- 1Department of Ocean Science and Engineering, Southern University of Science and Technology, Shenzhen, Guangdong, China
- 2School of Engineering, The University of Queensland, St.Lucia, QLD, Australia
The lightest engineering metal magnesium (Mg) alloys have many potential structural and functional applications. However, due to the intrinsic activity of Mg, Mg alloys are not corrosion-resistant. Particularly the severe galvanic corrosion of Mg alloys in contact with other metals in engineering limits the industrial applications. There is currently no cost-effective solution to this stubborn problem. This short review systematically introduces the strategy of galvanic corrosion mitigation, and briefly summarizes the existing approaches that have been used to reduce the galvanic corrosion damage. It appears that the surface alloying that can convert the surface of a Mg alloy into a passive metal is the most promising technique. Based on the existing results in the area of Mg surface alloying, future research directions are listed at last.
1 Introduction
Magnesium (Mg) alloys have many potential applications, particularly in the auto, aerospace, military, and electronic industries, as structural and functional materials. Firstly, Mg alloys as a structural material due to the well-known low density are very attractive to engineers. They have great potential in weight-sensitive industries like electronics, automotive and aerospace (Zeng et al., 2018; Song et al., 2020; Luo et al., 2019; Xie et al., 2023; Zhang et al., 2023). Secondly, Mg alloys have many favorable properties to enable their functions in special applications. For example, due to the negative open-circuit potential (OCP) of Mg, Mg alloys have been traditionally used as a sacrificial anode to cathodically protect other engineering metals (Song and Atrens, 2023; Song et al., 2004). A new development in this area is the use of Mg alloys as intelligent anodes to smartly protect reinforced concrete (Wu et al., 2021; Yan et al., 2019). Recently, researchers also carried out many investigations in the fields of Mg-air battery and hydrogen storage (Ma et al., 2020; Khajondetchairit et al., 2022; Bao et al., 2023; Chen et al., 2024; Cao et al., 2023; Ouyang et al., 2020). Moreover, the great biocompatibility and high corrodibility of Mg have also interested many researchers who are trying to use Mg alloys as biodegradable implants in the human body (Sekar and Panigrahi, 2024; Kim and Pan, 2023; Cui et al., 2020; Song, 2007; Antoniac et al., 2020).
However, Mg alloys generally have low corrosion resistance in water containing media (Benbouzid et al., 2022; Sha et al., 2022). Particularly due to the highly active nature of Mg in comparison with other structural metals (ASTM G82-98, 1998), the macro-galvanic corrosion of Mg alloys in connect with other engineering metals, which is commonly encountered in engineering applications, has become the main hurdle badly restricting the industrial applications (Isacsson et al., 1997). To enable the use of Mg alloys in engineering, the stubborn galvanic corrosion issue must be addressed.
Although galvanic corrosion of Mg alloys is a small scope in research, it is a big challenge in engineering. In theory, the protection against galvanic corrosion can also inherently inhibit the self-corrosion of a metal. This mitigation effect is particularly significant for Mg alloys, because the additional dissolution damage due to the negative difference effect of Mg can also be inhibited when the galvanic corrosion process is suppressed. Hence, it is of great significance to summarize and review promising results and progress in time in this narrow field.
2 Galvanic corrosion of Mg alloys
Galvanic corrosion is simply the anodic dissolution of a relatively active metal (anode) being accelerated by a relatively noble metal (cathode) in electronic contact (Lee, 2006; Yadava et al., 2007). It should be noted that the galvanic effect induced additional corrosion can also occur microscopically between different phases in an alloy (Andrade et al., 2008; Tsai and Chen, 2007). In this review, galvanic corrosion, if not specified, will simply refer to the macro-galvanic corrosion between two metals, which has been commonly known in most industrial communities.
The rate of galvanic corrosion in general can be simply expressed by the galvanic current Ig from the anodic metal through the solution to the coupled cathodic metal (Saeed, 2024; Song et al., 2004):
where EMcorr and EPcorr are the corrosion potentials of the corroding metal (anode) and coupled metal (cathode), respectively, RMp and RPp are their average polarization resistances respectively, and RS is the total solution resistance between them. Around this simple equation, there have been many studies so far (Wagner, 1951; Hack, 1988; Tavakkolizadeh and Saadatmanesh, 2001; Wu et al., 2022; Oldham and Mansfeld, 1972; Liang et al., 2023; Zhang et al., 2008; Schneider et al., 2014) on the damage estimation (Ma et al., 2020; Wagner, 1951), the experimental measurements (Ma et al., 2020), the numerical (Verbrugge, 2006; Jia et al., 2006) and analytical predictions of galvanic processes (Song, 2010).
Compared with the other metals, Mg alloys suffer from much severe and complex galvanic corrosion in most natural environments. This is primarily because Mg has the most negative OCP in all the engineering metals, and secondly its anodic polarization resistance is very low (i.e., the anodic polarization current densities are always high). Moreover, the unique processes involved in the dissolution of a Mg alloy, such as the negative difference effect (Song and Atrens, 2023; Huang et al., 2020; Huang et al., 2023), poisoning effect, passivation effect, and alkalization effect (Song et al., 2004), also further complicate and exacerbate the damage. Unfortunately, the galvanic corrosion of Mg alloys in practice is almost inevitable, because in industry the electronic continuity between the anodic and cathodic metals cannot be simply stopped. For example, 1) the anode and cathode sometimes must be electronically connected to transfer signals, 2) the physical disconnection of the joint should usually be avoided from a viewpoint of structural strength, or 3) an additional manufacturing cost always incurs if an insulator is inserted in the anode-cathode joint, which may be unaffordable in enterprise management. Even worse, the ionic path between the anode and cathode through the electrolyte cannot be easily blocked either by coverage of the couple surfaces with an insulating coating or alteration of the geometric shapes of the couple (Song and Yao, 2025). Consequently, even though galvanic corrosion is a simple electrochemical process (there is nothing new in theory), the mitigation of galvanic corrosion for Mg alloys in practice is extremely challenging (Song and Atrens, 2023).
3 Approaches of mitigating galvanic corrosion
Since it is impractical to cut off the electronic path or block the ionic flow between the galvanic anode and cathode, the only effective way of mitigating the galvanic corrosion of a Mg alloy should be passivating the Mg alloy surface (i.e., enhancing its average anodic polarization resistance RpM up to an extremely high level) to lower the galvanic current density according to Equation 1. The basic principles are further illustrated in Figure 1.
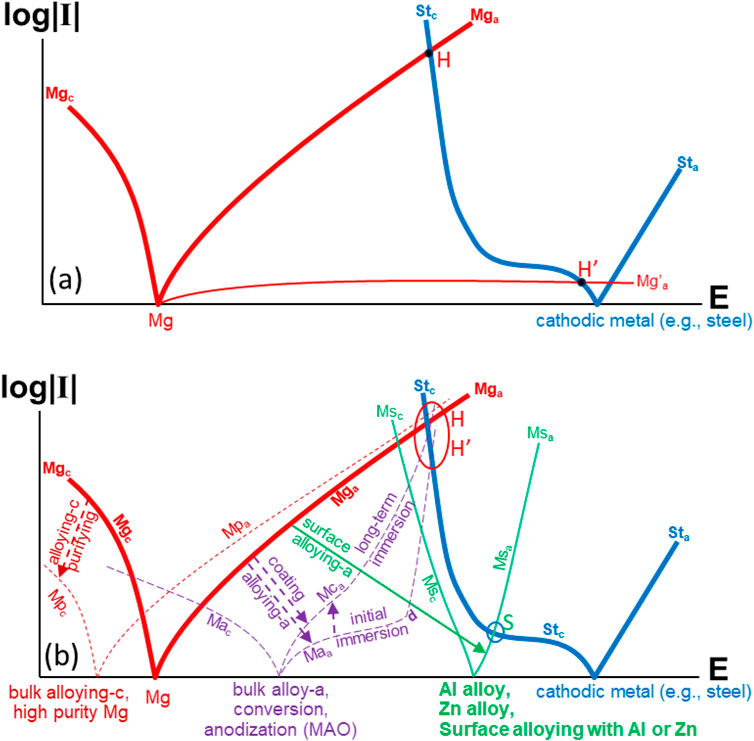
Figure 1. Schematic illustration of mitigating the galvanic corrosion of Mg caused by an electronically coupled cathode (e.g., steel): (a) effect of varied anodic polarization curve of Mg on galvanic corrosion (b) effect of bulk alloying, coating, surface conversion, and surface alloying of Mg on anodic polarization curve and galvanic corrosion of Mg (polarization curves of cathodic metal steel, anodic Mg, Mg alloys, Mg covered with different coatings, and Mg surface alloyed with Al or Zn).
In Figure 1a, the cathodic and anodic polarization curves of Mg are denoted as Mgc and Mga, while those of the cathode (steel) are Stc and Sta, respectively. When Mg and steel are coupled together, the anodic polarization curve (i.e., curve Mga in Figure 1a) of the Mg and the cathodic polarization curve (i.e., curve Stc in Figure 1a) of the cathodic metal (e.g., steel) intersect at point H, which represents the galvanic potential (Eg) and current density (Ig) of the couple. The higher the H (i.e., Ig), the more severe galvanic corrosion the Mg alloy will have. Generally, the galvanic corrosion rate of a Mg alloy coupled with a steel is very high. If the Mg can be passivated, its anodic polarization curve Mga will be dramatically lowered down to curve Mg’a, which intersects with the cathodic polarization curve Stc of the steel at a very low point H’ (see Figure 1a). Thus, the galvanic corrosion of the self-passivated Mg can be effectively suppressed. In this case, the most outstanding feature of such a self-passivated Mg is its self-healing capability. If the Mg surface is activated mechanically or electrochemically during installation or service, it can be rapidly re-passivated, which will fundamentally decrease the risk of accelerated corrosion locally in the damaged area. However, ideal passivation of Mg is difficult, and so-far it has not been achieved in engineering.
There have been many research efforts on mitigating the galvanic corrosion of Mg alloys in industry (Song et al., 2004; Zhang et al., 2008). Figure 1b schematically illustrates the approaches that have been taken to improve the corrosion resistance, including the galvanic corrosion resistance, of Mg alloys. Alloying (i.e., bulk alloying) is one of the most popular methods. Various elements have been added to Mg to reduce the corrosion rate (Liang et al., 2023; Li et al., 2022; Gusieva et al., 2014). Some of the alloying elements mainly remove the impurities (mainly Fe, Cu and Ni) in Mg (Liu and Song, 2013; Prasad et al., 2012) (which is also termed as purification), or basically inhibit the cathodic reaction on Mg (Makar and Kruger, 1993; Liu et al., 2018). This kind of alloying in effect lowers the cathodic polarization curve of Mg (curve Mgc shifts down to curve Mpc along arrow “alloying-c” as shown in Figure 1b). Although the alloying can reduce the self-corrosion rate of Mg, negatively shifting the OCP, it cannot effectively lower the anodic polarization curve of Mg (curve Mpa is not lower than curve Mga as shown in Figure 1b). Hence, the galvanic corrosion rate indicated by point H′ in Figure 1b is still high, close to point H. In some sense, the alloying has an effect similar to purifying, which inhibits the self-corrosion of Mg at the OCP, but does not satisfactorily suppress the galvanic corrosion at the galvanic potential.
There are also some alloying elements, like Al, Zn, Ti, Sn, Cr, etc. (Candan et al., 2016; Kubásek et al., 2013; Staišiūnas et al., 2014) that can more or less retard the anodic reaction on Mg, positively shifting the OCP, and consequently lowering the galvanic corrosion rate. In this case, the anodic polarization curve Mga in Figure 1b is lowered down to curve Maa along arrow “alloying-a”. However, such bulk alloyed Mg still has relatively high anodic current densities at more positive potentials. Thus, curve Maa eventually intersects with curve Stc at point H′, which is still very high (close to point H as shown in Figure 1b). So far, in experiment no element has been identified that can alloy with Mg within its solid solubility limit to dramatically reduce the anodic current densities of Mg at potentials more positive than −1.4 V ∼ Ag/AgCl (This potential is much more negative than the OCP of a steel, and Mg can easily be galvanically polarized to the potential or a more positive level if it is in contact with the steel). This implies that almost all the Mg alloys will suffer from severe galvanic corrosion if they form a joint with steels. In other words, the galvanic corrosion of Mg alloys cannot be effectively suppressed through their conventional bulk alloying.
The reduction of anodic current densities of Mg in the potential range around the OCP by the bulk alloying with those elements can be attributed to the direct buildup of a corrosion product film on the Mg surface (Annamalai et al., 2019; Zeng et al., 2014). Unfortunately, due to the limited solid solubility of these elements in Mg, a highly protective film cannot be stably formed. Hence, the film will lose its retarding effect at a more positive potential, and the anodic current density will eventually increase more rapidly (curve Maa bends up after point “d” as shown in Figure 1b). Even worse, when the amounts of the elements exceed their solid solubility limits in Mg, the precipitation of the element-containing phases may act as a cathode to accelerate the corrosion of the Mg matrix through micro-galvanic effect.
Apart from the self-grown surface film on Mg in the service environment, films may also be formed in some specially prepared media before service either with (e.g., anodized coatings) or without (e.g., conversion coatings) the aid of electric field (Pillado et al., 2023; Mu et al., 2014; Zhang et al., 2019; Muhaffel and Cimenoglu, 2019; Zhang et al., 2018). The Mg surface coated with such a coating or film has much lower anodic current densities at low anodic potentials initially, having an anodic polarization curve similar to that of a bulk alloyed Mg (see curve Maa which shifts from curve Mga along arrow “coating” in Figure 1b). However, the coating cannot withstand a higher potential or long-term exposure in service environments. The anodic polarization current densities increase with time (curve Maa moves up to curve Mca in Figure 1b). Therefore, if such coated Mg is coupled with a steel, its galvanic corrosion rate will become higher eventually (also close to point H as indicated by point H′ in Figure 1b).
Since neither surface coating nor bulk alloying can render Mg passivity to exhibit an ideal anodic polarization behaviour as illustrated in Figure 1a. To inhibit the galvanic corrosion of Mg, surface alloying must be considered. It can convert Mg surface into a self-passive non-Mg metal (Song and Atrens, 2023; Song et al., 2016; Cao et al., 2016; Zhu et al., 2021a) like stainless steel.
The word “stainless” used to describe a steel generally refers to the self-passivating phenomenon. It will be of great significance if the “stainless” performance could be transplanted to Mg alloys. Inspired by this idea, Song and Atrens in their early publication (Song and Atrens, 2003) urged to develop “stainless steel”-like corrosion resistant Mg alloys via properly alloying Mg with suitable elements to produce a passive film on the surface. In 2013, the concept of “stainless Mg” was clearly proposed again (Atrens et al., 2013), and further discussed based on some non-equilibrium Mg alloys (Song et al., 2016; Cao et al., 2016). Strong self-passivity is regarded as an essential pre-requisite to ensure the important self-healing capacity (Song and Atrens, 2023; Song et al., 2016; Cao et al., 2016). Unfortunately, experiments so far have proved it extremely challenging to produce a real stainless Mg alloy through alloying Mg bulk with passivating elements, like Cr, Ni, Mo in Mg (Zhu et al., 2021a), in a conventional way because of the relatively low solid solubility limits of these elements. Also, the high densities of these passivating elements can easily turn a Mg alloy into a heavy metal, which limits their addition amounts in Mg. Without sufficient addition, it is impossible to suppress the Mg activity.
Different from bulk alloying, surface alloying can change the composition only in a thin layer to generate a self-passivating surface (Song et al., 2016; Cao et al., 2016). In this case, addition amounts of the alloying elements will not be limited by their solubilities and densities, because the surface can more easily be alloyed than the bulk through a non-equilibrium approach. More attractively, the surface alloying does not change the bulk properties of a Mg alloy. These offer many new possibilities for the development of a “stainless” surface layer for Mg alloys.
Ideally, the alloyed surface layer should have an anodic polarization curve similar to a stainless steel, i.e., the anodic current densities should be always very low in the potential range from the OCP of the substrate Mg up to the OCP of the coupled cathodic metal (e.g., steel) to ensure the galvanic current density Ig to be low enough as indicated by point H′ in Figure 1a. Following this idea, research work should be focused on the selection of suitable passivating elements and the development of surface alloying techniques. A promising approach is the surface alloying with Al or Zn as shown in Figure 1b, which is summarized as follows:
In Figure 1b, the intersection of curve Msa with curve Stc at point S implies that Al or Zn has a very low galvanic corrosion rate if it is coupled with a steel. If the surface of a Mg alloy can be converted into Al or Zn or their alloys, then there will be no concern about the galvanic corrosion. In experiment, the Mg surface may be converted to Zn or Al through a surface alloying process. This can be realized via thermal-diffusion or hot-dipping. Such an alloyed Mg surface layer can be relatively thick and resistant to corrosion and galvanic corrosion, having great adhesion to the substrate (Zhu et al., 2021a; Shigematsu et al., 2000; Zhu et al., 2005). Compared with other methods, such as cladding, platting, or ion implantation, the thermal-diffusion and hot-dipping are relatively simple, low cost, robust, corrosion-resistant, and strongly adhesive. They are practically feasible, and have appeared to be most promising so far, having attracted many research interests recently.
4 History and recent developments
The thermal-diffusion to form a surface alloy layer was first developed by Shigematsu et al., (Shigematsu et al., 2000), through embedding AZ91D in Al powder at 450°C. The 750 μm thick aluminum alloy surface layer they obtained had enhanced resistance to corrosion and wear. Soon the surface alloying process for Mg alloy was improved by zhang et al. (Zhang and Kelly, 2002) using a powder mixture containing 70% Al and 30% Zn at 430°C. Further to the surface alloying, Zhu and Song (2006) pre-coated AZ91D with a paste made of liquid ethylene glycol and solid powder mixture of Al + Zn, and then heated the paste-coated Mg alloy in sand at 420°C for 1.5 h to speed up the thermal diffusion of Al and Zn into the substrate alloy. The alloyed surface was measured to corrosion resistance about 20 times higher than the uncoated counterpart. Figure 2a schematically illustrates the simple setup of the thermal-diffusion process. That study implied that any components made of Mg alloys with complicated geometric shapes could be placed in a crucible to alloy their surfaces at a controlled temperature for a certain period of time. The success of this method is critically determined by the thermal-diffusion temperature. If the temperature is too low, it will be difficult for alloying elements to diffuse into the surface layer of the substrate Mg alloy, whereas a too high temperature will over-heat the substrate and adversely alter its microstructure and deteriorate the mechanical performance of the alloy.
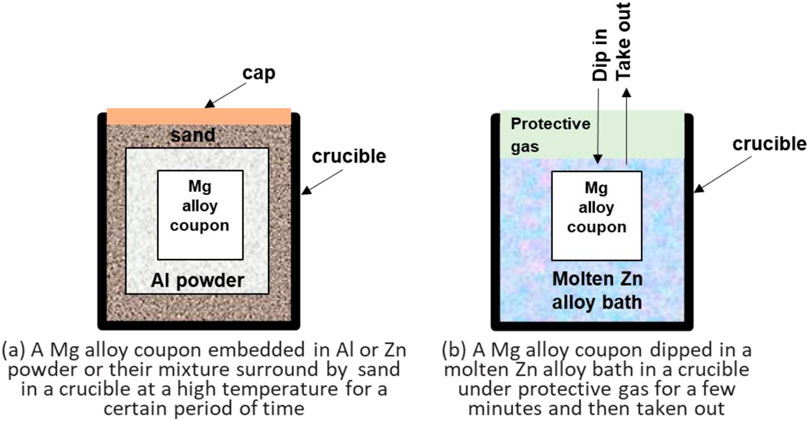
Figure 2. Schematical illustration of the setup for surface alloying of a Mg alloy through (a) thermal diffusion in metallic powder containing passivating elements (e.g., Al) at a high temperature, and (b) hot-dipping in a molten alloy (e.g., Zn alloy) bath under argon protection.
To understand the thermal-diffusion and phase transformation during the surface alloying, a multi-layer surface was fabricated on AZ91E in powder mixtures with different ratios of Al over Zn at different temperatures (Hirmke et al., 2011). It was found that the presence of Zn in the powder could promote the diffusion of Al into the substrate. As shown in Figure 3, with increasing Zn content in the powder mixture, the thickness of the alloyed surface layer significantly increased.
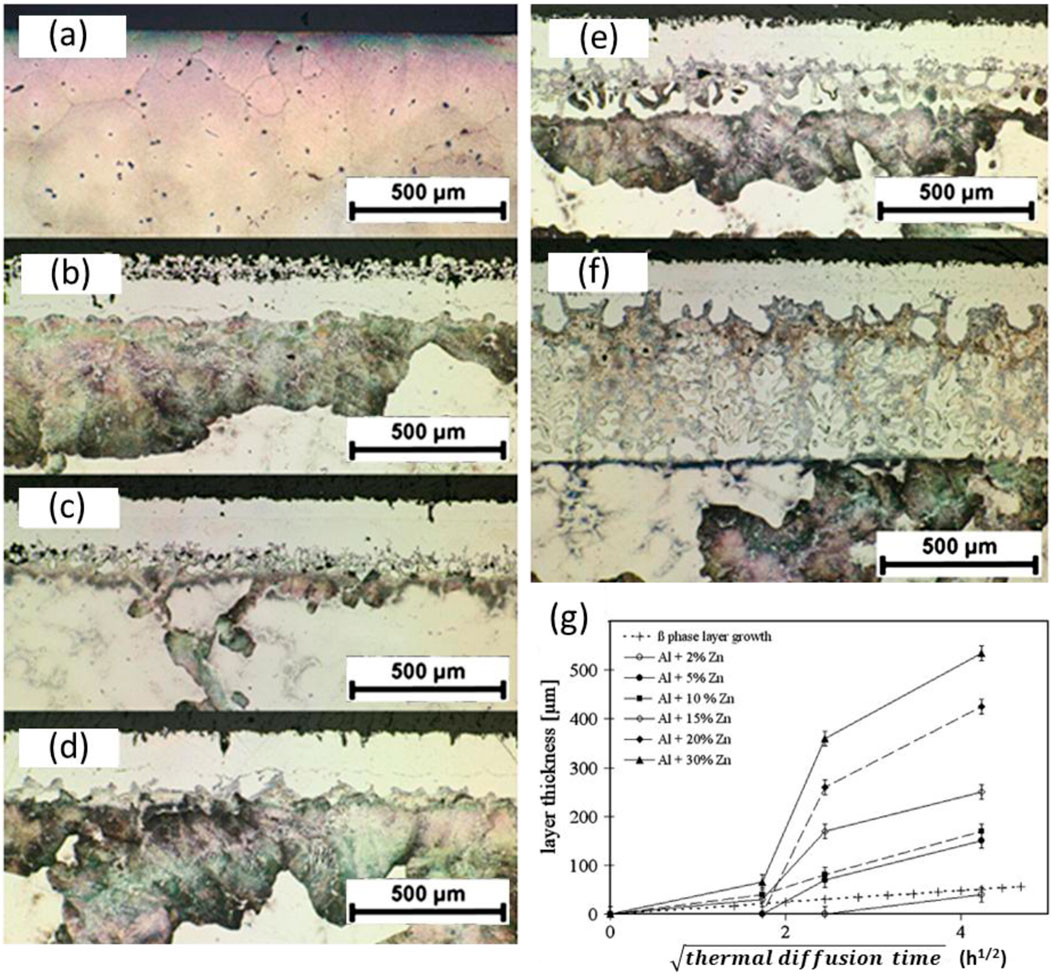
Figure 3. Cross-sectional optical micrographs of AZ91E samples embedded in packed Al-Zn powder mixtures with varying Zn contents (a) 0wt%, (b) 2wt%, (c) 5wt%, (d) 10wt%, (e) 20wt%, and (f) 30wt% at 413°C for 18 h, and (g) the dependence of alloyed surface layer thickness on thermal diffusion time at 400°C in the powder mixtures with different zinc contents (Hirmke et al., 2011).
So far, all the reported thermal-diffusion surface alloying treatments were performed at a relatively high temperature for a relatively long time, which will inevitably alter the microstructure, and may badly influence the properties of the substrate Mg alloy. It is unacceptable in industrial applications. To lower the processing temperature, Zhu et al. (Zhu et al., 2021a) burnished Mg and its alloy surfaces before thermal-diffusion, and found that the burnishing could refine the Mg grains, and change the crystal orientation of the grains in the surface layer, resulting in basal crystalline planes on the Mg alloy surface exposed to the environment, which significantly enhanced the corrosion resistance (Pu et al., 2011; Pu et al., 2012). It was originally expected that the burnishing induced grain refinement and crystal orientation sped up the Al diffusion during the surface alloying. However, neither the thermal-diffusion temperature nor the processing time was satisfactorily reduced in experiment. In spite of the unsatisfactory diffusion temperature and time, the study had a few impressive findings: 1) The Al-alloyed surface layer was a few millimeters thick and had a transient zone, which ensured high wear resistance and good adhesion (see Figure 4a). 2) The Al-alloyed surface had good passivity and was very resistant to galvanic corrosion; the burnished and Al-alloyed surface had a breakdown potential more positive than 1 V ∼ Ag/AgCl (see Figure 4b). 3) Scratching on the burnished and Al-alloyed surface did not lead to significantly increased galvanic current densities (see Figures 4c, d). In that work, it was the first time that the alloyed Mg surface after scratching was still resistant to galvanic corrosion attack.
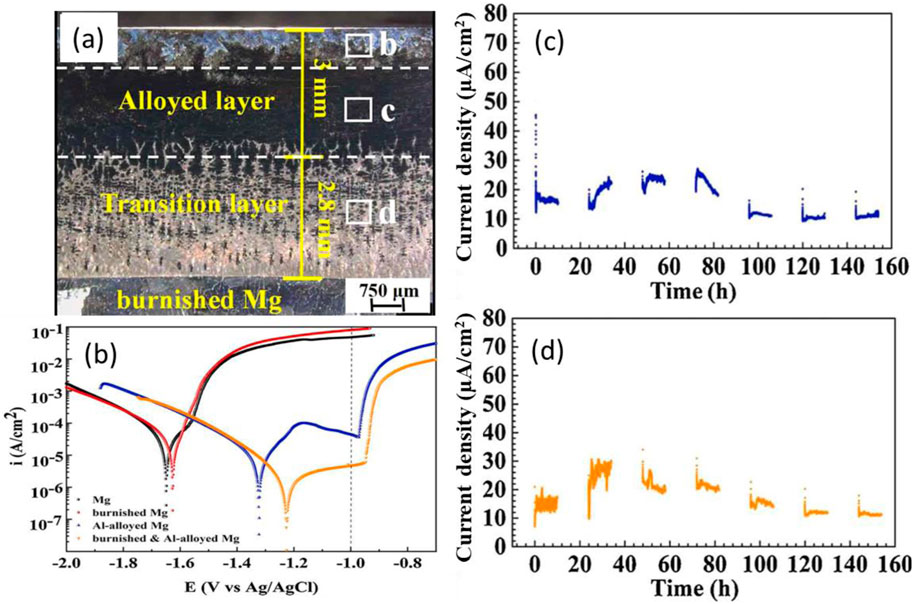
Figure 4. (a) Cross-section of pure Mg after burnishing and surface-alloying in Al powder at 450°C for 2 h (see Figure 2a), (b) polarization curves of pure Mg, the burnished surface, the Al-alloyed surface, and the burnished and Al-alloyed surface of Mg, and the galvanic current densities changing with time for (c) the burnished and Al-alloyed surface of Mg before, and (d) after scratching coupled with a pure Zn coupon in 3.5 wt% NaCl solution (Zhu et al., 2021a; Zhu et al., 2021b).
In addition to the improved galvanic corrosion resistance by thermal-diffusion, it was also found that the alloyed surface provided a suitable base for formation and growth of layered double hydroxide (LDH), which further enhanced the passivity and thus suppressed the galvanic corrosion of a Mg alloy (Zhu et al., 2021b).
However, the thermal-diffusion temperature or time required for the surface alloying remains an issue to address, as the high temperature and/or long heating time can change the microstructure of a Mg alloy, and consequently deteriorate its mechanical performance.
5 The most promising process
An alloyed surface layer can also be obtained by hot-dipping. Such a process has the potential in theory to significantly shorten the surface alloying time.
In fact, hot-dipping has been used to galvanize steels for a long-time, which can generate a Zn-alloy coating to sacrificially protect the substrate steel, and has been widely used in various industries and everyday life (Marder, 2000; Schuerz et al., 2009; Seré et al., 1999; Shibli et al., 2015). It is a rapid treatment performed in a molten Zn alloy bath. Different from an electro or electroless plating/galvanizing process, hot-dipping does not use any solution bath, and its molten Zn alloy bath can be easily recycled. There is no environment pollution issue in industry. The idea of transplanting this method to Mg alloy surfaces was recently tested by Hu et al. (Hu et al., 2022). The results indicated that after a few seconds of dipping in a molten Zn-3Mg bath at 390°C ± 5°C, an alloyed surface layer could be formed on AZ31, which had an alloyed zone containing Zn, Mg2Zn11, Mg7Zn3, and MgZn2 phases, and a diffusion zone consisting of MgZn and Mg7Zn3 MgZn2 phases. The study validated that an alloyed surface layer could be very well formed on a Mg alloy. However, the galvanic corrosion performance of the hot-dipped Mg alloy was not tested in that impressive work.
On basis of the successful hot-dipping process developed by Hu et al. (Hu et al., 2022), we recently further investigated the galvanic corrosion behavior of such an alloyed surface layer on WE43 via a similar hot-dipping process as schematically illustrated in Figure 2b (Hu et al., 2022). In our study, a Mg alloy WE43 coupon was dipped in a molten Zn alloy bath containing 3 wt% Al and 2 wt% Mg at 360°C for less than 30 s (Song, 2011). This hot-dipping temperature was the lowest in all the reported surface alloying processes, and the time was also very short. In such a short dipping time, the microstructural changes of the substrate Mg alloy would be negligible, which would ensure a high production efficiency if the process could be industrialized. The detailed study will be published separately (Yang and Song, 2019). Only some of the preliminary results are presented in Figure 5 to illustrate the innovative points of the hot-dipping method and to demonstrate the future research directions.
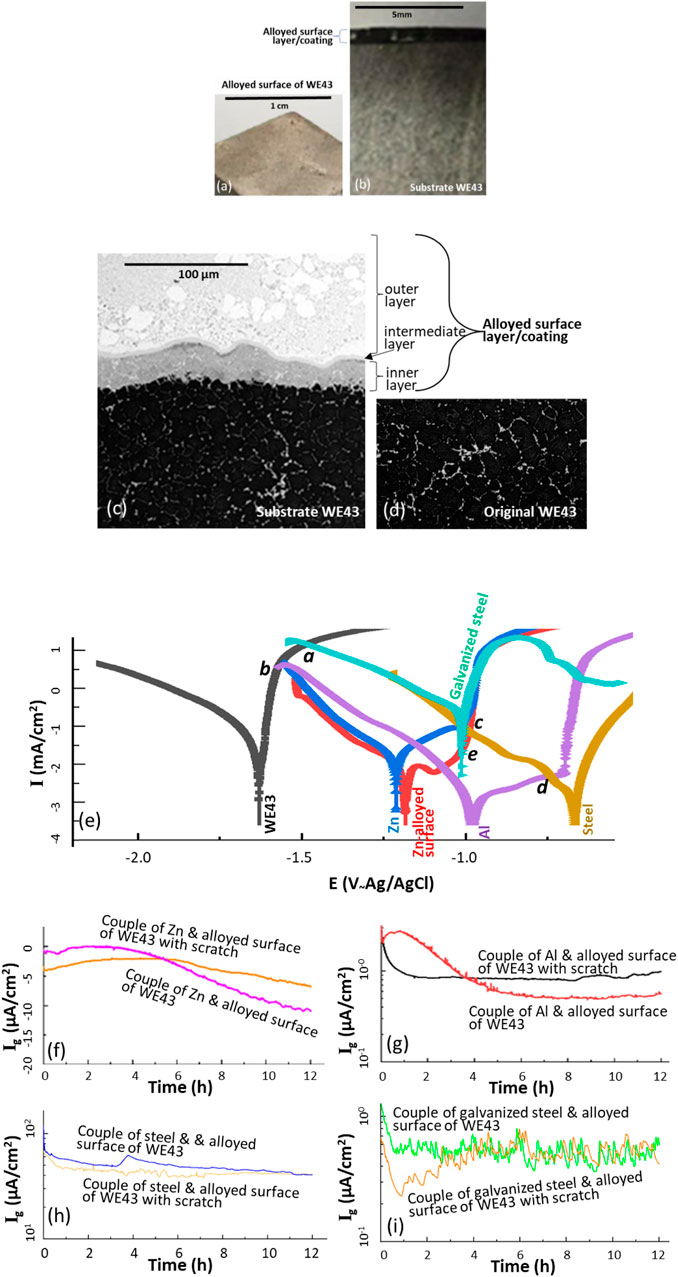
Figure 5. (a) Appearance of the alloyed surface of WE43 after hot-dipping in the molten Zn alloy bath at 360°C for 10–30 s in argon atmosphere (see Figure 3b), (b) optical image and (c) SEM image of the cross-section of the alloyed surface layer formed on Mg alloy WE43 after the hot-dipping, (d) the SEM image of the WE43 before the hot-dipping, (e) polarization curves of Zn, Al, the original WE43, the alloyed surface of the WE43, steel and galvanized steel in 3.5 wt% NaCl solution at room temperature, the galvanic current densities of galvanic couples of (f) Zn coupon and alloyed surface of WE43 with and without scratch, (g) Al coupon and alloyed surface of WE43 with and without scratch, (h) alloyed surface of WE43 and steel, and (i) alloyed surface of WE43 and galvanized steel.
Figure 5a presents the macro-appearance of the alloyed surface of WE43 via the hot-dipping. The alloyed surface layer was uniform in thickness, around 1 mm (see Figure 5b), having three sublayers: inner, intermediate and outer (see Figure 5c). The multi-sublayer microstructure had a compositional gradient from Mg alloy to Zn alloy, which could further reduce the detrimental galvanic effect between the surface layer and the substrate Mg alloy in case the former is damaged and the latter exposed locally. A comparison of the substrate Mg alloy before (Figure 5d) and after (Figure 5c) the hot-dipping does not show any difference in microstructure, verifying that this hot-dipping did not alter the microstructure of the substrate Mg alloy.
The polarization curve measurements (see Figure 5e) indicated that the Zn-alloyed surface of Mg alloy WE43 had an OCP similar to Zn, and better passivity than the latter. The passive current densities in the passive region from the OCP to -1 V ∼ Ag/AgCl of the Zn-alloyed surface lower than those of Zn could be ascribed to the beneficial effect of Mg in Zn (Yao et al., 2016). The Zn-alloyed surface of the of the Mg alloy had a much lower corrosion rate and more positive OCP than those of the Mg alloy before hot-dipping. In Figure 5e, the anodic polarization curve of WE43 intersects with the cathodic polarization curve of steel or galvanized steel at point a, in the order of 10 mA/cm2, which is a galvanic current density high enough to lead to disastrous galvanic corrosion damage if the Mg alloy is directly coupled with the steel or galvanize steel. The anodic polarization curve of the Mg alloy intersects with the cathodic polarization curve of the Zn-alloyed surface at point b. This means that severe galvanic corrosion will occur on the substrate if the Zn-alloyed surface layer is broken. Therefore, the alloyed surface layer must be thick and adhesive enough to be resistant to mechanical damage.
A meaningful result of the polarization measurements was the anodic polarization curves of Zn and Al which met with the cathodic polarization curves of the steel and galvanized steel at points c and d, respectively. They were two orders of magnitude lower than points a and b, respectively, suggesting that the galvanic corrosion caused by the steel or the galvanized steel could be effectively suppressed if the Mg alloy surface could be converted to Zn or Al. This idea was tested experimentally with the hot-dipping process that converted the WE43 surface into a Zn alloy in the molten bath containing 3 wt% Al and 2 wt% Mg at 360°C for less than 30 s. As shown in Figure 5e, the anodic polarization curve of the Zn-alloyed surface of WE43 intersects with the cathodic polarization curves of the steel and galvanized steel at c and e, respectively. Point e corresponds to a galvanic current density around 10–30 μA/cm2, close to a passivating current density (a few µA/cm2), one order of magnitude lower than point c. This implies that the galvanic corrosion of the surface-alloyed WE43 caused by the galvanized steel would be significantly lower than that caused by the steel. In other words, the severe galvanic corrosion problem of a Mg alloy coupled with a steel could be solved if the surface of the Mg alloy could be alloyed properly with Zn and meanwhile the steel be galvanized.
The galvanic corrosion behaviors expected from the polarization curve measurements were further verified by surface-alloyed WE43 coupons. They were one-to-one coupled with Zn and Al coupons, respectively. Some of the alloyed surfaces of the WE43 were scratched while the others were not. As shown in Figures 5f, g, the galvanic current densities of the alloyed surfaces of the WE43 with and without scratch coupled with Zn or Al were all negligible. Further to the promising results, it was measured that the alloyed surfaces of the WE43 with and without scratch had galvanic current densities around 50 μA/cm2 when they were coupled with steel (see Figure 5h). If the steel was galvanized, then the galvanic current densities of the alloyed surfaces of the WE43 with and without scratch were less than 1 μA/cm2 (see Figure 5i), which is negligible in engineering. According to this electrochemical result, the average depth of galvanic corrosion on the surface alloyed Mg alloy in contact with galvanized steel will be 1 mm in 50 years only. It is even not deep enough to penetrate the alloyed surface layer. Hence, the self-passive surface coating generated by hot-dipping is much more durable than any other coatings formed via chemical conversion or electrochemical MAO. It should be noted that in reality, galvanized steels are widely used. It is quite possible to use a galvanized steel to replace bare steels. This should to a great extent solve the galvanic corrosion problem with Mg alloys in industry.
Another interesting finding from Figure 5e was point d in the order of µA/cm2. This signifies that the galvanic corrosion of a Mg alloy caused by a steel may be effectively retarded if the surface of the Mg alloy can be converted to Al. Certainly, the generation of such a high-quality surface layer similar to pure Al on a Mg alloy is quite challenging.
6 Challenges
The hot-dipping process in theory can quickly generate a thick alloy surface layer on a Mg alloy, but many complicated changes and processes are involved in the process (Hu et al., 2022). At least, the surface alloying concerns the diffusion of alloying elements, the nucleation, growth and transformation of some equilibrium and non-equilibrium phases in the zone between the substrate Mg alloy and the adjacent molten alloy bath, the solidification of the molten alloy, and the heating and cooling of the substrate alloy, molten bath and their interface. Specifically speaking, there are endothermic and exothermic reactions associated with Zn containing intermetallic phases (Morishita et al., 2006) during the surface alloying process, which may significantly alter the temperature distribution in the transitional zone between the substrate Mg alloy and the molten alloy bath, complicating the surface alloying and thus influencing the quality of the alloyed surface layer. Only after the detailed alloying mechanism is comprehensively understood, can the hot-dipping technique be further improved, and an ideally alloyed surface of Mg alloys be achieved.
Another challenge is the control of surface quality and geometry of the alloyed surface of a Mg alloy. The alloyed surface layer may not be so uniform in thickness, composition and microstructure. For example, the surfaces obtained via thermal-diffusion (Zhu and Song, 2006) and hot-dipping (see Figure 5a) are rougher than the original surface of the substrate Mg alloy. Therefore, the configuration of a Mg alloy part may be changed after the alloying process, which may not be suitable for a joint as originally designed. If an additional finishing process is needed, that will increase production complexity and cost, which may be acceptable in industry.
The third difficulty of the surface alloying process is cost, which is always a real challenge in industry. Even though the hot-dipping can remarkedly shorten the processing time and thus significantly lower the cost, sometimes a slightly increased cost or an additional step in production is not acceptable in a cost-sensitive enterprise. For example, in the auto industry, if the surface alloying is introduced into the production line for a Mg alloy part, then at least the maintenance of a molten alloy bath at the high temperature and the preheating and cooling of Mg alloy parts before and after the hot-dipping must be considered in the production line. The overall cost can be significantly higher than that incurred by addition of a top-coating in the painting line.
7 Concluding remarks and outlook
While the existing galvanic corrosion prevention methods, such as bulk alloying, surface treatment and coating, fail to meet the lightweight, strength, conductivity and some other functional requirements of Mg alloys in engineering joints, the surface alloying successfully converts the surface of a Mg alloy into a passive non-Mg metal, which reduces the galvanic corrosion risk without scarifying the essential joint performance. Experiments have proved that the surface alloying through hot-dipping is promising in theory, feasible in practice, and likely acceptable in engineering. Particularly, the hot-dipping in a molten Zn alloy bath can produce a Zn-alloyed surface layer on a Mg alloy quickly without changing the microstructure of the Mg alloy. It may be further improved for industrial applications.
Based on the effective mitigation of galvanic corrosion and inhibition of self-corrosion of Mg alloys by the surface alloying, future research may be focused on the following areas.
1) Simplification of the surface alloying process to reduce the production cost: It will be possible to include the surface alloying process in the production line of a Mg alloy component. Ideally, it can be combined into a heat-treatment step. This could be where cost-saving can kick in.
2) Deepening of the understanding of metallurgic changes in the alloyed surface layer of a Mg alloy: This is an essential foundation for precise control of the surface quality and geometric shape, which may reduce additional processing steps for the Mg alloy used in a joint.
3) Further modification of the alloyed surface of a Mg alloy for new surface properties: Since the Mg alloy surface has been changed to a different alloy, some treatments that are traditionally used for the alloy may now be applied to the surface. For example, the electroplating that is rarely used on Mg alloys may be adopted to improve the surface hardness after the Mg alloy surface has been converted to Zn.
Author contributions
G-LS: Conceptualization, Formal Analysis, Funding acquisition, Investigation, Methodology, Project administration, Resources, Supervision, Writing – original draft, Writing – review and editing. MY: Data curation, Validation, Visualization, Writing – review and editing.
Funding
The author(s) declare that financial support was received for the research and/or publication of this article. The support from the National Natural Science Foundation of China (Nos. 52250710159, 51731008, 51671163) is acknowledged.
Conflict of interest
The authors declare that the research was conducted in the absence of any commercial or financial relationships that could be construed as a potential conflict of interest.
The author(s) declared that they were an editorial board member of Frontiers, at the time of submission. This had no impact on the peer review process and the final decision.
Generative AI statement
The author(s) declare that no Generative AI was used in the creation of this manuscript.
Publisher’s note
All claims expressed in this article are solely those of the authors and do not necessarily represent those of their affiliated organizations, or those of the publisher, the editors and the reviewers. Any product that may be evaluated in this article, or claim that may be made by its manufacturer, is not guaranteed or endorsed by the publisher.
References
Andrade, C., Garces, P., and Martinez, I. (2008). Galvanic currents and corrosion rates of reinforcements measured in cells simulating different pitting areas caused by chloride attack in sodium hydroxide. Corros. Sci. 50, 2959–2964. doi:10.1016/j.corsci.2008.07.013
Annamalai, S., Periyakgoundar, S., and Gunasekaran, S. (2019). Magnesium alloys: a review of applications. Mater. Technol. 53 (6), 881–890. doi:10.17222/mit.2019.065
Antoniac, I., Miculescu, F., Cotrut, C., Ficai, A., Rau, J., Grosu, E., et al. (2020). Controlling the degradation rate of biodegradable Mg–Zn-Mn alloys for orthopedic applications by electrophoretic deposition of hydroxyapatite coating. Materials 13 (2), 263. doi:10.3390/ma13020263
ASTM G82-98 (1998). Standard Guide for Development and use of a galvanic series for predicting galvanic corrosion performance. PA, United States: ASTM 3.02, 356–361.
Atrens, A., Song, G. L., Cao, F., Shi, Z., and Bowen, P. K. (2013). Advances in Mg corrosion and research suggestions. J. Magnesium Alloys 1, 177–200. doi:10.1016/j.jma.2013.09.003
Bao, J., Sha, J., Li, L., Liu, Z., Tian, J., Liu, W., et al. (2023). Electrochemical properties and discharge performance of Mg-3Sn-xCa alloy as a novel anode for Mg-air battery. J. Alloys Compd. 934, 167849. doi:10.1016/j.jallcom.2022.167849
Benbouzid, A. Z., Gomes, M. P., Costa, I., Gharbi, O., Pébère, N., Rossi, J. L., et al. (2022). A new look on the corrosion mechanism of magnesium: an EIS investigation at different pH. Corros. Sci. 205, 110463. doi:10.1016/j.corsci.2022.110463
Candan, S., Celik, M., and Candan, E. (2016). Effectiveness of Ti-micro alloying in relation to cooling rate on corrosion of AZ91 Mg alloy. J. Alloys Compd. 672, 197–203. doi:10.1016/j.jallcom.2016.02.043
Cao, F., Song, G. L., and Atrens, A. (2016). Corrosion and passivation of magnesium alloys. Corros. Sci. 111, 835–845. doi:10.1016/j.corsci.2016.05.041
Cao, F., Xiao, B., Wang, Z., Ying, T., Zheng, D., Atrens, A., et al. (2023). A Mg alloy with no hydrogen evolution during dissolution. J. Magnesium Alloys 11, 2084–2095. doi:10.1016/j.jma.2021.08.024
Chen, X., Venezuela, J., Shi, Z., Wang, L., and Dargusch, M. (2024). Ultra-high-purity Mg-Ge anodes enable a long-lasting, high energy-density Mg-air battery. Nano Energy 122, 109269. doi:10.1016/j.nanoen.2024.109269
Cui, L. Y., Cheng, S. C., Liang, L. X., Zhang, J. C., Li, S., Wang, Z., et al. (2020). In vitro corrosion resistance of layer-by-layer assembled polyacrylic acid multilayers induced Ca-P coating on magnesium alloy AZ31. Bioact. Mater. 5, 153–163. doi:10.1016/j.bioactmat.2020.02.001
Gusieva, K., Davies, C. H. J., Scully, J. R., and Birbilis, N. (2014). Corrosion of magnesium alloys: the role of alloying. Int. Mater. Rev. 60 (3), 169–194. doi:10.1179/1743280414y.0000000046
Hirmke, J., Zhang, M. X., and StJohn, D. H. (2011). Surface alloying of AZ91E alloy by Al–Zn packed powder diffusion coating. Surf. Coatings Technol. 206, 425–433. doi:10.1016/j.surfcoat.2011.07.050
Hu, C., Le, Q., Zhou, X., Cheng, C., Guo, R., Li, X., et al. (2022). The growth and corrosion mechanism of Zn-based coating on AZ31 magnesium alloys by novel hot-dip process. Mater. Charact. 189, 111988. doi:10.1016/j.matchar.2022.111988
Huang, J., Song, G. L., Atrens, A., and Dargusch, M. (2020). What activates the Mg surface—a comparison of Mg dissolution mechanisms. J. Mater. Sci. and Technol. 57, 204–220. doi:10.1016/j.jmst.2020.03.060
Huang, J., Song, G. L., Zhu, Y., Zheng, D., and Wang, Z. (2023). The anodically polarized Mg surface products and accelerated hydrogen evolution. J. Magnesium Alloys 11, 2230–2248. doi:10.1016/j.jma.2021.05.008
Isacsson, M., Rootzen, H., and Lunder, O., Galvanically induced atmospheric corrosion on magnesium alloys: a designed experiment evaluated by extreme value statistics and conventional techniques, SAE, SP-1250, No. 970328 doi:10.4271/9703281997), pp43-55.
Jia, J., Song, G., and Atrens, A. (2006). Influence of geometry on galvanic corrosion of AZ91D coupled to steel. Corros. Sci. 48, 2133–2153. doi:10.1016/j.corsci.2005.08.013
Khajondetchairit, P., Ngamwongwan, L., Hirunsit, P., and Suthirakun, S. (2022). Synergistic effects of V and Ni catalysts on hydrogen sorption kinetics of Mg-based hydrogen storage materials: a computational study. J. Phys. Chem. C 126, 5483–5492. doi:10.1021/acs.jpcc.1c10535
Kim, J., and Pan, H. (2023). Effects of magnesium alloy corrosion on biological response – perspectives of metal-cell interaction. Prog. Mater. Sci. 133, 101039. doi:10.1016/j.pmatsci.2022.101039
Kubásek, J., Vojtěch, D., Lipov, J., and Ruml, T. (2013). Structure, mechanical properties, corrosion behavior and cytotoxicity of biodegradable Mg–X (X=Sn, Ga, In) alloys. Mater. Sci. Eng. C 33 (4), 2421–2432. doi:10.1016/j.msec.2013.02.005
Lee, J. M. (2006). Numerical analysis of galvanic corrosion of Zn/Fe interface beneath a thin electrolyte. Electrochimica Acta 51, 3256–3260. doi:10.1016/j.electacta.2005.09.026
Li, B., Sun, J., Xu, B., and Wu, G. (2022). Corrosion behavior of Mg-5.7Gd-1.9Ag Mg alloy sheet. J. Alloys Compd. 915, 165241. doi:10.1016/j.jallcom.2022.165241
Liang, J., Liu, S., Peng, Z., Li, R., and Wang, B. (2023). Galvanic corrosion behavior of AZ31 Mg alloy coupled with mild steel: effect of coatings. J. Mater. Res. Technol. 24, 7745–7755. doi:10.1016/j.jmrt.2023.05.077
Liu, M., and Song, G. L. (2013). Impurity control and corrosion resistance of magnesium-aluminum alloy. Corros. Sci. 77, 143–150. doi:10.1016/j.corsci.2013.07.037
Liu, R. L., Zeng, Z. R., Scully, J. R., Williams, G., and Birbilis, N. (2018). Simultaneously improving the corrosion resistance and strength of magnesium via low levels of Zn and Ge additions. Corros. Sci. 140, 18–29. doi:10.1016/j.corsci.2018.06.027
Luo, K., Zhang, L., Wu, G., Liu, W., and Ding, W. (2019). Effect of Y and Gd content on the microstructure and mechanical properties of Mg–Y–RE alloys. J. Magnesium Alloys 7 (2), 345–354. doi:10.1016/j.jma.2019.03.002
Ma, J., Zhang, Y., Ma, M., Qin, C., Ren, F., and Wang, G. (2020). Corrosion and discharge performance of a magnesium aluminum eutectic alloy as anode for magnesium-air batteries. Corros. Sci. 170, 108695. doi:10.1016/j.corsci.2020.108695
Makar, G. L., and Kruger, J. (1993). Corrosion of magnesium. Int. Mater. Rev. 38 (3), 138–153. doi:10.1179/095066093790326320
Marder, A. R. (2000). The metallurgy of zinc-coated steel. Prog. Mat. Sci. 45, 191–271. doi:10.1016/S0079-6425(98)00006-1
Morishita, M., Yamamoto, H., Shikada, S., Kusumoto, M., and Matsumoto, Y. (2006). Thermodynamics of the formation of magnesium–zinc intermetallic compounds in the temperature range from absolute zero to high temperature. Acta Mater. 54, 3151–3159. doi:10.1016/j.actamat.2006.03.004
Mu, S., Du, J., Jiang, H., and Li, W. (2014). Composition analysis and corrosion performance of a Mo–Ce conversion coating on AZ91 magnesium alloy. Surf. Coatings Technol. 254, 364–370. doi:10.1016/j.surfcoat.2014.06.044
Muhaffel, F., and Cimenoglu, H. (2019). Development of corrosion and wear resistant micro-arc oxidation coating on a magnesium alloy. Surf. Coatings Technol. 357, 822–832. doi:10.1016/j.surfcoat.2018.10.089
Oldham, K. B., and Mansfeld, F. (1972). Galvanic corrosion resulting from rupture of a protective metallic coating. J. Appl. Electrochem. 2, 183–191. doi:10.1007/bf02354975
Ouyang, L., Liu, F., Wang, H., Liu, J., Yang, X. S., Sun, L., et al. (2020). Magnesium-based hydrogen storage compounds: a review. J. Alloys Compd. 832, 154865. doi:10.1016/j.jallcom.2020.154865
Pillado, B., Mingo, B., Olmo, R. del, Matykina, E., Kooijman, A. M., Gonzalez−Garcia, Y., et al. (2023). LDH conversion films for active protection of AZ31 Mg alloy. J. Magnesium Alloys 11 (1), 201–216. doi:10.1016/j.jma.2022.09.014
Prasad, A., Uggowitzer, P. J., Shi, Z., and Atrens, A. (2012). Production of high purity magnesium alloys by melt purification with Zr. Adv. Eng. Mater. 14 (7), 477–490. doi:10.1002/adem.201200054
Pu, Z., Song, G. L., Yang, S., Outeiro, J. C., Dillon, O. W., Puleo, D. A., et al. (2012). Grain refined and basal textured surface produced by burnishing for improved corrosion performance of AZ31B Mg alloy. Corros. Sci. 57, 192–201. doi:10.1016/j.corsci.2011.12.018
Pu, Z., Yang, S., Song, G. L., Dillon, O. W., Puleo, D. A., and Jawahir, I. S. (2011). Ultrafine-grained surface layer on Mg–Al–Zn alloy produced by cryogenic burnishing for enhanced corrosion resistance. Scriptal Mater. 65, 520–523. doi:10.1016/j.scriptamat.2011.06.013
Saeed, F. F. M. (2024). Galvanic corrosion monitoring and analyzing system: US20080012819. US2008257729A1.
Schneider, M., Kremmer, K., Lämmel, C., Sempf, K., and Herrmann, M. (2014). Galvanic corrosion of metal/ceramic coupling. Corros. Sci. 80, 191–196. doi:10.1016/j.corsci.2013.11.024
Schuerz, S., Fleischanderl, M., Luckeneder, G. H., Preis, K., Haunschmied, T., Mori, G., et al. (2009). Corrosion behaviour of Zn-Al-Mg coated steel sheet in sodium chloride-containing environment. Corros. Sci. 51, 2355–2363. doi:10.1016/j.corsci.2009.06.019
Sekar, P., and Panigrahi, S. K. (2024). Understanding the corrosion and bio-corrosion behaviour of magnesium composites – a critical review. J. Magnesium Alloys 12, 890–939. doi:10.1016/j.jma.2024.02.014
Seré, P. R., Culcasi, J. D., Elsner, C. I., and Di Sarli, A. R. (1999). Relationship between texture and corrosion resistance in hot-dip galvanized steel sheets. Surf. Coat. Technol. 122, 143–149. doi:10.1016/S0257-8972(99)00325-4
Sha, J., Qiao, M., Bao, J., Liu, H., Yin, S., Liu, W., et al. (2022). Improving the electrochemical behaviors and discharge performance of as-rolled Mg-4Li alloys through multicomponent alloying. J. Alloys Compd. 895, 162536. doi:10.1016/j.jallcom.2021.162536
Shibli, S. M. A., Meena, B. N., and Remya, R. (2015). A review on recent approaches in the field of hot dip zinc galvanizing process. Surf. Coat. Technol. 262, 210–215. doi:10.1016/j.surfcoat.2014.12.054
Shigematsu, I., Nakamura, M., Saitou, N., and Shimojima, K. (2000). Surface treatment of AZ91D magnesium alloy by aluminum diffusion coating. J. Mater. Sci. Lett. 19, 473–475. doi:10.1023/A:1006737200466
Song, G. (2007). Control of biodegradation of biocompatible magnesium alloys. Corros. Sci. 49, 1696–1701. doi:10.1016/j.corsci.2007.01.001
Song, G., and Atrens, A. (2003). Understanding magnesium corrosion—a framework for improved alloy performance. Adv. Eng. Mat. 5, 837–858. doi:10.1002/adem.200310405
Song, G., Johannesson, B., Hapugoda, S., and StJohn, D. (2004). Galvanic corrosion of magnesium alloy AZ91D in contact with an Aluminium alloy, steel and zinc. Corros. Sci. 46, 955–977. doi:10.1016/S0010-938X(03)00190-2
Song, G. L. (2010). Potential and current distributions of one-dimensional galvanic corrosion systems. Corros. Sci. 52, 455–480. doi:10.1016/j.corsci.2009.10.003
Song, G. L., and Atrens, A. (2023). Recently deepened insights regarding Mg corrosion and advanced engineering applications of Mg alloys. J. Magnesium Alloys 11 (11), 3948–3991. doi:10.1016/j.jma.2023.08.012
Song, G. L. (2011). Prevention and utilization of Galvanic corrosion of Mg alloys, in The 8th international conference on Magnesium (ICM 8). Chongqing, China, 2nd–6th.
Song, G. L., Unocic, K. A., Harry, I. I. I. M., Cakmak, E., Brady, M. P., Gannon, P. E., et al. (2016). The corrosion and passivity of sputtered Mg–Ti alloys. Corros. Sci. 104, 36–46. doi:10.1016/j.corsci.2015.11.028
Song, G. L., and Yao, X. (2025). Electro-isolation of galvanic current. Electrochem. Commun. 170, 107850. doi:10.1016/j.elecom.2024.107850
Song, J., She, J., Chen, D., and Pan, F. (2020). Latest research advances on magnesium and magnesium alloys worldwide. J. Magnesium Alloys 8 (1), 1–41. doi:10.1016/j.jma.2020.02.003
Staišiūnas, L., Miečinskas, P., Leinartas, K., Selskis, A., Grigucevičienė, A., and Juzeliūnas, E. (2014). Sputter-deposited Mg–Al–Zn–Cr alloys – electrochemical characterization of single films and multilayer protection of AZ31 magnesium alloy. Corros. Sci. 80, 487–493. doi:10.1016/j.corsci.2013.11.061
Tavakkolizadeh, M., and Saadatmanesh, H. (2001). Galvanic corrosion of carbon and steel in aggressive environments. J. Compos. Constr. 5, 200–210. doi:10.1061/(asce)1090-0268(2001)5:3(200)
Tsai, W. T., and Chen, J. R. (2007). Galvanic corrosion between the constituent phases in duplex stainless steel. Corros. Sci. 49, 3659–3668. doi:10.1016/j.corsci.2007.03.035
Verbrugge, M. (2006). Galvanic corrosion over a semi-infinite, planar surface. Corros. Sci. 48, 3489–3512. doi:10.1016/j.corsci.2006.02.004
Wagner, C. (1951). Theoretical analysis of the current density distribution in electrolytic cells. J. Electrochem. Soc. 98, 116. doi:10.1149/1.2778113
Wu, P. P., Song, G. L., Zhu, Y. X., Deng, Y. J., and Zheng, D. J. (2022). An intelligent Mg anode for protection of the concrete-covered steel tubing in carbon capture and storage. Compos. Part B 243, 110165. doi:10.1016/j.compositesb.2022.110165
Wu, P. P., Song, G. L., Zhu, Y. X., Yan, L., Feng, Z. L., and Zheng, D. J. (2021). Improvement of intelligent corrosivity-detection and corrosion-protection for reinforcing steel. Corros. Sci. 184, 109396. doi:10.1016/j.corsci.2021.109396
Xie, J., Zhang, J., Zhang, Z., Yu, Z., Xu, Z., Wang, R., et al. (2023). Corrosion mechanism of Mg alloys involving elongated long-period stacking ordered phase and intragranular lamellar structure. J. Mater. Sci. and Technol. 151, 190–203. doi:10.1016/j.jmst.2023.01.005
Yadava, A. P., Yadav, A. P., Katayama, H., Noda, K., Masuda, H., Nishikata, A., et al. (2007). Surface potential distribution over a zinc/steel galvanic couple corroding under thin layer of electrolyte. Electrochimica Acta 52, 3121–3129. doi:10.1016/j.electacta.2006.09.061
Yan, L., Song, G. L., and Zheng, D. (2019). Magnesium alloy anode as a smart corrosivity detector and intelligent sacrificial anode protector for reinforced concrete. Corros. Sci. 155, 13–28. doi:10.1016/j.corsci.2019.04.027
Yang, M., and Song, G. L. (2019). Surface alloying coating for a Mg alloy against galvanic corrosion .
Yao, C., Lv, H., Zhu, T., Zheng, W., Yuan, X., and Gao, W. (2016). Effect of Mg content on microstructure and corrosion behavior of hot dipped Zn–Al–Mg coatings. J. Alloys Compd. 670, 239–248. doi:10.1016/j.jallcom.2016.02.026
Zeng, R., Cui, L., and Ke, W. (2018). Biomedical magnesium alloys: composition, microstructure and corrosion. Acta Metall. Sin. 54 (9), 1215–1235. doi:10.11900/0412.1961.2018.00032
Zeng, R. C., Sun, L., Zheng, Y. F., Cui, H. Z., and Han, E. H. (2014). Corrosion and characterisation of dual phase Mg–Li–Ca alloy in Hank’s solution: the influence of microstructural features. Corros. Sci. 79, 69–82. doi:10.1016/j.corsci.2013.10.028
Zhang, B., Yao, R., Li, L., Li, M., Yang, L., Liang, Z., et al. (2019). Bionic tea stain–like, all-nanoparticle coating for biocompatible corrosion protection. Adv. Mater. Interfaces 6 (20), 1900899. doi:10.1002/admi.201900899
Zhang, C., Zhang, J., Zhang, S., and Wang, Z. (2018). Comparison of calcium phosphate coatings on AZ31 and fluoride-treated AZ31 alloy prepared by hydrothermal method and their electrochemical corrosion behaviour. Mater. Chem. Phys. 220, 395–401. doi:10.1016/j.matchemphys.2018.08.085
Zhang, J., Zeng, R., and Chen, J. (2008). Research and progress of galvanic corrosion of magnesium alloys. Mater. Rev. 22 (1), 107–117.
Zhang, M. X., and Kelly, P. M. (2002). Surface alloying of AZ91D alloy by diffusion coating. J. Mater. Res. 17, 2477–2479. doi:10.1557/JMR.2002.0360
Zhang, Z., Xie, J., Zhang, J., Liu, S., Wu, R., and Zhang, X. (2023). Simultaneously improving yield strength and formability potential of Mg alloy via introducing nano precipitates and texture-weakened heterogeneous grains. J. Mater. Res. Technol. 24, 5486–5500. doi:10.1016/j.jmrt.2023.04.171
Zhu, L., Liu, H., Li, W., and Song, G. (2005). Zinc alloyed coating on AZ 91 D magnesium alloys. J. Beijing Univ. Aeronautics Astronautics 31, 8–12. (in Chinese).
Zhu, L., and Song, G. (2006). Improved corrosion resistance of AZ91D magnesium alloy by an aluminium-alloyed coating. Surf. Coatings Technol. 200, 2834–2840. doi:10.1016/j.surfcoat.2004.11.042
Zhu, Y. X., Song, G. L., Wu, P. P., Huang, J. F., and Zheng, D. J. (2021b). A protective superhydrophobic Mg-Zn-Al LDH film on surface-alloyed magnesium. J. Alloys Compd. 855, 157550. doi:10.1016/j.jallcom.2020.157550
Keywords: mg, surface, alloying, galvanic corrosion, coating
Citation: Song G-L and Yang M (2025) Strategy of galvanic corrosion mitigation for Mg alloys. Front. Mater. 12:1582380. doi: 10.3389/fmats.2025.1582380
Received: 24 February 2025; Accepted: 31 March 2025;
Published: 28 April 2025.
Edited by:
Nicola Maria Pugno, University of Trento, ItalyReviewed by:
Weichen Xu, Chinese Academy of Sciences (CAS), ChinaCopyright © 2025 Song and Yang. This is an open-access article distributed under the terms of the Creative Commons Attribution License (CC BY). The use, distribution or reproduction in other forums is permitted, provided the original author(s) and the copyright owner(s) are credited and that the original publication in this journal is cited, in accordance with accepted academic practice. No use, distribution or reproduction is permitted which does not comply with these terms.
*Correspondence: Guang-Ling Song, Z3VhbmdsaW5nLnNvbmdAaG90bWFpbC5jb20=, c29uZ2dsQHN1c3RlY2guZWR1LmNu