- 1Department of Chemistry, College of Science, Imam Mohammad ibn Saud Islamic University (IMSIU), Al Riyadh, Saudi Arabia
- 2Department of Production Technology, Faculty of Technology and Education, Helwan University, Cairo, Egypt
- 3Department of Engineering and Construction, University of East London, London, United Kingdom
- 4Executive Principal Office, Oxford Business College, Oxford, United Kingdom
- 5Department of Materials Science and Engineering, Korea Advanced Institute of Science and Technology (KAIST), Daejeon, Republic of Korea
- 6Nanotechnology Research Institute, Jiaxing University, Jiaxing, China
- 7Department of Mechanical Engineering, College of Engineering, San Diego State University, San Diego, CA, United States
Introduction: Metal matrix composites reinforced with ceramic and carbon nanotubes (CNTs) are considered recently as new materials for thermal managements and heat sink applications of electronic components.
Method: Cu nanocomposites reinforced with CNTs and different content of Si3N4 up to 5 wt.% (CNTs-xSi3N4/Cu) are synthesized by electroless Cu deposition process. The produced (CNTs-xSi3N4/Cu) nanocomposites powder were divided into two groups of samples. The first group were consolidated by two steps of cold pressing at 600 MPa compaction pressure followed by sintered under Ar atmosphere at 850°C for 90 min. However, the second group of powders are spark plasma sintered (SPS) under vacuum by simultaneously applying compaction pressure of 50 MPa at sintering temperature of 850°C for one min. The microstructure and the chemical composition of the investigated CNTs and the produced CNTs-xSi3N4/Cu powders as well as the CNTs-xSi3N4/Cu sintered nanocomposites were investigated by FTIR, SEM, TEM, EDX, X-ray mapping and XRD. The sinterability of the produced CNTs-xSi3N4/Cu nanocomposites is evaluated by measuring the Archimedes’ density and the coefficient of thermal expansion (CTE).
Results and discussion: The electroless coating process enhancing the homogeneous distribution of CNTs and Si3N4 reinforced particles in the Cu matrix by preventing the formation of the agglomerations and segregations in the Cu matrix and retaining the nanostructure. The density and the CTE of the obtained CNTs-xSi3N4/Cu nanocomposites were improved by consolidation with SPS. The CNTs-xSi3N4/Cu nanocomposites sintered by SPS process have higher relative density approaches 100 % and lower CTE of 1.8 × 10−5°C-1–1.6 × 10−5°C-1 than, the density of the CNTs-xSi3N4/Cu nanocomposites sintered by conventional powder metallurgy technique with relative sintered density approaches 85 % and CTE of 2.6 × 10−5°C-1–1.9 × 10−5°C-1. Our findings owing that; the produced CNTs-Si3N4/Cu nanocomposites are expected as suitable candidate materials for thermal managements and heat sink packaging materials of electronic components.
1 Introduction
Metal matrix nanocomposites reinforced by novel carbon materials such as carbon fibers, graphene, and diamond are developed to fabricate thermal management and heat sink materials due to their low coefficient of thermal expansion (CTE) and good thermal conductivity (Balandin, 2011). Metal matrix composites containing carbon nanotubes (CNTs) have attracted increasing attention for different thermal applications due to their low or negative CTE, ranging from −2.5 to 0 ppm/K (Alamusi et al., 2012; Lindsay et al., 2013; Schebling and Keblinski, 2003; Berber et al., 2000; Kim et al., 2001). Few research studies on the thermal properties of metal matrix composites reinforced by CNTs are reported in the literature (Duan et al., 2017). It was mentioned in a previous report that CNTs/Al metal matrix composites have lower CTE values than pure Al metal itself (Carvalho et al., 2013).
Challenges related to the dispersion of CNTs in metal matrices composed of Cu, Al, and Ni and their interfacial bonding require more extensive studies due to their significant impact on the physical and mechanical properties. The technical problems of the CNTs/metal matrix composites sintered by conventional powder metallurgy processes have not been completely solved and still have limited thermal management applications due to the poor wettability between the CNTs and several types of metals and CNT agglomeration in the metal matrix. There are four technical difficulties in preparing CNTs/Cu composites: interface between CNTs and the Cu matrix, dispersion of CNTs, densification of the CNTs/Cu composites, and orientation of CNTs in the Cu matrix (Huang et al., 2017). Thus, electroless plating of CNTs by Cu nanolayers is used to build up strong interactions between CNTs and Cu matrices, and this research provides novel ideas and technology for the distribution and directional alignment of CNTs in the Cu matrix. The particle coating process is developed, as reported in the literature, based on the electroless deposition of some metal nanoparticles on the graphitic surface of CNTs and carbon fibers (Daoush et al., 2020; Daoush et al., 2009). This coating process reduces agglomeration and segregation of the reinforcements within the Cu metal matrix. It was reported in a previous work that the hardness, strength, and abrasion resistance of Cu electrical contact materials were improved by aligning CNTs in Cu matrix composites through die-stretching, owing to their excellent mechanical properties and abrasion resistance (Huang et al., 2017).
Silicon nitride (Si3N4) is a promising engineering material due to its superior thermal properties, chemical stability, and oxidation resistance (Cheng et al., 2019). Si3N4 has unique wear resistance, corrosion resistance, and high-temperature mechanical properties. Moreover, Si3N4 has excellent thermal shock resistance due to its low CTE and high thermal conductivity (Li et al., 2020; Parsi et al., 2019; Wang et al., 2021). In addition, the strong covalent bonding between Si and N and the high grain boundary energy of Si3N4 result in a low driving force for the sintering process at high temperatures over prolonged periods, which prevents grain coarsening and structural shrinkage, thereby maintaining the nanostructure after sintering (Zhang Y. et al., 2021; Zhang X. et al., 2021).
Copper (Cu) is one of the most important metals used in electric and thermal applications. It is inexpensive and offers good formability, castability, and machinability. Compared with other common metals used in thermal applications, such as Al, Cu has higher thermal and electrical conductivities and a lower CTE value. These unique properties make Cu, its alloys, and its composites excellent candidate materials for thermal management applications, such as heat sinks and packaging of the electronic components, which helps dissipate the heat generated when electric current passes through the electronic components (Daoush et al., 2020; Daoush et al., 2009).
The influence of Si3N4 reinforcement addition on the mechanical behavior of Al–Si3N4 composites has been previously studied. The results obtained support the use of Si3N4 in enhancing the mechanical performance of aluminum-based metal matrix systems for structural applications (Raghavendra Rao and Mohan, 2020). Another research work involved the development of an aluminum alloy hybrid composite using Al6061 as the matrix and Si3N4 as hybrid reinforcement particles, fabricated through a dual-step stir casting method. The hybrid compositions reported an increase in hardness and ultimate tensile strength (Arya et al., 2023). Si3N4-reinforced Cu–Sn-based composites were also successfully prepared by the two-step stir casting technique. The addition of hard Si3N4 particles is found to increase the hardness and ultimate tensile strength of the composite (Hanumantharayappa et al., 2021). Recently, the effect of the addition of Si3N4 and synthesized graphene oxide (GO) on the physical, wear, and corrosive characteristics of the Cu matrix was also studied. The microhardness is increased with the GO and Si3N4 addition. The wear rate of the Cu matrix decreases with reinforcement addition due to the self-lubricating nature of GO and the hardness of the Si3N4 ceramic. The worn surface analysis confirms the transition from severe wear to mild wear with Si3N4 addition. The corrosion results suggest that the composite reinforced with 0.3% GO and 15% Si3N4 yielded better corrosion resistance than the other developed composites (Kalidas et al., 2025).
Electroless metal deposition is an autocatalytic process in which reduction with continuous deposition of metal ions and oxidation of a reducing agent simultaneously occur on catalytic or conductive surfaces. It can be deposited with uniform thickness over the surfaces of various substrate materials, regardless of their size, shape, and electrical conductivity (Daoush et al., 2009; Ejaz et al., 2022; Cui et al., 2015; Kilicarslan et al., 2012). Electroless plating with Cu is mostly used for the metallization of nonconductive surfaces in printed circuit boards, electronic devices, and jewelry plating. Traditional electroless Cu deposition uses formaldehyde as the reducing agent, as shown in the following redox chemical reaction (Daoush et al., 2009): Cu2+ + 2HCHO + 4OH− = Cu + 2HCOO− + 2H2O+ H2. It is known that the incorporation of hydrogen into the deposited Cu causes brittleness in the coating layer. This brittleness can be influenced by the deposition rate, temperature, and certain additives. However, a more direct way to avoid hydrogen embrittlement is to deposit the metal without hydrogen evolution or at least by reducing the amount of evolved gas. CNTs, as the material of interest, can trap the evolved hydrogen gas within their graphitic nanocage structure. The electroless Cu deposition process on nonconductive surfaces such as epoxy polymer was also studied (Uzunlar et al., 2013). The conditions of electroless Cu deposition are optimized in order to produce high-quality coating layers, as reported in the literature (Tian and Guo, 2010). Tartrate (Deckert, 1995) and ethylene diamine tetra acetic acid (EDTA) (Lowenheim, 1974; Nadiia et al., 2012) were also added as complexing agents in the electroless Cu bath to prevent the precipitation of Cu(OH)2 under the alkaline condition and improve the deposition rate and the bath stability for a short time. The autocatalytic mechanism, thermodynamics, and kinetic aspects of the Cu2+ ion reduction by formaldehyde were also reported in the literature (Mallory and Hajdu, 1990). The use of ionic surfactants such as sodium dodecyl sulfate and cetyltrimethylammonium bromide detergents in controlling the shape and size of Cu nanoparticles has also been reported in the literature (Lisiecki et al., 1996; Mustafa and İlkay, 2010). In this study, the NaBH4 reducing agent gets absorbed on the surface of PEEK/MWCNT, and in situ electroless Cu coating takes place. A dense Cu layer was deposited on the interconnected micro-pores through strong adhesion of Cu coating to the surface of the PEEK/MWCNT.
Spark plasma sintering (SPS) is an advanced sintering method used to consolidate various ceramic (Azarniya et al., 2017a) or metallic (Azarniya et al., 2017b) materials using lower sintering temperatures and shorter dwell times than those of the conventional sintering techniques. The SPS technique is similar to hot isostatic pressing (HIP); however, SPS uses a pulsed direct current with low voltage to heat the compacted powders during the process, enabling the production of fully densified, pore-free materials with outstanding sinterability and properties (Munir et al., 2011; Garay, 2010; Orru et al., 2009a). Previous studies have been conducted to develop the sintering process for metal matrix composite powders, such as CNTs/Cu (Daoush et al., 2009; Darabi et al., 2018) and Cu/W (Nicolicescu et al., 2023) powders, fabricated by electroless coating and subsequently consolidated using SPS. It was revealed that the improvements in the physical and mechanical properties of these materials are due to the combination of the electroless powder coating of the reinforcement particles, followed by sintering at a moderate temperature using SPS. SPS products are typically achieved in a short sintering time, resulting in fully densified net-shape materials by inhibiting grain growth and retaining the nanostructure, preventing the segregation and agglomeration of the reinforcement particles in the metal matrix after sintering (Zhu et al., 2022).
Materials used in the design and development of different heat sink components are employed for the thermal management of electronic system devices. The function of heat sinks is the thermal dissipation of heat from the electronic component at a relatively high temperature to an object with greater heat capacity. Recently, heat sinks have become essential in integrated circuits, microprocessors, and computer central processing units (CPUs). The ideal materials used for the development of the heat sink materials are obtained by designing new composites through the combination of different reinforced and matrix materials that possess high thermal conductivity and high heat capacity to absorb the generated thermal energy. Metals have a high thermal conductivity and are commonly used as heat sinks because they easily absorb and emit heat energy; however, they have low heat capacity. Therefore, in recent years, new heat sinks have been developed by combining metals with ceramic and carbon-based reinforcement materials to fabricate advanced composites. Metal matrix composites containing reinforced particles of the highest intrinsic thermal conductivity and CTEs could cover the requirements of the heat sink materials (Sotgiu et al., 2024; Singh and Gautam, 2019; Ahmed et al., 2016; Uddin et al., 2010).
In this work, a step-by-step process was developed to fabricate new composite materials composed of CNTs–xSi3N4/Cu reinforced with different Si3N4 contents by the combination of the electroless deposition technique and consolidation by conventional powder metallurgy or SPS processes to improve the homogeneity and distribution and prevent the agglomeration and segregation of the CNTs and Si3N4 ceramic-reinforced particles in the Cu matrix. The homogeneous dispersion of CNTs and the formation of strong metal–CNT interfacial bonding are the major challenges to the effective use of CNTs in metal matrix composites (Xia et al., 2021). CNTs are treated with heat and acid to functionalize their graphitic surfaces and improve their dispersion in an aqueous solution. The homogeneous dispersion of CNTs and Si3N4 particles can be improved by the electroless deposition coating of the CNTs and Si3N4 particles, followed by the SPS process in a short sintering time, which retains the nanostructure of the sintering composites. It was expected that the preparation of the CNTs–xSi3N4/Cu nanocomposite powders by the electroless Cu deposition technique would decrease the cost of the process compared with that of the other expensive processes, such as chemical vapor deposition (CVD), physical vapor deposition (PVD), or sputtering techniques. In addition, the combination of CNTs, Si3N4 reinforcement particles, and the Cu metal as a matrix is expected to improve the thermal management properties of the sintered Cu-based material for heat sink applications. Although several articles have reported on the electroless copper deposition process (Daoush et al., 2020; Daoush et al., 2009; Uzunlar et al., 2013; Tian and Guo, 2010; Deckert, 1995; Lowenheim, 1974; Nadiia et al., 2012; Mallory and Hajdu, 1990; Lisiecki et al., 1996; Mustafa and İlkay, 2010), to the best of our knowledge, this is the first study focused on the properties of CNTs, Si3N4, and Cu ternary-phase materials. The microstructure, density, and CTE of the obtained CNTs–xSi3N4/Cu nanocomposites are also investigated. The distribution of CNTs and Si3N4 reinforcements in the Cu matrix, along with its chemical composition, was also investigated using field emission scanning electron microscopy (FESEM) coupled with energy dispersive X-ray (EDX) spectroscopy, high-resolution transmission electron microscopy (HRTEM), and X-ray diffraction (XRD). The treated CNTs are investigated by Fourier transform infrared spectroscopy (FT-IR). The effect of the electroless coating process of the CNTs and Si3N4-reinforced particles and the SPS process on the sinterability, density, and CTE of the produced CNTs-xSi3N4/Cu nanocomposites was also studied to evaluate the performance of the produced CNTs-xSi3N4/Cu nanocomposites for thermal management and heat sink applications.
2 Materials and methods
2.1 Materials
Si3N4 powder with a particle size of 500–700 nm and multi-walled CNTs (MWCNTs) with a length of 10–50 µm, a diameter of 15–10 nm, and a surface area of ∼200 m2/g were purchased from Iljin Nanotech Co., Ltd. (Seoul, South Korea). High-purity analytical-grade HNO3, H2SO4, CuSO4.5H2O, and NaOH were used in the preparation of the electroless Cu deposition bath. Potassium–sodium tartrate was used as a complexing agent to prevent the deposition of Cu(OH)2. Formaldehyde solution (HCHO 38vol%) was used as a reducing agent of Cu ions to Cu metal.
2.2 Methods
The as-received MWCNTs underwent heat-treatment in an oven at 450°C for 30 min to remove any organic volatile impurities. The obtained powder was chemically treated with acetone to dissolve any remaining organic compounds, after heat-treatment. Then, the powder was acid-treated using 33 vol% conc. HCl for 15 min to dissolve any inorganic impurities. An acid mixture of HNO3 and H2SO4 was prepared to functionalize the surfaces of the graphitic structure of MWCNTs. Then, the obtained powder was repeatedly centrifuged at 3,000 rpm for 5 min, followed by washing several times with double-distilled water to remove any remaining acids (Daoush et al., 2009). The produced powders of the treated CNTs were characterized using an FT-IR analyzer, model Nicolet 6700.
Preliminary studies were conducted to determine the lower and upper limits of the Si3N4 and CNT reinforcement wt%. It was found that the addition of more than 5 wt% Si3N4 content and more than 0.1 wt% CNTs will deteriorate the properties due to the agglomeration of the Si3N4 ceramic reinforcement particles in the metal matrix (Darabi et al., 2018). Then, two groups of CNTs–xSi3N4/Cu nanoparticles were fabricated by an electroless coating process. Each group consists of six samples containing 0.0, 1.0, 2.0, 3.0, 4.0, and 5.0 wt% of Si3N4 particles and 0.1 wt% of MWCNTs coated with the Cu metal (see Table 1). Preliminary studies were developed according to previous research work for optimizing the electroless Cu deposition conditions on the surface of MWCNTs and Si3N4 particles (Daoush et al., 2020; Daoush et al., 2009). The calculated amounts of MWCNTs and Si3N4 particles were weighed using a four-digit electronic balance and then dispersed in an aqueous solution consisting of 70 g/L CuSO4.5H2O and 170 g/L potassium sodium tartrate (KNaC4H4O6.4H2O). The pH of the prepared solution was adjusted to 12.5 using 50 g/L of NaOH. An appropriate amount of 150–200 mL of HCHO (37 vol%) was added dropwise to the abovementioned solution and magnetically stirred at 500 RPM. By controlling the concentration, the pH value, and the temperature of the solution at room temperature, the autocatalytic electroless Cu coating process on the surface of functionalized MWCNTs and Si3N4 particles started spontaneously and completed within 30–40 min. Table 1 lists the electroless bath composition and conditions. The obtained Cu-coated/MWCNTs and Cu-coated/Si3N4 particles were repeatedly centrifuged at 3,000 RPM for 5 min, followed by decantation of the supernatant; then, they were washed with double-distilled water, centrifuged again, dried under vacuum at 60°C, and then stored for further investigations. The abovementioned process was repeated for fabricating all the samples with different compositions. The yield of Cu-coated MWCNTs and Si3N4 particles was estimated from the differences in the weight of MWCNTs and Si3N4 before and after the coating process.
The obtained CNTs–xSi3N4/Cu nanocomposites were divided into two groups for processing by consolidation with sintering, as listed in Table 2. The samples of the first group were cold-pressed at 600 MPa in a 12.50-mm diameter uniaxial die, followed by heating in a tube furnace under argon (Ar) gas at 850°C for 90 min, according to the heating cycle presented in Figure 1, based on preliminary findings reported in our previous studies (Daoush et al., 2020). In brief, the samples were first heated at 120°C for 30 min at a slow heating rate of 2°C/min to remove any water content trapped inside the samples. In the second stage, the dried samples were heated up to 425°C for 30 min at a heating rate of 2°C/min to degas any trapped gas in the pores inside the samples. The samples were then heated again in the third stage at a heating rate of 5°C/min to start the sintering process at 850°C for 90 min. After that, the sintered samples were cooled under an argon atmosphere. The second group of samples was spark plasma sintered in a cylindrical graphite die with an inner diameter of 15 mm using SPS equipment, model Dr. Sinter 515S SPS (SPS Syntex Inc., Kanagawa, Japan). A high pulsed electrical current was passed through the graphite die containing an appropriate amount of the CNTs–xSi3N4/Cu nanoparticle powder. Heat is thus generated, and the sintering process is started in few seconds. The powders of the CNTs–xSi3N4/Cu nanoparticle samples were sintered at 850°C, with a pulse duration of 2.8 m, a pulse on–off sequence of 12:2, a holding time of 1 min, heating profiles ranging from 50/min to 250/min, and a compaction pressure of 50 MPa simultaneously with heating (Daoush et al., 2009). Figure 2 illustrates a schematic diagram of the SPS apparatus.
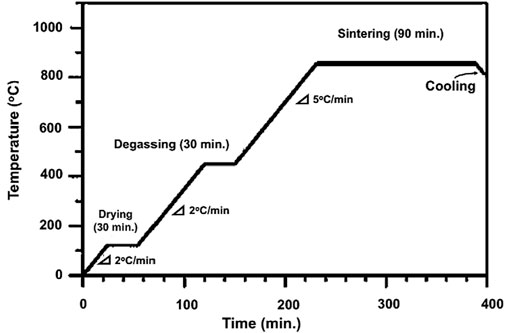
Figure 1. Heating cycle of the powder metallurgy sintering process of CNTs–xSi3N4/Cu nanocomposites.
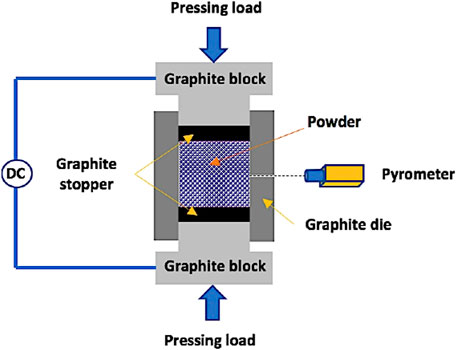
Figure 2. Schematic diagram of the SPS apparatus used in the fabrication of CNTs–xSi3N4/Cu nanocomposites.
The dimensions of the compacts were measured after sintering to evaluate the sintering process by calculating the shrinkage. To assess the sintering process, we used a dial gauge micrometer of 10−3 mm sensitivity to measure the changes in the dimensions of each sample.
The obtained specimens were mounted and grounded using SiC papers with grit sizes of 1,200, 2,000, 3,000, and 4,000, followed by polishing with 0.3 µm diamond paste. The microstructure was then examined using a scanning electron microscope, model Quanta 450 FEG, and a field emission scanning electron microscope, model JEOL JSM-7600F, equipped with an EDX analysis unit. A transmission electron microscope, model JEOL JEM-145 1011, operated at an acceleration voltage of 300 kV, was used to determine the size, shape, and surface morphology of the investigated MWCNTs and Cu-coated MWCNTs. The volume fractions of the reinforcement particles and the metal matrix were calculated from two-dimensional cross-sections by averaging the reinforcement content and metal matrix volume fraction across five micrographs for each polished sample, using an image analysis program (Matrox Inspector 2.1). In addition, crystalline phase identification of the investigated samples was performed using the Bruker D8 discover XRD model.
The theoretical densities of the sintered samples were calculated using the rule of mixtures (ROM) as represented in Equation 1
where ρ Si3N4, ρ m, and ρ CNTs are the densities of the Cu matrix, Si3N4, and CNT dispersed phases, respectively; and VCu, VSi3N4, and VCNTs are the volume fraction of the Cu matrix, Si3N4, and CNT dispersed phases, respectively.
The densities of the obtained sintered samples were determined by measuring Archimedes’ densities according to the ASTM B962-23 standard test using double-distilled water as a floating liquid and applying Equation 2
where Wair and Wwater are the weights of the specimen in air and water, respectively.
The relative densities of the sintered samples were calculated by determining the ratio of the actual density ρr, obtained using the Archimedes’ method, to the theoretical density ρth, using Equation 2
The CTE was determined by the thermomechanical analysis technique, according to the ASTM E831-19 standard test, by measuring the change in the transverse dimensions of the specimen as a function of the change in temperature. The experiment was conducted by heating the specimen continuously up to 200°C, the change in the dimension was measured using a digital micrometer, and the CTE was calculated using Equation 4
where α is the CTE; ΔT is the temperature interval, equal to T − To; and To is the room temperature (∼295 K). ε = ΔL/Lo is the relative change in the dimension of the specimen under investigation, where ΔL is the expansion of the specimen due to heating during the test. ΔL = L- Lo, where Lo is the original length.
The effect of the addition of the CNTs and Si3N4 contents in the theoretical values on the CTEs can be calculated by the ROM using Equation 5
where α CNT, α Si3N4, and α Cu are the CTE of CNTs, Si3N4, and Cu, respectively, and V CNT, V Si3N4, and VCu are the volume fractions of the CNTs, Si3N4, and Cu, respectively.
3 Results and discussion
3.1 FT-IR spectroscopy of acid-functionalized CNTs
The CNTs under investigation were heat-treated, followed by chemical treatments with the (HNO3/H2SO4) acid mixture to introduce active functional groups on the inert graphitic surfaces. The FT-IR spectrum of the heat treatment, followed by chemical treatment of CNTs by acid functionalization, is represented in Figure 3. It was revealed that the infrared spectrum indicates the predominated characteristic bands of different chemical bonds of its graphitic structure. The first one appears as a broad band (at 3,400 cm-1) due to the intermolecular hydrogen bonding of O–H in alcohols and carboxylic acids. The second type of bonding is the C–H bond in the aldehyde CHO group, which appeared at 2,910 and 2,840 cm-1. The third one is the vibration band of the carboxylic group, which was detected as a weak band of C=O stretching mode at 1,750 cm-1. The fourth functional group is the C=C bond, which was detected as a stretching band at 1,650 cm-1; however, the fifth type of band is the stretching bands of the N–O group at 1,550 cm-1 and 1,310 cm-1, indicating the presence of the nitro (NO2) group due to the functionalization process by the (HNO3/H2SO4 acid oxidation mixture) graphitic backbone of the carbon skeleton of the CNTs. In addition, the band (at 1,410 cm-1) is assigned to the bonds of the functional group C–O–C. The C–O group of phenols was present at 1,100 cm-1. The phenyl rings are also detected by two bands (at 924 cm-1 and 822 cm-1) (Tadjine et al., 2022; Ribeiro et al., 2022; Chevallier et al., 2022; Dai et al., 2007; Geeth et al., 2022; Daoush and Imae, 2015; Daoush and Imae, 2012). It was mentioned in the literature that the main surface oxidation of the graphene structure occurred at the de-capped ends of the CNT segments introducing carboxylic groups. However, the aldehydic, ketonic, and phenolic groups were introduced at the sidewall of CNTs due to the oxidation of the conjugated double bonds and the aromatic rings in the graphene chain. This is a characteristic feature of MWCNTs and serves as the backbone structure for CNTs. In addition, the substitution of a hydrogen atom in the hydrocarbon chain of CNTs with a hydroxyl group is reflected in the FT-IR spectrum as absorption bands corresponding to O–H and C–O stretching vibrations (Tadjine et al., 2022; Omori, 2000). The incorporation of oxide-bearing functional groups, such as hydroxide, carboxylic, and ketonic groups, onto the graphitic structure of CNTs is key to enhancing the formation of a uniform coating layer on their surface, providing good results in terms of the growth of nanoparticles on the graphitic surface (Daoush et al., 2009; Chevallier et al., 2022; Dai et al., 2007; Geeth et al., 2022; Daoush and Imae, 2015; Daoush and Imae, 2012).
3.2 Synthesis and characterization of Cu and CNTs–xSi3N4/Cu nanoparticles
Figures 4a,b show high-resolution SEM images at high magnifications of the as-received CNTs and the CNTs after being coated with electroless copper deposition. It was observed from the results that the investigated CNTs have an inner diameter of 4–5 nm and an outer diameter of 19–20 nm. Figure 4c represents a high-resolution TEM image of the CNTs after functionalization and coating with electroless Cu deposition. It was observed from the results that CNTs were decorated with the deposited Cu nanoparticles. Figures 4d–f show high-resolution SEM images of the uncoated and coated Si3N4 particles by Cu, where the Si3N4 particles have a cubic shape with a particle size of 300–700 nm. Si3N4 particles were completely encapsulated with the Cu nanoparticles, as shown in Figure 4f. By coating CNTs and Si3N4 particles using the electroless deposition technique, ultrafine copper particles were deposited onto their surfaces. The deposited copper nanoparticles adhered well to the surface of CNTs and Si3N4 particles, resulting in a uniformly coated copper layer, which can be observed.
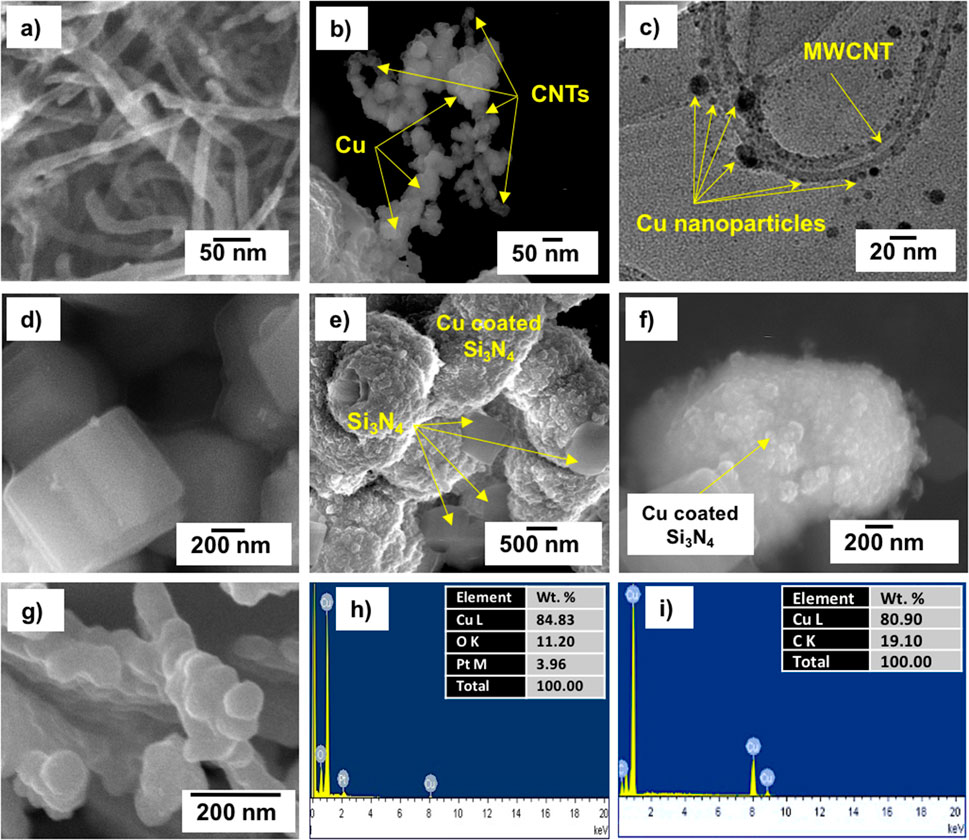
Figure 4. High-resolution FESEM and HRTEM images; the EDS compositional analysis of the investigated nanoparticles: (a) uncoated CNTs, (b) Cu-coated CNTs, (c) TEM image of Cu-coated CNTs, (d) uncoated Si3N4 particles, (e) (f) Cu-coated Si3N4, and (g) the pure Cu nanoparticles; (h) EDS analysis of Cu nanoparticles; and (i) EDS analysis of Cu-coated CNTs by the electroless chemical reduction method (platinum is the background of the coated layer by sputtering).
Pure Cu nanoparticles were successfully synthesized by electroless chemical reduction in aqueous media as a reference sample of the prepared CNTs–xSi3N4/Cu nanocomposites. It was observed from the results presented in Figure 4g that the deposited Cu nanoparticles have a spherical shape with a particle size range of 50–200; however, some large Cu nanoparticles were also observed, resulting from the agglomeration of fine Cu nanoparticles due to their high surface area-to-volume ratio. In addition, the EDX compositional analysis indicated two types of peaks of the deposited Cu nanoparticles (see Figure 4H); the main high-intensity peak indicated the presence of Cu, while a low-intensity peak represented the presence of a small amount of oxygen, which appeared due to the combination of oxygen with Cu in the aqueous media of the electroless deposition bath. This oxygen content can be removed during the sintering process under a controlled atmosphere. Figure 4i represents the EDX elemental compositional analysis of the Cu-coated CNTs by electrodeposition. It was revealed that the high-intensity peak represents the deposited Cu element, and the low-intensity peak represents the carbon element of the CNTs.
3.3 Microstructure investigations
Figure 5a shows photographic images of the prepared CNTs–xSi3N4/Cu nanocomposites by powder metallurgy and spark plasma sintering processes. It was observed from the results that the samples with low Si3N4 content, prepared by the powder metallurgy technique at 850°C, exhibited less swelling and porosity due to their good sinterability. However, by increasing the Si3N4 content in the CNTs–xSi3N4/Cu nanocomposites, the porosity and the swelling regions are increased, especially in the sample containing 4 wt% and 5 wt% of Si3N4, as shown in the SEM images of the microstructure presented in Figure 5c which is discussed later. The formation of the swelling and porosity content in the samples containing high Si3N4 content may be due to the low wettability between the Si3N4 ceramic particles and CNTs and the Cu metal matrix. This limited wettability can enhance the formation of de-binding regions and agglomeration of some Si3N4 particles and/or CNTs in the interface between the Si3N4 ceramic particles and/or CNTs with the Cu metal matrix (see Figures 5a,c). On the other hand, it was observed from Figure 5b that the CNTs–xSi3N4/Cu nanocomposites samples prepared by spark plasma sintering have higher sinterability and low dimensional shrinkage than the CNTs–xSi3N4/Cu nanocomposites samples prepared by the powder metallurgy technique. The good sinterability of the SPS samples is due to the simultaneous pressing and heating in a short time, which consolidated the samples quickly, retained the fine grains of the nanostructure, and inhibited the grain growth.
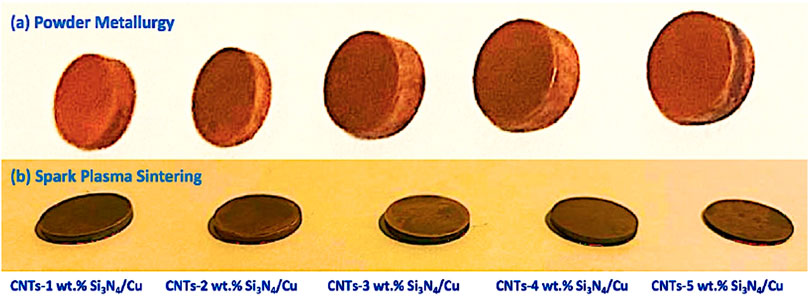
Figure 5. Photographical images of the fabricated CNTs–xSi3N4/Cu nanocomposites by (a) powder metallurgy and (b) spark plasma sintering processes.
Figure 6 shows the SEM images and BSE mode with low and high magnifications of the microstructure for the prepared CNTs–xSi3N4/Cu sintered at 850°C by the powder metallurgy technique. It was observed from the microstructure that Si3N4 and CNT reinforcements are mainly distributed in the Cu matrix. However, some agglomerated regions of Si3N4 and CNTs and pore areas are also observed in the Cu matrix. It may be due to the low wettability of Si3N4 and CNTs with the Cu matrix and the contribution of the high-volume fraction of the ultrafine Si3N4 particles and CNTs in the Cu matrix. On the other hand, Figure 7 shows the SEM microstructural images and BSE mode with low and high magnifications of the prepared CNTs–xSi3N4/Cu nanocomposites sintered by spark plasma process under 50 Mpa at 850°C for 1 min. It was observed that Si3N4 and CNT reinforcements are homogeneously distributed in the Cu matrix, and the microstructure is better than that of the CNTs–xSi3N4/Cu sintered samples prepared by the conventional powder metallurgy technique. It may be due to the optimization of the sintering conditions of spark plasma sintering in a short sintering time of 1 min, which retains the nanostructure of the prepared CNTs–xSi3N4/Cu nanocomposites. Figures 6c, d represent the dispersion and homogeneous distribution of the CNTs in the Cu matrix. In addition, the microstructure of the sintered composites fabricated by SPS represents a better homogeneous distribution of CNTs in the Cu matrix than those fabricated by the conventional powder metallurgy process. This is because the prolonged sintering time in the powder metallurgy process allows the formation of agglomerations and grain growth. However, the short sintering time of the SPS process retains the nanostructure and prevents the CNT agglomeration and grain growth. In addition, it inhibits any carbide formation or CNT dissociation that can be expected to form during the 90-min prolonged time of sintering via the powder metallurgy technique. The long sintering time allows for enhanced CNT dissociation due to carbide formation between the silicon component of Si3N4 with carbon component of CNTs, which, in turn, affects the physical properties of the CNTs–xSi3N4/Cu nanocomposites. Figures 8a, b show the optical micrographs of the produced CNTs–4%Si3N4/Cu composites fabricated using conventional powder metallurgy and SPS techniques. It was observed from the microstructure that the reinforcement particles are homogeneously distributed in the Cu matrix; however, some agglomerated areas and pore regions are observed, which are expected to affect the physical and thermal properties. Figures 8c, d show optical micrographs of different regions in the sintered CNTs–xSi3N4/Cu nanocomposites by SPS. It was observed from the results that Cu-rich zones appeared due to the sintering at high direct current during the consolidation process. The high pulsed electric current density applied at 2.8 m through the powder sample during the SPS process generates the required quantity of heat at 850°C, which intrinsically influences the sintering kinetics and the densification mechanisms of the CNTs–xSi3N4/Cu powder (Daoush et al., 2009; Dong et al., 2021; Orru et al., 2009b; Munir et al., 2006; Tokita, 1999). As reported in the literature, the high electric current density applied to the powdered sample is the main driving force of heat generation during the SPS process. Four types of heating sources can be generated: the first type is formed due to the dielectric breakdown of the oxide layers on the surface of the Cu nanoparticles. The second one is formed based on the plasma generation between the Cu and CNTs and Si3N4 reinforcement particles. The third is formed due to overheating caused by an increase in the current density at the contact between CNTs, Si3N4, and Cu particles. Finally, the fourth is the activation of electromigration and electroplasticity through the sample (Daoush et al., 2009; Tokita, 1999; Omori, 2000; Okazaki, 2000; Groza and Zavaliangos, 2000; Ye et al., 2006; Yanagisawa et al., 2003). A previous work reported that as a result of the SPS process of the Si3N4/Cu composite, diffusion of Si atoms in Si3N4 facilitated the formation of the copper silicide (CuSi) interface between the two constituents during sintering, creating strong chemical bonding and improving sinterability and conductivity (Wu et al., 2024).However, according to the Cu–C phase diagram, the solubility of C in Cu is less than 0.04%, and this value is achieved only at a high temperature of 1,084°C. This means that the sintering of a mixture of Cu powder and carbon-based reinforcements such as CNTs will give rise to a composite with pure interfaces between the matrix and reinforcements, especially at a sintering temperature less than 1,000°C (Veillere et al., 2020).
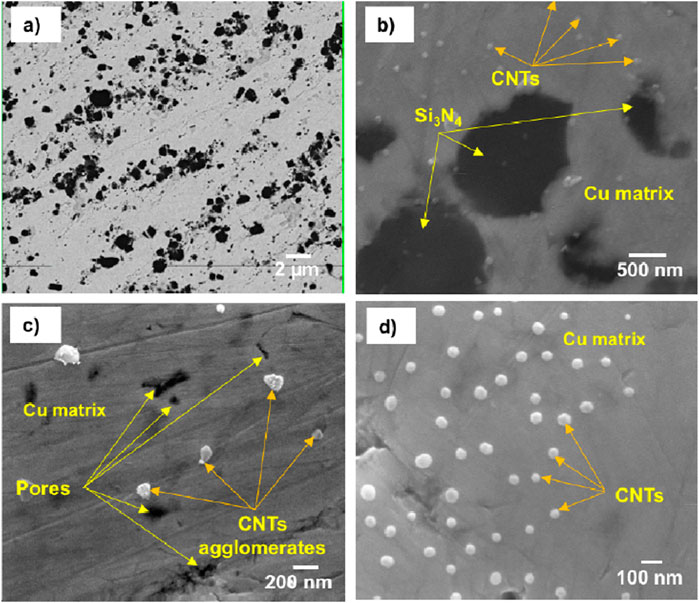
Figure 6. FESEM/BSE mode microstructure images with low and high magnifications of the fabricated CNTs–4 wt.%Si3N4/Cu sintered at 850°C by the powder metallurgy technique: (a) BSE mode; (b), (c), and (d) SE mode.
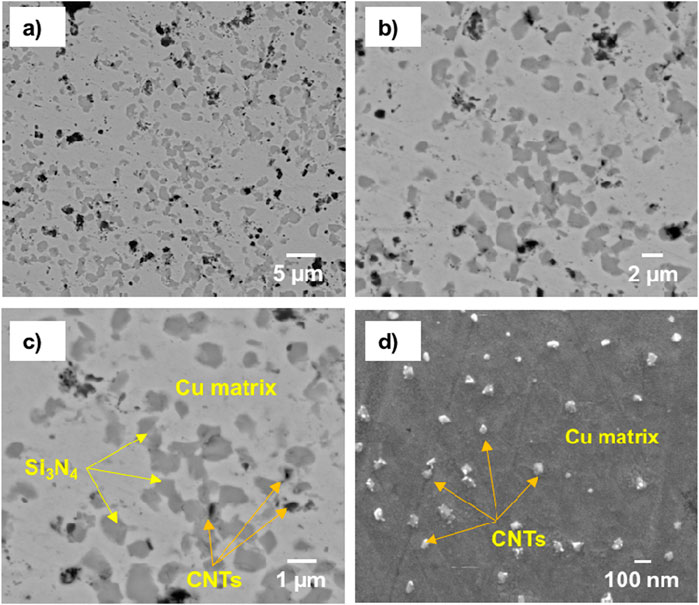
Figure 7. FESEM/BSE mode microstructure images with low and high magnifications of the produced CNTs–3 wt.%Si3N4/Cu sintered by the spark plasma sintering technique: (a), (b), (c) BSE mode; (d) SE mode.
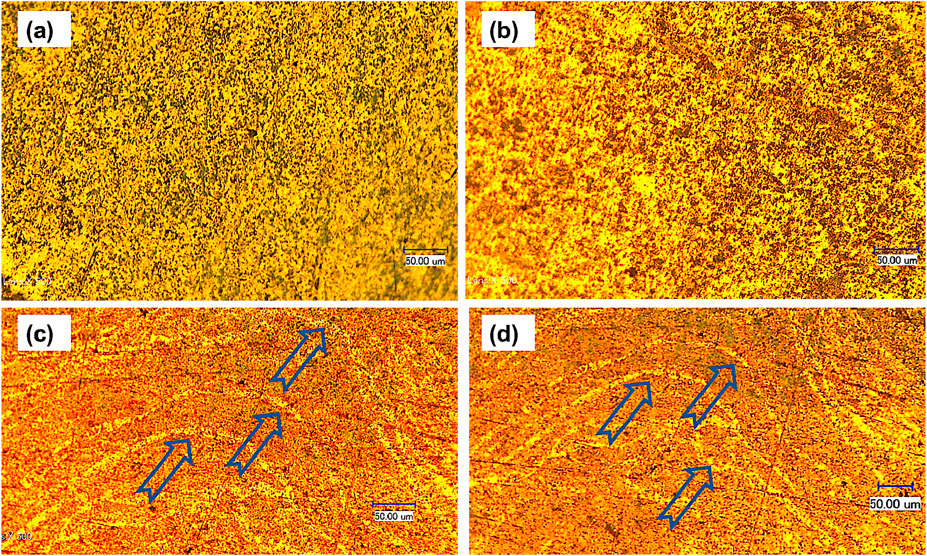
Figure 8. Optical micrograph of the sintered CNTs–4wt.%Si3N4/Cu nanocomposites (a) by conventional powder metallurgy and (b) SPS; (c) and (d) the sintered CNTs–5wt.%Si3N4/Cu by SPS. Arrows represent the copper-rich zone during sintering at high direct current during the process.
Figures 9, 10 show mapping, the secondary electron scanning images (FESEM/SE mode), and the energy dispersive X-ray spectroscopy (EDX) elemental compositional analysis of the fabricated CNTs–xSi3N4/Cu nanocomposites sintered by powder metallurgy and SPS, respectively. It was observed from the results that there is a homogeneous distribution of the elements composed of the Si3N4 particles and the CNTs in the Cu metal matrix. In addition, the reinforced CNTs and Si3N4 particles are dispersed in the Cu matrix without the formation of any segregations or agglomerations, and no foreign elements are detected apart from Si, N, C, and Cu, which emphasizes the high purity of the raw materials used to prepare CNTs–Si3N4/Cu nanocomposites and the optimization of the conditions during the sintering processes (Daoush et al., 2020). It was observed from the mapping that elemental silicon is dispersed in the Cu matrix. This result is matched with previous reports that mentioned that silicon is diffused in the Cu matrix by forming copper silicide (CuSi) and can enhance the interfacial bonding between Si3N4 reinforcement particles and the Cu matrix (Wu et al., 2024). It was also observed from the results that some voids and pores are formed in the samples prepared by the powder metallurgy technique (see FESEM/SE mode image in Figure 9). The reason behind that is the pulling out of some CNTs and Si3N4-reinforced particles from the surface of the Cu matrix during the grinding and polishing technique, which indicates the poor adhesion between the Cu matrix and CNTs and Si3N4-reinforced particles for the samples prepared by the conventional powder metallurgy technique. On the other hand, the ground and polished samples prepared by the SPS technique did not exhibit any voids or porosity, which revealed the strong adhesion between CNTs and Si3N4-reinforced particles. These adhesion forces affect the physical properties, such as density and CTE, as discussed in the next section.
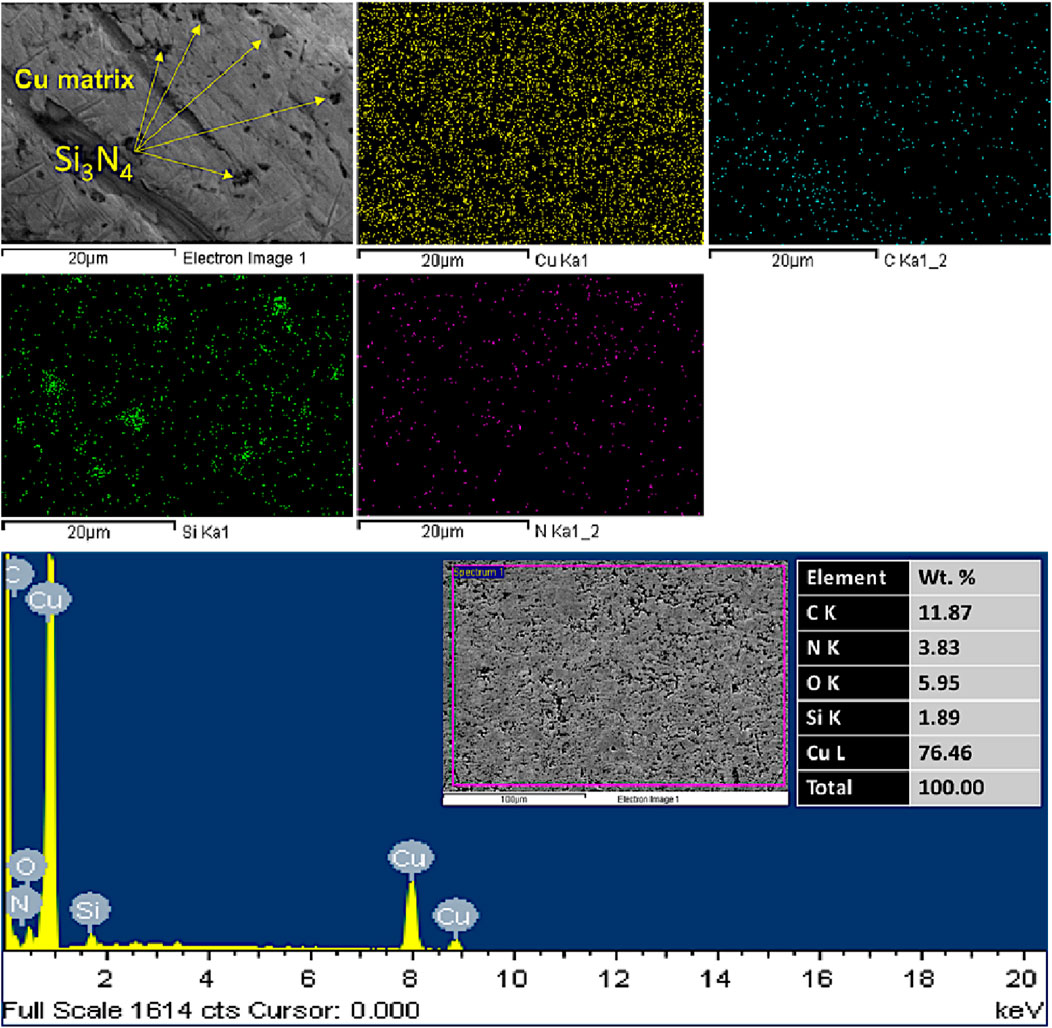
Figure 9. Mapping, FESEM/SE mode, and EDX compositional analysis of the fabricated CNTs–3wt.%Si3N4/Cu sintered by the powder metallurgy technique for 90 min at 850°C.
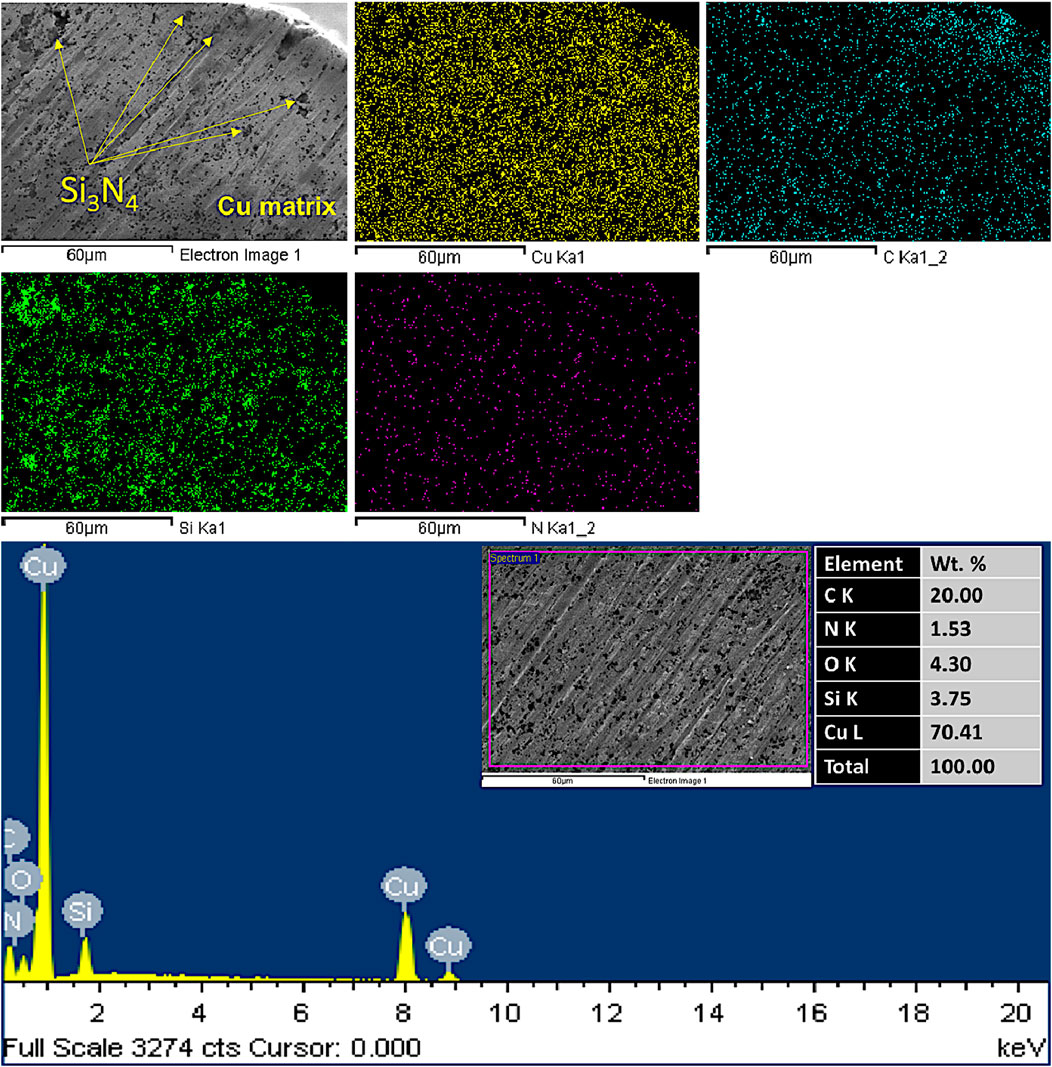
Figure 10. Mapping, FESEM/SE mode, and EDX compositional analysis of the fabricated CNTs–4wt.%Si3N4/Cu by spark plasma sintering at 850°C for 1 min.
3.4 XRD phase identifications
Figure 11a shows the XRD pattern of the investigated CNTs. The diffraction peaks were identified at angles of 26°, 43°, 53°, and 79°, corresponding to 002, 100, 004, and 110 crystalline planes, respectively, as per JCPDS No. 96-101-1061. Figure 11b shows the XRD pattern of the as-prepared pure reference Cu nanoparticle sample by the electroless deposition process and the sintered sample by the powder metallurgy technique. It was revealed from the results that the observed peaks are due to the presence of the face-centered cubic (FCC) structure of the deposited Cu nanoparticles, corresponding to (111), (200), and (220) crystalline planes, in accordance with JCPDS No. 04-0836. The Scherrer crystallite size of the produced copper nanoparticles, calculated by the X-ray line broadening method using the mathematical formula of Scherrer’s equation (D = 0.9 λ/B cos θ), is estimated at 1.8 × 102 Å (Daoush et al., 2020). In addition, a very low-intensity peak is observed at a diffraction angle of 26.3o, which is due to the presence of the crystalline planes (002) of the reinforced CNTs, as identified by JCPDS No. 65-6212. In addition, a low-intensity peak of the (111) crystalline plane at 2 θ value of 37o corresponds to Cu2O, as identified by JCPDS No. 65-3288. Cu2O may be formed due to the presence of a small amount of trapped oxygen in the nanoparticles fabricated by the electroless deposition process in the aqueous solution, which can interact with the Cu nanoparticles and form Cu2O. This peak of Cu2O disappeared as a result of the sintering process of Cu nanoparticles. It was reported in the literature that by decorating the surface of CNTs with CuO nanoparticles and taking advantage of the strong wettability between CuO and the Cu matrix, CuO nanoparticles on the surface of CNTs are reduced to Cu. High-density interfacial dislocations and interfacial disordered areas are formed between the Cu matrix and CNTs, thus forming a strong interfacial bond (Xia et al., 2021).
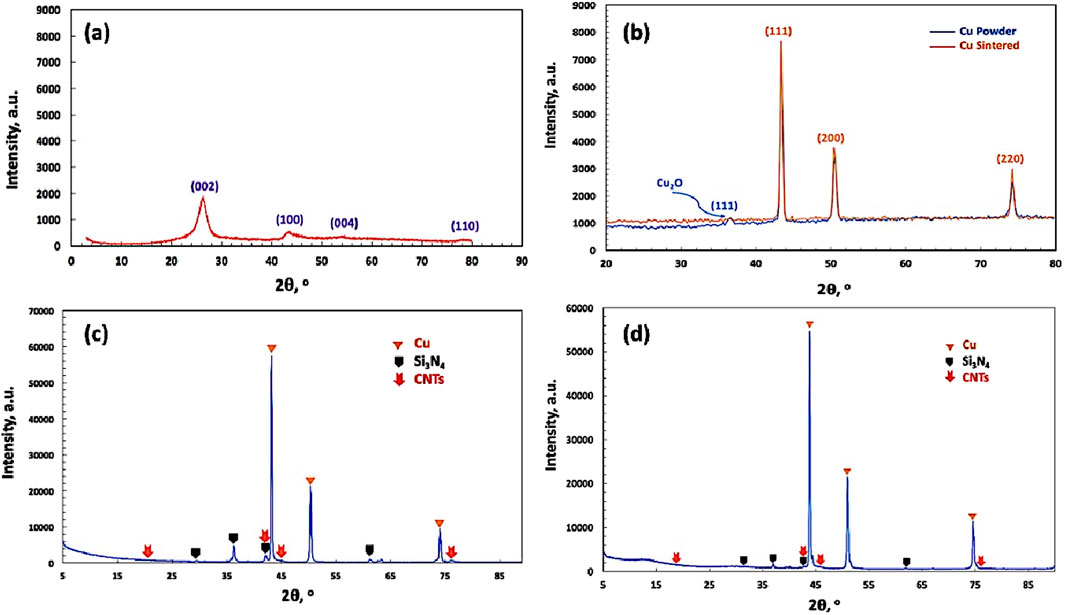
Figure 11. XRD pattern of the investigated (a) CNTs, (b) deposited Cu nanoparticles, (c) CNTs–3wt.% Si3N4/Cu sintered by the powder metallurgy technique, and (d) CNTs-4 wt.% Si3N4/Cu sintered by the spark plasma technique.
Figures 11c,d show the XRD pattern of CNTs–xSi3N4/Cu samples sintered by powder metallurgy and spark plasma sintering processes. It was observed from the results that the samples fabricated by both methods are mainly composed of CNTs, Cu, and Si3N4 crystalline phases. It was also observed that no foreign phases were detected in both sintered samples (Daoush et al., 2009; Singh and Gautam, 2019; Ahmed et al., 2016; Uddin et al., 2010).
3.5 Sintering and density
Figure 12a shows the relationship between the volume fractions of the Si3N4 dispersed phase in the Cu matrix, which is determined by image analysis of the microstructures of the two-dimensional cross-section for the prepared CNTs–xSi3N4/Cu nanocomposite samples and their weight percent. It was observed from the results that by increasing the weight percent of Si3N4 particles, the volume fraction is linearly increased. The volume fractions, obtained from the image analysis of the microstructure for each composition, were used to calculate the expected theoretical density and CTE of the corresponding compositions. This was achieved by applying the ROM to evaluate the correlation between the physical properties and the addition of CNTs and Si3N4 reinforcement particles in the Cu matrix of the produced CNTs–xSi3N4/Cu sintered nanocomposites (Singh and Gautam, 2019; Ahmed et al., 2016; Uddin et al., 2010).
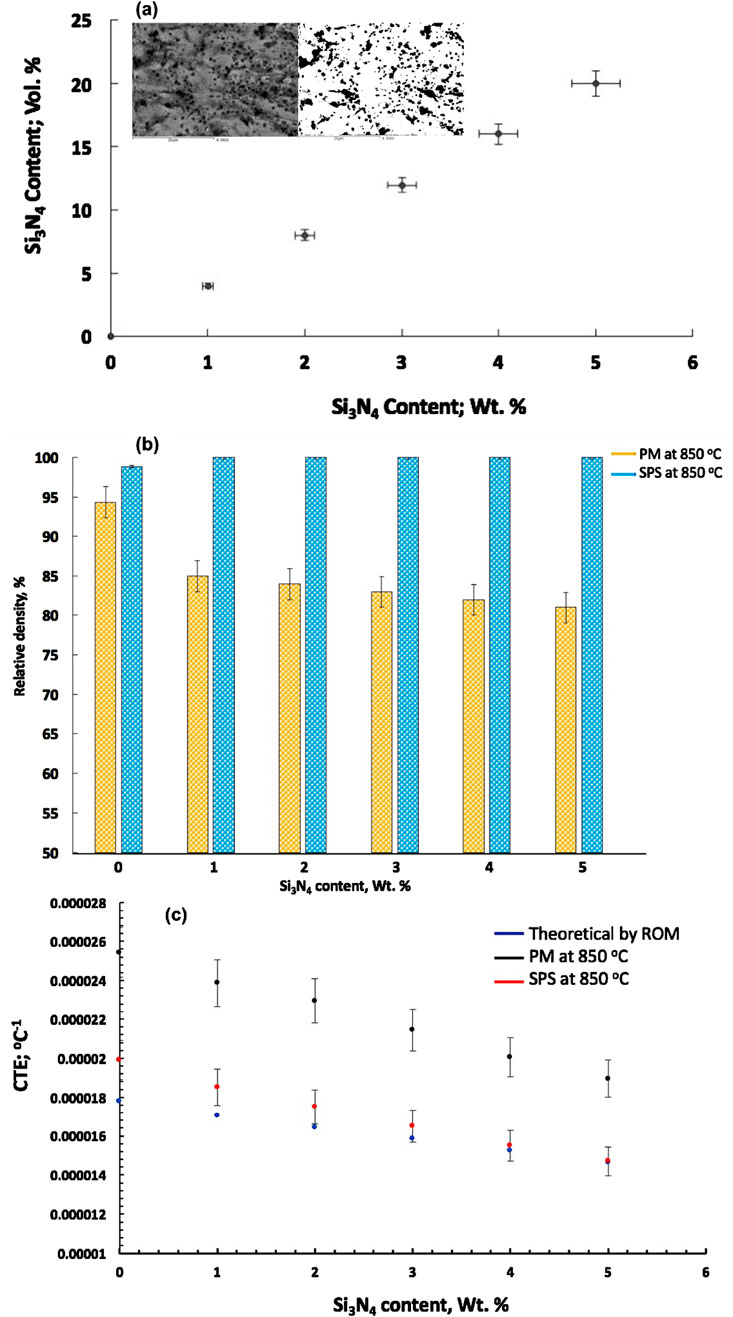
Figure 12. (a) Relationship between the weight and the volume percentages of the Si3N4 dispersed phase in the Cu matrix, depending on the microstructure investigation by image analysis, (b) relative sintered density, and (c) theoretical and measured CTE values of the produced CNTs–xSi3N4/Cu nanocomposites by powder metallurgy and SPS processes.
Figure 12b shows the relative sintered densities of the prepared CNTs–xSi3N4/Cu nanocomposites by the powder metallurgy technique and the SPS process correlated with the addition of different weight percentages of Si3N4. It was observed from the results that the reference pure Cu compacts, prepared by the powder metallurgy process at 850°C, exhibited a relative sintering density of 94%, which was higher than that of the reinforced CNTs–xSi3N4/Cu nanocomposites. By increasing the Si3N4 content, the sintered density decreased to reach 85% in the case of CNTs–1wt% Si3N4/Cu nanocomposites and 81% in the case of CNTs–5wt% Si3N4/Cu nanocomposites. The reason behind the low values of the relative sintered density for the produced CNTs–xSi3N4/Cu nanocomposites by the powder metallurgy technique is that the sintering process at 850°C is not sufficient to reach the optimum sinterability conditions of the compacts. It was also revealed that by increasing the Si3N4 reinforcement particle content, the density of the CNTs–xSi3N4/Cu nanocomposites can be decreased (Daoush et al., 2009; Singh and Gautam, 2019; Ahmed et al., 2016; Uddin et al., 2010). It may be due to the low density of Si3N4 (3.44 g/cm3) and CNTs ((1.7 g/cm3) reinforced particles than the Cu matrix itself (8.9 g/cm3). On the other hand, it was observed from the obtained data of the reference pure Cu sample and CNTs–xSi3N4/Cu nanocomposite samples prepared by SPS that the sintered density approaches the theoretical value, and the relative sintered density reaches 100%. It is because the solid-state sintering mechanism enhances the binding and high sinterability of the CNTs-–/Cu nanocomposite powder at a temperature of 850°C and a pressure of 5 MPa during the sintering process. The SPS process achieves full densification of the material in just 1 min, even with a shorter sintering time (Singh and Gautam, 2019; Ahmed et al., 2016; Uddin et al., 2010; Yin et al., 2023).
3.6 Coefficient of thermal expansion
Figure 12c shows the effect of the addition of CNTs and Si3N4 contents on the theoretical values of the CTEs, which were calculated by the ROM according to Equation 5. It was observed from the results that the ROM model predicts a decrease in the CTEs of the CNTs–xSi3N4/Cu nanocomposites with an increase in the Si3N4 content. This directly relates to the lower CTE values of Si3N4 and CNT reinforcement particles compared to the Cu matrix. Additionally, the inclusion of the porosity in the samples after sintering contributes to this effect. It was observed from the obtained data of the calculated values of CTEs by ROM that the CTE decreased linearly with an increase in the content of Si3N4 reinforcement particles up to 5 wt% and CNTs of 0.1 wt%. The reason behind that is the contribution of Si3N4 reinforcement particles in CNTs–xSi3N4/Cu nanocomposites, which have one-fourth of the CTE value of the Cu metal matrix itself (Yin et al., 2023; Massalski et al., 1995; Lee and Rainforth, 1994). In addition, CNTs have become a popular additive material for reducing CTEs of CNTs–xSi3N4/Cu nanocomposites (Bakshi et al., 2010; Tjong, 2013; Uddi et al., 2009; Deng et al., 2008; Liu et al., 2012; Liu et al., 2014; Shin et al., 2016; Sharma and Sharma, 2016; Yang et al., 2016) because of the very low or even negative CTE value of CNTs, in the range of -2x10-5–0.5 × 10−5 K−1, which depends on the characteristics and the properties of the CNTs used in the fabrication process (Shirasu et al., 2017).
Figure 12c also shows the measured CTE values of the CNTs–xSi3N4/Cu nanocomposites prepared by powder metallurgy and SPS processes. It was observed from the results that CNTs–xSi3N4/Cu nanocomposite samples prepared by the SPS process have lower CTE values, approaching the theoretical values predicted by the ROM. The decrease in the CTE values is due to the good sinterability of the samples, which were obtained by optimizing SPS conditions with a shorter sintering time of 1 min than that of the powder metallurgy process of 90 min. Decreasing the sintering temperature time can control and retain the fine grains of the nanostructure by inhibiting the nanoparticle coalescence of the obtained CNTs–xSi3N4/Cu nanocomposite samples, which improves their physical and thermal properties (Yoo et al., 2023; German, 2023).
4 Conclusion
CNTs–Si3N4/Cu reinforced with different silicon nitride contents of 1, 2, 3, 4, and 5 wt% are fabricated by electroless copper deposition, followed by consolidation with powder technology and spark plasma sintering processes. The graphitic surfaces of CNTs are treated by acid-functionalization to improve their dispersion during the electroless deposition technique. The FT-IR analysis indicated that some functional groups were introduced on the functionalized CNTs, such as carboxylic, ketonic, and hydroxyl groups. The microstructure, density, and CTE of the obtained (CNTs–xSi3N4/Cu) sintered samples were investigated to evaluate their physical properties. The distribution of CNTs and Si3N4 reinforcement particles in the Cu matrix was improved via the electroless coating and sintering process by SPS. For Cu matrix composites reinforced by CNTs and Si3N4, the homogeneous dispersion of CNTs or Si3N4 and efficient Cu–CNTs and Cu–Si3N4 interfacial bonding are the major challenges for the efficient use of CNTs and Si3N4 in the Cu matrix. By decorating the surface of CNTs and Si3N4 with Cu nanoparticles and taking advantage of strong wettability between Cu-coated CNTs and Cu-coated Si3N4 with the Cu matrix, uniform dispersion of CNTs and Si3N4 is realized through particle coating by electroless deposition. It was expected that high-density interfacial dislocations and interfacial disordered areas are formed between the Cu matrix and CNTs and Si3N4 reinforcement particles, thus forming strong interfacial bonding, and interfacial shear stress between the Cu matrix and CNTs or Si3N4 reinforcement particles is improved due to the extrusion effect of Cu nanoparticles on the surface of CNTS or Si3N4. Consequently, the Cu matrix composites simultaneously improve the physical and mechanical properties. By using the acid functionalization of CNTs and the electroless coating of CNTs and Si3N4 reinforcement particles, the particles are encapsulated by Cu nanolayers, which help in the distribution of the CNTs and Si3N4 in the matrix and decrease the (CNT–CNT or Si3N4–Si3N4 or CNT–Si3N4) particle–particle interactions, thus decreasing the segregation and agglomeration of the reinforcement particles in the Cu metal matrix. The sintering process of powder metallurgy takes a prolonged time (90 min) to start the different steps of the sintering mechanism (surface diffusion, neck growth, pore elimination, and bulk diffusion) between the constituents of the compacted powders. However, the consolidation of the powder by SPS takes a shorter time (1 min) than that of the powder metallurgy technique, which helps in retaining the nanostructure of the sintered materials and, as a result, improves physical properties, such as density and the coefficient of thermal expansion. The microstructure investigation of the CNTs–xSi3N4/Cu nanocomposites, which were prepared by the powder metallurgy technique, shows high porosity content due to the low sintering temperature of 850°C, which may lead to partial sintering, voids, and swelling formation in the sample after sintering. On the other hand, CNTs–XSi3N4/C nanocomposites prepared by the SPS process have very low porosity content with high relative density that approaches 100%. In addition, the relative sintering density of the CNTs–xSi3N4/Cu nanocomposites prepared by the powder metallurgy technique decreases with an increase in the Si3N4 reinforcement particle content in the Cu matrix. However, the CNTs–xSi3N4/Cu nanocomposite samples with different Si3N4 reinforcement particle content prepared by the SPS at 850°C are fully sintered, with the relative sintered density approaching 100%. The CTE values of both CNTs–xSi3N4/Cu nanocomposite groups prepared by powder metallurgy and SPS were decreased by increasing the Si3N4 reinforcement particle content. In addition, the CNTs–xSi3N4/Cu nanocomposites prepared by the SPS have CTE values approaching the theoretical values predicted by the ROM, especially the samples that contain higher wt% of Si3N4 reinforcement particles. Our work introduces a new nanocomposite as an appropriate candidate material for thermal management and heat sink applications.
Data availability statement
The raw data supporting the conclusions of this article will be made available by the authors, without undue reservation.
Author contributions
WD: Conceptualization, Data curation, Formal Analysis, Funding acquisition, Investigation, Methodology, Project administration, Resources, Software, Supervision, Validation, Visualization, Writing – original draft, Writing – review and editing. FI: conceptualization, data curation, Investigation, Validation, Visualization, Writing – review and editing, Writing – original draft. SH: Conceptualization, Investigation, Methodology, Validation, Visualization, Writing – review and editing, and Writing – original draft. EO: conceptualization, Data curation, Investigation, Methodology, Software, Validation, Visualization, Writing – review and editing, and Writing – original draft. RG: Conceptualization, Data curation, Formal Analysis, Investigation, Methodology, Validation, Visualization, Writing – review and editing, Writing – original draft.
Funding
The author(s) declare that financial support was received for the research and/or publication of this article. The authors gratefully acknowledged the Binational Fulbright Commission (program no. N0011696326 G1-00005) in Egypt for supporting this research work. The authors also gratefully acknowledge Brain Korea 21 (BK21) in South Korea for funding and supporting this study.
Acknowledgments
The authors gratefully acknowledge Steve Barlow, professor at San Diego State University, for his assistance with the FESEM work. Also, the authors extend their appreciation to the Deanship of Scientific Research at Imam Mohammad Ibn Saud Islamic University (IMSIU) for funding and supporting this work through Research Partnership Program no RP-21-09-72.
Conflict of interest
The authors declare that the research was conducted in the absence of any commercial or financial relationships that could be construed as a potential conflict of interest.
Publisher’s note
All claims expressed in this article are solely those of the authors and do not necessarily represent those of their affiliated organizations, or those of the publisher, the editors and the reviewers. Any product that may be evaluated in this article, or claim that may be made by its manufacturer, is not guaranteed or endorsed by the publisher.
References
Ahmed, M. A., Daoush, W. M., and El-Nikhaily, A. E. (2016). Fabrication and characterization of copper/silicon nitride composites. Adv. Mater. Res. 5 (3), 131–140. doi:10.12989/amr.2016.5.3.131
Alamusi, N.Hu, Jia, B., Arai, M., Yan, C., Li, J., Liu, Y., et al. (2012). Prediction of thermal expansion properties of carbon nanotubes using molecular dynamics simulations. Comput. Mater. Sci. 54, 249–254. doi:10.1016/j.commatsci.2011.10.015
Arya, R. K., Kumar, R., Telang, A., and Yadav, A. S. (2023). Effect of microstructure on mechanical behaviors of Al6061 metal matrix composite reinforced with silicon nitride (Si3N4) and silicon carbide (SiC) micro particles. Silicon 15, 5911–5923. doi:10.1007/s12633-023-02468-6
Azarniya, A., Sovizi, S., Hosseini, H. R. M., Varol, T., Kawasaki, A., et al. (2017b). Physicomechanical properties of spark plasma sintered carbon nanotube-reinforced metal matrix nanocomposites. Prog. Mater. Sci. 90, 276–324. doi:10.1016/j.pmatsci.2017.07.007
Azarniya, A., Sovizi, S., Rahmani Taji Boyuk, M. R., Varol, T., Nithyadharseni, P., et al. (2017a). Physicomechanical properties of spark plasma sintered carbon nanotube-containing ceramic matrix nanocomposites. Nanoscale 9 (35), 12779–12820. doi:10.1039/c7nr01878a
Bakshi, S. R., Lahiri, D., and Agarwal, A. (2010). Carbon nanotube reinforced metal matrix composites - a review. Int. Mater Rev. 55 (1), 41–64. doi:10.1179/095066009x12572530170543
Balandin, A. A. (2011). Thermal properties of graphene and nanostructured carbon materials. Nat. Mater. 10, 569–581. doi:10.1038/nmat3064
Berber, S., Kwon, Y. K., and Tomanek, D. (2000). Unusually high thermal conductivity of carbon nanotubes. Phys. Rev. Lett. 84, 4613–4616. doi:10.1103/physrevlett.84.4613
Carvalho, O., Miranda, G., Soares, D., and Silva, F. S. (2013). CNT-reinforced aluminum composites: processing and mechanical properties. Ciência and Tecnologia dos Materiais 25 (2), 75–78. doi:10.1016/j.ctmat.2014.03.002
Cheng, Z. L., Ye, F., Liu, Y. S., Qiao, T., Li, J., Qin, H., et al. (2019). Mechanical and dielectric properties of porous and wave-transparent Si3N4–Si3N4 composite ceramics fabricated by 3D printing combined with chemical vapor infiltration. J. Adv. Ceram. 8, 399–407. doi:10.1007/s40145-019-0322-8
Chevallier, C., Bose, S., Hamady, S., Horwat, D., Pierson, J., Boulet, P., et al. (2022). Effect of temperature and D-sorbitol reducing agent content on the structural and optical properties of copper oxide thin films deposited by ultrasonic spray pyrolysis. Thin Solid Films 758, 139435. doi:10.1016/j.tsf.2022.139435
Cui, H. W., Jiu, J. T., Sugahara, T., Nagao, S., Suganuma, K., Uchida, H., et al. (2015). Using the Friedman method to study the thermal degradation kinetics of photonically cured electrically conductive adhesives. J. Therm. Anal. Calorim. 119, 425–433. doi:10.1007/s10973-014-4195-3
Dai, K., Shi, L., Fang, J., and Zhang, Y. (2007). Synthesis of silver nanoparticles on functional multi-walled carbon nanotubes. Mater Sci. Eng. A 465, 283–286. doi:10.1016/j.msea.2007.03.052
Daoush, W., and Imae, T. (2012). Syntheses and characterizations of multi-walled carbon nanotubes-supported palladium nanocomposites. J. Mater. Res. 27, 1680–1687. doi:10.1557/jmr.2012.123
Daoush, W., and Imae, T. (2015). Fabrication of PtNi bimetallic nanoparticles supported on multi-walled carbon nanotubes. J. Exp. Nanosci. 10, 392–406. doi:10.1080/17458080.2013.838703
Daoush, W. M., Alkhuraiji, T. S., Khamis, M. A., and Albogmy, T. S. (2020). Microstructure and electrical properties of carbon short fiber reinforced copper composites fabricated by electroless deposition followed by powder metallurgy process. Carbon Lett. 30, 247–258. doi:10.1007/s42823-019-00093-1
Daoush, W. M., Lim, B. K., Mo, C. B., Nam, D. H., and Hong, S. H. (2009). Electrical and mechanical properties of carbon nanotube reinforced copper nanocomposites fabricated by electroless deposition process. Mater. Sci. Eng. A 513–514, 247–253. doi:10.1016/j.msea.2009.01.073
Darabi, M., Rajabi, M., Junipour, B., and Noghani, M. T. (2018). The effect of sintering temperature on Cu-CNTs nano composites properties produced by PM method. Sci. Sinter. 50 (4), 477–486. doi:10.2298/sos1804477d
Deckert, C. A. (1995). Electroless copper plating: a review, Part II. Plat. Surf. Finish. 82, 58–64.
Deng, C. F., Ma, Y. X., Zhang, P., Zhang, X. X., and Wang, D. Z. (2008). Thermal expansion behaviors of aluminum composite reinforced with carbon nanotubes. Mater Lett. 62 (15), 2301–2303. doi:10.1016/j.matlet.2007.11.086
Dong, Z., Peng, Y., Zhang, X., and Xiong, D.-B. (2021). Plasma assisted milling treatment for improving mechanical and electrical properties of in-situ grown graphene/copper composites. Compos Commun. 24, 100619. doi:10.1016/j.coco.2020.100619
Duan, K., Li, Li, Hu, Y., and Wang, X. (2017). Enhanced interfacial strength of carbon nanotube/copper nanocomposites via Ni-coating: molecular-dynamics insights. Phys. E Low-dimensional Syst. Nanostructures 88, 259–264. doi:10.1016/j.physe.2017.01.015
Ejaz, F., Hwang, L. K., Son, J., Kim, J. S., Lee, D. S., and Kwon, B. (2022). Convolutional neural networks for approximating electrical and thermal conductivities of Cu-CNT composites. Sci. Rep. 12 (1), 13614. doi:10.1038/s41598-022-16867-z
Garay, J. (2010). Current-activated, pressure-assisted densification of materials. Annu. Rev. Mater. Res. 40, 445–468. doi:10.1146/annurev-matsci-070909-104433
Geeth, M., Maury, M., Al-maadeed, S., Muthalif, A., and Sadasivuni, K. (2022). High precision nonenzymatic electrochemical glucose sensing based on CNTs/CuO nanocomposite. J. Electron. Mater. 51, 4905–4917. doi:10.1007/s11664-022-09727-z
German, R. (2023). Sintering window and sintering mechanism for diamond. Int. J. Refract. Metals Hard Mater. 117, 106401. doi:10.1016/j.ijrmhm.2023.106401
Groza, J. R., and Zavaliangos, A. (2000). Sintering activation by external electrical field. Mater. Sci. Eng. A 287, 171–177. doi:10.1016/s0921-5093(00)00771-1
Hanumantharayappa, A. K. B., Prasanna, C., Ragavendra, C. C., Beekam, C. S., Boluvar, L. S., Nagaral, M., et al. (2021). Synthesis and mechanical characterization of Si3N4 reinforced copper-tin matrix composites. J. Mech. Behav. Mater. 30 (1), 199–206. doi:10.1515/jmbm-2021-0020
Huang, Z., Zhong, Z., Shan, Z., Dong, S., Luo, P., and Chen, L. (2017). Copper matrix composites reinforced by aligned carbon nanotubes: mechanical and tribological properties. Mater. and Des. 133, 570–578. doi:10.1016/j.matdes.2016.08.021
Kalidas, N., Gopal, P. M., and Kavimani, V. (2025). Development and characterization of silicon nitride and synthesized graphene oxide reinforced Cu/GO/xSi3N4 composites. Silicon 17, 141–153. doi:10.1007/s12633-024-03192-5
Kilicarslan, A., Toptan, F., and Kerti, I. (2012). Electroless nickel–phosphorus coating on boron carbide particles. Mater. Lett. 76, 11–14. doi:10.1016/j.matlet.2012.02.037
Kim, P., Shi, L., Majumdar, A., and McEuen, P. L. (2001). Thermal transport measurements of individual multiwalled nanotubes. Phys. Rev. Lett. 87, 215502. doi:10.1103/physrevlett.87.215502
Lee, W. E., and Rainforth, W. M. (1994). Ceramic microstructures, property control by processing. New York: Chapman and Hall.
Li, X. Q., Yao, D. X., Zuo, K. H., Xia, Y., Yin, J., Liang, H., et al. (2020). Microstructure and gas permeation performance of porous silicon nitride ceramics with unidirectionally aligned channels. J. Am. Ceram. Soc. 103, 6565–6574. doi:10.1111/jace.17351
Lindsay, L., Broido, D. A., and Reinecke, T. L. (2013). First-principles determination of ultra-high thermal conductivity of boron arsenide: a competitor for diamond. Phys. Rev. Lett. 111, 025901. doi:10.1103/physrevlett.111.025901
Lisiecki, I., Billoudet, F., and Pileni, M. P. (1996). Control of the shape and the size of copper metallic particles. J. Phys. Chem. 100, 4160–4166. doi:10.1021/jp9523837
Liu, Z. Y., Xiao, B. L., Wang, W. G., and Ma, Z. Y. (2012). Elevated temperature tensile properties and thermal expansion of CNT/2009Al composites. Compos Sci. Technol. 72 (15), 1826–1833. doi:10.1016/j.compscitech.2012.07.021
Liu, Z. Y., Xiao, B. L., Wang, W. G., and Ma, Z. Y. (2014). Effect of carbon nanotube orientation on mechanical properties and thermal expansion coefficient of carbon nanotube-reinforced aluminum matrix composites. Acta Metall. Sin. Engl. Lett. 27 (5), 901–908. doi:10.1007/s40195-014-0136-1
Mallory, G. O., and Hajdu, J. B. (1990). Electroless plating, fundamentals and applications. Orlando: American Electroplaters and surface Finishers Society.
Massalski, T. B., Okamoto, H., Subramanian, P. R., and Kacprzak, L. (1995). Binary alloy phase diagrams. ASM Int. 3, 1485–1486.
Munir, Z. A., Anselmi-Tamburini, U., and Ohyanagi, M. (2006). The effect of electric field and pressure on the synthesis and consolidation of materials: a review of the spark plasma sintering method. J. Mater. Sci. 41, 763–777. doi:10.1007/s10853-006-6555-2
Munir, Z. A., Quach, D. V., and Ohyanagi, M. (2011). Electric current activation of sintering: a review of the pulsed electric current sintering process. J. Am. Ceram. Soc. 94 (1), 1–19. doi:10.1111/j.1551-2916.2010.04210.x
Mustafa, B., and İlkay, Ş. (2010). Controlled synthesis of copper nano/microstructures using ascorbic acid in aqueous CTAB solution. Powder Technol. 198 (Issue 2), 279–284. doi:10.1016/j.powtec.2009.11.022
Nadiia, K., Serhiy, C., and Chung, C. H. (2012). Copper electroless plating in weakly alkaline electrolytes using DMAB as a reducing agent for metallization on polymer films. Electrochimica Acta 59, 179–185. doi:10.1016/j.electacta.2011.10.053
Nicolicescu, C., Nicoară, V. H., Pascu, C. I., Gheorghe, Ș., Burada, C. O., Marinca, T. F., et al. (2023). Morphological analyses of W/Cu functional graded materials obtained by conventional and spark plasma sintering. Materials 16 (11), 4126. doi:10.3390/ma16114126
Okazaki, K. (2000). Electro-discharge consolidation applied to nanocrystalline and RSP/MA powders. Mater. Sci. Eng. A 287, 189–197. doi:10.1016/s0921-5093(00)00775-9
Omori, M. (2000). Sintering, consolidation, reaction and crystal growth by the spark plasma system (SPS). Mater. Sci. Eng. A 287, 183–188. doi:10.1016/s0921-5093(00)00773-5
Orru, R., Licheri, R., Locci, A. M., Cincotti, A., and Cao, G. (2009a). Consolidation/synthesis of materials by electric current activated/assisted sintering. Mater. Sci. Eng. R Rep. 63 (4-6), 127–287. doi:10.1016/j.mser.2008.09.003
Orru, R., Licheri, R., Locci, A. M., Cincotti, A., and Cao, G. (2009b). Consolidation/synthesis of materials by electric current activated/assisted sintering. Mater. Sci. Eng. R. Rep. 63, 127–287. doi:10.1016/j.mser.2008.09.03
Parsi, A., Golestani-Fard, F., and Mirkazemi, S. M. (2019). The effect of gelcasting parameters on microstructural optimization of porous Si3N4 ceramics. Ceram. Int. 45, 9719–9725. doi:10.1016/j.ceramint.2019.01.222
Raghavendra Rao, P. S., and Mohan, C. B. (2020). Study on mechanical performance of silicon nitride reinforced aluminium metal matrix composites. Mater. Today Proc. 33 (8), 5534–5538. doi:10.1016/j.matpr.2020.03.495
Ribeiro, Y., Pereira, J., David, D., and da Silv, M. (2022). Growth, characterization, and photovoltaic application of copper oxide thin films. Thin Solid Films 757, 139381. doi:10.1016/j.tsf.2022.139381
Schebling, P. K., and Keblinski, P. (2003). Thermal expansion of carbon structures. Phys. Rev. B 68, 035425. doi:10.1103/physrevb.68.035425
Sharma, M., and Sharma, V. (2016). Chemical, mechanical, and thermal expansion properties of a carbon nanotube-reinforced aluminum nanocomposite. Int. J. Min. Metall. Mater 23 (2), 222–233. doi:10.1007/s12613-016-1230-3
Shin, S. E., Ko, Y. J., and Bae, D. H. (2016). Mechanical and thermal properties of nanocarbon-reinforced aluminum matrix composites at elevated temperatures. Compos Part B 106, 66–73. doi:10.1016/j.compositesb.2016.09.017
Shirasu, K., Nakamura, A., Yamamoto, G., Ogasawara, T., Shimamura, Y., Inoue, Y., et al. (2017). Potential use of CNTs for production of zero thermal expansion coefficient composite materials: an experimental evaluation of axial thermal expansion coefficient of CNTs using a combination of thermal expansion and uniaxial tensile tests. Compos Part A 95, 152–160. doi:10.1016/j.compositesa.2016.12.027
Singh, M. K., and Gautam, R. K. (2019). Structural, mechanical, and electrical behavior of ceramic-reinforced copper metal matrix hybrid composites. J. Mater Eng. Perform. 28 (2), 886–899. doi:10.1007/s11665-019-3860-x
Sotgiu, G., De Santis, S. O., Bavasso, M., Sarasini, F., and Petrucci, E. (2024). Copper-decorated titanium electrodes: impact of surface modifications of substrate on the morphology and electrochemical performance. ACS Appl. Mater. and Interfaces 16 (19), 24483–24493. doi:10.1021/acsami.4c00203
Tadjine, R., Houimi, A., Alim, M., and Oudini, N. (2022). Oxygen flow rate effect on copper oxide thin films deposited by radio frequency magnetron sputtering. Thin Solid Films 741 (2022), 139013. doi:10.1016/j.tsf.2021.139013
Tian, Q. h., and Guo, x.y. (2010). Electroless copper plating on microcellular polyurethane foam. Trans. Nonferrous Metals Soc. China 20 (S1), s283–s287. doi:10.1016/s1003-6326(10)60057-x
Tjong, S. C. (2013). Recent progress in the development and properties of novel metal matrix nanocomposites reinforced with carbon nanotubes and graphene nanosheets. Mater Sci. Eng. R. 74, 281–350. doi:10.1016/j.mser.2013.08.001
Tokita, M. (1999). Development of large-size ceramic/metal bulk FGM fabricated by spark plasma sintering. Mater. Sci. Forum 308–311, 83–88. doi:10.4028/www.scientific.net/msf.308-311.83
Uddi, S. M., Mahmud, T., Wolf, C., Glanz, C., Kolaric, I., and Hulman, M. (2009). Thermal expansion co-efficient of nanotube–metal composites. Phys. Status Solidi B 246 (11–12), 2836–2839. doi:10.1002/pssb.200982295
Uddin, S. M., Mahmud, T., Wolf, C., Glanz, C., Kolaric, I., Volkmer, C., et al. (2010). Effect of size and shape of metal particles to improve hardness and electrical properties of carbon nanotube reinforced copper and copper alloy composites. Compos Sci. Technol. 70 (16), 2253–2257. doi:10.1016/j.compscitech.2010.07.012
Uzunlar, E., Wilson, Z., and Kohl, P. A. (2013). Electroless copper deposition using Sn−Ag catalyst on epoxy laminates. J. Electrochem. Soc. 160, D3237–D3246. doi:10.1149/2.039312jes
Veillere, A., Constantin, L., Lu, Y. F., Constantin, L., and Lu, Y. F. (2020). A review of processing of Cu/C base plate composites for interfacial control and improved properties. Int. J. Extrem. Manuf. 2 (1), 012002. doi:10.1088/2631-7990/ab61c5
Wang, L., He, G., Yang, Z. C., and Li, J. (2021). Combustion synthesis of high flexural strength, low linear shrinkage and machinable porous β-Si3N4 ceramics. J. Eur. Ceram. Soc. 41, 2395–2399. doi:10.1016/j.jeurceramsoc.2020.11.017
Wu, D., Yan, Y., Liu, Z., and Wang, C. (2024). Fabrication of a novel high electrical conductivity Si3N4 matrix composite with Cu three-dimensional network structure by spark plasma sintering. J. Alloys Compd. 1001, 175158. doi:10.1016/j.jallcom.2024.175158
Xia, W., Tao, J., Hu, Y., Liu, Y., Bao, R., Li, F., et al. (2021). Enhancement of mechanical properties and conductivity in carbon nanotubes (CNTs)/Cu matrix composite by surface and intratube decoration of CNTs. Mater. Sci. Eng. A 816, 141248. doi:10.1016/j.msea.2021.141248
Yanagisawa, O., Kuramoto, H., Matsugi, K., and Komatsu, M. (2003). Observation of particle behavior in copper powder compact during pulsed electric discharge. Mat. Sci. Eng. A 350, 184–189. doi:10.1016/s0921-5093(02)00726-8
Yang, X., Zou, T., Shi, C., Liu, E., He, C., and Zhao, N. (2016). Effect of carbon nanotube (CNT) content on the properties of in-situ synthesis CNT reinforced Al composites. Mater Sci. Eng. A 660, 11–18. doi:10.1016/j.msea.2016.02.062
Ye, J., Ajdelsztajn, L., and Schoenung, J. M. (2006). Bulk nanocrystalline aluminum 5083 alloy fabricated by a novel technique: cryomilling and spark plasma sintering. Metall. Mater. Trans. A 37, 2569–2579. doi:10.1007/bf02586229
Yin, S., Wan, W., Fang, X., Ma, H., Xie, X., Zhou, C., et al. (2023). Mechanical and thermal properties of Si3N4 ceramics prepared by gelcasting using high-solid-loading slurries. Ceram. Int. 49 (24), 40930–40941. doi:10.1016/j.ceramint.2023.10.084
Yoo, S., Lee, D., Ryu, S., Kang, B., Ryu, H., and Hong, S. (2023). Recent progress in low-dimensional nanomaterials filled multifunctional metal matrix nanocomposites. Prog. Mater. Sci. 132, 101034. doi:10.1016/j.pmatsci.2022.101034
Zhang, X., Yuan, J., Ding, Y., Liu, B., Zhang, S., and Yang, J. (2021b). Directly growing nanowire-assembled nanofibrous ceramic foams with multi-lamellar structure via freeze-casting process. J. Eur. Ceram. Soc. 41, 1041–1047. doi:10.1016/j.jeurceramsoc.2020.09.012
Zhang, Y., Yu, X., Gu, H., Yao, D., Zuo, K., Xia, Y., et al. (2021a). Microstructure evolution and high-temperature mechanical properties of porous Si3N4 ceramics prepared by SHS with a small amount of Y2O3 addition. Ceram. Int. 47, 5656–5662. doi:10.1016/j.ceramint.2020.10.151
Keywords: carbon nanotube, silicon nitride, copper composites, heat sink, powder metallurgy, spark plasma sintering, coefficient of thermal expansion
Citation: Daoush WM, Inam F, Hong SH, Olevsky E and German RM (2025) Novel synthesis of CNTs–Si3N4/Cu nanocomposites: electroless deposition, powder metallurgy, spark plasma sintering, microstructure, and physical properties. Front. Mater. 12:1427381. doi: 10.3389/fmats.2025.1427381
Received: 03 May 2024; Accepted: 05 May 2025;
Published: 17 June 2025.
Edited by:
Qinghong Yuan, East China Normal University, ChinaReviewed by:
Jose Ygnacio Pastor, Universidad Politécnica de Madrid, SpainVaibhav S. Kathavate, MIT World Peace University, India
Copyright © 2025 Daoush, Inam, Hong, Olevsky and German. This is an open-access article distributed under the terms of the Creative Commons Attribution License (CC BY). The use, distribution or reproduction in other forums is permitted, provided the original author(s) and the copyright owner(s) are credited and that the original publication in this journal is cited, in accordance with accepted academic practice. No use, distribution or reproduction is permitted which does not comply with these terms.
*Correspondence: Walid M. Daoush, d21kYW91c2hAaW1hbXUuZWR1LnNh