- School of Civil Engineering, Guangxi University of Science and Technology, Liuzhou, China
A study was conducted to investigate the effect of steel slag powder on the compressive strength of concrete cubes at high temperatures using 150 specimens with dimensions of 100 mm × 100 mm × 100 mm. The specimens were fabricated by incorporating steel slag powder (SS) and zeolite powder (ZP), along with varying temperatures. A cubic compression test was performed, and the effect of different factors on the maximum stress was evaluated based on the test results. The results show that adding the correct proportion of steel slag powder under ZP00 conditions significantly improves the compressive strength of concrete, with an optimal replacement rate of 10% (SS10). The compressive strength of SS10-ZP20 exhibits the most significant increase under various operational conditions, with a 30.1% enhancement compared to SS00-ZP00. Moreover, an optimal quantity of zeolite powder can effectively improve the reactivity of steel slag powder. The compressive strength of concrete decreases to different extents under various operational conditions with rising temperatures. Concrete with steel slag powder has greater strength and a denser microstructure than that with SS00-ZP00. A fitting relationship was determined based on experimental data among steel slag replacement rate, mass loss rate, and concrete compressive strength.
1 Introduction
The rapid economic and societal development leads to the continuous expansion of various high-rise residential buildings, bridges, and underground spaces. The complexity of building structures contributes to frequent fire incidents, significantly hindering the swift progress of the social economy (Ma et al., 2015). Considering concrete’s extensive usage as a composite material in contemporary buildings, its exposure to high-temperature environments in practical scenarios is unavoidable, negatively impacting the stability of concrete structures. Since modern buildings are composite structures tightly integrating concrete and steel bars, their capability to withstand high temperatures significantly impacts the efficiency and safety of fire rescue operations during fire incidents. Consequently, academic research on the mechanical properties of concrete post-high temperatures has progressively emerged as a prominent area requiring profound investigation. Currently, both domestic and international scholars have achieved notable advancements in investigating the impact of high-temperature environments on concrete’s mechanical properties. Commonly observed is a substantial decline in concrete strength following simulated fire, showcasing diverse deterioration patterns among different concrete types exposed to high temperatures (Xie et al., 2021; Xiao et al., 2009; Khoury, 2000; Serrano et al., 2016; Bao et al., 2023; Luhar et al., 2021).
Steel slag concrete is prepared by mixing steel slag powder and cement. The compressive strength, flexural strength and elastic modulus of steel slag concrete after high temperature are improved to a certain extent compared with those at room temperature. The research shows that steel slag and waste glass aggregate can significantly improve the fire resistance of concrete (Yu et al., 2016). Chen et al. (2015) conducted an in-depth examination of the mechanical characteristics of steel slag incorporated in concrete under high-temperature circumstances. They highlighted that at 800°C, the impact of steel slag on concrete performance equals that of slag. Netinger et al. (2011), Amin et al. (2022) extended their investigation into the impact of using steel slag as a substitute aggregate on concrete performance within the high-temperature span from 200°C to 800°C. The results indicate a decline in the residual compressive strength of steel slag concrete as temperature rises. However, within the temperature band of 200°C–800°C, the residual compressive strength remains superior to that of the steel slag-free control group, robustly demonstrating the advantageous impact of steel slag addition on enhancing concrete’s fire resistance.
Steel slag concrete is primarily applied in two methods: direct substitution of coarse aggregate with steel slag, and grinding steel slag into fine powder for partial or full cement replacement. For the latter approach, the complexity of steel slag composition, particle size fineness, low innate activity, curing conditions, and selection of alkali activator are pivotal constraints for its integration (Wang, 2008; Wang et al., 2020; Li, 2015; Dingqiang et al., 2023). Wang et al. (2013) discovered that enhancing fineness can effectively boost steel slag activity and enhance concrete’s compressive strength through investigating the impact of steel slag fineness on concrete performance. Shi and Yi (2011) employed a ball mill to refine steel slag and examined its hydration activity effects, discovering that grinding can notably enhance the activity index of steel slag. Furthermore, scholars from both domestic and international domains have elevated steel slag activity through strategic activator selection. Bilim and Atis (2012) researched the alkali activation of steel slag, highlighting the need to account for the activator’s impact on steel slag activity when substituting part of cement clinker, as its activity is notably higher in an alkaline setting. Zhang et al. (2023) utilized diverse testing approaches to emphasize that alkaline activators can accelerate the hydration rate of steel slag powder, boosting the compressive strength of composite cementitious materials; however, the effects differ based on activator types. Building on the previous studies, Liu and Guo (2018) showed that substituting steel slag powder for up to 10% of ultra-high-performance concrete (UHPC) components achieves satisfactory compressive strength levels. Ba et al. (2013) concentrated on investigating steel slag powder-modified cement-based steel slag aggregate concrete, establishing the recommended steel slag powder dosage range as 10%–20%. Additionally, achieving around 10% in micro-powder content (by mass fraction) enhances performance beyond that of the control concrete (Sun and Wang, 2006; Xiao et al., 2021); yet, with a higher steel slag powder content, a decrease in compressive strength becomes evident.
Due to the rapid global industrialization and increased fire safety consciousness, there is a growing demand for improved mechanical properties and high-temperature resistance in concrete structures. Currently, while there is accumulated research on the fundamental mechanical properties (e.g., compressive strength, tensile strength) of steel slag aggregate concrete at room temperature and the impact of steel slag powder as a cement substitute, studies on the high-temperature mechanical properties of steel slag powder concrete remain scarce. Considering that steel slag powder concrete represents a novel construction material offering environmental advantages and outstanding characteristics, exploring its mechanical attributes and operational mechanisms in high-temperature settings becomes crucial.
In previous studies, the use of steel slag powder instead of cement will lead to agglomeration, low activity and insufficient hydration, and the mechanical properties of concrete do not meet the engineering standards. Therefore, this study aims to use the porous structure of zeolite powder to reduce agglomeration, and at the same time, it can release active substances to react with steel slag powder in an alkaline environment to generate more C-S-H gels. On this basis, the synergistic degradation mechanism of zeolite powder modified steel slag under high temperature coupling was revealed by advanced characterization methods such as scanning electron microscopy and X-ray diffraction, and the internal rules of C-S-H gel reconstruction, hydration product stability and interfacial transition zone evolution in modified steel slag concrete under high temperature were clarified. Building upon existing research, this paper delves deeper into the mechanical properties of steel slag powder concrete post-exposure to high temperatures. Its objective is to comprehensively unveil the behavioral patterns and influencing mechanisms in high-temperature settings, offering a scientific foundation for its utilization in such conditions. This research holds significant value in guiding practical engineering endeavors.
2 Test scheme
2.1 Test materials and mix proportion
Concrete consists of water, cement, fine aggregate, coarse aggregate, zeolite powder, and steel slag powder. Ordinary tap water is used as the test water during component pouring, and the chloride content can be disregarded. The cement grade utilized is 42.5-grade Portland cement, ensuring a 28-day compressive strength of no less than 42.5 MPa and are presented in Table 1; the fine aggregate consists of manufactured sand with a fineness modulus of 2.60. The coarse aggregate consists of continuous grading gravel ranging from 3 to 17mm; steel slag powder, derived from steel slag in Gongyi City, Shandong Province, serves as a substitute for cement. The primary chemical constituents of steel slag powder were analyzed using X-ray diffractometer (XRD) and are presented in Table 2, respectively. Zeolite powder exhibited outstanding adsorption capabilities and strong catalytic properties attributed to its notable specific surface area and microporous structure (Arvind and Annadurai, 2024). Triethanolamine was employed as a grinding aid during testing to refine the steel slag powder, followed by screening through a 200-mesh standard sieve to guarantee uniform particle size distribution in the test-grade steel slag powder. The steel slag powder exhibited a specific surface area of 491 m2/kg in the BET test. The formulation of the modified steel slag powder concrete adhered to the specifications outlined in the JGJ55-2011 ordinary concrete mix design. Details of the specimen’s mix design are provided in Table 3.
2.2 Raw material composition analysis
The qualitative and quantitative analysis of steel slag powder reveals a high concentration of CaO and Fe2O3, totaling over 40%. Iron oxide exhibits commendable catalytic and adsorption capabilities, effectively enhancing the generation of cementitious materials during the hydration reaction. Simultaneously, calcium oxide reacts with water to produce calcium hydroxide, facilitating the cementitious system’s curing process and significantly enhancing concrete strength and durability. The ethylene glycol-EDTA titration method was employed to ascertain the f-CaO content in the steel slag powder. The determined f-CaO content was 1.28%, meeting the specifications of the national standard (GB/T 20,491–2017) for Steel slag powder used in cement and concrete, signifying excellent volume stability and laying a theoretical foundation for utilizing steel slag powder in concrete design. Conversely, the qualitative and quantitative analysis of zeolite powder indicates that it primarily comprises SiO2 and Al2O3, with SiO2 constituting a significant 76% of the mass.
2.3 Specimen design
To ensure consistent stirring between steel slag powder and zeolite powder, facilitating the activating impact of zeolite powder on steel slag powder, a blend of steel slag powder, cement, and zeolite powder is premixed in a set ratio to create a foundational mix, then stirred and poured into the specimen. The precise pouring procedure for steel slag powder concrete adheres rigorously to the specifics outlined for pouring samples: initially, river sand and graded crushed stone undergo 2 min of vibrational dry mixing, followed by adding the mixture in a stirred state with an additional 3-min mixing duration to ensure thorough and consistent dispersion of steel slag powder in the concrete, preventing clumping before water inclusion. This step prevents the clustering of steel slag powder and concludes with the addition of water for further stirring.
2.4 High temperature test
Utilizing fire temperatures (25°C, 200°C, 400°C, 600°C, 800°C) as varying parameters, 10 groups were established, each comprising 15 specimens, resulting in a total of 150 cubic specimens sized at 100 mm × 100 mm × 100 mm for compression testing. All samples were cured at 25°C ± 3°C with a relative humidity of ≥90% for a duration of 28 days (Dingqiang et al., 2023). To prevent specimen cracking caused by significant temperature differentials between its interior and exterior, impacting subsequent compressive strength and mechanism analysis, specific methods are employed to address this issue (Chia et al., 2024).
The whole process is divided into three stages, namely:
(1) Pretreatment stage: To ensure the consistency and accuracy of the experiment, the specimens are first subjected to pretreatment. The specimens to be processed are placed in a blast-type drying oven at a set temperature of 60°C for 8 h to remove excess moisture. After drying, they are naturally cooled to room temperature and properly preserved for subsequent processing.
(2) Heat treatment stage: The heat treatment stage aims to replicate how thermal conditions affect specimen performance across various temperatures. Put the pretreated test blocks into the high-temperature furnace individually, adjust the heating rate to 10 °C/min, and precisely regulate it to reach the predetermined target temperatures (200°C, 400°C, 600°C, 800°C). Once the furnace stabilizes at the target temperature, maintain it for 3 h to ensure uniform specimen temperature distribution and complete reaction.
(3) Cooling Stage: Following the completion of heat treatment, to prevent thermal stress cracks resulting from rapid temperature changes in the specimen that could impact subsequent compressive strength testing and mechanism analysis, adopt natural cooling. Switch off the high-temperature furnace power supply and let the specimen cool gradually to room temperature within the furnace. Ensure the furnace door is shut during this process to prevent external cold air from directly affecting the specimen’s surface and causing cracking.
2.5 Cube compressive strength test
For the standard cube compressive strength test, consult the ‘Standard for Test Method of Concrete Physical and Mechanical Properties’ (GB/T 50,081–2019). Employ the RMT301 high-precision mechanical testing system as the loading apparatus. The test system is equipped with a highly sensitive sensor that accurately collects and records stress and strain data in real-time throughout the test, guaranteeing precise and reliable test results. Following the compression test of the concrete test block, spray phenolphthalein test liquid onto the fractured surface. Wait for 30 s, then examine the color of the failed surface and the alteration in the width of the marginal white boundary line of the specimen to analyze temperature effects on the concrete.
2.6 Composition analysis of steel slag micro-powder concrete
The microstructure alterations in modified steel slag powder concrete following exposure to high temperatures were examined using a scanning electron microscope (SEM) to observe changes in pore size, distribution, and morphology. Following that, X-ray diffraction analysis (XRD) was employed to analyze the composition, with a scanning range of 5°–90°, elucidating the impact of high temperatures on material composition changes.
3 Test results and analysis
3.1 Test phenomenon after high temperature
Figure 1 illustrates the color changes in steel slag powder concrete (SS10-ZP20) following various high-temperature treatments. The concrete test block appears predominantly grayish-black at room temperature. As the temperature rises gradually to T = 200°C, the surface color of the concrete test block lightens, transitioning to a pale yellow hue. At T = 400°C, the surface color of the concrete test block darkened from light yellow to yellowish-gray. Subsequently, at T = 600°C, the color deepened to off-white with hints of gray and visible micro-cracks (Luo et al., 2020). After exposure to high temperatures at T = 800°C, the surface color turned grayish-white, showcasing numerous surface micro-cracks, detachment, and exposure of coarse aggregates (Peng et al., 2022). Here, T-fire temperature refers to the temperature (°C) endured by the concrete specimen inside the high-temperature furnace.
Figure 2 illustrates the color variation of phenolphthalein on the surface of failed steel slag micro-powder concrete (SS10-ZP20) specimens under varying temperatures. Clearly observable is the lightening of phenolphthalein’s color applied to the failed surface of the test block as temperature rises, with white coloration at the edges, signifying complete decomposition of the alkaline hydration product, slaked lime. This occurs due to the higher external temperature experienced by the test specimen during the heating process. The internal temperature is lower, leading to a staggered temperature distribution within the concrete test piece, resulting in less decomposition of the internal alkaline hydration product.
Figure 3 is the compressive failure morphology of steel slag micro-powder concrete exhibits distinct variations following exposure to different high temperatures. The specimen demonstrates a characteristic progressive failure under ambient temperature conditions. Initially, the surface remains undamaged upon application of initial stress, followed by gradual longitudinal crack propagation culminating in penetration failure. Nevertheless, as the fire temperature rises, the failure mode undergoes significant changes: at 200°C, the original microcracks on the specimen surface rapidly propagate under axial pressure, eventually penetrating the entire specimen to create macroscopic cracks. At 400°C, the cracking and shedding of certain concrete test blocks intensify notably due to axial pressure. At 600°C, there is noticeable uneven expansion in the central region. At 800°C, visible cracks appear on the specimen’s surface along with the shedding of concrete material from the blocks. Throughout the loading process, there is an exacerbation of block shedding on the specimen’s surface, accompanied by aggregate shedding. Following the release of pressure, the test block’s aggregate disperses, leading to a near-complete loss of interface bonding strength.
In the high temperature test, the surface deterioration of the specimen shows significant temperature characteristics. When the temperature reaches 400 °C, the surface of the specimen still maintains structural integrity, and no obvious peeling phenomenon is observed, which indicates that the thermal stability of the material can be maintained at this temperature. However, when the temperature rises to 600 °C and 800 °C, the material system begins to undergo essential changes: the surface layer of the specimen appears to be partially fragmented and peeled off, and the aggregate wrapped in mortar is also exposed, suggesting that the interface transition zone between the cement matrix and the aggregate at this time also causes stress concentration due to the difference in thermal expansion coefficient.
3.2 The mass loss rate of specimen after high temperature
Formula 1 is used to calculate the mass loss rate of steel slag powder concrete in a high-temperature environment, with the specific value illustrated in Figure 4. The mass loss rate of the specimens rises progressively with temperature elevation, primarily due to two factors: firstly, the physical evaporation of free water in concrete specimens directly reduces mass; secondly, chemical alterations at the hydration product level, for instance, ettringite decomposition and weakly bound water loss, also influence mass depletion. Concrete containing steel slag powder exhibits a reduced mass loss rate compared to concrete without it, as the inclusion of steel slag powder notably enhances the concrete’s microstructure, resulting in higher density and lower porosity. This compact structure not only limits the evaporation pathways of free water but also minimizes the mass loss directly resulting from water evaporation (He and Na, 2023). Additionally, steel slag powder and zeolite powder will continue to undergo hydration reactions in high-temperature environments, leading to water consumption and the formation of new hydration products, consequently reducing the rate of mass loss (Chia et al., 2024).
At 400°C, the concrete experiences a notably higher mass loss rate compared to that at 200°C, primarily due to the dehydration and detachment of tightly bound water within the cement hydration products. While steel slag powder can partially absorb or react with water molecules and produce a small quantity of new hydration products, its overall reaction efficiency is constrained. Hence, concrete containing steel slag powder exhibits only a marginal reduction in mass loss rate under high temperature conditions compared to standard concrete without steel slag powder (SS00-ZP00) (Manzoor et al., 2024).
Between 400°C and 800°C, the mass loss rate of concrete continues to rise. At this point, the mass loss primarily results from the decomposition of chemical components in the mortar and fine aggregate, leading to irreversible physical damage to the concrete specimens. The decomposition of numerous hydration products leads to a substantial increase in pore structure and internal cracks within the concrete. Meanwhile, thermal stress variation causes an escalation in inter-aggregate cracking, collectively exacerbating the internal structural degradation of the concrete. Additionally, the temperature widens the gaps between incompletely reacted steel slag powder particles, enhancing the level of porosity and expanding the material’s overall volume, resulting in thermal expansion (Kodur and Sultan, 2003).
In the formula: I is the mass loss rate (%), m is the mass of the specimen at room temperature (kg), m1 is the mass of the specimen after high temperature (kg).
3.3 Strength loss curve of concrete after high temperature
In the design of concrete load-bearing structures, it is necessary to consider the performance and strength loss of concrete in high-temperature environments. Therefore, the strength loss of concrete is an important index to measure the stability of concrete in a fire environment. The relationship between fire temperature and residual strength of concrete is shown in the figure.
Figure 5 illustrates the correlation between the strength reduction rate of steel slag micro-powder concrete test blocks and temperature. Negative values indicate higher strength of steel slag micro-powder concrete test blocks at elevated temperatures compared to normal conditions, while positive values signify strength decrease. From Figure 5, it is evident that the strength loss rate of steel slag powder concrete specimens occurs at 400°C. This is because concrete strength is primarily influenced by the quantity of hydration products and the density of the specimens. Below 400°C, the strength loss rate of concrete specimens following exposure to high temperatures remains relatively low across various steel slag replacement rates. This phenomenon occurs because, within this temperature range, the rise in temperature causes the free water in the concrete specimen to vaporize due to volume expansion, creating a steam pathway for its release and relieving the internal steam pressure. Consequently, the porosity inside the specimen increases at this temperature, leading to a decrease in concrete strength. Nevertheless, since the structure between the mortar and the aggregate inside the specimen remains intact, the impact on the concrete’s overall strength is not significant.
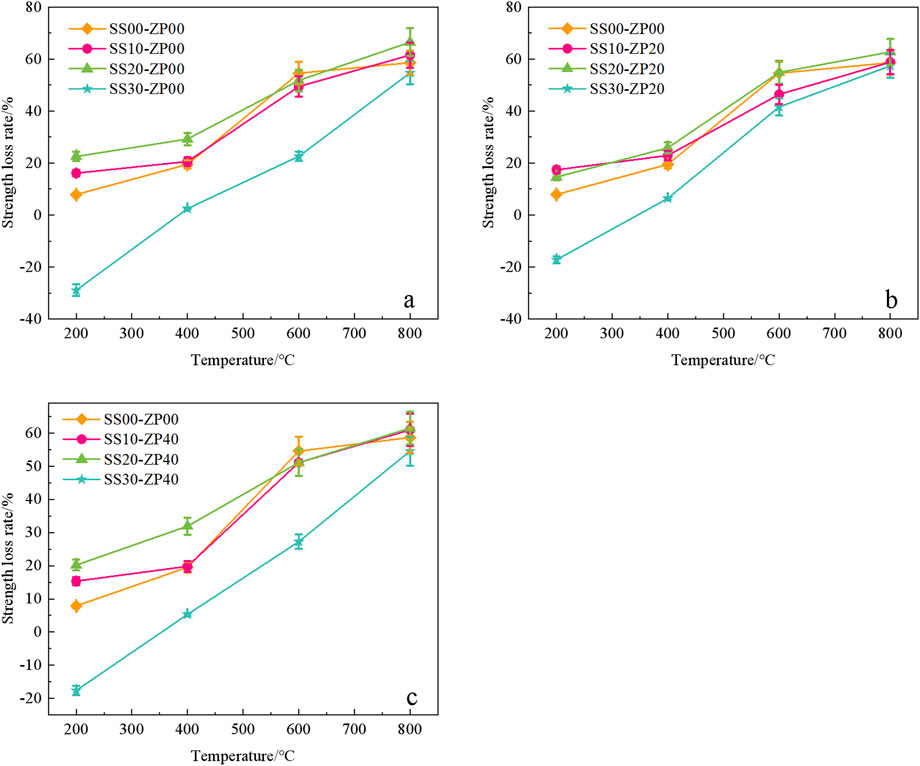
Figure 5. Strength loss curve of concrete test block at different temperatures: (a) SS(/)-ZP00; (b) SS(/)-ZP20; (c) SS(/)-ZP40.
The strength loss rate increases significantly when the temperature exceeds 400°C, attributed to the decomposition of hydration products within the specimen and the thermal stress difference between the aggregate and the cement matrix (He and Na, 2024; He et al., 2023). With rising temperature, the deterioration effect on concrete intensifies, and the ongoing decomposition of hydration products further accelerates the strength loss rate of concrete specimens. At 800°C, the compressive strength of the specimen decreases significantly, with numerous cracks forming on the surface. Consequently, the overall interface bonding force of the specimen is greatly diminished, resulting in the formation of numerous cracks between the internal aggregates. Furthermore, treatment of the SS30-ZP20 and SS30-ZP40 specimen groups at 200°C resulted in an increase in the residual compressive strength of concrete (Malik et al., 2021). The primary cause of this phenomenon is that in a high-temperature setting, the cementitious material partially participating in the hydration reaction within the specimen reacts with steam to generate limited hydration products, filling the pores and consequently enhancing the residual compressive strength of the steel slag micropowder concrete specimen.
3.4 Stress-strain curve of steel slag powder concrete after high temperature
The stress-strain curve is commonly utilized to depict the material, component, or structure’s resistance to deformation and failure when subjected to a load. The compressive test, an essential method, assesses the capacity of concrete and other components to withstand external pressure. It closely simulates the real stress conditions of engineering components while considering operational convenience. This study transforms the load-deformation data using Equation 2 obtained during testing, calculates the average from three datasets, and plots the average stress-strain curve of the steel slag powder concrete specimen under stress conditions.
In the formula: N is the axial force of the specimen (KN), A is the total cross-sectional area of the specimen (mm2), and f is the size conversion coefficient (0.95).
Figure 6 displays stress-strain curves of concrete at varying steel slag powder replacement rates. The figure illustrates the dual impact of steel slag content and temperature on the mechanical properties of concrete. Firstly, as the steel slag powder replacement rate rises, the concrete’s peak stress initially rises before declining. The peak stress peaks at a 10% replacement rate (SS10-ZP00), signifying that integrating the right amount of steel slag powder can boost the ultimate compressive strength of concrete specimens. Nonetheless, a high substitution rate reduces the cement matrix proportion, raises concrete’s internal pores, and lowers compactness, resulting in decreased peak stress. Conversely, the peak stress of steel slag micro-powder concrete declines to various extents with rising temperatures, and the curve’s downward slope notably decreases (Chen et al., 2017). Nevertheless, at a 30% steel slag replacement rate (SS30-ZP00), the strength rises post-temperature impact, primarily due to excessively high steel slag replacement rates causing inadequate activity of steel slag powder at room temperature. Conversely, in a high-temperature setting, the interaction of temperature and water vapor activates steel slag powder, enhancing hydration product formation, filling cracks and pores effectively, resulting in strength increment rather than decline (Zheng and Deng, 2024). As the temperature rises, concrete’s peak strain increases, while the specimen’s elastic modulus decreases.
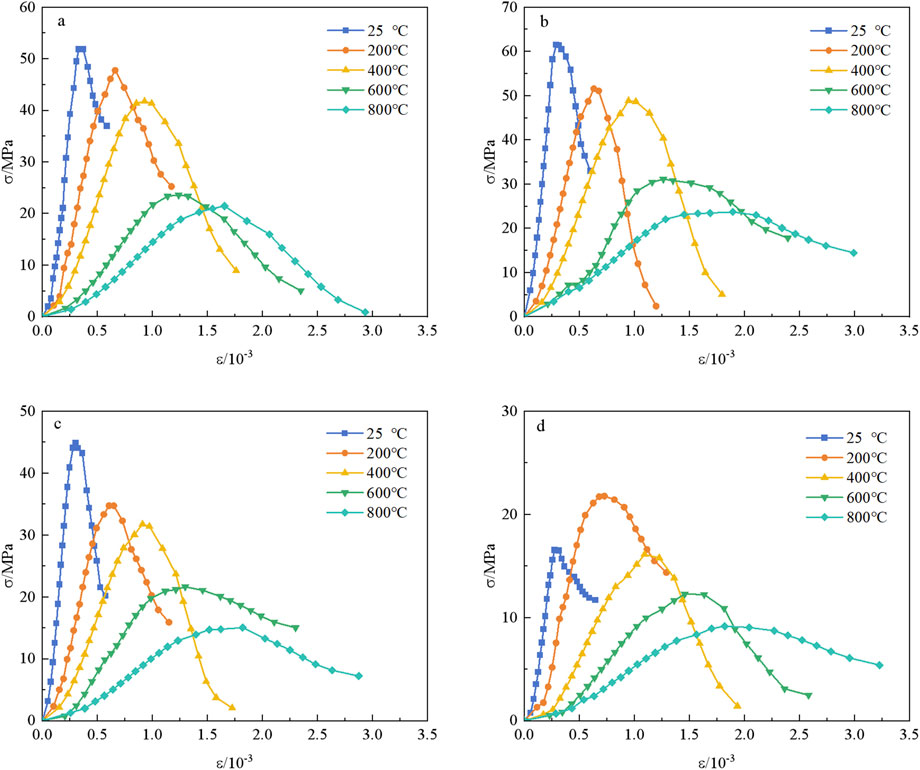
Figure 6. Stress-strain curves of steel slag concrete samples subjected to different temperatures: (a) SS00-ZP00; (b) SS10-ZP00; (c) SS20-ZP00; (d) SS30-ZP00.
3.5 Peak stress of steel slag powder concrete after high temperature
As shown in the diagram, the data in the diagram represents the peak stress of concrete after exposure to different temperatures for specimens with varying content of steel slag powder and zeolite powder. Due to the discrete nature of concrete specimens, the data in the diagram reflects the average values of three specimens in each group.
Figure 7 illustrates a peak stress comparison diagram for different temperature-steel slag powder substitution rates and zeolite powder contents. It shows that, with a constant steel slag powder replacement rate, the peak stress of the specimen increases initially and then decreases as the zeolite powder content (ZP) rises. Particularly, the optimal strength is found at ZP20 regardless of the steel slag content variations. This superiority mainly stems from zeolite powder’s enhancement of cement hydration reactions, leading to the formation of products such as aluminum hydroxide gel. These products interact with the oxides in steel slag, aiding in hardening and strengthening the steel slag. Nevertheless, an excessive zeolite powder amount, reaching 40% of the steel slag powder’s mass fraction, increases the internal porosity of concrete, exacerbating shrinkage deformation, causing concrete cracking, and ultimately reducing peak strength. Furthermore, as the temperature continues to rise, the peak strength of each group typically decreases to different degrees. Interestingly, at 200°C, the specimen with a 30% steel slag powder substitution rate shows higher peak strength compared to 25°C. This phenomenon is linked to the increased reactivity of steel slag powder in high-temperature environments, triggering a secondary hydration reaction and consequently raising the peak stress of the specimen.
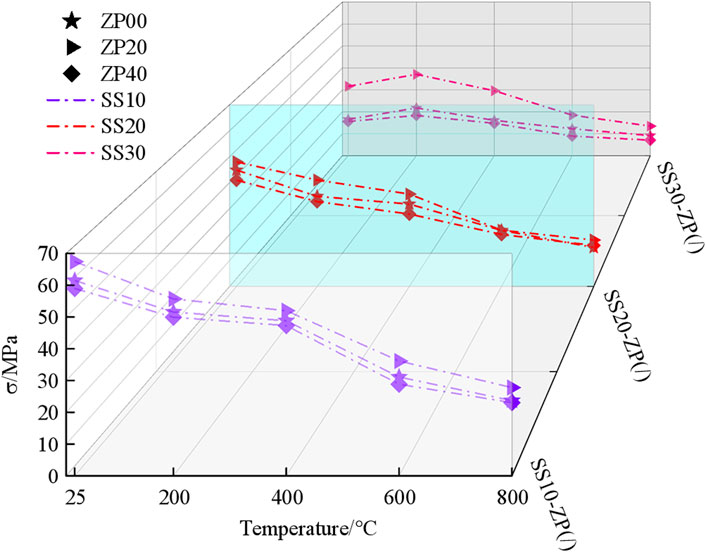
Figure 7. Control the peak stress after high temperature of specimens with different zeolite powder content under different steel slag micro powder content.
Figure 8 presents three peak stress comparison graphs depicting the influence of various steel slag micro-powder substitution rates in combination with a constant amount of zeolite powder at different temperatures. The graph illustrates an initial increase followed by a decrease in peak stress as the steel slag micro-powder substitution rate rises. Concrete with a 10% steel slag micro-powder substitution rate exhibits the highest peak stress across varying temperature conditions, with SS10-ZP20 achieving a peak stress enhancement of 30.1% over SS00-ZP00. This is attributed to the ability of steel slag micro-powder to fill concrete pores, thereby increasing the concrete density. Additionally, steel slag micro-powder can enhance hydration reactions, leading to increased production of hydration products and ultimately boosting the concrete’s compressive strength. When subjected to varying temperatures, concrete samples with a 10% steel slag micro-powder substitution rate exhibit higher residual compressive strength than the control group, with a decreasing trend as the substitution rate rises. This phenomenon occurs because a 10% steel slag micro-powder substitution rate can enhance cement hydration reactions in high-temperature settings, resulting in more hydration products, denser concrete, and increased compressive strength. Excessive addition of steel slag micro-powder replaces the cement effect, diminishes the concrete’s cement matrix content, and hinders the proper dispersion of cement and hydration particles, resulting in decreased residual compressive strength of concrete specimens.
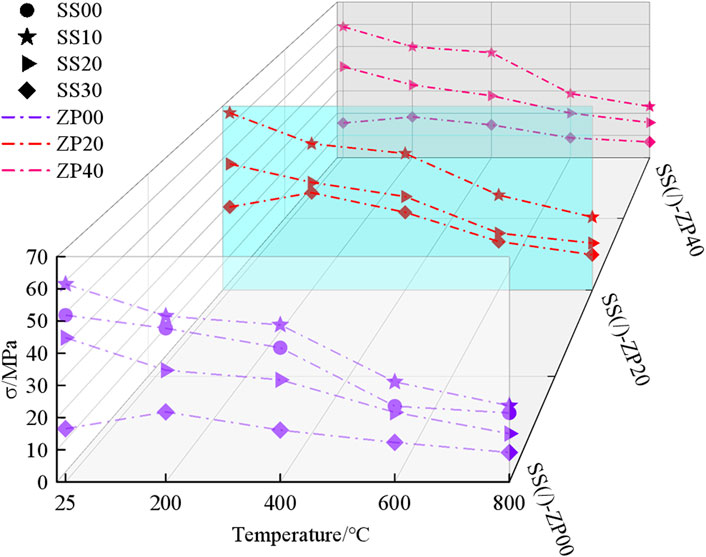
Figure 8. Control the peak stress after high temperature of specimens with different steel slag powder content under the condition that the amount of zeolite powder is controlled.
4 Fitting relationship of residual compressive strength of steel slag concrete after high temperature
The peak stress of concrete specimens under different steel slag powder substitution rate (SS) in the test was selected for Gauss fitting (Formula 3), and the relationship curves between steel slag powder substitution rate and peak stress and temperature were obtained. The R2 is greater than 0.90, and the fitting effect is good. The specific results are shown in Figure 9.
In the formula:
By analyzing Formula 3 and the peak stress fitting curve on the graph, it is evident that the peak strength of concrete containing steel slag powder initially rises and then declines as the substitution rate of steel slag powder increases. This is primarily because adding a small proportion of steel slag powder can greatly enhance the microstructure of concrete, improving its density and overall strength by filling the minute pores within the cement mixture. Nevertheless, at high substitution rates, the optimization effect becomes saturated, resulting in the inability to further enhance the internal microstructure. Conversely, the peak strength decreases due to the accumulation of unfavorable phases. Furthermore, with rising temperatures, although the secondary hydration reaction of steel slag may partially improve the mechanical properties of concrete, this enhancement does not sufficiently counterbalance the adverse impact of high temperature on the rapid degradation of the cement matrix and the overall deterioration of the specimen. Ultimately, the peak stress of concrete consistently decreases as the temperature rises.
Considering the challenge of determining the precise temperature encountered by a concrete structure during a real fire incident, a fitting model correlating mass loss rate with peak stress is developed using both mass loss rate and temperature variables (Formula 4) to better quantify the peak stress-temperature relationship. The aim is to indirectly demonstrate the significant impact of fire temperature on the mechanical properties of concrete materials. The fitting results are illustrated in Figure 10.
In the formula:
The curve fitted in the diagram indicates a continuous decrease in the peak stress of the specimen as the mass loss rate gradually increases. This is primarily because both the mass loss rate and peak stress are influenced by variations in the cement matrix content and porosity within the specimen. The rise in mass loss rate directly corresponds to escalated decomposition of cement hydration products in the specimen, along with increased liberation of free water and bound water, consequently resulting in a reduced residual peak stress of the specimen.
5 SEM and XRD analysis
Figure 11a 25°C, X-ray diffraction spectra analysis at room temperature (25°C) reveals a similarity in phase composition between steel slag micro-powder concrete and the control group, with both containing components like calcium hydroxide and calcite. Nonetheless, the incorporation of steel slag micro-powder in concrete specimens leads to a notable increase in composition complexity compared to the control group, attributed to the presence of limited unstable active elements in the steel slag. SEM images reveal abundant needle-like and flaky calcium hydroxide crystals dispersed in the matrix of both control and steel slag groups, creating a closely packed layered structure. In the microstructure of the steel slag group, hydration products intricately interlace within the transition zone between aggregates and matrix, enhancing interface adhesion and creating a denser internal slurry structure in concrete specimens at room temperature, forming a strong bond between aggregate surfaces and the cement matrix. Substituting a portion of cement with steel slag micro-powder not only enhances calcium oxide and silica content but also accelerates the hydration reaction process. Abundant needle-like calcium hydroxide and interlocking C-S-H gel structures in the transition zone of the steel slag group interface lead to reduced porosity compared to the control group specimens, resulting in a high-density concrete structure overall (He et al., 2024).
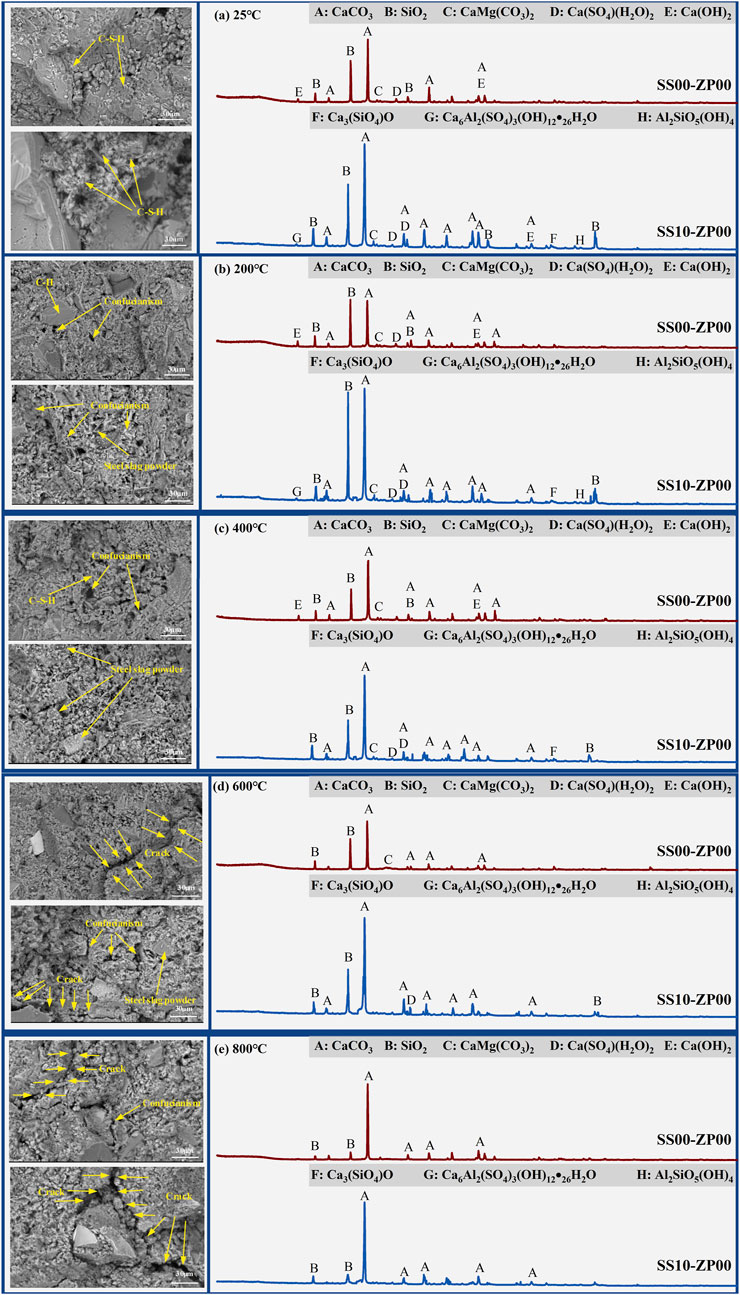
Figure 11. The microstructure and XRD patterns of concrete with 0% and 10% steel slag powder substitution rate under different temperatures: (a) 25°C; (b) 200°C; (c) 400°C; (d) 600°C; (e) 800°C.
When the temperature reaches 200°C (Figure 11b), free water within the concrete begins to evaporate, leading to the release of some water from the concrete specimens and the formation of pore structures in its place. In contrast to cement hydration reactions, adding steel slag powder decreases the usage of free water in hydration processes, enabling a higher retention of free water within the specimens. This condition facilitates the secondary hydration of steel slag micro-powder and zeolite powder. The majority of free water undergoes a phase change into a gaseous state due to temperature effects, expanding in volume. The original uniformly dense matrix structure is disrupted under the pressure of steam. Moreover, gas accumulates within the specimens due to limited interactions between mortar and aggregate. If the internal pressure of the specimens reaches a critical threshold, it can lead to specimen explosion. Even if the pressure does not reach the critical point, the gas liquefying into water after the specimen exits the high-temperature environment can create voids within the specimens. Electron microscope images of specimens containing steel slag powder reveal a significant presence of steel slag micro-powder distributed within the pores of the C-S-H gel. These micro-aggregates act by filling the voids between cement particles, effectively reducing the quantity and size of capillary pores, thereby enhancing the density and strength of the concrete.
The decline in strength of concrete specimens at a high temperature of 400°C (Figure 11c) can be explained by two factors: firstly, the evaporation of free and bound water from the cementitious material leads to the formation of interconnected channels inside the specimens, creating a more porous structure; secondly, the thermal decomposition of the cement matrix weakens the concrete strength and reveals the steel slag powder within the pores, compromising the structural integrity. Furthermore, while the “high-temperature steam curing” conceals part of the degradation from cementitious material decomposition, boosting the residual compressive strength of concrete, the improvement is modest compared to the prominent “steam curing” impact observed in the steel slag powder samples.
At temperatures of 600°C and 800°C (Figure 11d), calcium hydroxide and other hydration products undergo almost complete decomposition, resulting in the specimens being mainly comprised of calcite and quartz. Relative to the state at 400°C, the cracks between the cement matrix and aggregates deepen and widen, causing a significant structural coarsening. Analysis of the images reveals that high temperatures significantly harm the chemical composition and microstructure of concrete, exacerbating deformation mismatches and internal stress accumulation arising from disparate thermal expansion coefficients between aggregates and the cement matrix, subsequently triggering a considerable rise in microcracks within the interface region. Furthermore, with increased temperature exposure, the disparity in thermal stress between aggregates and the matrix intensifies, leading to enhanced interface loosening and the fundamental breakdown of CH and C-S-H cementitious materials (Singh et al., 2023; Long et al., 2013), nearly nullifying the interface bond strength. Consequently, the concrete specimens exhibit pronounced looseness and experience a substantial decrease in residual compressive strength post-loading.
6 Conclusion
This study is based on the compressive strength test of 150 specimens of steel slag micro-powder concrete. By investigating the effects of different substitution rates and temperatures on the mechanical properties of concrete, the degradation law of the strength of steel slag micro-powder concrete at different temperatures was determined. Based on the experimental results, the following conclusions were drawn:
(1) Under the condition of maintaining ZP00, the compressive strength of concrete specimens with a slag micro-powder replacement rate of 10% (SS10) has been improved compared to the blank group concrete. However, as the replacement rate continues to increase, it shows a decreasing trend, indicating that adding an appropriate amount of slag micro-powder helps to improve the compressive strength.
(2) The compressive strength of concrete under the SS10-ZP20 condition is the highest among all conditions, resulting in a maximum strength increase of 30.1% when compared to the baseline condition of SS00-ZP00. However, keeping the steel slag content constant, a continuous increase in the proportion of zeolite powder will lead to a decrease in concrete compressive strength. At the same time, under the SS10-ZP20 condition, it has been proven that zeolite powder can effectively activate the activity of steel slag micro powder.
(3) After high temperature treatment, the compressive strength of concrete decreases under various working conditions with increasing temperature. Additionally, the damage to the compressive strength of concrete containing steel slag micro powder is lower, indicating that replacing some cement with steel slag micro powder helps to improve the fire resistance of concrete. Compared to SS00-ZP00, the residual compressive strength of concrete containing steel slag micro powder is higher, and it has a beneficial effect on filling the internal pores of concrete, making the microstructure of concrete more compact.
(4) By establishing a fitting relationship between the steel slag replacement rate, quality loss rate, and residual compressive strength of concrete, it can be described with Equations 3, 4. The results show that the R2 values are both greater than 0.90, indicating a strong fitting effect. It is possible to indirectly determine the variation pattern of residual compressive strength by analyzing the steel slag replacement rate and quality loss rate.
Data availability statement
The original contributions presented in the study are included in the article/supplementary material, further inquiries can be directed to the corresponding author.
Author contributions
XY: Conceptualization, Data curation, Investigation, Methodology, Project administration, Visualization, Writing – original draft, Writing – review and editing, Funding acquisition. YY: Investigation, Project administration, Resources, Supervision, Validation, Visualization, Writing – original draft, Writing – review and editing.
Funding
The author(s) declare that financial support was received for the research and/or publication of this article. This research was funded by the National Natural Science Foundation of China, No. 51668010.
Conflict of interest
The authors declare that the research was conducted in the absence of any commercial or financial relationships that could be construed as a potential conflict of interest.
Generative AI statement
The author(s) declare that no Generative AI was used in the creation of this manuscript.
Publisher’s note
All claims expressed in this article are solely those of the authors and do not necessarily represent those of their affiliated organizations, or those of the publisher, the editors and the reviewers. Any product that may be evaluated in this article, or claim that may be made by its manufacturer, is not guaranteed or endorsed by the publisher.
References
Amin, M., Hakeem, I. Y., Zeyad, A. M., Tayeh, B. A., Maglad, A. M., and Agwa, I. S. (2022). Influence of recycled aggregates and carbon nanofibres on properties of ultra-high-performance concrete under elevated temperatures. Case Stud. Constr. Mater. 16, e01063. doi:10.1016/j.cscm.2022.e01063
Arvind, S. R., and Annadurai, R. (2024). Prediction on partial replacement of cement and coarse aggregate by zeolite powder and steel slag in high-performance concrete. Eng. Res. Express 6 (2), 025115. doi:10.1088/2631-8695/ad4cb8
Ba, M. F., Liu, J. Z., He, Z. M., and He, J. (2013). Preparation and properties of steel slag powder modified cement-based steel slag aggregate concrete. Mater. Rep. 27 (22), 119–124. doi:10.3969/j.issn.1005-023X.2013.22.032
Bao, J., Zheng, R., Sun, Y., Zhang, P., Cui, Y., Xue, S., et al. (2023). A state-of-the-art review on high temperature resistance of lightweight aggregate high-strength concrete. J. Build. Eng. 69, 106267. doi:10.1016/j.jobe.2023.106267
Bilim, C., and Atis, C. D. (2012). Alkali activation of mortars containing different replacement levels of ground granulated blast furnace slag. Constr. Build. Mater. 28 (1), 708–712. doi:10.1016/j.conbuildmat.2011.10.018
Chen, X. X., Han, M. Z., Wu, H., and Zhou, Z. Y. (2015). Mathematical analysis of compressive strength of steel slag-slag-fly ash composite powder concrete after high temperature. Bull. Chin. Ceram. Soc. 34 (8), 2254–2259. doi:10.16552/j.cnki.issn1001-1625.2015.08.035
Chen, Z. P., Zhou, C. H., Li, Y., Chen, J. J., and Wu, B. (2017). Study on mechanical properties of recycled concrete after high temperature. J. Build. Struct. 38 (12), 105–113. doi:10.14006/j.jzjgxb.2017.12.012
Chia, M. H., Shu, I. D., Siew, C. C., and Li, X. F. (2024). The effect of particle sizes of steel slag as cement replacement in high strength concrete under elevated temperatures. Constr. Build. Mater. 411, 134531. doi:10.1016/j.conbuildmat.2023.134531
Dingqiang, F., Chunpeng, Z., Jian-Xin, L., Kangning, L., Tianyi, Y., Enlai, D., et al. (2023). Recycling of steel slag powder in green ultra-high strength concrete (UHSC) mortar at various curing conditions. J. Build. Eng. 70, 106361. doi:10.1016/j.jobe.2023.106361
He, R., and Na, L. L. (2023). Unveiling the dielectric property change of concrete during hardening process by ground penetrating radar with the antenna frequency of 1.6 GHz and 2.6 GHz. Cem. Concr. Compos. 144, 105279. doi:10.1016/j.cemconcomp.2023.105279
He, R., and Na, L. L. (2024). Air void system and freezing-thawing resistance of concrete composite with the incorporation of thermo-expansive polymeric microspheres. Constr. Build. Mater. 419, 135535. doi:10.1016/j.conbuildmat.2024.135535
He, R., Nantung, T., Olek, J., and Lu, N. (2023). Field study of the dielectric constant of concrete: a parameter less sensitive to environmental variations than electrical resistivity. J. Build. Eng. 74, 106938. doi:10.1016/j.jobe.2023.106938
He, R., Tommy, N., and Na, L. L. (2024). Unraveling microstructural evolution in air-entrained mortar and paste: insights from MIP and micro-CT tomography amid cyclic freezing-thawing damage. J. Build. Eng. 94, 109922. doi:10.1016/j.jobe.2024.109922
Khoury, G. A. (2000). Effect of fire on concrete and concrete structures. Prog. Struct. Eng. Mater. 2 (4), 429–447. doi:10.1002/pse.51
Kodur, V. K. R., and Sultan, M. A. (2003). Effect of temperature on thermal properties of high-strength concrete. J. Mater. Civ. Eng. 15 (2), 101–107. doi:10.1061/(ASCE)0899-1561(2003)152(101)
Li, K. (2015). Experimental study on steel slag powder cement stabilized macadam pavement base material. Master's Thesis (Wuhan, China: Wuhan Polytechnic University).
Liu, J., and Guo, R. (2018). Applications of steel slag powder and steel slag aggregate in ultra-high performance concrete. Adv. Civ. Eng. 2018, 1–8. doi:10.1155/2018/1426037
Long, T., Shi, X. S., Wang, Q. Y., and Li, L. (2013). Mechanical properties and microstructure of fly ash based geopolymer recycled concrete. Adv. Eng. Sci. 45 (S1), 43–47. doi:10.15961/j.jsuese.2013.s1.007
Luhar, S., Nicolaides, D., and Luhar, I. (2021). Fire resistance behaviour of geopolymer concrete: an overview. Buildings 11 (3), 82. doi:10.3390/buildings11030082
Luo, D. M., Wang, Y., Zhang, S. H., Niu, D. T., and Song, Z. P. (2020). Frost resistance of coal gangue aggregate concrete modified by steel fiber and slag powder. Appl. Sci. 10 (9), 3229. doi:10.3390/app10093229
Ma, Q., Guo, R., Zhao, Z., Lin, Z., and He, K. (2015). Mechanical properties of concrete at high temperature—a review. Constr. Build. Mater. 93, 371–383. doi:10.1016/j.conbuildmat.2015.05.131
Malik, M., Bhattacharyya, S. K., and Barai, S. V. (2021). Thermal and mechanical properties of concrete and its constituents at elevated temperatures: a review. Constr. Build. Mater. 270, 121398. doi:10.1016/j.conbuildmat.2020.121398
Manzoor, T., Bhat, J. A., and Shah, A. H. (2024). Performance of geopolymer concrete at elevated temperature−A critical review. Constr. Build. Mater. 420, 135578. doi:10.1016/j.conbuildmat.2024.135578
Netinger, I., Kesegic, I., and Guljas, I. (2011). The effect of high temperatures on the mechanical properties of concrete made with different types of aggregates. Fire Saf. J. 46 (7), 425–430. doi:10.1016/j.firesaf.2011.07.002
Peng, S., Yu, Z., Zhao, Q., Du, X., Xie, X., Chen, B., et al. (2022). Research on dynamic compressive performance and failure mechanism analysis of concrete after high temperature and rapid cooling. Materials 15 (13), 4642. doi:10.3390/ma15134642
Serrano, R., Cobo, A., Prieto, M. I., and González, M. d. l. N. (2016). Analysis of fire resistance of concrete with polypropylene or steel fibers. Constr. Build. Mater. 122, 302–309. doi:10.1016/j.conbuildmat.2016.06.055
Shi, Y. L., and Yi, G. L. (2011). Effect of physical activation method on activity of steel slag, slag and fly ash. China Resour. Compr. Util. 29 (10), 17–20. doi:10.3969/j.issn.1008-9500.2011.10.002
Singh, H., Kumar, T. A., and Singh, S. (2023). Experimental investigation on the performance of ground granulated blast furnace slag and nano-silica blended concrete exposed to elevated temperature. Constr. Build. Mater. 394, 132088. doi:10.1016/j.conbuildmat.2023.132088
Sun, J., and Wang, Z. X. (2006). Effect of steel slag powder on road performance of concrete. J. Build. Mater. 9 (4), 477–480. doi:10.3969/j.issn.1007-9629.2006.04.019
Wang, Q., Yang, J., and Yan, P. (2013). Cementitious properties of super-fine steel slag. Powder Technol. 245, 35–39. doi:10.1016/j.powtec.2013.04.016
Wang, T. (2008). Experimental study and preliminary simulation of Pangang steel slag as foundation backfill. Master's Thesis (Kunming, China: Kunming University of Science and Technology).
Wang, X. H., Wang, J., Bai, J. F., Jin, Q., and Zhu, L. (2020). Long-term dry shrinkage performance of steel slag cement mortar under unconstrained multi-conditions. J. Changjiang River Sci. Res. Inst. 37 (2), 153–158+163. doi:10.11988/ckyyb.20181053
Xiao, J., Long, C. J., He, J. G., Chang, J., and Wu, C. P. (2021). Performance and microscopic characteristics of high-volume activated steel slag powder-cement stabilized crushed stone. China J. Highw. Transp. 34 (10), 204–215. doi:10.19721/j.cnki.1001-7372.2021.10.016
Xiao, J. Z., Huang, Y. B., and Zheng, Y. C. (2009). Residual flexural strength of recycled concrete after high temperature. J. Archit. Civ. Eng. 26 (3), 32–36. doi:10.3321/j.issn:1673-2049.2009.03.005
Xie, K. Z., Liu, Z. W., Zhu, M. J., and Ma, D. L. (2021). Mechanical properties of manufactured sand concrete with different stone powder content after high temperature. J. Archit. Civ. Eng. 38 (3), 80–89. doi:10.19815/j.jace.2020.09070
Yu, X., Tao, Z., Song, T. Y., and Pan, Z. (2016). Performance of concrete made with steel slag and waste glass. Constr. Build. Mater. 114, 737–746. doi:10.1016/j.conbuildmat.2016.03.217
Zhang, C. L., Wang, B., Li, T. H., Wang, Y. F., and Li, N. L. (2023). Alkali-activated characteristics of high-volume steel slag powder-cement. China Powder Sci. Technol. 29 (2), 55–65. doi:10.13732/j.issn.1008-5548.2023.02.007
Keywords: steel slag powder, high temperature, microstructure, compressive strength, degradation mechanism
Citation: Yang X and Ye Y (2025) Study on mechanical properties of modified steel slag powder concrete after high temperature. Front. Mater. 12:1589342. doi: 10.3389/fmats.2025.1589342
Received: 07 March 2025; Accepted: 07 April 2025;
Published: 17 April 2025.
Edited by:
Svetlana Tretsiakova, Ulster University, United KingdomReviewed by:
Chuanqing Fu, Zhejiang University of Technology, ChinaSyahrul Fithry Senin, Universiti Teknologi Teknologi MARA, Cawangan Pulau Pinang, Malaysia
Copyright © 2025 Yang and Ye. This is an open-access article distributed under the terms of the Creative Commons Attribution License (CC BY). The use, distribution or reproduction in other forums is permitted, provided the original author(s) and the copyright owner(s) are credited and that the original publication in this journal is cited, in accordance with accepted academic practice. No use, distribution or reproduction is permitted which does not comply with these terms.
*Correspondence: Yanbing Ye, MTAwMDAxMTYwQGd4dXN0LmVkdS5jbg==