- 1Xi’an Modern Control Technology Research Institute, Xian, China
- 2School of Materials and Chemical Engineering, Xi’an Technological University, Xian, China
With the miniaturization and integration of microelectronic components, the demand for high-thermal-conductivity electronic packaging materials has grown substantially. Diamond/copper (Dia/Cu) composites have become a focus of research due to their ultra-high thermal conductivity and low coefficient of thermal expansion. However, poor interfacial bonding and high interfacial thermal resistance between diamond and copper limit their practical performance. This paper reviews strategies to enhance interfacial bonding, including diamond surface metallization (e.g., electroless plating, magnetron sputtering, molten salt method, vacuum electroplating, and embedding) and copper matrix alloying (e.g., gas atomization and alloy smelting), and evaluates their effects on thermal transport properties. Additionally, the influence of preparation processes—such as vacuum hot-pressing sintering, high-temperature high-pressure sintering, spark plasma sintering, and melt infiltration on the microstructure and thermal conductivity of composites are discussed. Key factors including diamond surface roughness, particle size, volume fraction, and sintering conditions (e.g., temperature, pressure, and dwell time) are analyzed. Experimental and computational studies demonstrate that systematic optimization of these factors enhances the thermal conductivity of Dia/Cu composites, providing critical insights for developing next-generation high-performance electronic packaging materials.
1 Introduction
The relentless advancement of high-power density and miniaturization in modern microelectronics has positioned thermal management as the paramount challenge for ensuring device reliability (Wu et al., 2024; Moore and Shi, 2014; Jiang et al., 2015). To mitigate this thermal bottleneck, substantial research efforts have been directed toward developing advanced electronic packaging materials with superior thermal transport capabilities. Contemporary packaging materials are systematically classified into three distinct categories based on composition: ceramic-based, polymer-based, and metal-based systems. While ceramic (AlN: 170–320 W m-1·K−1) and polymer (epoxy: 0.2 W m-1·K−1) systems face inherent thermal limitations, copper matrix composites—particularly diamond-reinforced variants—offer superior solutions (Li et al., 2022a; Gu et al., 2016; Dai et al., 2020).
Diamond/copper composites integrate the extreme anisotropic thermal conductivity (1,200–2,000 W m-1·K−1) and ultralow CTE (≈1 × 10−6 K−1) with copper’s processability (400 W m-1·K−1) (Ward et al., 2009; Dai et al., 2020). However, interfacial thermal resistance (TBR >10−7 m2 K·W−1) caused by weak metal-ceramic bonding degrades performance via phonon scattering. Current efforts focus on interfacial engineering strategies, including diamond surface metallization and matrix alloying, to minimize TBR and optimize thermal transport (Zhang et al., 2018; Dai et al., 2020).
The relentless advancement of high-power-density microelectronics demands packaging materials capable of dissipating heat fluxes exceeding 1 kW/cm2 to ensure device reliability. While ceramics (AlN: 170–320 W m-1·K−1) and polymers (epoxy: <0.2 W m-1·K−1) systems are thermally inadequate, diamond/copper (Dia/Cu) composites offer unmatched potential by synergizing diamond’s anisotropic thermal conductivity (1,200–2,000 W m-1·K−1) and ultralow CTE (≈1 × 10-6 K−1) with copper’s processability (400 W m-1·K−1; Cui et al., 2024; Dai et al., 2020). However, interfacial thermal resistance (TBR >10−7 m2 K·W−1) arising from weak diamond-Cu bonding remains a critical bottleneck, degrading thermal transport via phonon scattering. Recent studies emphasize interfacial engineering—such as surface metallization (e.g., W, TiC coatings) and matrix alloying (e.g., Zr, B)—to mitigate TBR. Yet, the scalable fabrication of defect-free carbide layers and precise control of interfacial crystallography for phonon matching remain unresolved (Li R. et al., 2022). This work addresses these gaps by systematically optimizing metallization parameters and alloy compositions to achieve TBR <5 × 10-8 m2 K·W−1, bridging the divide between lab-scale innovation and industrial viability.
2 Diamond surface metallization
Diamond surface metallization involves depositing carbide-forming elements (e.g., W, Mo, Cr, Ti) through various coating techniques to create a continuous carbide interlayer (Zhang et al., 2023). In unmodified diamond/copper composites, pristine diamond surfaces exhibit poor interfacial adhesion The copper matrix forms weakly bonded interfaces, exhibiting excessive thermal boundary resistance (TBR > 10−7 m2 K·W−1) that severely degrade thermal conductivity (typically <400 W m-1·K−1).The metallized carbide layer addresses these limitations through three mechanisms: (i) enhancing interfacial bonding strength via chemical interactions, (ii) reducing porosity-induced thermal resistance through conformal coating, and (iii) protecting diamond from graphitization during processing. Established metallization methods include electroless plating, magnetron sputtering, molten salt synthesis, vacuum electroplating, and embedded powder sintering (Zhou et al., 2023).
2.1 Electroless Plating (ELP)
Electroless plating, also known as chemical plating or autocatalytic plating, is a metal deposition method that reduces metal ions in a plating solution to metallic form and deposits them onto substrate surfaces through the action of appropriate reducing agents, without the application of external electrical current. Typically, the surface of the substrate to be plated requires pretreatment, particularly for non-conductive and hydrophobic materials such as diamond. Li et al. (2022b) formed a thin TiC coating on diamonds using molten salt with NaCl-KCl-NaF, then applied electroless plating of Cu. The hot-pressing diamond/Cu composite with 60 vol% modified diamonds exhibits the best thermal conductivity of 495.5 W·m−1 K−1. However, ELP has limited industrial adoption due to three critical drawbacks. First, ELP relies on physical metal attachment rather than atomic diffusion bonding, leading to poor coating-substrate adhesion (interfacial strength <50 MPa). Second, the deposited metallic layer may catalyze the graphitization of diamond at elevated temperatures, significantly degrading its intrinsic thermal conductivity. Third, the non-uniform nucleation and growth characteristics of electroless plating often lead to incomplete surface coverage, particularly on geometrically complex substrates (Liu L.-Y. et al., 2023).
2.2 Magnetron sputtering
Magnetron sputtering utilizes an electric field to generate a plasma discharge in a low-pressure argon environment. Electrons accelerated by the field ionize argon atoms, producing argon ions and secondary electrons. The ions are then accelerated toward the cathode (target material), where their bombardment sputters target atoms via momentum transfer, forming the coating layer. The sputtered atoms and secondary electrons migrate to deposit on diamond surfaces, forming uniform coatings. Sang et al. (2021) employed this technique to deposit tungsten coatings (45–300 nm thickness) on diamond particles, followed by pressureless infiltration of liquid copper into the coated diamond bed to fabricate diamond/copper composites. Characterization revealed that tungsten coatings exceeding 93 nm thickness demonstrated optimal effectiveness in enhancing composite densification and reducing interfacial thermal resistance between diamond reinforcements and the copper matrix (Zhao et al., 2021).
2.3 Molten salt coating (MSC)
Molten salt coating involves a diffusion-driven metallurgical reaction where modified metal powders are dissolved in chloride-based salt baths. At elevated temperatures (typically 600°C–900°C), diamond particles react with molten metallic species over 1–2 h to form chemically bonded carbide interfacial layers. Li et al. (2022b) systematically investigated chromium carbide formation on diamond surfaces by introducing NaF into a ternary NaCl-KCl-LiCl molten salt system within 600°C–750°C. Their experimental investigations demonstrated that NaF served as an effective activator, enabling the formation of Cr7C3 coatings at temperatures below 697°C through enhanced ion mobility. In a separate study, Kang et al. (2013b) synthesized molybdenum carbide (Mo2C)-coated diamond particles via MSC, followed by vacuum pressure infiltration to fabricate copper-diamond composites. Microstructural characterization revealed that the Mo2C interlayer significantly improved wettability between diamond reinforcements and copper matrix. The composite containing 65 vol% Mo2C -coated diamond exhibited exceptional thermal conductivity of 608 W m-1·K−1, representing a 142% enhancement compared to uncoated diamond counterparts.
2.4 Vacuum micro-evaporation plating (VMEP)
Vacuum micro-evaporation plating (VMEP) enables low-temperature (<500°C) synthesis of interfacial compounds through activated metal-diamond reactions under vacuum, offering cost-effective processing with minimal structural damage. Wu et al. demonstrated that VMEP-processed Cu/diamond composites achieve thermal conductivities up to 846.5 W m-1·K−1 when employing large diamond particles (400 μm diameter) (Wu et al., 2019). This enhancement arises from optimized interfacial bonding that facilitates coherent phonon transport, with conductivity scaling proportionally to particle size due to reduced interfacial defect density. However, its application in precision thermal management components is constrained by high equipment costs, limited geometric adaptability, and diamond degradation risks under prolonged high-pressure sintering. Addressing these limitations requires prioritized development of low-temperature activating agents and pulsed pressure strategies to optimize interfacial engineering while mitigating mechanical/thermal damage.
2.5 Powder encapsulation and sintering (PES)
PES employs solid-state carbon-metal interdiffusion at 900°C–1,200°C to create adherent carbide interfacial layers. To further optimize interfacial properties, Li et al. achieved 670 W m-1·K−1 in Cu-WC composites through W2C/WC graded interfaces formed at 1,050°C (Li et al., 2015). Similarly, Shen et al. enhanced this to 726 W m-1·K−1 via MoC interlayers using pressure-assisted melt infiltration (Shen et al., 2012). The nanostructured carbide interfacial layers in these studies effectively suppress interfacial phonon scattering by establishing coherent crystallographic continuity with the matrix phase. However, PES faces three limitations: (1) Diamond graphitization (>900°C) degrading thermal properties; (2) Thermal stress-induced delamination (ΔT >800°C) in large components; (3) Stoichiometric heterogeneity in carbide phases (e.g., Cr3C2/Cr7C3 mixtures from EBSD). Mitigation strategies include thermal gradient optimization and precursor particle size control for scalability.
3 Matrix alloying
Matrix alloying represents a widely implemented interface engineering strategy for copper-based diamond composites. This non-destructive processing approach involves pre-introduction of strategic alloying elements (e.g., Zr, B, Cr) into the copper matrix prior to composite fabrication. During thermal processing, these active elements diffuse toward diamond-copper interfaces, reacting with surface carbon atoms to form epitaxial carbide transition layers. Such interfacial engineering simultaneously optimizes phonon transport pathways through crystallographic matching and enhances interfacial bonding strength, ultimately elevating the composite’s thermal conductivity (Liu et al., 2020).
3.1 Gas atomization
Gas atomization enables the synthesis of Cu-Zr alloy powders (0.25–1.0 wt% Zr) through high-velocity inert gas fragmentation of molten metal streams (Zhu et al., 2022). Chu et al. demonstrated that hot-press sintering of gas-atomized Cu-Zr with diamond yields composites where Zr content critically governs interfacial carbide evolution (Chu et al., 2013). At 0.5 wt% Zr, discontinuous ZrCx nanostructures (two to five nm thick) form at diamond-Cu interfaces, optimizing phonon transmission to achieve 615 W m-1·K−1 thermal conductivity. Excessive Zr (1.0 wt%) promotes continuous ZrCx interphases (15–20 nm thick), introducing phonon scattering at ZrCx/Cu boundaries that elevate interfacial thermal resistance (Chu et al., 2013). This nanoscale control of carbide discontinuity highlights the precision required in alloy design for thermal management applications.
3.2 Alloy smelting process
Alloy smelting enables precise interfacial engineering through thermochemical synthesis of modified Cu matrices. Weber et al. demonstrated Cr-B co-alloying via pressurized melt infiltration creates metastable CrBx interfacial phases, achieving 600 W m-1·K−1 at 60 vol% diamond loading (Weber and Tavangar, 2007). Bai et al. further optimized this strategy, showing 0.3 wt% B addition precipitates discrete CrB2 nanostructures (three to eight nm) at interfaces, yielding 868 W m-1·K−1 – a 44.7% enhancement over unmodified systems (Bai et al., 2018).
Critical analysis reveals carbide interlayers require dual optimization: (1) intrinsic thermal conductivity >400 W m-1·K−1 and (2) thickness control (50–100 nm). Sub-30 nm layers inadequately relieve lattice mismatch stresses, while >150 nm interphases induce phonon scattering at grain boundaries. Ciupiński et al. validated this through Cu-0.65Cr composites with 81 ± 5 nm Cr3C2 layers, achieving 687 W m-1·K−1 (92% of Hashin-Shtrikman theoretical limit) via gradient thermal protocols (Ciupiński et al., 2017). These findings establish atomic-scale interface tailoring as paramount for maximizing thermal transport in electronic packaging materials (Zhong et al., 2024).
4 Optimization of fabrication processes for diamond/copper composites
The selection of fabrication methodology critically governs the microstructure development, relative density (>98% theoretical), and interfacial integrity of diamond/copper composites, making process optimization essential for achieving superior thermal conductivity. Established consolidation techniques include vacuum hot-press sintering, high-pressure high-temperature (HPHT) sintering, spark plasma sintering (SPS), and melt infiltration, each with distinct interfacial engineering mechanisms. A typical sketch of the preparation process of composites is shown in Figure 1.
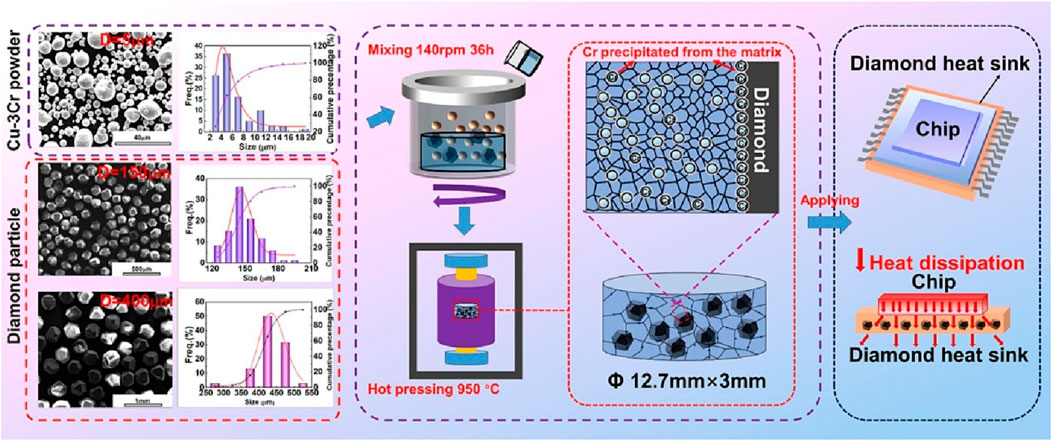
Figure 1. The sketch of the preparation process and the application of composites (Zhang and Lei, 2024).
4.1 Vacuum hot-press sintering
Vacuum hot-press sintering integrates thermal activation and uniaxial pressure (typically 20–100 MPa) within vacuum chambers (<10−3Pa) to consolidate diamond-copper powder mixtures. The applied pressure facilitates particle rearrangement and plastic deformation, enhancing interfacial bonding through solid-state diffusion. This synergistic effect enables composites with near-theoretical density and optimized thermal pathways (Tan et al., 2020; Liu X. et al., 2023; Zhang et al., 2024).
Shen et al. (2010) fabricated diamond/Cu-5wt%Si composites via low-pressure sintering (25.5 MPa) at 1,000°C for 10 min, achieving a thermal conductivity of 455 W m-1·K−1. Advanced interfacial engineering was demonstrated by Zhang et al. (2015), who employed tungsten-coated diamond particles with electroless copper overlayers. Subsequent consolidation at 900°C under 80 MPa for 30 min yielded composites with 721 W m-1·K−1 thermal conductivity, attributable to the graded W-Cu interfacial architecture.
4.2 High-temperature high-pressure (HPHT) sintering
HPHT sintering leverages extreme conditions (three to six GPa, 1,000°C–1,300°C) to induce atomic-scale dissolution-reprecipitation mechanisms between diamond and copper matrix (Hayat et al., 2022). This process achieves metastable phase equilibria through: (1)Diamond surface graphitization inhibition via pressure-stabilized sp3bonding; (2)Liquid-phase enhanced copper diffusion along diamond grain boundaries; (3)Stress-assisted recrystallization for void elimination (Chen et al., 2013).
Yoshida and Morigami (2004) synthesized 70 vol% diamond/Cu composites using 90–110 μm diamonds under 4.5 GPa at 1,200°C, achieving a record thermal conductivity of 742 W m-1·K−1. While HPHT enables ultra-dense composites (>99.5% density), its practical implementation faces challenges including technically demanding equipment specifications (multi-anvil hydraulic systems) and prohibitive operational costs for large-scale production.
4.3 Spark plasma sintering (SPS)
SPS employs pulsed direct currents (1,000–5000 A) and uniaxial pressures (30–100 MPa) to achieve rapid densification (≤500°C/min) via joule heating and electron bombardment-activated surface diffusion (Liu et al., 2019). While enabling near-full densification, SPS-fabricated composites exhibit inherent constraints: interfacial porosity (5–15 vol%) and limited component dimensions (<50 mm diameter), restricting thermal conductivity optimization. Liu et al. demonstrated SPS-processed 50 vol% diamond/Cu composites achieve exceptional high-temperature tribological performance (friction coefficient: 0.133; wear rate: 2.1–2.7 × 10−6 mm3/Nm at 500°C), attributed to in situ formation of CuO lubricants from oxidized debris. Pan et al. enhanced thermal transport by integrating ZrC/Zr bilayer coatings via SPS, attaining 609 W m-1·K−1 at 60 vol% loading through controlled zirconium-carbon reactions (Pan et al., 2019). These advances highlight SPS’s dual capability in tailoring interfacial chemistry and rapid prototyping, though scalability remains hindered by residual porosity and dimensional limitations (TAO et al., 2014).
4.4 Melt infiltration technique
Beyond the aforementioned consolidation techniques, emerging methodologies such as chemical vapor deposition (CVD) and cold-press sintering demonstrate niche potential for fabricating diamond/copper composites. To achieve next-generation thermal management materials (κ > 900 W m-1·K−1), researchers should focus on synergistic optimization.Melt infiltration leverages capillary forces and external pressure (1–15 MPa) to drive molten metal through diamond beds, with infiltration kinetics governed by pressure-particle size synergies. Increased pressure enhances flow velocity, while larger diamond particles (>500 μm) reduce capillary resistance through widened interstices, promoting coherent Cu-diamond interfaces (Dai et al., 2020). Kang et al. achieved 680.3 W m-1·K−1 in Cu-B/diamond composites via 10 MPa infiltration, where continuous B4C layers optimized interfacial bonding (Kang et al., 2013a). Bai et al. elevated this to 868 W m-1·K−1 through B-alloyed matrices, while Dai et al. (Bai et al., 2018) demonstrated record 930 W m-1·K−1 conductivity in Cu-0.5Zr composites via ZrC-induced acoustic impedance matching (Dai et al., 2020). Acoustic impedance matching uses intermediate layers (e.g., ZrC) to reduce phonon reflection by bridging impedance gaps between matrix and reinforcement, enhancing thermal conductivity. These breakthroughs underscore the criticality of carbide-mediated interface engineering in balancing infiltration dynamics and phonon transport efficiency. Future advances demand synergistic optimization of alloy chemistry and pressure-temperature protocols to surpass 900 W m-1·K−1 thresholds for next-gen thermal management.
5 Critical performance Determinants
5.1 Diamond surface roughness
Compared to smooth diamond surfaces, roughened diamond surfaces increase the contact area with modifying elements, thereby promoting carbide nucleation and enhancing the thermal performance of diamond/copper composites. Merabia and Termentzidis (2014) employed molecular dynamics simulations to study interfacial roughness effects on thermal boundary conductance (TBC) in solid-solid systems (Merabia and Termentzidis, 2014). They found TBC remains constant at low roughness (approaching flat interface values), but exceeds planar interface levels under significant roughness, demonstrating boundary-dominated heat transfer mechanisms. Wu et al. (2019) demonstrated a thermal conductivity improvement of 45% (685 W m-1·K−1) in modified diamond/copper composites by surface roughening via molten potassium nitrate treatment. This enhancement was attributed to optimized interfacial interactions resulting from the increased surface roughness.
5.2 Diamond particle size and volume fraction
The thermal conductivity of diamond/copper composites is governed by percolative networks formed by diamond particles, with their size and volume fraction critically dictating phonon transport efficiency. At low volumetric loadings (<35 vol%), uniform dispersion creates excessive interparticle distances that impede phonon-mediated heat transfer (Monje et al., 2014). Increasing diamond content to 60–70 vol% establishes low-thermal-resistance percolation pathways, yet exceeding 70 vol% induces defect proliferation through incomplete copper infiltration, generating interfacial voids and cracks that dominate phonon scattering. This dual-phase behavior results in a characteristic thermal conductivity maximum at critical diamond loading. Surface modification (e.g., carbide coatings) elevates this threshold by enhancing interfacial phonon coupling, as demonstrated by Zhu et al. where optimized composites achieved 602 W/(m·K) at 35 vol% loading through tailored carbide interfaces (Zhu et al., 2020). Particle size (>400 μm) synergistically enhances this effect by reducing interfacial scattering sites per unit volume. These findings underscore the necessity of balancing percolation physics with defect minimization for maximizing thermal performance (Feng et al., 2010).
5.3 Sintering parameters
Sintering process parameters significantly influence the thermal conductivity of diamond/copper composites by modulating both intrinsic material properties and interfacial interactions. The sintering temperature directly governs the interdiffusion behavior between diamond and copper matrix, as well as the inherent characteristics of both phases (Kang et al., 2013b). Excessive temperatures (>1,050°C) induce diamond graphitization, whereas optimized interfacial reactions can be achieved through controlled sintering durations (e.g., 9 min), as demonstrated by Xia et al. Furthermore, applied pressure emerges as a critical factor in thermal transport optimization. Enhanced pressure promotes densification through improved diamond-copper consolidation, thereby reducing interfacial defects and elevating thermal conductivity (Lei et al., 2020; Wang et al., 2020). Ciupiński et al. (2017) achieved a maximum thermal conductivity of 687 W m-1·K−1 in chromium-coated diamond/copper composites by optimizing pulsed plasma sintering parameters, specifically employing a sintering temperature of 850°C with a 10-min holding time.
6 Discussion
6.1 Interfacial engineering synergy
Surface metallization techniques (e.g., TiC/WC interlayers via magnetron sputtering) establish chemically bonded interfaces that simultaneously enhance wettability and suppress thermal boundary resistance (TBR <10−8 m2 K·W−1). These layers mitigate phonon scattering by reducing interfacial defects, as evidenced by the 846.5 W m-1·K−1 achieved in vacuum-metallized composites. Matrix alloying complements this approach: Zr doping (0.5 wt%) generates discontinuous ZrC nanostructures (two to five nm) that enable phonon impedance matching, pushing thermal conductivity to 930 W m-1·K−1. Crucially, the synergy between carbide crystallography (e.g., Cr7C3 vs. Cr3C2) and sintering dynamics (e.g., pressure-assisted recrystallization) dictates interfacial coherence, with graded architectures (W2C/WC) demonstrating superior phonon transmission.
6.2 Process-defect interplay
While high-pressure sintering and melt infiltration achieve dense composites (>740 W m-1·K−1), their scalability is hampered by energy-intensive protocols. Spark plasma sintering (SPS) offers rapid densification but introduces interfacial porosity (5–15 vol%), underscoring the trade-off between process efficiency and microstructural perfection. The thermal transport hierarchy—dictated by diamond size (>400 μm), loading (60–70 vol%), and surface roughness—reveals a percolation threshold: exceeding 70 vol% disrupts copper infiltration, while suboptimal sintering temperatures (>1,050°C) trigger graphitization-dominated failure. These phenomena highlight the necessity of multiscale parameter coupling, where atomic-scale interface design must align with macroscopic process constraints.
Despite progress, critical challenges persist: (1) Multi-property synergy—mechanical robustness must be reconciled with ultrahigh conductivity; (2) Cost-effective fabrication—emerging techniques like additive manufacturing require development to circumvent high-energy processes; (3) Atomic-level interface engineering—crystallographic orientation effects of carbide layers on phonon scattering demand fundamental exploration (4) Industrial translation—metallization protocols (e.g., molten salt, vacuum plating); necessitate parameter standardization for large-area production. Current limitations in diamond/Cu composites include inadequate interface phonon control, high-energy fabrication dependence, and non-standardized industrial protocols. Future directions demand: ML-guided carbide gradients with topological diamond architectures, laser-assisted cold spray additive manufacturing, and plasma-enhanced infiltration for defect-free interfaces. Quantum-enabled thermal mapping via NV centers and digital twin-assisted metallization could establish ZT-like standards, bridging atomic engineering to scalable production.
7 Conclusion
This review highlights interfacial engineering and process optimization as critical enablers for diamond/copper composites in high-power electronics. Surface metallization and matrix alloying synergistically enhance bonding and reduce thermal resistance via carbide layers and phonon transport optimization. While HPHT sintering and melt infiltration yield high-density composites, scalability and cost barriers remain. Precise control of diamond morphology, size (>400 μm), volume fraction (60–70 vol%), and sintering parameters is essential to maximize thermal conductivity (>900 W/(m·K)) and minimize defects. Future work must prioritize hybrid strategies (e.g., surface roughening with multilayered coatings), scalable manufacturing, and interfacial phonon dynamics to meet next-generation microelectronics demands. The synergistic integration of interfacial phonon engineering with hierarchical multiscale architectures (nanoscale interface design to macroscale structural optimization) represents the fundamental strategy to overcome thermal transport barriers exceeding 1000 W/(m·K) in next-generation thermal management composites.
Author contributions
YX: Writing–original draft. RL: Writing–original draft. Yongru Deng: Investigation, Supervision, Writing–review and editing. ZZ: Writing–review and editing. JC: Investigation, Writing–review and editing. AM: Writing–review and editing. Ruilong Wen: Writing–review and editing.
Funding
The author(s) declare that financial support was received for the research and/or publication of this article. This work was also supported by the Scientific Research Program of Shaanxi Provincial Science and Technology Department (2024JC-YBQN-0592).
Acknowledgments
The authors thank Xi’an Technological University for the support of this work.
Conflict of interest
The authors declare that the research was conducted in the absence of any commercial or financial relationships that could be construed as a potential conflict of interest.
Generative AI statement
The author(s) declare that no Generative AI was used in the creation of this manuscript.
Publisher’s note
All claims expressed in this article are solely those of the authors and do not necessarily represent those of their affiliated organizations, or those of the publisher, the editors and the reviewers. Any product that may be evaluated in this article, or claim that may be made by its manufacturer, is not guaranteed or endorsed by the publisher.
References
Bai, G., Li, N., Wang, X., Wang, J., Kim, M. J., and Zhang, H. (2018). High thermal conductivity of Cu-B/diamond composites prepared by gas pressure infiltration. J. Alloys Compd. 735, 1648–1653. doi:10.1016/j.jallcom.2017.11.273
Chen, H., Jia, C., and Li, S. (2013). Effect of sintering parameters on the microstructure and thermal conductivity of diamond/Cu composites prepared by high pressure and high temperature infiltration. Int. J. Minerals, Metallurgy, Mater. 20, 180–186. doi:10.1007/s12613-013-0711-x
Chu, K., Jia, C., Guo, H., and Li, W. (2013). On the thermal conductivity of Cu–Zr/diamond composites. Mater Des. 45, 36–42. doi:10.1016/j.matdes.2012.09.006
Ciupiński, Ł., Kruszewski, M. J., Grzonka, J., Chmielewski, M., Zielińsk, R., Moszczyńska, D., et al. (2017). Design of interfacial Cr3C2 carbide layer via optimization of sintering parameters used to fabricate copper/diamond composites for thermal management applications. Mater Des. 120, 170–185. doi:10.1016/j.matdes.2017.02.005
Cui, S., Sun, F., Wang, D., Zhang, X., Zhang, H., and Feng, Y. (2024). Enhancing interfacial heat conduction in diamond-reinforced copper composites with boron carbide interlayers for thermal management. Compos B Eng. 287, 111871. doi:10.1016/j.compositesb.2024.111871
Dai, S., Li, J., and Lu, N. (2020). Research progress of diamond/copper composites with high thermal conductivity. Diam. Relat. Mater 108, 107993. doi:10.1016/j.diamond.2020.107993
Feng, H., Yu, J. K., and Tan, W. (2010). Microstructure and thermal properties of diamond/aluminum composites with TiC coating on diamond particles. Mater Chem. Phys. 124, 851–855. doi:10.1016/j.matchemphys.2010.08.003
Gu, J., Yang, X., Lv, Z., Li, N., Liang, C., and Zhang, Q. (2016). Functionalized graphite nanoplatelets/epoxy resin nanocomposites with high thermal conductivity. Int. J. Heat Mass. Transf. 92, 15–22. doi:10.1016/j.ijheatmasstransfer.2015.08.081
Hayat, M. D., Singh, H., Karumbaiah, K. M., Xu, Y., Wang, X.-G., and Cao, P. (2022). Enhanced interfacial bonding in copper/diamond composites via deposition of nano-copper on diamond particles. JOM 74, 949–953. doi:10.1007/s11837-021-05054-6
Jiang, L., Wang, P., Xiu, Z., Chen, G., Lin, X., Dai, C., et al. (2015). Interfacial characteristics of diamond/aluminum composites with high thermal conductivity fabricated by squeeze-casting method. Mater Charact. 106, 346–351. doi:10.1016/j.matchar.2015.06.023
Kang, Q., He, X., Ren, S., Zhang, L., Wu, M., Guo, C., et al. (2013a). Preparation of copper–diamond composites with chromium carbide coatings on diamond particles for heat sink applications. Appl. Therm. Eng. 60, 423–429. doi:10.1016/j.applthermaleng.2013.05.038
Kang, Q., He, X., Ren, S., Zhang, L., Wu, M., Liu, T., et al. (2013b). Preparation of high thermal conductivity copper–diamond composites using molybdenum carbide-coated diamond particles. J. Mater Sci. 48, 6133–6140. doi:10.1007/s10853-013-7409-3
Lei, L., Bolzoni, L., and Yang, F. (2020). High thermal conductivity and strong interface bonding of a hot-forged Cu/Ti-coated-diamond composite. Carbon N. Y. 168, 553–563. doi:10.1016/j.carbon.2020.07.001
Li, H., Xie, Y., Wang, H., Qian, Z., Cao, P., and Zhang, W. (2022a). Facile formation of a thin chromium carbide coating on diamond particles via quaternary molten salt. J. Alloys Compd. 928, 167142. doi:10.1016/j.jallcom.2022.167142
Li, H., Xie, Y., Zhang, L., and Wang, H. (2022b). Thermal properties of diamond/Cu composites enhanced by TiC plating with molten salts containing fluoride and electroless-plated Cu on diamond particles. Diam. Relat. Mater 129, 109337. doi:10.1016/j.diamond.2022.109337
Li, J., Wang, X., Qiao, Y., Zhang, Y., He, Z., and Zhang, H. (2015). High thermal conductivity through interfacial layer optimization in diamond particles dispersed Zr-alloyed Cu matrix composites. Scr Mater 109, 72–75. doi:10.1016/j.scriptamat.2015.07.022
Li, R., Yang, X., Li, J., Shen, Y., Zhang, L., Lu, R., et al. (2022c). Review on polymer composites with high thermal conductivity and low dielectric properties for electronic packaging. Mater. Today Phys. 22, 100594. doi:10.1016/j.mtphys.2021.100594
Liu, D., Tian, H., Lin, L., and Shi, W. (2019). Microstructure, mechanical and elevated temperature tribological behaviors of the diamond/Cu composites prepared by spark plasma sintering method. Diam. Relat. Mater 91, 138–143. doi:10.1016/j.diamond.2018.10.022
Liu, L.-Y., Yang, Q.-S., and Liu, X. (2023a). Microstructure design and mechanical properties of grain-gradient graphene/aluminum composites. Eng. Fract. Mech. 277, 108944. doi:10.1016/j.engfracmech.2022.108944
Liu, X., Sun, F., Wang, L., Wu, Z., Wang, X., Wang, J., et al. (2020). The role of Cr interlayer in determining interfacial thermal conductance between Cu and diamond. Appl. Surf. Sci. 515, 146046. doi:10.1016/j.apsusc.2020.146046
Liu, X., Zhang, H., Lin, G., Wang, Z., Zhang, J., and Shi, H. (2023b). Advances in deposition of diamond films on cemented carbide and progress of diamond coated cutting tools. Vacuum 217, 112562. doi:10.1016/j.vacuum.2023.112562
Merabia, S., and Termentzidis, K. (2014). Thermal boundary conductance across rough interfaces probed by molecular dynamics. Phys. Rev. B 89, 054309. doi:10.1103/PhysRevB.89.054309
Monje, I. E., Louis, E., and Molina, J. M. (2014). On critical aspects of infiltrated Al/diamond composites for thermal management: diamond quality versus processing conditions. Compos Part A Appl. Sci. Manuf. 67, 70–76. doi:10.1016/j.compositesa.2014.08.015
Moore, A. L., and Shi, L. (2014). Emerging challenges and materials for thermal management of electronics. Mater. Today 17, 163–174. doi:10.1016/j.mattod.2014.04.003
Pan, Y., He, X., Ren, S., Wu, M., and Qu, X. (2019). Improvement of ZrC/Zr coating on the interface combination and physical properties of diamond-copper composites fabricated by spark plasma sintering. Materials 12, 475. doi:10.3390/ma12030475
Sang, J., Zhou, L., Yang, W., Zhu, J., Fu, L., and Li, D. (2021). Enhanced thermal conductivity of copper/diamond composites by fine-regulating microstructure of interfacial tungsten buffer layer. J. Alloys Compd. 856, 157440. doi:10.1016/j.jallcom.2020.157440
Shen, W., Shao, W., Wang, Q., and Ma, M. (2010). Thermal conductivity and thermal expansion coefficient of diamond/5wt%Si–Cu composite by vacuum hot pressing. Fusion Eng. Des. 85, 2237–2240. doi:10.1016/j.fusengdes.2010.08.043
Shen, X.-Y., He, X.-B., Ren, S.-B., Zhang, H.-M., and Qu, X.-H. (2012). Effect of molybdenum as interfacial element on the thermal conductivity of diamond/Cu composites. J. Alloys Compd. 529, 134–139. doi:10.1016/j.jallcom.2012.03.045
Tan, X., Zhang, B., Liu, K., Yan, X., Han, J., Liu, X., et al. (2020). Microstructure and mechanical property of the 2024Al matrix hybrid composite reinforced with recycled SiCp/2024Al composite particles. J. Alloys Compd. 815, 152330. doi:10.1016/j.jallcom.2019.152330
Tao, J., Zhu, X., Tian, W., Yang, P., and Yang, H. (2014). Properties and microstructure of Cu/diamond composites prepared by spark plasma sintering method. Trans. Nonferrous Metals Soc. China 24, 3210–3214. doi:10.1016/S1003-6326(14)63462-2
Wang, C., Li, H., Chen, M., Li, Z., and Tang, L. (2020). Microstructure and thermo-physical properties of Cu Ti double-layer coated diamond/Cu composites fabricated by spark plasma sintering. Diam. Relat. Mater 109, 108041. doi:10.1016/j.diamond.2020.108041
Ward, A., Broido, D. A., Stewart, D. A., and Deinzer, G. (2009). Ab initio theory of the lattice thermal conductivity in diamond. Phys. Rev. B 80, 125203. doi:10.1103/PhysRevB.80.125203
Weber, L., and Tavangar, R. (2007). On the influence of active element content on the thermal conductivity and thermal expansion of Cu–X (X=Cr, B) diamond composites. Scr Mater 57, 988–991. doi:10.1016/j.scriptamat.2007.08.007
Wu, K., Zhang, L., Li, F., Sang, L., Liao, M., Tang, K., et al. (2024). Enhancement of interfacial thermal conductance by introducing carbon vacancy at the Cu/diamond interface. Carbon N. Y. 223, 119021. doi:10.1016/j.carbon.2024.119021
Wu, X., Li, L., Zhang, W., Song, M., Yang, W., and Peng, K. (2019). Effect of surface roughening on the interfacial thermal conductance of diamond/copper composites. Diam. Relat. Mater 98, 107467. doi:10.1016/j.diamond.2019.107467
Yoshida, K., and Morigami, H. (2004). Thermal properties of diamond/copper composite material. Microelectron. Reliab. 44, 303–308. doi:10.1016/S0026-2714(03)00215-4
Zhang, C., Wang, R., Cai, Z., Peng, C., Feng, Y., and Zhang, L. (2015). Effects of dual-layer coatings on microstructure and thermal conductivity of diamond/Cu composites prepared by vacuum hot pressing. Surf. Coat. Technol. 277, 299–307. doi:10.1016/j.surfcoat.2015.07.059
Zhang, H., Zhang, J., Liu, Y., Zhang, F., Fan, T., and Zhang, D. (2018). Unveiling the interfacial configuration in diamond/Cu composites by using statistical analysis of metallized diamond surface. Scr Mater 152, 84–88. doi:10.1016/j.scriptamat.2018.04.021
Zhang, X., and Lei, Q. (2024). High thermal conductivity Cu-3Cr/Diamond composites fabricated by powder metallurgy. Mater Lett. 363, 136253. doi:10.1016/j.matlet.2024.136253
Zhang, Y., Wang, Z., Li, N., Sun, F., Hao, J., Wu, H., et al. (2023). Amorphous carbon interlayer modulated interfacial thermal conductance between Cu and diamond. Appl. Surf. Sci. 638, 158001. doi:10.1016/j.apsusc.2023.158001
Zhang, Z., He, X., Zhang, T., Liu, P., and Qu, X. (2024). Preparation of bimodal-diamond/SiC composite with high thermal conductivity. J. Eur. Ceram. Soc. 44, 643–650. doi:10.1016/j.jeurceramsoc.2023.09.069
Zhao, D., Zha, S., and Liu, D. (2021). Influence of sputtering and electroless plating of Cr/Cu dual-layer structure on thermal conductivity of diamond/copper composites. Diam. Relat. Mater 115, 108296. doi:10.1016/j.diamond.2021.108296
Zhong, Z., Jiang, X., Sun, H., Wu, Z., Yang, L., and Matamoros-Veloza, A. (2024). Recent research on the optimization of interfacial structure and interfacial interaction mechanisms of metal matrix composites: a review. Adv. Eng. Mater 26. doi:10.1002/adem.202401392
Zhou, L., Liu, J., Ding, R., Cao, J., Zhan, K., and Zhao, B. (2023). A review of diamond interfacial modification and its effect on the properties of diamond/Cu matrix composites. Surfaces Interfaces 40, 103143. doi:10.1016/j.surfin.2023.103143
Zhu, C., Cui, C., Wu, X., Zhang, B., Yang, D., Zhao, H., et al. (2020). Study on surface modification of diamond particles and thermal conductivity properties of their reinforced metal-based (Cu or Mg) composites. Diam. Relat. Mater 108, 107998. doi:10.1016/j.diamond.2020.107998
Keywords: high thermal conductivity, diamond/copper, composite material, surface metallization, matrix alloying
Citation: Xue Y, Li R, Deng Y, Zhang Z, Chen J, Ma A and Wen R (2025) Research progress in interface optimization and preparation technology of high thermal conductivity diamond/copper composite materials. Front. Mater. 12:1582990. doi: 10.3389/fmats.2025.1582990
Received: 25 February 2025; Accepted: 19 March 2025;
Published: 24 April 2025.
Edited by:
Yutai Su, Northwestern Polytechnical University, ChinaReviewed by:
Luke Yan, Chang’an University, ChinaLeiming Du, Delft University of Technology, Netherlands
Copyright © 2025 Xue, Li, Deng, Zhang, Chen, Ma and Wen. This is an open-access article distributed under the terms of the Creative Commons Attribution License (CC BY). The use, distribution or reproduction in other forums is permitted, provided the original author(s) and the copyright owner(s) are credited and that the original publication in this journal is cited, in accordance with accepted academic practice. No use, distribution or reproduction is permitted which does not comply with these terms.
*Correspondence: Aijie Ma, bWFhaWppZUB4YXR1LmVkdS5jbg==