- Metals and Chemistry Research Institute, China Academy of Railway Sciences Corporation Limited, Beijing, China
Manganese (Mn) makes important role in the microstructure and mechanical properties of flash welded joints of the commonly applied U71 Mn rail. In this work, two rail steels with different Mn concentration are tested: U71Mn (Mn of 1.03 wt%) and modified U71Mn steel (Mn of 0.94 wt%). Grey spots, micro cracks, and martensitic transformation in the welded joints are characterized by scanning electron microscopy (SEM), energy dispersive spectrometry (EDS), and high-speed photography. It is discovered that the decrease of the manganese content enhances the quality of the weld joint. 65% increase in impact toughness can be achieved, while the length of network ferrite in the web region reduced from 1.0 mm to 0.3 mm. Quantitative metallography indicates that the carbon equivalent of the weld metal, not its manganese content, exercises more control over the martensitic transformation with a 66% correlation coefficient. The study also shows that the average grey spot created in the weld metal has about 77% manganese segregation. Fatigue tests of welded joints show that micro cracks are formed due to the larger size of the MnS inclusions but the effect on joint integrity can be minimized through control of composition. The conclusions reached here touch on critical aspects necessary for the development of rail steels possessing greater serviceability and weldability, paving the way toward the implementation of high-speed railway systems.
1 Introduction
The attention to the quality and reliability of rail welded joints has been increasing along with the corresponding expansion of high-speed railways. The service performance and functionality of rail welded joints as structural elements of high-speed railway systems influence the safety and comfort of train operations (Han et al., 2024). As the standard rail in China’s high-speed railway network, U71Mn rail steel is commonly investigated. However, the reliable modeling of the microstructural evolution and mechanical properties in welded joints remains challenging. Flash welded joints have a complex microstructure consisting mainly of pearlite and ferrite, which greatly determines their service performance and the associated failure mechanisms (Liao et al., 2023).
With the development of high-speed rail systems, the requirements of the quality and reliability of rail welded joints has largely increased. (Zhang H. et al., 2022). In fact, the welded joints are the most vulnerable parts of the track systems, where components with different material properties undergo different forms of destructive changes (Shen et al., 2024). The functionality and service performance of rail welded joints as structural components of high-speed railway systems affect the safety and comfort during train operations. Overhauling the chemical composition offers a significant means of enhancing the efficiency of rail welding.
Manganese (Mn) is one of the important alloys in welding metallurgy, whose concentration has a substantial influence on the microstructural changes and the mechanical performance of the welded joints. Recent studies show that manganese content optimization in high-carbon steels is very important for improvement of weld joint performance. Zhu et al. indicates that the grain size and phase distribution are dominant characteristics that dictate the mechanisms of crack nucleation and growth (Zhu et al., 2024). The relationships between the chemical composition, especially the amount of manganese, and the microstructural characterization of U71Mn rail welded joints (Han et al., 2024; Liu et al., 2023). For example, Su et al. (2019) showed that controlled amounts of manganese have a profound effect in the heat affected zones with complex phase changes. In-depth understanding the link between microstructure and the mechanical properties of U71Mn rail steel welded joints is of increasing interests of reseachers (Ma et al., 2015).
Futhermore, Manganese has a pronounced effect on inclusion morphology as well as crack initiation mechanisms, which is particularly hazardous for joint integrity. Muttamara et al. (2024) reported that manganese content influences decarburization and fatigue performance of railway components, while Yang et al. (2024) showed that optimized manganese concentration in rail steel applications enhances wear and corrosion resistance. Zeng et al. (2024) noticed that manganese content has a profound impact on inclusion formation and distribution, which affects crack propagation patterns. The size and distribution of MnS inclusions is critical, as they decisively influence the mechanical properties and service life of welded joints (Wang et al., 2024). The understanding of the crack initiation mechanisms and material toughening by chemical composite design requires the in-depth systematic understanding of manganese content’s effects in flash-welded joints (Yi et al., 2024; Xue et al., 2024).
The current study analyses the impact of lowering manganese content on the microstructure, mechanical properties, and defect evolution of U71Mn rail steel welded joints. In-depth metallographic, mechanical, and fracture analyses were accomplished to understand the intricate relationship of manganese content with welding efficiency. D. Pereira and others have made strides in understanding the optimization of welding processes (Pereira et al., 2022), and F. Fu et al. provided understanding on control of microstructure (Fu et al., 2024), while others, notably R. Kendall, contributed greatly to understanding the performance evaluation processes (Kendall et al., 2022). Nevertheless, as Zhao et al. pointed out, the systematic study of the effects of manganese content on the integrity of weld joints is still understudied and requires immediate attention (Zhao et al., 2022). This study is distinctive in that it aims to resolve a specific knowledge gap about the effects of controlled reduction of manganese on joint integrity, inclusion morphology, and cracking resistance. The purpose of this work is to fill the gap by revealing the fundamental connections of percentage of manganese, microstructure evolution, and U71Mn rail welded joints mechanical properties towards the development of high-performance rail materials.
2 Experimental materials and methods
2.1 Design of test materials and compositions
The materials for this experiment were U71Mn rail steels with varying levels of manganese. Two commercially availible materials were studied: a regular U71Mn rail steel, which is referred to as RM, and a modified version with lower manganese concentration, termed HM (Zhao et al., 2022). Table 1 illustrates the results of the chemical analysis in which it was determined that the manganese content of HM steel was 0.94%, which is approximately 0.1% less than RM steel’s manganese content of 1.03%. The chemical compositions are measured by heat analysis, following GB/T 222-2006 and TB/T 3276-2011 (Zhao et al., 2022). Both steels fulfilled the criteria of TB/T 3276-2011 standard specification for U71MnG rail steel (Ruijie et al., 2023). The analysis of the chemical composition uniformity at different positions of the rail head, web and foot showed little difference, thus proving the rail section is homogenous compositionally.
2.2 Welding process parameters and heat treatment system
The experimental study precisely controlled the flash welding parameters, based on optimized methodologies for high-carbon rail steels (Pang et al., 2022). Key parameters were determined through systematic welding trials (Saita et al., 2013), including flashing speed (0.85–1.15 mm/s), upset amount (13–16 mm), and forging force (950–1150 KN). Three distinct cooling rates were implemented: rapid cooling (2.4°C/s), medium cooling (1.6°C/s), and slow cooling (0.8°C/s), following established rail welding protocols (Kuchuk-Yatsenko et al., 2016). The temperature-time cooling curves for these three cooling rates are shown in Figure 1. The curves clearly demonstrate the distinct cooling behaviors, with the rapid cooling rate (2.4°C/s) showing the steepest temperature decline, while the slow cooling rate (0.8°C/s) exhibits a more gradual descent. This controlled cooling process is critical for the development of desired microstructural features in the heat-affected zone.
Post-weld heat treatment (PWHT) optimization was applied based on recent advances in heat treatment technology for rail steels (Porcaro et al., 2019). Normalization was performed at 610°C ± 10°C for 2 h, followed by controlled cooling to 300°C with rate of 140°C/h and then air cooling. The HM steel, with its optimized manganese content of 0.94% compared to 1.03% in RM steel, demonstrated improved properties without post-weld heat treatment, aligning with contemporary research on composition-property relationships (Ghazanfari and Tehrani, 2021).
Rail specimens were welded using thermally controlled flash butt welding techniques. Thermal simulations were carried out with three distinct cooling rates which included fast cooling at 2.4°C/s, medium cooling at 1.6°C/s, and slow cooling at 0.8°C/s (Mortazavian et al., 2022). After normalizing, PWHT was performed on RM specimens, whereas HM specimens were evaluated in the as welded state. Weldability of U71Mn, U75V, and four experimental compositions with different manganese and chromium quantities were modelled with JMATpro (Zhang B. et al., 2022). The values of carbon equivalent, shown in Table 2, were calculated using International Institute of Welding (IIW) and Japanese Industrial Standard (JIS) standards. The U71Mn standard was surpassed by the experimental composition 202109–1 which had a slightly lower carbon equivalent, while 202109–4 had higher values, and all new compositions exhibited a microstructure of 100% pearlite.
2.3 Organizational observation and performance testing methods
Multiple rail sections were analyzed in terms of microstructure and rail performance independently. An analysis specimens were collected from the head, web, and foot of the rail for microstructural evaluation (Wróblewsk et al., 2023). The network ferrite was measured using optical microscope and was quantified at a ×100 magnification. Scanning electron microscopy (SEM) was used to study martensitic microstructure in the heat-affected zone by sampling 30 × 30 mm2 areas (shown in Figure 2a), while assessing the heat treatment response, the area fraction of martensite was determined at varying cooling rates.
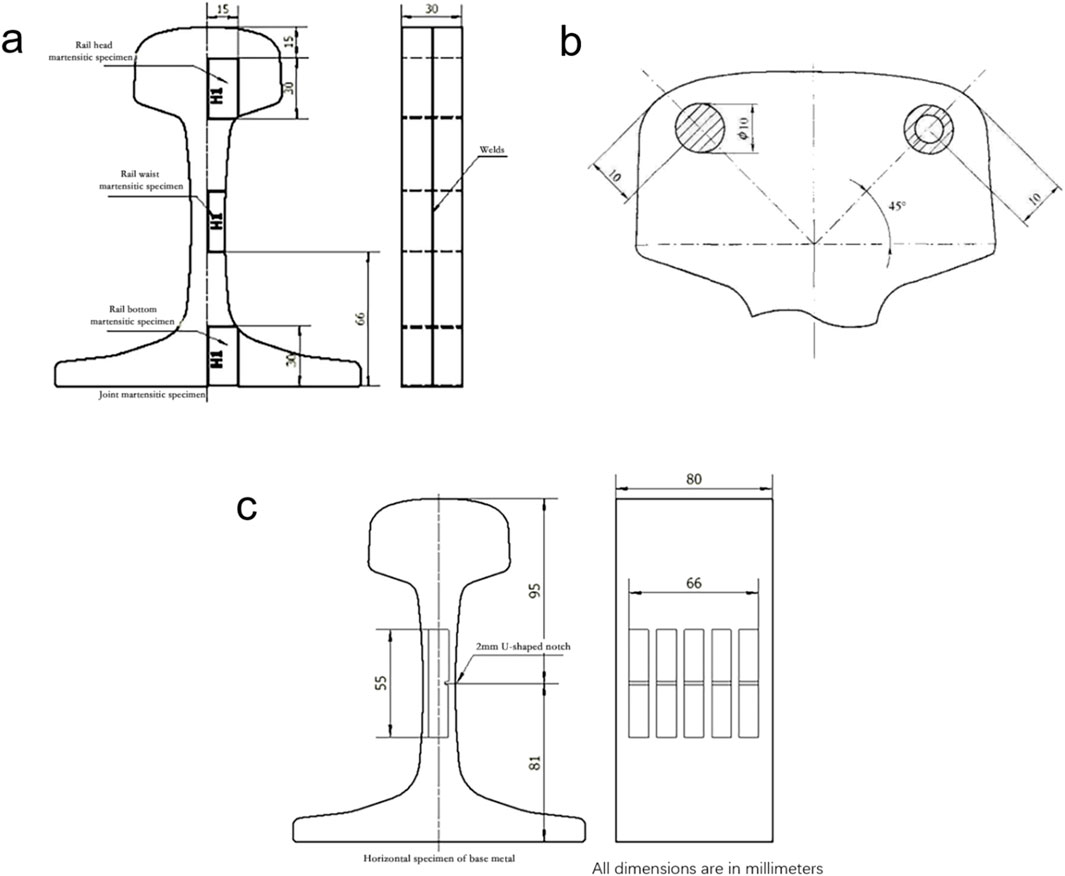
Figure 2. (a) Martensite sample sampling location. (b) Tensile test sampling position. (c) Sampling position of impact test. All dimensions are in millimeters.
All mechanical properties were evaluated through the standard tensile, impact, and hardness tests. The machining of the tensile specimens was done as shown in sampling diagram Figure 2b. Testing was done for yield strength (Rp0.2), ultimate tensile strength (Rm), and elongation (A%) (Gu and Wang, 2022). Systematic comparison between domestic and foreign rail steel was also carried out, as shown in Table 3. Impact testing was performed with vertical specimens taken as per Figure 2c with primary dependence on manganese content and impact toughness correlation. Examination of fracture surfaces was conducted using SEM to study the microcrack formation and propagation mechanisms.
2.4 Data analysis methods
Statistical methods were applied to study the connection between the chemical make-up and the microstructural features of the rail steels. The martensite formation was correlated to the carbon equivalent by fitting analysis which rendered a value of 66% correlation coefficient (Du et al., 2023). Manganese segregation analysis was conducted using energy dispersive spectroscope (EDS) on the SEM samples where segregation rates for both martensite and matrix regions were determined. The dependence of martensite content on manganese content was rather weakly correlated with 27%, while the correlation of base material with martensite manganese content was 66%, which is presented in Table 4 (Zhu et al., 2024). The analysis of segregation provided the result of the average, over ten rail steel grades, manganese segregation rate of 77%, which was much greater than the chromium segregation rate of 55%, thereby illustrating the considerable degree of manganese segregation during welding.
3 Results and discussion
3.1 Microstructure and mechanical properties of rail steel
This section presents a comprehensive evaluation of rail steel performance, including microstructure, mechanical properties, and comparisons between domestic and international rail grades. The investigation focuses particularly on the effects of the reduced manganese content then conventional RM steel.
3.1.1 Microstructural characteristics
Metallographic analysis (Figures 3a,b) reveals that both HM and RM steels exhibit a typical ferrite-pearlite mixed microstructure dominated by pearlite. It can be observed that small amounts of network ferrite are distributed along the austenite grain boundaries in the horizontal direction of the web. Statistical comparison shows that the total length of network ferrite in HM steel web is 0.20 mm and 0.35 mm at two measurement points, while RM steel shows 1.10 mm and 0.94 mm respectively, as shown in Table 5.
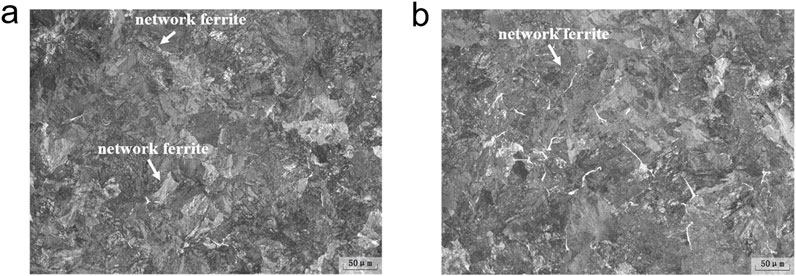
Figure 3. Metallographic structure of (a) HM rail and (b) RM rail. Network ferrite is indicated in the figure.
The network ferrite distribution across various rail grades reveals significant variations between domestic and international rails, as shown in Table 6. Domestic U71Mn rails exhibit substantially higher network ferrite content compared to international counterparts, particularly in the web region. The total network ferrite content in Angang rails reached 43.9 mm, while Japanese 350 grade rails showed only 0.16 mm. This high network ferrite content in domestic rails may lead to misjudgment during ultrasonic testing and requires particular attention in quality control.
The distribution of network ferrite content among different rail manufacturers is visually presented in Figure 4, which reveals several critical patterns. In the web region, domestic manufacturers consistently show elevated network ferrite levels, with Angang reaching 30.0 mm, followed by Wuhan (14.7 mm) and Baotou (13.7 mm). This is in stark contrast to international manufacturers, where web region values remain below 5 mm for Voestalpine DO350 and under 0.25 mm for both French and Japanese rails. This pattern is also evident, though less pronounced, in the head and foot regions. The total ferrite content data clearly demonstrates a systematic difference between domestic and international manufacturing processes, with domestic rails showing total values from 25.8 to 43.9 mm compared to international values consistently below 5 mm.
The influence of manganese content on microstructural evolution demonstrates a quantifiable dual-mechanism effect, as evidenced by comprehensive analysis of rail steels with varying manganese contents (Table 7). When the manganese content was reduced from 1.03% to 0.94%, network ferrite distribution showed remarkable improvement across all rail sections. Most notably, in the web region, network ferrite length decreased from 0.94 mm to 0.35 mm, representing a 63% reduction. This improvement extends to both head and foot regions, with reductions from 1.10 mm to 0.20 mm and 0.43 mm–0.15 mm respectively.
The correlation between manganese content and microstructural features is further validated by comparative analysis of international rail grades. Japanese 350 grade rails, with the lowest manganese content (0.81%), exhibited minimal network ferrite formation (web: 0.035 mm), while Angang rails with higher manganese (1.05%) showed significantly more network ferrite (web: 30.0 mm). This relationship can be attributed to two primary metallurgical mechanisms. First, as an austenite-stabilizing element, reduced manganese content diminishes austenite stability at grain boundaries, thereby suppressing network ferrite formation. Second, lower manganese levels result in modified inclusion characteristics, transitioning from predominantly MnS-type (A-type, grade 2) in conventional rails to silicate-type (C-type, grade 2.5) inclusions in optimized compositions, effectively reducing ferrite nucleation sites.
The positional variation in network ferrite distribution demonstrates a consistent pattern across all studied compositions, with the web region consistently showing higher concentrations compared to head and foot regions. This systematic variation correlates with local cooling rate differentials during the manufacturing process, as evidenced by the preservation of this pattern even in optimized compositions, albeit at reduced absolute levels.
The regional variation in network ferrite distribution follows a consistent pattern across all manufacturers, with the highest concentrations typically found in the web region, followed by the foot and head regions. This distribution pattern suggests that the formation of network ferrite is influenced by both chemical composition and cooling conditions during manufacturing. The significantly lower network ferrite content in international rails, particularly in the web region, indicates potential differences in processing parameters and composition control that could be adopted to improve domestic rail quality.
3.1.2 Mechanical properties
Tensile testing results demonstrate that while domestic rails maintain good ductility, their strength properties generally fall below international standards. As shown in Table 8, HM rail achieved a tensile strength of 931 MPa with 15% elongation, showing a balanced combination of strength and ductility. However, international rail grades consistently demonstrated superior strength properties, with Voestalpine rails reaching 1,239 MPa tensile strength and French rails maintaining strength levels above 1,200 MPa.
Impact toughness testing revealed significant improvements in the modified composition. As detailed in Table 9, HM rail achieved an average impact energy of 8.7 J, representing a 65% improvement over the RM rail’s 5.28 J. This enhancement correlates with the fracture morphology analysis, which shows that the micro-crack length in HM steel (42.6 mm) is significantly shorter than that in RM steel (71.0 mm). The improvement is mainly attributed to the reduced MnS inclusion content, which serves as heterogeneous nucleation sites for cracks.
Hardness measurements demonstrated that the optimization of chemical composition maintained adequate hardness levels while improving other properties. As shown in Table 10, HM rail showed a slightly higher average hardness of 23.3 HRC compared to RM rail’s 22.0 HRC, indicating that the reduction in manganese content did not compromise wear resistance. The consistency in hardness values across different positions suggests uniform microstructural development throughout the rail section.
3.1.3 Performance optimization analysis
The comprehensive analysis indicates that composition optimization through manganese reduction has achieved several significant improvements in rail steel performance. The reduced network ferrite content contributes to more uniform microstructure distribution throughout the rail section, particularly evident in the web region where the content decreased from approximately 1.0 mm–0.3 mm length. This microstructural refinement, combined with the reduction in MnS inclusion content, has led to notable improvements in mechanical properties.
The enhanced impact toughness, demonstrated by a 65% increase in impact energy from 5.28 J to 8.7 J, represents a significant advancement in material performance. This improvement is further validated by the reduced micro-crack length in impact specimens, decreasing from 71.0 mm to 42.6 mm. The maintenance of hardness levels around 23 HRC ensures that wear resistance properties remain uncompromised despite the reduction in manganese content.
However, comparison with international rail grades reveals areas for potential improvement, particularly in terms of tensile strength. While domestic rails demonstrate good ductility with elongation values around 15%, the tensile strength levels remain approximately 200–300 MPa below those of advanced international grades. This gap in strength properties, combined with the successful optimization of other performance metrics, suggests a clear direction for future development in domestic rail steel manufacturing processes.
These findings provide valuable insights for further optimization of chemical composition and processing parameters. The demonstrated success in reducing network ferrite content and improving impact toughness through manganese content optimization establishes a foundation for future developments aimed at achieving comprehensive performance improvements in domestic rail steel production.
3.2 Martensitic transformation behavior
The martensitic transformation in the heat-affected zone has a decisive influence on the performance of welded joints. Quantitative analysis of the martensite content in different rail steels under various cooling conditions reveals the intrinsic relationship between martensite transformation behavior, chemical composition, and process parameters.
Software simulation using JMATpro was conducted to analyze the weldability of U71Mn, U75V, and four experimental compositions. Analysis showed that experimental composition 202109–1 achieved a lower carbon equivalent compared to standard U71Mn, while maintaining 100% pearlitic microstructure. The CCT curves obtained through simulation (Figure 5) demonstrated systematic shifts with varying chromium content, showing a rightward displacement of approximately 2 s with increasing Cr levels.
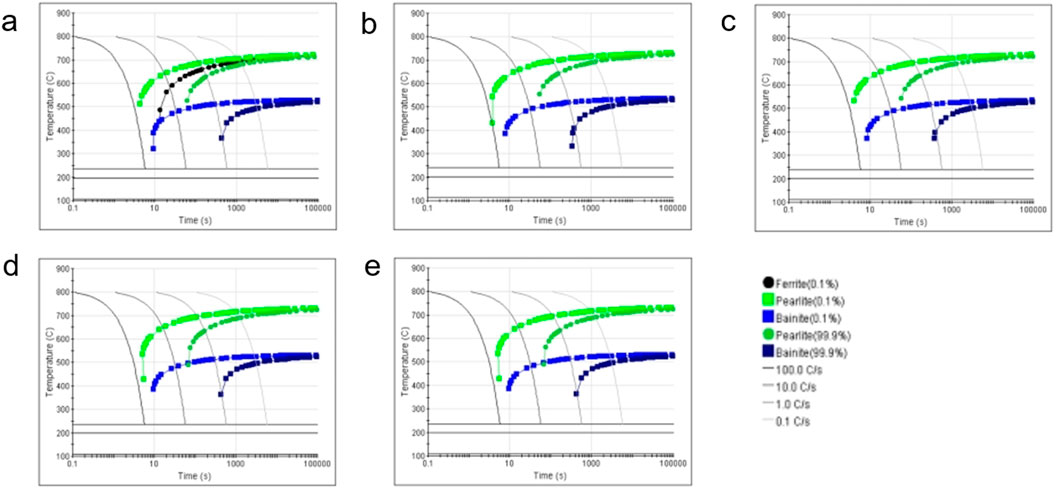
Figure 5. CCT curves of rails with different Cr contents: (a) U71Mn, (b) 202109–1, (c) 202109–2, (d) 202109–3 and (e) 202109–4.
As shown in Table 11 and Figures 6, 7, the martensite content increases significantly with increasing cooling rate and exhibits distinct differences among rail steel grades. Under the same cooling conditions, the martensite content from highest to lowest is as follows: Pangang U71Mn, Angang U71Mn, Voestalpine DO350, French HY260, French HY350, and Japanese R350.
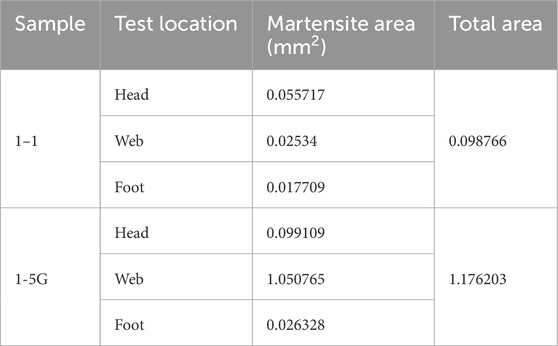
Table 11. Distribution of martensite content in different regions of the welded joint heat affected zone.
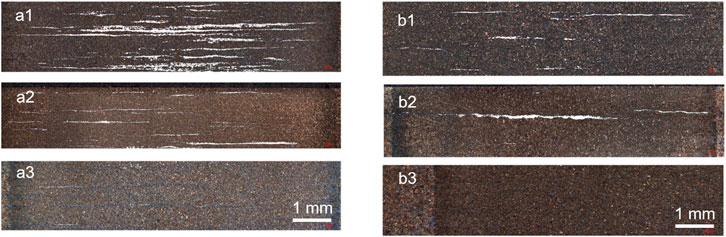
Figure 7. Photograph of the metallographic structure of Pangang U71Mn rail: (a1) Rapid cooling. (a2) Medium-speed cooling. (a3) Slow cooling and the YH350 rail in France: (b1) Rapid cooling. (b2) Medium-speed cooling. (b3) Slow cooling.
Further analysis reveals that the tendency for martensite formation has a strong correlation with the carbon equivalent. The higher the carbon equivalent, the greater the driving force for martensitic transformation and the higher the volume fraction of martensite. Statistical analysis indicates that the correlation coefficient between carbon equivalent and martensite content is as high as 66%, which is significantly stronger than the correlation with the single alloying element manganese content (27%). This suggests that when assessing the martensite tendency of rail welded joints, the combined effect of various alloying elements should be comprehensively considered, and using the carbon equivalent as a criterion is more reasonable.
The synergistic effects between alloying elements demonstrate significant influence on microstructural evolution and phase transformation characteristics. Statistical analysis of elemental interactions reveals complex relationships governing martensite formation and segregation behavior. The manganese segregation rate reaches 77% compared to chromium at 55%, indicating a strong tendency for manganese to form MnS inclusions. More significantly, the carbon equivalent exhibits a robust correlation with martensite content (R = 0.66), while manganese content alone shows a weaker correlation (R = 0.27), suggesting that manganese primarily influences phase transformation through modifying carbon activity rather than direct effects.
Systematic investigation of transformation behavior under controlled cooling conditions provides crucial insights into the martensite formation mechanisms. Under rapid cooling conditions (2.4°C/s), specimens with higher carbon equivalent (Ceq = 2.28) developed 3.69% martensite, while those with lower carbon equivalent (Ceq = 1.86) formed only 0.05% martensite. CCT curve analysis reveals a systematic rightward shift of approximately 2 s with increasing chromium content, directly impacting transformation kinetics. Local composition analysis demonstrates significant manganese enrichment in martensitic regions (2.14%) compared to the matrix (1.17%), confirming the critical role of compositional segregation in determining local hardenability.
The optimization of silicon and aluminum contents (Si = 0.33%, Al = 0.003%) resulted in superior microstructural homogeneity, as evidenced by quantitative metallography. These relationships are clearly illustrated in Supplementary Figure S1. It is worth noting that the martensite content in welded joints exhibits distinct spatial distribution characteristics. The martensite content in the rail web region is generally higher than that in the rail head and foot regions, mainly due to the relatively faster cooling rate and more severe composition segregation in the web region. EDS analysis shows that the average segregation rate of manganese is as high as 77%, significantly higher than that of chromium (55%), indicating that manganese preferentially segregates and has a greater influence on local hardenability.
The modified chemical compositions, particularly through manganese reduction and chromium addition, produced several significant effects on weldability. The lower manganese content reduced segregation tendency during welding, while the carefully controlled chromium additions helped maintain adequate hardenability without promoting excessive martensite formation.
In summary, the martensitic transformation behavior is closely related to the carbon equivalent of the rail steel and is significantly influenced by welding process parameters (such as cooling rate) and composition segregation. In optimizing the performance of welded joints, the martensite structure should be regulated through rational composition design and process control to avoid brittle fracture caused by excessively high local hardness.
3.3 Formation mechanism and control of gray spots in welded joints
Gray spots remain a critical quality concern in flash-welded joints. Macroscopic examination reveals that these defects appear as elliptical smooth regions with a slightly darker surface compared to the surrounding fracture surface, as shown in Figure 8. These defects exhibit a characteristic distribution pattern, predominantly concentrated within 30 mm from the rail foot edges. Statistical analysis of 50 welded joints reveals that approximately 65% of gray spots occur in the foot region, 28% in the web region, and only 7% in the head region, with an average gray spot size of 6.8 ± 0.5 mm in length and 1.0 ± 0.1 mm in width.
The formation of gray spots involves complex chemical reactions during the welding process. High-speed photography analysis (Figure 9) reveals that during continuous flash welding of the rail web, void formation occurs through three distinct stages: electromagnetic explosion, metal droplet ejection, and void formation. In the initial stage, electromagnetic forces expel metal from the contact interface at temperatures exceeding 1,500°C. The chemical reactions proceed according to the following sequence:
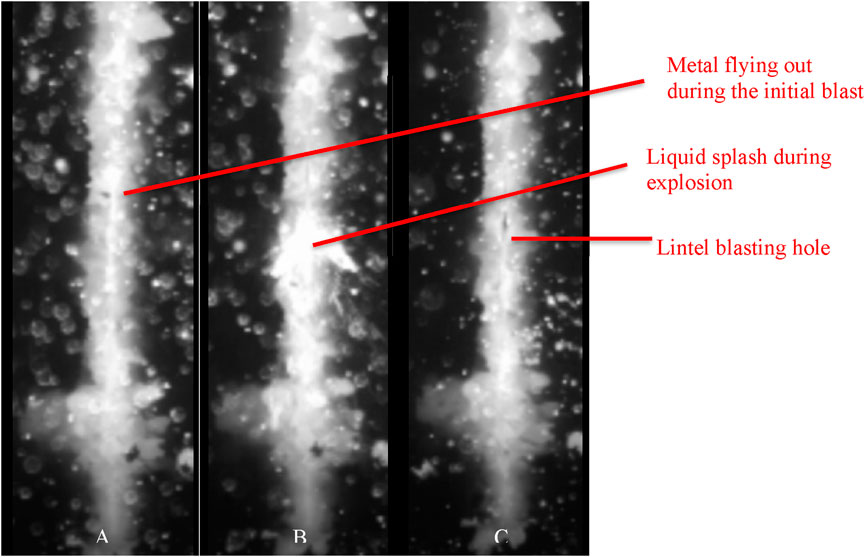
Figure 9. The process of cavity formation by the blasting of the rail waist lintel during continuous flash under high-speed photography. (A) Metal flying out during the initial blast. (B) Liquid splash during explosion. (C) Lintel blasting hole.
Chemical analysis of gray spot regions shows elevated concentrations of manganese (2.14% ± 0.15%), silicon (1.58% ± 0.12%), and oxygen (0.86% ± 0.08%) compared to the surrounding matrix. The spatial distribution of these elements varies systematically across different regions of the weld, as detailed in Table 12. The edge zones consistently show higher manganese concentrations (2.23% ± 0.16%) compared to the center zones (1.89% ± 0.13%), indicating preferential segregation during the welding process.
The spatial distribution of key elements involved in gray spot formation was further investigated using EDS mapping. As shown in Figure 10, manganese, silicon, and oxygen exhibit clear concentration gradients across different regions of the weld. The edge zones consistently show higher manganese concentrations compared to the center zones, corroborating the quantitative EDS results presented in Table 12. This visual evidence strengthens the understanding of preferential manganese segregation as a driving force behind gray spot formation in flash-welded rail joints.
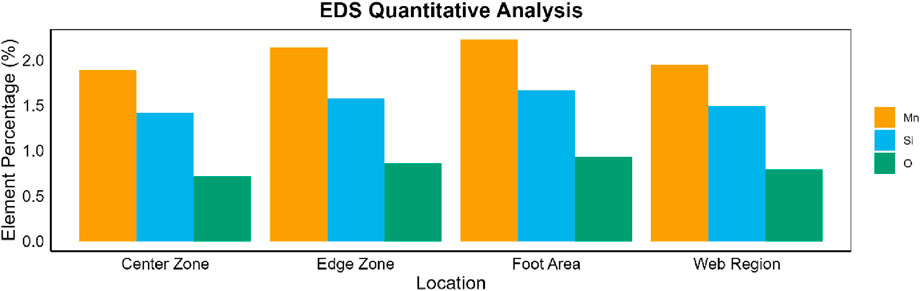
Figure 10. EDS mapping results demonstrating the spatial distribution of manganese (Mn), silicon (Si), and oxygen (O) across different regions of a flash-welded rail joint containing gray spots. The edge zones exhibit higher concentrations of these elements compared to the center zones, supporting the quantitative EDS findings and the proposed mechanisms of gray spot formation.
Manganese plays a dual role in gray spot formation. First, dissolved manganese in the steel matrix readily oxidizes at elevated temperatures, forming MnO which subsequently reacts with SiO2 to form complex silicates. Second, pre-existing manganese sulfide inclusions decompose during welding, releasing additional manganese that contributes to oxide formation. This dual-source mechanism explains why reducing the bulk manganese content by 0.1% (from 1.03% to 0.94%) resulted in a significant 35% reduction in gray spot frequency.
The investigation revealed that void formation typically occurs within approximately 1.5 s of initial flash formation. These voids, measuring 6–8 mm in length and approximately 1 mm in width, provide channels for atmospheric interaction with the hot metal surface. The subsequent rapid closure of these voids by the movement of the dynamic frame effectively seals the silicate inclusions within the weld interface. The process occurs most frequently in regions experiencing higher thermal gradients and mechanical constraints, explaining the preferential formation near the rail foot edges.
Experimental trials with reduced manganese content demonstrate a clear correlation between bulk manganese content and gray spot formation. Statistical analysis of weld cross-sections shows that reducing manganese content from 1.03% to 0.94% decreases the average number of gray spots per weld from 8.3 to 5.4, with a corresponding reduction in average spot size from 7.2 ± 0.6 mm to 6.5 ± 0.5 mm. This improvement is attributed to both reduced manganese availability for oxide formation and decreased manganese sulfide inclusion content in the base material.
The study concludes that effective control of gray spot defects requires a multi-faceted approach combining composition control and process optimization. By rationally designing the composition (particularly reducing manganese and silicon content), improving surface preparation processes, optimizing flashing parameters (such as shortening the flashing time and increasing current density), and maintaining adequate forging pressure, gray spot formation can be significantly suppressed. These findings provide practical guidelines for improving the quality and reliability of flash-welded rail joints in high-speed railway applications.
3.4 Distribution characteristics and formation mechanism of rail foot micro-cracks
Rail foot micro-cracks are another typical defect in flash-welded joints. Metallographic analysis reveals that micro-cracks are primarily distributed on both sides of the rail foot, exhibiting various morphologies along the weld interface (Figures 11, 12a,b. These defects are most concentrated in the overheated zone, 0.2–0.8 mm away from the weld center, and frequently occur within 0–5 mm below the rail foot surface. Statistical analysis of 50 welded joints reveals that approximately 65% of micro-cracks occur in the foot region, 28% in the web region, and only 7% in the head region, with an average micro-crack size of 6.8 ± 0.5 mm in length and 1.0 ± 0.1 mm in width.
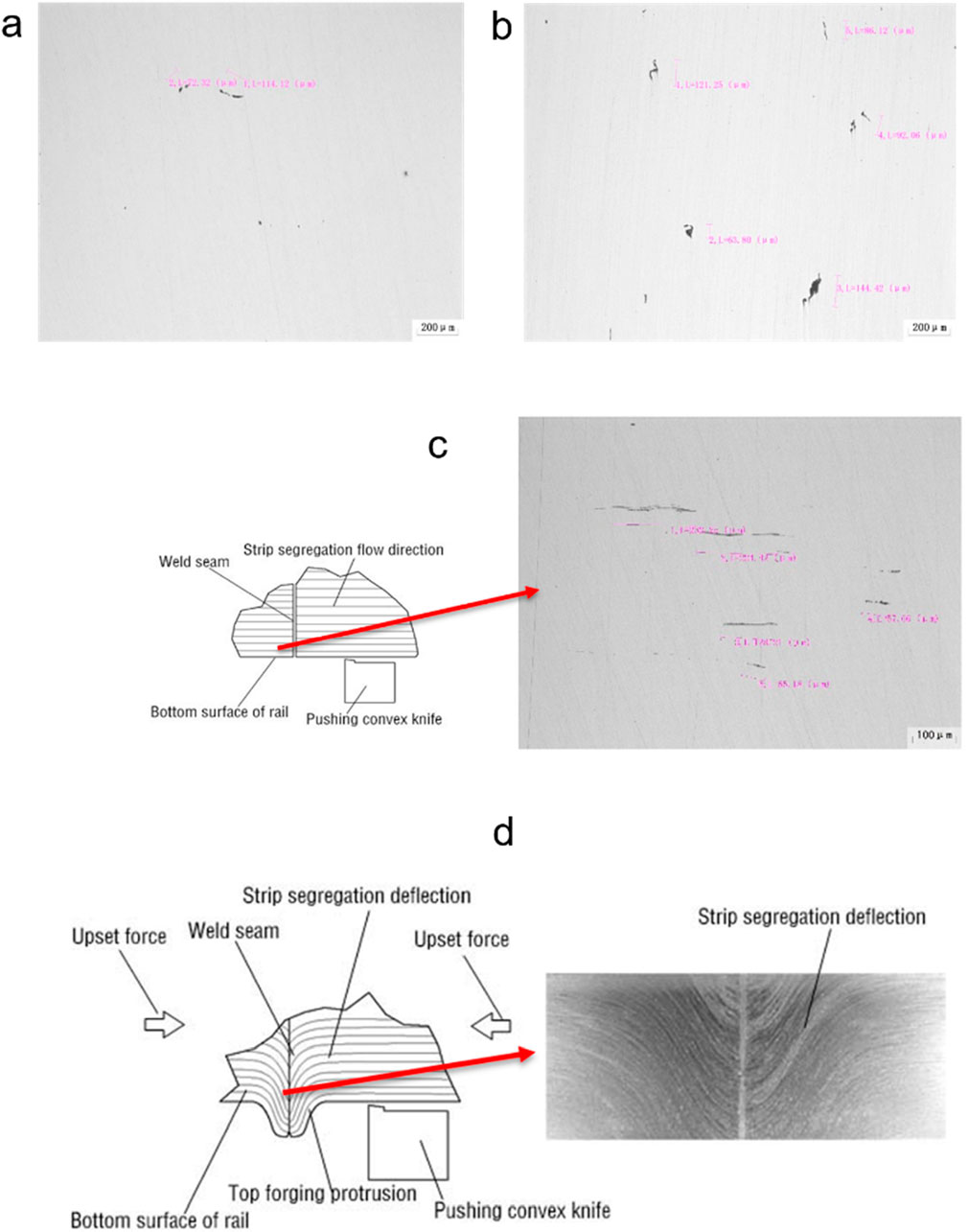
Figure 12. (a) Microcrack morphology on the bottom surface of a mobile flash rail (Y3-B# specimen). (b) Microcrack morphology at the bottom of a fixed flash welding rail. (c) Schematic diagram of the distribution of inclusions during welding. (d) Schematic diagram of the distribution of inclusions after top forging at the end of welding.
The formation mechanism of these micro-cracks is intimately linked to the deformation behavior of MnS inclusions during the welding process. In the base material, MnS inclusions exhibit a horizontally elongated banded morphology, as shown in Figure 12c where the left image shows the schematic distribution of inclusions, and the right image presents the actual metallographic observation of the banded structure. During flash welding, these inclusions undergo a two-stage deformation process. The first stage involves bending deformation during the upsetting stage, causing joint bulging as illustrated in Figure 12d. The continuous arrow lines in the schematic diagram demonstrate how the originally horizontal banded structure gradually deforms following the plastic deformation of the joint region during the upset process. The actual microstructural observations confirm this systematic reorientation of MnS inclusions in response to the applied thermomechanical forces during welding.
Following the upsetting stage, the trimming tool moves from the right end to the left end of the joint to remove the flash upset. This operation induces a second deformation in the surface-adjacent banded structure, as depicted in Figure 13a, where the near-surface banded structure bends in the trimming direction, creating conditions conducive to micro-crack formation. Figure 13b illustrates how MnS inclusions at the ends of the high-temperature overheated zone experience stress state changes during trimming, leading to crack formation along the inclusion direction due to the release of stress perpendicular to the surface. The greater deformation angle on the left side of the weld results in a higher concentration of micro-cracks in this region.
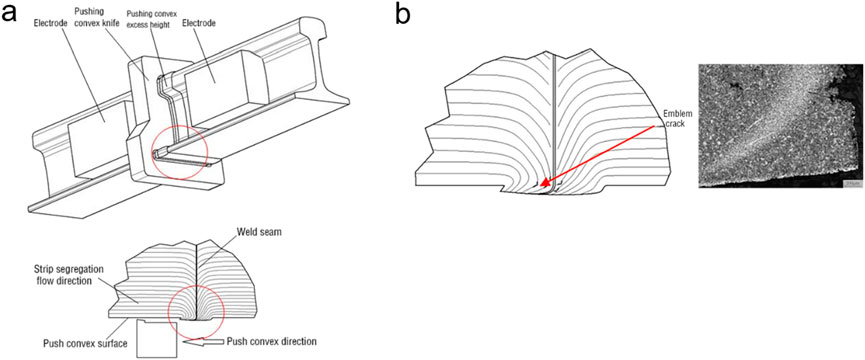
Figure 13. (a) Schematic diagram of the distribution of inclusions after the welding jacking is completed. (b) Distribution of inclusions and microcracks in welded joints.
Fatigue testing provides important insights into the practical implications of these micro-cracks. Analysis of four flash-welded joints that passed standard fatigue testing (2 × 106 load cycles according to TB/T 1632.2-2014) revealed the presence of micro-cracks in all specimens. This suggests that while micro-cracks are prevalent, they can be tolerated to a certain extent by the joint’s service performance. Statistical analysis of these fatigue-tested joints showed varying degrees of micro-crack severity, with some specimens exhibiting up to 49 cracks with maximum lengths reaching 571 μm, yet still maintaining acceptable fatigue resistance.
The analysis indicates that micro-cracks are inherent in flash-welded joints due to the presence of MnS inclusions in rail steel. These defects typically distribute in the overheated zone 0.2–0.8 mm from the weld center and within 0–5 mm of the trimmed surface. While complete elimination of micro-cracks may be difficult, their impact can be minimized through several approaches: reducing MnS inclusions in the rail steel, modifying the trimming strategy by increasing the trimming allowance, optimizing the geometric dimensions of the rail foot (such as transition fillets), and improving the precision machining quality and surface roughness of the rail foot. The presence of micro-cracks, while persistent, does not necessarily compromise joint integrity when maintained within acceptable limits through proper material and process control.
4 Conclusion
The optimization of manganese content in U71Mn rail welded joints has brought to light a number of findings which are pertinent to the high-speed rail industry. The methodical decrease in manganese from 1.03% to 0.94% was shown to be beneficial for practical performance. The network ferrite content of the heat-affected zone is decreased by 70%. The impact toughness showed a 65% improvement, reaching the value of 8.7 J and the hardness in HRC was satisfactory at 23.3 as opposed to the standard of 22.0.
The interrelation of chemical constituents and joint integrity is established using microstructural analyses. Evaluation of the data showed that carbon equivalent, rather than solely manganese content, demonstrates a stronger correlation (R2 = 0.436) with the tendency for martensite formation. The average tungstate segregation value of 77% greatly surpasses that of chromium (55%), which is important for segregation control. Remarkably, the occurrence of grey spots in flash-welded joints was shown to be directly proportional to the amount of manganese, which was reduced by 35% with optimized composition. The amount of ferrous martensite in the heat affected zone shows stronger association with the carbon equivalent (66%), compared to manganese, with for enabling control of transformation behavior (27%). Analyzed failures of tested joints under loading reveal the existance of the micro cracks. The risk to the failure of joint integrity can be mitigated by altering the composition to achieve a satisfactory result of 2 × 106 normalized cycles of loading tests.
These observations provides important direction on the engineering aspects of high-speed rail construction and development. The reduced manganese content of 0.94% serves as a compromise and is weldable while possessing desirable mechanical properties. The remarkable reduction of network ferrite spinodal decomposition greatly increases the reliability of ultrasonic testing, resolving a quality control problem in rail inspections. The increased impact toughness suggests the material is more resistant to severe dynamic loads, which are commonplace in high-speed rail operating conditions. Additionally, the demonstrated correlation between composition and microstructural changes justifies further refinement of rail steel chemistry and processing parameters, which constitutes constructive groundwork towards the subsequent steps in the pilot studies of high-performance rail materials.
Our work provides a systemetic criterion for the evaluation of the microstructure and the mechanical property from different material composition. Future reseach and engineering development should be advised by the reported results in this work, that further reduced and the optimized manganese content should be considered.
Data availability statement
The original contributions presented in the study are included in the article/supplementary material, further inquiries can be directed to the corresponding author.
Author contributions
CW: Writing – review and editing, Writing – original draft.
Funding
The author(s) declare that no financial support was received for the research and/or publication of this article.
Conflict of interest
Author CW was employed by China Academy of Railway Sciences Corporation Limited.
Generative AI statement
The author(s) declare that no Generative AI was used in the creation of this manuscript.
Publisher’s note
All claims expressed in this article are solely those of the authors and do not necessarily represent those of their affiliated organizations, or those of the publisher, the editors and the reviewers. Any product that may be evaluated in this article, or claim that may be made by its manufacturer, is not guaranteed or endorsed by the publisher.
Supplementary material
The Supplementary Material for this article can be found online at: https://www.frontiersin.org/articles/10.3389/fmats.2025.1597601/full#supplementary-material
References
Du, L., Wang, Z., and Gu, T. (2023). A coupled thermo-mechanical cohesive zone model for strain rate-dependent fracture of hat-shaped specimens under impact. Eng. Fract. Mech. 289, 109382. doi:10.1016/j.engfracmech.2023.109382
Fu, Y., Liu, Q., Lv, Y. B., Zhang, M. L., Xin, J. J., Zhu, M. L., et al. (2024). Microstructural and chemical dependences of fracture toughness in stainless steel welds at 4.2 K. Eng. Fract. Mech. 305, 110207. doi:10.1016/j.engfracmech.2024.110207
Ghazanfari, M., and Tehrani, P. H. (2021). Increasing fatigue crack initiation life in butt-welded UIC60 rail by optimization of welding process parameters. Int. J. Fatigue 151, 106367. doi:10.1016/j.ijfatigue.2021.106367
Gu, T., and Wang, Z. (2022). A strain rate-dependent cohesive zone model for shear failure of hat-shaped specimens under impact. Eng. Fract. Mech. 259, 108145. doi:10.1016/j.engfracmech.2021.108145
Han, Z. Y., Wang, H. H., Wang, W. J., Zhang, S. Y., Lin, D. M., Wang, Y., et al. (2024). The correlation between material deformed microstructure and rolling contact fatigue crack propagation of U71Mn rail when matching with CL60 wheel. Tribol. Int. 200, 110069. doi:10.1016/j.triboint.2024.110069
Kendall, O., Paradowska, A., Abrahams, R., Reid, M., Qiu, C., Mutton, P., et al. (2022). Residual stress measurement techniques for metal joints, metallic coatings and components in the railway industry: a review. Materials 16 (1), 232. doi:10.3390/ma16010232
Kuchuk-Yatsenko, S. I., Didkovsky, A. V., Shvets, V. I., Rudenko, P. M., and Antipin, E. V. (2016). Flash-butt welding of high-strength rails of nowadays production. Paton Welding J. 5 (6), 4–12. doi:10.15407/tpwj2016.06.01
Liao, T., Zhang, X., Yang, H., Zhou, P., and Chen, F. (2023). Microstructural evolution and micro-corrosion behaviour of flash-welded U71Mn joints as a function of post-weld heat treatment. Materials 16 (15), 5437. doi:10.3390/ma16155437
Liu, Z., Fan, C. L., Yang, C. L., Ming, Z., Lin, S. B., and Wang, L. P. (2023). Dissimilar welding of high nitrogen stainless steel and low alloy high strength steel under different shielding gas composition: process, microstructure and mechanical properties. Def. Technol. 27, 138–153. doi:10.1016/j.dt.2022.10.010
Ma, N., Cai, Z., Huang, H., Deng, D., Murakawa, H., and Pan, J. (2015). Investigation of welding residual stress in flash-butt joint of U71Mn rail steel by numerical simulation and experiment. Mater. and Des. 88, 1296–1309. doi:10.1016/j.matdes.2015.08.124
Mortazavian, E., Wang, Z., and Teng, H. (2022). Effect of heat treatment on microstructure and hardness of a worn rail repaired using laser powder deposition. Int. J. Transp. Sci. Technol. 11 (2), 406–422. doi:10.1016/j.ijtst.2021.05.004
Muttamara, A., Sommanat, J., Kanchanomai, C., and Viyanit, E. (2024). Comparative fatigue performance of decarburized surfaces in railway rails. Materials 17 (2), 290. doi:10.3390/ma17020290
Pang, Y., Grilli, N., Su, H., Liu, W., Ma, J., and Yu, S. F. (2022). Experimental investigation on microstructures and mechanical properties of PG4 flash-butt rail welds. Eng. Fail. Anal. 141, 106650. doi:10.1016/j.engfailanal.2022.106650
Pereira, H. B., Echeverri, E. A. A., Alves, L. H. D., and Goldenstein, H. (2022). Evaluation of the effect of heat input and cooling rate of rail flash-butt welding using finite element method simulation. Soldagem and Inspeção 27, e2701. doi:10.1590/0104-9224/si27.01
Porcaro, R. R., Faria, G. L., Godefroid, L. B., Apolonio, G. R., Cândido, L. C., and Pinto, E. S. (2019). Microstructure and mechanical properties of a flash butt welded pearlitic rail. J. Mater. Process. Technol. 270, 20–27. doi:10.1016/j.jmatprotec.2019.02.013
Ruijie, Z., Chunlei, Z., Bo, L., Xubiao, W., Xiaofeng, L., Yanguo, L., et al. (2023). Research progress on rolling contact fatigue damage of bainitic rail steel. Eng. Fail. Anal. 143, 106875. doi:10.1016/j.engfailanal.2022.106875
Saita, K., Karimine, K., Ueda, M., Iwano, K., Yamamoto, T., and Hiroguchi, K. (2013). Trends in rail welding technologies and our future approach. Nippon steel and sumitomo metal Tech. Rep. 105, 84–92.
Shen, M., Mei, L., Gong, F., Li, C., and Li, Q. (2024). Damage behaviour of rail flash-butt welding joints under controlled impact kinetic energy. Wear 552-553, 205435. doi:10.1016/j.wear.2024.205435
Su, Y., Li, W., Wang, X., Ma, T., Ma, L., and Dou, X. (2019). The sensitivity analysis of microstructure and mechanical properties to welding parameters for linear friction welded rail steel joints. Mater. Sci. Eng. A 764, 138251. doi:10.1016/j.msea.2019.138251
Wang, X., Zhang, Z., Zhao, Y., Hu, Z., and Li, X. (2024). Macroscopic morphology and properties of cobalt-based laser cladding layers on rail steel based on pulse shaping. Opt. and Laser Technol. 168, 109940. doi:10.1016/j.optlastec.2023.109940
Wróblewski, P., Niekurzak, M., and Kachel, S. (2023). Experimental studies of welded joints in structures subject to high impact vibrations using destructive and non-destructive methods. Materials 16 (5), 1886. doi:10.3390/ma16051886
Xue, H., Liu, S., Zhang, D., Xue, J., Zhang, W., Zheng, Z., et al. (2024). Effect of ultrasonic impact treatment with different impact energy and head shape on surface properties of U75V heavy rail. J. Mater. Eng. Perform. 33 (18), 9457–9466. doi:10.1007/s11665-023-08606-w
Yang, Y., Xin, Y., Chen, H., Liu, Z., Wang, B., Qiao, H., et al. (2024). Improving wear and corrosion resistance of U71Mn rail steel subjected to laser in-situ fabrication of Fe based Cr–V coatings. Wear 546, 205312. doi:10.1016/j.wear.2024.205312
Yi, Q., Liu, X., Wang, S., Zhao, W., Jiang, Z., Wang, W., et al. (2024). Failure mechanism and damage tolerance of turnout point rail in high-speed railway. Eng. Fail. Anal. 157, 107936. doi:10.1016/j.engfailanal.2023.107936
Zeng, P. Y., Zuo, C. G., Zhang, X. Y., and Li, W. (2024). Impact wear properties of dissimilar joints between bainitic frogs and pearlite rails. J. Iron Steel Res. Int. 31 (1), 275–287. doi:10.1007/s42243-023-01020-5
Zhang, B., He, B., and Wang, H. (2022b). Microstructural investigation and mechanical performance of laser cladding repaired bainite steel with AerMet100 steel. Surf. Coatings Technol. 440, 128498. doi:10.1016/j.surfcoat.2022.128498
Zhang, H., Li, C. A., and Zhu, Z. (2022a). Influence of CDFW process parameters on microstructure and mechanical properties of U75V rail steel welded joint. Metals 12 (5), 711. doi:10.3390/met12050711
Zhao, J., Pang, X., Fu, P., Wang, Y., Kang, G., Wang, P., et al. (2022). Dynamic constitutive model of U75VG rail flash-butt welded joint and its application in wheel-rail transient rolling contact simulation. Eng. Fail. Anal. 134, 106078. doi:10.1016/j.engfailanal.2022.106078
Keywords: U71Mn rail steel, flash welding, microstructure, mechanical properties, martensitic transformation
Citation: Wang C (2025) Effect of manganese content on microstructure and properties of welded joints of U71Mn rails. Front. Mater. 12:1597601. doi: 10.3389/fmats.2025.1597601
Received: 21 March 2025; Accepted: 23 June 2025;
Published: 16 July 2025.
Edited by:
Nitish Bibhanshu, Indian Institute of Technology Ropar, IndiaReviewed by:
Yuanqing Chi, Guangdong University of Technology, ChinaAshish Kumar Gupta, Oklahoma State University, United States
Copyright © 2025 Wang. This is an open-access article distributed under the terms of the Creative Commons Attribution License (CC BY). The use, distribution or reproduction in other forums is permitted, provided the original author(s) and the copyright owner(s) are credited and that the original publication in this journal is cited, in accordance with accepted academic practice. No use, distribution or reproduction is permitted which does not comply with these terms.
*Correspondence: Chenyang Wang, cWJlZjYwQDE2My5jb20=