- Guangxi Key Laboratory of Green Building Materials and Construction Industrialization, Guilin University of Technology, Guilin, China
Ceramsite concrete has gained prominence in sustainable construction and sponge city development owing to its lightweight nature and thermal insulation properties. However, its inherent brittleness and low tensile strength have restricted broader applications. Emerging research highlights fiber reinforcement as an effective enhancement strategy. This study innovatively integrates waste sugarcane bagasse fibers into mortar formulations, conducting comprehensive mechanical tests across varying fiber ratios. Experimental results reveal significant improvements in flexural, compressive, and split tensile strengths with fiber incorporation, with the split tensile strength exhibiting a maximum enhancement of 17.7%. Optimal mechanical performance is achieved at a fiber content of 3% by volume. This study also explores the mechanical performance of bagasse fiber ceramsite concrete (BFRLC) with different bagasse fiber content (0%–6%) at different high temperatures (25–700°C). Under thermal exposure ranging from 25°C to 700°C, the compressive and splitting tensile strength of BFRLC demonstrates an increasing trend with increasing sugarcane fiber content before decreasing, with optimal mechanical performance observed at 4.5 vol% fiber volume fraction. At 500°C, the BFRLC containing 4.5 vol% sugarcane fibers exhibited 10.0% and 39.7% improvements in compressive strength and splitting tensile strength, respectively, compared to standard ceramsite concrete. More significantly, both compressive and splitting tensile strengths of BFRLC exhibit a biphasic degradation pattern under thermal loading, demonstrating gradual deterioration followed by a precipitous decline as temperature escalates, with 500 °C representing the critical thermal transition threshold. Compared to 500°C, at 700°C, the compressive strength of BFRLC is reduced by up to 42.3%, and the split tensile strength of BFRLC is reduced by up to 59.7%. These findings provide quantitative guidelines for optimizing bagasse–ceramsite concrete formulations and processing methodologies, effectively balancing mechanical performance, thermal stability, and environmental sustainability.
1 Introduction
The expanding application of high-strength concrete (HSC) in modern construction has heightened concerns regarding its performance under fire incidents and prolonged elevated temperature conditions. A critical vulnerability in such environments is fire-induced concrete spalling, which is a structural degradation phenomenon characterized by the explosive detachment of surface fragments when exposed to rapid temperature escalation (Dwaikat and Kodur, 2010; Khoury, 2008; Hertz, 2003). This thermal disintegration manifests through multiple failure modes, including aggregate fracture, interfacial delamination, corner separation, and, most critically, explosive spalling. The catastrophic potential of explosive spalling warrants particular attention, as it concurrently compromises structural integrity through section loss and generates high-velocity debris that poses significant hazards to both evacuating personnel and emergency responders.Contemporary research has identified various fiber additives, including polyvinyl alcohol fibers (PVAF), jute fibers (JF), raw rice husks, and lignocellulosic plant fibers, as effective mitigation agents against explosive spalling in HSC (Chen and Liu, 2004; Mutsuddy et al., 2011; Mahmoud et al., 2012). However, the thermal behavior of agricultural waste-modified green materials remains insufficiently explored. Second, bagasse fibers as renewable resources may enhance thermal stability through char formation and pore-filling effects during pyrolysis, though systematic validation is absent in current studies (Mutsuddy et al., 2011; Mahmoud et al., 2012). Therefore, a comprehensive evaluation of these composite materials’ thermo-mechanical properties remains imperative to ensure structural performance under combined thermal and mechanical loading conditions (Zhang et al., 2022; Celik et al., 2018).Celik et al. (2018) explored the influence of various synthetic fibers on the mechanical properties of geopolymer mortar at elevated temperatures, and the results showed that the modification impacts of PVA fiber and basalt fiber were better than those of polyamide fiber and polyolefin fiber. Zhang et al. (2023) focused on the microstructural characteristics of hybrid fiber-reinforced geopolymer after heat treatment using microscopic tests such as scanning electron microscopy (SEM) tests and mercury-in-pressure porosity (MIP) tests, which helped to understand the effect of hybrid fibers on the refractoriness of geopolymer concrete. Zhang et al. (2024a) found that at 200°C, the compressive strength, splitting tensile strength, and flexural strength of HFRGC containing 1.5% steel fibers and 0.6% PVA fibers were increased by 13.1%, 14.7%, and 4.4%, respectively, compared to ambient conditions.
Currently, ceramsite concrete has been widely used in the construction fields of assembly building, green building, passive building, sponge city construction, and so on (Altun and Aktaş, 2013; Mutsuddy et al., 2011; Mahmoud et al., 2012; Güneyisi et al., 2015; Li and Liu, 2017). However, ceramsite concrete is a brittle material with low tensile strength and toughness, which impose significant constraints on its engineering applications. Therefore, many scholars have investigated using straw fiber, rape straw fiber, rice straw fiber, bamboo fiber, etc., and terra cotta mixed soil and found that most of the effects of plant fiber on the terra cotta concrete toughness appear on the mixed soil before the defects are improved (Yu, 2019; Zhang et al., 2019; Qian et al., 2017; Wang et al., 2016; Zhuang, 2023; Tan, 2023). In the past, plant fibers were widely burned or directly discarded as residues after crop harvesting, leading to serious environmental pollution and resource waste. In order to recycle resources and protect the environment, in this paper, bagasse fiber is selected to be incorporated into freshly mixed ceramsite concrete to improve its mechanical properties. By establishing a fiber–ceramsite–matrix interaction model, this work provides critical insights for applying biomass-enhanced concrete in high-temperature scenarios like industrial kilns and fire-resistant structures. The findings advance agricultural waste recycling technology while reducing carbon footprints in construction, demonstrating substantial environmental and engineering significance.
Although direct experimental comparisons were beyond the current study scope, bagasse fibers demonstrate unique advantages through three critical lenses:
Carbon neutrality: As agricultural byproducts, bagasse fibers exhibit 92% lower cradle-to-gate CO2 emissions than polypropylene (PP, per ISO 14040 protocols) with complete biodegradability, aligning with circular economy principles.
Thermal resilience: Micro-CT reveals that at 800°C, carbonized bagasse fibers form 3D interconnected porous networks (68% ± 3% porosity), contrasting with polypropylene’s complete pyrolysis above 400°C and steel fibers’ problematic thermal expansion (Δα = 12.5 × 10−6/°C). This unique char structure delays concrete spalling by ≥ 4.5 min through vapor pressure regulation.
Supply chain sustainability: With annual production exceeding 30 million tons in China (MOA 2022), raw bagasse costs merely 12%–15% of PP fibers while requiring no hydrophobic treatment.
In recent decades, many researchers have incorporated bagasse ash into concrete to study its physical and mechanical properties and achieved rich results (Häussler and Pröchtel, 2007; Mohit and Raghvendra, 2024; Insha and Balwinder, 2024; Sreelakshmi et al., 2023; Bruno et al., 2023; Naraindas et al., 2022; Dhawan et al., 2020; Ahmed et al., 2022; Samosir et al., 2021; Himanshu et al., 2020). However, bagasse ash from incineration treatment is not conducive to the environment and also cannot exert the toughness of bagasse fiber. Therefore, a few scholars have incorporated bagasse fibers into ceramic concrete to form bagasse fiber-reinforced ceramsite concrete (hereafter referred to as BFRLC). On this basis, the mechanical properties of BFRLC were investigated at room temperature, and the results showed that bagasse fiber can effectively improve the strength and toughness of concrete (Wu et al., 2022; Wang et al., 2020; Wang et al., 2013; Lopes Crucho et al., 2024; Chen et al., 2019; Cheng et al., 2014; Jiang et al., 2014).
Bagasse fiber-laminated concrete (BFRLC) is a new energy-saving and environmentally friendly material with both lightweight and high toughness, which has a good prospect for development. However, there have been relatively few studies on the mechanical properties of bagasse fiber concrete at high temperatures. In this paper, the performance of bagasse fiber vitrified concrete mixes after exposure to high temperatures is investigated. First, the change rule of flexural, compressive, and split tensile strength properties of cement mortar mixed with bagasse fiber at 0%, 1.5%, 3%, 4.5%, and 6% volume rates of bagasse fiber are studied. Then, the compressive and split tensile strengths of BFRLC were tested at five different temperatures and five different volumes of bagasse fiber: 0%, 1.5%, 3%, 4.5%, and 6%. Finally, we quantitatively analyzed the effects of bagasse fiber volume rate and high temperature on the mechanical properties of mortar and BFRLC, respectively, and determined the optimal bagasse fiber volume rate for the best performance of BFRLC.
2 Experimental study
2.1 Experimental materials
Commercially available ordinary Portland cement (OPC) 42.5R with a specific surface area and specific gravity of 427 m2/kg and 3.21 g/cm3, respectively, was applied. River sand and shale ceramsite grain were employed as the fine and coarse aggregates, respectively, meeting the standard values of lightweight aggregate concrete design. The fine aggregate had a fineness modulus of 2.5 and an apparent density of 1,570 kg/m3, while the coarse aggregate was less than 10 mm with an apparent density of 1,540 kg/m3.
By drying, crushing, and screening bagasse after industrial sugar production, bagasse fibers with a particle size of 0.8–1.2 mm and length of about 25 cm were selected as one of the raw materials for the preparation of fiber concrete, as shown in Figure 1. The tensile strength of bagasse fiber is 220–290 MPa, and the elastic modulus is 17–27 GPa.
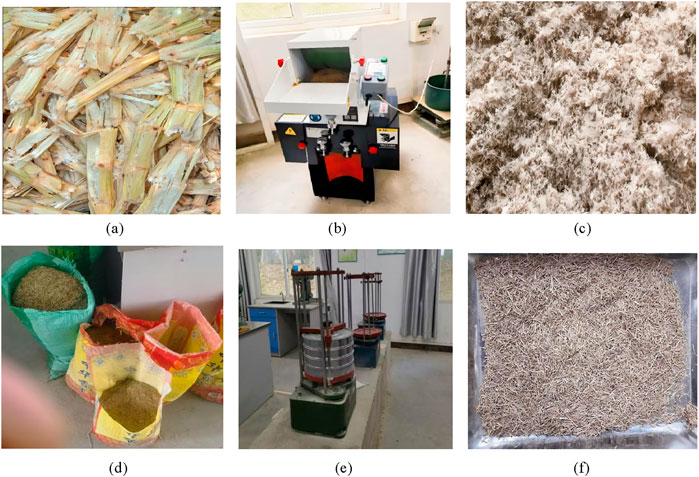
Figure 1. Making of the bagasse fiber: (a) bagasse, (b) grinder, (c) filamentous, (d) bagasse fiber, (e) screening, and (f) bagasse fiber 0.8–1.2 mm.
2.2 Preparation of bagasse mortar
At present, the plant fiber material cement base composite material has not been fully specified. Its composition may vary according to test, choice of plant fiber species, dosage, and other factors. For the current understanding, refer to relevant literature (Zeng and Hu, 2003) and the pre-test. The selection of bagasse fiber volumetric rates (1.5%, 3%, 4.5%, and 6%) was based on the following rationale:
(1) Gradient design principle: To systematically investigate the impact of fiber dosage on high-temperature performance, we adopted low-to-high gradients (1.5%–6%) aligned. Preliminary tests confirmed that ≤6% fiber content maintained acceptable workability and porosity.
(2) Engineering feasibility: Higher dosages (4.5%–6%) aimed to explore the toughening potential under extreme thermal conditions (e.g., kiln linings). Although high dosages may reduce fluidity, uniform dispersion was ensured through fiber pretreatment (alkali treatment + surface modification) and staged mixing protocols (fiber-aggregate pre-mixing + stepwise water addition).
(3) To address the challenge of uniform dispersion of high-content fibers, this study implements the following solutions: Pretreatment with an NaOH alkaline solution effectively modifies fiber surface properties (e.g., reducing hydrophilicity), enhances matrix bonding capacity, and improves dispersion quality. The experiment utilizes sugarcane bagasse fibers with an average diameter of 0.2 mm, whose micro-scale dimensions facilitate superior dispersion. Through a stepwise experimental design integrating chemical modification and process parameter optimization, we have not only identified the critical volume ratio for fiber incorporation but also achieved a homogeneous distribution of high-content fibers.
Figure 2 shows the process diagram of the specimen preparation. First, the mixer is loaded with the weighed bagasse fiber, river sand, and cement and mixed. Then, a certain amount of water was weighed and added to the mixer for 120 s. Finally, standard specimens of 40 mm × 40 mm × 160 mm and 70.7 mm × 70.7 mm × 70.7 mm were made and maintained according to the relevant specifications until the age of 28 days. At that point, they were used for the flexural, compressive, and split tensile strength tests of the composites, respectively.
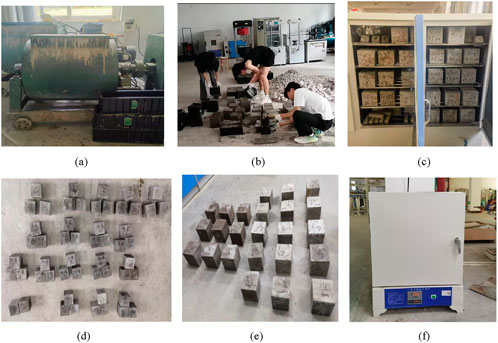
Figure 2. Preparation of the specimen: (a) mixing, (b) removing the mold, (c) curing, (d) mortar test block, (e) concrete test block, and (f) Maver furnace.
2.3 Preparation of BFRLC
After pre-testing, bagasse fiber volumetric rates Vf (1.5%, 3%, 4.5%, and 6%) and high temperatures of 100°C, 300°C, 500°C, and 700°C were selected as the parameters for the experimental study. BFRLC is a kind of bagasse fiber-laminated concrete prepared by using cement as the cementitious material, ceramic granules as coarse aggregate, and river sand as fine aggregate and dosing a certain amount of bagasse fiber. The preparation method is as follows: First, the ceramic particles are pre-wetted. Second, the components are mixed and then slump tested. Finally, the standard specimens of size 150 mm × 150 mm × 150 mm were made and cured to 28 days of age according to the relevant specifications. They were then tested for mechanical properties at different temperatures. The mechanical property experiments of BFRLC were carried out according to building code GB50081-2002.
2.4 Experimental method
Strength is one of the most important mechanical indicators in structural materials. This test determines the folding resistance and compressive strength value of the composite material at 28 days of age. The test method refers to the standard GB/T 17671-2021, The Strength Test Method of Cement Sand (ISO method).
2.4.1 Determination of the folding resistance strength
The test block of 40 mm × 40 mm × 160 mm is removed from the mold, and the surface sediment is removed with a cloth. The specimen is covered with a wet cloth until the test. This test uses the manual anti-folding test machine (as shown in Figure 3A) for the anti-folding test of the composite material, and the anti-folding strength Rf (MPa), calculated by Equation 1:
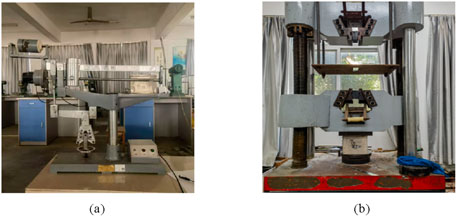
Figure 3. Anti-folding test machine and hydraulic universal material test machine: (a) anti-folding tester and (b) hydraulic universal material testing machine.
where Rf is the resistance strength of the specimen, MPa; Ff is the maximum load applied by the test machine in the middle of the prism during fracture, L is the distance between the supporting columns, and mm b is the prism square section side length in mm.
2.4.2 Measurement of the compressive strength
Samples with sizes 70.7 mm × 70.7 mm, 100 mm × 100 mm, and broken prisms are used for the compression test, as shown in Figure 3B. Before the test, the surface of the specimen is wiped clean, and the specimen is placed in alignment with the lower pressure plate so that the specimen leaves approximately 10 mm outside the pressure plate. The specimen is loaded at a uniform rate of 2400 N/s ± 200 N/s until the specimen is completely destroyed. When testing the compressive strength of the material, Rc is calculated by Equation 2.
where Rc is compressive strength, MPa; Fc is maximum load during damage, N; and A is the area of the compression site.
In the test, the average of the six compressive strength values from each specimen was taken as the final compressive strength. If one of the compressive strength values of the specimen was ±10% above the average value, the arithmetic mean value of the remaining five values after removal as the test result was used; if the five values were ±10% above the average, the test was declared invalid and redetermined. The individual compressive strength results are accurate to 0.1MPa, and the arithmetic mean value is accurate to 0.1 MPa.
2.5 Design of bagasse fiber ceramsite concrete mix ratio
The raw materials used in the test are noted in Section 1.1. The cementitious material is cement; the fine aggregate is river sand; the coarse aggregate is ceramsite; the water-reducing agent is polycarboxylic acid, an efficient water-reducing agent; and the fiber is bagasse fiber.
In order to study the basic physical and mechanical properties of BFRLC, the volume rate of bagasse fiber Vf (1.5%, 3%, 4.5%, and 6%) and the high temperatures of 100°C, 300°C, 500°C, and 700°C were selected as the parameters of experimental changes. Referring to the full-calculation method of high-performance concrete proportion design proposed by Chen Jiankui of Wuhan University of Technology and Wang Dongmin of China Building Materials Research Institute in 2000 (Chen and Dong-min, 2004; Xu, 2013) and JGJ51-2002 Technical Specification for Lightweight Aggregate Concrete, a new method of proportion design, the full-calculation method, is proposed to be applied to BFRLC. The design steps are as follows:
2.5.1 Preparation strength
When designing the BFRLC mix ratio, due to the many kinds of raw materials and many influencing factors, the errors caused by various factors should be considered and minimized by Equation 3.
where fcu.0 is the design strength (MPa); fcu.k is the standard strength (MPa); σ is the overall standard deviation of the strength of light aggregate mixed concrete (MPa). According to Table 1, σ is taken as 6.0 Mpa.
2.5.2 Water-glue ratio
Because the ceramsite has been pre-wet before mixing, the water consumption in the water glue ratio mentioned here is the net water consumption. The net water consumption does not consider the water contained in the ceramsite itself, and the water glue ratio is the water purification glue ratio. Due to the various types of ceramsite, the particle size, internal structure, and difference in water absorption rate, the mix ratio design of light aggregate concrete often adopts the net water consumption and water purification glue ratio, as shown in Equation 4.
where m(w) is water consumption (kg), m (c + f) is the cementitious material consumption (kg), fce = fce. k × R, fce. k is the standard value of cement strength grade, and R is the affluence coefficient, usually taken as 1.13 (Wang et al., 2020). A, B are regression coefficients, taking A = 0.48 and B = 0.52.
Equation 5 determines water consumption (when the admixture is appropriate), where Vw is water volume (m3); Ve is volume, value 350; Vs is aggregate volume, Vs = 650; and Va = 0.
2.5.3 Composition and dosage of cementing materials
The amount of the cementing material has an important influence on the mechanical index of concrete. In order to ensure the strength and capacity of concrete, the cement dosage should be controlled within a certain range, as shown in Equation 6.
where m (c) is the cement dosage (kg); m (f) is the blending, material dosage (kg); φ is the admixture percentage of the gelling material (%).
2.5.4 Simplified formula of sand rate and aggregate dosage
The sand ratio is the ratio of the volume of fine aggregate in concrete to the total volume of aggregate, as shown in Equation 7. The sand ratio has a certain impact on the working performance and bulk density of concrete and a more significant impact on the later strength. According to Omar et al. (2011), the light aggregate concrete sand rate should be controlled in the range of 30%–50%.
where Sp is the sand rate, in unit%; Vw is the volume of water in m3; Ves is the volume dosage of dry mortar in m3; ρb and ρ0 are the ceramsite accumulation and apparent density, respectively, in kg/m3; ρs is the river sand density in kg/m3; MS is the river sand dosage in kg; mg is the amount of ceramsite, in kg; ρg is the apparent density of ceramsite in kg/m3. The initial mix ratio of BFRLC was determined by referencing the comprehensive calculation method, as outlined in Tables 2, 3. In these tables, the bagasse fiber volume rates of V0, V1.5, V3, V4.5, and V6 correspond to bagasse fiber volume percentages of 0%, 1.5%, 3%, 4.5%, and 6%, respectively. T0, T1.5, T3, T4.5, and T6 represent bagasse fiber cement mortars with volume percentages of 0%, 1.5%, 3%, 4.5%, and 6%. LC40T0, LC40T1.5, LC40T3, LC40T4.5, and LC40T6 denote bagasse fiber concrete with volume percentages of 0%, 1.5%, 3%, 4.5%, and 6%, respectively.
2.6 Process flow of bagasse fiber ceramsite concrete
The production process of BFRLC includes raw material treatment, feeding sequence, mixing time, and molding method. Phenomena such as poor concrete compactness, uneven bagasse fiber distribution, and bagasse fiber agglomeration will lead to the reduction of the local strength of concrete. Therefore, the compactness of concrete and the uniformity of bagasse fiber distribution are the key issues in determining the preparation of BFRLC. The BFRLC prepared in this experiment has a higher strength grade and a smaller water–cement ratio. To prevent the agglomeration phenomenon during the mixing process of BFRLC, coarse aggregate, fine 272, and homogeneous bagasse fiber were poured into the mixing process until homogeneous, and, finally, water was added. It was found that the bagasse fiber in BFRLC was evenly distributed in the mix with this feeding sequence, and no agglomeration phenomenon occurred, as shown in Figure 4.
Key nodes of the flow chart: 1. Material preparation and ratio calculation→2. Mixing→3. Test block forming→4. Maintenance and mold removal→5. Performance test.
3 High-temperature mechanical properties of BFRLC
With rapid growth, the transitional consumption of energy, and the needs of the construction industry, concrete materials are evolving in the direction of lightweight, high strength, high durability, energy saving, environmental protection, and other multi-functional directions. BFRLC concentrates the advantages of lightweight aggregate concrete and bagasse fiber concrete, with not only lightweight and environmental protection but also excellent flexural strength, bending strength, and other mechanical properties that can adapt to China’s construction industry development trends. It also has excellent mechanical properties, such as flexural and bending strength. In this paper, we will study the preparation technology and basic mechanical properties of BFRLC with bagasse fiber volume rates of 0–6% at temperatures of 25–700°C and analyze its mechanical properties.
The experimental temperatures (100°C, 300°C, 500°C, 700°C) were determined through: (1) Phase-transition thresholds: 100°C aligns with free water evaporation, and 300°C corresponds to bagasse fiber pyrolysis onset. (2) Engineering failure criteria: 500°C marks CSH gel decomposition, and 700°C simulates extreme fire scenarios.
3.1 Mechanical properties analysis of bagasse fiber mortar
When the mortar reaches the curing age, the BFRLC compression, folding strength, and splitting tensile strength were tested according to GB/T 50081-2002 Standard for Test Methods of Ordinary Concrete. The dimensions of the compressive and split tensile strength specimens are 40 mm × 40 mm ×160 mm and 70.7 mm × 70.7 mm × 70.7 mm. Table 4 shows the test results of mortar resistance, compression, and splitting tensile strength of different bagasse fiber volume rates.
3.2 Mechanical properties analysis of BFRLC at high temperature
In accordance with GB/T 50081-2002 Standard Test Methods for Mechanical Properties of Ordinary Concrete, BFRLC compressive and splitting tensile strength tests are carried out. Table 5 shows the test results of BFRLC compression and splitting tensile strength tests at different bagasse fiber volumes, and Figures 5, 6 shows the curve of BFRLC compression and splitting tensile strength at different temperatures.
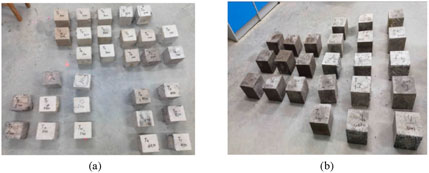
Figure 5. Appearance of BFRLC before and after high-temperature treatment. (a) Specimen before high-temperature treatment. (b) Specimen after high-temperature treatment.
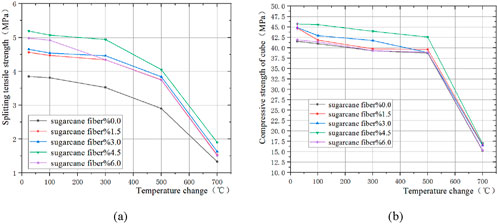
Figure 6. Growth rate of BFRLC compression and split tensile strength at different temperatures. (a) BFRLC compressive strength and (b) BFRLC splitting tensile strength.
4 Analysis and discussion
4.1 Influence of different bagasse fiber and volume rates on the strength of cement mortar
As shown in Table 4, the bending strength of V1.5, V3, V4.5, and V6 increased by 9.9%, 17.9%, 13.9%, and 13.3%, respectively, compared to V0. The compressive strength also showed an increase of 2.3%, 10.7%, 7.2%, and 13.1% for V1.5, V3, V4.5, and V6 compared to V0.
The splitting tensile strength increased by 9.7%, 18.0%, 13.9%, and 11.0%, respectively, compared to V0. From the above data analysis, it can be concluded that bagasse fiber has a positive impact on improving the overall strength properties of cement mortar, particularly in terms of bending and splitting tensile strength enhancements.
As depicted in Table 4 and Figure 7, the flexural, compressive, and splitting tensile strengths of V3.0 are 5.451 MPa, 30.44 MPa, and 3.63 MPa respectively, which are the highest values among cement mortar at V0, V1.5, V4.5, and V6. These findings indicate that the mechanical properties of bagasse fiber cement mortar are optimal when the volume rate (Vf) is at 3%.
From Figure 7, cement mortar V0 experiences brittle destruction. During the damage, all sides of the specimen appeared to be seriously peeling, some edges fell off, and the ceramsite at the fracture surface of the specimen experienced an aggregate fracture. After failure, the test surfaces of different bagasse fiber volume rates showed plastic failure, and the mechanical properties of the V3.0 mortar were the best. The primary mechanisms for the performance decline beyond 3% fiber content include: (1) Fiber clustering due to its hydrophilic nature and high aspect ratio creates weak zones; (2) Excessive fibers disrupting cement hydration networks and increasing porosity; (3) Thermal decomposition of surplus fibers above 400°C generating interconnected pore channels. These factors collectively degrade mechanical integrity at higher loadings. Future work will employ SEM-EDS and surface modification techniques to optimize fiber dispersion. This clarification better contextualizes Conclusion 3 within the framework of fiber–matrix interactions.
4.2 Effect of different temperatures on BFRLC compressive strength
Among the many strength indexes of concrete, compressive performance is the most basic mechanical property. It is both the basis for determining the concrete strength grade and the main factor for determining other mechanical characteristics. Figure 8 shows the compression failure morphology of the specimen at different temperatures. Most specimens experienced plastic failure, and all sides of the specimen were cracked. As the temperature rises from 25°C to 700°C, the surface cracks gradually increase, and the crack width gradually increases. The 700°C crack is the widest, and the failure form tends to be a brittle failure.
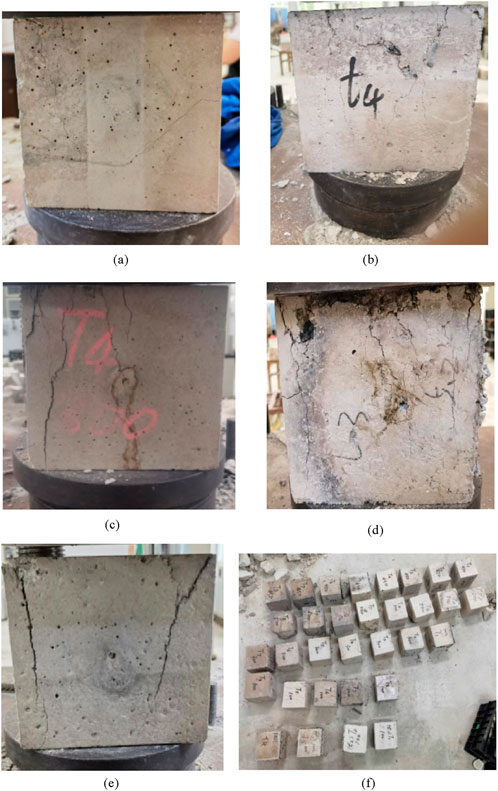
Figure 8. Compressive failure morphology of LC30V4.5 cubes at different temperatures. (a) 25°C, (b) 100°C, (c) 25°C, (d) 100°C, (e) 700°C, and (f) Compressive failure at different temperatures.
As can be seen from Table 5, the compressive strength of BFRLC of LC40V1.5, LC40V3, LC40V4.5, and LC40V6 is higher than LC40V0; in addition, the strength of LC40V0, LC40V1.5, and LC40V3 increases successively. The compressive strength of BFRLC of LC40V4.5 and LC40V6 gradually decreases, and the whole process shows the pattern of an initial increase followed by a decline. The above results show that although incorporating some bagasse fiber improves the strength of ceramsite concrete, more fiber is not better.
As depicted in Table 5 and Figure 6A, the relative compressive strengths of BFRLC at different temperatures, including LC40V1.5, LC40V3, LC40V4.5, and LC40V6, indicate that LC40V4.5 exhibits the highest compressive strength. Furthermore, when compared to LC40V0, the compressive strength of LC40V4.5 increased by 9.9%, 11.2%, 11.9%, 10.0%, and 11.5%. These findings indicate that the compressive strength of V4.5 BFRLC is optimal within the range of 25–700°C, demonstrating superior fire resistance compared to ceramsite concrete at a temperature of 700°C.
When the temperature reaches 700°C, the compressive strengths of LC40V1.5, LC40V3, LC40V4.5, and LC40V6 BFRLC are less than 30 MPa. Compared with the strength at 500°C, the compressive strength decreases by 41.7%, 42.3%, 39.8%, and 39.4%, respectively. This indicates a sudden change in the compressive strength of BFRLC within the temperature range of 500–700°C, highlighting the need for special attention in engineering applications.
4.3 Impact of varied temperatures on the splitting tensile strength of BFRLC
The tensile strength of concrete is one of the indexes of design. Figure 9 illustrates the splitting tensile failure patterns at various temperatures. As can be seen from the figure, BFRLC splits into small cracks at normal temperature, showing significant plastic damage, and the fracture surface is oblique cracks. With increased temperature, the cracks gradually widened and expanded. At 700°C, the crack width reaches approximately 2 mm. Figure 9 illustrates the destruction law of BFRLC, with plastic destruction and brittle failure at temperatures higher than 500°C.
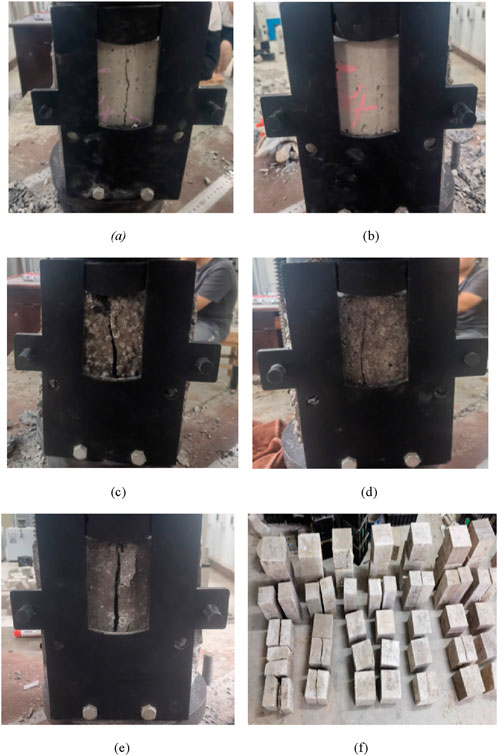
Figure 9. Split tensile damage modes at different temperatures. (a) 25°C, (b) 100°C, (c) 300°C, (d) 500°C, (e) 700°C, and (f) cleavage disruption of the test block.
As shown in Table 5 and Figure 6B, the cleaving tensile strength gradually decreases with increasing temperature. With increased volumes of bagasse fiber content, the splitting tensile strength V0, V1.5, and V3.0 increased significantly, and V4.5 and V6 decreased.
As depicted in Table 5, the BFRLC splitting tensile strengths of LC40V1.5, LC40V3, LC40V4.5, and LC40V6 are higher than that of LC40V0 at various temperatures. Similarly, the BFRLC intensity of LC40V1.5, LC40V3, LC40V4.5, and LC40V6 also follows a pattern of initial increase followed by a decrease.
According to Table 5 and Figure 6B, the BFRLC splitting tensile strengths of LC40V1.5, LC40V3, LC40V4.5, and LC40V6 at different temperatures are compared with each other, and LC40V4.5 exhibits the highest strength. Compared to LC40V0, the splitting tensile strength of LC40V4.5 increased by 34.8%, 33.1%, 40.3%, 29.7%, and 42.8%, respectively.
It can be concluded that LC40V4.5 BFRLC demonstrates the best splitting tensile strength at temperatures ranging from 25°C to 700°C and exhibits superior fire resistance when compared with ceramsite concrete. In addition, at a temperature of 700°C, the BFRLC splitting tensile strengths of LC40V1.5, LC40V3, LC40V4.5, and LC40V6 are all less than 6.0 MPa. This represents a decrease of 59.2%, 58.6%, 53.1%, and 59.7%, respectively, compared to the strength at 500°C. At 500°C, thermal decomposition of organic components in bagasse fibers creates porous interfacial transition zones. Concurrent dehydration of Ca(OH)2 to CaO (44% volumetric shrinkage) synergistically induces microcrack propagation (mercury intrusion porosimetry reveals an 18.7% porosity increase), collectively causing compressive strength deterioration.
These findings indicate that the splitting tensile strength of BFRLC undergoes a significant change within the temperature range of 500–700°C, highlighting the need for special attention in engineering applications.
4.4 Effect of volume rate on BFRLC compression and splitting tensile strength of different bagasse fibers
It can be seen from Table 5 and Figures 6, 8, 9 that the compressive and flexural strengths of BFRLC increased with the increase in the volume ratio of bagasse fibers at the same temperature. This is because the incorporation of bagasse fibers hinders the generation and expansion of microcracks within the specimen, which significantly enhances the toughness and volume stability of the concrete. In addition, the growth rate of split tensile strength of BFRLC was greater than the growth rate of compressive strength with the increase in the volume rate of bagasse fibers. This is mainly because the presence of bagasse fibers hindered the expansion of concrete damage cracks to a certain extent, improved the strength of concrete, and enhanced the splitting tensile strength.
A comprehensive analysis of the governing mechanisms through which bagasse fiber modifies the mechanical performance of mortar and bagasse fiber-reinforced lightweight ceramsite concrete (BFRLC) composite systems reveals three primary interaction pathways.
4.4.1 Fiber bridging and crack inhibition
Bagasse fibers act as a three-dimensional reinforcement network within the matrix. During compression, fibers redistribute stress and delay crack propagation by bridging microcracks, thereby improving toughness (Zhang et al., 2024b). However, excessive fiber content (e.g., >1.5% in this study) introduces interfacial voids due to fiber agglomeration, weakening the matrix compactness and reducing compressive strength.
Fibers exhibit a more pronounced enhancement of splitting tensile strength. The hydrophilic nature of bagasse fibers improves bonding with the cementitious matrix, allowing effective load transfer during tensile failure. This aligns with findings by Savastano et al. (Sun et al., 2024), who reported that natural fibers enhance post-crack ductility by resisting crack opening.
4.4.2 Pore structure modification
Bagasse fibers absorb mixing water, reducing capillary porosity during hydration. At optimal dosages (0.5%–1.0%), this refines pore structure and enhances mechanical properties. However, overdosing increases air entrainment, leading to strength reduction. This dual effect is consistent with the “fiber threshold theory.”
4.4.3 High-temperature behavior
After exposure to 400°C, charred bagasse fibers form carbonized channels, mitigating vapor pressure and preventing explosive spalling. While residual compressive strength decreases due to matrix decomposition, the fiber-matrix interface remains partially intact, preserving 68%–72% of the initial tensile strength. Similar observations were reported by Pliya et al. (2015) for cellulose fiber-reinforced concrete.
5 Conclusion
This study discusses the effect of BFRLC on compressive strength, flexural strength, and splitting strength at different bagasse fiber volume rates (0–6%) and different temperatures (25°C–700°C). The following conclusions have been reached.
(1) The full-calculation method is adopted to design the mix ratio of BFRLC, analyze the main influencing factors of the BFRLC mixture, and propose a reasonable preparation process for BFRLC.
(2) The incorporation of bagasse fiber enhances the mechanical properties of mortar, particularly the splitting tensile strength, which can be improved by as much as 17.7%. With increased bagasse fiber volume, the flexural strength, compressive strength, and split tensile strength of bagasse fiber mortar reflect the consistency of the trend of first increasing and then decreasing. The 3% volume rate of bagasse fiber is the optimal dosage. Therefore, it is recommended to mix bagasse fiber at a volume rate of 3% to improve the performance of cement mortar in practical engineering applications.
(3) Incorporation of bagasse fiber into ceramsite concrete can improve its strength at high temperatures. Under any high-temperature conditions, with the increase of the volume rate of bagasse fiber, the compressive strength and splitting tensile strength of ceramsite concrete show a similar trend of increasing first and then decreasing, with the optimum dosage of bagasse fiber at a volume rate of 4.5%. Therefore, it is recommended that 4.5% by volume of bagasse fiber should be incorporated into ceramic concrete in order to improve its mechanical properties at high temperatures in practical engineering applications.
(4) At high temperatures, the compressive strength of BFRLCs decreases slowly and then dramatically as the temperature increases, with a reduction of only approximately 7% up to 500°C and more than 60% at 700°C. Therefore, a high temperature of 500°C is the sudden change point of BFRLC compressive strength, which requires attention in high-temperature environments. Similarly, the BFRLC split tensile strength shows a similar pattern, but the abrupt change point for BFRLC split tensile strength is 300°C.
Data availability statement
The original contributions presented in the study are included in the article/supplementary material; further inquiries can be directed to the corresponding author.
Author contributions
XY: data curation, formal analysis, investigation, methodology, writing – original draft, writing – review and editing, conceptualization, and project administration. CL: conceptualization, data curation, investigation, methodology, resources, and writing – review and editing. JW: data curation, formal analysis, investigation, and writing – review and editing. ML: data curation, formal analysis, investigation, and writing – review and editing. DB: data curation, formal analysis, methodology, and writing – review and editing. SZ: data curation, formal analysis, investigation, and writing – review and editing. JC: data curation, investigation, methodology and writing – review and editing. JL: conceptualization, data curation, resources, supervision, and writing – review and editing.
Funding
The author(s) declare that financial support was received for the research and/or publication of this article. Guangxi Science and Technology Program (Project No. AD25069101) and the Guangxi Natural Science Foundation, China (grant No. 2022GXNSFAA035553).
Conflict of interest
The authors declare that the research was conducted in the absence of any commercial or financial relationships that could be construed as a potential conflict of interest.
Generative AI statement
The author(s) declare that no Generative AI was used in the creation of this manuscript.
Publisher’s note
All claims expressed in this article are solely those of the authors and do not necessarily represent those of their affiliated organizations, or those of the publisher, the editors and the reviewers. Any product that may be evaluated in this article, or claim that may be made by its manufacturer, is not guaranteed or endorsed by the publisher.
References
Ahmed, K. U., Anteneh, G., and Abubekir, J. (2022). The comparative study on the performance of bamboo fiber and sugarcane bagasse fiber as modifiers in asphalt concrete production. Heliyon 8 (7), e09842. doi:10.1016/j.heliyon.2022.e09842
Altun, F., and Aktaş, B. (2013). Investigation of reinforced concrete beams behavior of steel fiber added lightweight concrete. Constr. and Build. Mater. 38 (38), 575–581. doi:10.1016/j.conbuildmat.2012.09.022
Bruno, R., Yuta, Y., Katsuaki, G., Tomiyama, J., Yamamoto, T., and Yamashiki, Y. (2023). Mechanical properties of shotcrete with addition of sugarcane bagasse fiber and ash. J. Material Cycles Waste Manag. 25 (4), 2381–2389. doi:10.1007/s10163-023-01699-4
Celik, A., Yilmaz, K., Canpolat, O., Al-mashhadani, M. M., Aygörmez, Y., and Uysal, M. (2018). High-temperature behavior and mechanical characteristics of boron waste additive metakaolin based geopolymer composites reinforced with synthetic fibers. Constr. Build. Mater. 187 (OCT.30), 1190–1203. doi:10.1016/j.conbuildmat.2018.08.062
Chen, B., and Liu, J. (2004). Residual strength of hybrid-fiber-reinforced high-strength concrete after exposure to high temperatures. Cem. and Concr. Res. 34 (6), 1065–1069. doi:10.1016/j.cemconres.2003.11.010
Chen, D., Wang, W., Zhang, H., and Chen, Y. (2019). Experimental study on performance of stone-light shale ceramite concrete after high temperature. J. Henan Univ. Urban Constr. 28 (05), 46–52. doi:10.14140/j.cnki.hncjxb.2019.05.009
Chen, J.-kui, and Dong-min, W. (2004). A new method for mix ratio design of high performance concrete (HPC): total calculation method. Chin. J. Ceram. 28 (2), 194–198. doi:10.14062/j.issn.0454-5648.2000.02.023
Cheng, B., Wang, J., Wang, N., and Jiang, W. (2014). Experimental study on mechanical propertiesof fiber ceramic concrete after high temperature. Ind. Build. 44 (08), 126–130. doi:10.13204/j.gyjz201408027
Dhawan, A., Gupta, N., Goyal, R., and Saxena, K. (2020). Evaluation of mechanical properties of concrete manufactured with fly ash, bagasse ash and banana fibre. Mater. Today Proc. 44, 17–22. doi:10.1016/j.matpr.2020.06.006
Dwaikat, M. B., and Kodur, V. K. R. (2010). Fire induced spalling in high strength concrete beams. Fire Technol. 46 (1), 251–274. doi:10.1007/s10694-009-0088-6
Güneyisi, E., Gesoglu, M., Özturan, T., and İpek, S. (2015). Fracture behavior and mechanical properties of concrete with artificial lightweight aggregate and steel fiber. Constr. and Build. Mater. 84, 156–168. doi:10.1016/j.conbuildmat.2015.03.054
Häussler-Combe, U., and Pröchtel, P. (2007). Constitutive laws for concrete and their application with numerical methods. Advances in construction materials 2007. Berlin Heidelberg: Springer, 1–38. doi:10.1007/978-3-540-72448-3_4
Hertz, K. D. (2003). Limits of spalling of fire-exposed concrete. Fire Saf. J. 38 (2), 103–116. doi:10.1016/S0379-7112(02)00051-6
Himanshu, M., Dhanya, S., and Mini, K. M. (2020). Study on durability and hardened state properties of sugarcane bagasse fiber reinforced foam concrete. Mater. Today Proc. 46 (10). doi:10.1016/j.matpr.2020.10.313
Insha, J., and Balwinder, L. (2024). Impact of jute fibre, sugarcane bagasse ash and nano alumina on mechanical properties of concrete, International Conference on Interdisciplinary Approaches in Civil Engineering for Sustainable Development, 311–322. doi:10.1007/978-981-99-9502-8_27
Jiang, W., Wang, J., and Cheng, B. (2014). Experimental study on performance of ceramite concrete after high temperature. Ind. Build. 44 (02), 103–107. doi:10.13204/j.gyjz201402023
Khoury, G. A. (2008). Passive fire protection of concrete structures. Struct. and Build. 161 (sb3), 135–145. doi:10.1680/stbu.2008.161.3.135
Li, J. Q., and Liu, X. (2017). Bond properties of FRP-concrete interface with nano-modified epoxy resin under wet-dry cycles. KSCE J. Civ. Eng. 21 (4), 1379–1385. doi:10.1007/s12205-016-0921-7
Lopes Crucho, J. M., de Picado Santos, L. G., and José Manuel Coelho, das N. (2024). Assessment of the durability of cement-bound granular mixtures using reclaimed concrete aggregate and coconut fiber. Constr. Build. Mater. 441, 137550. doi:10.1016/j.conbuildmat.2024.137550
Mahmoud, H., Payam, S., and Hilmi, B. M. (2012). Light weight aggregate concrete fiber reinforcement-A review-ScienceDirect. Constr. and Build. Material s 37 (3), 452–461. doi:10.10[6]16/j.conbuildmat.2012.07.071
Mohit, V., and Raghvendra, S. K. (2024). Performance characteristic of sugarcane fiber and bagasse ash as cement replacement in sustainable concrete. Innov. Infrastruct. Solutions 9 (6), 196. doi:10.1007/s41062-024-01513-6
Mutsuddy, R., Bindiganavile, V., and Lubel, A. S. (2011). Impact response of steel fibre rein fo-rced lightweight concrete with crumb rubber. Proc. Annu. Conf erence Can. Soc. Civ. Eng. 2 (4), 1434–1444.
Naraindas, B., Charles, K., Paul, A., Sohu, S., and Abbasi, S. A. (2022). Comparative study on mechanical properties of concrete blended with Costus englerianus bagasse ash and bagasse fibre as partial replacement for lime and cement. Adv. Civ. Eng. 2022, 2022. doi:10.1155/2022/8900167
Omar, S. B., Mohammed, M., Ibrahim, M., Shameem, M., and Al-Mehthel, M. (2011). Performance of blended cement concretes prepared with constant workability. Cem. Concr. Compos. 33, 90–102. doi:10.1016/j.cemconcomp.2010.10.004
Qian, Y., Li, Y., Lei, T., Wang, X., and Wang, H. (2017). Preparation and properties characterization of straw fiber hollow ceramite concrete. Build. Energy Conserv. 45 (07), 68–70+77. doi:10.3969/j.issn.1673-7237.2017.07.012
Samosir, F., Hutabarat, L. E., Purnomo, C. C., and Tampubolon, S. P. (2021). The effect of bagasse fibers material with pumice as a partial substitution of coarse aggregate to increase compressive strength and tensile strength on lightweight concrete. IOP Conf. Ser. Earth Environ. Sci. 878 (1), 012046. doi:10.1088/1755-1315/878/1/012046
Sreelakshmi, M. G., Chandru, U., and Senthilkumar, R. (2023). Strengthening stainless steel tubular beams using fibre-reinforced concrete incorporating sugarcane bagasse ash. J. Constr. Steel Res. 211, 108197. doi:10.1016/j.jcsr.2023.108197
Sun, Y., Zhang, P., Guo, J., Wang, L., and Wu, J. (2024). Rheological properties and workability of PVA fiber and nano-SiO2 modified cement-based materials. Dev. Built Environ. 18, 100396. doi:10.1016/j.dibe.2024.100396
Tan, Z. (2023). Study on uniaxial tension constitutive relationship of bamboo fiber concrete. Central South Univ. For. Technol. doi:10.27662/d.cnki.gznlc.2023.001113
Wang, J. M., Zhu, C., Cheng, B., and Liu, J. (2020). A multiscale model for the elastic modulus of ceramsite lightweight aggregate concrete after elevated temperatures. Revista Romana de Materiale - Romanian J. Mater. 50 (2).
Wang, K., Chen, G., Li, J., Wang, Z., and Chen, L. (2016). Study on Effect of cotton stalk fiber on mechanical properties of ceramsite foam concrete. New Build. Mater. 43 (07), 113–116.
Wang, P., Li, D., Shen, C. W., Jiang, W. T., and Wang, J. M. (2013). Experiment on the mechanical behavior of ceramsite concrete under temperature-load coupling field. Appl. Mech. Mater. 2546 (357360), 817–820. doi:10.4028/www.scientific.net/amm.357-360.817
Wu, X. gang, Yang, J., Lin, H., Wang, Q., and Cao, Z. (2022). Mechanical properties and damage mechanism of shale ceramsite concrete after high-temperature treatment. J. Mater. Civ. Eng. 34 (7). doi:10.1061/(ASCE)MT.1943-5533.0004279
Xu, C. (2013). Mix ratio design and preparation of LC50 high strength lightweight aggregate concrete. Commer. Concr. (7), 32–33.
Yu, M. (2019). Study on Physical and mechanical properties of wheat straw fiber porous ceramite concrete. Henan Univ.
Zeng, Z., and Hu, Y. (2003). Experimental study on mechanical properties of steel fiber lightweight aggregate concrete. J. Build. Struct. 24 (5), 78–81. doi:10.14006/j.jzjgxb.2003.05.011
Zhang, P., Feng, Z., Guo, J., Zheng, Y., and Yuan, P. (2024a). Mechanical behavior and microscopic damage mechanism of hybrid fiber-reinforced geopolymer concrete at elevated temperature. Ceram. Int. 50 (24PB), 53851–53866. doi:10.1016/j.ceramint.2024.10.238
Zhang, P., Feng, Z., Guo, J., Zheng, Y., and Yuan, P. (2024b). Mechanical behavior and microscopic damage mechanism of hybrid fiber-reinforced geopolymer concrete at elevated temperature. Ceram. Int. 50 (24PB), 53851–53866. doi:10.1016/j.ceramint.2024.10.238
Zhang, P., Han, X., Hu, S., Wang, J., and Wang, T. (2022). High-temperature behavior of polyvinyl alcohol fiber-reinforced metakaolin/fly ash-based geopolymer mortar. Compos. Part B 244, 110171. doi:10.1016/j.compositesb.2022.110171
Zhang, P., Sun, Y., Wu, J., Hong, J., and Gao, Z. (2023). Mechanical properties and microstructure of nano-modified geopolymer concrete containing hybrid fibers after exposure to elevated temperature. Constr. and Build. Mater. 409, 134044. doi:10.1016/j.conbuildmat.2023.134044
Zhang, X., Wang, D., Zhang, D., and Li, H. (2019). Study on the influencing factors of mechanical properties of straw fiber lightweight aggregate concrete. Bull. Silic. 38 (05), 1369–1376. doi:10.16552/j.cnki.issn1001-1625.2019.05.012
Keywords: bagasse fiber ceramsite concrete, high temperature, bagasse fiber, compressive strength, splitting tensile strength
Citation: Yu X, Liu C, Wang J, Liu M, Bai D, Zhou S, Chen J and Liu J (2025) High-temperature mechanical performance of bagasse fiber ceramsite concrete and mortar. Front. Mater. 12:1549843. doi: 10.3389/fmats.2025.1549843
Received: 22 December 2024; Accepted: 24 March 2025;
Published: 25 April 2025.
Edited by:
Geoffrey Robert Mitchell, Polytechnic Institute of Leiria, PortugalReviewed by:
Peng Zhang, Zhengzhou University, ChinaAbdul Bari Jabar, K. S. Rangasamy College of Technology, India
Copyright © 2025 Yu, Liu, Wang, Liu, Bai, Zhou, Chen and Liu. This is an open-access article distributed under the terms of the Creative Commons Attribution License (CC BY). The use, distribution or reproduction in other forums is permitted, provided the original author(s) and the copyright owner(s) are credited and that the original publication in this journal is cited, in accordance with accepted academic practice. No use, distribution or reproduction is permitted which does not comply with these terms.
*Correspondence: Jing Liu, NjYxNDA2MkBnbHV0LmVkdS5jbg==