- 1Industry & Equipment Technology, Hefei University of Technology, Hefei, China
- 2School of Materials Science and Engineering, Hefei University of Technology, Hefei, China
- 3National–Local Joint Engineering Research Centre of Nonferrous Metals and Processing Technology, Hefei, China
- 4Institute for Integrated Radiation and Nuclear Science, Kyoto University, Osaka-fu, Japan
- 5Research Centre for Powder Metallurgy Engineering and Technology of Anhui Province, Hefei, China
Ultrafine tungsten carbide (WC) powder refers to WC powders with a particle size between 100 and 500 nm. Researchers have improved the comprehensive properties of WC-based cemented carbides by preparing ultra-fine WC powders. Because of the preparation and application of nanoscale WC powders, ultrafine-grain cemented carbides with excellent hardness and wear resistance have been successfully produced. In this paper, the preparation methods of ultra-fine WC powder are divided into solid-phase, liquid-phase, and vapor-phase methods according to the state of the raw materials (i.e., the W or C source). The liquid-phase methods could realize the preparation of WC at the temperature between 500 and 800°C. The purity of WC prepared by vapor-phase method is the highest. The solid-phase reduction carbonization method has potential industrial application.
Introduction
Cemented carbides using tungsten carbide (WC) as main raw materials with high hardness and excellent wear resistance are widely used in drill, mold, needle, cutting tool, and other special processing industries. Due to the high bonding strength and fine microstructure between ultrafine WC particles and metal binder phase, ultrafine-grain cemented carbide combines the characteristics of ceramics and metal at the same time, which has high toughness, good strength and excellent hardness. Thus, a large number of studies on the optimal preparation of composite powders, the most suitable proportions of bonding phases, the effects of doping with other elements, and the best size and morphology of WC grains, among others, have been conducted to improve the hardness and toughness of cemented carbides (Zheng et al., 2015; Wang et al., 2017).
Among many factors, the size of WC particles generates the greatest impact on the mechanical properties of cemented carbides. As shown in Figure 1, the hardness and bending strength of cemented carbides increase as the proportion of fine WC particles increases (Akhtar et al., 2007). The conventional and ultrafine WC particles’ size is 4, 0.2 μm, respectively. The samples were prepared by mixing two kinds of WC powders with different mass ratio between conventional and ultrafine powders. The particle size of WC powders directly determines the size of WC grain in cemented carbide during the sintering process. And the grain size of WC is related to the mechanical properties of sintered cemented carbides. Hardness of cemented carbide increased with the mass fraction of ultrafine WC particles. The bending strength presented the same trend as the hardness.
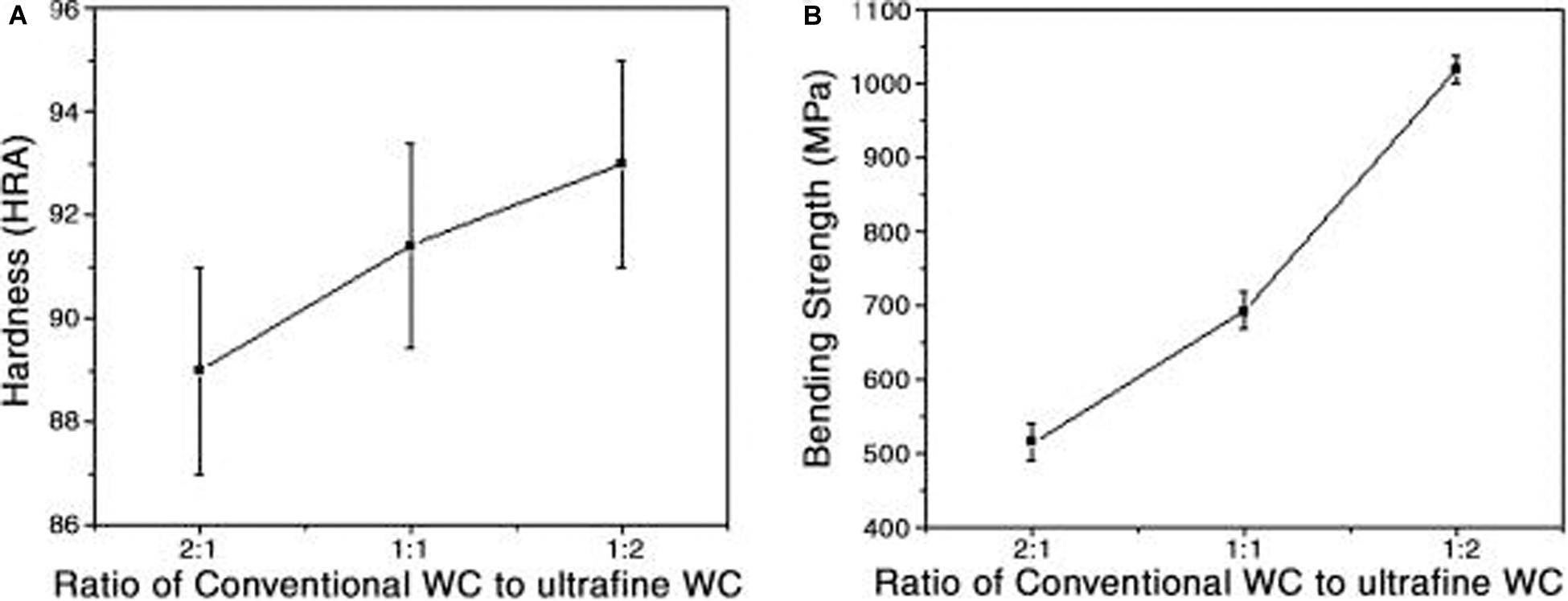
Figure 1. Changes in the (A) hardness and (B) bending strength of cemented carbides with increasing proportion of coarse and fine grained WC (Akhtar et al., 2007) [Figure 3 of Akhtar et al. (2007), Copyright Elsevier Ltd].
Ultrafine WC powders improve sintering performance and enhance the mechanical properties of the cemented carbide (Liu et al., 2010; Emani et al., 2015). As shown in Figure 2; Liu et al. (2010) carried out studies on the displacement rate curve of WC–10 wt% Co powder samples by taking WC powders of different particle sizes and Co powder of equal particle sizes as sintering materials and found that smaller WC particle sizes result in higher displacement rates and degrees of densification of powder sintering.
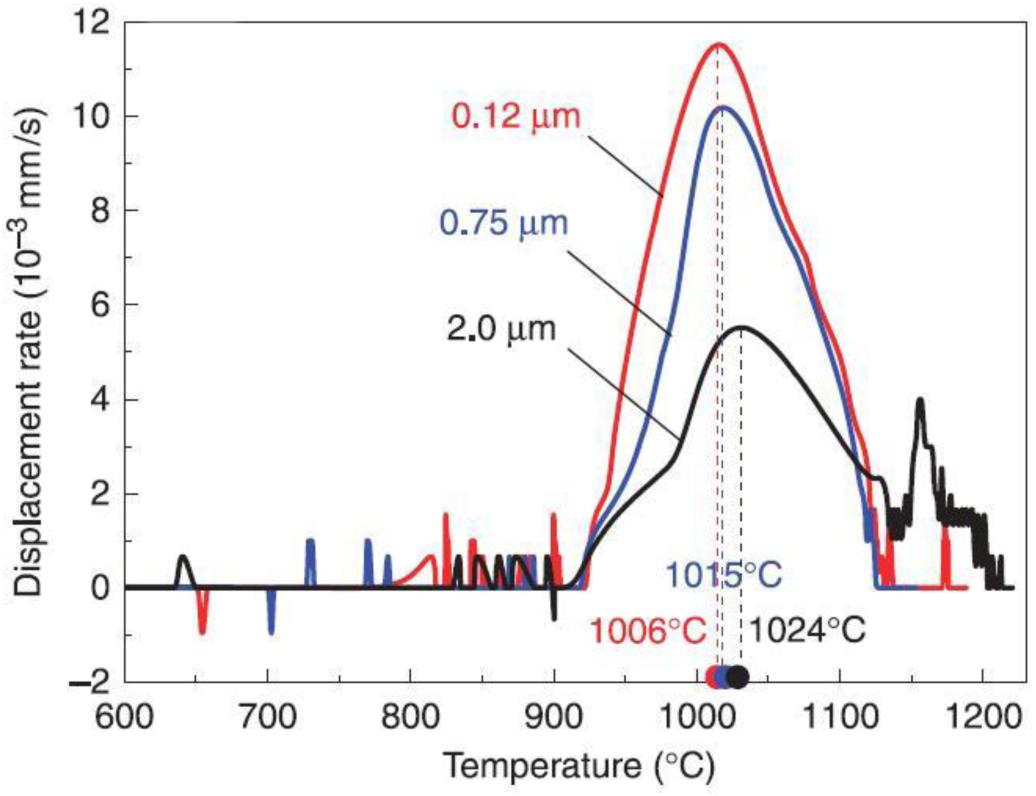
Figure 2. Displacement rates of sintering of WC powder with different particle sizes (Liu et al., 2010) [Figure of Liu et al. (2010), Copyright The American Ceramic Society].
Maheshwari et al. (2007) carried out a comprehensive study by sintering WC–10Co powders with different initial particle sizes. Figure 3 shows the relationship between the sintering densification and sintering temperature of WC powders of different initial particle sizes. The entire sintering temperature range decreased gradually as the initial average particle size decreased from 30 μm to 10 nm. When the initial particle size was 10 nm, the densification of the alloy was up to 90% approximately.
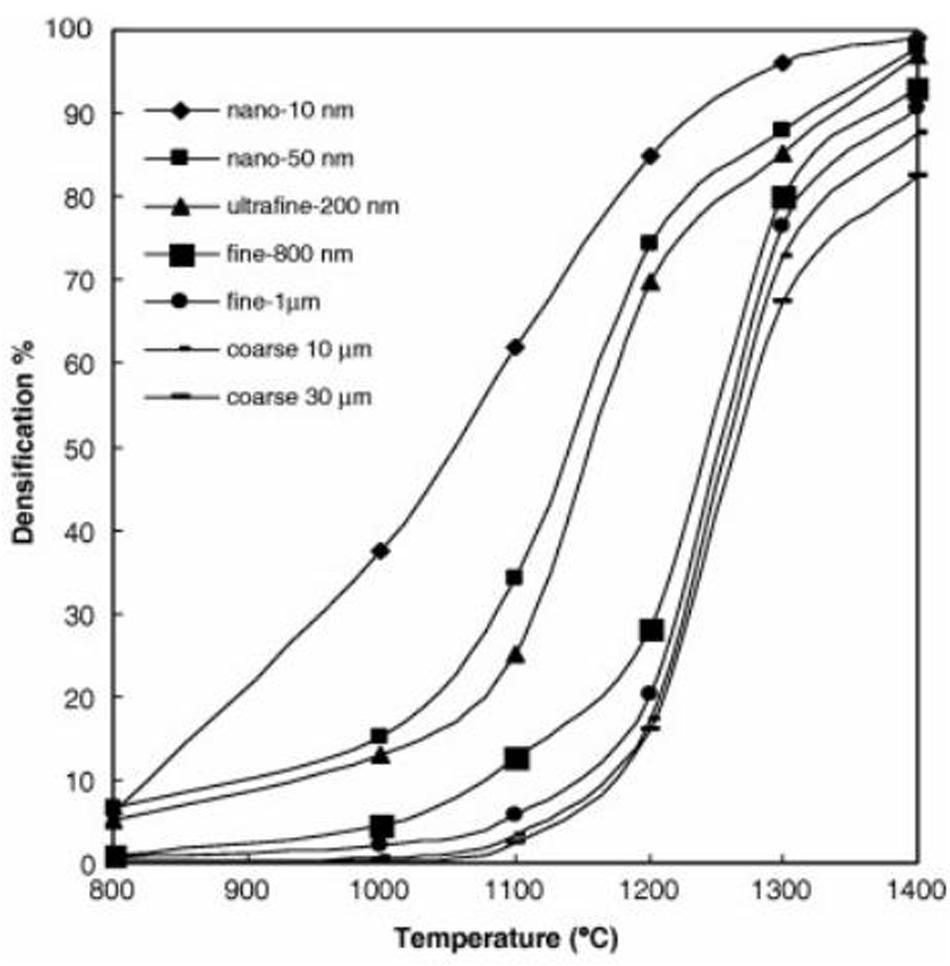
Figure 3. Relationship between sintering temperature and sintering densification of powders with different initial particle sizes (Maheshwari et al., 2007) [Figure 2 of Maheshwari et al. (2007), Copyright Amer Powder Metallurgy Inst].
Some researchers have proved that ultrafine WC powders have better activation in plating binder-phase mental coat on the WC particles. Such as, Luo et al. (2011) have studied the activation technique of ultra-fine powders and prepared a uniform Ni-coated WC composite powder, taking less than 1 μm WC as a matrix. As shown in Figure 4B, ultrafine WC powders after ultrasonic-assisted electroless plating appear step-like defects on the surface of WC particles. These defect make nucleation and growth of Ni cell generate on the activated WC particle surface more effectively. Further studies showed that the thinner the WC powder, the better the Ni coating (Luo et al., 2011; Chen H. Y. et al., 2017).
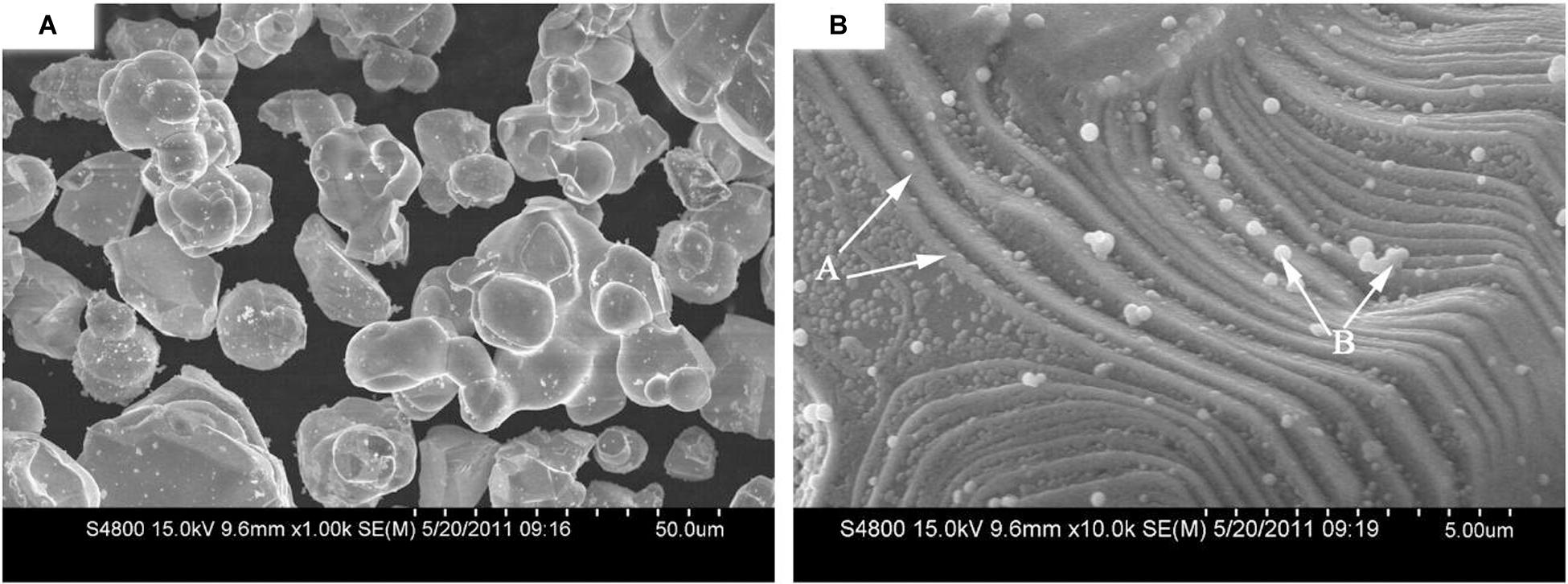
Figure 4. Surface appearance of Ni-coated WC powders after 30 min of electroplating: (A) Low-power image; (B) high-power image (The Ni particles prioritized nucleation and growth at the surface step defects (arrow A in panel B). The uncompleted Ni coating showed a cell structure with some free-formed Ni particles (arrow B in panel B) (Luo et al., 2011) [Figure 3 of Luo et al. (2011), Copyright Elsevier B.V.].
Some scholars have carried out further theoretical studies to figure out how ultra-fine WC powders can improve the comprehensive performance of cemented carbides (Chuvil’deev et al., 2015; Postek and Sadowski, 2018). The most consistent view at present is that the use of ultra-fine WC powders decreases the average thickness of the bonding phase, which increases the dispersion of the former through the latter and, thus, improves the strength and toughness of the resulting alloy (Zhang et al., 2012). Several studies have focused on the preparation method and industrial production of ultra-fine WC (Xu et al., 2018; Luo et al., 2019). A number of methods to prepare ultra-fine WC powder, such as mechanical alloying (Li et al., 2019), in situ carburizing reduction (Li et al., 2019), direct reduction of carbonization (Chen L. J. et al., 2018), gas-phase reaction synthesis (Zhang et al., 2018), and spray conversion (Guo et al., 2015), have been proposed. These methods can generally be summarized into three synthesis categories, namely, solid-phase methods, vapor-phase methods, and liquid-phase methods, based on the initial state of the reactants.
Solid-Phase Method
When preparing tungsten carbide by the solid-phase method, WO3 is usually taken as the W source. Carbonization of WO3 can be divided into reduction carbonization and direct carbonation according to the generation of elemental W; it can also be divided into mechanical alloying and high temperature carbonization according to the temperature of carbonization.
Reduction Carbonization
Reduction carbonization is a traditional WC preparation process that is commonly used for the high-volume industrial production of WC (Borchardt et al., 2012). A typical synthesis route is: W source [Ammonium paratrungstate (APT) or ammonium metatungstate (AMT)] calcination → WO3 → hydrogen reduction → ultrafine W powders → carbonization → ultrafine WC powders.
Ma and Zhu, 2010 calcined a mechanically activated WO3 and graphite mixture at 1215°C under vacuum conditions and achieved the solid C thermal reduction of WO3 to nano-WC particles. The specific preparation process was as follows: WO3 (purity 99.9%) and graphite (purity 99%) powders as raw materials were mixed at a molecular weight of 1:4 and then ball milled under an Ar atmosphere for 10 h. The composite powder was placed in a ceramic vessel, first heated to 741°C and then heated to 1215°C in a vacuum tube furnace at a rate of 10°C/min, finally kept in the temperature for 1 h.
Ma and Zhu (2010, analyzed ultrafine WC particles’ generation based on homogeneity increase and associated decrease during the diffusion period of mechanical milling. Besides, formation of some intermediates, such as WO2.72 and WO2, are also responsible for the successful production of ultra-fine WC powders. Thermodynamic calculations for reactions that may occur during the calcination process have accurately detected the reaction process and generation phase, and the results are shown in Figure 5. As the calcination temperature increases, WO3 is reduced to other lower-valence WO3 types, such as WO2.72 and WO2. These low valence WO3 forms are called Magneli-phase WO3 (meta-stable phase WO3) (Ma and Zhu, 2010; Lee et al., 2019). When the temperature is higher than 273, 346, or 489°C, the solid-phase carbothermal reaction of WO3 generates these Magneli phases. Magneli-phase WO3 is reduced to elemental W by graphite when the temperature is 599–794°C. X-ray diffractometry (XRD) of the samples was carried out at 741°C, and only the diffraction peaks of mesophase WO2.72, WO2, and W were found; no diffraction peaks of WO3 were observed, likely due to the initial reaction temperature of 599–644°C, which fully reduces the metal oxide to WO2.72, WO2, and W (Ma and Zhu, 2010). The peaks of WO2.72 and WO2 were still present at 741°C because the initial reaction temperatures of WO2.72 and WO2 are 726–754°C and 747–794°C, respectively, or slightly higher than 741°C. As the temperature continues to increase, W reacts with graphite to generate WC. The reaction route can be summarized as WO3 + C→W + WO2 + WO2.72 + C→WC (Ma and Zhu, 2010).
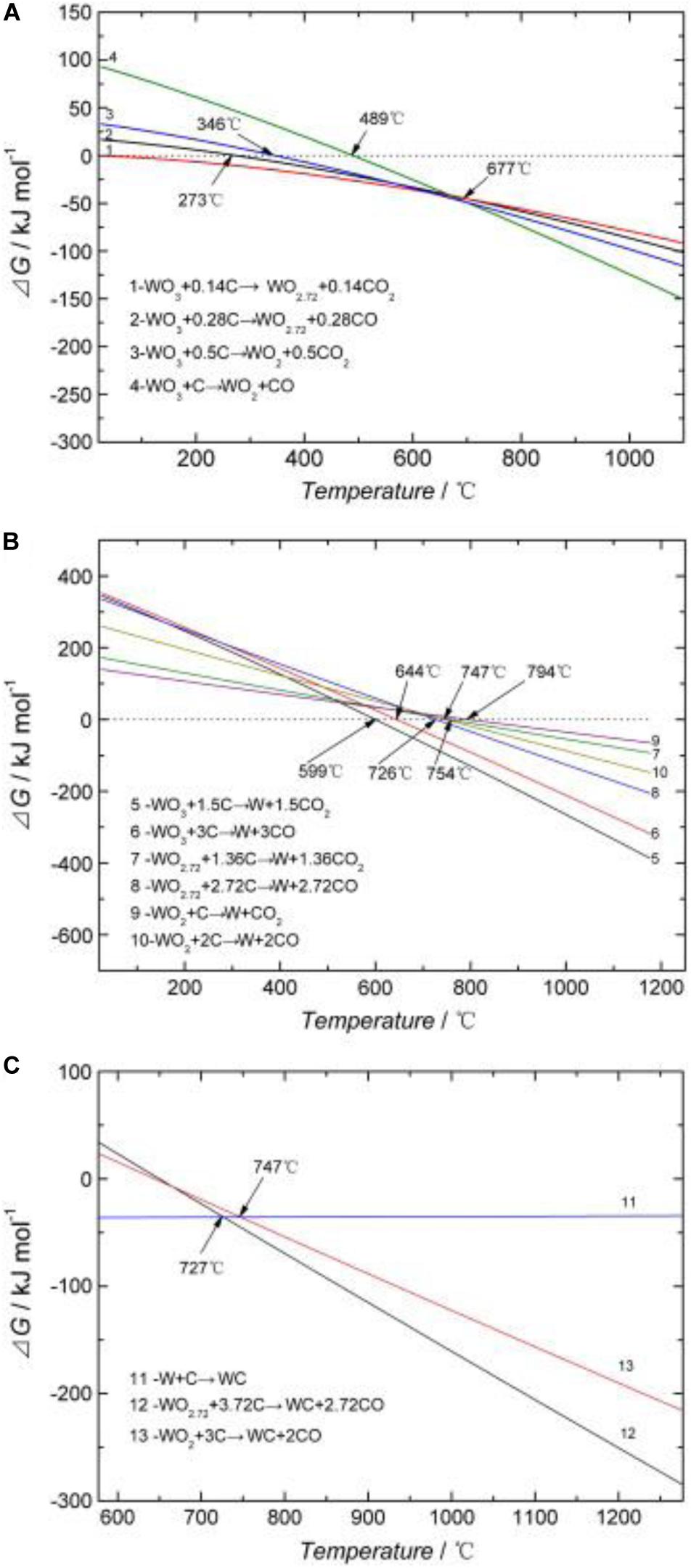
Figure 5. Changes of ΔG with the temperature of different tungsten oxides when reacting with graphite: (A) Magneli-phase WO3 formation; (B) W formation; (C) WC formation (Ma and Zhu, 2010) [Figure 4 of Ma and Zhu (2010), Copyright Elsevier Ltd.].
Using ammonium paratungstate (APT) as a raw material, Ryu et al. (2009) prepared nano-WC powders by using the thermal plasma method. The preparation process was divided into three stages:
Stage 1: Thermal decomposition of ammonium paratungstate (APT):
Stage 2: Hydrogen reduction:
Stage 3: CH4 carbonization:
In the thermal plasma reaction system, APT generates a nano-WC1–x powder which the powders sometimes contain a small amount of the W2C phase after the period of thermal decomposition, reduction, and carburization. By using this way to prepare WC, the particle size of the prepared WC1–x powder is less than 20 nm. The synthetic powder is heated by hydrogen to fully carburize the WC1–x and W2C phases to WC. After removing excess C, we could obtain WC powders whose particle size is less than 100 nm, as shown in Figure 6.
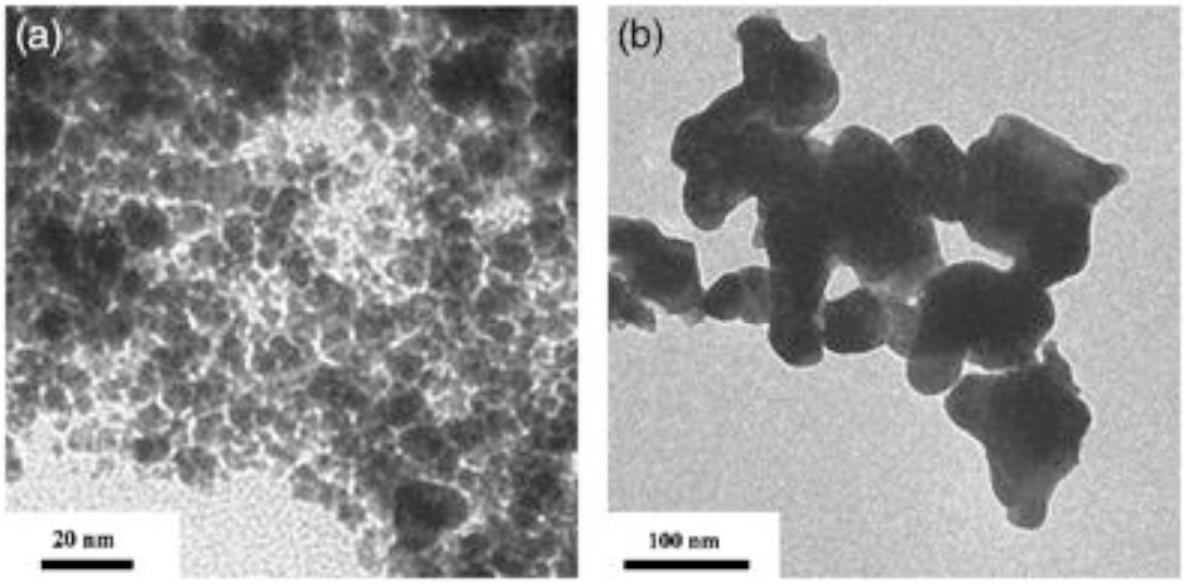
Figure 6. TEM micrographs of WC1–x powders obtained (a) from the plasma reactor and (b) after 3 h of hydrogen heat treatment at 900°C (Ryu et al., 2009) [Figure 8 of Ryu et al. (2009), Copyright The American Ceramic Society].
Direct Carbonization
Direct carbonization to prepare WC is known as a one-step method. Researchers have developed different techniques for the one-step preparation of WC powder. For example, Won et al. (2010) prepared WC powders with particle size of 50–100 nm through carbonization at a high temperature by using WO3 and C powder as raw materials and NaN3 as a combustion agent (Won et al., 2010; Lin et al., 2013). Lee et al. (2003) converted WO3 into WC by heating WO3 to 300–700°C in He atmosphere; here, −HX, −NaX, and −KX were added to WO3 powder as catalysts, and CO gas was used as the C source. He and Tang (2011) had prepared ultra-fine WC powders with particle size of 0.3 μm through direct reduction and carbonization of AMT by using carbon-black as the C source in N2 atmosphere. The direct carbonization method utilizes the reducibility of C to conduct direct reduction of WO3 and generate WC. During the reduction process, only Magneli phases W is generated, and eventually WC powder particles are difficult to gather. In the traditional method, W powder is prepared and then carbonized to generate WC via hydrogen reduction of WO3. During the reduction process, hydrates of WO3, such as WO2(OH)2 and WOx⋅H2O, are generated, and these compounds cause W powder particles to grow. Thus, the carbonized WC powder yields large particles that must be ground to obtain a fine WC powder (Venables and Brown, 1996; Gu et al., 2002).
Wang et al. (2006) invented a supercritical CO2 heat treatment method to prepare WC based on the direct carbonation method. The reaction route of this method is shown in Figure 7, and the reaction could divide into two stages. In Stage 1, dense CO2 is reduced to graphite sheets by Na, and metal W is oxidized into WO3 by excess CO2; in Stage 2, WO3 reacts with the graphite sheets and then converted into WC.
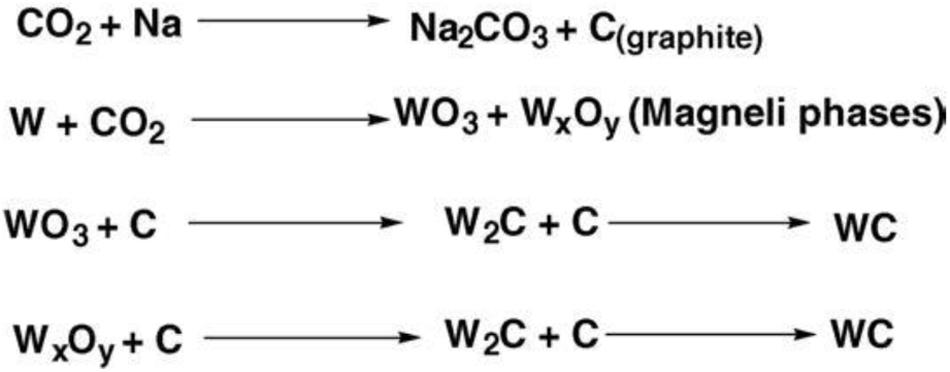
Figure 7. Reaction scheme of the CO2 heat treatment method (Wang et al., 2006) [Scheme 1 of Wang et al. (2006), Copyright Elsevier B.V.].
Based on the reaction route described above, Wang et al. realized the carbonization of W powder at a moderate temperature of 600°C by placing W powder, dry ice, and Na metal in an autoclave, which was then sealed and heated in a heating furnace to 600°C at a heating rate of 10°C/min with insulation for 20 h. Black solid products were obtained when the furnace was finally cooled to room temperature. Dilute HCl was added to the product, which was subsequently heated to remove Na2CO3. Finally, the solid product was washed with distilled water and dried at 80°C for 2 h. The resultant WC powder is shown in Figure 8; Wang et al. (2006).
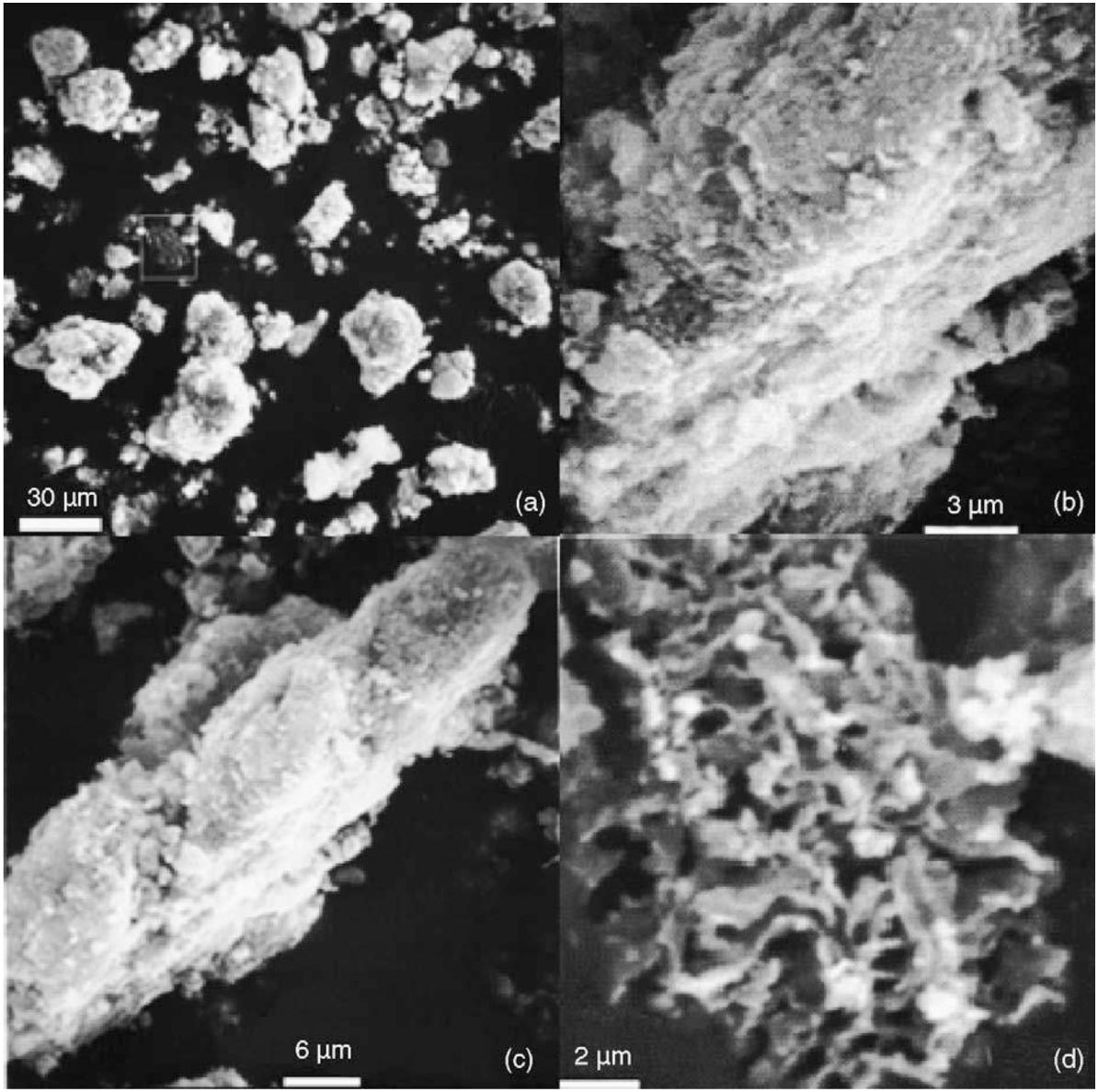
Figure 8. (a) Low-resolution SEM image of the WC sample, (b) cross-sectional morphology of typical WC particles, (c) surface morphology of WC particles, and (d) SEM image of the residual graphite network (Wang et al., 2006) [Figure 2 of Wang et al. (2006), Copyright Elsevier B.V.].
Mechanical Alloying
Mechanical alloying involves the high-speed and long-running transmission of mechanical energy to the powder through a high-energy ball mill to improve the powder activity. During the ball milling process, the ball in the milling jar repeatedly collides with the powder, thus subjecting it to various forces, such as impact, compression, friction, and shearing. The powder is further refined, crushed, and cold welded into dispersed ultra-fine particles and then alloyed at room temperature. The basic principle behind powder alloying at room temperature is the repeated mixing, crushing, and cooling of weld powder particles through high-energy ball milling. The mixed powder in the ball mill can form high-density dislocations, and the particles are gradually refined to the nanoscale level. Increases in powder activity accelerate the mutual diffusion of atoms. Under certain conditions, alloy phase nuclei are formed through ball milling and gradually grow into an alloy phase until all elemental powders are consumed (Dai et al., 2013; Maat et al., 2018; Sadeghi et al., 2018).
By using the ball-milling method, Wu et al. (2009) mixed pure WO3, graphite, and Mg powder according to a certain atomic ratio at room temperature and characterized the resulting powder through SEM, XRD and TEM. As shown in Figure 9, the XRD peaks of MgO and WC could be clearly detected after 4.5 h of ball milling. These results show that a redox reaction occurs between the WO3 powder, Mg, and graphite during ball milling to form MgO and WC via the following reaction:
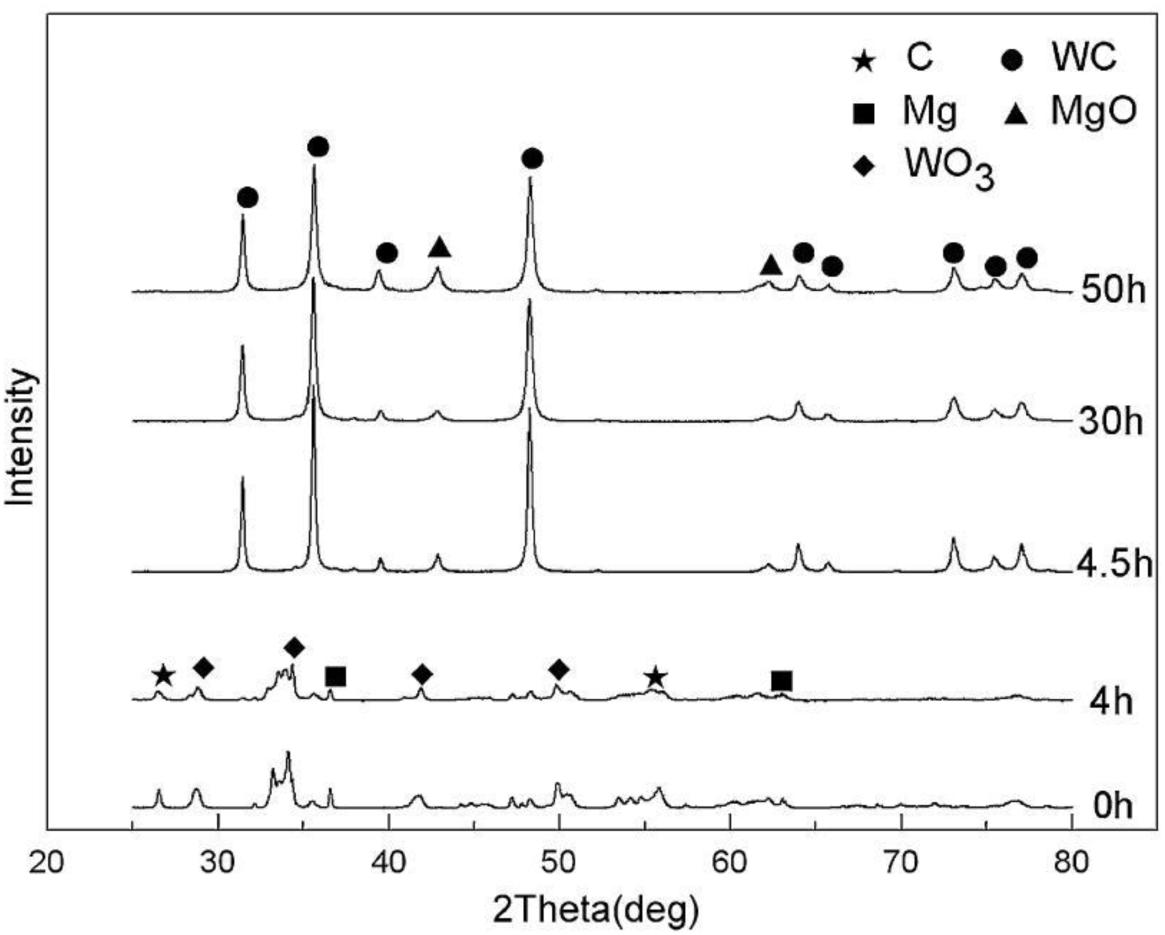
Figure 9. XRD patterns of composite powders at different ball milling time (Wu et al., 2009) [Figure 1 of Wu et al. (2009), Copyright Elsevier B.V.].
The powder was further refined with ball milling going on. As shown in Figure 10, after 80 h ball- milling, nanocrystalline WC particles (25 nm) were embedded in the fine MgO matrix, thus forming a nanoscale MgO–WC composite powder with diameters close to 100 nm. This process could overcome the shortcomings of the high-cost preparation of WC by using MgO instead of Co, Ni, and Fe which are the conventional binder. Besides, the newly developed binder could be used for other carbide substrates.
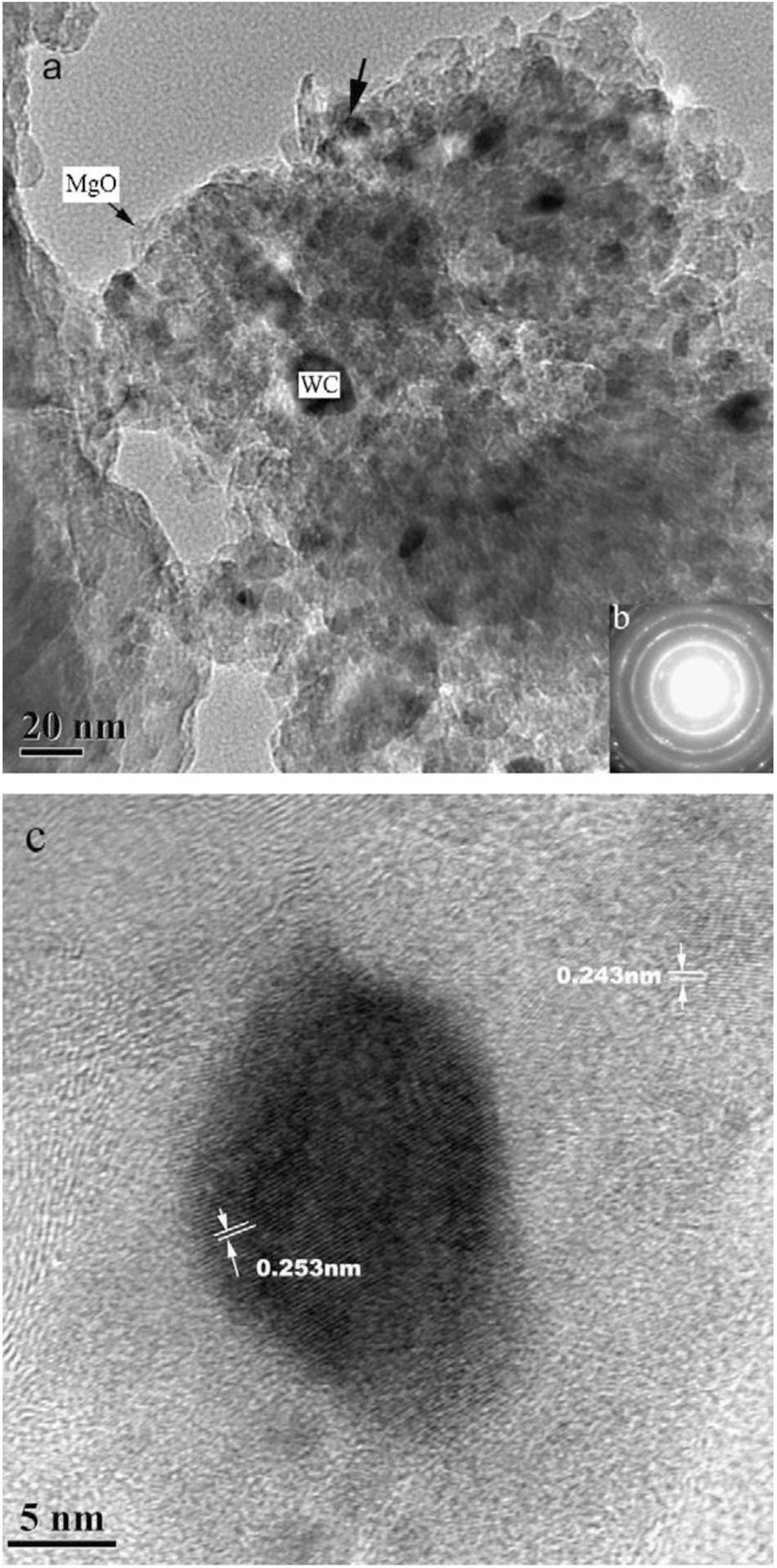
Figure 10. High-power microscopic image of WC powders after 80 h of ball milling: (a) High power micrograph; (b) the selected-area diffraction pattern; (c) enlarged micrograph of selected-area (Wu et al., 2009) [Figure 3 of Wu et al. (2009), Copyright Elsevier B.V.].
High-Temperature Carbonization
The high-temperature carbonization of solid metal W essentially involves the diffusion reaction of C in W. When the temperature is above 1000°C, C atoms can be soluble into W particles to form WC phase which the process called C diffusion reaction, which is also the basic principle in high-temperature carbonization. C diffusion is based on the formation of a thin polycrystalline WC layer around W particles; this layer gradually develops toward the core, thus enabling the growth of polycrystalline WC by extending toward the center of the W particles and moving to the grain boundary of WC (Yang et al., 2015). Although the principle of high-temperature carbonization of metal W is similar, researchers have developed different methods to prepare ultra-fine WC. For instance, Li (2013) used AMT and violet tungsten as raw materials to prepare W powders with a minimum particle size of about 30 nm through hydrogen reduction; thereafter, the scholar prepared a nano-WC powder with a minimum particle size of 60 nm after carbonization at 1200°C and microwave heating (Li, 2013). Chen Z. et al. (2017) combined C with W, Co, Cr3C2, and VC as raw materials and then placed this mixture into a combustion reaction chamber for carbonization with burning; finally, WC powders with a grain size of 30–100 nm were obtained.
Wang et al. (2018) studied the effects of as on the growth of WC powders by adding As element into the high-temperature carbonization process of nano-W. The experimental process is as follows: First, the W–As composite powder was mixed with C black at 100 rpm for 1 h by a planetary mill. Next, the mixed powder of W, As, and C was placed in a graphite boat and placed into a tube furnace for high-temperature carbonization at 1300, 1400, 1500, and 1600°C with a controlled heating rate of 5°C/min.
Figure 11 shows the XRD patterns of the samples obtained by carbonization of W powder and W–As powder at 1300 and 1400°C. The diffraction peak shown in Figure 11A reveals the presence of a W2C phase in the WC powder after carbonization of the W powder at 1300°C. As shown in Figure 11C, W2C phase was not observed in the diffraction peak after the carbonization at 1400°C, contrasting to Figure 11A, which indicate that pure W powder was not fully carbonized at 1300°C but was totally carbonized at 1400°C. According to the diffraction peaks in Figures 11B,D, only WC could be detected, and no W2C phase was found. Comparison of the peaks of the two composite powders after carbonization at high temperature reveals that addition of As have decreased the temperature of complete carbonization (Wang et al., 2018).
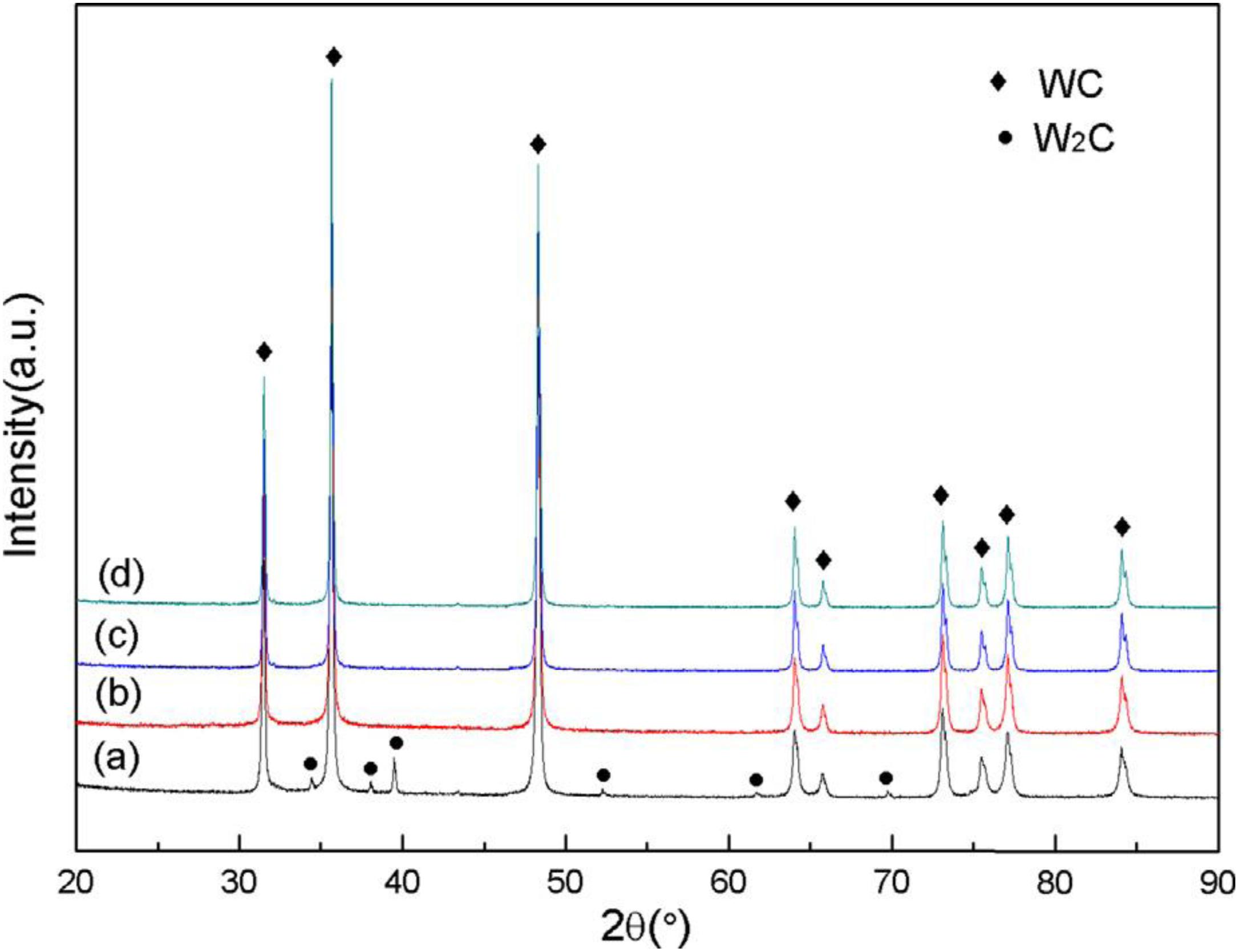
Figure 11. XRD patterns of: (a) W powder at 1300°C; (b) W-As powder at 1300°C; (c) W powder at 1400°C; (d) W-As powder at 1400°C (Wang et al., 2018) [Figure 3 of Wang et al. (2018), Copyright Elsevier B.V. and The Society of Powder Technology Japan].
As shown in Figure 12, the average particle size of the WC–As powder is less than that of WC at the same temperature, which indicates that addition of arsenic has decreased the concentration of WC during the carbonization process. Wang provided the following explanation for this phenomenon: during carbonization, W and As generate a WAs2 mesophase, which attaches to the grain boundaries of WC and hinder the growth of WC grains through migration of these boundaries. Therefore, uniform WC composite powders could be obtained even at high carbonization temperatures.
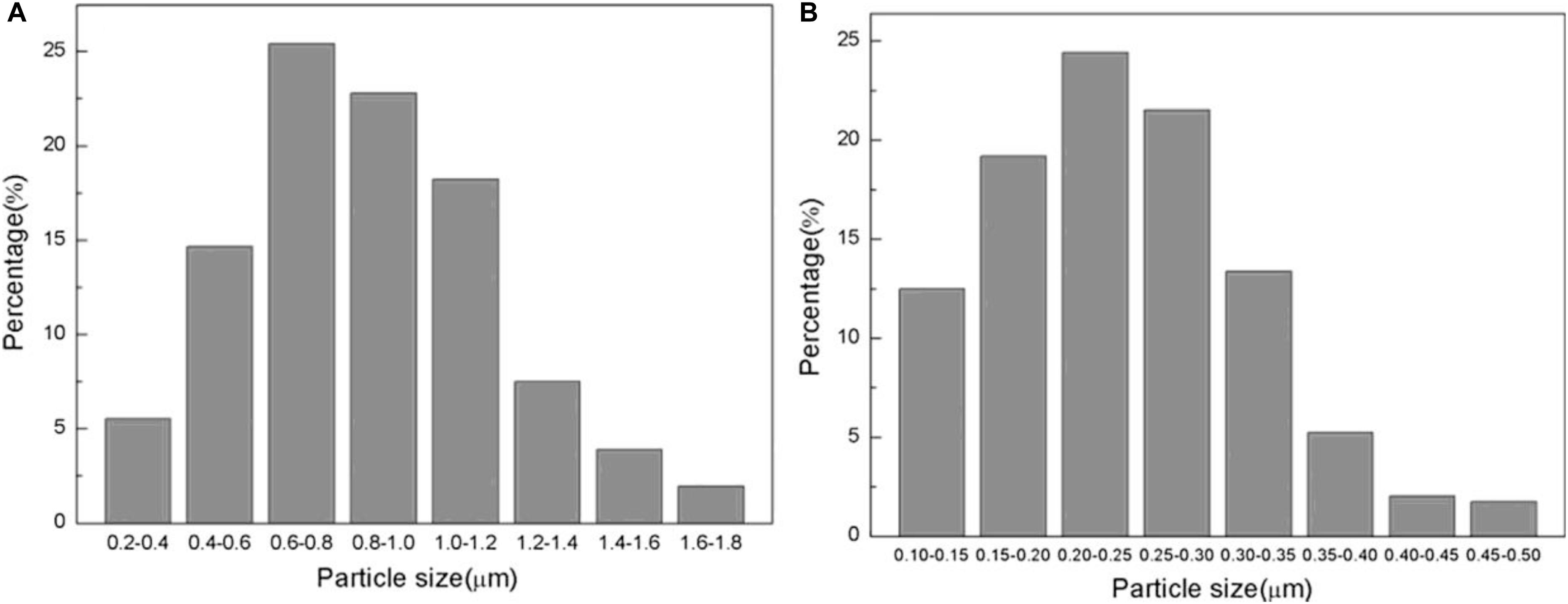
Figure 12. Particle distributions of (A) WC and (B) WC-As powders after 2 h of carbonization at 1400°C (Wang et al., 2018) [Figure 13 of Wang et al. (2018), Copyright Elsevier B.V. and The Society of Powder Technology Japan].
Liquid-Phase Method
The traditional liquid-phase method refers to the coprecipitation of tungstate and cobaltate in the liquid phase, and then makes the sediment completely decomposed at a low temperature. The precursor of the highly dispersed and highly active W–Co compound is prepared to generate ultra-fine WC–Co composite powders through reduction and carbonization in a fixed or fluidized bed. This method is also called chemical precipitation (Yang et al., 2018). Compared with other methods, chemical precipitation presents the advantages of simple equipment and easy process control; moreover, the prepared nano-WC–Co powders have small particle size, uniform distribution, and high reaction activity. However, chemical precipitation method also have a number of issues need to be overcome, such as introduction of impurities during the preparation process, physical statement change of the generated sediment, high difficulty in filtering and washing the product, high preparation cost, and poor scaling to batch production. All advantages mentioned above have limited the technique’s applications (Fan et al., 2013).
Several researchers have developed a solvothermal method to prepare WC powder. Solvothermal method is a synthetic method that uses organic or non-aqueous solvents as solvents to react the original mixture with the solution at a certain temperature under the spontaneous pressure in a closed system (Hosokawa, 2016).
Preparation of WC powder via the solvothermal method generally takes WO3 as the W source and C-based organic solvents as the C source. The raw materials are mixed proportionally and then react by heating to 500–800°C after addition of a reducing agent to the reactor. This method can be used to generate WC at low temperatures, but the subsequent processing of reaction products is often complex. Indeed, high-purity WC can only be obtained after several cycles of removal of the reducing agent, distillation drying, immersion, and filtration with ethanol (Kumar et al., 2010).
Zeng et al. (2008) took Mg as a reducing agent, anhydrous ethanol and WO3 as C and W sources, respectively. He synthesized WC nanocrystals using a simple solvothermal method. The effect of reaction temperature on the synthesis of WC was discussed. Figure 13 shows the XRD patterns of products obtained at different reaction temperatures. There are WO3 and MgWO4 existing at different temperature. The peaks of WO3 disappear at 550°C and the peaks of MgWO4 disappear at 650°C. With the increase of temperature, the peaks of WO3 and MgWO4 disappeared gradually, while the peak intensity of WC increased obviously. The activity of C and W atoms increased with the increase of reaction temperature which made the reaction more completely and WC crystallization more completely. The pressure produced in the high pressure reactor greatly reduces the synthesis temperature of WC. When the temperature was 500°C, hexagonal WC phases with particle sizes of about 40–70 nm could be synthesized.
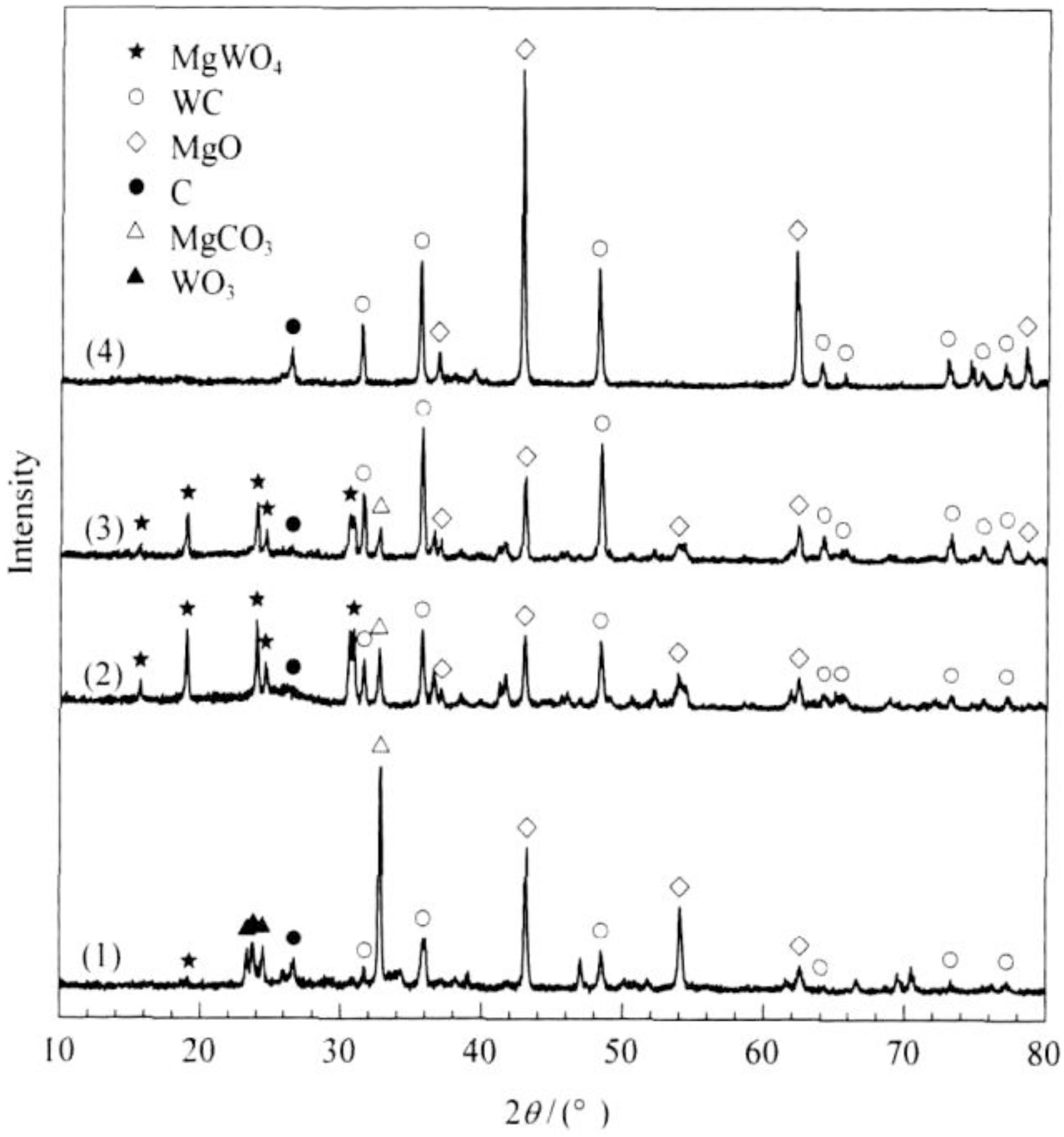
Figure 13. XRD patterns of WC powders synthesized at different temperatures for 15 h: (1) 500°C; (2) 550°C; (3) 600°C; (4) 650°C (Zeng et al., 2008) [Figure 1 of Zeng et al. (2008), Copyright Science Press].
Singla et al. (2015) prepared WC nanoparticles with a particle size between 30–80 nm by using Mg, acetone (C3H6O), and WO3 as raw materials. During the reaction, acetone was used as a hot solvent and C source, Mg acted as the catalyst, and the mixed raw material was placed in an electric furnace to heat to 600°C and kept warm for different periods of time. Then, it was cooled to room temperature using an autoclave. The product was washed with dilute HCl to remove MgO, leached, and washed with distilled water several times to remove the acid. Finally, the product was washed with acetone and then dried under vacuum at 100°C. The synthesized WC powder had plate- or sphere-shaped grains that dispersed without aggregation, and ultra-fine WC powders could be obtained without pulverization. However, because the oxygen content of the powders increased with increasing insulation time, control of the insulation time is the key to prepare high-quality WC via this method.
Vapor-Phase Method
The chemical vapor-phase synthesis (CVS) of WC powder refers to the preparation of WC powders via hydrogen and hydrocarbon vapor reduction precursors (Dushik et al., 2018). If WCl6 is used as a precursor, CH4 and hydrogen are taken as the C source and reducing agent, respectively, and the reaction temperature is set to 1200°C, the following reaction takes place (Aneela and Srikanth, 2018):
WCl6, WF6, and W(CO)6 are preferred W sources for preparing WC because these raw materials have a low volatilization temperature and are easy to reduce or thermally dissociate by hydrogen; hydrocarbon gases often used as C sources such as methane, ethylene and propane (Wu et al., 2018). The preparation of WC powders via the vapor-phase method can result in uniform and controllable particle sizes; moreover, because no other solid products are generated, the WC purity is usually higher than that obtained from other methods. However, this kind of method requires raw materials and substrates with high initial purity, and the use of flammable gases presents significant risk during mass production.
The plasma chemical vapor deposition method is a widely used to prepare nano-WC. The raw material is quickly heated to above 1500°C using plasma as the heat source, and the raw materials decompose, react, and synthesize the product. The raw materials are generally W or WO3, and the C source is usually CH4 or acetylene. The plasma chemical vapor deposition method can also be used to produce other nano-powders, such as TiC, TiN, and Si3N4 (Morimitsu et al., 2013; Chen L. et al., 2018).
Using WCl6 as raw materials, Sohn et al. prepared nano-WC by plasma heating to ultra-high temperature. In this experiment, H2 and CH4 were used as reducing and carburizing agents, respectively. WC1–x with a particle size of less than 30 nm was obtained. The particle size of this product increased with increasing plasma transmitter power and decreasing plasma flow rate. Hydrogen was used for the heat treatment of the WC1–x powder. The C content was reduced to stoichiometric levels and the WC1–x phase was fully carburized to generate the WC phase. However, the particle size of the powder increased from 30 nm to approximately 100 nm after hydrogen heat treatment, as shown in Figure 14; Sohn et al. (2007).
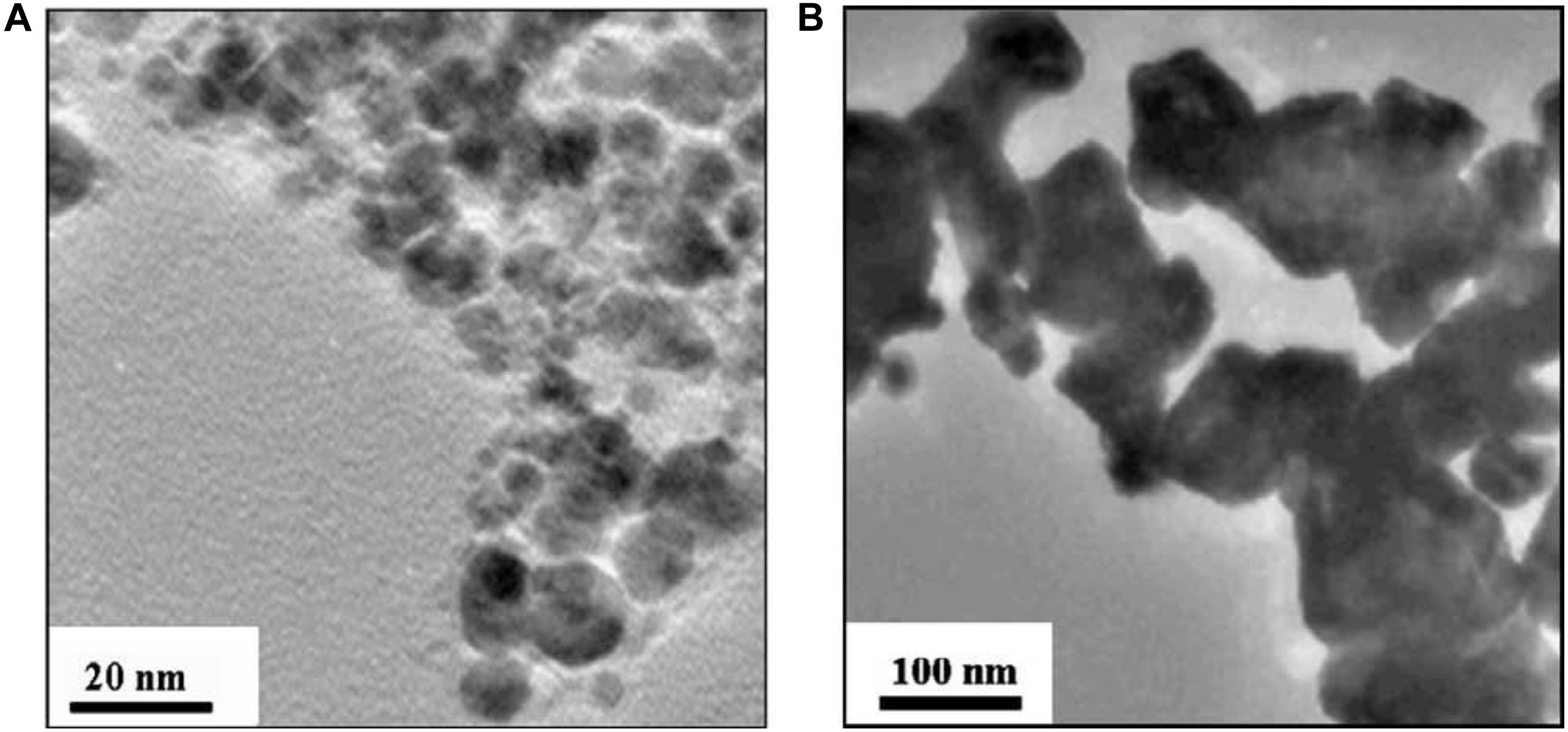
Figure 14. TEM micrographs of (A) WC1–x powder synthesized by plasma-assisted CVS from WCl6 and (B) WC powders obtained after 5 h of hydrogen heat treatment of WC1–x powders at 900°C (Sohn et al., 2007) [Figure 1 of Sohn et al. (2007), Copyright Elsevier Ltd].
Ryu et al. (2008) taking WCl6 as a precursor, reduced and carbonized it by using CH4-H2 mixed gas, and then prepared nano-WC powder by the thermal plasma method. His team also studied the effects of other factors on the product composition and particle size, such as molar ratio of the reaction gas, plasma torch power, plasma gas flow rate and addition of a secondary plasma gas. Results showed that nano-WC1–x powder containing WC and W2C phases could be synthesized by using the thermal plasma method with WCl6 and CH4 as the W and C sources, respectively. The content of W2C in the product decreased with increasing plasma torch power and plasma gas flow rate. In addition, the particle size of WC1–x was affected by the plasma torch power, plasma gas flow rate, and addition of a secondary plasma gas (H2) but is not subject to the CH4 concentration within the range tested. The generated WC1–x and W2C phases were carburized into the fully carbidized WC phase, and excess C in the product was removed completely by hydrogen heat treatment at 900°C. The particle size of WC1–x obtained by the thermal plasma process was less than 20 nm, and the particle size of the WC powder obtained after hydrogen heat treatment was between 40 and 100 nm. Since the plasma process can operate continuously, it is also suitable for the mass production of nano-WC powders.
Table 1 lists different WC preparation methods in the literature. Compared with the liquid-phase and vapor-phase method, the solid-phase method on preparing WC powders have a more wider range of particle size which means that the accuracy of WC particle size is not easy to control in the period of carbonization by the solid-phase method. Except for mechanical alloying, the intermediate products of other solid-phase methods are all related to tungsten compounds which could be carbonize completely by promoting the temperature of carbonization.
Conclusion and Expectations
In general, high-quality ultra-fine WC powders are often evaluated with some characteristic like these: (a) Tungsten needs to be completely carbonized. The amount of material that is not completely carbonized, such as WxOy and W2C, should be as small as possible; (b) The content of impurities should be as low as possible; () The particle size distribution should be as uniform as possible. The precipitation methods which have mentioned in the literature are able to make the WC powders meet these characteristics, but some of them have some problems in the period of preparation.
Using reduction carbonization to prepare ultra-fine WC powders needs to generate simple-substance W, and then make W powders carbonize to WC powders. The particle size of WC depends on the W powder. If size of W particle during preparation of WC was not as small as possible, WC nanoparticles may be failed to produce. The other methods in the Soild-phase methods, which have taken Na, Mg, and, As as catalyst or inhibitor, WC can be prepared directly, but the effect of additions on crystallization of tungsten carbide during the sintering period need to be made further research. Besides, using solid-phase methods to prepare WC often proceed in the high temperature environment and need to keep the high temperature for a long time in order to completely carbonize. However, the liquid-phase method could prepare WC powders at low temperatures. Zeng et al. (2008), researchers achieved preparation of WC at 500°C which had greatly decreased the temperature of carbonization. But the liquid-phase method in preparing WC powders often generates other by-products. In order to remove these intermediates, it is necessary to add other solvents to dissolve them which may increase the difficulty of WC preparation. The vapor-phase method could get high-purity ultrafine WC powders. But the cost of large-scale preparation of WC by vapor-phase method is higher than others which limit its application and development. Compared with the vapor-phase method, the solid-phase reduction carbonization method has potential industrial application. Because it is much closer to current commercial production mode of tungsten carbide, which just replaces graphite to CH4 as the C source comparing to the traditional method to produce WC.
Throughout all methods mentioned above, useful studies have been made on the option of W and C sources around the refinement of WC particles, which has laid a foundation for the industrial production of ultrafine WC powders. The preparation technology of ultra-fine WC powders is an interesting branch of nanotechnology that shows the importance of this field in the research and development of new materials. Although different methods have been developed to prepare nano-WC powder, the approaches proposed are often limited to laboratory-scale production. Thus, the large-scale industrial production of ultra-fine WC powders remains a very important direction for future research.
Author Contributions
Y-CW, YY, and LL drafted the manuscript. Y-CW and LL supervised the experiments. X-YT, LL, XZ, X-YZ, QX, and J-GC were involved in the data analysis and discussions.
Funding
This work was supported by the National Key Research and Development Program of China (2017YFE0302600), the National Natural Science Foundation of China (21671145), the State Key Laboratory of Powder Metallurgy, the Foundation of Laboratory of Non-ferrous Metal Material and Processing Engineering of Anhui Province (15CZS08031), and the 111 Project (B18018).
Conflict of Interest
The authors declare that the research was conducted in the absence of any commercial or financial relationships that could be construed as a potential conflict of interest.
References
Akhtar, F., Humail, I. S., Askari, S. J., Tiana, J., and Shijua, G. (2007). Effect of WC particle size on the microstructure, mechanical properties and fracture behavior of WC-(W, Ti, Ta) C-6 wt% Co cemented carbides. Int. J. Refrac. Met. Hard Mater. 25, 405–410. doi: 10.1016/j.ijrmhm.2006.11.005
Aneela, R., and Srikanth, V. S. (2018). Thermodynamic aspects of co-formation of different condensed phases from CH4-WCl6 gas mixtures diluted in H2. Appl. Phys. A Mater. 124, 9–14.
Borchardt, L., Hoffmann, C., Oschatz, M., Mammitzsch, L., Petasch, U., Herrmannb, M., et al. (2012). Preparation and application of cellular and nanoporous carbides. Chem. Soc. Rev. 41, 5053–5067.
Chen, L., Chen, N. N., Wu, H. M., Li, W., Fang, Z., Xu, Z., et al. (2018). Flexible design of carbon nanotubes grown on carbon nanofibers by PECVD Chock for enhanced Cr(VI) adsorption capacity. Sep. Purif. Technol. 207, 406–415. doi: 10.1016/j.seppur.2018.06.065
Chen, L. J., Xie, Z. H., Wang, R. X., Tian, L., and Nie, H.-P. (2018). Reduction carbonization mechanism analysis of tungsten oxide powder and preparation of ultrafine tungsten carbide powder. Rare Met. Cement. Carb. 46, 14–20.
Chen, Z., Qin, M. L., Chen, P. Q., Huang, M., Li, R., Zhao, S., et al. (2017). WC-Co-Cr3C2-VC nanocomposite powders fabricated by solution combustion synthesis and carbothermal reduction. Ceram. Int. 43, 68–72.
Chen, H. Y., Wang, Z. C., Luo, L. M., Liu, Z., Zhibiaob, T., and Yuchengac, W. (2017). Effect of Ni Content on Microstructure and Properties of WC-Ni Composites Prepared by Electroless Plating and Powder Metallurgy. Rare. Metal. Mat. Eng. 46, 2820–2824. doi: 10.1016/s1875-5372(18)30013-4
Chuvil’deev, V. N., Blagoveshchenskii, Y. V., Sakharov, N. V., and Boldin, M. (2015). Preparation and investigation of ultrafine-grained tungsten carbide with high hardness and fracture toughness. Dokl. Phys. 60, 288–291. doi: 10.1134/s1028335815070095
Dai, L. Y., Lin, S. F., Chen, J. F., and Wang, W. C. (2013). Synthesis of nano-WC by high-energy ball milling. Mater. Sci. Forum 745, 327–334. doi: 10.4028/www.scientific.net/msf.745-746.327
Dushik, V. V., Rozhanskii, N. V., Lifshits, V. O., Rybkina, T. V., and Kuzmin, V. P. (2018). The formation of tungsten and tungsten carbides by CVD synthesis and the proposed mechanism of chemical transformations and crystallization processes. Mater. Lett. 228, 164–167. doi: 10.1016/j.matlet.2018.06.003
Emani, S. V., Wang, C. L., Shaw, L. L., and Shaw, L. L. (2015). On the hardness of submicrometer-sized WC-Co materials. Mat. Sci. Eng. A Struct. 628, 98–103. doi: 10.1016/j.msea.2014.12.106
Fan, P., Fang, Z. Z., and Guo, J. (2013). A review of liquid phase migration and methods for fabrication of functionally graded cemented tungsten carbide. Int. J. Refract. Met. Hard Mater. 36, 2–9. doi: 10.1016/j.ijrmhm.2012.02.006
Gu, G., Zheng, B., Han, W. Q., Roth, S., and Liu, J. (2002). Tungsten oxide nanowires on tungsten substrates. Nano Lett. 2, 849–851. doi: 10.1021/nl025618g
Guo, S. D., Yang, J. G., Lü, J., Zhu, E., Chen, H., and Zhang, X. (2015). Morphology of nanophase WC/6Co composite powder prepared by spray conversion method. Chin. J. Rare Metals 39, 43–48.
He, L. M., and Tang, S. C. (2011). Preparation of ultrafine WC powders by direct reduction and carbonization process. Min. Metallurg. Eng. 31, 57–63.
Hosokawa, S. (2016). Synthesis of metal oxides with improved performance using a solvothermal method. J. Ceram. Soc. Jpn. 124, 870–874. doi: 10.2109/jcersj2.16109
Kumar, A., Singh, K., and Pandey, O. P. (2010). Optimization of processing parameters for the synthesis of tungsten carbide (WC) nanoparticles through solvo thermal route. Phys. E. 42, 2477–2483. doi: 10.1016/j.physe.2010.06.002
Lee, J. D., Jun, J. H., and Park, N. K. (2003). The effect of zeolite NaX, HX and KX on the reduction-carburization of WO3. Appl. Chem. 7, 253–256.
Lee, Y. J., Lee, T. H., and Soon, A. (2019). Phase stability diagrams of group 6 magneli oxides and their implications for photon-assisted applications. Chem. Mater. 31, 4282–4290. doi: 10.1021/acs.chemmater.9b01430
Li, J., Ni, J. J., Huang, B. X., Liao, S., Wang, C., Luo, W., et al. (2019). Long-term ball milling and hot pressing of in-situ nanoscale tungsten carbides reinforced copper composite and its characterization. Mater. Charact. 152, 134–140. doi: 10.1016/j.matchar.2019.04.014
Li, T. (2013). Research on Microwave Carbonization Process, And Properties Of Nano-Tungsten Carbide Powder. Nanchang: Nanchang University.
Lin, H., Tao, B. W., Xiong, J., Li, Q., and Li, Y. (2013). Tungsten carbide (WC) nanopowders synthesized Via novel core-shell structured precursors. Ceram. Int. 39, 2877–2881. doi: 10.1016/j.ceramint.2012.09.061
Liu, X. M., Song, X. Y., Zhao, S. X., and Zhang, J. (2010). Spark plasma sintering densification mechanism for cemented carbides with different WC particle sizes. J. Am. Ceram. Soc. 93, 3153–3158. doi: 10.1111/j.1551-2916.2010.03862.x
Luo, L. M., Wu, Y. C., Li, J., and Zheng, Y. (2011). Preparation of nickel-coated tungsten carbide powders by room temperature ultrasonic-assisted electroless plating. Surf. Coat. Tech. 206, 1091–1095. doi: 10.1016/j.surfcoat.2011.07.078
Luo, W. Y., Liu, Y. Z., and Shen, J. J. (2019). Effects of binders on the microstructures and mechanical properties of ultrafine WC-10%AlxCoCrCuFeNi composites by spark plasma sintering. J. Alloy. Compd. 791, 540–549. doi: 10.1016/j.jallcom.2019.03.328
Ma, J., and Zhu, S. G. (2010). Direct solid-state synthesis of tungsten carbide nanoparticles from mechanically activated tungsten oxide and graphite. Int. J. Refract. Met. Hard Mater. 28, 623–627. doi: 10.1016/j.ijrmhm.2010.06.004
Maat, N., Larde, R., Nachbaur, V., Le Breton, J. M., Isnard, O., Pop, V., et al. (2018). Investigation by mossbauer spectroscopy and atom probe tomography of the phase transformation of Nd-Fe-B alloys after high-energy ball milling. J. Appl. Phys. 12:22.
Maheshwari, P., Fang, Z. G. Z., and Sohn, H. Y. (2007). Early-stage sintering densification and grain growth of nanosized WC-Co powders. Int. J. Powder. Metall. 43, 41–47.
Morimitsu, L. C. A., Ospina, R. O., and Carmona, J. M. G. (2013). Deposition and computational analysis of WC thin films grown by PAPVD. Rev. Mex. Fis. 59, 106–111.
Postek, E., and Sadowski, T. (2018). Qualitative comparison of dynamic compressive pressure load and impact of WC/Co composite. Int. J. Refract. Met. Hard Mater. 77, 68–81. doi: 10.1016/j.ijrmhm.2018.07.009
Ryu, T., Sohn, H. Y., Hwang, K. S., and Fang, Z. Z. (2009). Plasma synthesis of tungsten carbide nanopowder from ammonium paratungstate. J. Am. Ceram. Soc. 92, 655–660. doi: 10.1111/j.1551-2916.2009.02961.x
Ryu, T., Sohn, H. Y., Hwang, K. S., and Zhigang, Z. (2008). Tungsten carbide nanopowder by plasma-assisted chemical vapor synthesis from WCl6-CH4-H2 mixtures. J. Mater. Sci. 43, 5185–5192. doi: 10.1007/s10853-008-2741-8
Sadeghi, N., Akbarpour, M. R., and Aghajani, H. (2018). A novel two-step mechanical milling approach and in-situ reactive synthesis to fabricate TiC/Graphene layer/Cu nanocomposites and investigation of their mechanical properties. Mat. Sci. Eng. A Struct. 734, 164–170. doi: 10.1016/j.msea.2018.07.101
Singla, G., Singh, K., and Pandey, O. P. (2015). Effect of Processing Variables on WC Nanoparticles Synthesized by Solvothermal Route. Particul. Sci. Technol. 33, 47–52. doi: 10.1080/02726351.2014.933147
Sohn, H. Y., Ryu, T., Choi, J. W., Hwang, K. S., Han, G., Choi, Y. J., et al. (2007). The chemical vapor synthesis of inorganic nanopowders. JOM 59, 44–49. doi: 10.1007/s11837-007-0151-z
Venables, D. S., and Brown, M. E. (1996). Reduction of tungsten oxides with carbon. Thermochim. Acta 10, 251–264. doi: 10.1016/0040-6031(95)02814-5
Wang, Q., Cao, F. Y., and Chen, Q. W. (2006). Synthesis of hexagonal tungsten carbide in tungsten-sodium and supercritical carbon dioxide system. Mater. Chem. Phys. 95, 113–116. doi: 10.1016/j.matchemphys.2005.06.008
Wang, W., Lu, Z. C., Zeng, M. Q., Bao, X., and Zhu, M. (2017). Achieving high transverse rupture strength of WC-8Co hardmetals through forming plate-like WC grains by plasma assisted milling. Mater. Chem. Phys. 190, 128–135. doi: 10.1016/j.matchemphys.2017.01.010
Wang, X. R., Tan, D. Q., Zhu, H. B., He, W., Ouyang, C., Zou, Z., et al. (2018). Effect mechanism of arsenic on the growth of ultrafine tungsten carbide powder. Adv. Powder Technol. 29, 291348–291356.
Won, H. I, Nersisyan, H. H., and Won, C. W. (2010). Combustion synthesis of nano-sized tungsten carbide powder and effects of sodium halides. J. Nanopart. Res. 12, 493–500. doi: 10.1007/s11051-009-9736-5
Wu, C., Zhu, S. G., Ma, J., and Zhang, M. L. (2009). Synthesis and formation mechanisms of nanocomposite WC-MgO powders by high-energy reactive milling. J. Alloy. Compd. 478, 615–619. doi: 10.1016/j.jallcom.2008.11.100
Wu, Y. J., Dang, J., Lv, Z. P., and Zhang, R. (2018). The preparation of tungsten carbides and tungsten powders by reaction of tungsten trioxide with methanol. Int. J. Refract. Met. Hard Mater. 76, 99–107. doi: 10.1016/j.ijrmhm.2018.06.002
Xu, Z. F., Zhou, X. K., Wang, K., and Wang, Q. (2018). Fabrication of ultrafine-grained gradient cemented carbide by SPS pre-sintered method. J. Northeastern Univer. 39:1593.
Yang, Q. M., Yang, J. G., Wen, Y., Zhang, Q., Chen, L., and Chen, H. (2018). A novel route for the synthesis of ultrafine WC-15wt %Co cemented carbides. J. Alloy. Compd. 748, 577–582. doi: 10.1016/j.jallcom.2018.03.197
Yang, T. M., Wei, Q. P., Qi, Y., and Yu, Z. (2015). The diffusion behavior of carbon in sputtered tungsten film and sintered tungsten block and its effect on diamond nucleation and growth. Diam. Relat. Mater. 52, 49–58. doi: 10.1016/j.diamond.2014.12.009
Zeng, J. H., Yuan, D. S., Liu, Y. L., Chen, J., and Tan, S. (2008). Synthesis of tungsten carbide nanocrystals and its electrochemical properties. Chin. J. Catal. 29, 607–611.
Zhang, H. C., Yu, X. D., Nie, Z. H., Tan, C., Wang, F., and Cai, H. (2018). Microstructure and growth mechanism of tungsten carbide coatings by atmospheric CVD. Surf. Coat. Tech. 344, 85–92. doi: 10.1016/j.surfcoat.2018.03.011
Zhang, L., Chen, S., Shan, C., and Cheng, X. (2012). Effects of cobalt additions on WC grain growth. Powder Metall. 55, 200–205. doi: 10.1179/1743290111y.0000000009
Keywords: ultra-fine tungsten carbide, preparation method, solid-phase method, liquid-phase method, vapor-phase method
Citation: Wu Y-C, Yang Y, Tan X-Y, Luo L, Zan X, Zhu X-Y, Xu Q and Cheng J-G (2020) Preparation Technology of Ultra-Fine Tungsten Carbide Powders: An Overview. Front. Mater. 7:94. doi: 10.3389/fmats.2020.00094
Received: 18 December 2019; Accepted: 27 March 2020;
Published: 06 May 2020.
Edited by:
Chao Yang, South China University of Technology, ChinaReviewed by:
Xuemei Liu, Beijing University of Technology, ChinaYan Long, South China University of Technology, China
Copyright © 2020 Wu, Yang, Tan, Luo, Zan, Zhu, Xu and Cheng. This is an open-access article distributed under the terms of the Creative Commons Attribution License (CC BY). The use, distribution or reproduction in other forums is permitted, provided the original author(s) and the copyright owner(s) are credited and that the original publication in this journal is cited, in accordance with accepted academic practice. No use, distribution or reproduction is permitted which does not comply with these terms.
*Correspondence: Yu-Cheng Wu, eWN3dUBoZnV0LmVkdS5jbg==; Laima Luo, bHVvbGFpbWFAMTI2LmNvbQ==