors and the reviewers. Any product that may be evaluated in this article, or claim that may be made by its manufacturer, is not guaranteed or endorsed by the publisher.
References
Afkham, Y., Khosroshahi, R. A., Rahimpour, S., Aavani, C., Brabazon, D., and Mousavian, R. T. (2018). Enhanced Mechanical Properties of In Situ Aluminium Matrix Composites Reinforced by Alumina Nanoparticles. Arch. Civil Mech. Eng. 18 (1), 215–226. doi:10.1016/j.acme.2017.06.011
Bartels, C., Raabe, D., Gottstein, G., and Huber, U. (1997). Investigation of the Precipitation Kinetics in an A16061/TiB2 Metal Matrix Composite. Mater. Sci. Eng. A 237 (1), 12–23. doi:10.1016/s0921-5093(97)00104-4
Chen, X. W., Pei, G. L., and Jin, Y. S. (2009a). Study on Accelerated Ageing of Aeronautical Perspex(PMMA) in Ultraviolet. J. Aeronaut. Mater. 29, 107–112. doi:10.3969/j.issn.1005-5053.2009.6.022
Chen, X. W., Zhang, T. J., and Liu, S. H. (2009b). Accelerated Ageing Behavior of PMMA under Hygrothermal Air and Water Conditions. Fail. Anal. Prev. 4, 193–195. doi:10.3969/j.issn.1673-6214.2009.04.001
Deepak, S., Jha, S. K., Karthik, D., and Mandal, A. (2019). Fatigue Analysis of A356-TiB2 (5wt%) In-Situ Nano Composites. Mater. Today-Proceedings 18 (3), 774–779. doi:10.1016/j.matpr.2019.06.494
Fattahi, M., Pazhouhanfar, Y., Delbari, S. A., Shaddel, S., Namini, A. S., and Shahedi Asl, M. (2020). Influence of TiB2 Content on the Properties of TiC-SiCw Composites. Ceramics Int. 46 (6), 7403–7412. doi:10.1016/j.ceramint.2019.11.236
Guan, C., Zhao, Y., Chen, G., Kai, X., Qian, W., Tao, R., et al. (2021). Synergistic Strengthening and Toughening of Copper Coated Graphene Nanoplates and In Situ Nanoparticles Reinforced AA6111 Composites. Mater. Sci. Eng. A 822, 141661. doi:10.1016/j.msea.2021.141661
Jelinek, B., Groh, S., and Horistemeyer, M. F. (2012). Modified Embedded Atom Method Potential for Al, Si, Mg, Cu, and Fe Alloys. Phys. Rev. B 85 (24), 5102–5113. doi:10.1103/physrevb.85.245102
Kai, X., Huang, S., Wu, L., Tao, R., Peng, Y., Mao, Z., et al. (2019). High Strength and High Creep Resistant ZrB2/Al Nanocomposites Fabricated by Ultrasonic-Chemical In-Situ Reaction. J. Mater. Sci. Technol. 35, 2107–2114. doi:10.1016/j.jmst.2019.04.020
Kai, X., Tian, K., Wang, C., Jiao, L., Chen, G., and Zhao, Y. (2016). Effects of Ultrasonic Vibration on the Microstructure and Tensile Properties of the Nano ZrB2/2024Al Composites Synthesized by Direct Melt Reaction. J. Alloys Compd. 668, 121–127. doi:10.1016/j.jallcom.2016.01.152
Kai, X., Wu, L., Peng, Y., Tan, Z., Li, G., Chen, G., et al. (2021). Effects of Zr Element on the Microstructure and Mechanical Properties of B4C/Al Composites Fabricated by Melt Stirring Method. Composites B: Eng. 224, 109156. doi:10.1016/j.compositesb.2021.109156
Karbalaei Akbari, M., Baharvandi, H. R., and Shirvanimoghaddam, K. (2015). Tensile and Fracture Behavior of Nano/micro TiB2 Particle Reinforced Casting A356 Aluminum alloy Composites. Mater. Des. (1980-2015) 66, 150–161. doi:10.1016/j.matdes.2014.10.048
Kim, S-W., Lee, S-J., Dae-Up, K., and Kim, M-S. (2021). Experimental Investigation on Tensile Properties and Yield Strength Modeling of T5 Heat-Treated Counter Pressure Cast A356 Aluminum Alloys. Metals 11, 1–17. doi:10.3390/met11081192
Liang, Z., Zhang, S.-L., Guan, C., Yin, H., Zhenya, Z., Wu, J.-L., et al. (2019). Effects of Rolling on Microstructures and Properties of In-Situ (TiB2 + ZrB2)/AlSi9Cu1 Composites. Mater. Res. Express 6 (10), 106584. doi:10.1088/2053-1591/ab3b36
Logesh, K., Hariharasakthisudhan, P., Arul Marcel Moshi, A., Rajan, B. S., and K, S. (2020). Mechanical Properties and Microstructure of A356 alloy Reinforced AlN/MWCNT/graphite/Al Composites Fabricated by Stir Casting. Mater. Res. Express 7 (1), 015004. doi:10.1088/2053-1591/ab587d
Mandal, A., Chakraborty, M., and Murty, B. S. (2008). Ageing Behaviour of A356 alloy Reinforced with In-Situ Formed TiB2 Particles. Mater. Sci. Eng. A 489, 220–226. doi:10.1016/j.msea.2008.01.042
Pariyar, A., Perugu, C. S., Toth, L. S., and Kailas, S. V. (2021). Microstructure and Mechanical Behavior of Polymer-Derived In-Situ Ceramic Reinforced Lightweight Aluminum Matrix Composite. J. Alloys Compd. 880, 160430. doi:10.1016/j.jallcom.2021.160430
Qian, W., Zhao, Y., Kai, X., Yan, Y., Gao, X., and Jin, L. (2020). Microstructure and Properties of 6111Al Matrix Composites Reinforced by the Cooperation of In Situ ZrB2 Particles and Y. J. Alloys Compd. 829, 154624. doi:10.1016/j.jallcom.2020.154624
Rahoma, H. K. S., Wang, X. P., Kong, F. T., Chen, Y. Y., Han, J. C., and Derradji, M. (2015). Effect of (α+β) Heat Treatment on Microstructure and Mechanical Properties of (TiB+TiC)/Ti-B20 Matrix Composite. Mater. Des. 87, 488–494. doi:10.1016/j.matdes.2015.08.028
Raveendran, S., Alam, M. M., Khan, M. I. K., Dhayalan, A., and Kannan, S. (2020). In Situ formation, Structural, Mechanical and In Vitro Analysis of ZrO2/ZnFe2O4 Composite with Assorted Composition Ratios. Mater. Sci. Eng. C 108, 110504. doi:10.1016/j.msec.2019.110504
Senthil Kumar, P., Kavimani, V., Soorya Prakash, K., Murali Krishna, V., and Shanthos Kumar, G. (2020). Effect of TiB2 on the Corrosion Resistance Behavior of In Situ Al Composites. Inter. Metalcast. 14 (1), 84–91. doi:10.1007/s40962-019-00330-3
Tao, R., Zhao, Y., Kai, X., Wang, Y., Qian, W., Yang, Y., et al. (2018). The Effects of Er Addition on the Microstructure and Properties of an In Situ Nano ZrB2-Reinforced A356.2 Composite. J. Alloys Compd. 731, 200–209. doi:10.1016/j.jallcom.2017.10.021
Wang, M., Chen, D., Chen, Z., Wu, Y., Wang, F., Ma, N., et al. (2014). Mechanical Properties of In-Situ TiB2/A356 Composites. Mater. Sci. Eng. A 590, 246–254. doi:10.1016/j.msea.2013.10.021
Xue, J., Wu, W., Ma, J., Huang, H., and Zhao, Z. (2020). Study on the Effect of CeO2 for Fabricating In-Situ TiB2/A356 Composites with Improved Mechanical Properties. Mater. Sci. Eng. A 786, 139416. doi:10.1016/j.msea.2020.139416
Zhang, H., Chen, G., Zhang, Z., Zhao, Y., Mu, S., Xu, J., et al. (2020). Study on the Grain Refinement of A356 alloy by Al-3wt-% VN Master alloy. Mater. Sci. Technol. 36 (7), 819–826. doi:10.1080/02670836.2020.1743925
Zhao, Z., Wang, S., Du, W., Bai, P., Zhang, Z., Wang, L., et al. (2021). Interfacial Structures and Strengthening Mechanisms of In Situ Synthesized TiC Reinforced Ti6Al4V Composites by Selective Laser Melting. Ceramics Int. 47 (24), 34127–34136. doi:10.1016/j.ceramint.2021.08.323
Keywords: in-situ composites, A356 alloy, TiB2, microstructure, mechanical properties
Citation: Wu W, Zeng T, Hao W and Jiang S (2022) Microstructure and Mechanical Properties of Aluminum Matrix Composites Reinforced With In-Situ TiB2 Particles. Front. Mater. 9:817376. doi: 10.3389/fmats.2022.817376
Received: 18 November 2021; Accepted: 04 January 2022;
Published: 07 February 2022.
Edited by:
Seunghwa Ryu, Korea Advanced Institute of Science and Technology, South KoreaReviewed by:
Raghvendra Kumar Mishra, Cranfield University, United KingdomMehdi Derradji, Ecole Militaire Polytechnique (EMP), Algeria
Copyright © 2022 Wu, Zeng, Hao and Jiang. This is an open-access article distributed under the terms of the Creative Commons Attribution License (CC BY). The use, distribution or reproduction in other forums is permitted, provided the original author(s) and the copyright owner(s) are credited and that the original publication in this journal is cited, in accordance with accepted academic practice. No use, distribution or reproduction is permitted which does not comply with these terms.
*Correspondence: Wenfeng Hao, aGFvd2VuZmVuZzIwMDdAMTYzLmNvbQ==; Shiping Jiang, anNwaW5nQDE2My5jb20=