- 1Functional Materials and Chemistry Research Group, Research Centre for Manufacturing and Materials (CMM), The Institute for Advanced Manufacturing and Engineering (AME), Coventry University, Coventry, United Kingdom
- 2Pillarhouse International Ltd., Chelmsford, United Kingdom
- 3GKN Automotive, Lohmar, Germany
- 4Faculty of Science and Engineering, Manchester Metropolitan University, Manchester, United Kingdom
- 5Micro Materials Ltd., Wrexham, United Kingdom
Diamond-like Carbon (DLC) coatings are well known for their use in protection against fretting wear due to their low friction and wear properties. DLCs are metastable, allowing them to graphitise under applied load to create a graphitic transfer layer which reduces friction. Their high intrinsic residual stresses also enable them to resist cracking effectively under fretting. Few studies have analysed the lubricated fretting performance of DLC coating systems. This work focuses on a series of lubricants with different additives and friction modifiers to explore their effects. This study analyses the performance of a DLC coating system (a-C:H) applied to hardened M2 tool steel and 316L stainless steel under loads of 20 and 40 N under dry fretting and lubricated fretting conditions. Lubricated uncoated substrates were also analysed for comparison. The counterfaces used were 10 mm diameter 52,100 steel balls. The lubricants tested included a base oil and a fully formulated oil, with and without the addition of MoDTC. Gross slip fretting was achieved using a bespoke electrodynamic shaker unit. Nanoindentation was employed to measure the mechanical properties of the coatings and substrates. Contact pressure and lubricant type had significant effects on the running-in behaviour of the coatings. Increased contact pressure led to instability in the running-in period. Lubrication reduced the dissipated energy in the contact, thereby decreasing wear. However, fully formulated oils and those containing MoDTC performed worse due to their higher viscosity, which impacted oil entrainment in the contact area. This study provides insights into the lubricated fretting performance of DLC coatings showing that these coatings can perform well, with the potential for further improvements with optimisations to the lubricant to the system. Performance improvements can be gained in automotive components such as high pressure bearings and gears.
1 Introduction
Fretting occurs due to small amplitude oscillatory wear between two surfaces in contact, typically under vibration (Waterhouse, 1976; 1984). Fouvry et al. analysed palliatives to fretting damage and recommended foremost the modification of the interface to reduce fretting contact loading but when this cannot be accommodated, the introduction of residual compressive stresses (protection against cracking) and the application of a liquid lubricant (Fouvry et al., 2006).
Diamond-like carbon coatings (DLC) are metastable amorphous carbon coatings with properties varying dependent upon the sp2/sp3 ratio, level of hydrogenation and presence of dopants (Robertson, 1992; 2002; Pierson, 1993; Grill, 1999; Lifshitz, 1999; Hainsworth and Uhure, 2007; Donnet and Erdemir, 2008). Generally, DLCs are hard chemically inert and exhibit low coefficients of friction (Grill, 1993; 1999; Hainsworth and Uhure, 2007). The low friction generally attributed to DLC coatings is typically applicable to hydrogenated DLCs. Their coefficient of friction rises with humidity (from 0.001–0.02 to 0.05–0.2). Hydrogen-free DLC has a high coefficient of friction in dry conditions (0.4–0.7), which reduces to the levels of hydrogenated DLC with high humidity (Ronkainen and Holmberg, 2008).
DLCs typically experience large compressive residual stresses however this varies with the substrate bias applied during deposition (Zhang et al., 1999; Pauleau, 2008). These high compressive residual stresses can protect against cracking phenomena as in the work of Fouvry et al., the further presence of the protective coating also adds protection so long as the substrate is not exposed (Fouvry et al., 2006).
Previous work has analysed oil lubrication in fretting contacts (against steel) with varying viscosity of oil and stroke length. The viscosity of the lubricant was noted to affect the coefficient of friction as a product of stroke length (and resulting fretting regime). Lower viscosity oil resulted in an overall lower coefficient of friction with smaller peak in the stick-slip region. This was attributed to the lubricant’s ability to penetrate and shield the fretting zone and inhibit oxygen access. The generation of surface damage and debris aided the lubricant entrainment at higher stroke lengths and a reasonable correlation was found between coefficient of friction and wear (Shima et al., 1997). Other work on the oil properties and their effect on the fretting wear of steel found no significant correlation between fretting wear volume and oil viscosity; the oil viscosity and its influence on the fretting wear is dependent on the boundary lubrication properties of the oil. In general, the presence of any oil at the interface decreases the fretting wear drastically (Neyman, 1992). In investigating the efficiency of worm gearboxes, Skulić et al. found that increasing the lubricant viscosity increased efficiency by 1%–2%. Furthermore, the material pairings were found to be extremely important by maintaining an oil film, resulting in better tribological performance (Skulić et al., 2022).
Kalin and Vizintin analysed the performance of DLC coatings under oil-lubricated fretting conditions (Kalin and Vižintin, 2006). The wear of the DLC/DLC and steel/DLC contacts in the fretting regime was 3–10 times lower as the DLC in the contact eliminated the adhesive wear and debris generation. With an increase in stroke length approaching sliding wear, the wear rate for the various contacts became similar and was dependent on the lubrication conditions. The friction of DLC/DLC contacts was noted to be two times lower due to the absence of adhesion and debris interlocking, the transition to gross-slip from partial slip promotion lubrication effects and low conformity between the self-mated DLC contacts resulting in lower real contact area and friction. Kalin and co-workers also reviewed the boundary lubrication mechanisms of DLC coatings (Kalin et al., 2008). Noted findings were that non-doped DLC coatings can react with different additives such as friction modifiers but the contact conditions and temperature plays an important role in the reactions. Hydrogen content in the DLC coatings significantly affected their tribological performance when interacting with additive-containing oils; MoDTC and ZDDP-containing oils were noted to have low friction with self-mated DLC contacts. The particular lubricating mechanisms were noted to not be understood but their beneficial effects were clear. Yue et al. also investigated the fretting behaviours of self-mated DLC contacts, hydrogenated DLC was found to have a lower friction coefficient but a larger wear volume when compared with Cr doped DLC. Adhesion was noted to contribute to the wear at the centre of the contact surface, and abrasive wear was noted at the contact edge. The generation of a third body layer occurred after run-in, this layer was gradually graphitised under fretting (Yue et al., 2023).
Mechanical properties and their derived ratios are a key metric in predicting performance in the tribology of dry contacts. H/E and H3/E2 are the most common ratios seen in literature and can be used to predict frictional performance via interfacial and ploughing components (Ni et al., 2004; Beake et al., 2013; Beake, 2022), elastic strain to break (Leyland and Matthews, 2000) and contact yield pressure respectively (Chen et al., 2019). For thin films such as DLC, nanoindentation is a key methodology for its ability to measure the properties of the coating independently of the substrate, so long as substrate effects are minimised (Beake et al., 2015; ISO, 2015; McMaster et al., 2023; 2023).
The synergistic interactions between MoDTC and DLC coatings has been previous studied by multiple authors. Kosarieh et al. investigated the effect of MoDTC friction modifier on DLC and the wear mechanisms of the coating (Kosarieh et al., 2013; 2016). High concentrations of the friction modifier was found to promote high wear of the coating but did reduce friction in sliding wear. The interaction with the iron counterface was found to accelerate wear of DLC with a proposed mechanism of acting as a catalyst for oxidation and/or dehydrogenation of the coating. De Feo et al. also explored the interaction of MoDTC with DLCs finding evidence that a MoS2 film is formed on the steel counterface which can then react with the DLC breaking the carbon network down eventually to the formation of a molybdenum carbide layer increasing the friction and wear rate (De Feo et al., 2016). Ueda et al. found that the presence of further additives in the oil contributed to a reduction in the wear of the DLC coating (Ueda et al., 2021).
More recent work by Fu et al. analysed the fluid-lubricated tribological performance of DLC films under sliding and fretting conditions (Fu et al., 2018). The fluids were ionic liquids and multipli-alkylated cyclopentanes. Under sliding conditions, the friction-reducing and wear resistance of the DLC were increased with the fluids; the ionic liquids performed best due to the physical absorption of the ionic liquid film. In fretting partial slip, the two fluid categories performed better than in gross slip as the fluid molecules were purported to cause the propagation of fatigue cracks. The wear resistance of the DLC films was improved due to the interplay of the physical absorption of formed lubricant films and the tribofilm formed during fretting.
Zhuang et al. investigated the fretting performance of DLC and MoS2 under fluid lubrication (Zhuang et al., 2019). Ionic liquids and multiply-alkylated cyclopentanes were investigated once again in addition to silicon oil and perfluoropolyethers at different applied loads. The fretting behaviour of both coatings was improved with all four fluids at higher loads due to graphitisation and transfer film formation at all material surfaces. Fretting damage of the DLC films under fluid lubrication was attributed to abrasive wear. The fluids were noted to change the fretting running regime but this was dependent upon the specific fluid performance characteristics.
More recent works have focused on the incorporation of nanocomposites in lubricant oils (Mousavi et al., 2019; Mousavi et al., 2020; Mousavi et al., 2021; Mousavi et al., 2024; Mousavi and Zeinali Heris, 2020; Aghaei Sarvari et al., 2022; Bukvić et al., 2023). These studies have explored additives such as MoS2, MnO2, TiO2 and MWCNT finding that the incorporation of the nanoparticles increased viscosity of the oil and reduced the coefficient of friction and wear.
This study analyses the friction and dissipated energy of a hydrogenated DLC applied to 316 stainless steel and hardened M2 tool steel under base oil and fully formulated oil with and without molybdenum dialkyldithiocarbamate (MoDTC). Hydrogenation in DLC generally benefits tribological performance due to interaction with dangling hydrogen bonds (Ronkainen and Holmberg, 2008). Additionally, the deposition methodology of plasma enhanced chemical vapour deposition allows for the engagement of a magnetron sputtering target to dope the coatings with metallic elements or lighter elements such as silicon (Beake et al., 2021). The friction coefficient across the fretting cycles was analysed to determine the effectiveness of the various lubricants and any adverse effects caused by the MoDTC. As the majority of studies of tribological interactions of DLC with MoDTC take place under the full sliding regime, the aim of this work is to explore how the well the friction modifier MoDTC will perform in the contact conditions of gross-slip fretting where replenishment of the lubricant is affected due to the centre contact region of unexposed wear surfaces. This is in contrast to full sliding, where replenishment will occur with each cycle. A high contact pressure was used to accelerate the testing to allow for analysis of the tribological behaviour in fewer fretting cycles however is it allows for exploration of the friction modifier is at higher contact pressures. This study is novel due to the lack of investigations on the use of MoDTC in fretting conditions. The results of this work can be used to improve the performance of high contact pressure bearings and gears in the automotive industry.
2 Methodology
2.1 Substrate preparation
The substrates were 316L stainless steel (SS) and hardened M2 tool steel (HTS). Coupons were prepared from cylindrical steel bars (Ø = 25 mm), cut to a thickness of 6 mm. A circular grinding/polishing wheel was used to polish the samples with varying grades of silicon carbide paper to successively finer grades of grit. The grit sizes were 120, 300, 450, 600, 800 and 1,200. Following surface grinding, polishing was performed to obtain the optimal surface roughness (Ra = 0.01 μm). Verdutex and MicroFloc fibre polishing cloths were utilised with polycrystalline diamond suspension (9 μm and 3 μm with Verdutex and 0.25 μm with Microfloc) to give a mirror finish (McMaster et al., 2020; 2023).
2.2 Coating deposition
Coatings were deposited with the Hauzer Flexicoat 850 Physical Vapour (PVD) and plasma-assisted chemical vapour (PACVD) coating system located in the School of Mechanical Engineering at the University of Leeds.
The coating layer structures were a Cr adhesive layer, WC gradient layer and the top DLC. The deposition steps for the coating were as follows (McMaster et al., 2020; 2023):
i. Chamber heating
ii. Target cleaning
iii. Plasma surface etching
iv. Cr layer deposition
v. Cr/WC layer deposition
vi. a-C:H deposition
The DLC coating in this paper was a-C:H of the same type identified in previous work by McMaster et al. however the final deposition step (a-C:H deposition) was carried out for 360 min to give a thicker top DLC layer (McMaster et al., 2020; 2023). Further details can be found in those works.
2.3 Mechanical characterisation
Mechanical properties were determined by load-controlled partial load nanoindentation using a NanoTest Vantage system (Micro Materials, United Kingdom) with a Berkovich diamond indenter. This results in a depth-sensitive measurement of mechanical properties however surface extrapolations have been used for this study. The plateau value was used for hardness and extrapolation to the surface was used for elastic modulus (Fischer-Cripps, 2006). A total of 10 indentations with 40 loading points, in a range of 0–500 mN, per sample, was used. The indenter contact velocity was set to 0.50 μms−1. The load and unload time for each indentation step was 2 s. A 1 s dwell was used at the maximum load to ensure there was no creep. A 60 s dwell period in the final unload step was used for thermal drift correction. The area function of the indenter was found by indentation into a fused silica reference sample. Hardness (H) and elastic modulus (E) were calculated by applying Oliver-Pharr analysis (Pharr and Oliver, 1992). E and ν (0.2) are Young’s modulus and Poisson’s ratio for the coating; Ei (1,140 GPa) and νi (0.07) are the same quantities for diamond respectively (Pharr and Oliver, 1992).
The roughness of all samples was measured using a topography scan performed in the scanning module of the NanoTest Vantage platform. A 4.5 µm radius spheroconical probe was used with a 200 µm scan distance and a probe velocity of 10 µms−1. The load applied during this topographic scan was 0.1 mN. A total of five scans were performed across the surface of one sample. Each scan was performed with a lateral separation distance of 500 μm from the previous scan.
2.4 Coating structures
Coating thickness was studied by Calotest with a 30 mm diameter ball and confirmed with FIB-SEM (FEI Helios G4 CX Dualbeam SEM). This diameter of Calotest wearing ball allows for the generation of a wear scar to reveal the coating layers and was used in our previous works (McMaster et al., 2020; 2023). The adhesive (Cr) layer was 0.29 ± 0.03 μm for all coatings. The gradient (WC) layer was 0.89 ± 0.08 μm for all coatings. The DLC coating thickness was 5.18 ± 0.07 μm on SS and 3.82 ± 0.09 μm on HTS. This resulted in total coating thicknesses of 6.36 ± 0.11 μm on SS and 5.00 ± 0.12 μm on HTS respectively. Pt was deposited to protect the coating surface during the focused-ion beam procedure. The FIB-SEM cross section of the coating structure can be seen in Figure 1.
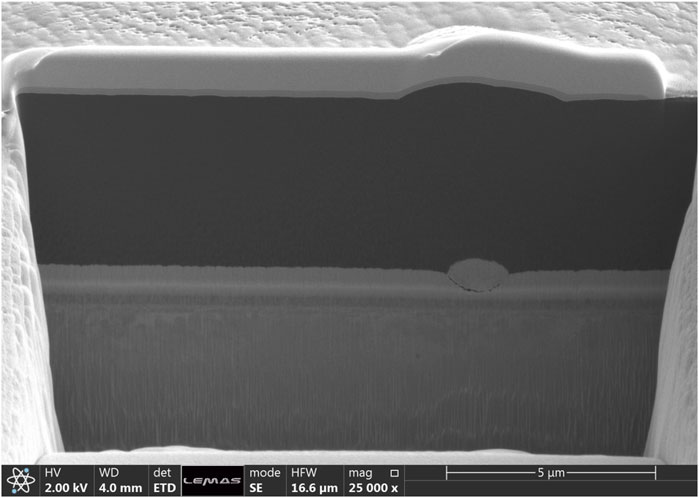
Figure 1. Cross-section FIB SEM micrograph of DLC coating on SS. Note the small defect in the WC gradient layer.
2.5 Fretting
Gross slip fretting conditions were simulated using a bespoke electrodynamic shaker unit, with 10 mm diameter 52,100 steel balls as counterfaces. The electrodynamic shaker unit can be seen other studies carried out at the University of Leeds by Wade et al. (Wade et al., 2020a; 2020b). A bespoke LabVIEW program controlled the system. Tangential force was monitored via a load cell. A feedback loop control system was used wherein an optical displacement sensor adjusts the displacement of the shaker to maintain displacement within the parameters specified. Two load levels, 20 N and 40 N, were employed, achieving high contact pressures ranging from 1.20 to 1.55 GPa. Contact pressures in this range/order of magnitude has been utilised by Januszewski et al. in the study of false brinelling damage (Januszewski et al., 2023), Kalin et al. in the study of phase transformations in fretting (Kalin and Vižintin, 2001), Lin et al. in the study of lubricated fretting wear of high nitrogen stainless bearing steel (Lin et al., 2020) and Zhuang et al. in the analysis of fretting performance of DLC and MoS2 films under fluid lubrication (Zhuang et al., 2019). Equation 1 used to predict the maximum Hertzian contact pressure (
where
The sliding ratio (
where
Table 1 shows the predicted contact pressures and sliding ratios for the test configurations.
The coefficient of friction (COF) for 15,000 cycles (at 5 Hz and a displacement amplitude of ±50 μm) was analysed along with the cumulative dissipated energy in the fretting contact. Each test lasted 50 min with the parameters specified. The effective maximum mid-stroke velocity was 250 μms−1. At least two repeats were performed to confirm the repeatability of the results. All tests were conducted in laboratory conditions with a temperature of 22°C and a humidity of 34%. No external heating was applied during testing. The Poisson’s ratio for the 52,100 steel, SS and HTS were 0.285 (AZoM, 2012a), 0.27 (Azom, 2013) and 0.285 (AZoM, 2012b) respectively. The same stated value of Poisson’s ratio for the DLC was used (0.2) (Pharr and Oliver, 1992).
The lubricants were the following:
• Base oil (BO): Yubase 4 without additives.
• Base oil (BO) + MoDTC): Yubase 4 with the addition of MoDTC friction modifier.
• Fully formulated oil (FFO): Yubase 4 with additive package and viscosity modifier.
• Fully formulated oil (FFO) + MoDTC: Yubase 4 with additive package, viscosity modifier and friction modifier.
Lubricants were provided by Croda. MoDTC added to 1% weight which is equivalent to 500 ppm.
3 Results
3.1 Mechanical properties
The mechanical properties and surface roughness of the coatings and substrates are shown in Table 2. The surface mechanical properties of the coatings are determined by extrapolating the multi-cycle nanoindentation data (determined from load partial unload) to the surface (zero contact depth). The hardness (H) was found by taking the plateau value from the measurement series as the initial indents will be lower than the true hardness (Fischer-Cripps, 2006). The values are less than the 1/10 relative indentation depth recommended by ISO 14577-4 (ISO, 2016, p. 145) ensuring that they were not affected by substrate plasticity. The elastic modulus (E) was determined by taking the mean of the maximum range (extrapolating to the surface, zero depth) to negate any surface contact effects that reduce the modulus at low contact depths (Fischer-Cripps, 2006). The standard deviation for these DLC coating systems has been estimated to be ∼0.7 GPa and ∼5 GPa for hardness and elastic modulus, respectively (McMaster et al., 2023). This methodology has been reported in previous works by McMaster et al (McMaster et al., 2020; 2023).
The substrates have distinct mechanical properties differences with the HTS having a much higher hardness of 10.0 GPa compared to 2.6 ± 0.1 GPa. The elastic moduli are quite similar for both materials. The H/E and H3/E2 differences for the substrates are therefore the result of the hardness differences. Both substrates were polished to the same surface roughness of 26 ± 4 nm Ra. The DLC coating deposited on HTS had a markedly higher surface roughness of 84.0 ± 32.7 nm Ra compared to the DLC on SS with 20.3 ± 5.1 nm Ra. Despite the same deposition times (360 min), the DLC on SS had a DLC thickness of 5.18 ± 0.07 µm. The overall DLC mechanical properties are similar across both substrates.
3.2 Friction results
The friction results are displayed as averages of specific cycle numbers across the whole testing regime. At least two repeats were performed for each material/coating configuration.
3.2.1 Uncoated
The analysis of uncoated fretting performance serves to compare against the lubricated conditions and can model the friction of a starved contact. Figure 2 shows the friction results of uncoated SS at 20 N load corresponding to a contact pressure of 1.26 GPa. The early fretting cycles display an increase in the coefficient of friction caused by the running-in period. The base oil (BO) had the highest friction in the running in period (0.77 ± 0.08) and also the highest standard running friction coefficient. The lowest friction coefficient was recorded with the FFO. After 2,500 cycles, the systems settle into standard running.
Figure 3 shows the coefficients of friction of the uncoated HTS at 20 N (a) and 40 N (b). The effect of load is clearly distinguished between these two test configurations with Figure 3a displaying similar running-in phenomena to uncoated SS in Figure 2. Base oil once again had the highest friction in the running in period (0.41 ± 0.14) and the highest steady-state friction. The lowest steady-state friction was observed with FFO with MoDTC. At 40 N load, the running-in period was hugely extended overall and variable between the lubricant configurations. The highest friction of the running-in period was BO with MoDTC with a value of 0.50 ± 0.06. The standard deviation increase was much higher than this value throughout the tests, however. Friction for this lubricant only stabilised at 9,000 cycles. Steady-state friction was reached at 4,500 cycles for BO, 5,250 cycles for FFO and 6,250 cycles for FFO with MoDTC.
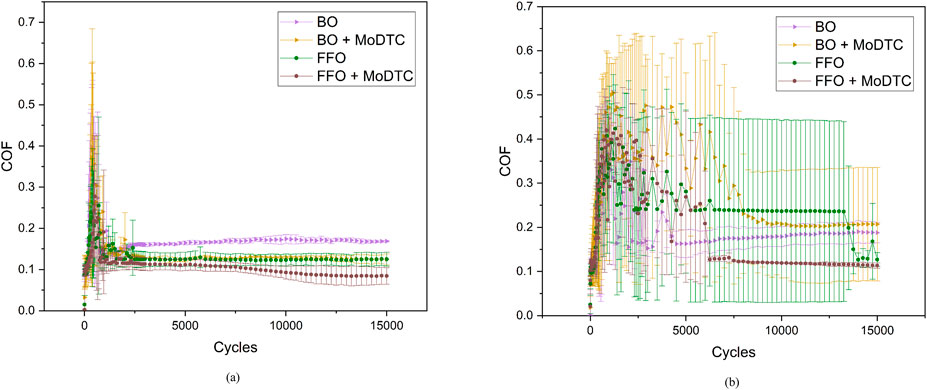
Figure 3. Coefficient of friction (COF) evolution of lubricated uncoated HTS at 20 N (a) and 40 N (b).
3.2.2 Coated
The friction of the unlubricated DLCs is shown in Figure 4. DLC on SS and HTS at 20 N had an extremely short running-in period with both reaching steady state within 500 cycles. At 40 N on HTS, the frictional progression was much smoother with a high of 0.25 ± 0.07 before reducing to approximately steady state at 5,750 cycles however the coefficient of friction continued to steadily decrease for the duration of the test.
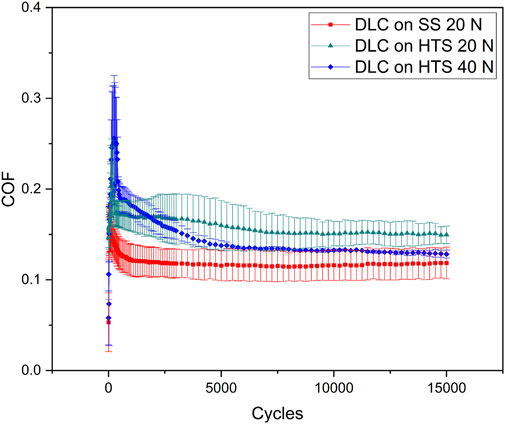
Figure 4. Coefficient of friction (COF) evolution of unlubricated coatings on SS (20 N) and HTS (20 N and 40 N).
The lubricated friction traces of DLC on SS is shown in Figure 5. In lubricated conditions, this coating experienced a smooth reduction in the coefficient of friction from the beginning of fretting to approximately 5,000 cycles where steady state was reached by all coatings. The highest overall friction was experienced by FFO with MoDTC and BO gave the lowest overall friction. The variability across the cycles was greater for the fully formulated oils compared to the base oils.
Figure 6 shows the coefficient of friction progressions for DLC on the HTS substrate at 20 N (a) and 40 N (b). At 20 N, BO and FFO almost instantly reached steady state. FFO with MoDTC appeared to reach steady state but we can note that it began to decrease the coefficient of friction from 7,500 cycles onwards. BO with MoDTC saw its friction decrease much earlier (2,500 cycles) reaching the lowest steady friction in this figure. Increasing the load to 40 N generally increases the variance in the friction across the cycles (larger relative error bars) however FFO has an extremely low variance for all the fretting cycles. Comparing the MoDTC containing oils to their non friction modifier containing counterparts, we can see the positive effect with the friction reduction of each set.
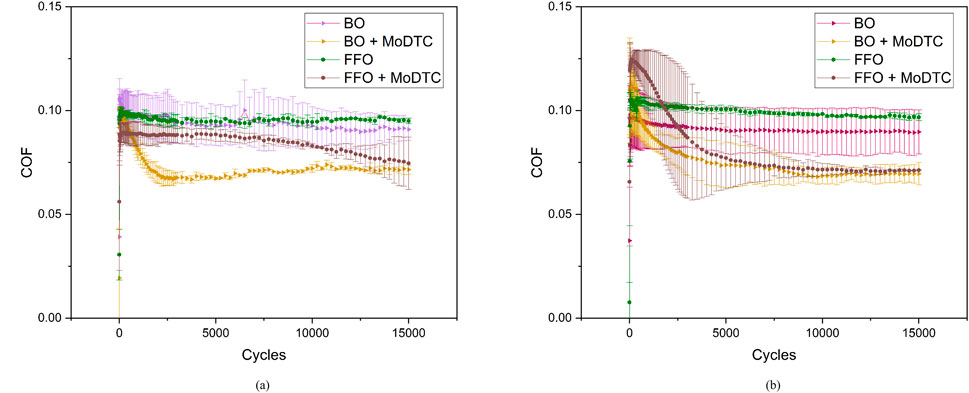
Figure 6. Coefficient of friction (COF) evolution of lubricated coating A on HTS at 20 N (a) and 40 N (b).
3.2.3 Average friction
The coefficients of friction as averaged across all the cycles is shown in Figure 7. It can be noted that configurations with large error bars correspond to those which had unstable friction traces across the full cycle such as lubricated uncoated HTS under 40 N load (shown in Figure 3b) or those with high friction running in periods as in lubricated uncoated SS (shown in Figure 2). These high initial friction in uncoated SS could be due to initial instabilities in entraining the lubricant in the fretting contact during running in. High friction such as this is observed in dry fretting tests as seen in the work of Kubiak et al (Kubiak et al., 2011). The lubricated DLCs display noticeably lower friction with low error bars showing reasonable stability across all the cycles. The lowest average COF was BO with MoDTC on lubricated DLC on HTS with a value of 0.08 ± 0.01. Comparing lubricated DLC on HTS at the different load levels shows that there is little difference in the average friction; the variance is slightly higher at 40 N however. The uncoated substrates have notably higher average friction and variance across the fretting cycles with the highest average being BO lubrication on uncoated SS with a value of 0.32 ± 0.20.
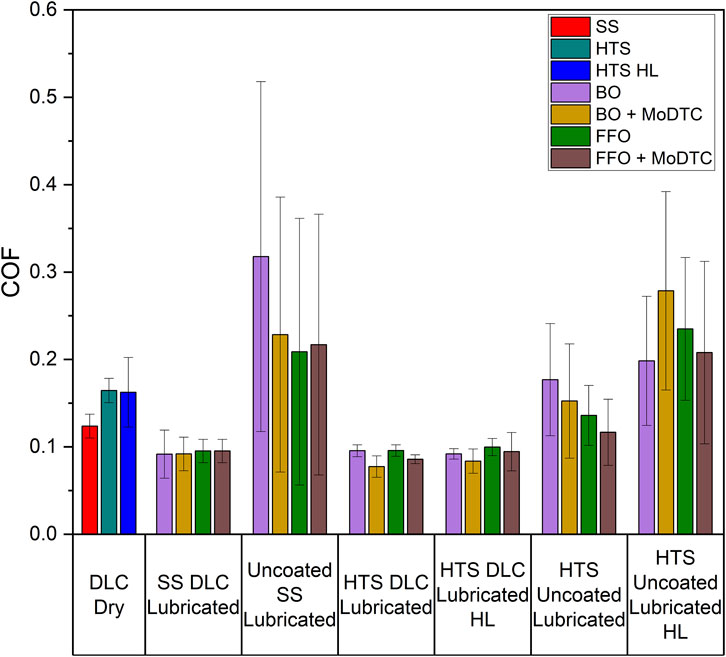
Figure 7. Average coefficient of friction (COF). Results are averaged across all fretting cycles so high standard deviations correspond to high instability. HL indicates 40 N load.
The friction of the dry DLCs was very similar for the different load levels on HTS. The variance at 40 N was 0.04 compared to 0.01 at 20 N. The friction of DLC on the SS substrate was 0.12 ± 0.01.
3.3 Dissipated energy
The total cumulative dissipated energy across all the fretting cycles is shown in Figure 8. The frictional force and displacement of each fretting cycle was integrated and summed to find the total dissipated energy. For a simplified interface, lower dissipated energy can correlate to lower wear in fretting but this does not hold for complex multi-layered materials where layer breakdown and varying wear rates complicate the relationship (Liskiewicz and Fouvry, 2005; McMaster et al., 2023). The addition of lubricants would additionally add complexities to the metric where the establishment of steady state may depend on the lubricant properties as we can see in Figures 2, 3, 5, 6. We can see that trends in friction from Figure 7 are generally magnified. The unlubricated DLCs in Figure 4 may be described by the wear and energy relation previously explored (McMaster et al., 2023). The highest cumulative dissipated energy was measured with BO lubricated uncoated HTS at 40 N with a value of 15.2 ± 1.5 J.
3.4 Wear images
The effect of load on DLC coated HTS is shown in Figure 9. Abrasive marks are shown in the centre of the wear scars for both loads with a larger amount of wear debris ejected at 40 N (Zhu and Zhou, 2011). Zhuang et al. also noted that the wear mechanism was mainly attributed to abrasion (Zhuang et al., 2019). There were no signs of fatigue or coating delamination. No signs of coating wear through are shown with no delamination present indicating that the coating has protected the substrate.
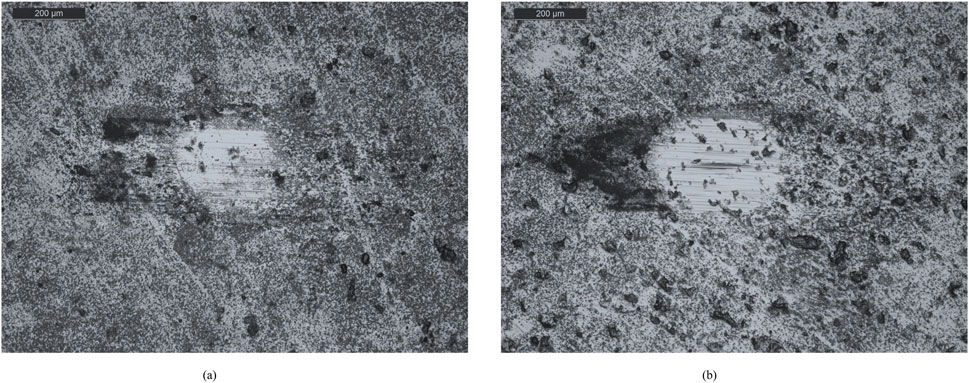
Figure 9. Wear scars of dry conditions on DLC on HTS. (a) Dry conditions on DLC on HTS at 20 N load. (b) Dry conditions on DLC on HTS at 40 N load.
Figure 10 shows the wear scars of lubricants on DLC coated HTS. In (a), mild abrasive marks are displayed when lubricated with base oil and 20 N load. Increasing the load to 40 N (b) generates small wear particulates that are likely generated early in the fretting before the lubricated fretting has stabilised. Some indications of abrasion are present also.
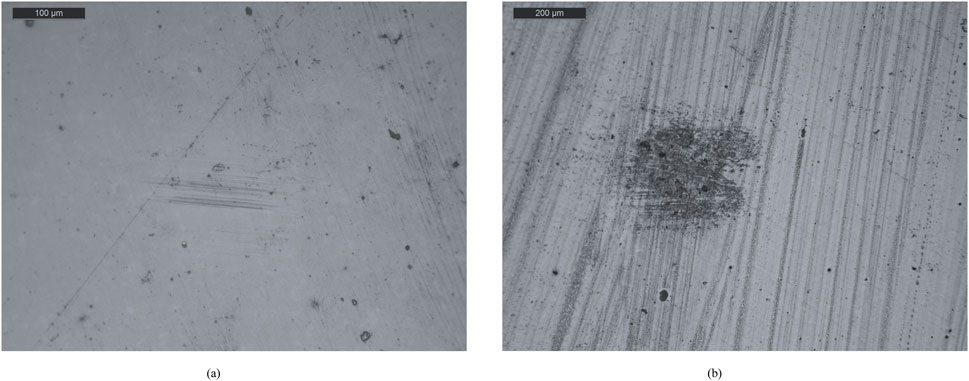
Figure 10. Wear scars of lubricated DLC on HTS and SS. (a) Base oil lubricated DLC on HTS at 20 N load. (b) Base oil lubricated DLC on HTS at 40 N load.
4 Discussion
Zhou and Vicent, in a review of lubrication in fretting, found that oil and grease lubrication was suitable for the gross slip regime (Zhou and Vincent, 1999). Oil lubrication in fretting is known to be affected by viscosity, boundary lubrication properties, the presence of additives and the deposition process (McColl et al., 1995). Shime et al. explored the behaviour of oil lubrication in fretting contacts and created a schematic comparing the friction against stroke length across the stick-slip and gross slip regions for unlubricated contacts and different viscosities of lubricant (Shima et al., 1997). Low viscosity lubricants were found to have a lower increase in friction in the stick-slip region (low stroke length) and lower friction as stroke increased (progressed into gross-slip). In this work, the fully formulated oil included a viscosity modifier. This corresponds to base oil having a lower coefficient of friction in Figures 5, 6. However, for Figures 2–4, we likely observe the effects of the MoDTC reducing the friction in these tests, especially as both surfaces were ferrous (Okubo et al., 2018). Januszewski et al. investigated lubricant properties and contact conditions in false brinelling damage. They found that in fretting conditions, lower viscosity oils reduced the amount of false brinelling damage. Frictional performance was also improved with the use of lower viscosity oils. It was noted that despite this, the contact still operated in boundary lubrication. In contrast, higher viscosity along with higher contact pressures and reciprocating frequencies caused the contact to be dry with friction coefficients of 0.5 for short periods (Januszewski et al., 2023).
Interactions of friction modifiers have generally been studied under reciprocating sliding or unidirectional pin-on-disk testing (De Barros’Bouchet et al., 2005; Sugimoto et al., 2013; De Feo et al., 2016; 2017; Garcia et al., 2021). Once steady state fretting had been established, all of the tests in this work were in the gross slip fretting regime as shown in Table 1 (sliding ratios from 0.45–0.58). The authors were unable to find studies that specifically considered the interaction of MoDTC friction modifier in this fretting regime. Comparing base oils and fully formulated oils in this study (Figure 7), we can see that the lowest coefficients of friction are achieved with base oil with the addition of MoDTC has seen with lubricated DLC on HTS at both 20 N and 40 N. The average COF with lubricated DLC on SS was also lower with the base oil lubricant variants however the lack of additive performed slightly better in this case.
The reasons for this performance difference could be a combination of viscosity as noted by Januszewski et al. (2023) but also additive interactions which require mechanistic investigation in fretting. Comparing the average COF in this work to sliding contacts, we can note that generally, friction in lubricated DLC fretting is lower with values less than 0.1 as opposed to around 0.12 in sliding with fresh oil. Aging for 2 h or more generally lowered the friction to 0.06–0.08 but friction rose with 8 h of oil aging (De Feo et al., 2015; De Feo et al., 2016; 2017; Ohara et al., 2017).
Several authors have investigated the wear mechanisms of DLC coatings interacting with MoDTC. Kosarieh and co-workers found a measurable reduction in friction, similar to Figures 5, 6 however, the wear coefficient was much higher at high MoDTC concentrations (Kosarieh et al., 2013; 2016). MoS2 formation and graphitisation reduced the friction in the contact but the molybdenum containing compounds were suggested to oxidise or dehydrogenate the coating thereby breaking down the DLC matrix. Espejo et al. also found MoS2 in sliding contact conditions and attributed the high wear to carbonaceous layer formation (Espejo et al., 2019). MoS2 was not found in additive containing fully formulated oil due to interactions with other additives in the oil. Sugimoto suggested that graphitisation was the main mechanism of DLC wear under boundary lubrication corresponding to the carbonaceous layer formation in Espejo’s work (Sugimoto et al., 2013). Al-Jeboori et al. found that MoDTC activation was enhanced in pure sliding in MTM testing (Al-Jeboori et al., 2018). We can note that the friction of the FFO with MoDTC was not the lowest in Figures 5, 6. Kassim et al. corroborated the tribological transformation with molybdenum containing compounds (Kassim et al., 2020). Raman observations were conducted by Okubo and coworkers who found Mo2C formed after MoS2 and MoO3 interaction were likely the cause of the DLC matrix breakdown (Okubo and Sasaki, 2017; Okubo et al., 2019). De Barros'Bouchet and coworkers have investigated the interactions of DLC with MoDTC and provided further evidence of the molybdenum containing intermediary compounds in breaking down the carbon matrix in the presence of a ferrous counterface (De Barros’Bouchet et al., 2005; De Feo et al., 2016; 2017). Further studies on the tribochemical interaction of MoDTC in fretting should explore the mechanisms of tribofilm formation and breakdown to elucidate the interplay between oil viscosity and additive interactions.
MoDTC interactions on steel also result from MoS2 formation. Temperature was found to be a factor in controlling the tribochemical process however heating was not utilised in this study. Carbonaceous material was also found in the contact however as the surfaces were ferrous, this was attributed to the base oil degradation. Increased load was found to increase the growth rate of MoS2 by supplying more mechanical energy to promote chemical reactions in the contact. As such the tribofilm formation was shown to be a mechanochemical process (Garcia et al., 2021). Figures 2, 3 show the effectiveness of the lubricants on the uncoated substrates.
Vengudusamy et al. explored the behaviour of DLC/steel contacts and presented Stribeck curves in the initial contact conditions and after 2 h of sliding (Vengudusamy et al., 2012). Friction for a-C:H (with steel and MoDTC) varied from 0.05–0.02 in the initial conditions and evolved to 0.06–0.02 in speeds varying from 0.007–5 ms−1. The speed of fretting was calculated to be 250 μms−1 in this work and was therefore too low to be captured in the Stribeck curve however the trend indicates, that at lower speed the friction coefficient will be higher as summarised in Figure 7.
Surface roughness in fretting has been explored in dry fretting (Kubiak et al., 2011). In these conditions, rougher surfaces had a lower coefficient of friction and the activation energy for wear was higher with smoother surfaces. In this work, the surface roughness was approximately the same for all surfaces apart from DLC on HTS as shown in Table 2 with a value of 84.0 ± 32.7 nm Ra compared to 20–26 nm Ra for the other surfaces. This may contribute to the frictional differences in Figure 4 and comparing DLC on SS and HTS in Figures 5, 6 respectively. The differences in surface roughness may affect lubricant entrainment as can be seen comparing DLC on SS in Figure 5 and DLC on HTS in Figure 6. The average friction was slightly lower on the lubricated HTS in Figure 7.
The mechanical properties of the fretted surfaces in this study were explored with nanoindentation (Table 2). In a previous work by McMaster and coworkers, the mechanical properties were found to correlate with the tribological performance, specifically an inverse correlation between wear volume and the ratios of H/E and H3/E2 (McMaster et al., 2023). Typically, H/E and H3/E2 can be used to relate tribological performance via the interfacial/adhesive component and ploughing contributions to friction (Ni et al., 2004; Beake et al., 2013; Beake, 2022), elastic strain to break (Leyland and Matthews, 2000) and contact yield pressure respectively (Chen et al., 2019). Comparing the mechanical properties shown in Table 2 and the average coefficients of friction in Figure 7 and dissipated energies in Figure 8, we can note that there is no correlation between the mechanical properties and tribological performance. As such the tribological performance, in this work is controlled by the lubricant behaviours as observed by other authors (De Barros’Bouchet et al., 2005; De Feo et al., 2016; Okubo et al., 2019; Januszewski et al., 2023).
The mechanical properties of unwashed and solvent washed tribofilms have been explored previously on EN31 steel (Bec et al., 2004). In this work by Bec et al., the MoDTC tribofilm was found to have a low hardness (below 0.6 GPa) on both the washed and unwashed variants. The coefficient of friction was also explored in relation to mean contact pressure. The formed MoDTC tribofilm was unable to resist the contact pressure (less than 1 GPa) and therefore was ineffective at reducing friction in comparison to the MoDTC and ZDTP tribofilms. However, the lubricant containing MoDTC was able to reach low coefficient of friction values of 0.01–0.05. Analysing the friction coefficients obtained in Figures 2–6; we can note that friction was not this low however the conditions differed. In Bec et al.’s work, reciprocating sliding was achieved with an approximate contact pressure of 0.36 GPa to simulate the contact conditions of a cam/follower system in an internal combustion engine.
Multiple authors have utilised dissipated energy in the study of fretting wear. Korsunsky and Kim explored the energy per cycle (in plastic and elastic terms as well as the energy ratio) as it evolved with accumulated reciprocal sliding distance and found that total dissipated energy decreased throughout the test (Korsunsky and Kim, 2010). Liskiewicz and Fouvry utilised dissipated energy as a metric to compare coating endurance (Liskiewicz and Fouvry, 2005).
The authors of this study previously examined cumulative dissipated energy in fretting wear of DLC coatings and found a reasonable positive correlation with wear volume (McMaster et al., 2023). Under dry conditions, cumulative dissipated energy was found to have a weak positive correlation with wear volume. In these conditions, frictional energy input will drive tribological transformation of the coating and wear however in the present study (Fouvry et al., 2002; Sugimoto et al., 2013), the lubricant entrained into the contact will reduce direct wear (comparing Figures 9, 10). Furthermore, the dynamics of lubricant entrainment affect the fretting system’s setting of required displacement and possible tribofilm formation suggests that cumulative dissipated energy is not a reliable measure of wear in these conditions. Comparing the different loads (corresponding to varying contact pressures) of uncoated HTS and DLC on HTS in Figure 8, the dissipated energy was notably higher for the higher contact pressure. A higher load will input more energy into the contact thereby increasing the cumulative dissipated energy. Additionally, we can see the higher instability in friction caused by higher load by comparing the loads in Figures 3, 6.
5 Conclusion
In this study, the frictional performance of DLC coatings was analysed in base oil and fully formulated oil with the friction modifier MoDTC. Contact pressure was varied between 1.20 and 1.55 GPa with loads of 20 N and 40 N.
The following conclusions could be drawn:
• Higher contact pressure created instabilities in the friction extending the time to reach steady state.
• The surface roughness of the coatings and its interaction with the viscosity of the lubricants affected the frictional performance. Surface roughness was also the main variable affecting the fretting performance of the DLCs in dry conditions. Performance differences in the DLCs on HTS and SS can be mainly attributed to the coating surface roughness.
• On DLCs on HTS, the higher viscosity of fully formulated oil performed worse, as the roughness of the coating may have affected entrainment. The activation of the MoDTC friction modifier in base oil and fully formulated oil was observable at both loads on DLC on HTS. On the smoother DLC on SS, the lower viscosity base oil performed best as it was likely entrained into the contact easily. As such, we can see that MoDTC was effective in reducing friction in the gross-slip fretting regime as it also is in full sliding.
• On the uncoated substrates, the addition of the additive pack and MoDTC consistently improved friction performance, indicating their effectiveness and activation of the MoDTC respectively.
• The instabilities in the fretting contact were captured in the cumulative dissipated energy however this metric is unlikely to be a reliable proxy for wear due to the fretting rig’s tendency to take several cycles to establish the desired fretting regime and the dynamics of lubricant entrainment that were also present.
• The commonly reported deleterious effects of MoDTC interacting with DLC (De Barros’Bouchet et al., 2005; Kosarieh et al., 2013; De Feo et al., 2016; Kosarieh et al., 2016; De Feo et al., 2017; Al-Jeboori et al., 2018) were not observed in this study as any excess wear caused by the lubricant interaction was not captured in light of lubricant dynamics.
Future work exploring the tribology of lubricated DLC fretting contacts should explore the extent of the graphitisation and transfer film generation of the DLCs themselves. Longer tests should be carried out to ensure that a larger wear volume is generated and such that any coating interactions (and tribofilms generated) from the lubricant additives can be discerned by Raman spectroscopy (Khaemba et al., 2015; Vaitkunaite et al., 2022) or X-ray Photoelectron Spectroscopy (Morina et al., 2006). Different fretting regimes could be investigated, and external heating could be applied which could be paired with other DLC types and mixed additives. Further analysis should be performed to identify the specific lubrication regime attained in the lubricated fretting contact. Tomović et al. explored a methodology to predict oil thickness in a trochoidal pump which could extend this work to a further industrial application where cost analysis of the efficacy of the lubricants and DLCs could be undertaken (Tomović et al., 2021). These results can be used as the basis of a statistical study to predict the results of varying contact pressures once a larger dataset is assembled.
Data availability statement
The original contributions presented in the study are included in the article/supplementary material, further inquiries can be directed to the corresponding author.
Author contributions
SM: Conceptualization, Formal Analysis, Investigation, Methodology, Validation, Visualization, Writing – original draft, Writing – review and editing, Resources. SK: Methodology, Supervision, Validation, Writing – original draft, Writing – review and editing. TL: Conceptualization, Funding acquisition, Methodology, Resources, Supervision, Writing – original draft, Writing – review and editing. BB: Conceptualization, Funding acquisition, Resources, Supervision, Writing – original draft, Writing – review and editing.
Funding
The author(s) declare that financial support was received for the research and/or publication of this article. This work was supported by the Engineering and Physical Sciences Research Council (EPSRC), Grant No. ELP01629X and Micro Materials Ltd. as part of the EPSRC Doctoral Training Centre in Integrated Tribology (iT-CDT).
Acknowledgments
The authors would like to thank Ishmaeel Ghouri, Mihhail Stotsjuk and Lei Cao for running some of the fretting tests.
Conflict of interest
Author SM was employed by Pillarhouse International Ltd. Author SK was employed by GKN Automotive. Author BB was employed by Micro Materials Ltd.
The remaining author declares that the research was conducted in the absence of any commercial or financial relationships that could be construed as a potential conflict of interest.
Generative AI statement
The author(s) declare that no Generative AI was used in the creation of this manuscript.
Publisher’s note
All claims expressed in this article are solely those of the authors and do not necessarily represent those of their affiliated organizations, or those of the publisher, the editors and the reviewers. Any product that may be evaluated in this article, or claim that may be made by its manufacturer, is not guaranteed or endorsed by the publisher.
References
Aghaei Sarvari, A., Zeinali Heris, S., Mohammadpourfard, M., Mousavi, S. B., and Estellé, P. (2022). Numerical investigation of TiO2 and MWCNTs turbine meter oil nanofluids: flow and hydrodynamic properties. Fuel 320, 123943. doi:10.1016/j.fuel.2022.123943
Al-Jeboori, Y., Kosarieh, S., Morina, A., and Neville, A. (2018). Investigation of pure sliding and sliding/rolling contacts in a DLC/Cast iron system when lubricated in oils containing MoDTC-Type friction modifier. Tribol. Int. 122, 23–37. doi:10.1016/j.triboint.2018.02.015
AZoM (2012a). AISI 52100 alloy steel (UNS G52986). AZO Mater, 1–2. Available online at: https://www.azom.com/article.aspx?ArticleID=6704 (Accessed July 27, 2018).
AZoM (2012b). M2 molybdenum high speed tool steel (UNS T11302). AZO Mater, 3–5. Available online at: https://www.azom.com/article.aspx?ArticleID=6174 (Accessed July 27, 2018).
Azom (2013). Stainless steel - grade 316L - properties, fabrication and applications (UNS S31603). 3–5. Available online at: https://www.azom.com/article.aspx?ArticleID=2382 (Accessed July 27, 2018).
Beake, B. D. (2022). The influence of the H/E ratio on wear resistance of coating systems – insights from small-scale testing. Surf. Coat. Technol. 442, 128272. doi:10.1016/j.surfcoat.2022.128272
Beake, B. D., Harris, A. J., and Liskiewicz, T. W. (2013). Review of recent progress in nanoscratch testing. Tribol. - Mater. Surf. Interfaces 7, 87–96. doi:10.1179/1751584X13Y.0000000037
Beake, B. D., Liskiewicz, T. W., Vishnyakov, V. M., and Davies, M. I. (2015). Development of DLC coating architectures for demanding functional surface applications through nano- and micro-mechanical testing. Surf. Coat. Technol. 284, 334–343. doi:10.1016/j.surfcoat.2015.05.050
Beake, B. D., McMaster, S. J., Liskiewicz, T. W., and Neville, A. (2021). Influence of Si- and W- doping on micro-scale reciprocating wear and impact performance of DLC coatings on hardened steel. Tribol. Int. 160, 107063. doi:10.1016/j.triboint.2021.107063
Bec, S., Tonck, A., Georges, J. M., and Roper, G. W. (2004). Synergistic effects of MoDTC and ZDTP on frictional behaviour of tribofilms at the nanometer scale. Tribol. Lett. 17, 797–809. doi:10.1007/s11249-004-8088-7
Bukvić, M., Gajević, S., Skulić, A., Savić, S., Ašonja, A., and Stojanović, B. (2023). Tribological application of nanocomposite additives in industrial oils. Lubricants 12, 6. doi:10.3390/lubricants12010006
Chen, X., Du, Y., and Chung, Y. W. (2019). Commentary on using H/E and H/E as proxies for fracture toughness of hard coatings. Thin Solid Films 688, 137265. doi:10.1016/j.tsf.2019.04.040
De Barros’Bouchet, M. I., Martin, J. M., Le-Mogne, T., and Vacher, B. (2005). Boundary lubrication mechanisms of carbon coatings by MoDTC and ZDDP additives. Tribol. Int. 38, 257–264. doi:10.1016/j.triboint.2004.08.009
De Feo, M., De Barros Bouchet, M. I., Minfray, C., Le Mogne, T., Meunier, F., Yang, L., et al. (2016). MoDTC lubrication of DLC-involving contacts. Impact of MoDTC degradation. Wear 348–349, 116–125. doi:10.1016/j.wear.2015.12.001
De Feo, M., De Barros Bouchet, M. I., Minfray, C., Esnouf, C., Le Mogne, T., Meunier, F., et al. (2017). Formation of interfacial molybdenum carbide for DLC lubricated by MoDTC: origin of wear mechanism. Wear 370–371, 17–28. doi:10.1016/j.wear.2016.10.002
De Feo, M., Minfray, C., De Barros Bouchet, M. I., Thiebaut, B., and Martin, J. M. (2015). MoDTC friction modifier additive degradation: correlation between tribological performance and chemical changes. RSC Adv. 5, 93786–93796. doi:10.1039/C5RA15250J
Donnet, C., and Erdemir, A. (2008). “Diamond-like carbon films: a historical overview,” in Tribology of diamond-like carbon films: fundamentals and applications. Editors C. Donnet, and A. Erdemir (Boston, MA: Springer US), 1–10. doi:10.1007/978-0-387-49891-1
Espejo, C., Thiébaut, B., Jarnias, F., Wang, C., Neville, A., and Morina, A. (2019). MoDTC tribochemistry in steel/steel and steel/diamond-like-carbon systems lubricated with model lubricants and fully formulated engine oils. J. Tribol. 141. doi:10.1115/1.4041017
Fischer-Cripps, A. C. (2000). Introduction to contact mechanics. Boston, MA: Springer US. Available online at: http://link.springer.com/10.1007/b97709 (Accessed September 10, 2017).
Fischer-Cripps, A. C. (2006). Critical review of analysis and interpretation of nanoindentation test data. Surf. Coat. Technol. 200, 4153–4165. doi:10.1016/j.surfcoat.2005.03.018
Fouvry, S., Fridrici, V., Langlade, C., Kapsa, P., and Vincent, L. (2006). Palliatives in fretting: a dynamical approach. Tribol. Int. 39, 1005–1015. doi:10.1016/j.triboint.2006.02.038
Fouvry, S., Kapsa, P., Sauger, E., Martin, J. M., Ponsonnet, L., and Vincent, L. (2002). Tribologically transformed structure in fretting. Wear 245, 39–52. doi:10.1016/s0043-1648(00)00464-6
Fouvry, S., Kapsa, P., and Vincent, L. (1995). Analysis of sliding behaviour for fretting loadings: determination of transition criteria. Wear 185, 35–46. doi:10.1016/0043-1648(94)06582-9
Fu, H., Fan, X., Li, W., Li, H., Cai, Z., and Zhu, M. (2018). Tribological behaviors of fluid-lubricated DLC films under sliding and fretting conditions. Appl. Surf. Sci. 459, 411–421. doi:10.1016/j.apsusc.2018.08.030
Garcia, C. E., Ueda, M., Spikes, H., and Wong, J. S. S. (2021). Temperature dependence of molybdenum dialkyl dithiocarbamate (MoDTC) tribofilms via time-resolved Raman spectroscopy. Sci. Rep. 11, 3621. doi:10.1038/s41598-021-81326-0
Grill, A. (1993). Review of the tribology of diamond-like carbon. Wear 168, 143–153. doi:10.1016/0043-1648(93)90210-D
Grill, A. (1999). Diamond-like carbon: state of the art. Diam. Relat. Mater. 8, 428–434. doi:10.1016/S0925-9635(98)00262-3
Hainsworth, S. V., and Uhure, N. J. (2007). Diamond like carbon coatings for tribology: production techniques, characterisation methods and applications. Int. Mater. Rev. 52, 153–174. doi:10.1179/174328007X160272
ISO (2015). ISO 14577-1:2015 Metallic materials -- Instrumented indentation test for hardness and materials parameters -- Part 1: test method. Available online at: https://www.iso.org/standard/56626.html (Accessed March 9, 2017).
ISO (2016). ISO 14577-4:2016 Metallic materials — instrumented indentation test of hardness and materials parameters Part 4: test method for metallic and nonmetallic coatings 19.
Januszewski, R., Brizmer, V., and Kadiric, A. (2023). Effect of lubricant properties and contact conditions on false brinelling damage. Tribol. Trans. 66, 350–363. doi:10.1080/10402004.2023.2183915
Kalin, M., Velkavrh, I., Vižintin, J., and Ožbolt, L. (2008). Review of boundary lubrication mechanisms of DLC coatings used in mechanical applications. Meccanica 43, 623–637. doi:10.1007/s11012-008-9149-z
Kalin, M., and Vižintin, J. (2001). High temperature phase transformations under fretting conditions. Wear 249, 172–181. doi:10.1016/S0043-1648(01)00549-X
Kalin, M., and Vižintin, J. (2006). The tribological performance of DLC coatings under oil-lubricated fretting conditions. Tribol. Int. 39, 1060–1067. doi:10.1016/j.triboint.2006.02.040
Kassim, K. A. M., Tokoroyama, T., Murashima, M., and Umehara, N. (2020). The wear classification of MoDTC-derived particles on silicon and hydrogenated diamond-like carbon at room temperature. Tribol. Int. 147, 106176. doi:10.1016/j.triboint.2020.106176
Khaemba, D. N., Neville, A., and Morina, A. (2015). A methodology for Raman characterisation of MoDTC tribofilms and its application in investigating the influence of surface chemistry on friction performance of MoDTC lubricants. Tribol. Lett. 59, 38. doi:10.1007/s11249-015-0566-6
Korsunsky, A. M., and Kim, K. (2010). Dissipated energy and friction coefficient evolution during fretting wear of solid lubricant coatings. Tribol. Int. 43, 861–867. doi:10.1016/j.triboint.2009.12.063
Kosarieh, S., Morina, A., Flemming, J., Lainé, E., and Neville, A. (2016). Wear mechanisms of hydrogenated DLC in oils containing MoDTC. Tribol. Lett. 64, 4. doi:10.1007/s11249-016-0737-0
Kosarieh, S., Morina, A., Lainé, E., Flemming, J., and Neville, A. (2013). The effect of MoDTC-type friction modifier on the wear performance of a hydrogenated DLC coating. Wear 302, 890–898. doi:10.1016/j.wear.2012.12.052
Kubiak, K. J., Liskiewicz, T. W., and Mathia, T. G. (2011). Surface morphology in engineering applications: influence of roughness on sliding and wear in dry fretting. Tribol. Int. 44, 1427–1432. doi:10.1016/j.triboint.2011.04.020
Leyland, A., and Matthews, A. (2000). On the significance of the H/E ratio in wear control: a nanocomposite coating approach to optimised tribological behaviour. Wear 246, 1–11. doi:10.1016/S0043-1648(00)00488-9
Lifshitz, Y. (1999). Diamond-like carbon — present status. Diam. Relat. Mater. 8, 1659–1676. doi:10.1016/S0925-9635(99)00087-4
Lin, H., Yang, M., and Shu, B. (2020). Fretting wear behaviour of high-nitrogen stainless bearing steel under lubrication condition. J. Iron Steel Res. Int. 27, 849–866. doi:10.1007/s42243-020-00414-z
Liskiewicz, T., and Fouvry, S. (2005). Development of a friction energy capacity approach to predict the surface coating endurance under complex oscillating sliding conditions. Tribol. Int. 38, 69–79. doi:10.1016/j.triboint.2004.06.002
McColl, I. R., Waterhouse, R. B., Harris, S. J., and Tsujikawa, M. (1995). Lubricated fretting wear of a high-strength eutectoid steel rope wire. Wear 185, 203–212. doi:10.1016/0043-1648(95)06616-0
McMaster, S. J., Kosarieh, S., Liskiewicz, T. W., Neville, A., and Beake, B. D. (2023). Utilising H/E to predict fretting wear performance of DLC coating systems. Tribol. Int. 185, 108524. doi:10.1016/j.triboint.2023.108524
McMaster, S. J., Liskiewicz, T. W., Beake, B. D., and Neville, A. (2020). Probing fatigue resistance in multi-layer DLC coatings by micro- and nano-impact: correlation to erosion tests. Surf. Coat. Technol. 402, 126319. doi:10.1016/j.surfcoat.2020.126319
Morina, A., Neville, A., Priest, M., and Green, J. H. (2006). ZDDP and MoDTC interactions and their effect on tribological performance – tribofilm characteristics and its evolution. Tribol. Lett. 24, 243–256. doi:10.1007/s11249-006-9123-7
Mousavi, S. B., Zeinali Heris, S., and Hosseini, M. G. (2019). Experimental investigation of MoS2/diesel oil nanofluid thermophysical and rheological properties. Int. Commun. Heat Mass Transf. 108, 104298. doi:10.1016/j.icheatmasstransfer.2019.104298
Mousavi, S. B., and Zeinali Heris, S. (2020). Experimental investigation of ZnO nanoparticles effects on thermophysical and tribological properties of diesel oil. Int. J. Hydrogen Energy 45, 23603–23614. doi:10.1016/j.ijhydene.2020.05.259
Mousavi, S. B., Zeinali Heris, S., and Estellé, P. (2021). Viscosity, tribological and physicochemical features of ZnO and MoS2 diesel oil-based nanofluids: An experimental study. Fuel 293, 120481. doi:10.1016/j.fuel.2021.120481
Mousavi, S. B., Pourpasha, H., and Heris, S. Z. (2024). High-temperature lubricity and physicochemical behaviors of synthesized Cu/TiO2/MnO2-doped GO nanocomposite in high-viscosity index synthetic biodegradable PAO oil. Int. Commun. Heat Mass Transf. 156, 107642. doi:10.1016/j.icheatmasstransfer.2024.107642
Mousavi, S. B., Heris, S. Z., and Estellé, P. (2020). Experimental comparison between ZnO and MoS2 nanoparticles as additives on performance of diesel oil-based nano lubricant. Sci. Rep. 10, 5813. doi:10.1038/s41598-020-62830-1
Neyman, A. (1992). The influence of oil properties on the fretting wear of mild steel. Wear 152, 171–181. doi:10.1016/0043-1648(92)90212-Q
Ni, W., Cheng, Y. T., Lukitsch, M. J., Weiner, A. M., Lev, L. C., and Grummon, D. S. (2004). Effects of the ratio of hardness to Young’s modulus on the friction and wear behavior of bilayer coatings. Appl. Phys. Lett. 85, 4028–4030. doi:10.1063/1.1811377
Ohara, K., Hanyuda, K., Kawamura, Y., Omura, K., Kameda, I., Umehara, N., et al. (2017). Analysis of wear track on DLC coatings after sliding with MoDTC-containing lubricants. Tribol. Online 12, 110–116. doi:10.2474/trol.12.110
Okubo, H., and Sasaki, S. (2017). In situ Raman observation of structural transformation of diamond-like carbon films lubricated with MoDTC solution: mechanism of wear acceleration of DLC films lubricated with MoDTC solution. Tribol. Int. 113, 399–410. doi:10.1016/j.triboint.2016.10.009
Okubo, H., Tadokoro, C., Sumi, T., Tanaka, N., and Sasaki, S. (2019). Wear acceleration mechanism of diamond-like carbon (DLC) films lubricated with MoDTC solution: roles of tribofilm formation and structural transformation in wear acceleration of DLC films lubricated with MoDTC solution. Tribol. Int. 133, 271–287. doi:10.1016/j.triboint.2018.12.029
Okubo, H., Yonehara, M., and Sasaki, S. (2018). In situ Raman observations of the formation of MoDTC-derived tribofilms at steel/steel contact under boundary lubrication. Tribol. Trans. 61, 1040–1047. doi:10.1080/10402004.2018.1462421
Pauleau, Y. (2008). “Residual stresses in DLC films and adhesion to various substrates,” in Tribology of diamond-like carbon films: fundamentals and applications (Boston, MA: Springer US), 102–136. doi:10.1007/978-0-387-49891-1_4
Pharr, G. M., and Oliver, W. C. (1992). Measurement of thin film mechanical properties using nanoindentation. Mrs Bull. 17, 28–33. doi:10.1557/S0883769400041634
Pierson, H. O. (1993). Handbook of carbon, graphite, diamonds and fullerenes: processing, properties and applications (materials science and process technology). Norwich, NY: Noyes Publications. doi:10.1016/B978-0-8155-1339-1.50008-6
Robertson, J. (1992). Properties of diamond-like carbon. Surf. Coat. Technol. 50, 185–203. doi:10.1016/0257-8972(92)90001-Q
Robertson, J. (2002). Diamond-like amorphous carbon. Mater. Sci. Eng. R. Rep. 37, 129–281. doi:10.1016/S0927-796X(02)00005-0
Ronkainen, H., and Holmberg, K. (2008). “Environmental and thermal effects on the tribological performance of DLC coatings,” in Tribology of diamond-like carbon films: fundamentals and applications (Boston, MA: Springer US), 155–200. doi:10.1007/978-0-387-49891-1_6
Shima, M., Suetake, H., McColl, I. R., Waterhouse, R. B., and Takeuchi, M. (1997). On the behaviour of an oil lubricated fretting contact. Wear 210, 304–310. doi:10.1016/S0043-1648(97)00078-1
Skulić, A., Milojević, S., Marić, D., Ivanović, L., Krstić, B., Radojković, M., et al. (2022). The impact of lubricant viscosity and materials on power losses and efficiency of worm gearbox. Teh. Vjesn. 29, 1853–1860. doi:10.17559/TV-20220207092015
Sugimoto, I., Honda, F., and Inoue, K. (2013). Analysis of wear behavior and graphitization of hydrogenated DLC under boundary lubricant with MoDTC. Wear 305, 124–128. doi:10.1016/j.wear.2013.04.030
Tomović, R., Ivanović, L., Mačkić, T., Stojanović, B., and Glišović, J. (2021). Prediction of oil film thickness in trochoidal pump. Trans. Can. Soc. Mech. Eng. 45, 374–383. doi:10.1139/tcsme-2020-0105
Ueda, M., Kadiric, A., and Spikes, H. (2021). Wear of hydrogenated DLC in MoDTC-containing oils. Wear 474-475, 203869–475. doi:10.1016/j.wear.2021.203869
Vaitkunaite, G., Espejo, C., Thiebaut, B., Neville, A., and Morina, A. (2022). Low friction tribofilm formation and distribution on an engine cylinder tested with MoDTC-containing low viscosity engine lubricants. Tribol. Int. 171, 107551. doi:10.1016/j.triboint.2022.107551
Vengudusamy, B., Green, J. H., Lamb, G. D., and Spikes, H. A. (2012). Behaviour of MoDTC in DLC/DLC and DLC/steel contacts. Tribol. Int. 54, 68–76. doi:10.1016/j.triboint.2012.04.028
Wade, A., Copley, R., Alsheikh Omar, A., Clarke, B., Liskiewicz, T., and Bryant, M. (2020a). Novel numerical method for parameterising fretting contacts. Tribol. Int. 149, 105826. doi:10.1016/j.triboint.2019.06.019
Wade, A., Copley, R., Clarke, B., Alsheikh Omar, A., Beadling, A. R., Liskiewicz, T., et al. (2020b). Real-time fretting loop regime transition identification using acoustic emissions. Tribol. Int. 145, 106149. doi:10.1016/j.triboint.2019.106149
Waterhouse, R. B. (1976). Fretting fatigue. Mater. Sci. Eng. 25, 201–206. doi:10.1016/0025-5416(76)90071-9
Yue, Z., Fan, X., Wang, Y., Li, H., Zhang, J., and Zhu, M. (2023). Fretting behaviors of self-mated diamond-like carbon films: the evolution of fretting regime and transfer film. Carbon 203, 695–705. doi:10.1016/j.carbon.2022.12.032
Zhang, S., Xie, H., Zeng, X., and Hing, P. (1999). Residual stress characterization of diamond-like carbon coatings by an X-ray diffraction method. Surf. Coat. Technol. 122, 219–224. doi:10.1016/S0257-8972(99)00298-4
Zhou, Z. R., and Vincent, L. (1999). Lubrication in fretting - a review. Wear 225–229, 962–967. doi:10.1016/S0043-1648(99)00038-1
Zhu, M. H., and Zhou, Z. R. (2011). “On the mechanisms of various fretting wear modes,” in Tribology international (Elsevier), 1378–1388. doi:10.1016/j.triboint.2011.02.010
Keywords: DLC, fretting, lubrication, contact pressure, lubricant additives
Citation: McMaster SJ, Kosarieh S, Liskiewicz TW and Beake BD (2025) Fretting wear of lubricated DLC coating systems. Front. Mech. Eng. 11:1584451. doi: 10.3389/fmech.2025.1584451
Received: 27 February 2025; Accepted: 01 July 2025;
Published: 16 July 2025.
Edited by:
Daniele Dini, Imperial College London, United KingdomReviewed by:
Seyed Borhan Mousavi, Texas A and M University, United StatesMilan Bukvic, University of Kragujevac, Serbia
Copyright © 2025 McMaster, Kosarieh, Liskiewicz and Beake. This is an open-access article distributed under the terms of the Creative Commons Attribution License (CC BY). The use, distribution or reproduction in other forums is permitted, provided the original author(s) and the copyright owner(s) are credited and that the original publication in this journal is cited, in accordance with accepted academic practice. No use, distribution or reproduction is permitted which does not comply with these terms.
*Correspondence: Tomasz W. Liskiewicz, dC5saXNraWV3aWN6QG1tdS5hYy51aw==