- 1Shandong Electric Power Engineering Consulting Institute Corp., Ltd., Jinan, Shandong, China
- 2School of Civil Engineering, Shandong Jianzhu University, Jinan, Shandong, China
- 3Key Laboratory of Building Structural Retrofitting and Underground Space Engineering (Shandong Jianzhu University), Ministry of Education, Jinan, Shandong, China
- 4Shandong Binhai Energy Co., Ltd., Weifang, Shandong, China
This study was conducted on an integrated wind-solar-storage-transmission base project located in a saline-alkali tidal flat area. The brine formation mechanism in saline-alkali tidal flats was revealed, and the chemical composition of the brine was comprehensively characterized by on-site tests. The mechanisms and causes of corrosion of PHC pipe piles under brine exposure were revealed. Field tests of the surface morphology and thickness changes for four types of anticorrosion coatings applied to PHC pipe piles were conducted to determine the protective performance of each anticorrosion coating. The results show that PHC pipe pile corrosion in the brine environment of saline-alkali tidal flats is primarily driven by hydrogen ion erosion. After nearly 1 year of in situ corrosion testing, the surfaces of ZB, ZH, TD-D (double-sided application), and LC exhibited oxidation and darkening in color, with coating thickness reductions ranging from 0 to approximately 0.35 mm; however, the coatings remained largely intact. For the TD-S specimens (single-sided application), the coated surface darkened, whereas the uncoated surface experienced severe corrosion, with a thickness reduction of approximately 1.8 mm, accompanied by mortar spalling and coarse aggregate exposure. All four anticorrosive coatings demonstrated favorable protective performances. A comprehensive evaluation model was employed to grade and score the coatings based on three performance indicators, which revealed that the TD anticorrosive coating exhibited the best overall performance. This study provides essential scientific evidence and technical support for the durability design and protective measures of concrete structures under aggressive environmental conditions.
1 Introduction
In recent years, photovoltaic (PV) power generation, an important form of renewable energy, has rapidly developed globally, becoming a key driver for energy transition and green low-carbon development. With the continuous expansion of the scale of PV projects, the application of traditional PHC pipe piles in PV foundations has become increasingly widespread, particularly in coastal seawater environments (Wang et al., 2022). In such environments, the primary factors contributing to pile corrosion are chloride and sulfate ions. However, compared with conventional seawater, brine contains much higher concentrations of corrosive substances, such as chloride and sulfate ions. These aggressive ions significantly accelerate the carbonation of the concrete surface and the corrosion of the internal steel reinforcement, resulting in a decline in the structural strength and a substantial reduction in the durability of the pipe piles. Moreover, the high permeability and electrical conductivity of brine further exacerbate the electrochemical corrosion process, rendering PHC pipe piles highly susceptible to cracking, spalling, and even fracturing during long-term service (Tian H. et al., 2023), as illustrated in Figure 1. Therefore, the corrosion of PHC pipe piles in brine environments poses a serious threat to engineering safety and significantly shortens their service life, necessitating the implementation of effective protective measures (Wang et al., 2024). Although heavy-duty anticorrosion systems developed for traditional marine engineering applications can technically address these issues, photovoltaic power generation projects differ in their structure anticorrosion. PV power generation projects are highly cost-sensitive, making such high-cost solutions impractical. Consequently, it is necessary to develop low-cost, yet highly durable, anticorrosion strategies for PHC pipe piles in brine-rich environments.
Currently, studies on the corrosion behavior of reinforced concrete have primarily focused on marine environmental conditions, with systematic investigations conducted on corrosion mechanisms, material degradation processes, and protective measures. Qian et al. (2023a) investigated the corrosion behavior of reinforced concrete beams exposed to a marine atmospheric environment for 7 years and analyzed the chloride distribution, carbonation, and corrosion products. The results indicated two distinct chloride accumulation zones located near the carbonation depth and at the boundary region, corresponding to an increasing corrosion depth. Wang and Zhang (2018) simulated harsh marine conditions through a combined “UV exposure + cyclic immersion” accelerated test to study the aging behavior of organic coatings. The experimental results revealed that, under the combined effects of ultraviolet radiation and water immersion, significant changes occurred in the coating thickness, gloss, and surface morphology. Chen et al. (2022) examined the structural performance of reinforced concrete columns in marine environments and proposed material degradation and structural strength reduction models based on the damage mechanisms induced by reinforcement corrosion. This study also estimated the service life of the corroded reinforced concrete columns under various corrosive conditions.
The aforementioned studies focused primarily on the corrosion and protection of reinforced concrete in marine environments. However, brine environments differ significantly from typical marine conditions. After bromine extraction, the brine exhibited much higher concentrations of hydrogen, chloride, and sulfate ions than conventional seawater. Zhao et al. (2018) investigated the effect of ion erosion in brine environments on the HPC strength and observed that the incorporation of mineral admixtures significantly improved the corrosion resistance of concrete. Sulfate ion erosion was identified as the main cause of concrete damage and compressive strength reduction, whereas chloride ions helped slow the progression of the sulfate attack. Tian H. et al. (2023) studied the corrosion characteristics of reinforced concrete in saline soil environments using electrochemical tests, chloride concentration measurements, and damage assessments. The results showed that the deterioration of reinforced concrete increased nonlinearly over time. Li Z. et al. (2024) explored the influence of temperature and water–cement ratio on the corrosion of reinforcements in high-salinity lake water environments. The findings indicated that, although temperature and salinity had limited effects on the corrosion potential, the initiation of corrosion in saline lake water was much faster than that in marine environments, with the corrosion rates accelerating as the temperature and water–cement ratio increased. Currently, studies on the performance of anticorrosive coatings largely rely on laboratory simulation tests, whereas field-based studies remain limited. This limitation may reduce the applicability of the test results in real-world scenarios, particularly in complex natural environments, where the long-term protective performance of coatings is difficult to evaluate accurately.
Therefore, based on an integrated wind-solar-storage-transmission base project in saline-alkali tidal flats, the corrosion mechanism of PHC pipe pile foundations under brine exposure was investigated. Four anticorrosive coating systems were selected for comparison through the field testing of the surface morphology and thickness variation. Furthermore, a comprehensive evaluation of the durability and cost-effectiveness of the coatings was conducted using an analytic hierarchy process (AHP), leading to the recommendation of a high-cost anticorrosion solution.
2 Corrosion mechanism of PV PHC pipe pile foundations in brine environments
2.1 Brine composition analysis
Based on the typical technological process of halogen production, the procedure can generally be divided into the following key functional zones:
(1) Water Intake Zone: This area is responsible for introducing raw brine or salt lake water. The water composition is complex, with relatively low salinity but a wide range of corrosive agents, making it a source of initial corrosion.
(2) Standard Brine Evaporation Zone: Comprising a series of solar ponds and evaporation basins, this zone facilitates brine concentration. The environment here is relatively stable in terms of water fluctuation, but the gradually increasing salinity leads to long-term corrosive effects.
(3) Concentration and Crystallization Zone: At this stage, the brine approaches saturation or even undergoes crystallization. Besides the extreme salt concentration, the formation of salt crystals on concrete or reinforcement surfaces may induce crystallization pressure and pore blockage, triggering stress corrosion and the development of microcracks.
(4) Drainage Outlet Zone: This is the outlet for brine circulation or discharge. Characterized by high flow velocity, strong hydrodynamic impact, and frequent wet–dry cycles, this zone also exhibits high salinity, elevated dissolved oxygen content, and significant temperature fluctuations.
Field investigations (see Figure 1) indicate that the drainage outlet zone is the most severely corroded area, where surface concrete spalling and propagation of microcracks in PHC piles are commonly observed. Therefore, this study selects the drainage outlet zone as the representative condition for corrosion testing and performance evaluation of protective coatings, providing guidance for optimizing protection strategies in high-risk corrosion environments.
The brine in saline-alkali tidal flat areas is rich in various salts. To analyze the salt components in the brine, ion chromatography was employed to determine the concentrations of major ions, such as Na+, Ca2+, Mg2+, Cl−, and SO42- (Wang, 2024) (see Table 1). According to the Code for Investigation of Geotechnical Engineering (GB 50021-2001) (Ministry of Construction of the People’s Republic of China, 2002), the environmental conditions of the site fall under the Type II classification. The site investigation results indicated that brine poses a strong corrosive threat to both the concrete structure and the embedded reinforcement. The evaluation of the corrosiveness of brine for construction materials is summarized in Table 1, and the main salt contents and corresponding corrosion grades are shown in Figure 2. The representative site conditions are shown in Figure 3.
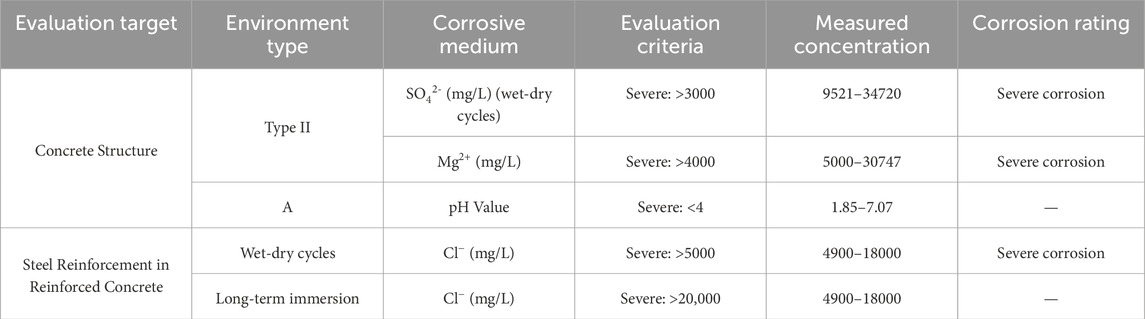
Table 1. Evaluation of the corrosiveness of brine from a typical brine pond to construction materials.
The brine corrosion environment in saline-alkali tidal flats is similar to that of marine environments but is characterized by higher salinity and stronger corrosiveness. Based on the exposure conditions of PHC pipe piles to brine environments, the brine corrosion environment in saline-alkali tidal flats can be divided into four zones: atmospheric zone, tidal zone, immersion zone, and brine mud zone (Li Y. et al., 2024) (see Figure 4). The tidal zone refers to the transitional area where, due to periodic water level fluctuations, the surface of the test specimens is repeatedly exposed to both air and liquid. According to field observations, the tidal zone in the brine pond is primarily influenced by artificial water level regulation and wind-induced disturbances, with a typical daily fluctuation range of approximately 20–30 cm. To ensure that the specimens are located within this zone, the top of the cylindrical specimens were positioned above the highest tidal level, while the square specimens were placed near the water surface. Based on the actual operational water level records of the brine pond, the location of the tidal range zone was reasonably determined, ensuring that the zone can accurately reflect the corrosion characteristics under alternating wetting and drying conditions. Each zone exhibits a distinct corrosion mechanism. The characteristics of the corrosive environment and corrosion in each zone are summarized in Table 2.
The atmospheric zone is located above the tidal zone. As the brine evaporates, a large quantity of salt particles enters the air, forming a salt spray. Simultaneously, water vapor condenses on the surface of the PHC pipe piles, forming a water film in which salt particles dissolve, creating a strong electrolyte solution. This solution penetrates the interior of PHC piles through capillary action and diffusion, resulting in salt-spray corrosion. In addition, acidic gases, such as CO2 and SO2, in the atmosphere can infiltrate concrete through pores and react with alkaline components inside the PHC pipe piles, leading to carbonation reactions (Qian et al., 2023b).
The tidal zone lies above and below the immersion and atmospheric zones. In this region, PHC pipe piles undergo alternating wetting and drying cycles. Chloride ions and other salts on the concrete surface can penetrate piles through capillary adsorption, diffusion, and permeation mechanisms (Zhang et al., 2018). During high tide, the dry concrete surface comes into contact with the brine and absorbs it through capillary action until saturation is reached. During low tide, as moisture evaporates from the concrete surface, the concentration of salts in the pore solution increases, resulting in a chloride ion concentration gradient between the surface and the interior. This drives the diffusion of salts from the surface pore solution into the interior of the concrete (Qiao et al., 2017), eventually reaching the reinforcing steel and initiating electrochemical reactions that accelerate corrosion.
The immersion and brine mud zones are located below the brine level, where the concentrations of chloride and sulfate ions are high. However, owing to the limited availability of oxygen in water, the corrosion rate of the reinforcing steel in these zones is relatively slow.
2.2 Corrosion mechanism of PV PHC pipe pile foundations
2.2.1 Chloride-induced corrosion mechanism
The pH of concrete is approximately 12.5. In such a strongly alkaline environment, a dense passive film forms on the surface of the embedded reinforcement (Wu et al., 2022), which is the fundamental reason why the steel in reinforced concrete structures does not corrode under normal conditions.
In a saline-alkali tidal flat environment, brine contains a high concentration of chlorides, and the corrosion of PHC pipe piles is driven by chloride ion intrusion and electrochemical reactions (Tian Y. et al., 2023; Xu et al., 2024). Chloride ions penetrate the interior of PHC piles through mechanisms, such as capillary suction, diffusion, permeation, and electrochemical migration. The typical diffusion coefficient of concrete ranges from 1 × 10−12 m2/s to 1 × 10−10 m2/s, with penetration depths usually between 10 mm and 50 mm. The chloride ions gradually accumulate on the reinforcement surface. As the chloride ion concentration increases, the local pH decreases. When the pH falls below 9.8, the passive film on the steel surface begins to deteriorate, exposing the reinforcement to the corrosive environment and leading to pitting or localized corrosion. The corroded regions of the reinforcement become anodic areas where oxidation reactions occur, whereas the regions still protected by the passive film act as cathodic areas where reduction reactions occur, as shown in Equations 1–3:
The Fe2+ ions generated in the anodic region react with Cl− to form water-soluble FeCl2, which subsequently diffuses into the surrounding solution. There, it reacts with OH− and O2 to form Fe(OH)2, accompanied by the generation of H+ ions. Throughout this process, Cl− is not consumed and functions essentially as a catalyst. Chloride ions not only participate in the formation of corrosion cells, but also accelerate the electrochemical reaction rate (Zuquan et al., 2018). This phenomenon is commonly referred to as anodic depolarization. The corresponding electrochemical reactions are shown in Equations 4, 5:
Meanwhile, Fe(OH)2 can be further oxidized to form Fe(OH)3 and Fe3O4.
2.2.2 Sulfate-induced corrosion mechanism
In brine environments, in addition to chloride ions, sulfate ions significantly contribute to the corrosion of PHC pipe piles. When external sulfate ions penetrate into the interior of the PHC pile, they react with calcium hydroxide (Ca(OH)2) and calcium aluminate hydrate (4CaO·Al2O3·19H2O) in the concrete, producing gypsum (CaSO4·2H2O) and ettringite (3CaO·Al2O3·3CaSO4·32H2O). As the corrosion products—gypsum and ettringite—have much larger volumes than the original reactants, expansive internal stresses develop within the concrete, leading to cracking and a reduction in compressive strength (Zhang et al., 2024). The chemical reactions are shown in Equations 6, 7:
2.2.3 Corrosion mechanism in acidic environments
Bromine extraction in brine ponds generates numerous hydrogen ions, significantly lowering the pH of the brine. Hydrogen ions infiltrate the interior of the PHC pipe piles and react with hydroxide ions (OH−), reducing the OH− concentration in the concrete, which lowers the pH and disrupts the alkaline environment required to stabilize various cement hydration products. When the pH drops below 10.4, these hydration products begin to decompose or the hydrogen ions directly react with the alkaline components of the hydration products. This leads to an increase in the concrete porosity, thereby reducing the strength and impermeability of the PHC pipe piles. Moreover, increased porosity facilitates the ingress of other harmful ions (Madraszewski et al., 2023; Youssari et al., 2023; Peng et al., 2022).
The investigations of the pH of brine and associated corrosion mechanisms indicate that hydrogen-ion-induced corrosion is predominant in the brine environments of saline-alkali tidal flats. Thus, anticorrosive coatings are proposed for application on the surface of PHC pipe piles to reduce the penetration rate of corrosive ions, such as H+ and Cl−, thereby achieving effective corrosion protection.
3 Field corrosion tests
3.1 Anticorrosive coating materials
Based on the existing concrete anticorrosion technologies and anticorrosion strategies used in similar brine environments (Vera et al., 2013), four types of coatings were selected: ZB solvent-free modified epoxy liquid coating, ZH acrylic anticorrosive coating, TD high-performance anticorrosive coating, and LC polyurea anticorrosive coating (see Table 3), considering factors, such as energy conservation and environmental protection. Field exposure tests were conducted on samples of these four coatings to establish the relationship between coating performance and natural corrosion conditions. Based on their anticorrosive performances in brine environments, the ultimate goal is to propose a cost-effective anticorrosion solution suitable for large-scale applications.
3.2 Experimental scheme
The drainage outlet of a brine pond was selected as the experimental site. After bromine extraction, the pH of the brine in this area was relatively low but gradually increased upon exposure to air.
Based on field investigation results (see Figure 1), it was found that the corrosion severity of PHC pipe piles is significantly greater in the tidal and immersion zones compared to the atmospheric and brine mud zones. To enhance the relevance and representativeness of the experiment, this study focused on conducting field exposure tests specifically in the tidal and immersion zones.
In the field test, cylindrical specimens with diameters of 120 mm, 80 mm, and 150 mm were used for ZB solvent-free modified epoxy coating, ZH acrylic anti-corrosion coating, and LC polyurea coating, respectively. These were labeled as P2 and P1 in the tidal and immersion zones. For the TD high-performance anti-corrosion coating, square specimens with a side length of 100 mm were used, with central points labeled as P3 and P4, and similarly placed in the tidal and immersion zones for testing. The specimen layout is illustrated in Figure 4.
The variation in size is mainly due to the fact that all specimens used in the experiment were provided by different anti-corrosion material manufacturers, and differences in mold fabrication led to slight inconsistencies in specimen dimensions. The square specimens were mainly used for the TD high-performance anti-corrosion coating, primarily to allow for separate investigation of different exposure zones. However, due to the larger quantity of test blocks and the inconvenience of storage, square specimens were not used for other coating materials in this study.
Considering that, under the same natural exposure conditions, the variation in corrosion resistance is mainly influenced by the type of coating and construction technique, while the geometric size and shape of the specimens have little effect on corrosion behavior. Thus, the impact of the specimen dimension can be neglected as long as other variables are properly controlled.
To ensure the consistency of the experimental results, the same specimens were used for both the surface morphology and thickness variation tests. The experimental schemes were primarily differentiated based on the coating thickness with the aim of observing the performance of coatings with varying thicknesses under the same environmental conditions. Fifteen series of tests with various anticorrosive coatings and coating schemes were performed, as listed in Table 4.
3.3 Corrosion test methods
The durability and anticorrosive performance of the coatings were evaluated by monitoring variations in the surface morphology and thickness under brine exposure in saline-alkali tidal flat environments during corrosion tests. The objective of the field test was to analyze the extent of coating damage after brine immersion and provide a scientific basis for material selection and the optimization of protective measures.
Surface morphology tests were conducted in accordance with the physical performance standards for Film-forming Coatings Specified In Film-forming Coatings For Concrete Structure Protection JG/T 335-2011 (2011). Each coating was uniformly applied to the surface of the concrete specimens and cured for 14 d under the specified conditions. Upon completion of the curing, the initial surface appearance of each specimen was recorded, including the coating smoothness and color uniformity. The specimens were then exposed to a brine environment, and every 120 d, the surface conditions were observed and recorded, focusing on discoloration, cracking, peeling, blistering, and other visual defects.
The thickness variation test was performed following the Pipeline Anticorrosion Coating Test Method-Part 7: Thickness Test SY/T 4113.7-2020 (2020). Each coating was applied to the specimen surface in accordance with the specified application procedures and cured for 14 d under the designated conditions. After curing, a digital caliper was used to measure the initial thickness of the coating. Two measurement locations were selected—one in the tidal zone and the other in the immersion zone—and marked using a permanent marker (see Figure 5). The specimens were then placed in a brine exposure environment, according to the experimental plan. Every 120 d, the coating thickness at the marked locations was measured using the digital caliper to assess the thickness variation over time.
4 Analysis of test results
4.1 Surface morphology analysis
Figures 6–10 show the specimens after different exposure durations. For the ZB solvent-free modified epoxy liquid coating, the surface color of specimens ZB1–ZB3 darkened, and the gloss significantly diminished. In contrast, specimens ZB4–ZB6 maintained a normal surface color, as shown in Figure 6.
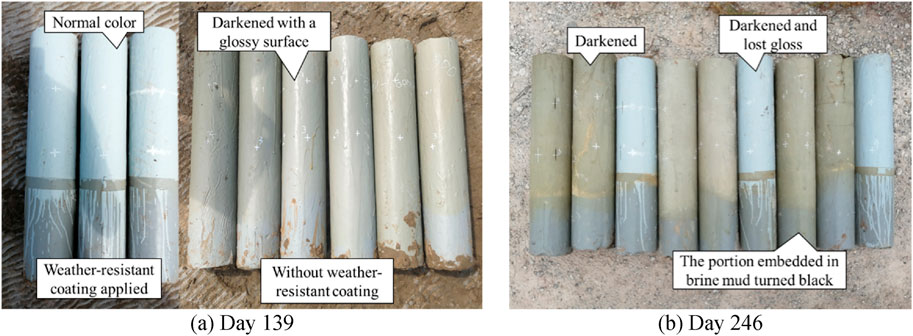
Figure 6. Surface morphology changes of ZB solvent-free modified epoxy liquid coating. (a) Day 139. (b) Day 246.
On day 246, for the ZH acrylic anticorrosive coating, specimens ZH1–ZH3 exhibited a noticeably dull and nonglossy surface. Additionally, black corrosion marks were observed on the portion embedded in the brine mud, as shown in Figure 7. This is primarily because acrylic coatings are based on organic polymer matrices. A dense cross-linking of acrylic coating is difficult to form, seriously limiting its durability and anticorrosion behavior, which was demonstrated by Faccini et al. (2021) and Ładosz et al. (2024). Brine mud is a special type of soft soil characterized by high cohesion and strong hydrophilicity. The colloidal fine particles in the mud can easily penetrate the micro-pores on the coating surface. Consequently, the acrylic anticorrosive coatings exhibited surface darkening after immersion in the brine mud zone.
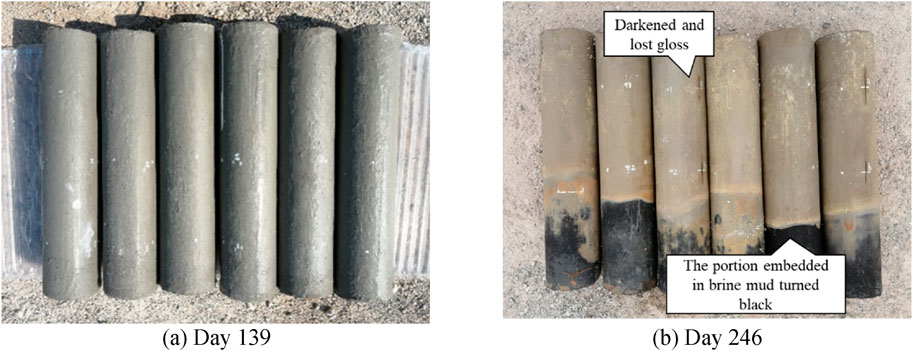
Figure 7. Surface morphology changes of ZH acrylic anti-corrosion coating. (a) Day 139. (b) Day 246.
After 246 d of exposure, the TD high-performance anticorrosive coating showed more severe surface degradation in specimens TD1–2-D and TD1–2-S, characterized by pronounced darkening and a complete loss of gloss, as illustrated in Figure 8. Similarly, the LC polyurea anticorrosive coating exhibited a loss of surface gloss in specimens LC1–2, as shown in Figure 9.

Figure 8. Surface morphology changes of TD high-performance anti-corrosion coating. (a) Day 1. (b) Day 246.
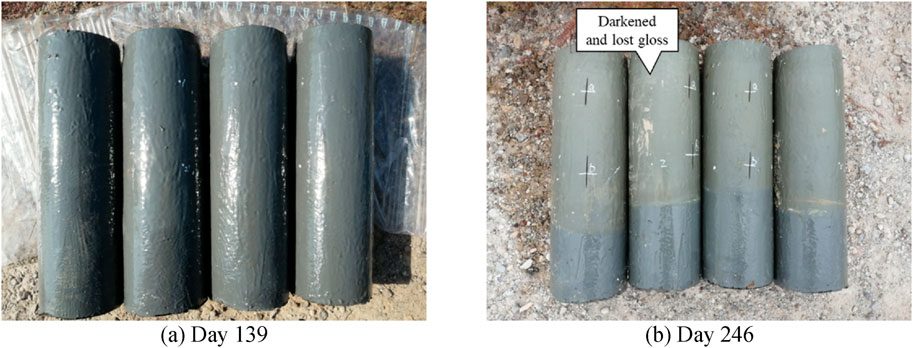
Figure 9. Surface morphology changes of LC polyurea anti-corrosion coating. (a) Day 139. (b) Day 246.
At the same observation point, the concrete surfaces without any protective coating exhibited significantly more severe corrosion. The coarse aggregates within the concrete were exposed, and the surface exhibited darkening, a loss of gloss, and the development of prominent cracks, as shown in Figure 10.
The test results demonstrate that anticorrosive coatings effectively mitigate the corrosion of concrete in brine environments, significantly enhancing the durability and service life of the structure.
4.2 Coating thickness analysis
The changes in the thicknesses of the four anticorrosive coatings are shown in Figures 11–14. The test results indicated an overall decreasing trend in the coating thickness in both the tidal and immersion zones. Moreover, the coatings experienced more severe degradation in the tidal zone than in the immersion zone.
As illustrated in Figures 11–14, the ZB, ZH, TD1, and LC coatings exhibited negligible changes in thickness during the initial 60 d of exposure. This was primarily attributed to the lower ambient temperatures during this period, which slowed the chemical corrosion processes. In addition, suspended operations at the test site during the winter season resulted in higher pH values and weaker brine acidity, thereby reducing its corrosive effect on the coatings. After 139 d, a more significant decrease in the coating thickness was observed. This can be attributed to rising temperatures, which accelerated chemical reactions and the resumption of production at the test site, leading to lower pH values and increased brine acidity, thereby intensifying coating corrosion. The annual temperature variations at the test sites are shown in Figure 15.
As shown in Figures 11–14, the reduction in coating thickness for the ZB, ZH, TD-D, and LC specimens generally ranged from 0 to 0.35 mm. By contrast, the TD-S specimens exhibited significantly more severe corrosion, with thickness reductions exceeding 1.8 mm. These results further demonstrate that anticorrosive coatings provide effective protection for concrete in brine environments.
5 Comprehensive evaluation of anticorrosive coating schemes
This study adopted an AHP to assess the overall performance of the four anticorrosive coatings to scientifically evaluate the protective performance of different anticorrosive coatings on PHC pipe piles in brine environments, and to compare and select the optimal solution based on the comprehensive performance. The AHP method proposed by American operations researcher Thomas L. Saaty in the early 1970s (Saaty, 2013) has been widely applied to multicriteria decision-making analyses. This method decomposes complex problems into multiple components, determines the relative importance of each factor through pairwise comparisons, and combines both quantitative and qualitative analyses to derive a comprehensive priority ranking (Tavana et al., 2023; Pant et al., 2022; Panchal and Shrivastava, 2022).
The anticorrosive coatings were evaluated based on three criteria: surface morphology change, thickness variation, and cost. The relative importance of each criterion in the overall decision-making process was determined accordingly. The experimental results indicated that all four coatings demonstrated good anticorrosive performance; therefore, cost emerged as a particularly critical factor in the comprehensive evaluation (see Table 5), with the average cost value taken as the assessment metric.
Regarding the importance scale, considering that the coatings showed only minor differences in anticorrosive performance but significant differences in cost, the relative importance of cost over thickness variation was set to 5 (strong preference), and that over surface morphology changed to 6 (very strong preference). Meanwhile, the thickness variation was considered to be slightly more important than the surface morphology change, with a relative importance of 2 (weak preference), as listed in Table 6. Based on the above judgment matrix and using the eigenvalue method for the calculation, the resulting weight coefficients for each criterion were obtained as follows: surface morphology change 0.1033, thickness variation 0.1741, and cost 0.7225. To verify the consistency of the judgment matrix, the maximum eigenvalue λ_max was calculated as approximately 3.0293, yielding a consistency index (CI) of 0.0146. Referring to the random index (RI) value of 0.58 for n = 3, the consistency ratio (CR) was determined to be CR = CI/RI = 0.0252 < 0.1, indicating that the judgment matrix had good consistency, and the assigned weights were reasonable and reliable.
As shown in Table 5, a 1-to-9 scale method was adopted for scoring. The surface appearance was evaluated based on the degree of visual degradation observed after natural exposure. A score of nine was assigned to coatings with no visible changes, indicating minimal degradation; a score of six corresponded to a darkened surface, reflecting moderate deterioration; and a score of three was assigned to coatings that darkened to black, indicating severe degradation.
The thickness variation was scored using the inverse grading principle, where a smaller reduction in thickness yielded a higher score. A linear normalization method was applied, assigning a score of nine to the minimum observed thickness loss and one to the maximum thickness loss, with intermediate values interpolated proportionally. The cost score was determined using the same normalization principle as the thickness variation, where a lower cost corresponded to a higher score.
The comprehensive scores of the anticorrosive coatings are listed in Table 7. The experimental results indicate that, excluding the effects of improper application, measurement errors, and force majeure factors, the ZB1 anticorrosive coating demonstrated the best overall performance in this study and can be considered the optimal anticorrosion solution for future applications to PHC pipe piles in brine environments.
In this study, a comprehensive evaluation of the various anticorrosive coatings was conducted using the Analytic Hierarchy Process (AHP), leading to the identification of an efficient corrosion protection strategy. The evaluation results are inherently influenced by multiple factors, including the judgment matrix and scoring criteria, which may introduce certain degrees of error and subjectivity. Therefore, the outcomes presented herein are intended solely for reference purposes based on the available data and scoring framework and should not be regarded as the sole basis for decision-making regarding corrosion protection strategies in saline-alkali tidal flat and brine environments.
6 Conclusion
To address the corrosion issues of PV PHC pipe pile foundations in saline-alkali tidal flat brine environments, the formation mechanisms and chemical composition of the brine were analyzed. The mechanisms and causes of corrosion of PHC pipe piles under brine exposure were comprehensively investigated. Four anticorrosive coating schemes were selected and evaluated using surface morphology and thickness variation tests to assess their durability. A comprehensive performance evaluation based on the AHP was conducted to determine cost-effectiveness and propose efficient anticorrosion solutions. The following conclusions were drawn:
1. The corrosion mechanisms of PHC pipe piles in brine environments are similar to those in marine environments, primarily involving chloride-, sulfate-, and acid-induced corrosion. Owing to the high concentration of hydrogen ions and the low pH of the brine, hydrogen ion erosion is the dominant mechanism. Therefore, it is recommended to apply anticorrosive coatings to the concrete surface to reduce the penetration of aggressive ions, such as H+ and Cl−, thereby effectively mitigating corrosion.
2. Surface morphology and thickness variation analyses revealed that, after 325 d of exposure, all the coatings experienced varying degrees of corrosion. The ZB, ZH, TD-D, and LC coatings showed signs of oxidation, yellowing, and darkening, with thickness reductions ranging approximately from 0 to 0.35 mm, though the coatings remained generally intact. By contrast, the TD-S specimens exhibited severe surface corrosion with a thickness reduction of approximately 1.8 mm, along with mortar spalling and coarse aggregate exposure.
3. A comprehensive evaluation model was used to assess the three performance indicators of the coatings. The results showed that, after 325 d of exposure, the TD high-performance coating demonstrated the best overall performance.
4. Anticorrosive coatings have proven to be an effective protective strategy for PHC pipe piles in brine environments. The following recommendations are proposed for the practical application of such coatings: Perform surface inspections every 6 months, focusing on cracks, peeling, or discoloration; promptly repair damaged areas to prevent the penetration of corrosive agents; and install corrosion sensors to monitor the real-time corrosion status of PHC piles, providing a scientific basis for maintenance decision-making.
5. The primary contribution of this study is the establishment of a systematic selection framework for anticorrosive materials tailored to high-salinity and high-humidity environments. By expanding the evaluation dimensions of PHC pile foundation materials, this study provides a quantifiable, comparable, and scalable technical basis for corrosion protection design in PV projects in saline-alkali regions. The findings not only offer practical guidance for engineering applications, but also serve as a methodological and empirical foundation for future research on protective systems for infrastructure in extreme environments.
Data availability statement
The raw data supporting the conclusions of this article will be made available by the authors, without undue reservation.
Author contributions
JW: Conceptualization, Data curation, Formal Analysis, Investigation, Methodology, Project administration, Resources, Supervision, Validation, Writing – original draft, Writing – review and editing. JH: Conceptualization, Data curation, Formal Analysis, Funding acquisition, Investigation, Methodology, Project administration, Validation, Visualization, Writing – original draft, Writing – review and editing. YL: Data curation, Formal Analysis, Investigation, Methodology, Resources, Validation, Visualization, Writing – original draft, Writing – review and editing. HS: Data curation, Formal Analysis, Investigation, Methodology, Resources, Validation, Writing – original draft, Writing – review and editing. HL: Data curation, Formal Analysis, Investigation, Methodology, Resources, Software, Supervision, Validation, Visualization, Writing – original draft, Writing – review and editing. XD: Data curation, Formal Analysis, Investigation, Validation, Writing – original draft, Writing – review and editing.
Funding
The author(s) declare that financial support was received for the research and/or publication of this article. This work was supported by the Key Research and Development Program of Gansu Province (22YF7FH224); and the Open Project of the Key Joint Laboratory of the Ministry of Education (2024KFKT-YB12).
Acknowledgments
This work was supported by the Key Research and Development Program of Gansu Province (22YF7FH224); and the Open Project of the Key Joint Laboratory of the Ministry of Education (2024KFKT-YB12). We deeply appreciate for the warm and efficient work by editors and reviewers.
Conflict of interest
Authors, JW, YL, and HS were employed by Shandong Electric Power Engineering Consulting Institute Corp., Ltd. Author XD was employed by Shandong Binhai Energy Co., Ltd.
The remaining authors declare that the research was conducted in the absence of any commercial or financial relationships that could be construed as a potential conflict of interest.
Generative AI statement
The author(s) declare that no Generative AI was used in the creation of this manuscript.
Publisher’s note
All claims expressed in this article are solely those of the authors and do not necessarily represent those of their affiliated organizations, or those of the publisher, the editors and the reviewers. Any product that may be evaluated in this article, or claim that may be made by its manufacturer, is not guaranteed or endorsed by the publisher.
References
Chen, H., Jiang, Y., and Markou, G. (2022). Structural performance deterioration of corroding reinforced concrete columns in marine environments. Ocean. Eng. 262, 112155. doi:10.1016/j.oceaneng.2022.112155
Faccini, M., Bautista, L., Soldi, L., Escobar, A. M., Altavilla, M., Calvet, M., et al. (2021). Environmentally friendly anticorrosive polymeric coatings. Appl. Sci. 11 (8), 3446. doi:10.3390/app11083446
Ładosz, Ł., Sudoł, E., Kozikowska, E., and Choińska, E. (2024). Artificial weathering test methods of waterborne acrylic coatings for steel structure corrosion protection. Materials 17, 1857. doi:10.3390/ma17081857
Li, Y., Tang, B., and Li, W. (2024). Durability of concrete structures in salt and freshwater confluence area. Bull. Chin. Ceram. Soc. 43 (12), 4389–4397.
Li, Z., Wang, Y., Sun, X., and Liu, B. (2024). Experimental investigation on the effects of temperature and w/c on corrosion characteristics of rebars in concrete exposed to salt lake environments. J. Mater. Sci. 59 (33), 15786–15801. doi:10.1007/s10853-024-10083-y
Madraszewski, S., Sielaff, A. M., and Stephan, D. (2023). Acid attack on concrete–Damage zones of concrete and kinetics of damage in a simulating laboratory test method for wastewater systems. Constr. Build. Mater. 366, 130121. doi:10.1016/j.conbuildmat.2022.130121
Ministry of Construction of the People's Republic of China (2002). Code for investigation of geotechnical engineering. Beijing: China Architecture and Building Press.
Panchal, S., and Shrivastava, A. K. (2022). Landslide hazard assessment using analytic hierarchy process (AHP): a case study of National Highway 5 in India. Ain Shams Eng. J. 13 (3), 101626. doi:10.1016/j.asej.2021.10.021
Pant, S., Kumar, A., Ram, M., Klochkov, Y., and Sharma, H. K. (2022). Consistency indices in analytic hierarchy process: a review. Mathematics 10 (8), 1206. doi:10.3390/math10081206
Peng, Y., Meng, X., Song, F., and Xu, G. (2022). Experimental study on the corrosion characteristics of concrete exposed to acid water containing aggressive carbon dioxide and sodium sulfate. Constr. Build. Mater. 321, 126397. doi:10.1016/j.conbuildmat.2022.126397
Qian, R., Li, Q., Fu, C., Zhang, Y., Wang, Y., Jin, N., et al. (2023b). Investigations on atmospheric carbonation corrosion of concrete structure beam exposed to real marine-environment for 7 years. J. Build. Eng. 71, 106517. doi:10.1016/j.jobe.2023.106517
Qian, R., Li, Q., Fu, C., Zhang, Y., Wang, Y., and Jin, X. (2023a). Atmospheric chloride-induced corrosion of steel-reinforced concrete beam exposed to real marine environment for 7 years. Ocean. Eng. 286, 115675. doi:10.1016/j.oceaneng.2023.115675
Qiao, C., Ni, W., and Weiss, J. (2017). Transport due to diffusion, drying, and wicking in concrete containing a shrinkage-reducing admixture. J. Mater. Civ. Eng. 29 (9), 04017146. doi:10.1061/(asce)mt.1943-5533.0001983
Saaty, T. L. (2013). The modern science of multicriteria decision making and its practical applications: the AHP/ANP approach. Operations Res. 61 (5), 1101–1118. doi:10.1287/opre.2013.1197
Tavana, M., Soltanifar, M., and Santos-Arteaga, F. J. (2023). Analytical hierarchy process: revolution and evolution. Ann. Operations Res. 326 (2), 879–907. doi:10.1007/s10479-021-04432-2
Tian, H., Qiao, H., Feng, Q., and Han, W. (2023). Corrosion deterioration of reinforced concrete in a saline soil environment. J. Mater. Civ. Eng. 35 (11), 4023387. doi:10.1061/jmcee7.mteng-16258
Tian, Y., Zhang, G., Ye, H., Zeng, Q., Zhang, Z., Tian, Z., et al. (2023). Corrosion of steel rebar in concrete induced by chloride ions under natural environments. Constr. Build. Mater. 369, 130504. doi:10.1016/j.conbuildmat.2023.130504
Vera, R., Apablaza, J., Carvajal, A. M., and Vera, E. (2013). Effect of surface coatings in the corrosion of reinforced concrete in acid environments. Int. J. Electrochem. Sci. 8 (10), 11832–11846. doi:10.1016/s1452-3981(23)13226-3
Wang, H., Chen, H., Yang, C., and Li, J. (2022). Durable life assessment of centrifugal stratified PHC piles in marine environment. Eng. Struct. 263, 114404. doi:10.1016/j.engstruct.2022.114404
Wang, H., and Zhang, H. (2018). Study on the anticorrosion performance of organic coatings in simulated marine environments. China Coatings 33 (09), 25–30. doi:10.13531/j.cnki.china.coatings.2018.09.005
Wang, J. (2024). Experimental study on corrosion resistance of PHC pipe pile foundation of saltern photovoltaic power station [D]. Beijing: Beijing University of Civil Engineering and Architecture. doi:10.26943/d.cnki.gbjzc.2024.000725
Wang, Y., Deng, M., Zhang, R., Yu, X., Xue, J., and Zhang, J. (2024). Durability of prestressed piles in a leachate environment. Materials 17 (11), 2497. doi:10.3390/ma17112497
Wu, W., He, X., Yang, W., Dai, L., Wang, Y., and He, J. (2022). Long-time durability of GFRP bars in the alkaline concrete environment for eight years. Constr. Build. Mater. 314, 125573. doi:10.1016/j.conbuildmat.2021.125573
Xu, Q., Liu, B., Dai, L., Yao, M., and Pang, X. (2024). Factors influencing chloride ion diffusion in reinforced concrete structures. Materials 17 (13), 3296. doi:10.3390/ma17133296
Youssari, F. Z., Taleb, O., and Benosman, A. S. (2023). Towards understanding the behavior of fiber-reinforced concrete in aggressive environments: acid attacks and leaching. Constr. Build. Mater. 368, 130444. doi:10.1016/j.conbuildmat.2023.130444
Zhang, C., Li, J., Yu, M., Lu, Y., and Liu, S. (2024). Mechanism and performance control methods of sulfate attack on concrete: a review. Materials 17 (19), 4836. doi:10.3390/ma17194836
Zhang, Y., Zhang, M., and Ye, G. (2018). Influence of moisture condition on chloride diffusion in partially saturated ordinary Portland cement mortar. Mater. Struct. 51, 36–18. doi:10.1617/s11527-018-1162-7
Zhao, X., Liu, L., and Liu, C. (2018). Influence of ion erosion on hpc strength in brine environment. Bull. Chin. Ceram. Soc. 37 (4), 1363–1369. doi:10.16552/j.cnki.issn1001-1625.2018.04.039
Keywords: saline-alkali tidal flats, salt-lake brine environment, PHC pipe piles, corrosion mechanism, photovoltaic power generation, anticorrosive coatings
Citation: Wu J, Han J, Luo Y, Song H, Li H and Dong X (2025) Performance of anticorrosive coatings for photovoltaic PHC pipe piles in brine environments of saline-alkali tidal flats. Front. Earth Sci. 13:1620850. doi: 10.3389/feart.2025.1620850
Received: 30 April 2025; Accepted: 30 June 2025;
Published: 15 July 2025.
Edited by:
Pengfei Liu, CCCC Second Harbor Engineering Co., Ltd., ChinaReviewed by:
Fengyuan Wu, Shenyang Jianzhu University, ChinaLuobin Zheng, Wuhan University of Science and Technology, China
Copyright © 2025 Wu, Han, Luo, Song, Li and Dong. This is an open-access article distributed under the terms of the Creative Commons Attribution License (CC BY). The use, distribution or reproduction in other forums is permitted, provided the original author(s) and the copyright owner(s) are credited and that the original publication in this journal is cited, in accordance with accepted academic practice. No use, distribution or reproduction is permitted which does not comply with these terms.
*Correspondence: Jianyong Han, aGFubHdiQDE2My5jb20=