- 1 School of Information Engineering, Yango University, Fuzhou, Fujian, China
- 2School of Jia Yang, Zhejiang Shuren University, Hangzhou, Zhejiang, China
- 3School of Mathematics and Big Data, Hohhot Minzu College, Hohhot, Inner Mongolia, China
- 4School of Sciences and Humanities, Mathematics Department, Nazarbayev University, Astana, Kazakhstan
This paper delves into the static and dynamic behavior of graphene cantilever beam resonators under electrostatic actuation at their free tips. A rigorous analysis of the system’s response is performed. The constitutive nonlinear equation of the system is derived using the energy method and Hamilton’s principle. An analytical solution to the nonlinear static problem is obtained. The generalized stiffness coefficient for the lumped model of the cantilever graphene beam under load at its tip is calculated, enabling a comprehensive analysis of its dynamic behavior. A key focus is on investigating the dynamic pull-in conditions of the system under both constant and harmonic excitation. Analytical predictions are validated through numerical simulations. The system exhibits periodic solutions when the excitation parameters are below a certain threshold described by a separatrix curve, leading to sustained oscillations. On the other hand, if the excitation parameters exceed this threshold, the system experiences pull-in instability, causing the beam to touch down. Furthermore, we explore the impact of excitation frequency on the dynamic response of the graphene cantilever beam under harmonic load. The simulations reveal that choosing the excitation frequency near the beam’s resonance frequency can lead to structural collapse under certain parameter conditions.
1 Introduction
Microelectromechanical systems (MEMS) have revolutionized numerous fields by enabling the creation of miniaturized devices with remarkable performance and functionalities. MEMS devices are distinguished by their compact size, low power consumption, and ability to integrate mechanical, electrical, and optical features on a single chip [1]. Among the vital components of MEMS are microresonators that are excited near their resonance frequencies. These microresonators find extensive applications in mass and force sensors, including the detection of proteins [2], molecules [3], electrons, and nanoparticles [4]. However, the sensitivity of these sensors can be improved by addressing the weight of the microbeam, as the minimum detectable quantity is often limited by the mass of the resonator. Therefore, lightweight and high-strength materials are highly desirable to overcome this limitation.
In this context, graphene has emerged as a promising material for MEMS and microresonators due to its light weight and outstanding mechanical properties, including high Young’s modulus and tensile strength. Table 1 shows the summary of graphene’s mechanical characteristics compared to common MEMS components such as steel and silicon.
Graphene is a single layer of carbon atoms tightly bound together. The superior properties of graphene stem from its carbon-carbon bond structure and
Interestingly, though graphene was not originally thought to exhibit piezoelectric properties due to its symmetry, recent advancements have enabled its application in the field of micro and nano-electromechanical systems (MEMS/NEMS). This could enable the development of new energy harvesting, actuation, and transduction technologies [12]. Furthermore, graphene’s high sensitivity and low mass make it an ideal candidate for high-resolution mass sensing, and its high thermal conductivity suggests potential use as a thermal management material [13]. Its thermal conductivity at room temperature equals
Graphene’s remarkable attributes offer opportunities for further miniaturization of MEMS resonators and have led to a new wave of research in this area. Utilizing graphene resonators in mass detection has become a particularly compelling topic of study. For example, in [16], it was found that nonlinear vibrations can enhance the sensitivity of a graphene microbeam resonator. A related approach involves studying nonlinear solutions, which have been widely applied in mathematical models of wave propagation and stability analysis in nonlinear systems in Li and Yu [17]. Natsuki et al., employing the continuum elasticity theory, have shown that the mass sensors with double-layered graphene sheets (DLGSs) provide higher sensitivity than single-layered graphene sheets (SLGSs) [18]. Another way to increase the detection sensitivity has been studied by Karličić et al. [19]. The study associates it with the increase in the magnetic field that results in the sensor’s frequency shift. Many works study the potential applications of graphene microresonators through experimental results. However, we are interested in the mathematical analysis of such systems. For instance, Wei et al. investigated the steady-state behavior of a graphene Euler beam subjected to a constant load and provided analytical and finite element solutions [20]. Using the Rayleigh–Ritz method with Hermite cubic interpolation yielded approximate finite element solutions, which were validated against analytical solutions.
Several studies have investigated the dynamic behavior of electrostatically actuated systems made of graphene. Among the notable research works are Anjum and He [21], Kadyrov et al. [22], Skrzypacz et al. [23], Wei et al. [24], and Omarov et al. [25]. Recent studies on soliton dynamics in nonlinear Schrödinger-type equations in Qing et al. [26] provide insights into analytical approaches that could complement the study of nonlinear MEMS resonators. Electrostatic actuation is widely preferred in the field of microelectromechanical systems due to its simplicity and efficiency, offering advantages over alternative actuation methods such as electrothermal, piezoelectric, and electromagnetic actuation [1, 27]. When electrostatically actuated resonators are employed, the electric load applied to a cantilever beam comprises both AC and DC components. The DC component induces deflection of the beam to its equilibrium position, while the AC component generates vibrations around this equilibrium position. The equilibrium position is attained when the restoring force of the beam matches the electrostatic force [1].
However, if the DC polarization voltage is increased beyond a certain threshold, exceeding the restoring force, the beam continues to deflect until it contacts an adjacent structure or surface, resulting in collapse. This phenomenon is known as the pull-in instability, and the threshold voltage at which it occurs is referred to as the pull-in voltage. Pull-in can be classified into two types: static pull-in and dynamic pull-in. Static pull-in describes the occurrence of pull-in solely due to DC actuation, while dynamic pull-in can arise from AC harmonic excitation or the motion of the structure [1]. Analyzing and understanding pull-in is essential in the design of MEMS resonators. It is crucial to tune the electric load parameters to avoid pull-in instability, as it can lead to structural collapse and device failure. Skrzypacz et al. [23] conducted a comprehensive investigation, providing the necessary and sufficient conditions for the existence of periodic solutions for a lumped mass model subjected to a constant DC voltage. This study contributed valuable insights into the dynamic behavior of the model under a constant loading scenario. Additionally, the pull-in phenomenon of the same lumped mass model excited by a harmonic load was explored in two separate research works: Kadyrov et al. [22] and Omarov et al. [25]. In Omarov et al. [25], Sturm’s theorem was employed to identify periodic solutions of the lumped mass model with general initial conditions, and their analytical results were verified through numerical simulations implemented in the Python programming language. Furthermore, the work of Anjum and He [21] and Wei et al. [24] delved into the study of the nonlinear graphene beam equation and the existence of several natural frequencies of the system. These studies utilized the variational iteration method based on a Laplace transform and the Pade technique to obtain approximate solutions. Recent examples of approximation techniques for periodic solutions to MEMS oscillators can be found in He [28], while the pull-down instability of the nonlinear quadratic oscillators is investigated in He et al. [29]. Studies on nonlinear wave equations have shown that higher-order dispersion effects play a crucial role in the stability and response of nonlinear systems, as in Li and Fajun [30].
This paper investigates the static and dynamic behavior of a graphene cantilever beam subjected to electrostatic actuation at its free tip. The same oscillator model proposed in Skrzypacz et al. [31] is employed, comprising a low-mass graphene beam of length
The study is structured as follows: In Section 2, the constitutive nonlinear equation governing the system is derived using the energy method and Hamilton’s principle, and boundary conditions are established. In Section 3, an analytical solution for the static problem is computed. Section 4 presents the development of a lumped mass model, which is employed to study the fundamental dynamics of the system and also provides the calculation of the generalized stiffness coefficient for the graphene cantilever beam under the load at its tip. The pull-in phenomenon under both constant and harmonic excitation is analyzed in Section 5. Simulation results for dynamic pull-in and resonance are presented in Section 6. Finally, conclusions are drawn in Section 7.
2 Mathematical model
This section focuses on deriving the constitutive nonlinear equation for a cantilever beam made of graphene by employing Hamilton’s principle, an essential concept in variational mechanics.
2.1 Constitutive stress–strain equation for graphene
It is theoretically and experimentally justified that the stress–strain relationship for the classical Euler–Bernoulli beam made of graphene can be written as
where
2.2 Model equation for a Euler–Bernoulli beam made of graphene
Here, we consider a cantilever beam subjected to a force applied at the free end and analyze a small segment on the beam before and after deflection (see Figure 2). In the following,
The axial strain
By integrating the stress–strain Equation 1 with respect to strain, we obtain the strain energy density, which represents the energy stored per unit volume in the material. This energy density is a measure of the potential energy stored within the beam due to deformation. Integrating this quantity over the entire volume of the beam allows us to determine the total potential energy of the system. Thus, we get
where
and
Therefore, Equation 2 simplifies to
Then, the total potential energy
Inserting the axial strain into Equation 3 yields
Note that
where
Equation 5 can be rewritten as
where
is the third moment of inertia of the cross section. Inserting Equations 6, 7 into Equation 4 gives the following potential energy equation:
The kinetic energy of a beam can be calculated based on the mass distribution along the length of the beam and the velocity of its individual mass elements. The general formula for the kinetic energy of a beam is given by
where
where
2.3 Hamilton’s principle
In order to derive the graphene beam equation of motion, we need to use the Lagrangian energy functional
Applying the Hamilton’s principle on the Lagrangian
where
and
By applying integration by parts to the variation of the kinetic energy expression by Equation 9, we can rewrite it in terms of the virtual displacement
The boundary term in time vanishes in Equation 10 due to the boundary conditions imposed on the virtual displacement. Specifically, it is assumed that the virtual displacement satisfies
To express Equation 11 in terms of displacement variation
Substituting Equations 12, 13 into Equation 8 and grouping the terms gives
According to the definition, the variation
Because the beam is fixed at
Furthermore, Equations 16, 17 imply
and from Equation 15 we can conclude that
3 Analytic solution for static problem
Let
subject to the boundary conditions.
Integrating Equation 18 twice and applying the boundary conditions by Equations 21, 22, we get
The right-hand side of Equation 23 is positive, which implies that the left-hand side of the equation is also positive for
which yields
The real solution of Equation 24 exists only if
Integrating Equation 25 once and twice results in
and
where
and
Thus, the analytic solution of the graphene beam equation under the point load at the tip can be written as
Note that when
4 Galerkin approximation
4.1 Lumped mass model
Let us consider the deflection of the vibrating elastic beam made of graphene at the axial position
with boundary and initial conditions given as follows.
and
where
We assume that the beam has a simple geometry and the deformation is not too large. Therefore, to study the essential dynamics of the graphene beam undergoing a point force at the free tip, we use a one-mode Galerkin approximation,
where
Employing boundary conditions by Equations 28–31 and dividing both sides by
Then, the corresponding Galerkin equation for Equation 32 is given as
where
The coefficient
4.2 Dimensionless single-degree-of-freedom model
Now, let us consider a choice of
where
and the spectral parameter
Here,
subject to boundary conditions
However, for our Galerkin ansatz, we choose
Now, let us compute
Then, one can show that
and
Employing the fact that
see Skrzypacz et al. [37]. Numeric integration in Mathematica with
Thus, we can conclude that
where
Note that
Substituting Equation 36 into Equation 33 gives
where
Then, dividing both sides of Equation 37 by
subject to
where
5 Pull-in and resonance
5.1 Constant voltage
In this section, we investigate the dynamic pull-in phenomenon of the lumped mass model Equation 48, considering a constant voltage applied to the cantilever beam. Our analysis is based on a phase diagram, which allows us to identify regions in the parameter space where the system exhibits periodic behavior and where pull-in occurs. Previous studies [23] have shown that the nondimensional model
exhibits periodic solutions for small values of
The constant
Next, we focus on the phase diagram, which plays a crucial role in understanding the system’s dynamics. The periodic solutions of Equation 39 correspond to closed curves or loops in the phase diagram, known as limit cycles. These limit cycles appear when the right-hand side of Equation 41 has a root in the interval (0,1), indicating periodic behavior; see Figure 3. In contrast, when there are no roots in this interval, pull-in occurs. Of particular importance is the curve that separates the regions with different dynamics of the system, known as the separatrix. If the model and excitation parameters of the system lie inside a certain region determined by the separatrix, the solution is periodic; otherwise, it is not periodic [1]. In order to determine the range of positive parameter values of
Note that Equation 42 has at most four roots. One root is negative and lies outside the interval (0,1), while another root occurs at
intersects the horizontal axis at the same points as
yields
where only
lies within the interval (0,1). Consequently, the system exhibits an oscillatory or periodic solution if
where
Rearranging the inequality and expressing
The operational diagram for the MEMS graphene oscillator is presented in Figure 4. The parameter values
Another crucial parameter in MEMS devices is the pull-in time, which represents the time required for the system to collapse. The pull-in time can be obtained from Equation 41, where we express the velocity of the beam’s tip at a given position and parameter value
Subsequently, the pull-in time, denoted as
The integration of this expression over the interval [0,1] corresponds to the distance that the beam’s tip needs to travel in order to reach the fixed electrode, thus leading to the occurrence of a pull-in phenomenon. In Figure 5, the effect of excitation parameter
Here,
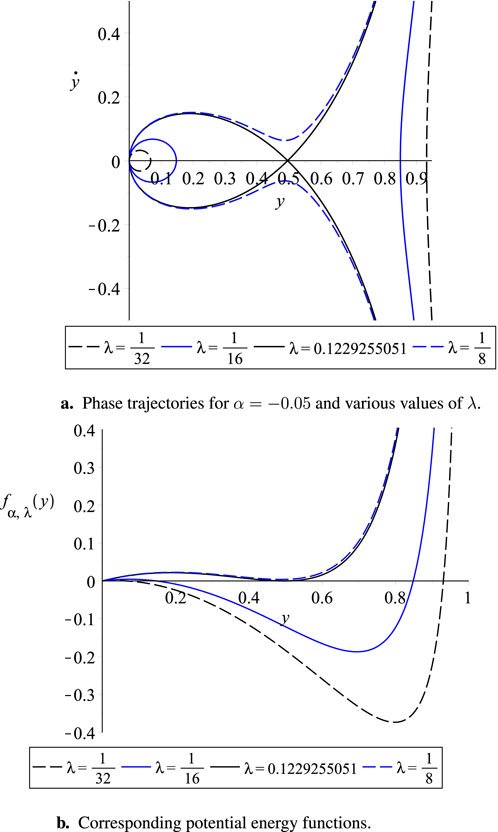
Figure 6. (a) Phase trajectories for
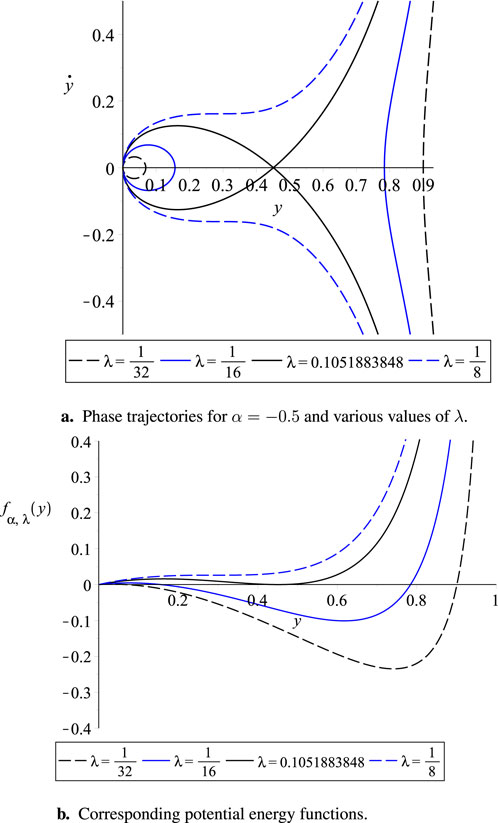
Figure 7. (a) Phase trajectories for

Figure 8. (a) Phase trajectories for
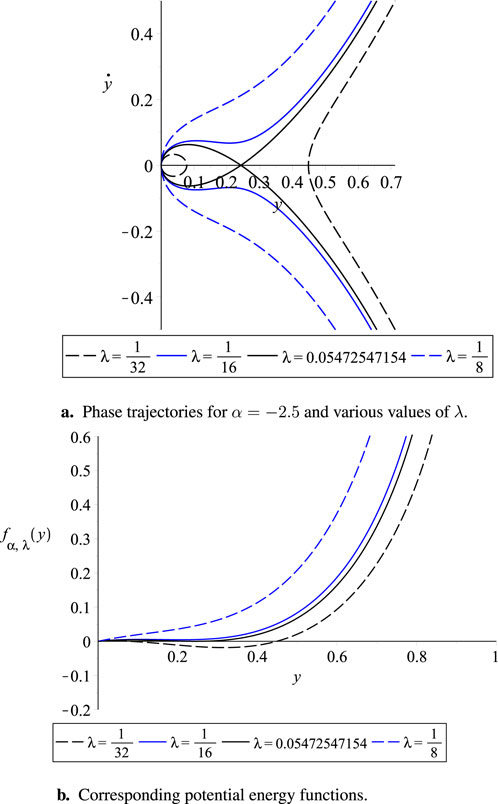
Figure 9. (a) Phase trajectories for
5.2 Time-dependent voltage
The pull-in phenomenon in a microelectromechanical system (MEMS) with a parallel-plate capacitor under time-dependent voltage
with the forcing frequency
has a periodic solution if the equation
has a root in (0,1), and it does not attain a periodic solution if the equation
does not have any roots in
Our nondimensional model by Equation 39 is the special case of Equation 49 with
According to the theorem, the second-order nonlinear and non-autonomous differential equation
has a periodic solution provided that
has a root in (0,1). Let us define the function
Note that for
Therefore,
By solving
Then, using the second derivative test, we can find that
where
Hence, the Intermediate Value theorem guarantees the existence of some
with
6 Simulation results
6.1 Constant voltage
In this section, we present numerical simulations of the normalized deflection of the beam’s free tip, denoted as
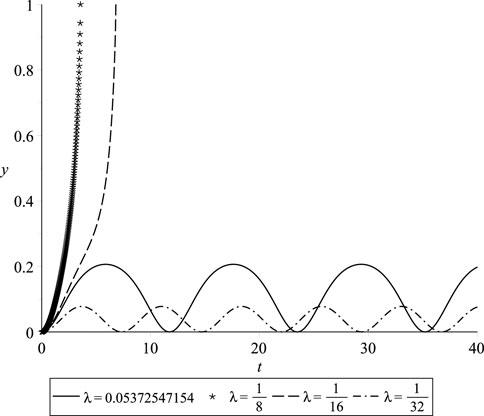
Figure 13. Profiles of periodic and pull-in solutions for
6.2 Time-dependent voltage
In this section, we will conduct an in-depth analysis of the resonance phenomenon in a cantilever beam that is subjected to a harmonic force. Depending on the frequency of harmonic excitation, the dynamic behavior of the system can be classified as primary and secondary resonance. Primary resonance refers to a dynamic behavior observed in a system when it is excited by a frequency that is close to its natural frequency. The dynamic response of the system becomes significantly amplified under primary resonance conditions, leading to large vibration amplitudes. On the other hand, secondary resonance occurs when the system is excited at frequencies that are different from its natural frequencies and are located relatively far from them [1]. However, for our analysis, we will specifically focus on primary resonance. For our analysis, we fix the value of
Recall that
Let us denote
and fix
The pull-in value of DC voltage indicates that, for the fixed values of
yields for
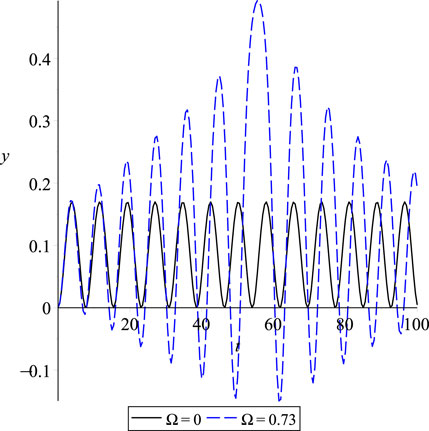
Figure 14. Dynamic response of a graphene cantilever beam under constant voltage and harmonic excitation near natural angular frequency.
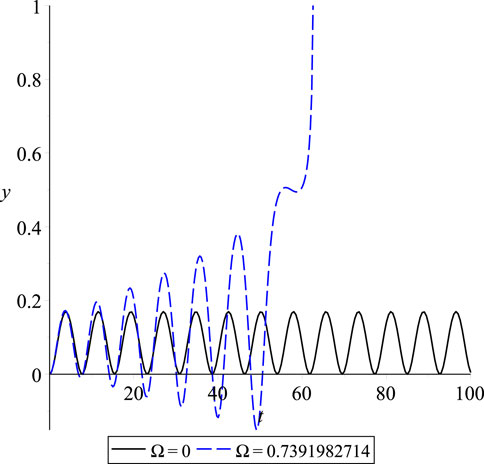
Figure 15. Dynamic response of a graphene cantilever beam under constant voltage and harmonic excitation at natural angular frequency,
7 Conclusion and outlooks
In this study, a comprehensive analysis of the static and dynamic behavior of a graphene cantilever beam subjected to electrostatic actuation at its free tip was conducted. First, an analytical solution for the nonlinear static problem was derived, and its consistency with the classical linear solution was demonstrated in the limit where the second-order elastic stiffness constant
Data availability statement
The original contributions presented in the study are included in the article/Supplementary Material; further inquiries can be directed to the corresponding author.
Author contributions
J-HH: conceptualization, methodology, writing – original draft, and writing – review and editing. QB: formal analysis, funding acquisition, writing – original draft, and writing – review and editing. Y-CL: conceptualization, writing – original draft, and writing – review and editing. DK: methodology, writing – original draft, and writing – review and editing. GE: formal analysis, investigation, writing – original draft, and writing – review and editing. YY: conceptualization, data curation, formal analysis, investigation, methodology, software, validation, visualization, writing – original draft, and writing – review and editing. PS: conceptualization, data curation, formal analysis, funding acquisition, investigation, methodology, project administration, resources, software, supervision, validation, visualization, writing – original draft, and writing – review and editing.
Funding
The author(s) declare that financial support was received for the research and/or publication of this article. PS and GE were supported by the Ministry of Education and Science of the Republic of Kazakhstan within the framework of Project AP19676969. QB was supported by Youth Top Talents Special Training Program of the “Yingcai Xingmeng” Project.
Conflict of interest
The authors declare that the research was conducted in the absence of any commercial or financial relationships that could be construed as a potential conflict of interest.
Generative AI statement
The author(s) declare that no Generative AI was used in the creation of this manuscript.
Publisher’s note
All claims expressed in this article are solely those of the authors and do not necessarily represent those of their affiliated organizations, or those of the publisher, the editors and the reviewers. Any product that may be evaluated in this article, or claim that may be made by its manufacturer, is not guaranteed or endorsed by the publisher.
Supplementary material
The Supplementary Material for this article can be found online at: https://www.frontiersin.org/articles/10.3389/fphy.2025.1551969/full#supplementary-material
References
1. Younis MI MEMS linear and nonlinear statics and dynamics, 20. Springer Science and Business Media (2011).
2. Hanay MS, Kelber S, Naik A, Chi D, Hentz S, Bullard E, et al. Single-protein nanomechanical mass spectrometry in real time. Nat Nanotechnology (2012) 7:602–8. doi:10.1038/nnano.2012.119
3. Jensen K, Kim K, Zettl A. An atomic-resolution nanomechanical mass sensor. Nat Nanotechnology (2008) 3:533–7. doi:10.1038/nnano.2008.200
4. Steele GA, Hüttel AK, Witkamp B, Poot M, Meerwaldt HB, Kouwenhoven LP, et al. Strong coupling between single-electron tunneling and nanomechanical motion. Science (2009) 325:1103–7. doi:10.1126/science.1176076
5. Fuhrer MS, Lau CN, MacDonald AH. Graphene: materially better carbon. MRS Bull (2010) 35:289–95. doi:10.1557/mrs2010.551
6. Pesin D, MacDonald AH. Spintronics and pseudospintronics in graphene and topological insulators. Nat Mater (2012) 11(5):409–16. doi:10.1038/nmat3305
7. Lee J-U, Yoon D, Cheong H. Estimation of young’s modulus of graphene by Raman spectroscopy. Nano Lett (2012) 12:4444–8. doi:10.1021/nl301073q
8. Li Y. Reversible wrinkles of monolayer graphene on a polymer substrate: toward stretchable and flexible electronics. Soft Matter (2016) 12:3202–13. doi:10.1039/c6sm00108d
9. Tomori H, Kanda A, Goto H, Ootuka Y, Tsukagoshi K, Moriyama S, et al. Introducing nonuniform strain to graphene using dielectric nanopillars. Appl Phys Express (2011) 4:075102. doi:10.1143/apex.4.075102
10. Khan ZH, Kermany AR, Öchsner A, Iacopi F. Mechanical and electromechanical properties of graphene and their potential application in mems. J Phys D: Appl Phys (2017) 50:053003. doi:10.1088/1361-6463/50/5/053003
11. Rüegg A, Lin C (2013). Bound states of conical singularities in graphene-based topological insulators. Phys Rev Lett 110(4). doi:10.1103/physrevlett.110.046401
12. Wang X, Tian H, Xie W, Shu Y, Mi W-T, Ali Mohammad M, et al. Observation of a giant two-dimensional band-piezoelectric effect on biaxial-strained graphene. NPG Asia Mater (2015) 7:e154. doi:10.1038/am.2014.124
13. Ghosh S, Calizo I, Teweldebrhan D, Pokatilov EP, Nika DL, Balandin AA, et al. Extremely high thermal conductivity of graphene: prospects for thermal management applications in nanoelectronic circuits. Appl Phys Lett (2008) 92. doi:10.1063/1.2907977
14. Balandin AA, Ghosh S, Bao W, Calizo I, Teweldebrhan D, Miao F, et al. Superior thermal conductivity of single-layer graphene. Nano Lett (2008) 8:902–7. doi:10.1021/nl0731872
15. Iacopi F, Brongersma S, Vandevelde B, O’Toole M, Degryse D, Travaly Y, et al. Challenges for structural stability of ultra-low-k-based interconnects. Microelectronic Eng (2004) 75:54–62. doi:10.1016/j.mee.2003.09.011
16. Dai MD, Kim C-W, Eom K. Nonlinear vibration behavior of graphene resonators and their applications in sensitive mass detection. Nanoscale Res Lett (2012) 7:499–10. doi:10.1186/1556-276x-7-499
17. Li L, Yu F, Qin Q (2024) Interaction and manipulation for non-autonomous bright soliton solution of the coupled derivative nonlinear Schrödinger equations with Riemann–Hilbert method. Appl Mathematics Lett 149. doi:10.1016/j.aml.2023.108924
18. Natsuki T, Shi J-X, Ni Q-Q. Vibration analysis of nanomechanical mass sensor using double-layered graphene sheets resonators. J Appl Phys (2013) 114. doi:10.1063/1.4820522
19. Karličić D, Kozić P, Adhikari S, Cajić M, Murmu T, Lazarević M. Nonlocal mass-nanosensor model based on the damped vibration of single-layer graphene sheet influenced by in-plane magnetic field. Int J Mech Sci (2015) 96:132–42. doi:10.1016/j.ijmecsci.2015.03.014
20. Wei D, Liu Y, Elgindi MB. Some analytic and finite element solutions of the graphene Euler beam. Int J Computer Mathematics (2014) 91:2276–93. doi:10.1080/00207160.2013.871784
21. Anjum N, He J-H. Nonlinear dynamic analysis of vibratory behavior of a graphene nano/microelectromechanical system. Math Methods Appl Sci (2020). doi:10.1002/mma.6699
22. Kadyrov S, Kashkynbayev A, Skrzypacz P, Kaloudis K, Bountis A. Periodic solutions and the avoidance of pull-in instability in nonautonomous microelectromechanical systems. Math Methods Appl Sci (2021) 44:14556–68. doi:10.1002/mma.7725
23. Skrzypacz P, Kadyrov S, Nurakhmetov D, Wei D. Analysis of dynamic pull-in voltage of a graphene mems model. Nonlinear Anal Real World Appl (2019) 45:581–9. doi:10.1016/j.nonrwa.2018.07.025
24. Wei D, Nurakhmetov D, Aniyarov A, Zhang D, Spitas C. Lumped-parameter model for dynamic monolayer graphene sheets. J Sound Vibration (2022) 534:117062. doi:10.1016/j.jsv.2022.117062
25. Omarov D, Nurakhmetov D, Wei D, Skrzypacz P. On the application of Sturm's theorem to analysis of dynamic pull-in for a graphene-based MEMS model. Appl Comput Mech (2018) 12. doi:10.24132/acm.2018.413
26. Qing Q, Li L, Fajun Y (2024) Non-autonomous exact solutions and dynamic behaviors for the variable coefficient nonlinear Schrödinger equation with external potential. Physica Scripta 100(1). doi:10.1088/1402-4896/ad9870
28. He J-H. Periodic solution of a micro-electromechanical system. Facta Universitatis, Ser Mech Eng (2024) 187–98. doi:10.22190/fume240603034h
29. He J-H, Yang Q, He C-H, Alsolami AA. Pull-down instability of the quadratic nonlinear oscillators. Facta Universitatis, Ser Mech Eng (2023) 21:191–200. doi:10.22190/fume230114007h
30. Li L, Fajun Y (2024). The fourth-order dispersion effect on the soliton waves and soliton stabilities for the cubic-quintic gross–pitaevskii equation, Chaos, Solitons and Fractals 179. doi:10.1016/j.chaos.2023.114377
31. Skrzypacz P, Wei D, Nurakhmetov D, Kostsov EG, Sokolov AA, Begzhigitov M, et al. Analysis of dynamic pull-in voltage and response time for a micro-electro-mechanical oscillator made of power-law materials. Nonlinear Dyn (2021) 105:227–40. doi:10.1007/s11071-021-06653-3
32. Poggetto VFD, Pal R, Pugno N, Miniaci M (2024). Topological bound modes in phononic lattices with nonlocal interactions. Int J Mech Sci 281. doi:10.1016/j.ijmecsci.2024.109503
33. Lee C, Wei X, Kysar JW, Hone J. Measurement of the elastic properties and intrinsic strength of monolayer graphene. Science (2008) 321:385–8. doi:10.1126/science.1157996
34. Lu Q, Huang R. Nonlinear mechanics of single-atomic-layer graphene sheets. Int J Appl Mech (2009) 1:443–67. doi:10.1142/s1758825109000228
35. Khan ZH, Kermany AR, Öchsner A, Iacopi F. Mechanical and electromechanical properties of graphene and their potential application in mems. J Phys D: Appl Phys (2017) 50:053003. doi:10.1088/1361-6463/50/5/053003
37. Skrzypacz P, Bountis A, Nurakhmetov D, Kim J. Analysis of the lumped mass model for the cantilever beam subject to grob’s swelling pressure. Commun Nonlinear Sci Numer Simulation (2020) 85:105230. doi:10.1016/j.cnsns.2020.105230
38. Maplesoft. Maple user manual. Waterloo, Ontario: Maplesoft, a division of Waterloo Maple Inc. (1996).
39. Chen Z, Gandhi U, Lee J, Wagoner R. Variation and consistency of young’s modulus in steel. J Mater Process Technology (2016) 227:227–43. doi:10.1016/j.jmatprotec.2015.08.024
41. Hopcroft MA, Nix WD, Kenny TW. What is the young’s modulus of silicon? J Microelectromechanical Syst (2010) 19:229–38. doi:10.1109/jmems.2009.2039697
42. Yajima S, Okamura K, Hayashi J. Structural analysis in continuous silicon carbide fiber of high tensile strength. Chem Lett (1975) 4:1209–12. doi:10.1246/cl.1975.1209
43. Moussa B, Youssouf M, Abdoul Wassiha N, Youssouf P. Homotopy perturbation method to solve Duffing - Van der Pol equation. Advances in Differential Equations and Control Processes (2024) 31(3):299–315. doi:10.17654/0974324324016
44. Alshomrani NAM, Alharbi WG, Alanazi IMA, Alyasi LSM, Alrefaei GNM, Al’amri SA, et al. Homotopy perturbation method for solving a nonlinear system for an epidemic. Advances in Differential Equations and Control Processes (2024) 31(3):347–355. doi:10.17654/0974324324019
Keywords: MEMS, graphene resonator, dynamic pull-in, periodic solutions, singular MEMS oscillators
Citation: He J-H, Bai Q, Luo Y-C, Kuangaliyeva D, Ellis G, Yessetov Y and Skrzypacz P (2025) Modeling and numerical analysis for MEMS graphene resonator. Front. Phys. 13:1551969. doi: 10.3389/fphy.2025.1551969
Received: 26 December 2024; Accepted: 06 March 2025;
Published: 25 April 2025.
Edited by:
Francisco Perez-Reche, University of Aberdeen, United KingdomReviewed by:
Fajun Yu, Shenyang Normal University, ChinaVinicius F. Dal Poggetto, University of Trento, Italy
Copyright © 2025 He, Bai, Luo, Kuangaliyeva, Ellis, Yessetov and Skrzypacz. This is an open-access article distributed under the terms of the Creative Commons Attribution License (CC BY). The use, distribution or reproduction in other forums is permitted, provided the original author(s) and the copyright owner(s) are credited and that the original publication in this journal is cited, in accordance with accepted academic practice. No use, distribution or reproduction is permitted which does not comply with these terms.
*Correspondence: Piotr Skrzypacz, cGlvdHIuc2tyenlwYWN6QG51LmVkdS5reg==