- Materials Science and Engineering, Nanjing University of Technology, Nanjing, China
Injection molding is the most common method for making plastic products. However, quick molds made with ultraviolet (UV) curing 3D printing frequently employ photosensitive resins with low mechanical strength, rendering plastic components prone to warpage deformation. To solve this issue, our research focuses on the design and development of fast molds using UV-curing 3D printing technology. A response surface model was used to explore the effect of different process parameters on component warpage, with the goal of minimizing deformation. An upgraded particle swarm optimization (PSO) technique was then created to fine-tune the process parameters and reduce warpage even more. The results revealed that raising injection pressure, reducing temperature, and prolonging holding time successfully reduced warpage. During the single-peak Schwefel function test, the modified PSO method displayed greater optimization capabilities, achieving convergence in around 40 iterations. Using the modified values, the maximum warpage was lowered by 0.55 mm. Experimental results demonstrate the suggested optimization model’s performance, allowing for increased mold design flexibility and aiding the industry’s migration to digital and customized production.
Introduction
With the advancement and implementation of ultraviolet curing 3D printing (UVC-3DP) technology, it has significant advantages in designing injection molds to fulfill the demands for high precision and intricate detail (Pan et al., 2022). 3D printing technology can be employed in the production of various types of molds. Its biggest advantage is that it can realize rapid prototyping, which can significantly improve manufacturing efficiency, reduce costs, and provide greater flexibility for product design (Park et al., 2022). Significant progress has been achieved in the application of UVC-3DP molds to injection molding. These successes include: (1) rapid mold prototyping that accelerates production cycles; (2) improved mold design optimization enabling more precise and complex geometries; and (3) reduction of plastic component warpage through enhanced process control. However, several persistent bottlenecks remain: (1) the limited mechanical strength and thermal stability of photosensitive resins, which affect the mold’s durability under injection molding conditions; (2) warpage deformation in molded parts caused by the low thermal conductivity of UV-curable resins; and (3) challenges in process parameter optimization, where current approaches may lack accuracy and are prone to converging on local optima.
Rapid mold is a kind of use of computers, CNC technology and other means, in a shorter period to produce product samples of mold manufacturing technology. The emergence of rapid mold makes it possible to reduce the product development timeline, accelerate the speed of product replacement and reduce the investment risk of enterprises (Park et al., 2022). UVC-3DP rapid molds have a shorter lifetime, and the photosensitive resin used in them has lower thermal conductivity and mechanical strength, which will be subjected to impacts from the melt temperature (MeT), which in turn will cause warpage deformation in the plastic part Liu et al., 2023) Therefore, optimizing the specifications of the injection molding (IM) process is crucial because it lowers the number of process parameters and enhances the use of UVC-3DP fast molds. However, when performing parameter optimization, the currently popular single approach has issues with low accuracy and a propensity to enter the local optimal solution (LOS). For this reason, the study is based on response surface methodology (RSM) to model UVC-3DP molds and build a process parameter optimization model (PPOM) based on the improved particle swarm optimization (IPSO) algorithm, in order to improve the accuracy and quality of plastic part produced by UVC-3DP molds and reduce the waste of raw materials. The innovation of the study is to model the UVC-3DP mold based on RSM and output the optimal IM process parameters using the IPSO algorithm. Other primary goals of this study are to increase the precision and speed of mold creation and improve the mechanical strength and thermal stability of UV-curing molds. To address the persistent issue of warpage deformation in plastic parts molded with UVC-3DP molds, our research adopts a two-stage problem-solving strategy. First, we utilize Response Surface Methodology (RSM) to construct a predictive model that characterizes the relationship between key injection molding parameters—holding time, holding pressure, mold temperature, and melt temperature—and the resulting warpage deformation. This allows us to identify the most significant contributors to part distortion. Second, we propose an enhanced optimization methodology by integrating Particle Swarm Optimization (PSO) with a Genetic Algorithm (GA), forming an improved PSO (IPSO) algorithm. This hybrid optimization approach is employed to determine the optimal combination of process parameters that minimize warpage. Through simulation and experimental validation, our methodology provides a robust and data-driven framework for improving part quality, enhancing mold performance, and advancing the industrial applicability of UVC-3DP technology in rapid tooling.
UVC-3DP technology is a 3D printing technology for additive manufacturing based on photosensitive resin materials, and the core principle is to cure the photosensitive resin layer by layer using high-intensity ultraviolet light or digital light processing technology (Chen et al., 2025). To create continuous fiber composites, Ding Y et al. suggested an embedded 3D printing technique that uses a deposition nozzle to accurately lay down continuous fibers beneath the resin layer. The results showed that the proposed 3D printing technique had the advantages of neat fiber alignment and void density minimization (Ding et al., 2024). Jiang H et al. investigated the effectiveness of a novel two-stage ultraviolet (UV)-curable resin material for 3D printing in response to the weak interfacial bonding and low mechanical strength of printed composites. The outcomes revealed that the material had strong mechanical stiffness, strength and inter-filament bonding, and could also be repaired, remodeled and recycled (Jiang et al., 2023). Yang Z et al. proposed the introduction of vaporized metal combustion for the preparation of high solid content UV epoxy resin/micro-silica powders in response to the short service life of injection molds fabricated using UVC-3DP technology. The findings demonstrated that the heat distortion temperature of the sample prepared by the proposed method reached 188°C (Yang et al., 2022). Komissarenko D et al. explored the possibility of using a UV curing system for the fabrication of high-strength, high-density zirconia parts using a low-cost desktop 3D printer. The results showed that the zirconia translucent ceramics prepared did not show any visible cracks or pores when the zirconia content of the slurry was 35 vol% and the density could reach 99.6% (Komissarenko et al., 2023). Abdullah A. M. et al. addressed the issue of poorly investigated characteristics of 3D-printed thermoset composites embedded with continuous fibers by creating an affordable 3D printing technique utilizing the direct ink writing technique (Abdullah et al., 2023). Zheng J et al. proposed a bio-based acrylate synthesized from eugenol and siloxane to address the problem of poor stability of UV-cured acrylates used in UVC-3DP technology. The outcomes revealed that the acrylate had low viscosity, good thermal properties and hydrophobicity after curing UV irradiation, and cytotoxicity values above 80% (Zheng et al., 2022).
Using an injection mold, molten plastic is injected into a mold, where it is subsequently cooled and pressured to create the required shape of the finished product. Berlin W et al. developed a numerical simulation model for the temperature control of injection molds. The potential to enhance the efficiency of metal energy input through infrared radiation was examined in the study using ray tracing models, which may aid in the thermal design of injection molds with intricate geometries (Berlin et al., 2022). Zhang Y et al. suggested a deep learning and computer vision detection-based process monitoring method for automated real-time quality monitoring in the injection mold manufacturing process. The results indicated that the proposed method could effectively detect the geometrical dimensions of parts as well as many types of IM defects (Zhang et al., 2022). Steijvers K et al. addressed the difficulty of applying current fabrication methods to the large-scale production of locally resonant metamaterials and proposed a method for the large-scale production of resonators using injection molds, which could help to account for fabrication-induced changes in metamaterial geometry and material properties (Steijvers et al., 2023). Araújo C et al. proposed a processing fault monitoring method based on pressure distribution analysis to address the problem of monitoring and diagnosing processing faults in the IM process of injection molds. This study demonstrated the feasibility of intra-cavity pressure monitoring in fault diagnosis and IM process optimization, which could help to identify defects present at different stages of the injected part (Araújo et al., 2023). To develop environmentally friendly bamboo fiber reinforced PLA composites, Rao G et al. proposed the use of injection molds to process green composites. The study analyzed the mechanical, thermal and morphological traits of the composites (Rao et al., 2024). For improving the quality requirements of IM and the efficiency of the design process, Michaeli W et al. proposed a three-dimensional finite element model derived from Galerkin’s formulation to numerically simulate the velocity, pressure and temperature fields of IM (Michaeli et al., 2022).
While prior studies have applied Particle Swarm Optimization (PSO) and Genetic Algorithms (GA) independently to various process parameter optimization problems, their individual limitations, such as premature convergence in PSO and slow convergence in GA, restrict their effectiveness in complex, multimodal search spaces typical of UVC-3DP mold optimization. Moreover, existing research on UVC-3DP focuses primarily on material properties and mold fabrication, with limited attention to integrated process parameter optimization for warpage reduction. Our study addresses this gap by developing a hybrid PSO-GA algorithm that combines the global search capability of PSO with the population diversity maintenance of GA. This hybrid approach enhances convergence reliability and solution accuracy, specifically tailored for optimizing injection molding parameters in UVC-3DP molds, thereby advancing the state-of-the-art in rapid mold process optimization.
In summary, although, the research about the quality control of plastic part of UV curing plastic molds is still not deep enough. For this reason, the study of optimizing the injection process parameters of UVC-3DP molds in the hope of reducing the warpage deformation of plastic part has important practical application value.
Methodology
This study focuses on optimizing the injection molding (IM) process parameters to minimize warpage deformation in plastic parts produced using UV curing 3D printed (UVC-3DP) molds. The methodology involves two main components.
Response surface methodology (RSM) modeling
The heat transfer characteristics of UVC-3DP molds are modeled using RSM to capture the relationship between process parameters and warpage deformation.
Four injection molding parameters—holding time (HoT), holding pressure (HP), mold temperature (MoT), and melt temperature (MeT)—are selected as design variables.
Central Composite Design (CCD) is employed to systematically vary these parameters at five levels each, generating experimental data to fit a second-order polynomial response surface model that predicts warpage deformation.
Design Expert software is used for experimental design, data sampling, and model fitting.
Analysis of variance (ANOVA) is conducted to evaluate the significance of each parameter and the overall model fit.
Process parameter optimization model (PPOM) using improved particle swarm optimization (IPSO) hybridized with genetic algorithm (GA)
Since RSM alone cannot guarantee the global optimal solution, an optimization model combining IPSO and GA is developed to search the parameter space more effectively.
The IPSO algorithm incorporates dynamic inertia weights to balance global search ability and local search accuracy.
GA’s selection, crossover, and mutation operations are embedded in a serial hybrid strategy to enhance diversity and avoid premature convergence.
The optimization objective is to minimize the warpage deformation predicted by the RSM model.
Algorithm performance is validated against benchmark functions and compared with conventional PSO and GA methods to ensure superior global search capability and convergence speed. Finally, the optimal injection molding parameters identified by the PPOM are validated through Moldflow simulation to confirm the reduction in warpage deformation.
Optimized design of molds based on UVC-3DP
To investigate the quality control of plastic part for curing 3D plastic molds, the study will model the UVC-3DP molds based on RSM. The PPOM based on the IPSO algorithm will be further constructed to improve the quality of the plastic part.
RSM-based modeling of UVC-3DP molds
The heat transfer (HT) characteristics between molds printed by UVC-3DP technology and traditional metal molds have large differences. The HT rate is lower, and the cooling rate is slower, which will easily lead to warpage deformation of the plastic part. The warpage deformation is the deviation of the shape of the plastic part from the shape of the cavity of the rapid molds. This affects the molding accuracy and appearance quality of the plastic part, which makes it difficult to perform subsequent processing. Therefore, the study will analyze the mechanism of warpage deformation of plastic parts. Inhomogeneity in the heat exchange process is one of the main causes of plastic part warpage deformation. The heat exchange process of the injection mold directly changes the temperature distribution and shrinkage of the plastic part, which consequently leads to the plastic part warpage deformation. According to the law of conservation of energy, the study simplifies the heat exchange process of the UV curing rapid molds into Equation 1.
In Equation 1,
In Equation 2,
In Equation 3,
In Equation 4,
The higher the order of the PF, the better the model aligns with the data, but it can also overfit the noise. Therefore, after comprehensive consideration, the study uses the second order RSM equation to build the model as expressed in Equation 5.
In Equation 5,
In Equation 6,
The study used Design Expert software for data sampling to obtain the response function
In Equation 7,
PPOM based on IPSO algorithm
The study employs a RSM to construct a model. However, the RSM is unable to identify the optimal solution for all discrete combinations within the specified factor level interval. This can result in the model converging on a LOS. In light of the considerations, the study will proceed to construct a PPOM based on the IPSO algorithm. The particle swarm optimization (PSO) algorithm is a progressive computation technique that was first suggested by Dr. Eberhart and Dr. Kennedy in 1995. It was developed from the behavioral study of bird flock predation (Alsaidy et al., 2022). The PSO algorithm can identify the optimal solution within the search space by emulating the social behavior observed in biological groups, such as flocks of birds or schools of fish. It has the advantages of strong global search ability (GSA), a few parameters, easy to implement, etc., and has been widely used in parametric optimization tasks. Equation 8 displays the revised velocity of particle
In Equation 8,
In Equation 9,
The inertia weight
In Equation 10,
In Equation 11,
In Figure 3, the selection operation of GA refers to selecting a certain number of individuals from the current population according to a certain strategy based on the selection probability, so that these individuals can have more chances to be inherited into the next-generation. The selection process employs a roulette wheel selection mechanism to guarantee that those with better fitness values (FVs) have a larger chance of getting chosen. The probability
In Equation 12,
Subsequently, a PSO-GA-based mathematical model for process parameter optimization is established. Equation 13, which is based on the RS model developed in the study, displays the algorithm’s goal function.
In Equation 13, the optimization objective of PSO-GA is to reduce the response function
Influence factors of plastic part warpage and the results of parameter optimization model
After modeling the UVC-3DP mold, to further reduce the warpage deformation, the study will analyze the process parameters affecting the plastic part warpage deformation. Additionally, the viability and efficacy of the suggested PPOM, which is based on the IPSO algorithm, in enhancing the warpage deformation of plastic parts will be examined.
Effect of process parameters on plastic part warpage
Table 2 displays the findings of the analysis of variance for the four response variables and the RS model. The study used F-values and P-values to value the overall level of accuracy of the RS model that was built. The effect of HoT, HP and MeT on warpage is more significant (P < 0.05). The F value of the RS model is 16.829, and the regression effect of the overall model is extremely significant.
To assess the efficacy of the RS model developed by the study in terms of fitting, a comparison was conducted between the predicted and actual values. The results of the comparison are presented in Figure 5. The discrepancy between the estimated and observed values is minimal, and the margin of error falls within an acceptable range. The findings demonstrate that the RS model developed by the study has a good fitting impact.
To explore the effect of material properties on plastic part warpage deformation, the study compares the pressure volume temperature (PVT) characteristic curves of semi-crystalline materials with amorphous materials. Figure 6 displays the findings. As illustrated in Figure 6a, the volume-specific volume of the semi-crystalline material demonstrates a gradual increase with rising temperature, reaching a maximum at 275°C. A pressure level of 50 MPa was applied. The volume specific volume of semi-crystalline material can reach 1.12 when the applied pressure level is 50 MPa. In Figure 6b, the volume specific volume of amorphous material also increases gradually with the increase of temperature. A comparison of Figures 6a,b reveals that the volume-specific volume of the semi-crystalline material is greater than that of the amorphous material, and that the volume change is more pronounced under identical conditions of temperature and applied pressure. The plastic part is more prone to warpage deformation. The results show that the material properties affect the plastic part warpage deformation.
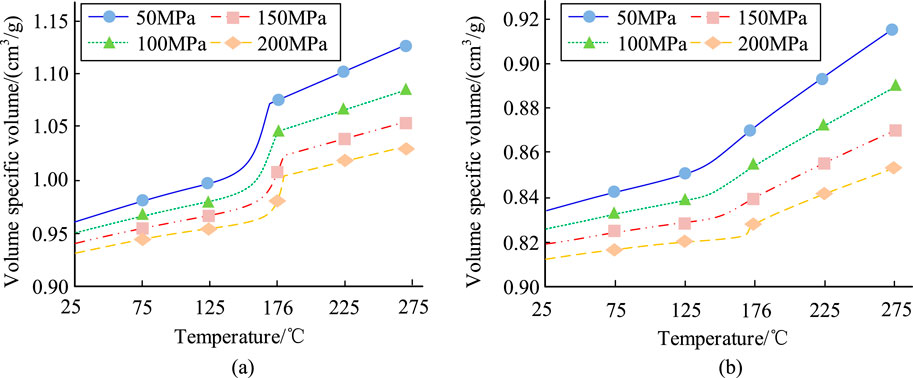
Figure 6. Comparison of PVT characteristic curves of different materials. (a) Semicrystalline materials, (b) Amorphous material.
The effects of four IM parameters, HoT, HP, MoT and MeT on the warpage deformation of plastic parts are shown in Figure 7. In Figure 7a, the warpage deformation of plastic part shows a gradual decrease with the increase of HP time. When the HoT increases from 3s to 5s, the warpage deformation of the plastic part also decreases from 2.51 mm to 2.46 mm. In Figure 7b, the warpage deformation of the plastic part shows a gradual decrease with the increase of the HP. When the HP rises from 45 MPa to 70 MPa, the warpage deformation of the plastic part also decreases from 2.53 mm to 2.32 mm. In Figure 7c, the warpage deformation of the plastic part does not show significant change with the increase of the MoT. As demonstrated in Figure 7d, the warpage deformation of the plastic component demonstrates a gradual increase in conjunction with an escalation in MeT. The results indicate that HoT and HP are negatively correlated with the amount of warpage deformation of the plastic part. The MeT is positively correlated with the amount of warpage deformation of plastic parts. There is no significant relationship between MoT and the amount of warpage deformation of plastic part.
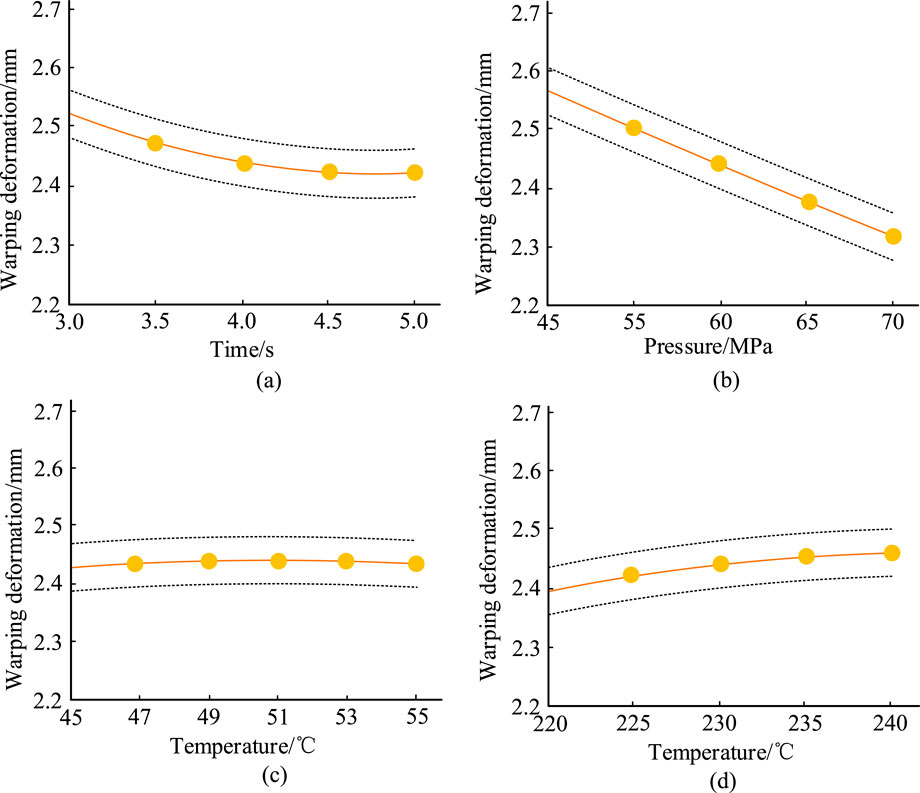
Figure 7. The influence of IM parameters on the warpage deformation of plastic parts. (a) Hold time, (b) Hold pressure, (c) Mold temperature, (d) Solution temperature.
Effectiveness analysis of parameter optimization model
To ascertain the efficacy of the proposed PSO-GA, the study establishes a population count of 100, a series of iterations of 100, inertia weights of [0.4,0.9], a crossover probability of 0.8, a variance probability of 0.1,
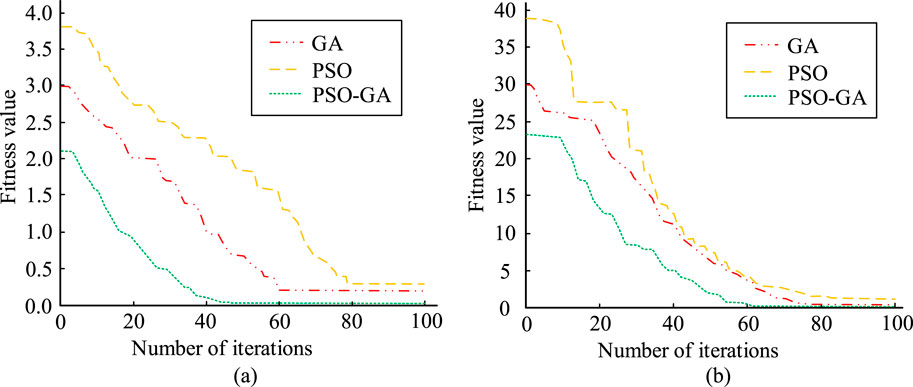
Figure 8. Test results of three algorithms on Schwefe function and Rastrigin function. (a) Schwefe function, (b) Rastrigin function.
To further verify the performance and superiority of the suggested PSO-GA for optimization search, the study uses the Iris dataset for testing, with accuracy and recall as the evaluation metrics. It is compared with the more advanced chaos artificial bee colony (CABC) algorithm, chaos moth-flame optimization (CMFO) algorithm and adaptive glowworm swarm optimization (AGSO). Figure 9 displays the findings. In Figure 9a, the recommended PSO-GA has a higher accuracy of 94.02% in comparison to the three alternative methods. As illustrated in Figure 9b, the proposed PSO-GA continues to exhibit the highest recall rate of 92.16%. The findings show that the anticipated PSO-GA exhibits superior performance in optimization search.
The optimal IM process parameters of PSO-GA output are HoT 6s, HP 80 MPa, MoT 53.4°C, and Melt Temperature (MeT) 224.6°C. To investigate the viability of the proposed PPOM found on the IPSO algorithm, the process parameters are input into Moldflow for simulation. It is compared with the warpage deformation obtained from the simulation of the process parameters before parameter optimization, the process parameters output from the traditional GA and the process parameters output from the TPSOA. The results are shown in Figure 10. The PPOM based on the IPSO algorithm can reduce the warpage deformation of the plastic part from 2.49 mm to 1.94 mm. The amount of warpage deformation is lower than that of 2.17 mm in the conventional GA and 2.02 mm in the conventional PSO algorithm. The results indicate that the proposed PPOM based on the IPSO algorithm can output better IM process parameters. This can effectively reduce the warpage deformation of plastic parts, which has certain feasibility and effectiveness.
In addition to accuracy and convergence performance, practical applicability also depends on computational efficiency. While the proposed PSO-GA hybrid algorithm demonstrates superior optimization performance compared to conventional PSO and GA in terms of fitness value and convergence rate, it incurs a higher computational cost due to the sequential integration of genetic operations (selection, crossover, mutation) within each PSO iteration. The added complexity results in longer processing times, particularly when handling larger parameter spaces or finer convergence criteria. However, the algorithm remains tractable on standard computing hardware (e.g., Intel Core i7 with 16 GB RAM), with total runtime remaining within acceptable limits for engineering applications. Despite the additional overhead, the performance gains in solution quality and robustness justify the moderate increase in computational load, making the method suitable for industrial process optimization tasks where reliability and precision are critical.
Conclusion
To reduce the warpage deformation of plastic part during the IM process of UVC-3DP mold, the study modeled the UVC-3DP mold based on RSM and built a PPOM based on the IPSO algorithm. The results indicated that HoT, HP and MeT had more significant effects on the warpage (P < 0.05). When the HoT was increased from 3s to 5s, the warpage deformation of plastic part decreased from 2.51 mm to 2.46 mm. When the HP was increased from 45 MPa to 70 MPa, the warpage deformation of plastic part decreased from 2.53 mm to 2.32 mm. When the HP was increased from 45 MPa to 70 MPa, the warpage deformation of plastic part also decreased from 2.53 mm to 2.32 mm. The warpage deformation of the plastic part did not show significant changes with the increase of MoT. In the test of single-peak Schwefe function, compared with the TPSOA and GA, the proposed PSO-GA had a smaller FV of 0.007 and a faster convergence rate, which tended to converge after about 40 iterations. In the test of complex multi-peak Rastrigin function, the proposed PSO-GA had smaller FV and converged at about 60 iterations. Compared with CABC algorithm, CMFO algorithm and AGSO algorithm, the accuracy and recall of the proposed PSO-GA were higher, 94.02% and 92.16%, respectively. The PPOM based on the IPSO algorithm could reduce the warpage deformation of the plastic part from 2.49 mm to 1.94 mm. The amount of warpage deformation was lower than that of the conventional GA, which was 2.17 mm, and that of the conventional PSO algorithm, which was 2.02 mm. However, the study only analyzed the warpage deformation of the plastic part, and the actual IM process of the plastic part may also have defects such as cracking, which affects its application performance. Therefore, it would be beneficial for future studies to further investigate the occurrence of quality issues in the IM process of UV curing molds, with the aim of promoting the application of rapid molds based on UVC-3DP technology. It is important to note that the current study’s validation of the optimized process parameters is based solely on Moldflow simulations, and no experimental trials were conducted to verify these results. Future work will focus on experimental validation to confirm the effectiveness of the proposed PPOM based on the IPSO-GA algorithm in reducing warpage deformation and improving the quality of plastic parts produced with UVC-3DP molds. While this study focused primarily on minimizing warpage deformation, other critical defects such as shrinkage, void formation, and cracking were not modeled due to simulation constraints. These factors can also significantly impact the performance and longevity of injection-molded parts. Accordingly, future research will extend the modeling approach to incorporate these additional quality indicators. Furthermore, the current optimization framework was developed and tested on specific mold material and process setup. To assess its broader applicability, subsequent studies should apply the framework to a wider range of mold geometries, resin types, and 3D printing technologies, ensuring the robustness and generalizability of the proposed methodology across diverse manufacturing contexts.
Data availability statement
The original contributions presented in the study are included in the article/supplementary material, further inquiries can be directed to the corresponding author.
Author contributions
HR: Conceptualization, Investigation, Writing – original draft, Formal Analysis, Data curation. XB: Investigation, Writing – review and editing, Methodology, Formal Analysis, Data curation. WY: Methodology, Investigation, Conceptualization, Data curation, Writing – review and editing, Formal Analysis. JL: Investigation, Formal Analysis, Writing – review and editing, Data curation, Methodology, Conceptualization.
Funding
The author(s) declare that no financial support was received for the research and/or publication of this article.
Conflict of interest
The authors declare that the research was conducted in the absence of any commercial or financial relationships that could be construed as a potential conflict of interest.
Generative AI statement
The author(s) declare that no Generative AI was used in the creation of this manuscript.
Publisher’s note
All claims expressed in this article are solely those of the authors and do not necessarily represent those of their affiliated organizations, or those of the publisher, the editors and the reviewers. Any product that may be evaluated in this article, or claim that may be made by its manufacturer, is not guaranteed or endorsed by the publisher.
References
Abdullah, A. M., Ding, Y., He, X., Dunn, M., and Yu, K. (2023). Direct-write 3D printing of UV-curable composites with continuous carbon fiber. J. Compos. Mater. 57 (4), 851–863. doi:10.1177/00219983221127182
Alhijawi, B., and Awajan, A. (2024). Genetic algorithms: theory, genetic operators, solutions, and applications. Evol. Intell. 17 (3), 1245–1256. doi:10.1007/s12065-023-00822-6
Alsaidy, S. A., Abbood, A. D., and Sahib, M. A. (2022). Heuristic initialization of PSO task scheduling algorithm in cloud computing. J. King Saud University-Computer Inf. Sci. 34 (6), 2370–2382. doi:10.1016/j.jksuci.2020.11.002
Araújo, C., Pereira, D., Dias, D., Marques, R., and Cruz, S. (2023). In-cavity pressure measurements for failure diagnosis in the injection moulding process and correlation with numerical simulation. Int. J. Adv. Manuf. Technol. 126 (1), 291–300. doi:10.1007/s00170-023-11100-1
Arpitha, G. R., Mohit, H., Madhu, P., and Verma, A. (2024). Effect of sugarcane bagasse and alumina reinforcements on physical, mechanical, and thermal characteristics of epoxy composites using artificial neural networks and response surface methodology. Biomass Convers. Biorefinery 14 (11), 12539–12557. doi:10.1007/s13399-023-03886-7
Bayuo, J., Rwiza, M. J., and Mtei, K. M. (2024). Optimization of divalent mercury removal from synthetic wastewater using desirability function in central composite design of response surface methodology. J. Environ. Health Sci. Eng. 22 (1), 209–227. doi:10.1007/s40201-023-00888-5
Berlin, W., Reichel, V., Hürkamp, A., and Dröder, K. (2022). Heat Control simulation for variothermal injection moulding moulds using infrared radiation. Int. J. Adv. Manuf. Technol. 119 (9), 6073–6089. doi:10.1007/s00170-022-08715-1
Chen, S., Khan, S. B., Li, N., and Xiao, C. (2025). In-depth analysis of sintering, exposure time, and layer height (um) in LRS 3D printed devices with DLP. J. Manuf. Process. 133, 576–591. doi:10.1016/j.jmapro.2024.11.060
Ding, Y., Gracego, A. X., Wang, Y., Dong, G., Dunn, M. L., and Yu, K. (2024). Embedded 3D printing of UV-curable thermosetting composites with continuous fiber. Mater. Horizons 11 (18), 4378–4392. doi:10.1039/d4mh00705k
Jiang, H., Abdullah, A. M., Ding, Y., Chung, C., Dunn, M. L., and Yu, K. (2023). 3D Printing of continuous fiber composites using two-stage UV curable resin. Mater. Horizons 10 (12), 5508–5520. doi:10.1039/d3mh01304a
Komissarenko, D., Roland, S., Seeber, B. S. M., Graule, T., and Blugan, G. (2023). DLP 3D printing of high strength semi-translucent zirconia ceramics with relatively low-loaded UV-curable formulations. Ceram. Int. 49 (12), 21008–21016. doi:10.1016/j.ceramint.2023.03.236
Liu, H., Jiang, G., Dong, Z., and Jin, S. (2023). A calculation method for the deformation behavior of warp-knitted fabric. AUTEX Res. J. 23 (1), 55–65. doi:10.2478/aut-2021-0052
Manojkumar, N., Muthukumaran, C., and Sharmila, G. (2022). A comprehensive review on the application of response surface methodology for optimization of biodiesel production using different oil sources. J. King Saud University-Engineering Sci. 34 (3), 198–208. doi:10.1016/j.jksues.2020.09.012
Michaeli, W., Hoffmann, S., Kratz, M., and Webelhaus, K. (2022). Simulation opportunities by a three-dimensional calculation of injection moulding based on the finite element method. Int. Polym. Process. 16 (4), 398–403. doi:10.3139/217.1654
Pan, Z., Wang, D., Guo, X., Li, Y., Zhang, Z., and Xu, C. (2022). High strength and microwave-absorbing polymer-derived SiCN honeycomb ceramic prepared by 3D printing. J. Eur. Ceram. Soc. 42 (4), 1322–1331. doi:10.1016/j.jeurceramsoc.2021.12.003
Park, S., Shou, W., Makatura, L., Matusik, W., and Fu, K. K. (2022). 3D printing of polymer composites: materials, processes, and applications. Matter 5 (1), 43–76. doi:10.1016/j.matt.2021.10.018
Rao, G. S., Debnath, K., and Mahapatra, R. N. (2024). Mechanical, Thermal, morphological, and fibre characteristics during injection moulding of green composites. Fibers Polym. 25 (1), 331–346. doi:10.1007/s12221-023-00424-0
Steijvers, K., Claeys, C., Van Belle, L., and Deckers, E. (2023). Incorporating manufacturing process simulations to enhance performance predictions of injection moulded metamaterials. J. Vib. Eng. & Technol. 11 (6), 2617–2629. doi:10.1007/s42417-023-01159-1
Yang, Z., Peng, S., Wang, Z., Miao, J. T., Zheng, L., Wu, L., et al. (2022). UV-curable, low-viscosity resin with a high silica filler content for preparing ultrastiff, 3D-printed molds. ACS Appl. Polym. Mater. 4 (4), 2636–2647. doi:10.1021/acsapm.1c01920
Zhang, Y., Shan, S., Frumosu, F. D., Calaon, M., Yang, W., Liu, Y., et al. (2022). Automated vision-based inspection of mould and part quality in soft tooling injection moulding using imaging and deep learning. CIRP Ann. 71 (1), 429–432. doi:10.1016/j.cirp.2022.04.022
Keywords: ultraviolet curing 3D printing, rapid mold, particle swarm optimization algorithm, photosensitive resin, viscosity
Citation: Rao H, Bai X, Yan W and Liu J (2025) Rapid mold optimization based on ultraviolet curing 3D printing technology. Front. Mater. 12:1605771. doi: 10.3389/fmats.2025.1605771
Received: 03 April 2025; Accepted: 13 June 2025;
Published: 02 July 2025.
Edited by:
Teng Zhou, Hainan University, ChinaReviewed by:
Amir Ali Shahmansouri, Washington State University, United StatesAli Rıza Deniz, Hakkari University, Türkiye
Mahmood Ahmad, International Islamic University Malaysia, Malaysia
Copyright © 2025 Rao, Bai, Yan and Liu. This is an open-access article distributed under the terms of the Creative Commons Attribution License (CC BY). The use, distribution or reproduction in other forums is permitted, provided the original author(s) and the copyright owner(s) are credited and that the original publication in this journal is cited, in accordance with accepted academic practice. No use, distribution or reproduction is permitted which does not comply with these terms.
*Correspondence: Jie Liu, a3ZuejA4MkAxNjMuY29t